Page 1889 of 4264
ENGINE MECHANICAL (6VE1 3.5L) 6A-65
014RW060
2. Remove twenty fixing bolts from inlet and exhaust
camshaft bracket on one side bank, then camshaft
brackets (2).
014RW027
3. Remove camshaft assembly (3), (4).
4. Remove three fixing bolts (7) from camshaft drive
gear retainer (8), then camshaft drive gea
r
assembly.
Inspection and Repair
1. Use a micrometer to measure the cam lobe height
and uneven wear. Replace the camshaft if eithe
r
the lobe height or the uneven wear exceeds the
specified limit.
Lobe height: 44.709 mm (1.7602 in)
Uneven wear: 0.05 mm (0.0020 in)
014RW043
2. Use a micrometer to measure the diameter and
the uneven wear of the camshaft journals.
Replace the camshaft if the diameter or the
uneven wear exceeds the specified limit.
Journal Diameter
Standard: 25.972 mm
25.993 mm (1.0225
in
1.0233 in)
Limit: 25.8 mm (1.0157 in)
Uneven wear: 0.05 mm (0.0020 in)
014RS023
Page 1890 of 4264
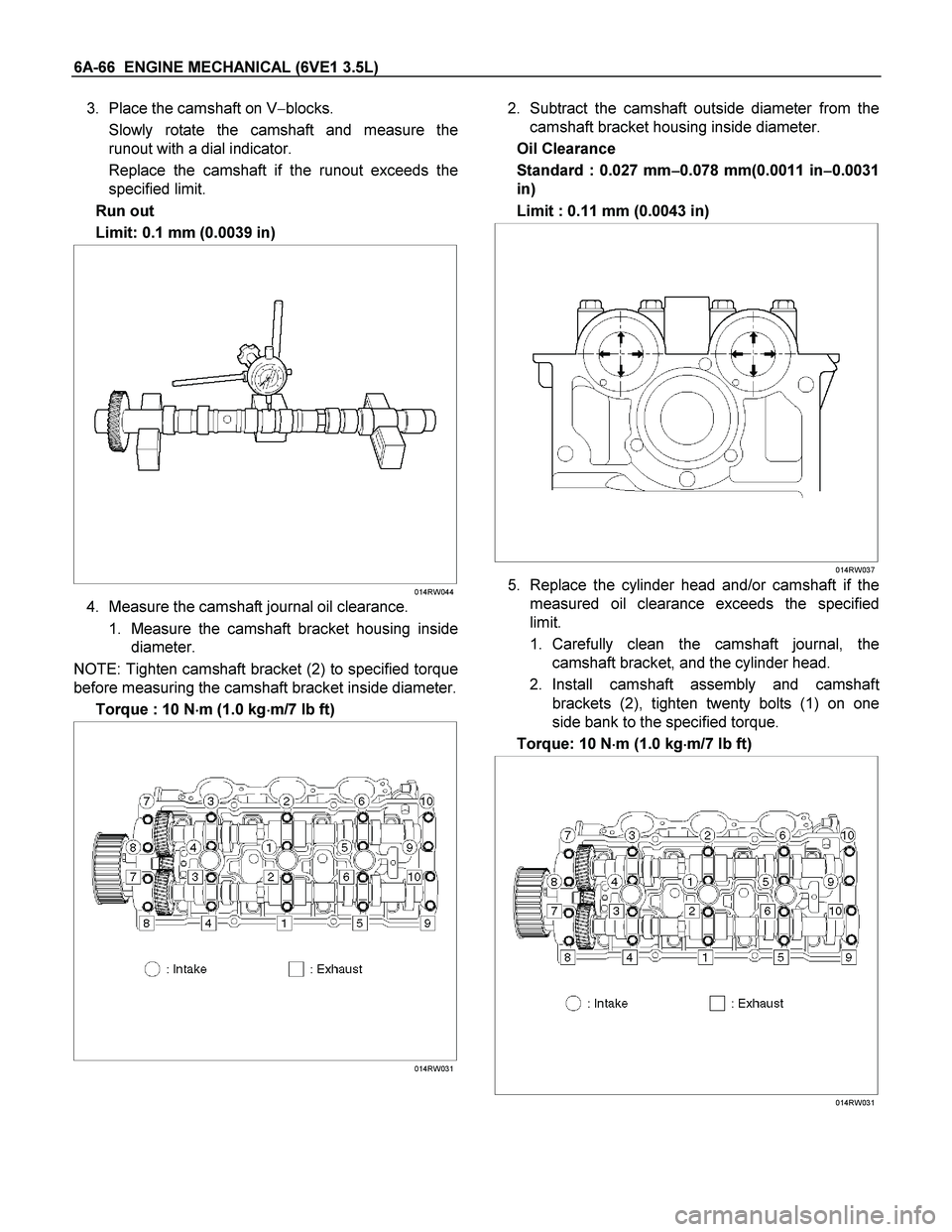
6A-66 ENGINE MECHANICAL (6VE1 3.5L)
3. Place the camshaft on Vblocks.
Slowly rotate the camshaft and measure the
runout with a dial indicator.
Replace the camshaft if the runout exceeds the
specified limit.
Run out
Limit: 0.1 mm (0.0039 in)
014RW044
4. Measure the camshaft journal oil clearance.
1. Measure the camshaft bracket housing inside
diameter.
NOTE: Tighten camshaft bracket (2) to specified torque
before measuring the camshaft bracket inside diameter.
Torque : 10 N
m (1.0 kg
m/7 lb ft)
014RW031
2. Subtract the camshaft outside diameter from the
camshaft bracket housing inside diameter.
Oil Clearance
Standard : 0.027 mm
0.078 mm(0.0011 in
0.0031
in)
Limit : 0.11 mm (0.0043 in)
014RW037
5. Replace the cylinder head and/or camshaft if the
measured oil clearance exceeds the specified
limit.
1. Carefully clean the camshaft journal, the
camshaft bracket, and the cylinder head.
2. Install camshaft assembly and camshaf
t
brackets (2), tighten twenty bolts (1) on one
side bank to the specified torque.
Torque: 10 N
m (1.0 kg
m/7 lb ft)
014RW031
Page 1891 of 4264
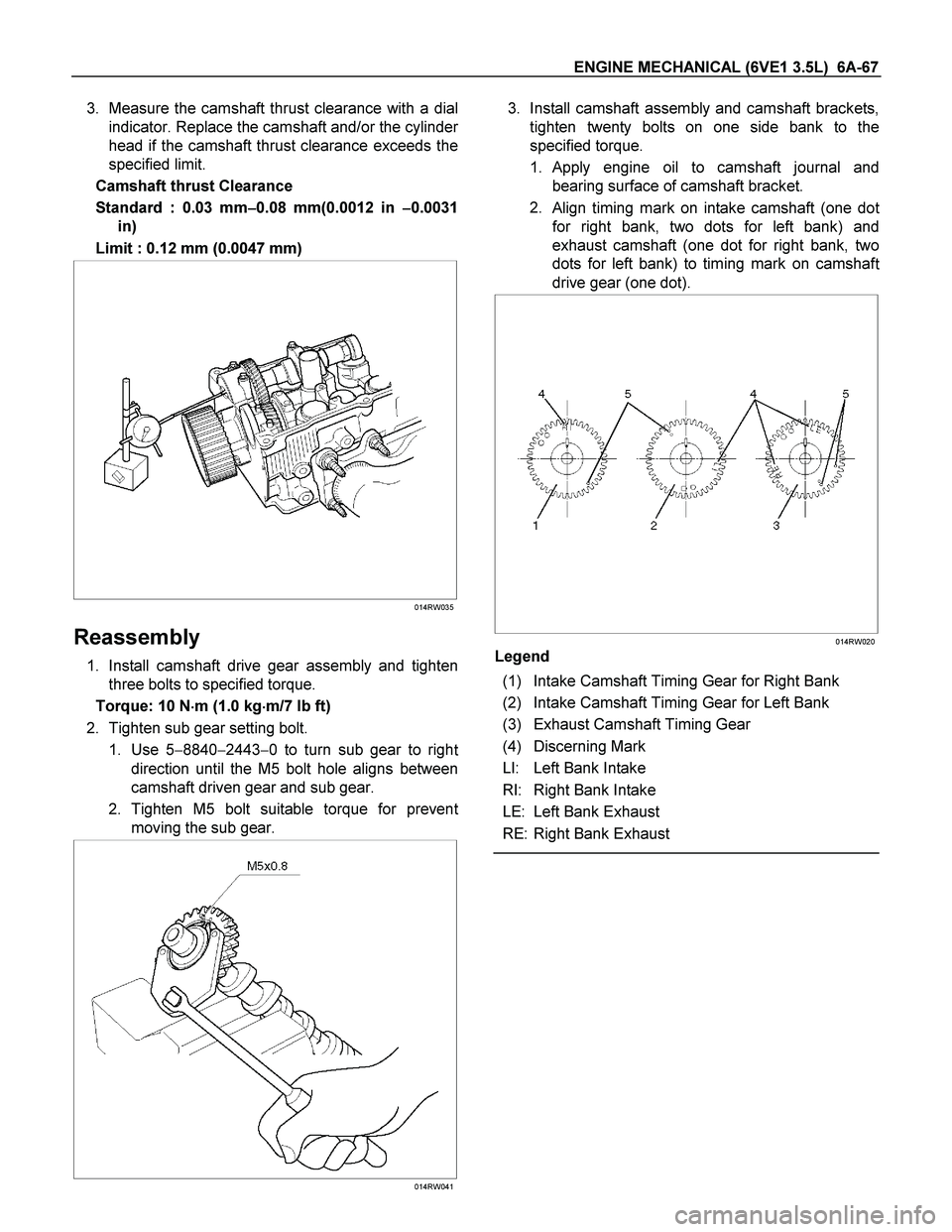
ENGINE MECHANICAL (6VE1 3.5L) 6A-67
3. Measure the camshaft thrust clearance with a dial
indicator. Replace the camshaft and/or the cylinde
r
head if the camshaft thrust clearance exceeds the
specified limit.
Camshaft thrust Clearance
Standard : 0.03 mm
0.08 mm(0.0012 in
0.0031
in)
Limit : 0.12 mm (0.0047 mm)
014RW035
Reassembly
1. Install camshaft drive gear assembly and tighten
three bolts to specified torque.
Torque: 10 N
m (1.0 kg
m/7 lb ft)
2. Tighten sub gear setting bolt.
1. Use 5884024430 to turn sub gear to righ
t
direction until the M5 bolt hole aligns between
camshaft driven gear and sub gear.
2. Tighten M5 bolt suitable torque for preven
t
moving the sub gear.
014RW041
3. Install camshaft assembly and camshaft brackets,
tighten twenty bolts on one side bank to the
specified torque.
1.
Apply engine oil to camshaft journal and
bearing surface of camshaft bracket.
2.
Align timing mark on intake camshaft (one dot
for right bank, two dots for left bank) and
exhaust camshaft (one dot for right bank, two
dots for left bank) to timing mark on camshaf
t
drive gear (one dot).
014RW020
Legend
(1) Intake Camshaft Timing Gear for Right Bank
(2) Intake Camshaft Timing Gear for Left Bank
(3) Exhaust Camshaft Timing Gear
(4) Discerning Mark
LI: Left Bank Intake
RI: Right Bank Intake
LE: Left Bank Exhaust
RE: Right Bank Exhaust
Page 1892 of 4264
6A-68 ENGINE MECHANICAL (6VE1 3.5L)
014RW023
Legend
(1) Right Bank Camshaft Drive Gear
(2) Left Bank Camshaft Drive Gear
(3) Timing Mark on Drive Gear
(4) Dowel Pin
Page 1893 of 4264
ENGINE MECHANICAL (6VE1 3.5L) 6A-69
014RW024
Legend
(1) Right Bank
(2) Left Bank
(3) Alignment Mark on Camshaft Drive Gear
(4) Alignment Mark on Camshaft
(5) Alignment Mark on Retainer
3. Tighten twenty bolts in numerical order on one
side bank as shown in the illustration.
Torque: 10 N
m (1.0 kg
m/7 lb ft)
014RW031
4. If the oil seal requires replacement, use the
5884024450 to install the oil seal.
014RW034
Page 1894 of 4264
6A-70 ENGINE MECHANICAL (6VE1 3.5L)
5. Tighten bolt for camshaft drive gear assembly
pulley to the specified torque using the
5884024470 universal holder.
Torque: 98 N
m (10.0 kg
m/72 lb ft)
014RW060
Page 1895 of 4264
ENGINE MECHANICAL (6VE1 3.5L) 6A-71
Crankshaft
Crankshaft and Associated Parts
013RW009
Legend
(1) Cylinder Head Assembly
(2) Crankcase with Oil Pan
(3) Oil Pipe and O-Ring
(4) Oil Strainer and O-Ring
(5) Oil Pump Assembly
(6) Cylinder Block Side Bolts
(7) Oil Gallery
(8) Piston and Connecting Rod Assembly
(9) Flywheel
(10) Rear Oil Seal Retainer and Oil Seal
(11) Main Bearing Cap
(12) Crankshaft
(13) Main Bearing Cap Fixing Bolts
(14) Oil Gallery Fixing Bolts
Disassembly
1. Remove cylinder head assembly (1). Refer to
“Head" in this manual. 2. Remove crankcase with oil pan (2). Refer to “Oil
Pan and Crankcase" in this manual.
CAUTION: Take care not to damage or deform the
sealing flange surface of crankcase.
Page 1896 of 4264
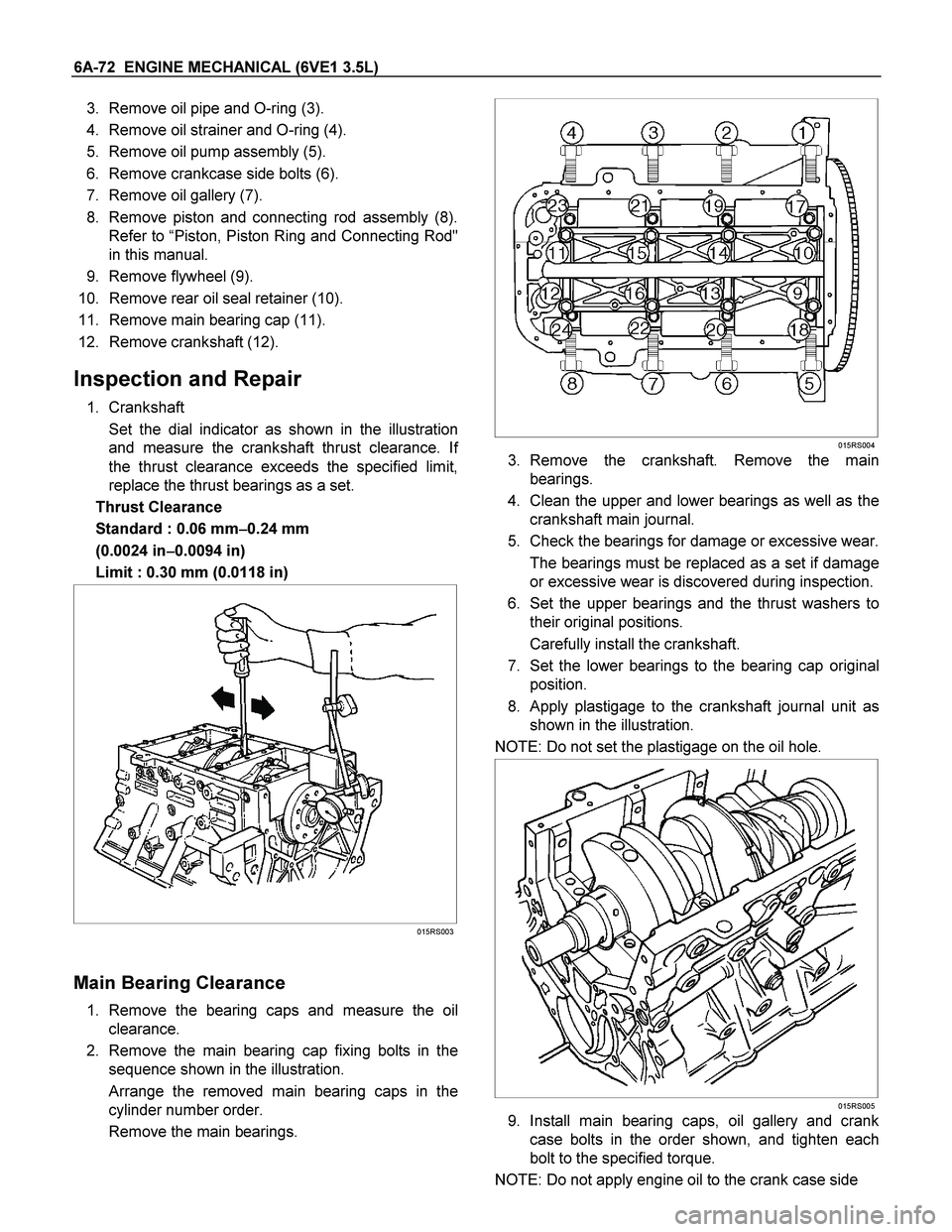
6A-72 ENGINE MECHANICAL (6VE1 3.5L)
3. Remove oil pipe and O-ring (3).
4. Remove oil strainer and O-ring (4).
5. Remove oil pump assembly (5).
6. Remove crankcase side bolts (6).
7. Remove oil gallery (7).
8. Remove piston and connecting rod assembly (8).
Refer to “Piston, Piston Ring and Connecting Rod"
in this manual.
9. Remove flywheel (9).
10. Remove rear oil seal retainer (10).
11. Remove main bearing cap (11).
12. Remove crankshaft (12).
Inspection and Repair
1. Crankshaft
Set the dial indicator as shown in the illustration
and measure the crankshaft thrust clearance. I
f
the thrust clearance exceeds the specified limit,
replace the thrust bearings as a set.
Thrust Clearance
Standard : 0.06 mm
0.24 mm
(0.0024 in
0.0094 in)
Limit : 0.30 mm (0.0118 in)
015RS003
Main Bearing Clearance
1. Remove the bearing caps and measure the oil
clearance.
2. Remove the main bearing cap fixing bolts in the
sequence shown in the illustration.
Arrange the removed main bearing caps in the
cylinder number order.
Remove the main bearings.
015RS004
3. Remove the crankshaft. Remove the main
bearings.
4. Clean the upper and lower bearings as well as the
crankshaft main journal.
5. Check the bearings for damage or excessive wear.
The bearings must be replaced as a set if damage
or excessive wear is discovered during inspection.
6. Set the upper bearings and the thrust washers to
their original positions.
Carefully install the crankshaft.
7. Set the lower bearings to the bearing cap original
position.
8.
Apply plastigage to the crankshaft journal unit as
shown in the illustration.
NOTE: Do not set the plastigage on the oil hole.
015RS005
9. Install main bearing caps, oil gallery and crank
case bolts in the order shown, and tighten each
bolt to the specified torque.
NOTE: Do not apply engine oil to the crank case side