Page 2305 of 4264
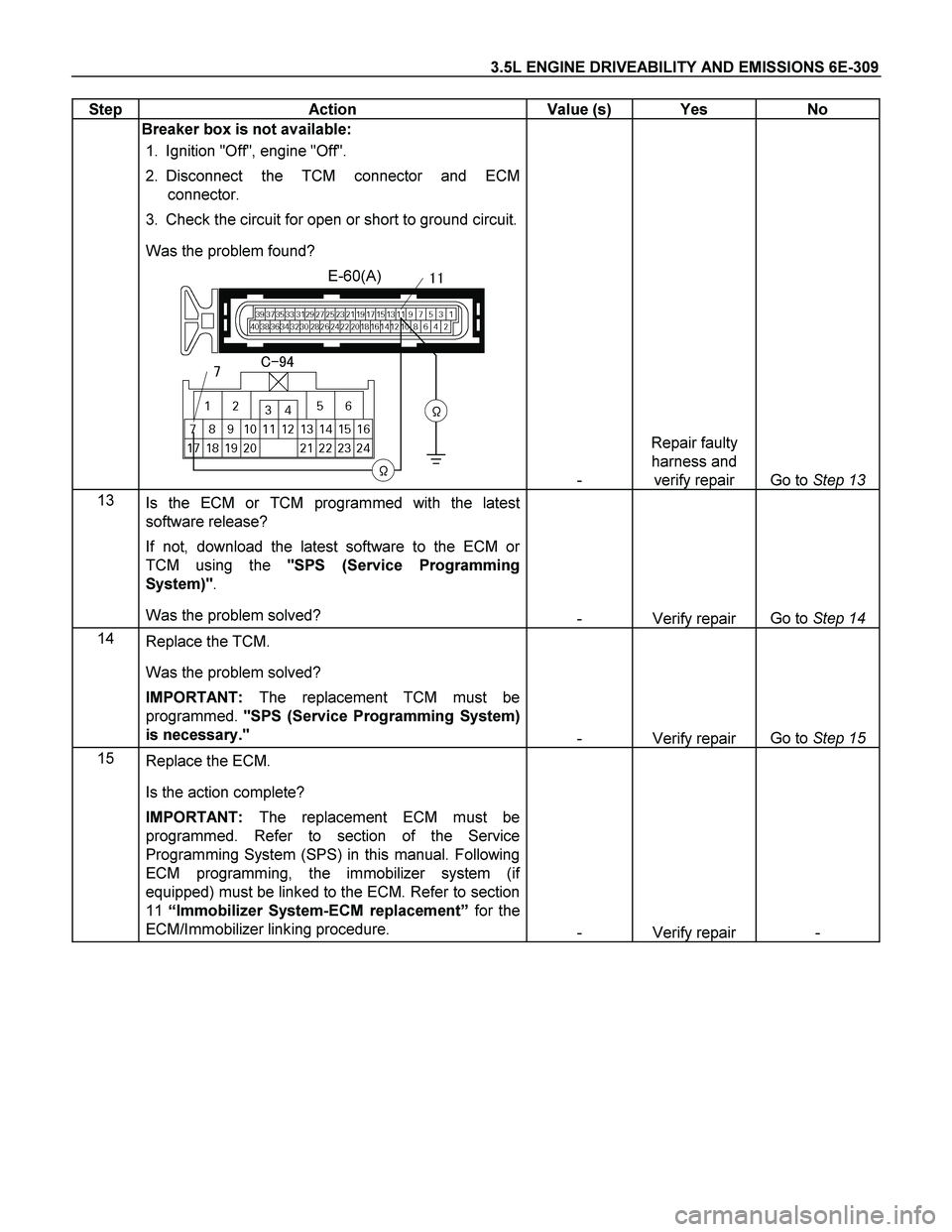
3.5L ENGINE DRIVEABILITY AND EMISSIONS 6E-309
Step Action Value (s) Yes No
Breaker box is not available:
1. Ignition "Off", engine "Off".
2. Disconnect the TCM connector and ECM
connector.
3. Check the circuit for open or short to ground circuit.
Was the problem found?
E-60(A)
-
Repair faulty
harness and
verify repair
Go to Step 13
13
Is the ECM or TCM programmed with the latest
software release?
If not, download the latest software to the ECM or
TCM using the "SPS (Service Programming
System)".
Was the problem solved?
- Verify repair Go to Step 14
14
Replace the TCM.
Was the problem solved?
IMPORTANT: The replacement TCM must be
programmed. "SPS (Service Programming System)
is necessary."
- Verify repair Go to Step 15
15
Replace the ECM.
Is the action complete?
IMPORTANT: The replacement ECM must be
programmed. Refer to section of the Service
Programming System (SPS) in this manual. Following
ECM programming, the immobilizer system (if
equipped) must be linked to the ECM. Refer to section
11 “Immobilizer System-ECM replacement” for the
ECM/Immobilizer linking procedure.
- Verify repair -
Page 2306 of 4264
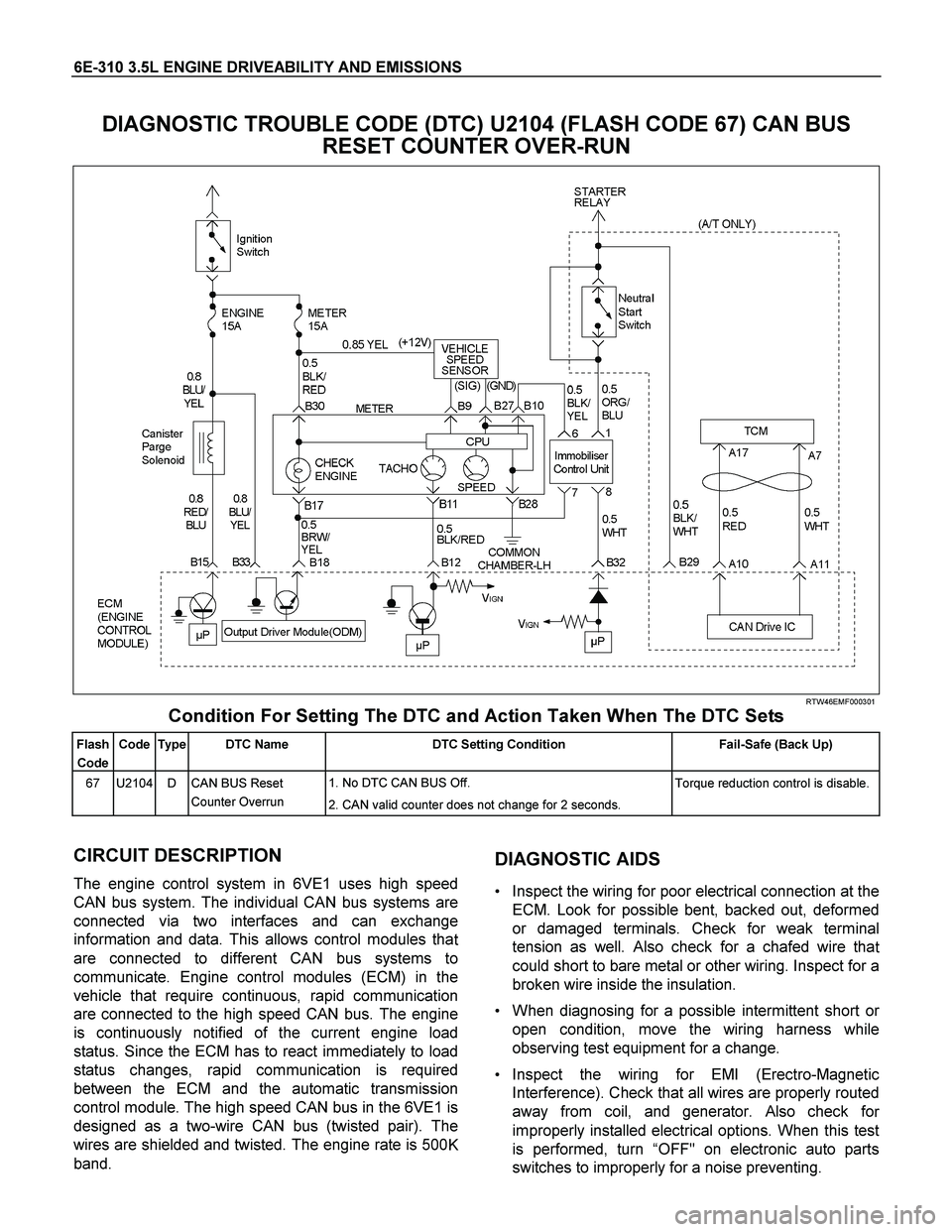
6E-310 3.5L ENGINE DRIVEABILITY AND EMISSIONS
DIAGNOSTIC TROUBLE CODE (DTC) U2104 (FLASH CODE 67) CAN BUS
RESET COUNTER OVER-RUN
RTW46EMF000301
Condition For Setting The DTC and Action Taken When The DTC Sets
Flash
Code Code Type DTC Name DTC Setting Condition Fail-Safe (Back Up)
67 U2104 D CAN BUS Reset
Counter Overrun 1. No DTC CAN BUS Off.
2. CAN valid counter does not change for 2 seconds. Torque reduction control is disable.
CIRCUIT DESCRIPTION
The engine control system in 6VE1 uses high speed
CAN bus system. The individual CAN bus systems are
connected via two interfaces and can exchange
information and data. This allows control modules tha
t
are connected to different CAN bus systems to
communicate. Engine control modules (ECM) in the
vehicle that require continuous, rapid communication
are connected to the high speed CAN bus. The engine
is continuously notified of the current engine load
status. Since the ECM has to react immediately to load
status changes, rapid communication is required
between the ECM and the automatic transmission
control module. The high speed CAN bus in the 6VE1 is
designed as a two-wire CAN bus (twisted pair). The
wires are shielded and twisted. The engine rate is 500
K
band.
DIAGNOSTIC AIDS
Inspect the wiring for poor electrical connection at the
ECM. Look for possible bent, backed out, deformed
or damaged terminals. Check for weak terminal
tension as well. Also check for a chafed wire tha
t
could short to bare metal or other wiring. Inspect for a
broken wire inside the insulation.
When diagnosing for a possible intermittent short o
r
open condition, move the wiring harness while
observing test equipment for a change.
Inspect the wiring for EMI (Erectro-Magnetic
Interference). Check that all wires are properly routed
away from coil, and generator. Also check fo
r
improperly installed electrical options. When this test
is performed, turn “OFF" on electronic auto parts
switches to improperly for a noise preventing.
Page 2307 of 4264
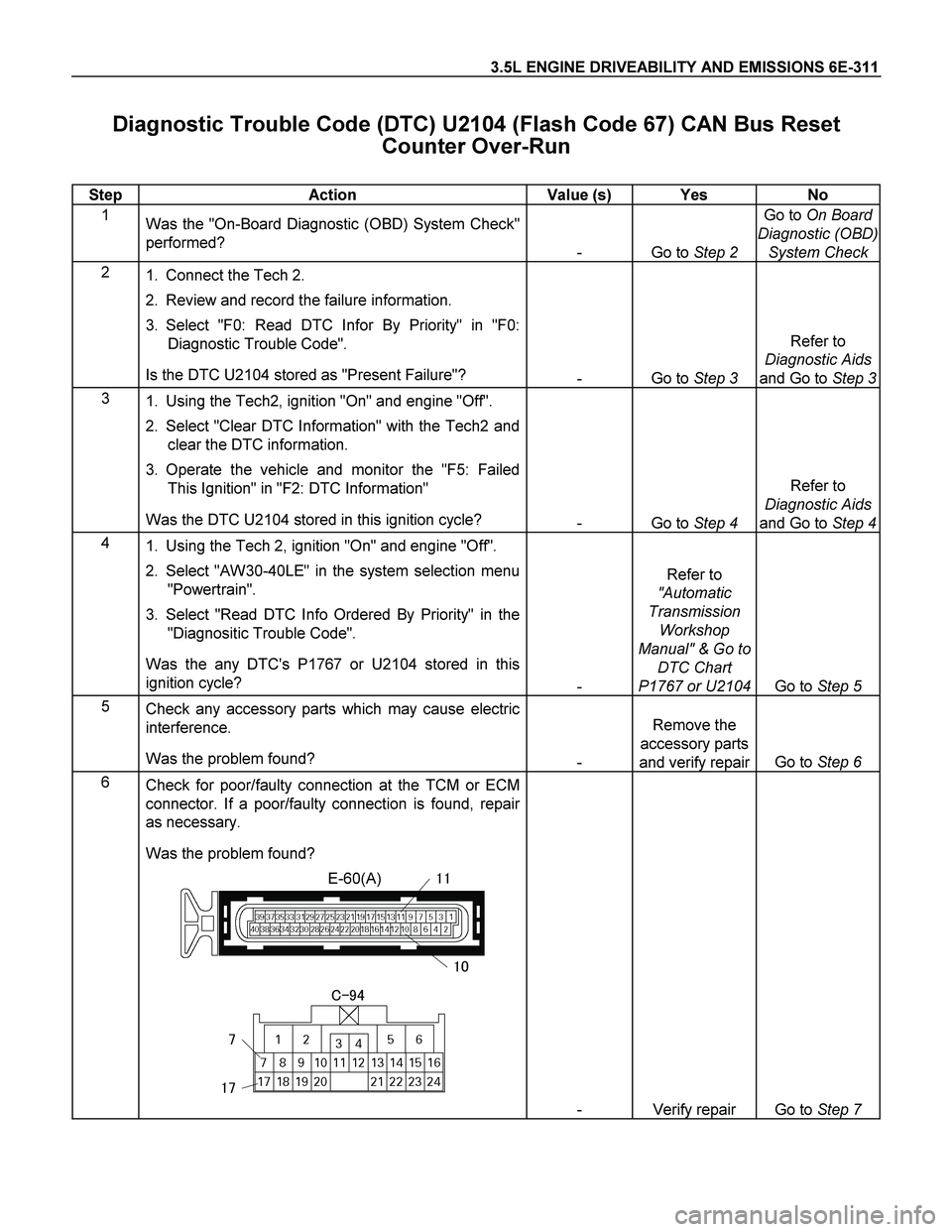
3.5L ENGINE DRIVEABILITY AND EMISSIONS 6E-311
Diagnostic Trouble Code (DTC) U2104 (Flash Code 67) CAN Bus Reset
Counter Over-Run
Step Action Value (s) Yes No
1
Was the "On-Board Diagnostic (OBD) System Check"
performed?
- Go to Step 2 Go to On Board
Diagnostic (OBD)
System Check
2
1. Connect the Tech 2.
2. Review and record the failure information.
3. Select "F0: Read DTC Infor By Priority" in "F0:
Diagnostic Trouble Code".
Is the DTC U2104 stored as "Present Failure"?
- Go to Step 3 Refer to
Diagnostic Aids
and Go to Step 3
3
1. Using the Tech2, ignition "On" and engine "Off".
2. Select "Clear DTC Information" with the Tech2 and
clear the DTC information.
3. Operate the vehicle and monitor the "F5: Failed
This Ignition" in "F2: DTC Information"
Was the DTC U2104 stored in this ignition cycle?
- Go to Step 4 Refer to
Diagnostic Aids
and Go to Step 4
4
1. Using the Tech 2, ignition "On" and engine "Off".
2. Select "AW30-40LE" in the system selection menu
"Powertrain".
3. Select "Read DTC Info Ordered By Priority" in the
"Diagnositic Trouble Code".
Was the any DTC's P1767 or U2104 stored in this
ignition cycle?
- Refer to
"Automatic
Transmission
Workshop
Manual" & Go to
DTC Chart
P1767 or U2104 Go to Step 5
5
Check any accessory parts which may cause electric
interference.
Was the problem found?
- Remove the
accessory parts
and verify repair Go to Step 6
6
Check for poor/faulty connection at the TCM or ECM
connector. If a poor/faulty connection is found, repair
as necessary.
Was the problem found?
E-60(A)
- Verify repair Go to Step 7
Page 2308 of 4264
6E-312 3.5L ENGINE DRIVEABILITY AND EMISSIONS
Step Action Value (s) Yes No
7
Using the DVM and check the CAN BUS high circuit.
1. Ignition "Off", engine "Off".
2. Disconnect the TCM connector.
3. Ignition "On".
4. Check the circuit for short to power supply circuit.
Was the problem found?
V
-
Repair faulty
harness and
verify repair
Go to Step 8
8
Using the DVM and check the CAN BUS low circuit.
1. Ignition "Off", engine "Off".
2. Disconnect the TCM connector.
3. Ignition "On".
4. Check the circuit for short to power supply circuit.
Was the problem found?
V
-
Repair faulty
harness and
verify repair
Go to Step 9
9
Using the DVM and check the ECM CAN BUS circuit.
1. Ignition "Off", engine "Off".
2. Disconnect TCM connector.
3. Measure the resistance of ECM CAN BUS circuit.
Does the tester indicate standard resistance?
Approximately
120
Go to Step 14
Close to 0: Go
to Step 10
No resistance:
Go to Step 11
Page 2309 of 4264
3.5L ENGINE DRIVEABILITY AND EMISSIONS 6E-313
Step Action Value (s) Yes No
10
Repair the open circuit between the ECM CAN BUS
high and low circuit.
Was the problem solved?
E-60(A)
- Verify repair Go to Step 15
Page 2310 of 4264
6E-314 3.5L ENGINE DRIVEABILITY AND EMISSIONS
Step Action Value (s) Yes No
11
Using the DVM and check the CAN BUS high circuit.
Breaker box is available:
1. Ignition "Off", engine "Off".
2. Install the breaker box as type A (ECM
disconnected).
Refer to 6E-95 page.
3. Disconnect the TCM connector.
4. Check the circuit for open or short to ground circuit.
Was the problem found?
A10
Breaker Box
Breaker box is not available:
1. Ignition "Off", engine "Off".
2. Disconnect the TCM connector and ECM
connector.
3. Check the circuit for open or short to ground circuit.
Was the problem found?
E-60(A)
-
Repair faulty
harness and
verify repair
Go to Step 12
Page 2311 of 4264

3.5L ENGINE DRIVEABILITY AND EMISSIONS 6E-315
Step Action Value (s) Yes No
12
Using the DVM and check the CAN BUS low circuit.
Breaker box is available:
1. Ignition "Off", engine "Off".
2. Install the breaker box as type A (ECM
disconnected).
Refer to 6E-95 page.
3. Disconnect the TCM connector.
4. Check the circuit for open or short to ground circuit.
Was the problem found?
A11
Breaker Box
Breaker box is not available:
1. Ignition "Off", engine "Off".
2. Disconnect the TCM connector and ECM
connector.
3. Check the circuit for open or short to ground circuit.
Was the problem found?
E-60(A)
-
Repair faulty
harness and
verify repair
Go to Step 13
13
Is the ECM or TCM programmed with the latest
software release?
If not, download the latest software to the ECM or
TCM using the "SPS (Service Programming
System)".
Was the problem solved?
- Verify repair Go to Step 14
14
Replace the TCM.
Was the problem solved?
IMPORTANT: The replacement TCM must be
programmed. "SPS (Service Programming System)
and is necessary."
- Verify repair Go to Step 15
Page 2312 of 4264
6E-316 3.5L ENGINE DRIVEABILITY AND EMISSIONS
Step Action Value (s) Yes No
15
Replace the ECM.
Is the action complete?
IMPORTANT: The replacement ECM must be
programmed. Refer to section of the Service
Programming System (SPS) in this manual. Following
ECM programming, the immobilizer system (if
equipped) must be linked to the ECM. Refer to section
11 “Immobilizer System-ECM replacement” for the
ECM/Immobilizer linking procedure.
- Verify repair -