Page 2089 of 4264
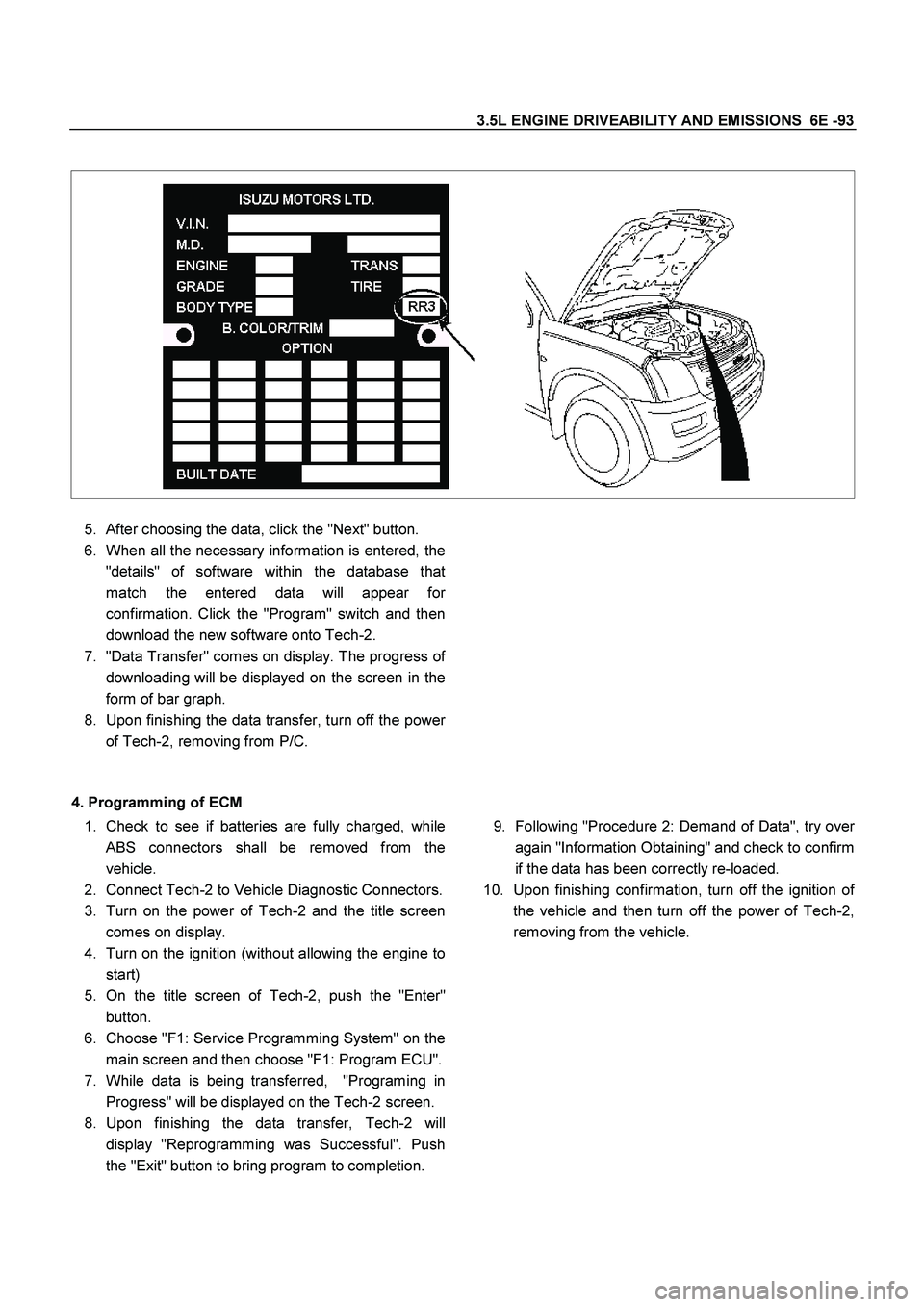
3.5L ENGINE DRIVEABILITY AND EMISSIONS 6E -93
5.
After choosing the data, click the "Next" button.
6.
When all the necessary information is entered, the
"details" of software within the database that
match the entered data will appear fo
r
confirmation. Click the "Program" switch and then
download the new software onto Tech-2.
7. "Data Transfer" comes on display. The progress o
f
downloading will be displayed on the screen in the
form of bar graph.
8.
Upon finishing the data transfer, turn off the powe
r
of Tech-2, removing from P/C.
4. Programming of ECM
1.
Check to see if batteries are fully charged, while
ABS connectors shall be removed from the
vehicle.
2.
Connect Tech-2 to Vehicle Diagnostic Connectors.
3.
Turn on the power of Tech-2 and the title screen
comes on display.
4.
Turn on the ignition (without allowing the engine to
start)
5.
On the title screen of Tech-2, push the "Enter"
button.
6.
Choose "F1: Service Programming System" on the
main screen and then choose "F1: Program ECU".
7.
While data is being transferred, "Programing in
Progress" will be displayed on the Tech-2 screen.
8.
Upon finishing the data transfer, Tech-2 will
display "Reprogramming was Successful". Push
the "Exit" button to bring program to completion.
9.
Following "Procedure 2: Demand of Data", try ove
r
again "Information Obtaining" and check to confirm
if the data has been correctly re-loaded.
10. Upon finishing confirmation, turn off the ignition o
f
the vehicle and then turn off the power of Tech-2,
removing from the vehicle.
Page 2090 of 4264
6E-94 3.5L ENGINE DRIVEABILITY AND EMISSIONS
HOW TO USE BREAKER BOX
3
2 1
Legend
(1)
Engine Control Module (ECM)
(2)
Harness Adapter
(3)
Breaker Box
The engine control module (ECM) and other connectors
have water proof connector and special terminal. Wate
r
proof terminal does not allow to use back prove. In
addition, the ECM special terminal can not let regula
r
digital voltage meter prove to access, because terminal
shape is very fin pin type.
In order to prevent damage of female terminal and
connector itself, the breaker box and adapter is the
most suitable special tool.
Page 2091 of 4264
3.5L ENGINE DRIVEABILITY AND EMISSIONS 6E -95
Breaker Box Connection Type A
1
5 2
3
4
Legend
(1)
Engine Control Module (ECM) (Under the harness
adaptoer)
(2)
Harness Adapter
(3)
Breaker Box
(4)
Digital Voltage Meter
(5)
ECM - Harness Adapter Disconnection
Breaker box connection type A, check for "open circuit"
and "short to ground circuit".
Page 2092 of 4264
6E-96 3.5L ENGINE DRIVEABILITY AND EMISSIONS
Breaker Box Connection Type B
2
5 1
4 3
Legend
(1)
Engine Control Module (ECM) (Under the harness
adapter)
(2)
Harness Adapter
(3)
Breaker Box
(4)
Digital Voltage Meter
(5)
ECM - Harness Adapter Connection
Breaker box connection type B, check for "short to
power supply circuit" and "power, signal voltage check"
between the engine control module (ECM) and
electrical components.
Page 2093 of 4264
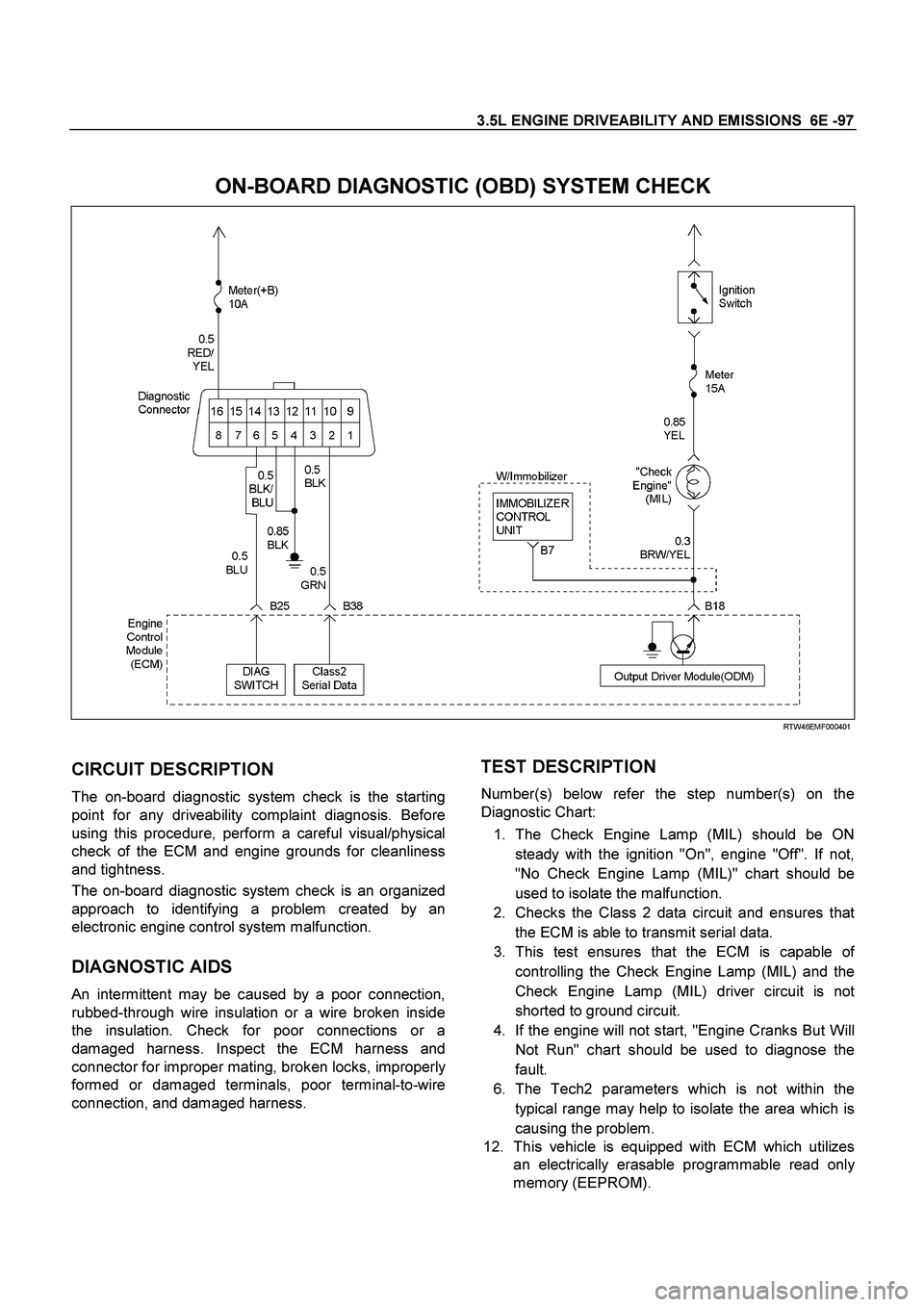
3.5L ENGINE DRIVEABILITY AND EMISSIONS 6E -97
ON-BOARD DIAGNOSTIC (OBD) SYSTEM CHECK
RTW46EM F000401
CIRCUIT DESCRIPTION
The on-board diagnostic system check is the starting
point for any driveability complaint diagnosis. Before
using this procedure, perform a careful visual/physical
check of the ECM and engine grounds for cleanliness
and tightness.
The on-board diagnostic system check is an organized
approach to identifying a problem created by an
electronic engine control system malfunction.
DIAGNOSTIC AIDS
An intermittent may be caused by a poor connection,
rubbed-through wire insulation or a wire broken inside
the insulation. Check for poor connections or a
damaged harness. Inspect the ECM harness and
connector for improper mating, broken locks, improperl
y
formed or damaged terminals, poor terminal-to-wire
connection, and damaged harness.
TEST DESCRIPTION
Number(s) below refer the step number(s) on the
Diagnostic Chart:
1. The Check Engine Lamp (MIL) should be ON
steady with the ignition "On", engine "Off". If not,
"No Check Engine Lamp (MIL)" chart should be
used to isolate the malfunction.
2. Checks the Class 2 data circuit and ensures that
the ECM is able to transmit serial data.
3. This test ensures that the ECM is capable o
f
controlling the Check Engine Lamp (MIL) and the
Check Engine Lamp (MIL) driver circuit is not
shorted to ground circuit.
4. If the engine will not start, "Engine Cranks But Will
Not Run" chart should be used to diagnose the
fault.
6. The Tech2 parameters which is not within the
typical range may help to isolate the area which is
causing the problem.
12. This vehicle is equipped with ECM which utilizes
an electrically erasable programmable read onl
y
memory (EEPROM).
Page 2094 of 4264
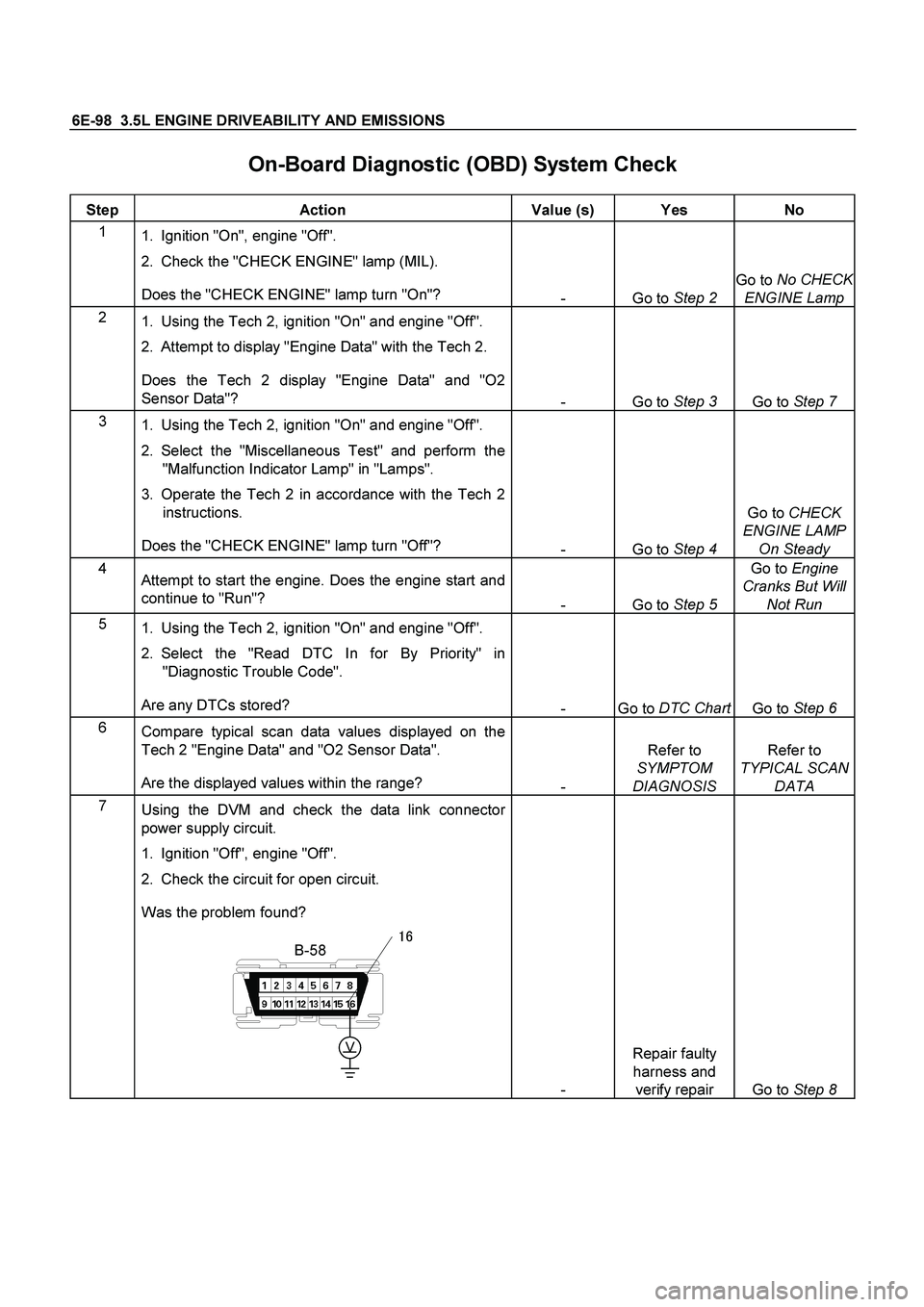
6E-98 3.5L ENGINE DRIVEABILITY AND EMISSIONS
On-Board Diagnostic (OBD) System Check
Step Action Value (s) Yes No
1
1. Ignition "On", engine "Off".
2. Check the "CHECK ENGINE" lamp (MIL).
Does the "CHECK ENGINE" lamp turn "On"?
- Go to Step 2
Go to No CHECK
ENGINE Lamp
2
1. Using the Tech 2, ignition "On" and engine "Off".
2. Attempt to display "Engine Data" with the Tech 2.
Does the Tech 2 display "Engine Data" and "O2
Sensor Data"?
- Go to Step 3
Go to Step 7
3
1. Using the Tech 2, ignition "On" and engine "Off".
2. Select the "Miscellaneous Test" and perform the
"Malfunction Indicator Lamp" in "Lamps".
3. Operate the Tech 2 in accordance with the Tech 2
instructions.
Does the "CHECK ENGINE" lamp turn "Off"?
- Go to Step 4
Go to CHECK
ENGINE LAMP
On Steady
4
Attempt to start the engine. Does the engine start and
continue to "Run"?
- Go to Step 5
Go to Engine
Cranks But Will
Not Run
5
1. Using the Tech 2, ignition "On" and engine "Off".
2. Select the "Read DTC In for By Priority" in
"Diagnostic Trouble Code".
Are any DTCs stored?
- Go to DTC Chart
Go to Step 6
6
Compare typical scan data values displayed on the
Tech 2 "Engine Data" and "O2 Sensor Data".
Are the displayed values within the range?
- Refer to
SYMPTOM
DIAGNOSIS Refer to
TYPICAL SCAN
DATA
7
Using the DVM and check the data link connector
power supply circuit.
1. Ignition "Off", engine "Off".
2. Check the circuit for open circuit.
Was the problem found?
V
B-58
-
Repair faulty
harness and
verify repair
Go to Step 8
Page 2095 of 4264
3.5L ENGINE DRIVEABILITY AND EMISSIONS 6E -99
Step Action Value (s) Yes No
8
Using the DVM and check the data link connector
ground circuit.
1. Ignition "Off", engine "Off".
2. Check the circuit for open circuit.
Was the problem found?
B-58
-
Repair faulty
harness and
verify repair
Go to Step 9
9
Using the DVM and check the data link connector
ground circuit.
1. Ignition "On", engine "Off".
2. Check the circuit for short to power supply circuit.
Was the DVM indicated specified value?
B-58
VV
Less than 1V Go to Step 10
Repair faulty
harness and
verify repair
10
Using the DVM and check the data link connector
communication circuit.
1. Ignition "On", engine "Off".
2. Check the circuit for short to power supply circuit.
Was the DVM indicated battery voltage?
V
B-58
-
Repair faulty
harness and
verify repair
Go to Step 11
Page 2096 of 4264
6E-100 3.5L ENGINE DRIVEABILITY AND EMISSIONS
Step Action Value (s) Yes No
11
Using the DVM and check the data link connector
communication circuit.
1. Ignition "Off", engine "Off".
2. Disconnect the ECM connector.
3. Check the circuit for open or short to ground circuit.
Was the problem found?
E-61(B)
B-58
-
Repair faulty
harness and
verify repair
Go to Step 12
12
Is the ECM programmed with the latest software
release?
If not, download the latest software to the ECM using
the "SPS (Service Programming System)"
.
Was the problem solved?
-
Verify repair
Go to Step 13
13
Replace the ECM.
Is the action complete?
IMPORTANT:
The replacement ECM must be
programmed. Refer to section of the Service
Programming System (SPS) in this manual. Following
ECM programming, the Immobilizer system (if
equipped) must be linked to the ECM. Refer to section
11 “Immobilizer System-ECM replacement”
for the
ECM/Immobilizer linking procedure.
-
Verify repair
-