Page 3841 of 4264
UNIT REPAIR (AW30–40LE) 7A4–33
Install and tighten the two bolts.
Torque: 25 N·m (19lbft)
25 2RY 0 000 4
26. Check end of output shaft.
Using a dial indicator, measure the end play of the
output shaft by hand.
End play: 0.27 – 0.86 mm (0.0106 – 0.0339 in)
24 7RY 0 002 0
27. Install the (flat ring) 4.0 mm (0.157 in) thick flange
with the rounded edge side of the flange facing the
disc.
Alternately install four discs and four plates. (Disc
first)
25 2RY 0 0009
28. Install the (stepped ring) flange with the flat side of
the flange facing the disc.
Install the snap ring.
Snap ring (Reference)
24 6RY 0 0001
Inside diameter 167.9 mm (6.61 in)
Page 3842 of 4264
7A4–34 UNIT REPAIR (AW30–40LE)
29. Check piston stroke of overdrive brake.
Place a dial indicator onto the overdrive brake
piston as shown in the figure.
25 2RY 0 000 3Measure the stroke by applying and releasing the
compressed air (390 – 780 kPa or 57 – 114 psi) as
shown in the figure.
Piston stroke: 1.40 – 1.70 mm (0.0551 – 0.0669 in)
If the values are nonstandard, check for an improper
installation.
Available flange size
24 4RY 0 000 1
Remove the snap ring.
24 6RY 0 0001Remove one flange, four plates and four discs.
24 6RY 0 0026
3.3 mm (0.130 in) 3.8 mm (0.150 in)
3.5 mm (0.138 in) 3.9 mm (0.154 in)
3.6 mm (0.142 in) 4.0 mm (0.158 in)
3.7 mm (0.146 in)
Page 3843 of 4264
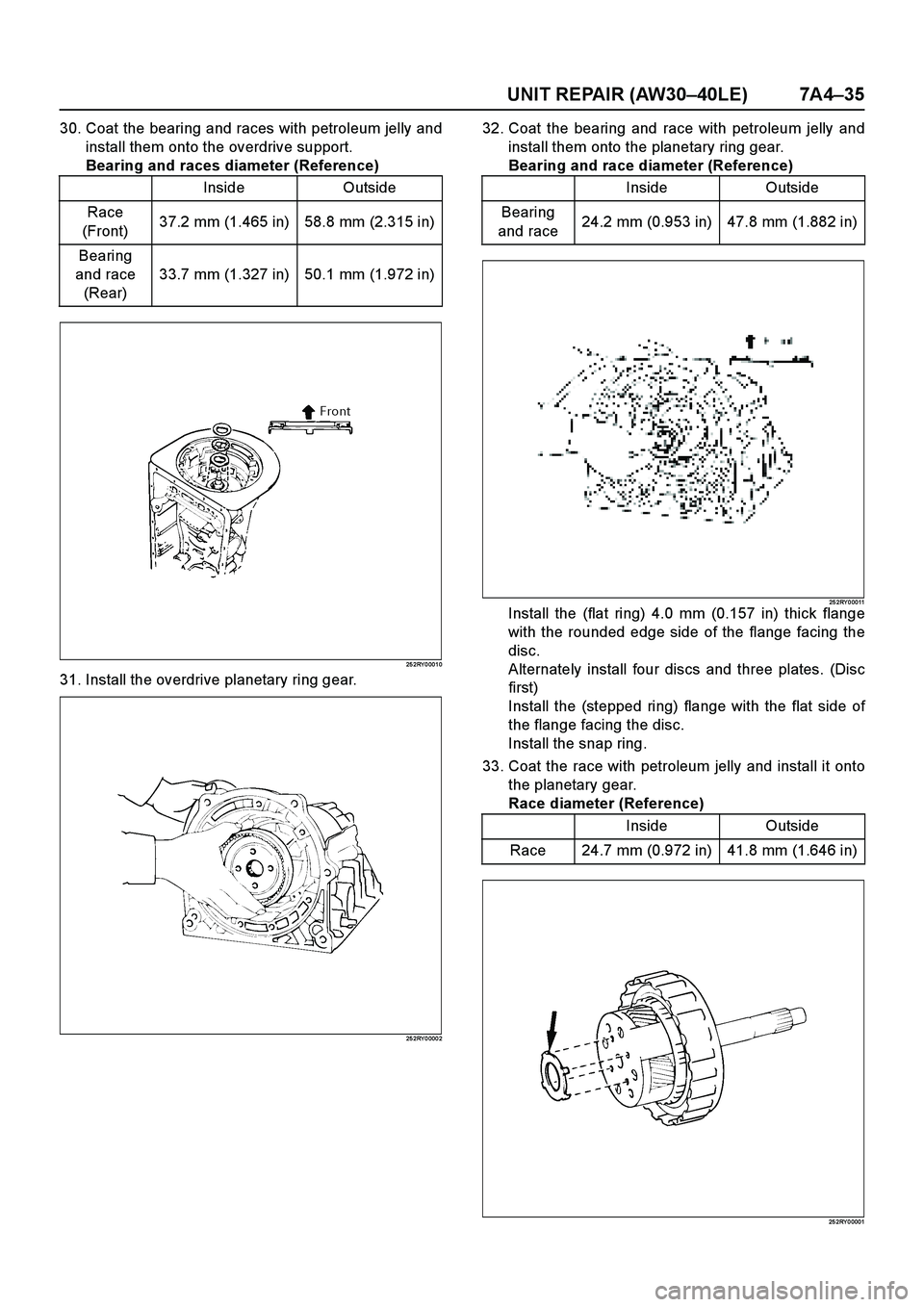
UNIT REPAIR (AW30–40LE) 7A4–35
30. Coat the bearing and races with petroleum jelly and
install them onto the overdrive support.
Bearing and races diameter (Reference)
25 2RY 0 001 0
31. Install the overdrive planetary ring gear.
25 2RY 0 000 2
32. Coat the bearing and race with petroleum jelly and
install them onto the planetary ring gear.
Bearing and race diameter (Reference)
25 2RY 0 0011Install the (flat ring) 4.0 mm (0.157 in) thick flange
with the rounded edge side of the flange facing the
disc.
Alternately install four discs and three plates. (Disc
first)
Install the (stepped ring) flange with the flat side of
the flange facing the disc.
Install the snap ring.
33. Coat the race with petroleum jelly and install it onto
the planetary gear.
Race diameter (Reference)
25 2RY 0 0001
Inside Outside
Race
(Front)37.2 mm (1.465 in) 58.8 mm (2.315 in)
Bearing
and race
(Rear)33.7 mm (1.327 in) 50.1 mm (1.972 in)Inside Outside
Bearing
and race24.2 mm (0.953 in) 47.8 mm (1.882 in)
Inside Outside
Race 24.7 mm (0.972 in) 41.8 mm (1.646 in)
Page 3844 of 4264
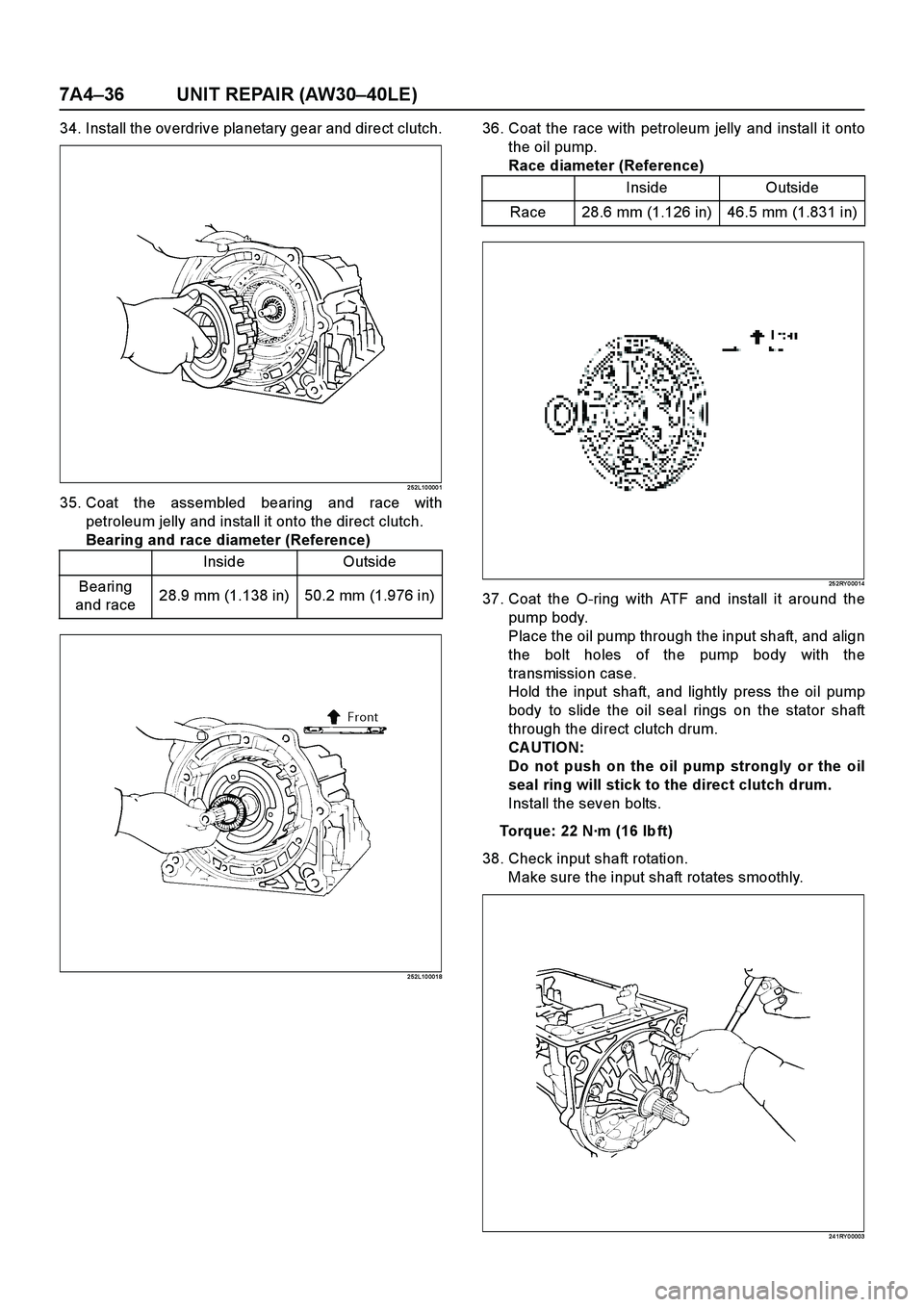
7A4–36 UNIT REPAIR (AW30–40LE)
34. Install the overdrive planetary gear and direct clutch.
2 52L10 000 1
35. Coat the assembled bearing and race with
petroleum jelly and install it onto the direct clutch.
Bearing and race diameter (Reference)
2 52L10 001 8
36. Coat the race with petroleum jelly and install it onto
the oil pump.
Race diameter (Reference)
25 2RY 0 0014
37. Coat the O-ring with ATF and install it around the
pump body.
Place the oil pump through the input shaft, and align
the bolt holes of the pump body with the
transmission case.
Hold the input shaft, and lightly press the oil pump
body to slide the oil seal rings on the stator shaft
through the direct clutch drum.
CA UTION:
Do not push on the oil pump strongly or the oil
seal ring will stick to the direct clutch drum.
Install the seven bolts.
Torque: 22 N·m (16 lb ft)
38. Check input shaft rotation.
Make sure the input shaft rotates smoothly.
24 1RY 0 0003
Inside Outside
Bearing
and race28.9 mm (1.138 in) 50.2 mm (1.976 in)
Inside Outside
Race 28.6 mm (1.126 in) 46.5 mm (1.831 in)
Page 3845 of 4264
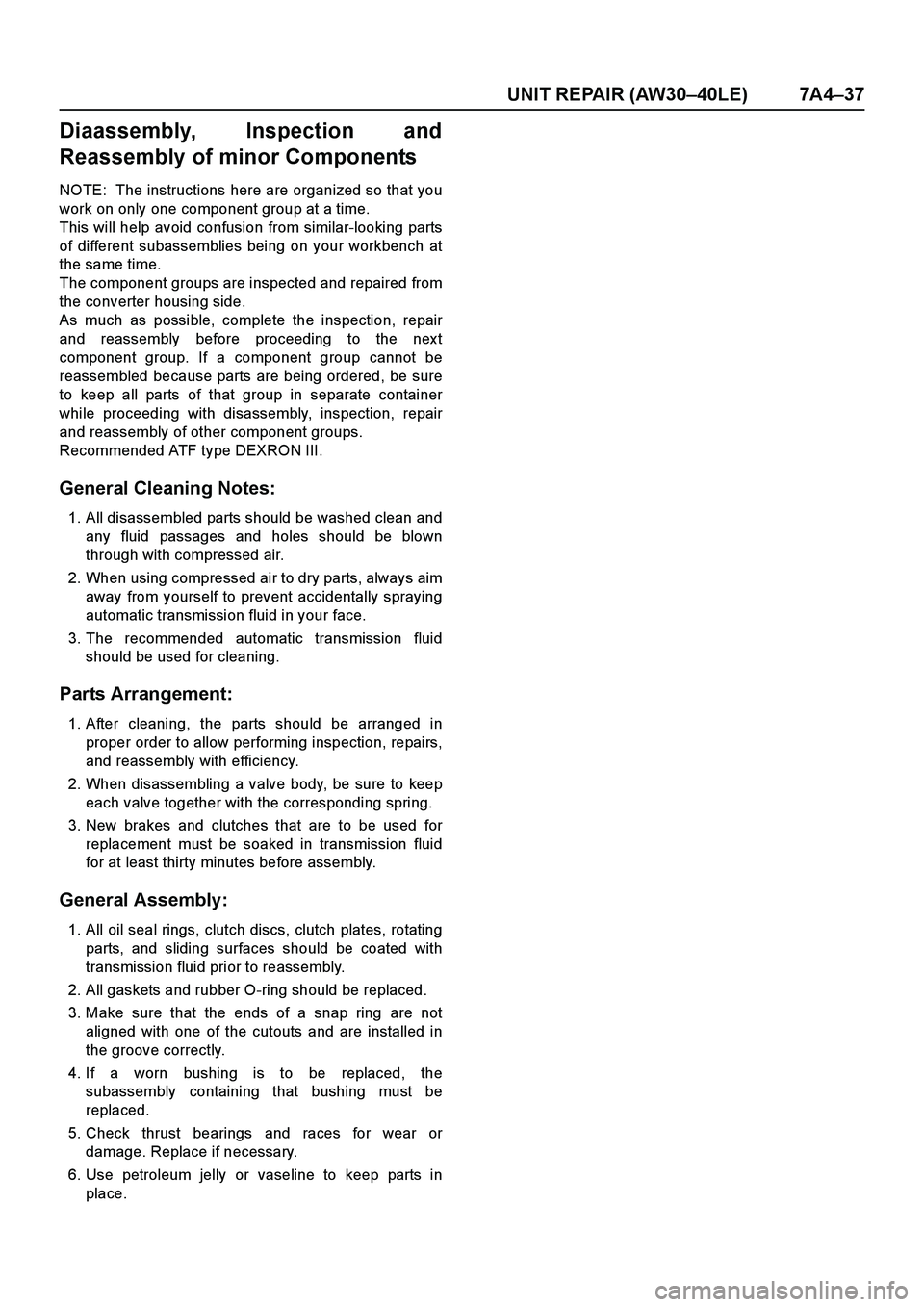
UNIT REPAIR (AW30–40LE) 7A4–37
Diaassembly, Inspection and
Reassembly of minor Components
NOTE: The instructions here are organized so that you
work on only one component group at a time.
This will help avoid confusion from similar-looking parts
of different subassemblies being on your workbench at
the same time.
The component groups are inspected and repaired from
the converter housing side.
As much as possible, complete the inspection, repair
and reassembly before proceeding to the nex t
component group. If a component group cannot be
reassembled because parts are being ordered, be sure
to keep all parts of that group in separate container
while proceeding with disassembly, inspection, repair
and reassembly of other component groups.
Recommended ATF type DEXRON III.
General Cleaning Notes:
1. All disassembled parts should be washed clean and
any fluid passages and holes should be blown
through with compressed air.
2. When using compressed air to dry parts, always aim
away from yourself to prevent accidentally spraying
automatic transmission fluid in your face.
3. The recommended automatic transmission fluid
should be used for cleaning.
Parts Arrangement:
1. After cleaning, the parts should be arranged in
proper order to allow performing inspection, repairs,
and reassembly with efficiency.
2. When disassembling a valve body, be sure to keep
each valve together with the corresponding spring.
3. New brakes and clutches that are to be used for
replacement must be soaked in transmission fluid
for at least thirty minutes before assembly.
General Assembly:
1. All oil seal rings, clutch discs, clutch plates, rotating
parts, and sliding surfaces should be coated with
transmission fluid prior to reassembly.
2. All gaskets and rubber O-ring should be replaced.
3. Make sure that the ends of a snap ring are not
aligned with one of the cutouts and are installed in
the groove correctly.
4. If a worn bushing is to be replaced, the
subassembly containing that bushing must be
replaced.
5. Check thrust bearings and races for wear or
damage. Replace if necessary.
6. Use petroleum jelly or vaseline to keep parts in
place.
Page 3846 of 4264
7A4–38 UNIT REPAIR (AW30–40LE)
Oil Pump
Disassembly View
2 41R20 0003
E nd O FCallo ut
Disassembly
1. Use torque converter as work stand.
Remove 2 oil seal rings from stator shaft.
24 1RY 0 0005
Legend
(1) Oil seal ring
(2) O-ring
(3) Stator shaft(4) Oil pump drive gear
(5) Oil pump driven gear
(6) Oil pump body
Page 3847 of 4264
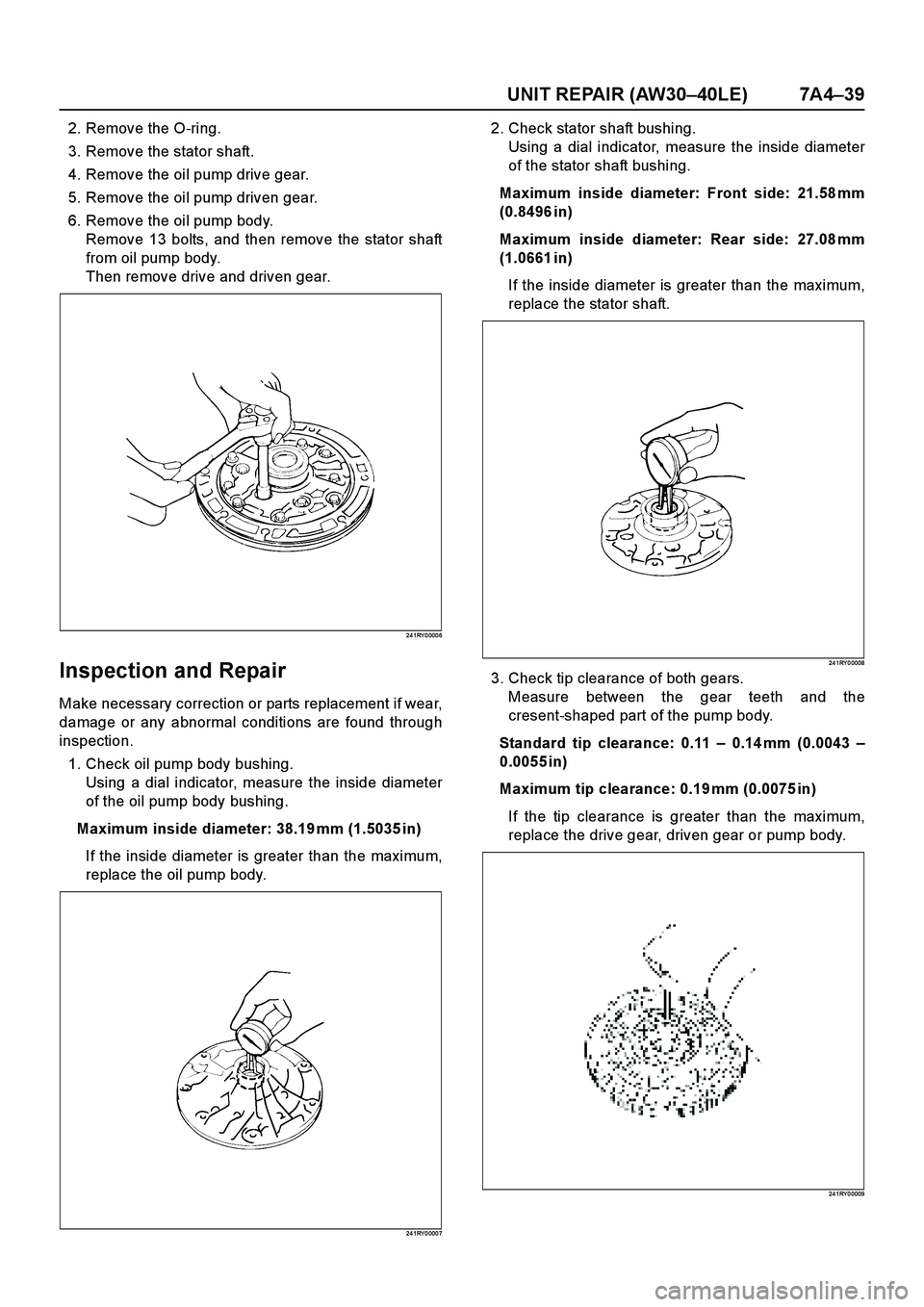
UNIT REPAIR (AW30–40LE) 7A4–39
2. Remove the O-ring.
3. Remove the stator shaft.
4. Remove the oil pump drive gear.
5. Remove the oil pump driven gear.
6. Remove the oil pump body.
Remove 13 bolts, and then remove the stator shaft
from oil pump body.
Then remove drive and driven gear.
24 1RY 0 000 6
Inspection and Repair
Make necessary correction or parts replacement if wear,
damage or any abnormal conditions are found through
inspection.
1. Check oil pump body bushing.
Using a dial indicator, measure the inside diameter
of the oil pump body bushing.
Maximum inside diameter: 38.19 mm (1.5035 in)
If the inside diameter is greater than the maximum,
replace the oil pump body.
24 1RY 0 000 7
2. Check stator shaft bushing.
Using a dial indicator, measure the inside diameter
of the stator shaft bushing.
Maximum inside diameter: Front side: 21.58 mm
(0.8496 in)
Maximum inside diameter: Rear side: 27.08 mm
(1.0661 in)
If the inside diameter is greater than the maximum,
replace the stator shaft.
24 1RY 0 0008
3. Check tip clearance of both gears.
Measure between the gear teeth and the
cresent-shaped part of the pump body.
Standard tip clearance: 0.11 – 0.14 mm (0.0043 –
0.0055 in)
Maximum tip clearance: 0.19 mm (0.0075 in)
If the tip clearance is greater than the maximum,
replace the drive gear, driven gear or pump body.
24 1RY 0 0009
Page 3848 of 4264
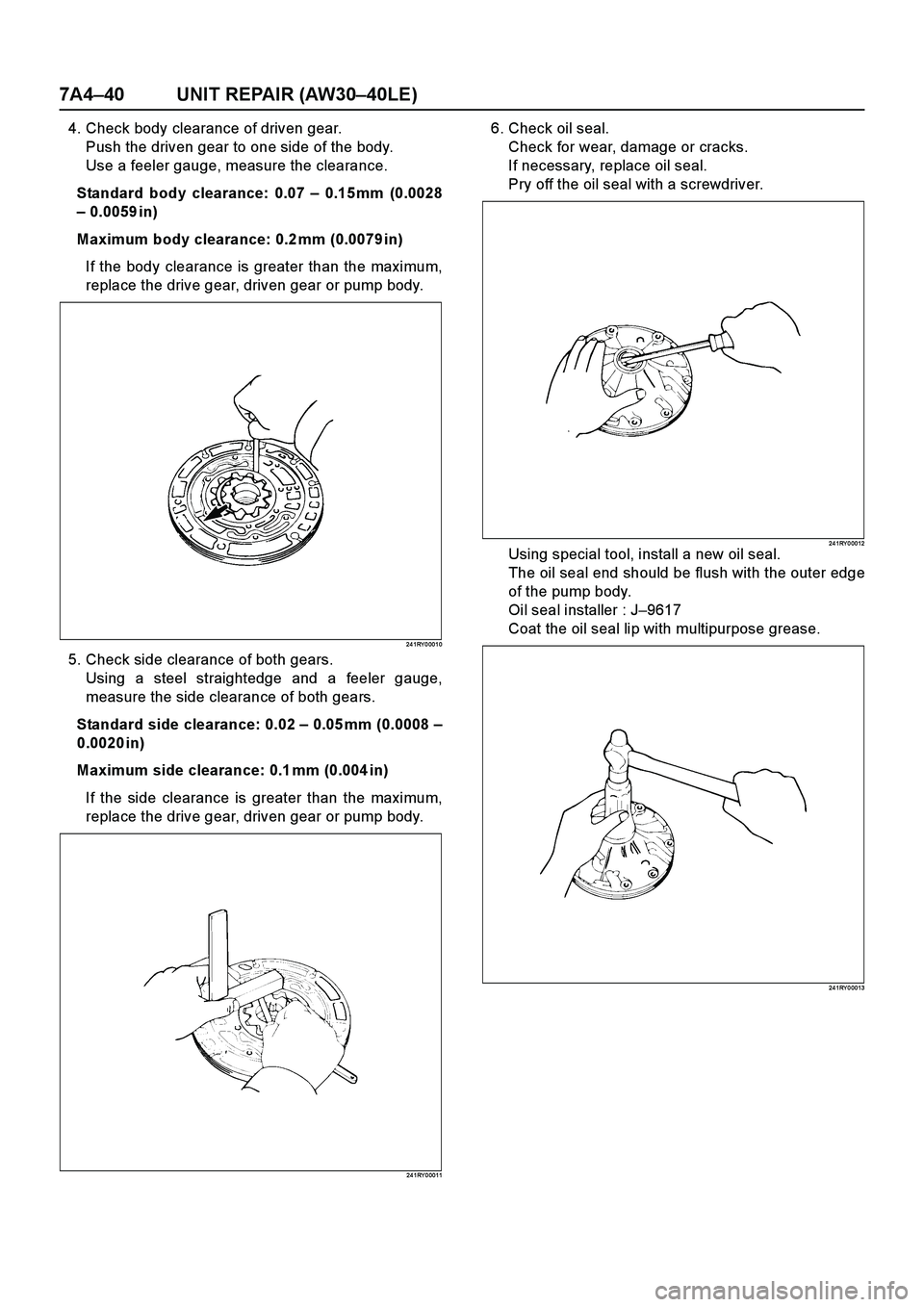
7A4–40 UNIT REPAIR (AW30–40LE)
4. Check body clearance of driven gear.
Push the driven gear to one side of the body.
Use a feeler gauge, measure the clearance.
Standard body clearance: 0.07 – 0.15 mm (0.0028
– 0.0059 in)
Maximum body clearance: 0.2 mm (0.0079 in)
If the body clearance is greater than the maximum,
replace the drive gear, driven gear or pump body.
24 1RY 0 001 0
5. Check side clearance of both gears.
Using a steel straightedge and a feeler gauge,
measure the side clearance of both gears.
Standard side clearance: 0.02 – 0.05 mm (0.0008 –
0.0020 in)
Maximum side clearance: 0.1 mm (0.004 in)
If the side clearance is greater than the maximum,
replace the drive gear, driven gear or pump body.
24 1RY 0 0011
6. Check oil seal.
Check for wear, damage or cracks.
If necessary, replace oil seal.
Pry off the oil seal with a screwdriver.
24 1RY 0 0012Using special tool, install a new oil seal.
The oil seal end should be flush with the outer edge
of the pump body.
Oil seal installer : J–9617
Coat the oil seal lip with multipurpose grease.
24 1RY 0 0013