Page 1321 of 4264
FUEL SYSTEM 6C – 21
020L200017
RTW46CSH000201
18. Timing Check Hole Cover
1) Remove the timing check hole cover.
2) For ease in reinstalling the injection pump, align the
timing mark on the timing gear case cover by turning
the crankshaft using wrench.
And bring the piston in the No.1 cylinder to TDC on the
compression stroke by turning the crankshaft until the
crankshaft pulley TDC line aligned with the timing
mark.
Note:
If the check hole cover is reinstalled with the lock bolt
still in place, the crank pulley will not turn.
6C-7
3) Insert the lock bolt (M6 x 30) into the scissors gear idle
gear “B” fixing hole to prevent the scissors gear from
turning.
29. Injection Pump Bracket
20. Injection Pump
Page 1322 of 4264
6C – 22 FUEL SYSTEM
RTW46CSH000201
Installation
1. Injection Pump
1) Install the injection pump gear (When gear is
removed).
Injection Pump Gear Nut N
m (kg
m/lb ft)
64 (6.5 / 47)
2) Bring the piston in the No.1 cylinder to TDC on the
compression stroke by turning the crankshaft until the
crankshaft pulley TDC line aligned with the timing
mark.
020L200017
3) Install the injection pump to the timing gear case with
align the timing mark on the pump gear to the arrow
mark on the timing gear case cover.
4) Check that the setting marks of the injection pump
gear and the idler gear B are aligned.
5) Remove the lock bolt (M6
30) from the idle gear “B”.
6C-7
6) Tighten the injection pump fixing bolts to the specified
torque.
Injection Pump Bolts Torque N·m (kg·m/lb ft)
19 (1.9 / 14)
Page 1323 of 4264
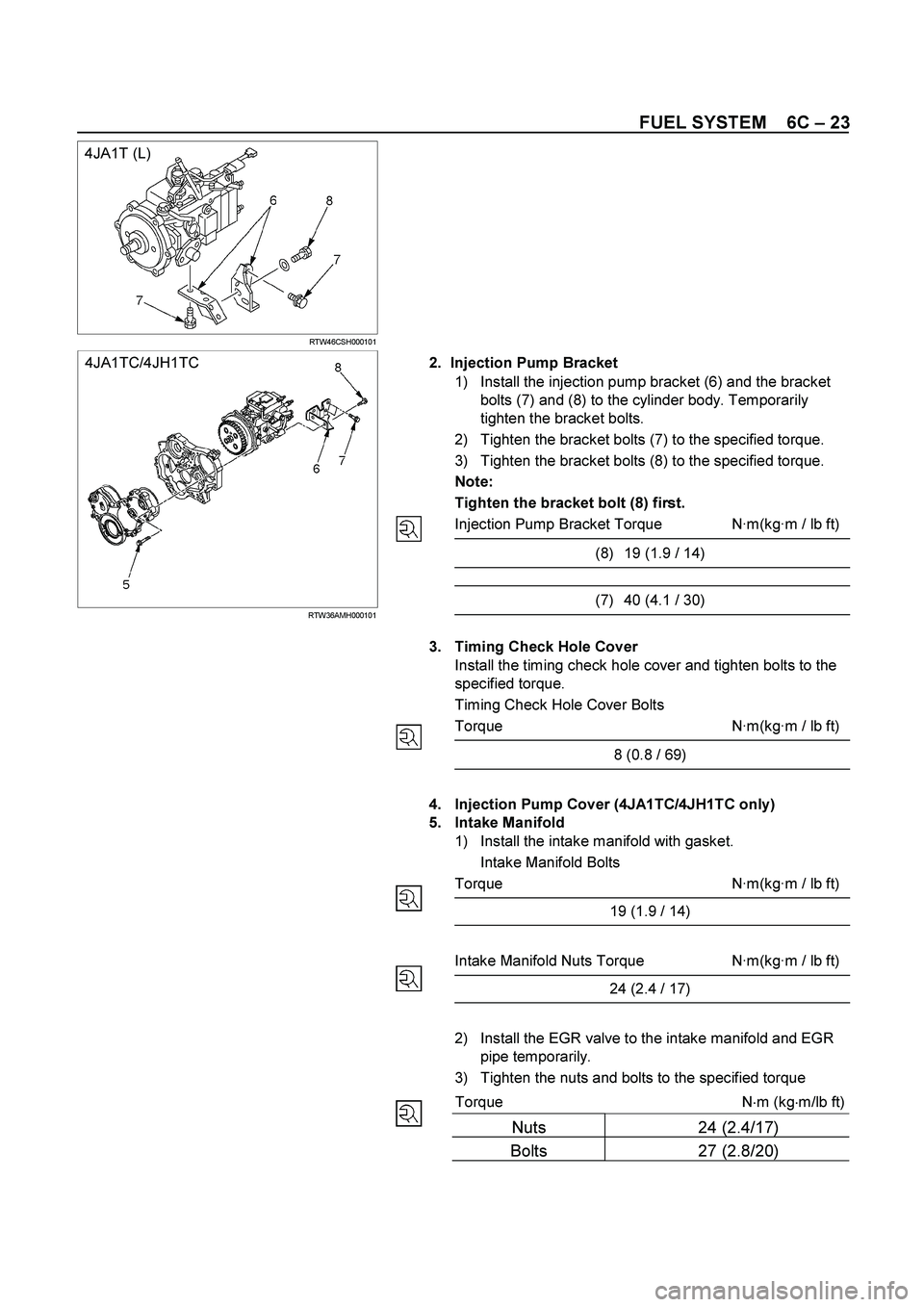
FUEL SYSTEM 6C – 23
4JA1T (L)
RTW46CSH000101
4JA1TC/4JH1TC
RTW36AMH000101
2. Injection Pump Bracket
1) Install the injection pump bracket (6) and the bracket
bolts (7) and (8) to the cylinder body. Temporarily
tighten the bracket bolts.
2) Tighten the bracket bolts (7) to the specified torque.
3) Tighten the bracket bolts (8) to the specified torque.
Note:
Tighten the bracket bolt (8) first.
Injection Pump Bracket Torque N·m(kg·m / lb ft)
(8) 19 (1.9 / 14)
(7) 40 (4.1 / 30)
3. Timing Check Hole Cover
Install the timing check hole cover and tighten bolts to the
specified torque.
Timing Check Hole Cover Bolts
Torque N·m(kg·m / lb ft)
8 (0.8 / 69)
4. Injection Pump Cover (4JA1TC/4JH1TC only)
5. Intake Manifold
1) Install the intake manifold with gasket.
Intake Manifold Bolts
Torque N·m(kg·m / lb ft)
19 (1.9 / 14)
Intake Manifold Nuts Torque N·m(kg·m / lb ft)
24 (2.4 / 17)
2) Install the EGR valve to the intake manifold and EGR
pipe temporarily.
3) Tighten the nuts and bolts to the specified torque
Torque Nm (kgm/lb ft)
Nuts 24 (2.4/17)
Bolts 27 (2.8/20)
Page 1324 of 4264
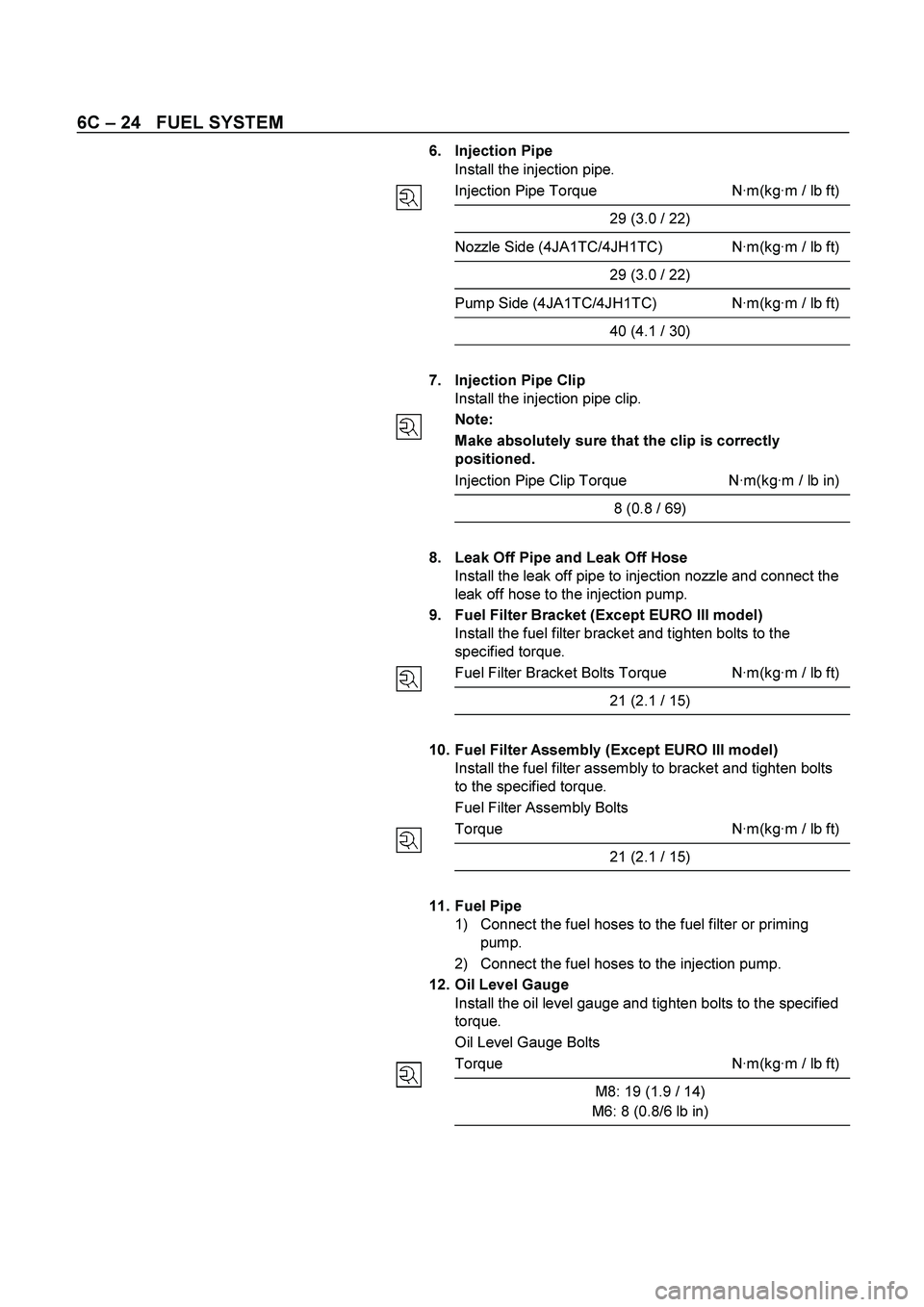
6C – 24 FUEL SYSTEM
6. Injection Pipe
Install the injection pipe.
Injection Pipe Torque N·m(kg·m / lb ft)
29 (3.0 / 22)
Nozzle Side (4JA1TC/4JH1TC) N·m(kg·m / lb ft)
29 (3.0 / 22)
Pump Side (4JA1TC/4JH1TC) N·m(kg·m / lb ft)
40 (4.1 / 30)
7. Injection Pipe Clip
Install the injection pipe clip.
Note:
Make absolutely sure that the clip is correctly
positioned.
Injection Pipe Clip Torque N·m(kg·m / lb in)
8 (0.8 / 69)
8. Leak Off Pipe and Leak Off Hose
Install the leak off pipe to injection nozzle and connect the
leak off hose to the injection pump.
9. Fuel Filter Bracket (Except EURO III model)
Install the fuel filter bracket and tighten bolts to the
specified torque.
Fuel Filter Bracket Bolts Torque N·m(kg·m / lb ft)
21 (2.1 / 15)
10. Fuel Filter Assembly (Except EURO III model)
Install the fuel filter assembly to bracket and tighten bolts
to the specified torque.
Fuel Filter Assembly Bolts
Torque N·m(kg·m / lb ft)
21 (2.1 / 15)
11. Fuel Pipe
1) Connect the fuel hoses to the fuel filter or priming
pump.
2) Connect the fuel hoses to the injection pump.
12. Oil Level Gauge
Install the oil level gauge and tighten bolts to the specified
torque.
Oil Level Gauge Bolts
Torque N·m(kg·m / lb ft)
M8: 19 (1.9 / 14)
M6: 8 (0.8/6 lb in)
Page 1325 of 4264
FUEL SYSTEM 6C – 25
13. Throttle Position Sensor Harness Connector
(4JA1TC/4JH1TC only)
Reconnect the harness connector to the throttle position
sensor.
14. Power Steering Pump Bracket
15. Fan
16. Vacuum Hose
Connect the vacuum hose to the EGR valve and the
intake throttle.
Euro under Euro I Euro II Euro III
4JA1L without with with Not used
4JA1TC Not used Not used Not used With cooler
(EGR cooler)
4JH1TC without with with With
(EGR cooler)
17. Accelerator Control Cable
1) Connect the accelerator cable to the injection pump
(4JA1T) the intake throttle. (4JA1TC/4JH1TC only)
18. Power Steering Pump Assembly
19. Drive Belt
Install the drive belt and adjust the belt tension.
20. Battery
Page 1326 of 4264
6C – 26 FUEL SYSTEM
INJECTION NOZZLE (4JA1L)
DISASSEMBLY
080L200009
Disassembly Steps
1.
Retaining nut 9.
Collar
2.
Nozzle & pin 10.
Spring seat
3.
Spacer & pin 11.
First spring
4.
Lift Piece 12.
Shim (First nozzle opening
pressure adjustment)
5.
Spring seat 13.
Nozzle holder body
6.
Push rod 14.
Eye bolt
7.
Shim (Second nozzle opening
pressure adjustment) 15.
Gasket
8.
Second spring
Important Operations
Injection nozzle adjustment is possible only on the 4JA1L
engine.
The two-spring nozzle holder has been developed to
reduce NOx (Nitrogen Oxides) and particulates from direct
injection diesel engine exhaust.
Before disassembly remove carbon deposit from nozzle
and nozzle holder using a wire brush and wash the outside
nozzle holder assembly.
Caution:
Do not touch nozzle holes with the wire brush during
cleaning it.
Disassemble the nozzle holder assembly to numerical
order.
Page 1327 of 4264
FUEL SYSTEM 6C – 27
REASSEMBLY
080L200010
Reassembly Steps
1.
Nozzle holder body 9.
Spring seat
2.
Shim (First opening pressure
adjustment) 10.
Lift Piece
3.
First spring 11.
Spacer & pin
4.
Spring seat 12.
Nozzle & pin
5.
Collar 13.
Retaining nut
6.
Second spring 14.
Gasket
7.
Push rod 15.
Eye bolt
8.
Shim (Second opening pressure
adjustment)
Important Operations
The nozzle holder is adjusted as the components are
reassembled in the sequence above.
As adjustment of the two-spring nozzle holder is made in
hundredths of a millimeter, clean the parts thoroughly in
light oil to completely remove any dirt or foreign matter.
Page 1328 of 4264
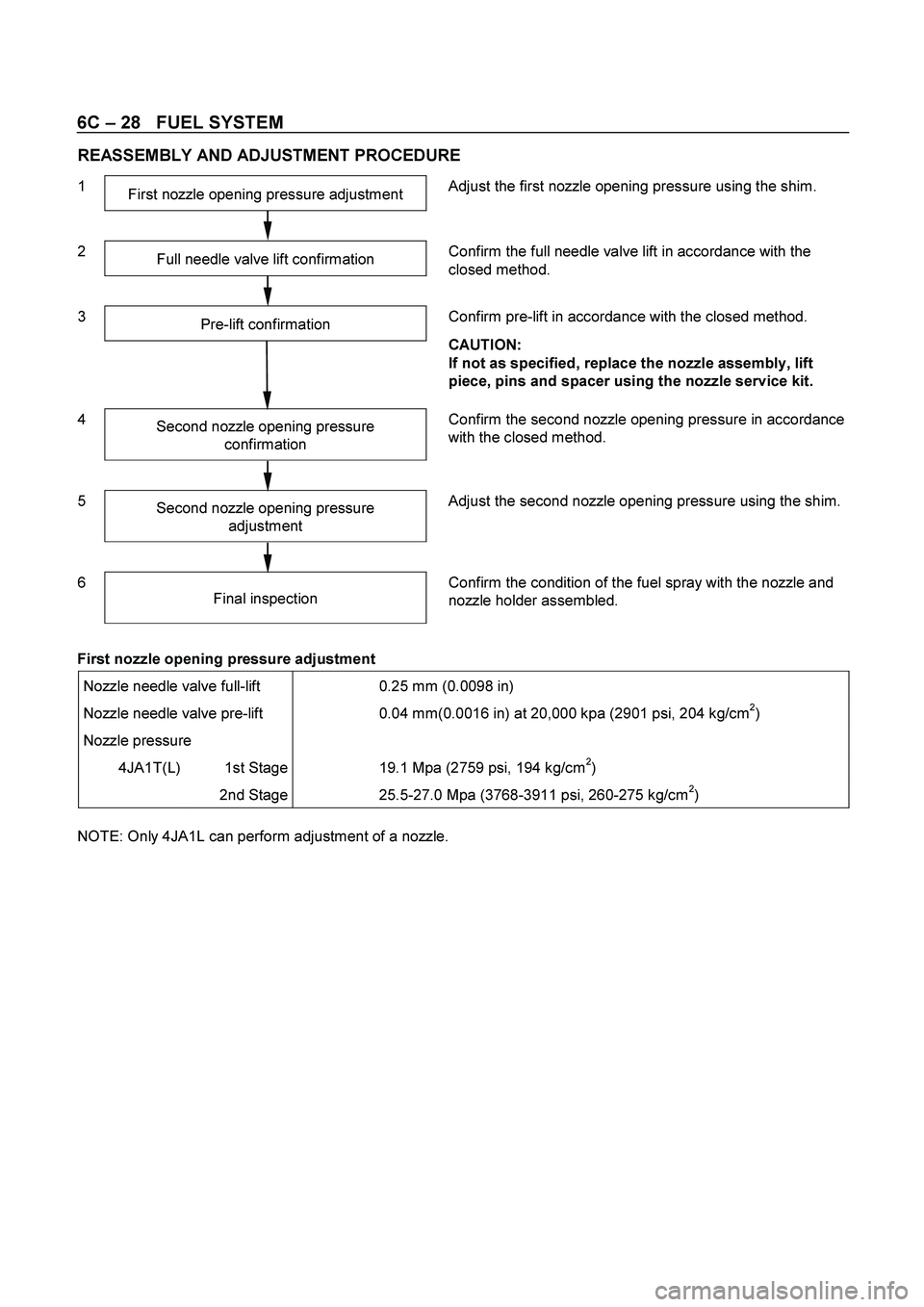
6C – 28 FUEL SYSTEM
REASSEMBLY AND ADJUSTMENT PROCEDURE
1
First nozzle opening pressure adjustment Adjust the first nozzle opening pressure using the shim.
2
Full needle valve lift confirmation Confirm the full needle valve lift in accordance with the
closed method.
3
Pre-lift confirmation
Confirm pre-lift in accordance with the closed method.
CAUTION:
If not as specified, replace the nozzle assembly, lift
piece, pins and spacer using the nozzle service kit.
4
Second nozzle opening pressure
confirmation Confirm the second nozzle opening pressure in accordance
with the closed method.
5
Second nozzle opening pressure
adjustment Adjust the second nozzle opening pressure using the shim.
6
Final inspection Confirm the condition of the fuel spray with the nozzle and
nozzle holder assembled.
First nozzle opening pressure adjustment
Nozzle needle valve full-lift 0.25 mm (0.0098 in)
Nozzle needle valve pre-lift 0.04 mm(0.0016 in) at 20,000 kpa (2901 psi, 204 kg/cm2)
Nozzle pressure
4JA1T(L) 1st Stage 19.1 Mpa (2759 psi, 194 kg/cm2)
2nd Stage 25.5-27.0 Mpa (3768-3911 psi, 260-275 kg/cm2)
NOTE: Only 4JA1L can perform adjustment of a nozzle.