Page 2985 of 5883
![NISSAN TIIDA 2007 Service Repair Manual EM-338
< SERVICE DATA AND SPECIFICATIONS (SDS) [K9K]
SERVICE DATA AND SPECIFICATIONS (SDS)
PISTON
Unit: mm (in)
PISTON RING
Unit: mm (in)
PISTON PIN
Unit: mm (in)
3 Used by the supplier only
4 Used by NISSAN TIIDA 2007 Service Repair Manual EM-338
< SERVICE DATA AND SPECIFICATIONS (SDS) [K9K]
SERVICE DATA AND SPECIFICATIONS (SDS)
PISTON
Unit: mm (in)
PISTON RING
Unit: mm (in)
PISTON PIN
Unit: mm (in)
3 Used by the supplier only
4 Used by](/manual-img/5/57395/w960_57395-2984.png)
EM-338
< SERVICE DATA AND SPECIFICATIONS (SDS) [K9K]
SERVICE DATA AND SPECIFICATIONS (SDS)
PISTON
Unit: mm (in)
PISTON RING
Unit: mm (in)
PISTON PIN
Unit: mm (in)
3 Used by the supplier only
4 Used by the supplier only
5 Used by the supplier only
6 Piston axis of symmetry
7 Piston pin hole axis
8 Offset between the hole axis (7) and the piston's axis of symmetry (6) is 0.3 mm (0.012 in)
Items Standard
Piston skirt diameter “A” mm (in) 75.938 - 75.952 (2.9897 - 2.9902)
“a” dimension mm (in) 56.0 (2.205)
Piston pin hole diameter mm (in)Category J 41.605 - 41.646 (1.6380 - 1.6396)
Category K 41.647 - 41.688 (1.6396 - 1.6413)
Category L 41.689 - 41.730 (1.6413 - 1.6429)
Category M 41.731 - 41.772 (1.6429 - 1.6446)
Category N 41.773 - 41.814 (1.6446 - 1.6462)
“b” dimension mm (in) 26.0 (1.024)
Capacity of combustion chamber
m (Imp fl oz)19.71 - 20.21 (0.67 - 0.71)
Piston protrusion mm (in) 0.030 - 0.288 (0.0012 - 0.113)
SEM882E
Items Standard
ThicknessTop 1.97 - 1.99 (0.0776 - 0.0783)
2nd 1.97 - 1.99 (0.0776 - 0.0783)
Oil ring 2.47 - 2.49 (0.0972 - 0.0980)
Side clearanceTop 0.10 - 0.12 (0.0039 - 0.0047)
2nd 0.08 - 0.10 (0.0031 - 0.0039)
Oil ring 0.03 - 0.05 (0.0012 - 0.0020)
Piston ring end gapTop 0.20 - 0.35 (0.0079 - 0.0138)
2nd 0.70 - 0.90 (0.0276 - 0.0354)
Oil ring 0.25 - 0.50 (0.0098 - 0.0197)
Items Standard
Length59.7 - 60.0 (2.350 - 2.362)
Piston pin outer diameter 25.995 - 26.000 (1.0234 - 1.0236)
Page 2986 of 5883
![NISSAN TIIDA 2007 Service Repair Manual SERVICE DATA AND SPECIFICATIONS (SDS)
EM-339
< SERVICE DATA AND SPECIFICATIONS (SDS) [K9K]
C
D
E
F
G
H
I
J
K
L
MA
EM
N
P O
CONNECTING ROD
Unit: mm (in)
CRANKSHAFT
Unit: mm (in)
TurbochargerINFOID:0000 NISSAN TIIDA 2007 Service Repair Manual SERVICE DATA AND SPECIFICATIONS (SDS)
EM-339
< SERVICE DATA AND SPECIFICATIONS (SDS) [K9K]
C
D
E
F
G
H
I
J
K
L
MA
EM
N
P O
CONNECTING ROD
Unit: mm (in)
CRANKSHAFT
Unit: mm (in)
TurbochargerINFOID:0000](/manual-img/5/57395/w960_57395-2985.png)
SERVICE DATA AND SPECIFICATIONS (SDS)
EM-339
< SERVICE DATA AND SPECIFICATIONS (SDS) [K9K]
C
D
E
F
G
H
I
J
K
L
MA
EM
N
P O
CONNECTING ROD
Unit: mm (in)
CRANKSHAFT
Unit: mm (in)
TurbochargerINFOID:0000000001381521
Items Standard
Center distance133.75 (5.266)
Connecting rod small end diameter (with bush) 26.013 - 26.025 (1.0241 - 1.0246)
Connecting rod big end diameter 47.610 - 47.627 (1.8744 - 1.8751)
Big end longitudinal play 0.205 - 0.467 (0.0081 - 0.0184)
Big end radial play 0.010 - 0.064 (0.004 - 0.025)
Items Standard
Main journal diameter “Dm” 47.99 - 48.01 (1.8894 - 1.8902)
Pin journal diameter “Dp” 43.96 - 43.98 (1.7307 - 1.7315)
Maximum run-out allowed on the flywheel bearing face of the flywheel 0.6 (0.024)
Lateral play (without lateral shim) 0.045 - 0.252 (0.0018 - 0.0099)
Lateral play (with lateral shim) 0.045 - 0.852 (0.0018 - 0.0335)
Journal radial play 0.010 - 0.054 (0.0004 - 0.0021)
E1BIA0067ZZ
Items Standard
Regulation value operating vacuum
kPa (bar, kg/cm
2, psi)50 (0.5, 0.51, 7.3)
Valve rod moving length mm (in) 1.7 (0.067)
Page 2987 of 5883
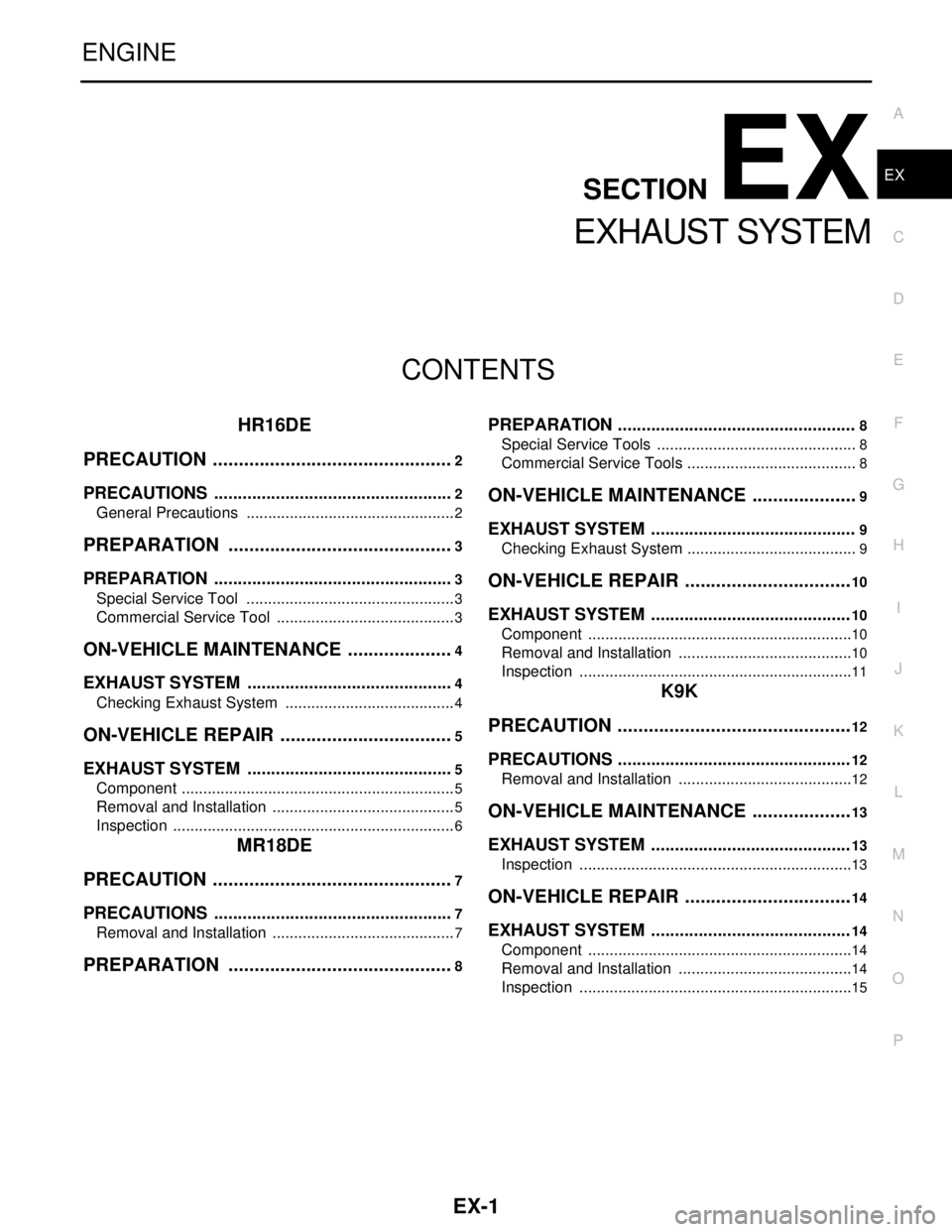
EX-1
ENGINE
C
D
E
F
G
H
I
J
K
L
M
SECTION EX
A
EX
N
O
P
CONTENTS
EXHAUST SYSTEM
HR16DE
PRECAUTION ...............................................
2
PRECAUTIONS ...................................................2
General Precautions .................................................2
PREPARATION ............................................3
PREPARATION ...................................................3
Special Service Tool .................................................3
Commercial Service Tool ..........................................3
ON-VEHICLE MAINTENANCE .....................4
EXHAUST SYSTEM ............................................4
Checking Exhaust System ........................................4
ON-VEHICLE REPAIR ..................................5
EXHAUST SYSTEM ............................................5
Component ................................................................5
Removal and Installation ...........................................5
Inspection ..................................................................6
MR18DE
PRECAUTION ...............................................
7
PRECAUTIONS ...................................................7
Removal and Installation ...........................................7
PREPARATION ............................................8
PREPARATION ..................................................8
Special Service Tools ...............................................8
Commercial Service Tools ........................................8
ON-VEHICLE MAINTENANCE .....................9
EXHAUST SYSTEM ...........................................9
Checking Exhaust System ........................................9
ON-VEHICLE REPAIR .................................10
EXHAUST SYSTEM ..........................................10
Component ..............................................................10
Removal and Installation .........................................10
Inspection ................................................................11
K9K
PRECAUTION ..............................................
12
PRECAUTIONS .................................................12
Removal and Installation .........................................12
ON-VEHICLE MAINTENANCE ....................13
EXHAUST SYSTEM ..........................................13
Inspection ................................................................13
ON-VEHICLE REPAIR .................................14
EXHAUST SYSTEM ..........................................14
Component ..............................................................14
Removal and Installation .........................................14
Inspection ................................................................15
Page 2988 of 5883
EX-2
< PRECAUTION >[HR16DE]
PRECAUTIONS
PRECAUTION
PRECAUTIONS
General PrecautionsINFOID:0000000001728590
CAUTION:
• Be sure to use genuine exhaust system parts or equivalents which are specially designed for heat
resistance, corrosion resistance, and shape.
Perform the operation with the exhaust system fully cooled down because the system will be hot
just after engine stops.
Be careful not to cut your hand on the heat insulator edge.
Page 2989 of 5883
PREPARATION
EX-3
< PREPARATION >[HR16DE]
C
D
E
F
G
H
I
J
K
L
MA
EX
N
P O
PREPARATION
PREPARATION
Special Service ToolINFOID:0000000001337856
Commercial Service ToolINFOID:0000000001337857
Tool number
Tool nameDescription
KV10114400
(J-38365)
Heated oxygen sensor wrenchLoosening or tightening heated oxygen sen-
sor
a: 22 mm (0.87 in)
NT636
Tool nameDescription
Heated oxygen sensor thread cleaner Reconditioning the exhaust system threads
before installing a new heated oxygen sensor
(Use with anti-seize lubricant shown below.)
a: 18 mm (0.71 in) dia. for zirconia heated
oxygen sensor
b: 12 mm (0.47 in) dia. for titania heated ox-
ygen sensor
Anti-seize lubricant (Permatex 133AR
or equivalent meeting MIL specifica-
tion MIL-A-907)Lubricating heated oxygen sensor thread
cleaner when reconditioning exhaust system
threads
AEM488
AEM489
Page 2990 of 5883
EX-4
< ON-VEHICLE MAINTENANCE >[HR16DE]
EXHAUST SYSTEM
ON-VEHICLE MAINTENANCE
EXHAUST SYSTEM
Checking Exhaust SystemINFOID:0000000001337858
Check exhaust pipes, muffler and mounting for improper attachment,
leaks, cracks, damage or deterioration.
• If necessary, repair or replace damaged parts.
SMA211A
Page 2991 of 5883
EXHAUST SYSTEM
EX-5
< ON-VEHICLE REPAIR >[HR16DE]
C
D
E
F
G
H
I
J
K
L
MA
EX
N
P O
ON-VEHICLE REPAIR
EXHAUST SYSTEM
ComponentINFOID:0000000001337859
Removal and InstallationINFOID:0000000001337860
REMOVAL
CAUTION:
Be sure to use genuine NISSAN exhaust system parts or equivalents which are specially designed
for heat resistance, corrosion resistance and shape.
Perform the operation with the exhaust system fully cooled down because the system will be hot
just after the engine stops.
Be careful not to cut your hand on heat insulator edge.
1. Disconnect harness connector of heated oxygen sensor 2.
Using Tool, remove heated oxygen sensor 2.
CAUTION:
Be careful not to damage heated oxygen sensor 2.
a.
1. Main muffler 2. Mounting rubber 3. Ring gasket
4. Center muffler 5. Mounting rubber 6. Spring
7. Seal bearing 8. Heated oxygen sensor 2 9. Exhaust front tube
10. Seal bearing 11. Stud bolt 12. Spring
13. Ground cable
WBIA0844E
Tool number : KV10114400 (J-38365)
Page 2992 of 5883
![NISSAN TIIDA 2007 Service Repair Manual EX-6
< ON-VEHICLE REPAIR >[HR16DE]
EXHAUST SYSTEM
2. Disconnect each joint and mounting rubber.
INSTALLATION
Installation is in the reverse order of removal.
CAUTION:
Always replace exhaust gaskets NISSAN TIIDA 2007 Service Repair Manual EX-6
< ON-VEHICLE REPAIR >[HR16DE]
EXHAUST SYSTEM
2. Disconnect each joint and mounting rubber.
INSTALLATION
Installation is in the reverse order of removal.
CAUTION:
Always replace exhaust gaskets](/manual-img/5/57395/w960_57395-2991.png)
EX-6
< ON-VEHICLE REPAIR >[HR16DE]
EXHAUST SYSTEM
2. Disconnect each joint and mounting rubber.
INSTALLATION
Installation is in the reverse order of removal.
CAUTION:
Always replace exhaust gaskets and seal bearings with new ones when installing.
Discard any heated oxygen sensor 2 which has been dropped from a height of more than 0.5 m (19.7
in) onto a hard surface such as a concrete floor; use a new one.
Before installing a new heated oxygen sensor 2, clean exhaust system threads using the heated oxy-
gen sensor thread cleaner and apply anti-seize lubricant (commercial service tool).
Do not over tighten heated oxygen sensor 2. Doing so may cause damage to the heated oxygen sen-
sor 2, resulting in the “MIL” coming on.
Remove deposits from the sealing surface of each connection. Connect them securely to avoid
exhaust leakage.
Temporarily tighten nuts on the exhaust manifold side and bolts on the vehicle side. Check each part
for unusual interference, and then tighten them to the specified torque.
When installing each mounting rubber, avoid twisting or unusual extension in up/down and right/left
directions.
Exhaust Manifold to Exhaust Front Tube
1. Securely insert seal bearing (2) into exhaust manifold (1) side in
the direction shown.
Exhaust front tube (5)
CAUTION:
Be careful not to damage seal bearing surface when install-
ing.
2. Install spring (3), tighten nut (4).
Be careful that the stud bolt nut does not interfere with the
flanged area ( ).
Make sure the spring (3) sits properly on the flange surface by
aligning it to the locator dimples.
Exhaust Front Tube to Center Muffler
1. Securely insert seal bearing (2) into exhaust front tube (1) side
in the direction shown.
Center muffler (5)
CAUTION:
Be careful not to damage seal bearing surface when install-
ing.
2. With spring (3), tighten bolt (4).
Be careful that the stud bolt does not interfere with the flanged
area ( ).
Make sure the spring (3) sits properly on the flange surface by
aligning it to the locator dimples.
InspectionINFOID:0000000001700348
INSPECTION AFTER INSTALLATION
With the engine running, check exhaust tube joints for exhaust leakage and unusual noise.
Check to ensure that brackets and mounting rubbers are installed properly and free from undue stress.
Improper installation could result in excessive noise and vibration.
PBIC3797E
PBIC3798E