Page 2849 of 4264

ENGINE DRIVEABILITY AND EMISSIONS 6E–273
7. Install fuel rail assembly. Tighten the nuts to 19 N·m
(1.9 kgf·m). Refer to Fuel Rail Installation
Procedure.
Tighten the flare nut to 27 - 33 N·m (2.8 - 3.4 kgf·m).
8. Connect the negative battery cable.FUEL PRESSURE REGULATOR
Removal Procedure
Caution: To reduce the risk of fire and personal
injury, it is necessary to relieve the fuel system
pressure before servicing the fuel system
components.
Caution: After relieving the fuel system pressure, a
small amount of fuel may be released when
servicing fuel lines or connections. Reduce the
chance of personal injury by covering the fuel line
fitting with a shop towel before disconnecting the
fittings. The towel will absorb any fuel that may leak
out. When the disconnect is completed, place the
towel in an approved container.
NOTE: Compressed air must never be used to test or
clean a fuel pressure regulator, as damage to the fuel
pressure regulator may occur.
NOTE: To prevent damage to the fuel pressure
regulator, do not immerse the pressure regulator in
solvent.
Removal Procedure
1. Depressurize the fuel system. Refer to Fuel
Pressure Relief Procedure.
2. Disconnect the negative battery cable.
3. Remove the fuel pump relay.
4. Disconnect the vacuum line form fuel pressure
regulator.
Page 2850 of 4264
6E–274 ENGINE DRIVEABILITY AND EMISSIONS
5. Remove the fuel pressure regulator retaining screw.
6. Remove the fuel pressure regulator from fuel rail.
Installation Procedure
1. Insert the fuel pressure regulator into the fuel rail.2. Install the fuel pressure regulator retaining bracket
and tighten with a screw.
3. Connect vacuum line onto the fuel pressure
regulator.
4. Install the fuel pump relay.
5. Connect the negative battery cable.
6. Crank the engine until it starts. Cranking the engine
may take longer than usual due to trapped air in the
fuel line.
7. Tighten the flare nut to 27 - 33 N·m (2.8 - 3.4 kgf·m).
Page 2851 of 4264
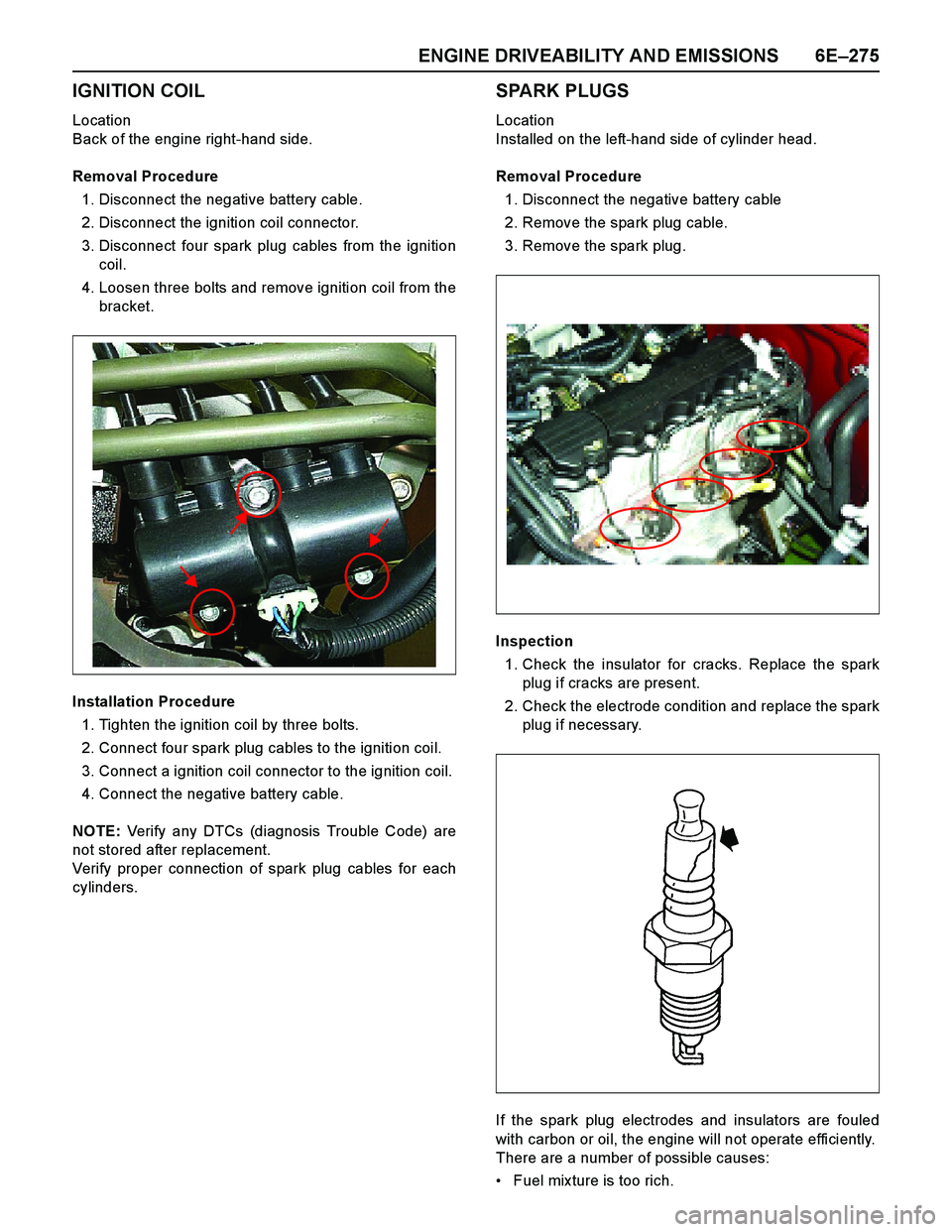
ENGINE DRIVEABILITY AND EMISSIONS 6E–275
IGNITION COIL
Location
Back of the engine right-hand side.
Removal Procedure
1. Disconnect the negative battery cable.
2. Disconnect the ignition coil connector.
3. Disconnect four spark plug cables from the ignition
coil.
4. Loosen three bolts and remove ignition coil from the
bracket.
Installation Procedure
1. Tighten the ignition coil by three bolts.
2. Connect four spark plug cables to the ignition coil.
3. Connect a ignition coil connector to the ignition coil.
4. Connect the negative battery cable.
NOTE: Verify any DTCs (diagnosis Trouble Code) are
not stored after replacement.
Verify proper connection of spark plug cables for each
cylinders.
SPARK PLUGS
Location
Installed on the left-hand side of cylinder head.
Removal Procedure
1. Disconnect the negative battery cable
2. Remove the spark plug cable.
3. Remove the spark plug.
Inspection
1. Check the insulator for cracks. Replace the spark
plug if cracks are present.
2. Check the electrode condition and replace the spark
plug if necessary.
If the spark plug electrodes and insulators are fouled
with carbon or oil, the engine will not operate efficiently.
There are a number of possible causes:
Fuel mix ture is too rich.
Page 2852 of 4264
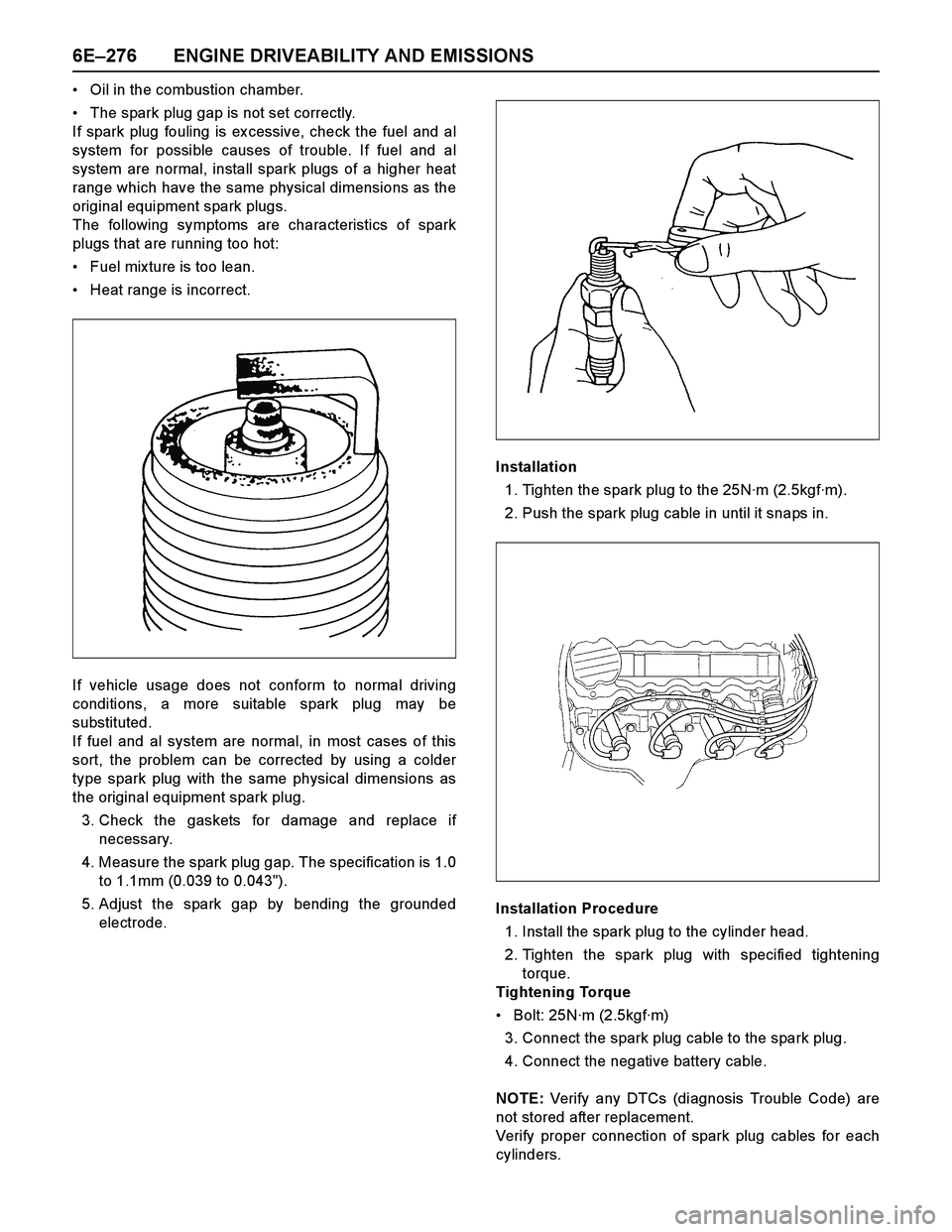
6E–276 ENGINE DRIVEABILITY AND EMISSIONS
Oil in the combustion chamber.
The spark plug gap is not set correctly.
If spark plug fouling is ex cessive, check the fuel and al
system for possible causes of trouble. If fuel and al
system are normal, install spark plugs of a higher heat
range which have the same physical dimensions as the
original equipment spark plugs.
The following symptoms are characteristics of spark
plugs that are running too hot:
Fuel mixture is too lean.
Heat range is incorrect.
If vehicle usage does not conform to normal driving
conditions, a more suitable spark plug may be
substituted.
If fuel and al system are normal, in most cases of this
sort, the problem can be corrected by using a colder
type spark plug with the same physical dimensions as
the original equipment spark plug.
3. Check the gaskets for damage and replace if
necessary.
4. Measure the spark plug gap. The specification is 1.0
to 1.1mm (0.039 to 0.043").
5. Adjust the spark gap by bending the grounded
electrode.Installation
1. Tighten the spark plug to the 25N·m (2.5kgf·m).
2. Push the spark plug cable in until it snaps in.
Installation Procedure
1. Install the spark plug to the cylinder head.
2. Tighten the spark plug with specified tightening
torque.
Tightening Torque
Bolt: 25N·m (2.5kgf·m)
3. Connect the spark plug cable to the spark plug.
4. Connect the negative battery cable.
NOTE: Verify any DTCs (diagnosis Trouble Code) are
not stored after replacement.
Verify proper connection of spark plug cables for each
cylinders.
Page 2853 of 4264
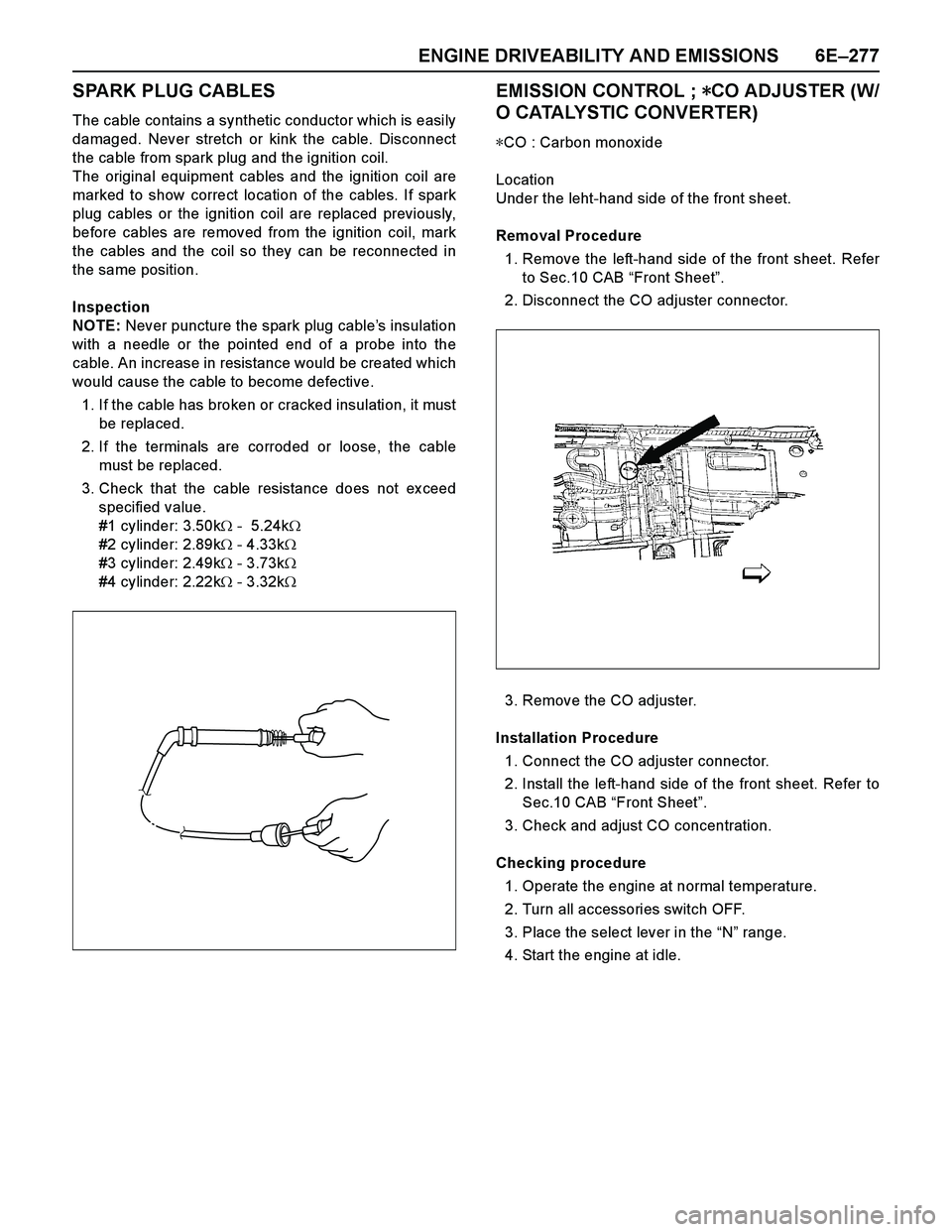
ENGINE DRIVEABILITY AND EMISSIONS 6E–277
SPARK PLUG CABLES
The cable contains a synthetic conductor which is easily
damaged. Never stretch or kink the cable. Disconnect
the cable from spark plug and the ignition coil.
The original equipment cables and the ignition coil are
marked to show correct location of the cables. If spark
plug cables or the ignition coil are replaced previously,
before cables are removed from the ignition coil, mark
the cables and the coil so they can be reconnected in
the same position.
Inspection
NOTE: Never puncture the spark plug cable’s insulation
with a needle or the pointed end of a probe into the
cable. An increase in resistance would be created which
would cause the cable to become defective.
1. If the cable has broken or cracked insulation, it must
be replaced.
2. If the terminals are corroded or loose, the cable
must be replaced.
3. Check that the cable resistance does not ex ceed
specified value.
#1 cylinder: 3.50k - 5.24k
#2 cylinder: 2.89k - 4.33k
#3 cylinder: 2.49k - 3.73k
#4 cylinder: 2.22k - 3.32k
EMISSION CONTROL ;
CO ADJUSTER (W/
O CATALYSTIC CONVERTER)
CO : Carbon monox ide
Location
Under the leht-hand side of the front sheet.
Removal Procedure
1. Remove the left-hand side of the front sheet. Refer
to Sec.10 CAB “Front Sheet”.
2. Disconnect the CO adjuster connector.
3. Remove the CO adjuster.
Installation Procedure
1. Connect the CO adjuster connector.
2. Install the left-hand side of the front sheet. Refer to
Sec.10 CAB “Front Sheet”.
3. Check and adjust CO concentration.
Checking procedure
1. Operate the engine at normal temperature.
2. Turn all accessories switch OFF.
3. Place the select lever in the “N” range.
4. Start the engine at idle.
Page 2854 of 4264
6E–278 ENGINE DRIVEABILITY AND EMISSIONS
5. Measure the CO concentration for 1-3 minutes, after
idlling the engine to allow the CO concentration to
stabilize.
6. Check the CO concentration.
7. If the value is not within specification, adjust the CO
concentration.A djustment Procedure
1. Warm-up the engine.
2. Turn OFF switches of all electrical equipment.
3. Open the CO adjuster cap.
4. Turn the CO adjuster screw checking the CO
concentration
.
5. Adjust the CO concentration within specification.
Specification:
CO concentration : 0.6 1.0 %
NOTE: Apply the liquid gasket to the CO adjuster screw
after the adjustment.
Page 2855 of 4264
ENGINE DRIVEABILITY AND EMISSIONS 6E–279
SPECIAL SERVICE TOOLS
ILLUSTRATION TOOL NO.
TOLL NAME
5-8840-0285-0
(J 39200)
High Impedance
Multimeter
(Digital Voltmeter -DVM)
(1) PCMCIA Card
(2) RS232 Loop Back
Connector
(3) SAE 16/19 Adapter
(4) DLC Cable
(5) TECH 2
5-8840-0385-0
(J 35616-A /BT-8637)
Connector Test Adapter Kit
5-8840-0378-0
(J34730-E)
Port Fuel Injection
Diagnostic Kit
Breaker Box
5-8840-2589-0
Injector Adapter Cable
Page 2856 of 4264