Page 1297 of 4264
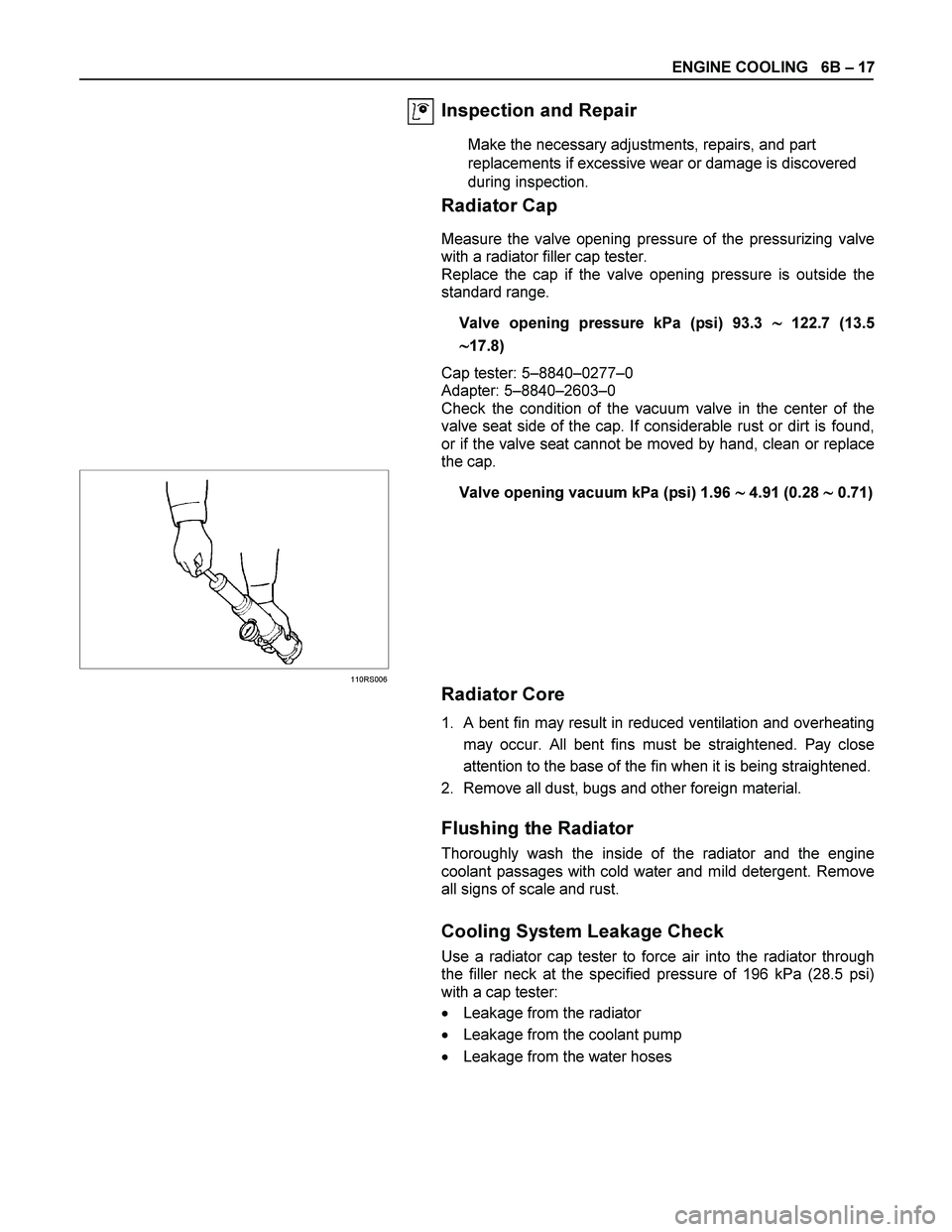
ENGINE COOLING 6B – 17
Inspection and Repair
Make the necessary adjustments, repairs, and part
replacements if excessive wear or damage is discovered
during inspection.
Radiator Cap
Measure the valve opening pressure of the pressurizing valve
with a radiator filler cap tester.
Replace the cap if the valve opening pressure is outside the
standard range.
Valve opening pressure kPa (psi) 93.3
122.7 (13.5
17.8)
Cap tester: 5–8840–0277–0
Adapter: 5–8840–2603–0
Check the condition of the vacuum valve in the center of the
valve seat side of the cap. If considerable rust or dirt is found,
or if the valve seat cannot be moved by hand, clean or replace
the cap.
110RS006
Valve opening vacuum kPa (psi) 1.96
4.91 (0.28
0.71)
Radiator Core
1. A bent fin may result in reduced ventilation and overheating
may occur. All bent fins must be straightened. Pay close
attention to the base of the fin when it is being straightened.
2. Remove all dust, bugs and other foreign material.
Flushing the Radiator
Thoroughly wash the inside of the radiator and the engine
coolant passages with cold water and mild detergent. Remove
all signs of scale and rust.
Cooling System Leakage Check
Use a radiator cap tester to force air into the radiator through
the filler neck at the specified pressure of 196 kPa (28.5 psi)
with a cap tester:
Leakage from the radiator
Leakage from the coolant pump
Leakage from the water hoses
Page 1298 of 4264
6B – 18 ENGINE COOLING
110RS005
Check the rubber hoses for swelling.
Installation
1. Install radiator assembly (9) with hose, taking care not to
damage the radiator core with a fan blade.
2. Support the radiator upper tank with the bracket (5) and
secure the radiator.
3. Connect reserve tank hose (6).
4. Install lower fan guide (3).
5. Connect radiator inlet hose and outlet hose (1) to the
engine.
RTW36BMH000101
6. Connect oil cooler hose to automatic transmission.
7. Connect battery ground cable.
Page 1299 of 4264
ENGINE COOLING 6B – 19
RTW36BSH000101
8. Pour engine coolant up to filler neck of radiator, and up to
MAX mark of reserve tank.
Important operation (in case of 100% engine coolant
change) procedure for filling with engine coolant.
Engine coolant change
Refer to 6B-8 (Draining and Refilling Cooling System).
Page 1300 of 4264
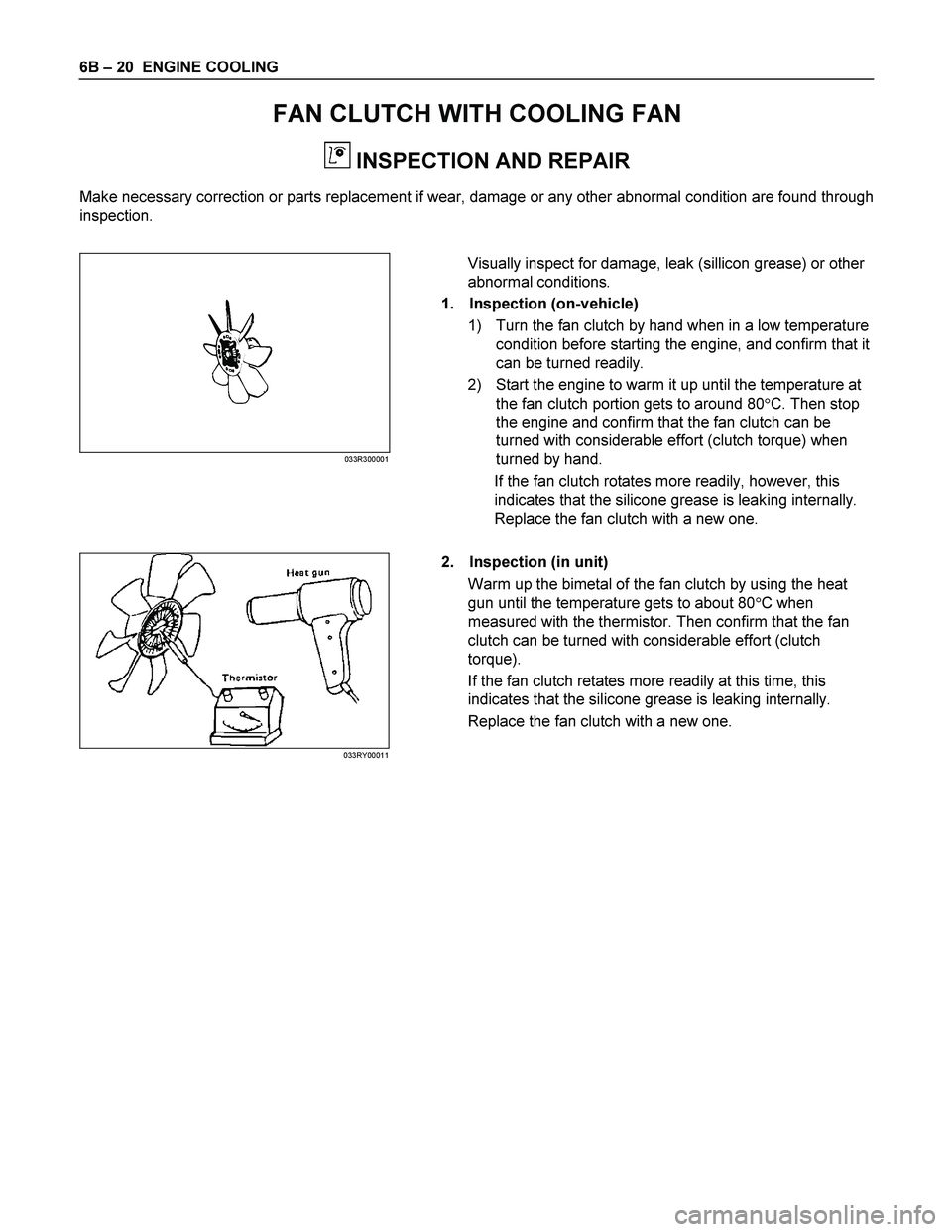
6B – 20 ENGINE COOLING
FAN CLUTCH WITH COOLING FAN
INSPECTION AND REPAIR
Make necessary correction or parts replacement if wear, damage or any other abnormal condition are found through
inspection.
033R300001
Visually inspect for damage, leak (sillicon grease) or other
abnormal conditions.
1. Inspection (on-vehicle)
1) Turn the fan clutch by hand when in a low temperature
condition before starting the engine, and confirm that it
can be turned readily.
2) Start the engine to warm it up until the temperature at
the fan clutch portion gets to around 80C. Then stop
the engine and confirm that the fan clutch can be
turned with considerable effort (clutch torque) when
turned by hand.
If the fan clutch rotates more readily, however, this
indicates that the silicone grease is leaking internally.
Replace the fan clutch with a new one.
033RY00011
2. Inspection (in unit)
Warm up the bimetal of the fan clutch by using the heat
gun until the temperature gets to about 80C when
measured with the thermistor. Then confirm that the fan
clutch can be turned with considerable effort (clutch
torque).
If the fan clutch retates more readily at this time, this
indicates that the silicone grease is leaking internally.
Replace the fan clutch with a new one.
Page 1301 of 4264
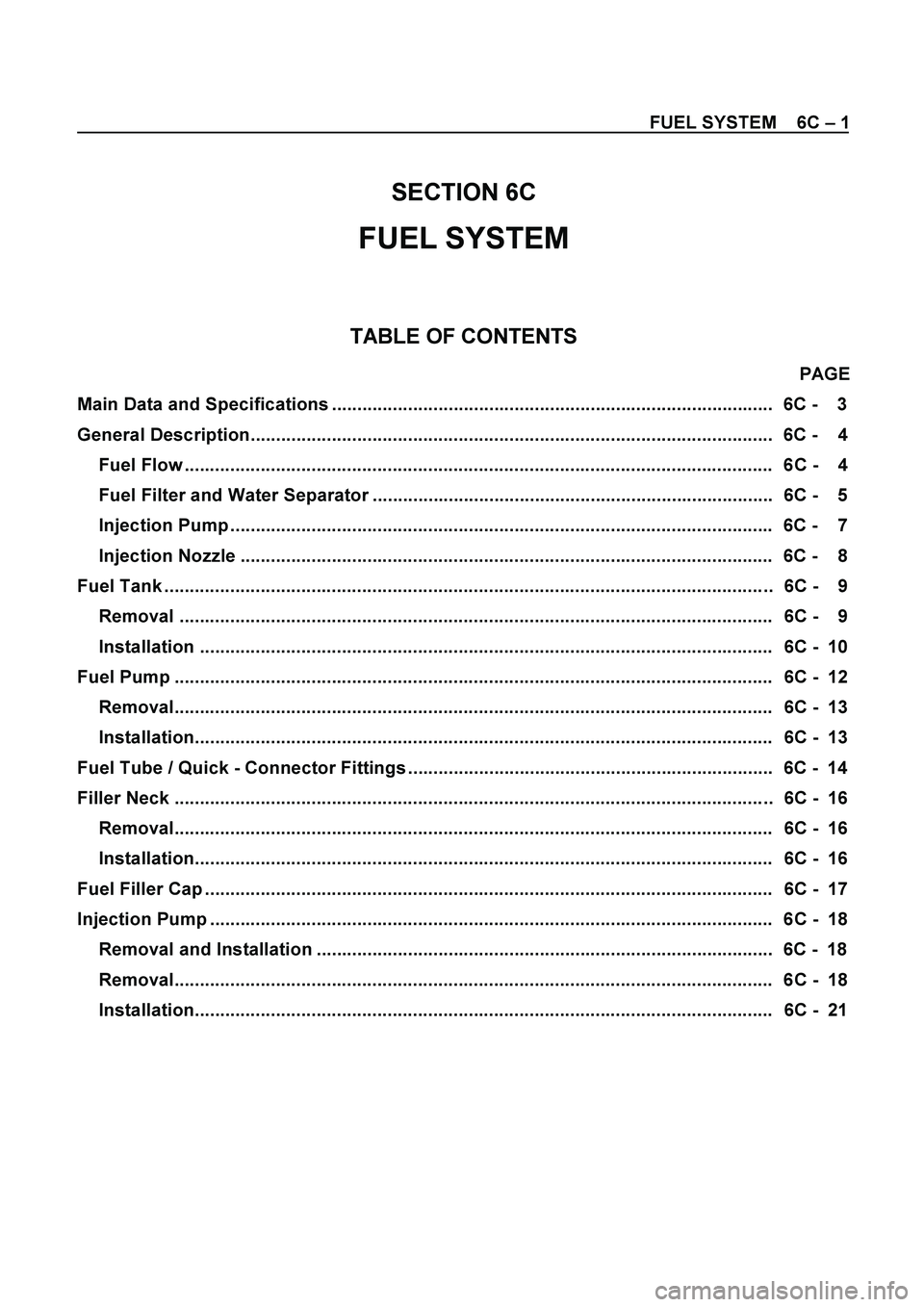
FUEL SYSTEM 6C – 1
SECTION 6C
FUEL SYSTEM
TABLE OF CONTENTS
PAGE
Main Data and Specifications ....................................................................................... 6C - 3
General Description....................................................................................................... 6C - 4
Fuel Flow .................................................................................................................... 6C - 4
Fuel Filter and Water Separator ............................................................................... 6C - 5
Injection Pump ........................................................................................................... 6C - 7
Injection Nozzle ......................................................................................................... 6C - 8
Fuel Tank ........................................................................................................................ 6C - 9
Removal ..................................................................................................................... 6C - 9
Installation ................................................................................................................. 6C - 10
Fuel Pump ...................................................................................................................... 6C - 12
Removal...................................................................................................................... 6C - 13
Installation.................................................................................................................. 6C - 13
Fuel Tube / Quick - Connector Fittings ........................................................................ 6C - 14
Filler Neck ...................................................................................................................... 6C - 16
Removal...................................................................................................................... 6C - 16
Installation.................................................................................................................. 6C - 16
Fuel Filler Cap ................................................................................................................ 6C - 17
Injection Pump ............................................................................................................... 6C - 18
Removal and Installation .......................................................................................... 6C - 18
Removal...................................................................................................................... 6C - 18
Installation.................................................................................................................. 6C - 21
Page 1302 of 4264
6C – 2 FUEL SYSTEM
PAGE
Injection Nozzle.............................................................................................................. 6C - 25
Inspection................................................................................................................... 6C - 25
Special Tools.................................................................................................................. 6C - 36
Page 1303 of 4264
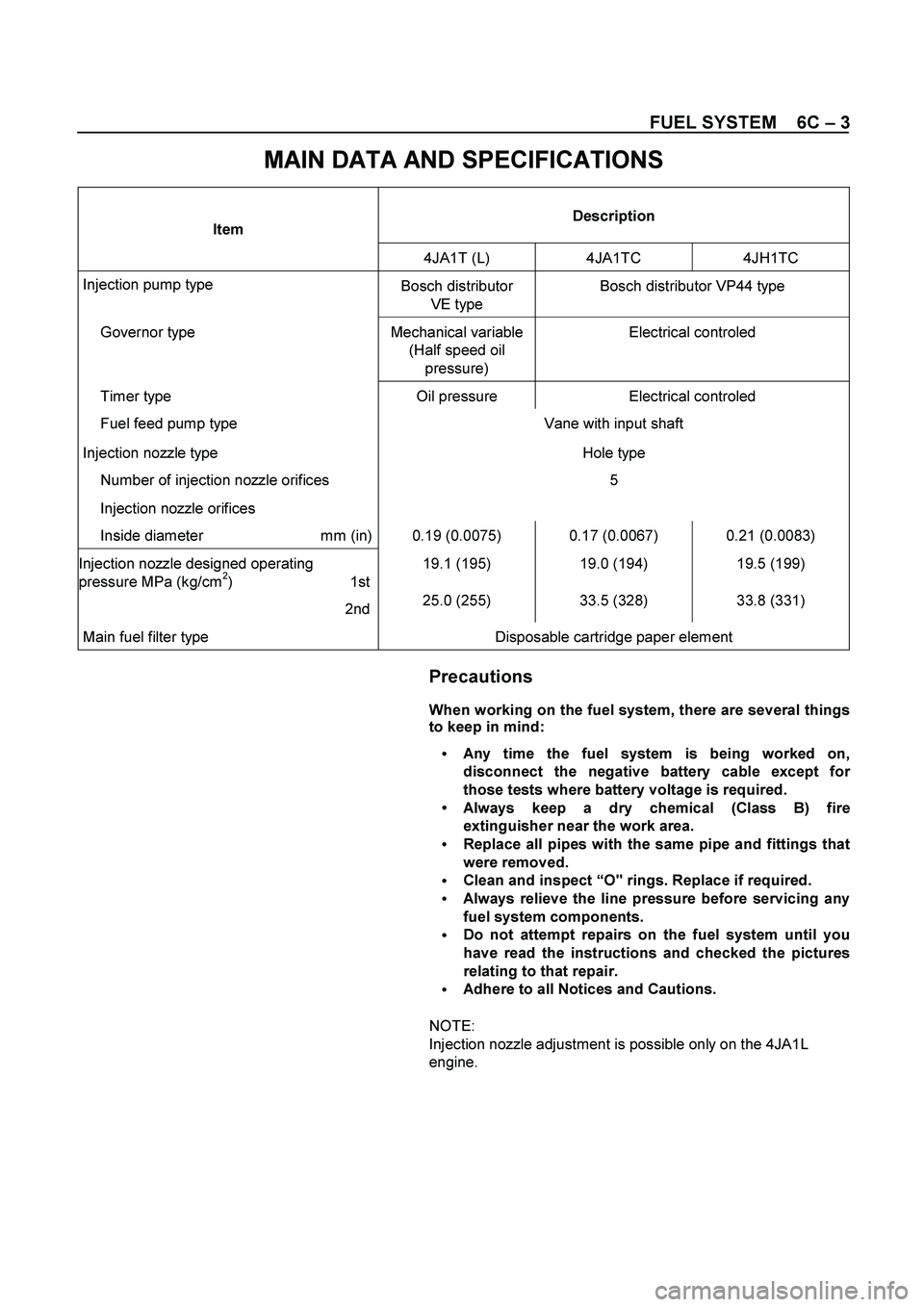
FUEL SYSTEM 6C – 3
MAIN DATA AND SPECIFICATIONS
Description Item
4JA1T (L) 4JA1TC 4JH1TC
Injection pump type
Bosch distributor
VE type Bosch distributor VP44 type
Governor type Mechanical variable
(Half speed oil
pressure) Electrical controled
Timer type Oil pressure Electrical controled
Fuel feed pump type Vane with input shaft
Injection nozzle type Hole type
Number of injection nozzle orifices 5
Injection nozzle orifices
Inside diameter mm (in) 0.19 (0.0075) 0.17 (0.0067) 0.21 (0.0083)
19.1 (195) 19.0 (194) 19.5 (199) Injection nozzle designed operating
pressure MPa (kg/cm2) 1st
2nd 25.0 (255) 33.5 (328) 33.8 (331)
Main fuel filter type Disposable cartridge paper element
Precautions
When working on the fuel system, there are several things
to keep in mind:
Any time the fuel system is being worked on,
disconnect the negative battery cable except fo
r
those tests where battery voltage is required.
Always keep a dry chemical (Class B) fire
extinguisher near the work area.
Replace all pipes with the same pipe and fittings that
were removed.
Clean and inspect “O" rings. Replace if required.
Always relieve the line pressure before servicing any
fuel system components.
Do not attempt repairs on the fuel system until you
have read the instructions and checked the pictures
relating to that repair.
Adhere to all Notices and Cautions.
NOTE:
Injection nozzle adjustment is possible only on the 4JA1L
engine.
Page 1304 of 4264
6C – 4 FUEL SYSTEM
GENERAL DESCRIPTION
FUEL FLOW
RTW46CM F000201
The fuel system consists of the fuel tank, the fuel filter, the water separator, the injection pump, and the injection
nozzle.
The fuel from the fuel tank passes through the water separator and the fuel filter where water particles and other
foreign material are removed from the fuel.
Fuel, fed by the injection pump plunger, is delivered to the injection nozzle in the measured volume at the optimum
timing for efficient engine operation.
NOTE:
1 If it find abnormal condition on the fuel injector, refer to section 6E ENGINE DRIVEABILITY AND
EMISSIONS.
2 Do not contain "Additive for water drain" with fuel.