Page 249 of 4264
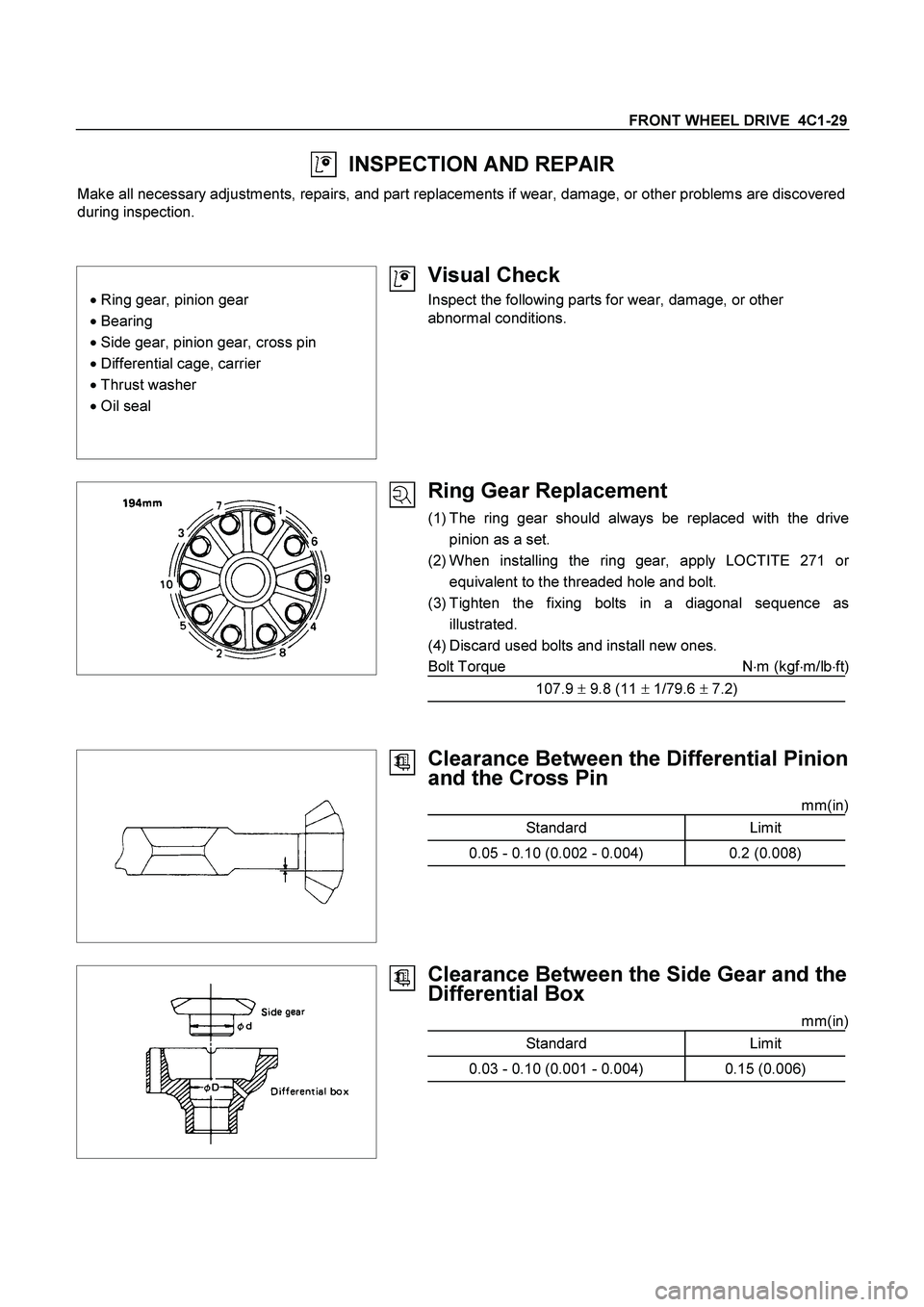
FRONT WHEEL DRIVE 4C1-29
INSPECTION AND REPAIR
Make all necessary adjustments, repairs, and part replacements if wear, damage, or other problems are discovered
during inspection.
Ring gear, pinion gear
Bearing
Side gear, pinion gear, cross pin
Differential cage, carrier
Thrust washer
Oil seal
Visual Check
Inspect the following parts for wear, damage, or other
abnormal conditions.
Ring Gear Replacement
(1) The ring gear should always be replaced with the drive
pinion as a set.
(2) When installing the ring gear, apply LOCTITE 271 o
r
equivalent to the threaded hole and bolt.
(3) Tighten the fixing bolts in a diagonal sequence as
illustrated.
(4) Discard used bolts and install new ones.
Bolt Torque Nm (kgfm/lbft)
107.9 9.8 (11 1/79.6 7.2)
Clearance Between the Differential Pinion
and the Cross Pin
mm(in)
Standard Limit
0.05 - 0.10 (0.002 - 0.004) 0.2 (0.008)
Clearance Between the Side Gear and the
Differential Box
mm(in)
Standard Limit
0.03 - 0.10 (0.001 - 0.004) 0.15 (0.006)
Page 250 of 4264
4C1-30 FRONT WHEEL DRIVE
Play in Splines Between the Side Gear
and the Axle Shaft
mm(in)
Standard Limit
0.07 - 0.36 (0.003 - 0.014) 0.25 (0.010)
Page 251 of 4264
FRONT WHEEL DRIVE 4C1-31
REASSEMBLY
MINOR COMPONENTS
Reassembly Steps
1. Differential cage
2. Thrust washer
3. Side gear
4. Pinion gear
5. Cross pin
6. Lock pin
7. Ring gear
8. Bolt
Important Operations
4. Pinion Gear
Install the pinion gear by engaging it with the side gears while
turning both pinion gears simultaneously in the same direction.
Page 252 of 4264
4C1-32 FRONT WHEEL DRIVE
5. Cross Pin
(1) Be sure to install the cross pin so that it is in alignment with
the lock pin hole in the differential cage.
(2)
Adjust the backlash between the side gear and the pinion
gear.
mm(in)
Backlash 0.10 - 0.20 (0.004 - 0.008)
Thickness of thrust washers available
mm(in)
1.00, 1.05, 1.10 (0.039, 0.041, 0.043)
6. Lock Pin
After lock pin installation, stake the cage to prevent discharge
of the lock pin.
7. Ring Gear
When installing the ring gear, apply LOCTITE 271 or
equivalent to the threaded hole and bolt.
8. Bolt
Tighten the bolts in diagonal sequence as illustrated.
Bolt Torque Nm (kgfm/lbft)
107.9 9.8 (11 1/79.6 7.2)
Note :
Discard used bolts and install new ones.
Note that all bolts have a left hand thread.
Page 253 of 4264
FRONT WHEEL DRIVE 4C1-33
MAJOR COMPONENTS
Reassembly Steps
1. Diff. carrier
2. Outer bearing outer race
3. Inner bearing outer race
4. Adjust shim
5. Inner bearing
6. Collapsible spacer
7. Pinion gear
8. Outer bearing
9. Oil seal
10. Dust cover
11. Flange
12. Flange nut and washer
13. Adjust shim
14. Side bearing
15. Bearing outer race
16. Diff. cage assembly
17. Bearing cap
18. Bolt
19. Axle case
20. Differential assembly
21. Bolt
Page 254 of 4264
4C1-34 FRONT WHEEL DRIVE
Important Operations
2. Outer Bearing Outer Race
Installer : 9-8522-1141-0
(J-24256)
Grip : 5-8840-0007-0
(J-8092)
3. Inner Bearing Outer Race
Installer : 9-8522-1274-0
Grip : 5-8840-0007-0
(J-8092)
4. Adjust Shim
Adjustment of drive pinion mounting distance
(1) Apply gear oil to the inner and outer drive pinion bearing.
Clean the pinion setting gage set.
Then install the gage set together with the inner and oute
r
bearings.
1. Pilot : 5-8840-2085-0
(J-21777-42)
2. Nut and bolt : 5-8840-2089-0
(J-23597-9)
3. Gage plate : 5-8840-2087-0
(J-23597-7)
Page 255 of 4264
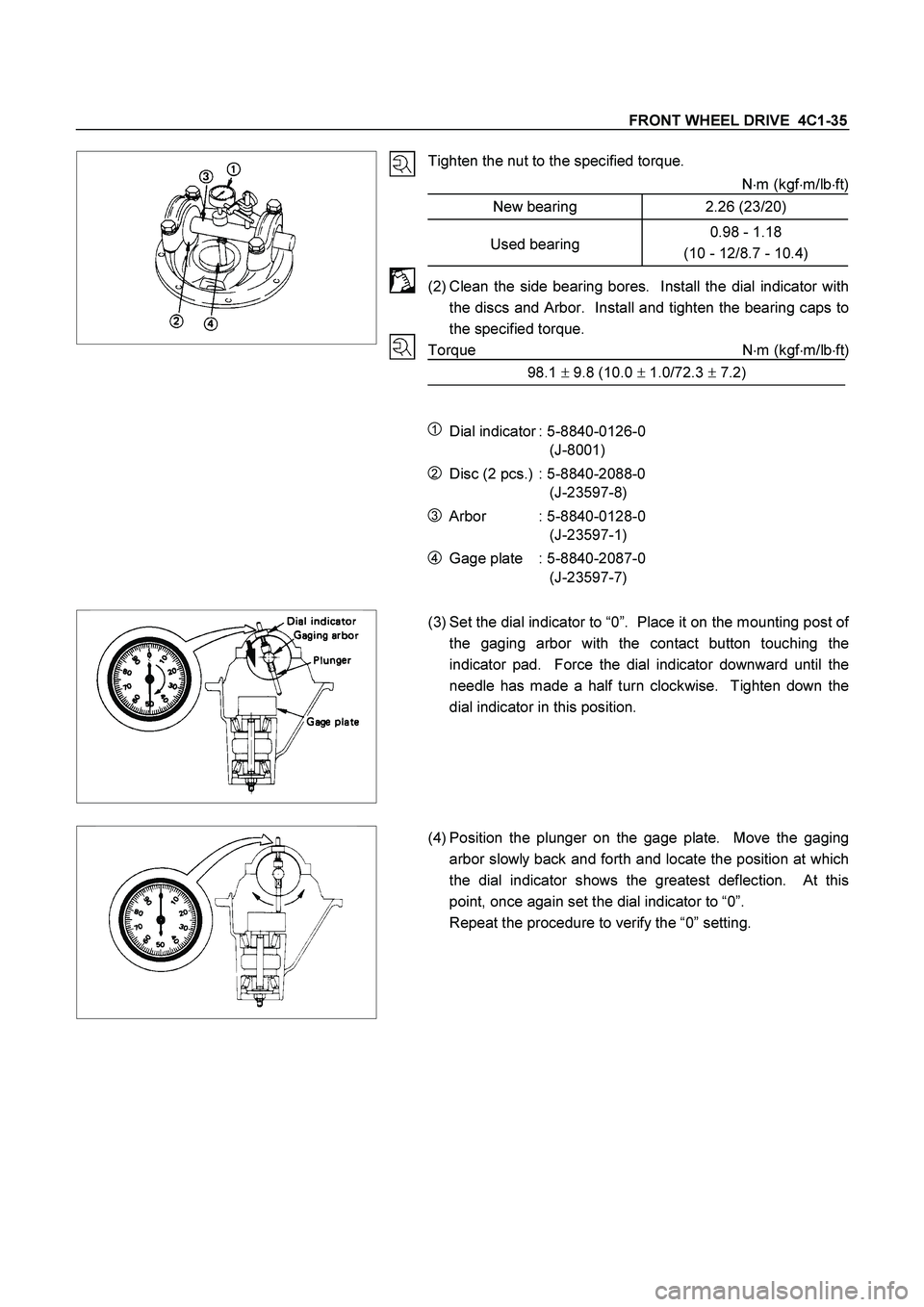
FRONT WHEEL DRIVE 4C1-35
Tighten the nut to the specified torque.
Nm (kgfm/lbft)
New bearing 2.26 (23/20)
Used bearing0.98 - 1.18
(10 - 12/8.7 - 10.4)
(2) Clean the side bearing bores. Install the dial indicator with
the discs and Arbor. Install and tighten the bearing caps to
the specified torque.
Torque N
m (kgf
m/lb
ft)
98.1 9.8 (10.0 1.0/72.3 7.2)
1 Dial indicator : 5-8840-0126-0
(J-8001)
2 Disc (2 pcs.) : 5-8840-2088-0
(J-23597-8)
3 Arbor : 5-8840-0128-0
(J-23597-1)
4 Gage plate : 5-8840-2087-0
(J-23597-7)
(3) Set the dial indicator to “0”. Place it on the mounting post of
the gaging arbor with the contact button touching the
indicator pad. Force the dial indicator downward until the
needle has made a half turn clockwise. Tighten down the
dial indicator in this position.
(4) Position the plunger on the gage plate. Move the gaging
arbor slowly back and forth and locate the position at which
the dial indicator shows the greatest deflection. At this
point, once again set the dial indicator to “0”.
Repeat the procedure to verify the “0” setting.
Page 256 of 4264
4C1-36 FRONT WHEEL DRIVE
(5)
After the ZERO setting is obtained, rotate the gaging arbor
until the dial indicator rod does not touch the gaging plate.
Record the number the dial indicator needle points to.
(6) Record the pinion depth code on the head of the drive
pinion.
The number indicates a necessary change in the pinion
mounting distance. A plus number indicates the need for a
greater mounting distance (which can be achieved b
y
decreasing the shim thickness). A minus number indicates
the need for a smaller mounting distance (which can be
achieved by increasing the shim thickness). If examination
reveals pinion depth code “0”, the pinion is “nominal”.