Page 1265 of 4264
ENGINE MECHANICAL 6A – 125
25. EGR Valve
Install the EGR valve assembly to the intake minifold with
the two gasket.
Tighten the four nuts to the specified torque.
Nut Tolque N·m(kg·m/Ib ft)
31 (3.1/23)
Connector the vacuum hose.
025R100008
RTW36ASH000301
26-1. EGR Pipe
Install the EGR valve adapter with the gasket to the EGR
valve assembly and install the EGR pipe with the gasket.
Tighten fixing bolts and nuts to the specified torque.
EGR Valve Adapter Bolts N·m(kg·m/Ib ft)
24 (2.4/17)
EGR Pipe Bolts and Nuts N·m(kg·m/Ib ft)
27 (2.7/20)
RTW48ASH001801
26-2. EGR Cooler (EURO III model only)
27. Intake Pipe and Throttle Body (4JA1TC/4JH1TC only)
Install the throttle body with the gasket to the intake
manifold and install the intake duct with the gasket.
Tighten the two bolts and the two nuts to the specified
torque.
Throttle Body and Intake Duct N·m(kg·m/Ib ft)
Bolt 19 (1.9/14)
Nut 24 (2.4/17)
RTW36ASH000201
28. Clutch Assembly or Flex Plate
Page 1266 of 4264
6A – 126 ENGINE MECHANICAL
LUBRICATION SYSTEM
LUBRICATING OIL FLOW
1. Oil Pump Relief Valve Operating Pressure: 6.2 - 7.8kg/cm 2 (608 - 764Kpa)
2. Regulating Valve Operating Pressure: 5.7 - 6.3kg/cm 2 (558.6 - 617.4Kpa)
3. Oil Cooler Relief Valve Opening Pressure: 2.8 - 3.4kg/cm 2 (270 - 330Kpa)
4. Oil Filter Relief Valve Opening Pressure: 0.8 - 1.2kg/cm 2 (78.4 - 117.6Kpa)
5. Oil Pressure Switch Operating Pressure: 0.3 - 0.5kg/cm 2 (29.4 - 49.0Kpa)
6. Regulating Valve: 1.8 - 2.2kg/cm 2 (176 - 216Kpa)
The 4J series engine has a full flow type lubricating system.
Lubricating oil is pumped from the oil pump to the cylinder body oil gallery through the oil cooler and the oil filter. It is
then delivered to the vital parts of the engine from the cylinder body oil gallery.
Oiling jets installed on the cylinder body spray engine oil to the piston backside faces to achieve maximum piston
cooling effect.
Page 1267 of 4264
ENGINE MECHANICAL 6A – 127
OIL PUMP AND OIL FILTER
RTW46ALF001501
The 4J series engine is equipped with a gear type oil pump.
The oil filter and the water cooled oil cooler integrated a single unit to increase the cooling effect.
Page 1268 of 4264
6A – 128 ENGINE MECHANICAL
OIL PUMP
DISASSEMBLY
Disassembly Steps
1.
Oil pipe 5.
Driven gear
2.
Strainer 6. Relief valve assembly
3. Pump cover 7. Pinion gear
4. Driven gear with bushing 8. Oil pump body
Disassembly procedure is shown in the illustration above numerical order.
051R100005
Page 1269 of 4264
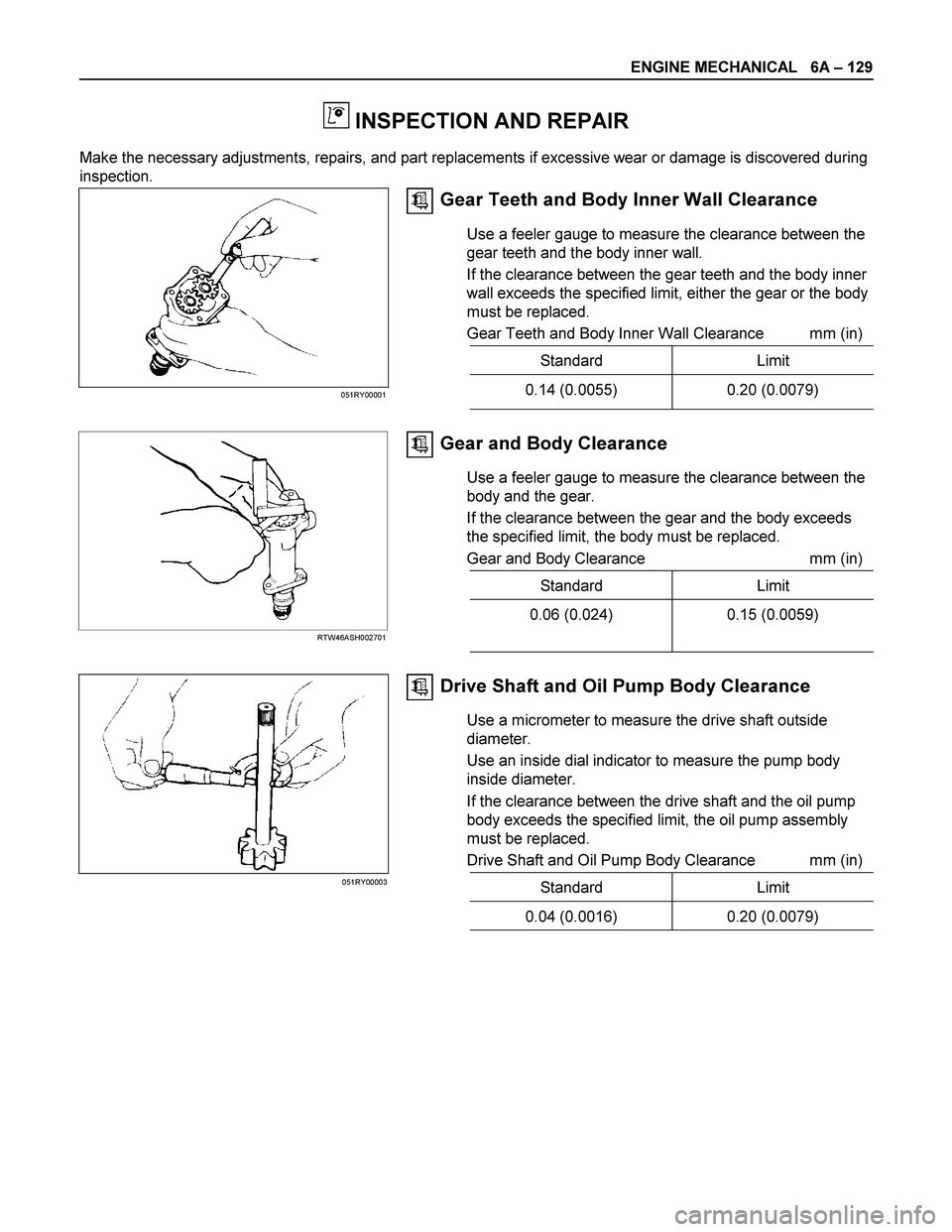
ENGINE MECHANICAL 6A – 129
INSPECTION AND REPAIR
Make the necessary adjustments, repairs, and part replacements if excessive wear or damage is discovered during
inspection.
Gear Teeth and Body Inner Wall Clearance
Use a feeler gauge to measure the clearance between the
gear teeth and the body inner wall.
If the clearance between the gear teeth and the body inner
wall exceeds the specified limit, either the gear or the body
must be replaced.
Gear Teeth and Body Inner Wall Clearance mm (in)
Standard Limit
051RY00001 0.14 (0.0055) 0.20 (0.0079)
Gear and Body Clearance
Use a feeler gauge to measure the clearance between the
body and the gear.
If the clearance between the gear and the body exceeds
the specified limit, the body must be replaced.
Gear and Body Clearance mm (in)
Standard Limit
RTW46ASH002701
0.06 (0.024) 0.15 (0.0059)
Drive Shaft and Oil Pump Body Clearance
Use a micrometer to measure the drive shaft outside
diameter.
Use an inside dial indicator to measure the pump body
inside diameter.
If the clearance between the drive shaft and the oil pump
body exceeds the specified limit, the oil pump assembly
must be replaced.
Drive Shaft and Oil Pump Body Clearance mm (in)
Standard Limit
0.04 (0.0016) 0.20 (0.0079)
051RY00003
Page 1270 of 4264
6A – 130 ENGINE MECHANICAL
REASSEMBLY
Reassembly Steps
1.
Oil pump body 5.
Pinion gear
2.
Drive gear 6. Strainer
3. Driven gear 7. Relief valve assembly
4. Pump cover 8.
Oil pipe
Reassembly procedure is shown in the illustration above numerical order.
Pump cover fixing bolts torque: 16 N·m (1.6 kg·m/12 lb ft)
051R100006
Page 1271 of 4264
ENGINE MECHANICAL 6A – 131
OIL FILTER AND OIL COOLER
DISASSEMBLY
Disassembly Steps
1.
Oil filter cartridge 5.
Body
2.
Bolt 6. Oil cooler relief valve
3. Gasket 7. Regulating valve
4. Oil cooler
Disassembly procedure is shown in the illustration above numerical order.
050R300004
Page 1272 of 4264
6A – 132 ENGINE MECHANICAL
INSPECTION AND REPAIR
Make the necessary adjustments, repairs, and part replacements if excessive wear or damage is discovered during
inspection.
Oil Cooler
Water Leakage at Water Passage
1. Plug one side of the oil cooler water passage.
2. Submerge the oil cooler in water.
3. Apply compressed air (200kPa (2kg/cm
2 / 28psi)) to
the other side of the oil cooler water passage.
If air bubbles rise to the surface, there is water leakage.
Should be replaced oil cooler assembly.
050RY00002