Page 2057 of 4264
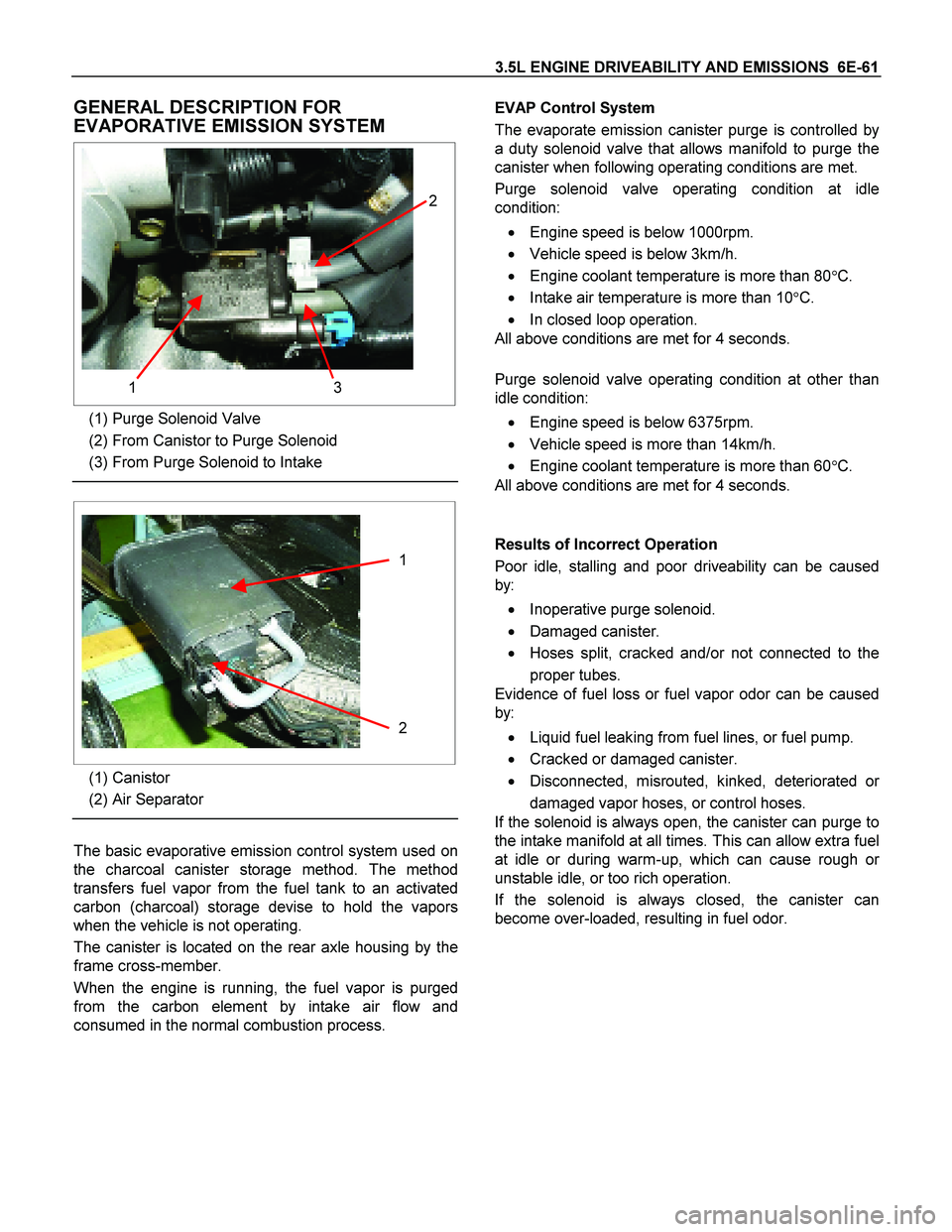
3.5L ENGINE DRIVEABILITY AND EMISSIONS 6E-61
GENERAL DESCRIPTION FOR
EVAPORATIVE EMISSION SYSTEM
3 1 2
(1) Purge Solenoid Valve
(2) From Canistor to Purge Solenoid
(3) From Purge Solenoid to Intake
1
2
(1) Canistor
(2) Air Separator
The basic evaporative emission control system used on
the charcoal canister storage method. The method
transfers fuel vapor from the fuel tank to an activated
carbon (charcoal) storage devise to hold the vapors
when the vehicle is not operating.
The canister is located on the rear axle housing by the
frame cross-member.
When the engine is running, the fuel vapor is purged
from the carbon element by intake air flow and
consumed in the normal combustion process.
EVAP Control System
The evaporate emission canister purge is controlled by
a duty solenoid valve that allows manifold to purge the
canister when following operating conditions are met.
Purge solenoid valve operating condition at idle
condition:
Engine speed is below 1000rpm.
Vehicle speed is below 3km/h.
Engine coolant temperature is more than 80C.
Intake air temperature is more than 10C.
In closed loop operation.
All above conditions are met for 4 seconds.
Purge solenoid valve operating condition at other than
idle condition:
Engine speed is below 6375rpm.
Vehicle speed is more than 14km/h.
Engine coolant temperature is more than 60C.
All above conditions are met for 4 seconds.
Results of Incorrect Operation
Poor idle, stalling and poor driveability can be caused
by:
Inoperative purge solenoid.
Damaged canister.
Hoses split, cracked and/or not connected to the
proper tubes.
Evidence of fuel loss or fuel vapor odor can be caused
by:
Liquid fuel leaking from fuel lines, or fuel pump.
Cracked or damaged canister.
Disconnected, misrouted, kinked, deteriorated o
r
damaged vapor hoses, or control hoses.
If the solenoid is always open, the canister can purge to
the intake manifold at all times. This can allow extra fuel
at idle or during warm-up, which can cause rough o
r
unstable idle, or too rich operation.
If the solenoid is always closed, the canister can
become over-loaded, resulting in fuel odor.
Page 2058 of 4264
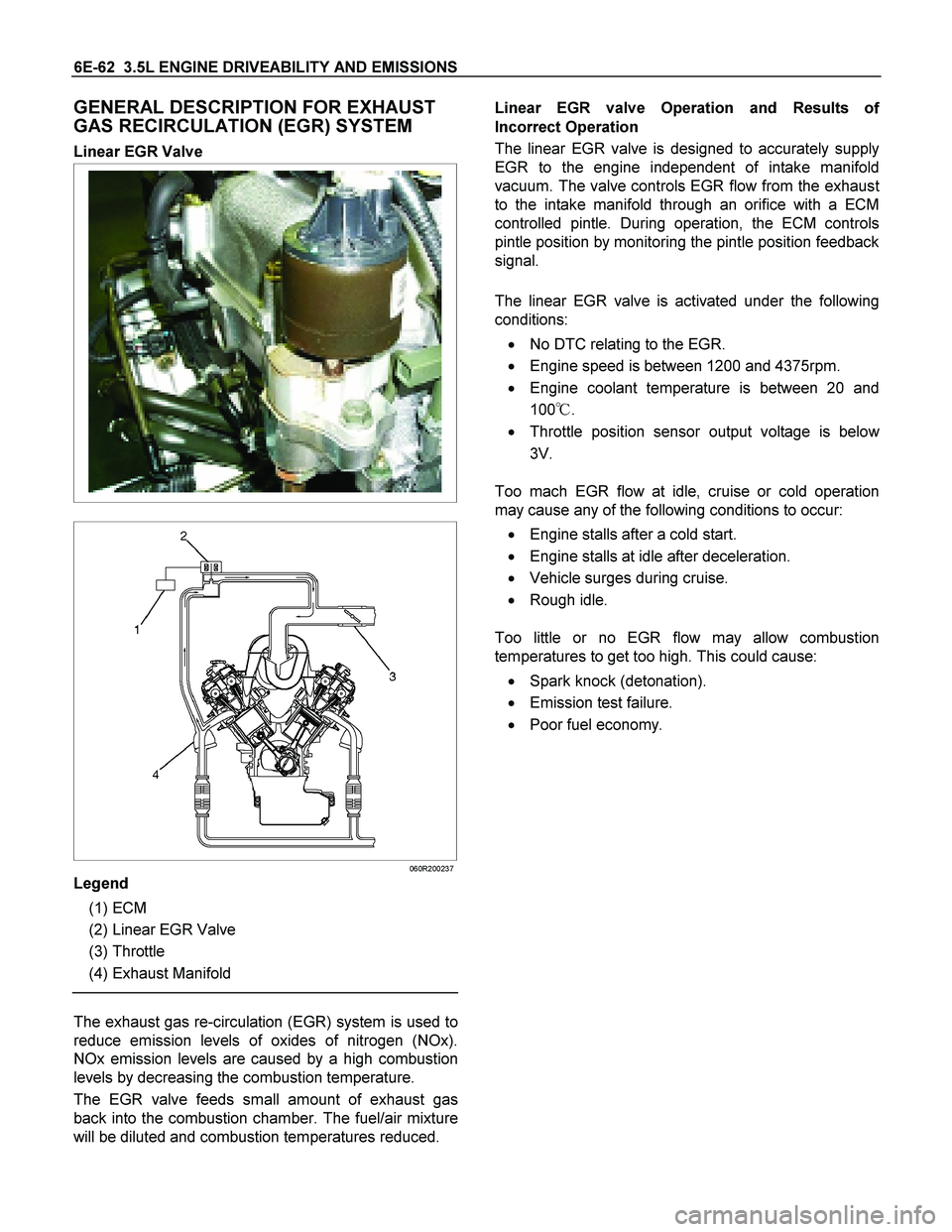
6E-62 3.5L ENGINE DRIVEABILITY AND EMISSIONS
GENERAL DESCRIPTION FOR EXHAUST
GAS RECIRCULATION (EGR) SYSTEM
Linear EGR Valve
060R200237
Legend
(1) ECM
(2) Linear EGR Valve
(3) Throttle
(4) Exhaust Manifold
The exhaust gas re-circulation (EGR) system is used to
reduce emission levels of oxides of nitrogen (NOx).
NOx emission levels are caused by a high combustion
levels by decreasing the combustion temperature.
The EGR valve feeds small amount of exhaust gas
back into the combustion chamber. The fuel/air mixture
will be diluted and combustion temperatures reduced.
Linear EGR valve Operation and Results o
f
Incorrect Operation
The linear EGR valve is designed to accurately supply
EGR to the engine independent of intake manifold
vacuum. The valve controls EGR flow from the exhaus
t
to the intake manifold through an orifice with a ECM
controlled pintle. During operation, the ECM controls
pintle position by monitoring the pintle position feedback
signal.
The linear EGR valve is activated under the following
conditions:
No DTC relating to the EGR.
Engine speed is between 1200 and 4375rpm.
Engine coolant temperature is between 20 and
100.
Throttle position sensor output voltage is belo
w
3V.
Too mach EGR flow at idle, cruise or cold operation
may cause any of the following conditions to occur:
Engine stalls after a cold start.
Engine stalls at idle after deceleration.
Vehicle surges during cruise.
Rough idle.
Too little or no EGR flow may allow combustion
temperatures to get too high. This could cause:
Spark knock (detonation).
Emission test failure.
Poor fuel economy.
Page 2059 of 4264
3.5L ENGINE DRIVEABILITY AND EMISSIONS 6E-63
ISUZU STRATEGY BASED DIAGNOSTICS
Overview
As a retail service technician, you are part of the ISUZU
service team. The team goal is FIX IT RIGHT THE
FIRST TIME for the satisfaction of every customer. You
are a very important member of the team as you
diagnose and repair customer vehicles. You have maximum efficiency in diagnosis when you
have an effective, organized plan for your work.
Strategy Based Diagnostics (refer to Figure 1) provides
you with guidance as you create and follow a plan of
action for each specific diagnostic situation.
STRATEGY BASED DIAGNOSTICS CHART
Page 2060 of 4264
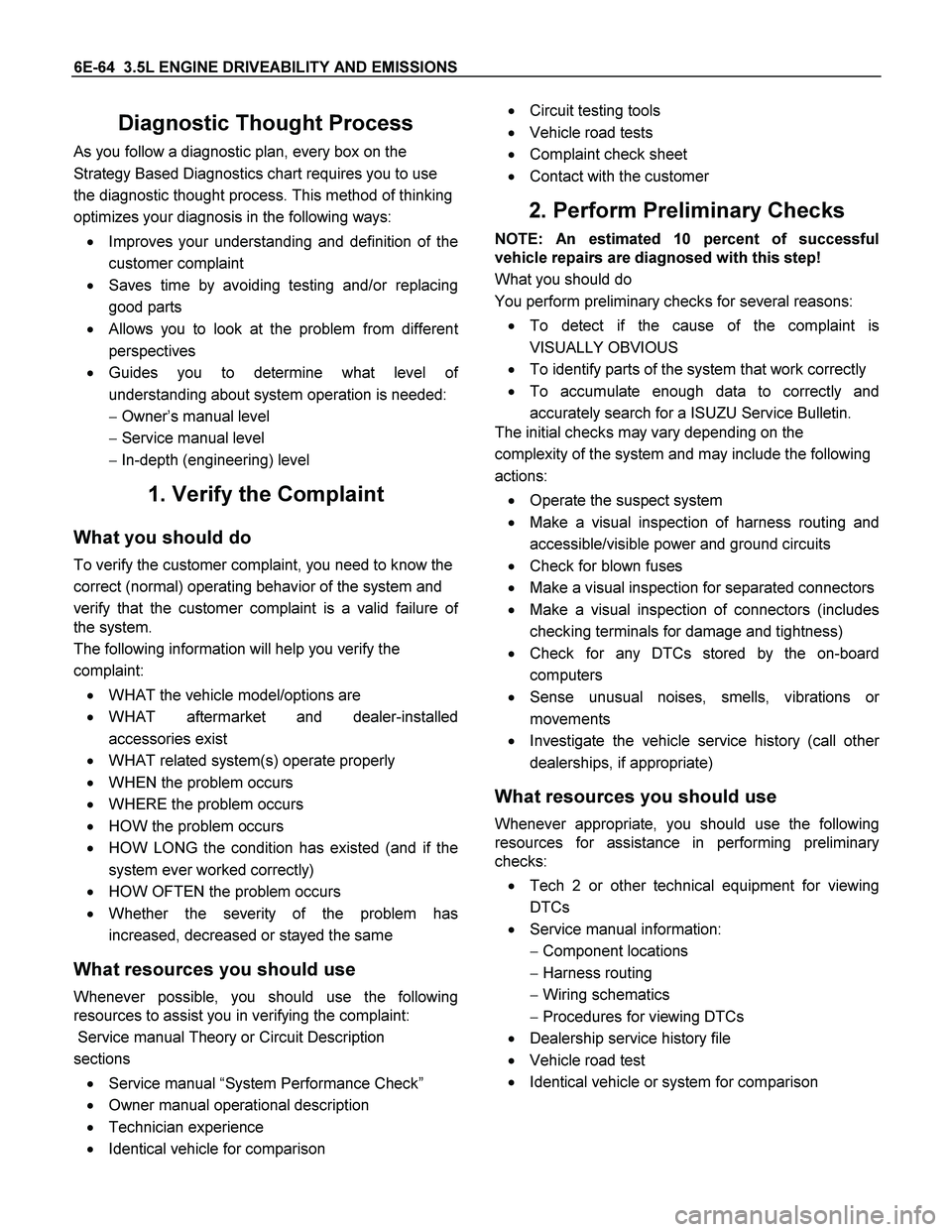
6E-64 3.5L ENGINE DRIVEABILITY AND EMISSIONS
Diagnostic Thought Process
As you follow a diagnostic plan, every box on the
Strategy Based Diagnostics chart requires you to use
the diagnostic thought process. This method of thinking
optimizes your diagnosis in the following ways:
Improves your understanding and definition of the
customer complaint
Saves time by avoiding testing and/or replacing
good parts
Allows you to look at the problem from different
perspectives
Guides you to determine what level o
f
understanding about system operation is needed:
Owner’s manual level
Service manual level
In-depth (engineering) level
1. Verify the Complaint
What you should do
To verify the customer complaint, you need to know the
correct (normal) operating behavior of the system and
verify that the customer complaint is a valid failure o
f
the system.
The following information will help you verify the
complaint:
WHAT the vehicle model/options are
WHAT aftermarket and dealer-installed
accessories exist
WHAT related system(s) operate properly
WHEN the problem occurs
WHERE the problem occurs
HOW the problem occurs
HOW LONG the condition has existed (and if the
system ever worked correctly)
HOW OFTEN the problem occurs
Whether the severity of the problem has
increased, decreased or stayed the same
What resources you should use
Whenever possible, you should use the following
resources to assist you in verifying the complaint:
Service manual Theory or Circuit Description
sections
Service manual “System Performance Check”
Owner manual operational description
Technician experience
Identical vehicle for comparison
Circuit testing tools
Vehicle road tests
Complaint check sheet
Contact with the customer
2. Perform Preliminary Checks
NOTE: An estimated 10 percent of successful
vehicle repairs are diagnosed with this step!
What you should do
You perform preliminary checks for several reasons:
To detect if the cause of the complaint is
VISUALLY OBVIOUS
To identify parts of the system that work correctly
To accumulate enough data to correctly and
accurately search for a ISUZU Service Bulletin.
The initial checks may vary depending on the
complexity of the system and may include the following
actions:
Operate the suspect system
Make a visual inspection of harness routing and
accessible/visible power and ground circuits
Check for blown fuses
Make a visual inspection for separated connectors
Make a visual inspection of connectors (includes
checking terminals for damage and tightness)
Check for any DTCs stored by the on-board
computers
Sense unusual noises, smells, vibrations o
r
movements
Investigate the vehicle service history (call othe
r
dealerships, if appropriate)
What resources you should use
Whenever appropriate, you should use the following
resources for assistance in performing preliminary
checks:
Tech 2 or other technical equipment for viewing
DTCs
Service manual information:
Component locations
Harness routing
Wiring schematics
Procedures for viewing DTCs
Dealership service history file
Vehicle road test
Identical vehicle or system for comparison
Page 2061 of 4264
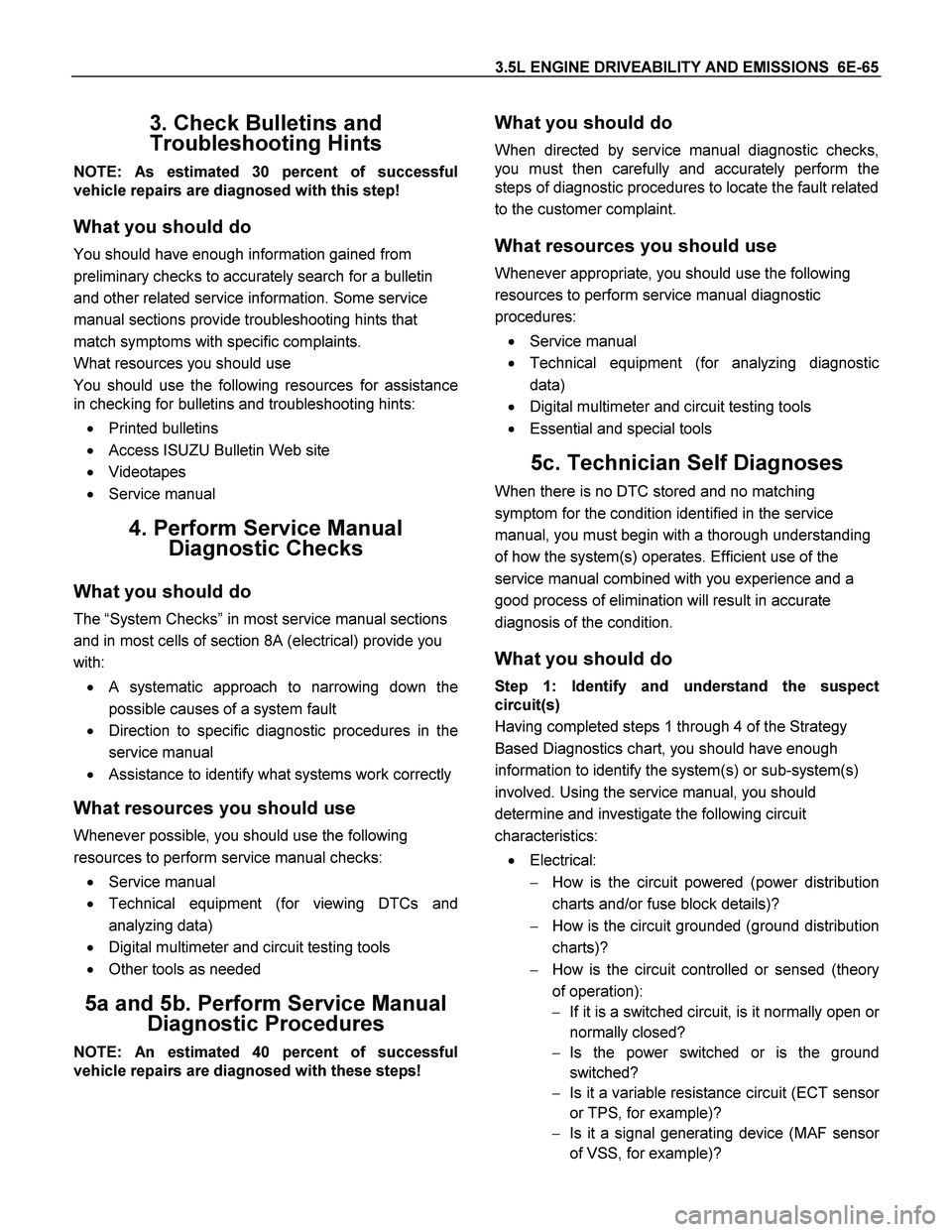
3.5L ENGINE DRIVEABILITY AND EMISSIONS 6E-65
3. Check Bulletins and
Troubleshooting Hints
NOTE: As estimated 30 percent of successful
vehicle repairs are diagnosed with this step!
What you should do
You should have enough information gained from
preliminary checks to accurately search for a bulletin
and other related service information. Some service
manual sections provide troubleshooting hints that
match symptoms with specific complaints.
What resources you should use
You should use the following resources for assistance
in checking for bulletins and troubleshooting hints:
Printed bulletins
Access ISUZU Bulletin Web site
Videotapes
Service manual
4. Perform Service Manual
Diagnostic Checks
What you should do
The “System Checks” in most service manual sections
and in most cells of section 8A (electrical) provide you
with:
A systematic approach to narrowing down the
possible causes of a system fault
Direction to specific diagnostic procedures in the
service manual
Assistance to identify what systems work correctly
What resources you should use
Whenever possible, you should use the following
resources to perform service manual checks:
Service manual
Technical equipment (for viewing DTCs and
analyzing data)
Digital multimeter and circuit testing tools
Other tools as needed
5a and 5b. Perform Service Manual
Diagnostic Procedures
NOTE: An estimated 40 percent of successful
vehicle repairs are diagnosed with these steps!
What you should do
When directed by service manual diagnostic checks,
you must then carefully and accurately perform the
steps of diagnostic procedures to locate the fault related
to the customer complaint.
What resources you should use
Whenever appropriate, you should use the following
resources to perform service manual diagnostic
procedures:
Service manual
Technical equipment (for analyzing diagnostic
data)
Digital multimeter and circuit testing tools
Essential and special tools
5c. Technician Self Diagnoses
When there is no DTC stored and no matching
symptom for the condition identified in the service
manual, you must begin with a thorough understanding
of how the system(s) operates. Efficient use of the
service manual combined with you experience and a
good process of elimination will result in accurate
diagnosis of the condition.
What you should do
Step 1: Identify and understand the suspect
circuit(s)
Having completed steps 1 through 4 of the Strategy
Based Diagnostics chart, you should have enough
information to identify the system(s) or sub-system(s)
involved. Using the service manual, you should
determine and investigate the following circuit
characteristics:
Electrical:
How is the circuit powered (power distribution
charts and/or fuse block details)?
How is the circuit grounded (ground distribution
charts)?
How is the circuit controlled or sensed (theory
of operation):
If it is a switched circuit, is it normally open o
r
normally closed?
Is the power switched or is the ground
switched?
Is it a variable resistance circuit (ECT senso
r
or TPS, for example)?
Is it a signal generating device (MAF senso
r
of VSS, for example)?
Page 2062 of 4264
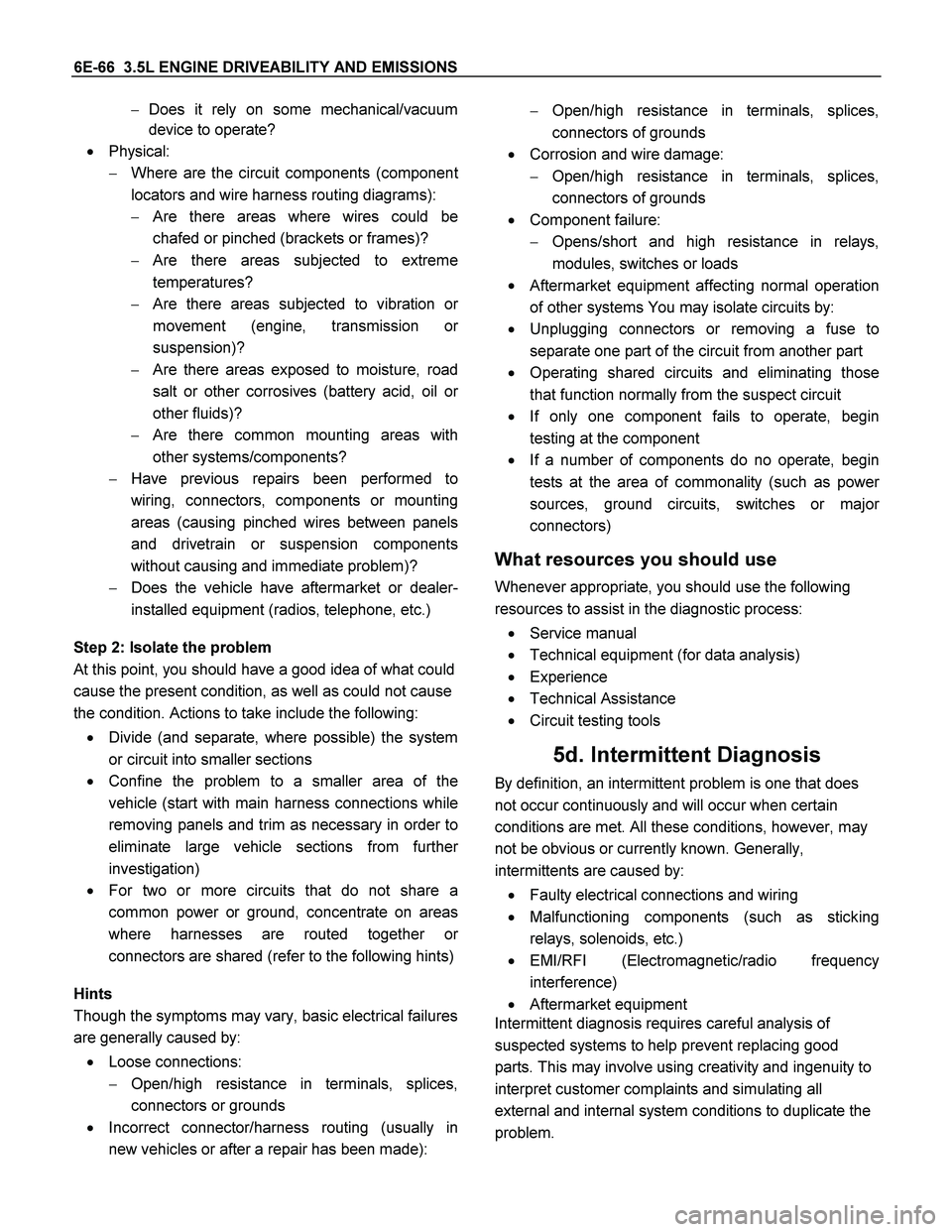
6E-66 3.5L ENGINE DRIVEABILITY AND EMISSIONS
Does it rely on some mechanical/vacuum
device to operate?
Physical:
Where are the circuit components (componen
t
locators and wire harness routing diagrams):
Are there areas where wires could be
chafed or pinched (brackets or frames)?
Are there areas subjected to extreme
temperatures?
Are there areas subjected to vibration or
movement (engine, transmission or
suspension)?
Are there areas exposed to moisture, road
salt or other corrosives (battery acid, oil o
r
other fluids)?
Are there common mounting areas with
other systems/components?
Have previous repairs been performed to
wiring, connectors, components or mounting
areas (causing pinched wires between panels
and drivetrain or suspension components
without causing and immediate problem)?
Does the vehicle have aftermarket or dealer-
installed equipment (radios, telephone, etc.)
Step 2: Isolate the problem
At this point, you should have a good idea of what could
cause the present condition, as well as could not cause
the condition. Actions to take include the following:
Divide (and separate, where possible) the system
or circuit into smaller sections
Confine the problem to a smaller area of the
vehicle (start with main harness connections while
removing panels and trim as necessary in order to
eliminate large vehicle sections from furthe
r
investigation)
For two or more circuits that do not share a
common power or ground, concentrate on areas
where harnesses are routed together o
r
connectors are shared (refer to the following hints)
Hints
Though the symptoms may vary, basic electrical failures
are generally caused by:
Loose connections:
Open/high resistance in terminals, splices,
connectors or grounds
Incorrect connector/harness routing (usually in
new vehicles or after a repair has been made):
Open/high resistance in terminals, splices,
connectors of grounds
Corrosion and wire damage:
Open/high resistance in terminals, splices,
connectors of grounds
Component failure:
Opens/short and high resistance in relays,
modules, switches or loads
Aftermarket equipment affecting normal operation
of other systems You may isolate circuits by:
Unplugging connectors or removing a fuse to
separate one part of the circuit from another part
Operating shared circuits and eliminating those
that function normally from the suspect circuit
If only one component fails to operate, begin
testing at the component
If a number of components do no operate, begin
tests at the area of commonality (such as powe
r
sources, ground circuits, switches or majo
r
connectors)
What resources you should use
Whenever appropriate, you should use the following
resources to assist in the diagnostic process:
Service manual
Technical equipment (for data analysis)
Experience
Technical Assistance
Circuit testing tools
5d. Intermittent Diagnosis
By definition, an intermittent problem is one that does
not occur continuously and will occur when certain
conditions are met. All these conditions, however, may
not be obvious or currently known. Generally,
intermittents are caused by:
Faulty electrical connections and wiring
Malfunctioning components (such as sticking
relays, solenoids, etc.)
EMI/RFI (Electromagnetic/radio frequency
interference)
Aftermarket equipment
Intermittent diagnosis requires careful analysis of
suspected systems to help prevent replacing good
parts. This may involve using creativity and ingenuity to
interpret customer complaints and simulating all
external and internal system conditions to duplicate the
problem.
Page 2063 of 4264
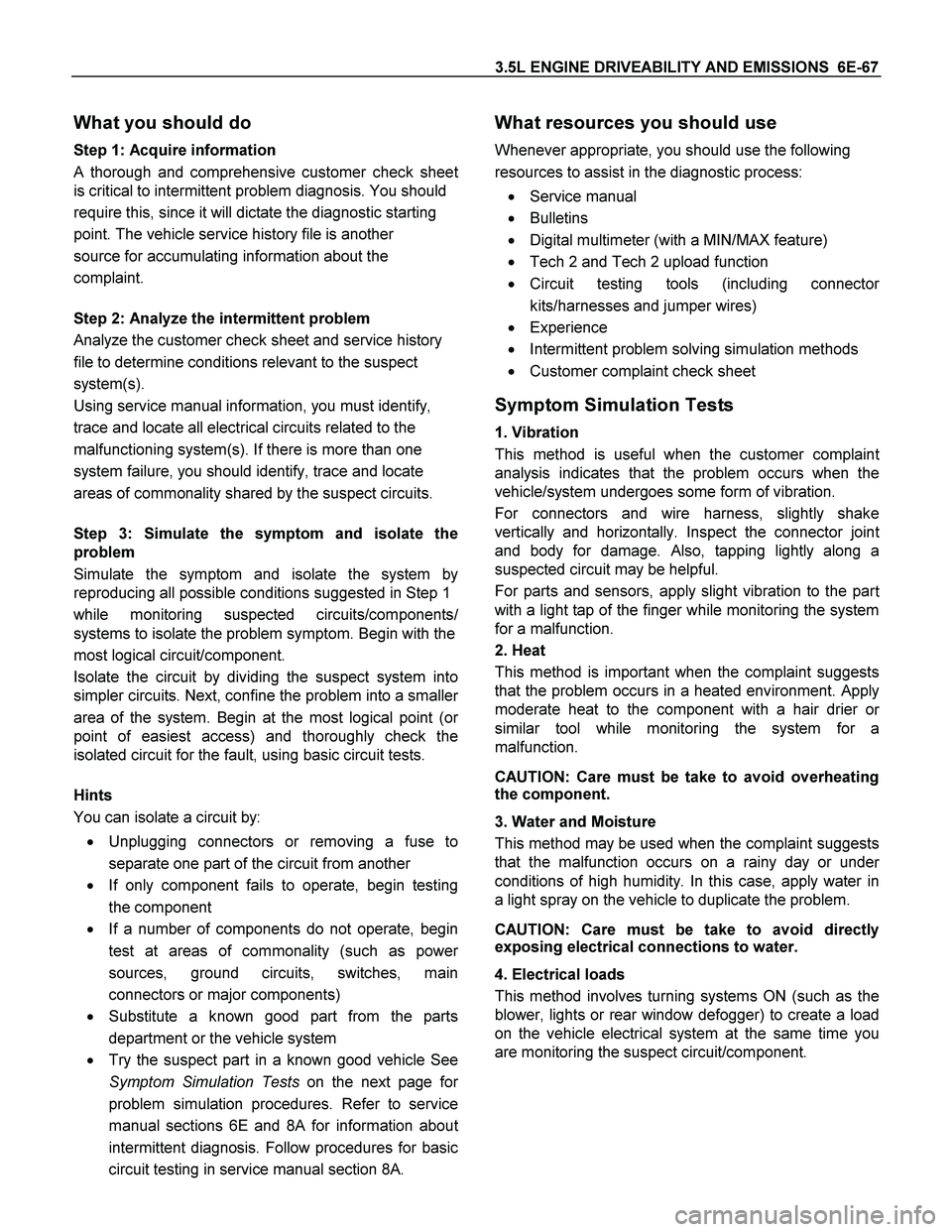
3.5L ENGINE DRIVEABILITY AND EMISSIONS 6E-67
What you should do
Step 1: Acquire information
A thorough and comprehensive customer check sheet
is critical to intermittent problem diagnosis. You should
require this, since it will dictate the diagnostic starting
point. The vehicle service history file is another
source for accumulating information about the
complaint.
Step 2: Analyze the intermittent problem
Analyze the customer check sheet and service history
file to determine conditions relevant to the suspect
system(s).
Using service manual information, you must identify,
trace and locate all electrical circuits related to the
malfunctioning system(s). If there is more than one
system failure, you should identify, trace and locate
areas of commonality shared by the suspect circuits.
Step 3: Simulate the symptom and isolate the
problem
Simulate the symptom and isolate the system by
reproducing all possible conditions suggested in Step 1
while monitoring suspected circuits/components
/
systems to isolate the problem symptom. Begin with the
most logical circuit/component.
Isolate the circuit by dividing the suspect system into
simpler circuits. Next, confine the problem into a smalle
r
area of the system. Begin at the most logical point (or
point of easiest access) and thoroughly check the
isolated circuit for the fault, using basic circuit tests.
Hints
You can isolate a circuit by:
Unplugging connectors or removing a fuse to
separate one part of the circuit from another
If only component fails to operate, begin testing
the component
If a number of components do not operate, begin
test at areas of commonality (such as powe
r
sources, ground circuits, switches, main
connectors or major components)
Substitute a known good part from the parts
department or the vehicle system
Try the suspect part in a known good vehicle See
Symptom Simulation Tests on the next page fo
r
problem simulation procedures. Refer to service
manual sections 6E and 8A for information abou
t
intermittent diagnosis. Follow procedures for basic
circuit testing in service manual section 8A.
What resources you should use
Whenever appropriate, you should use the following
resources to assist in the diagnostic process:
Service manual
Bulletins
Digital multimeter (with a MIN/MAX feature)
Tech 2 and Tech 2 upload function
Circuit testing tools (including connecto
r
kits/harnesses and jumper wires)
Experience
Intermittent problem solving simulation methods
Customer complaint check sheet
Symptom Simulation Tests
1. Vibration
This method is useful when the customer complain
t
analysis indicates that the problem occurs when the
vehicle/system undergoes some form of vibration.
For connectors and wire harness, slightly shake
vertically and horizontally. Inspect the connector join
t
and body for damage. Also, tapping lightly along a
suspected circuit may be helpful.
For parts and sensors, apply slight vibration to the par
t
with a light tap of the finger while monitoring the system
for a malfunction.
2. Heat
This method is important when the complaint suggests
that the problem occurs in a heated environment. Apply
moderate heat to the component with a hair drier o
r
similar tool while monitoring the system for a
malfunction.
CAUTION: Care must be take to avoid overheating
the component.
3. Water and Moisture
This method may be used when the complaint suggests
that the malfunction occurs on a rainy day or unde
r
conditions of high humidity. In this case, apply water in
a light spray on the vehicle to duplicate the problem.
CAUTION: Care must be take to avoid directly
exposing electrical connections to water.
4. Electrical loads
This method involves turning systems ON (such as the
blower, lights or rear window defogger) to create a load
on the vehicle electrical system at the same time you
are monitoring the suspect circuit/component.
Page 2064 of 4264
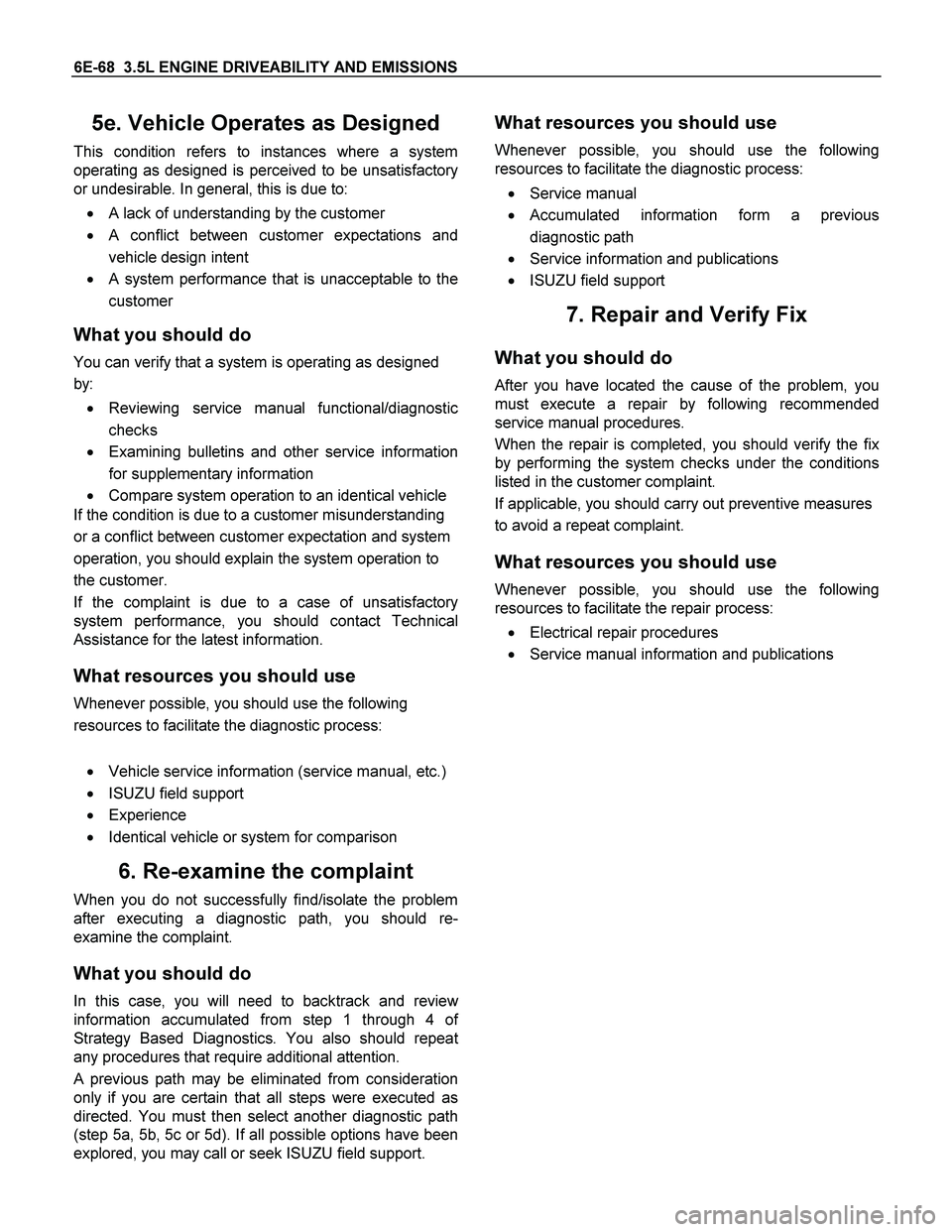
6E-68 3.5L ENGINE DRIVEABILITY AND EMISSIONS
5e. Vehicle Operates as Designed
This condition refers to instances where a system
operating as designed is perceived to be unsatisfactory
or undesirable. In general, this is due to:
A lack of understanding by the customer
A conflict between customer expectations and
vehicle design intent
A system performance that is unacceptable to the
customer
What you should do
You can verify that a system is operating as designed
by:
Reviewing service manual functional/diagnostic
checks
Examining bulletins and other service information
for supplementary information
Compare system operation to an identical vehicle
If the condition is due to a customer misunderstanding
or a conflict between customer expectation and system
operation, you should explain the system operation to
the customer.
If the complaint is due to a case of unsatisfactory
system performance, you should contact Technical
Assistance for the latest information.
What resources you should use
Whenever possible, you should use the following
resources to facilitate the diagnostic process:
Vehicle service information (service manual, etc.)
ISUZU field support
Experience
Identical vehicle or system for comparison
6. Re-examine the complaint
When you do not successfully find/isolate the problem
after executing a diagnostic path, you should re-
examine the complaint.
What you should do
In this case, you will need to backtrack and review
information accumulated from step 1 through 4 o
f
Strategy Based Diagnostics. You also should repeat
any procedures that require additional attention.
A previous path may be eliminated from consideration
only if you are certain that all steps were executed as
directed. You must then select another diagnostic path
(step 5a, 5b, 5c or 5d). If all possible options have been
explored, you may call or seek ISUZU field support.
What resources you should use
Whenever possible, you should use the following
resources to facilitate the diagnostic process:
Service manual
Accumulated information form a previous
diagnostic path
Service information and publications
ISUZU field support
7. Repair and Verify Fix
What you should do
After you have located the cause of the problem, you
must execute a repair by following recommended
service manual procedures.
When the repair is completed, you should verify the fix
by performing the system checks under the conditions
listed in the customer complaint.
If applicable, you should carry out preventive measures
to avoid a repeat complaint.
What resources you should use
Whenever possible, you should use the following
resources to facilitate the repair process:
Electrical repair procedures
Service manual information and publications