Page 25 of 4264
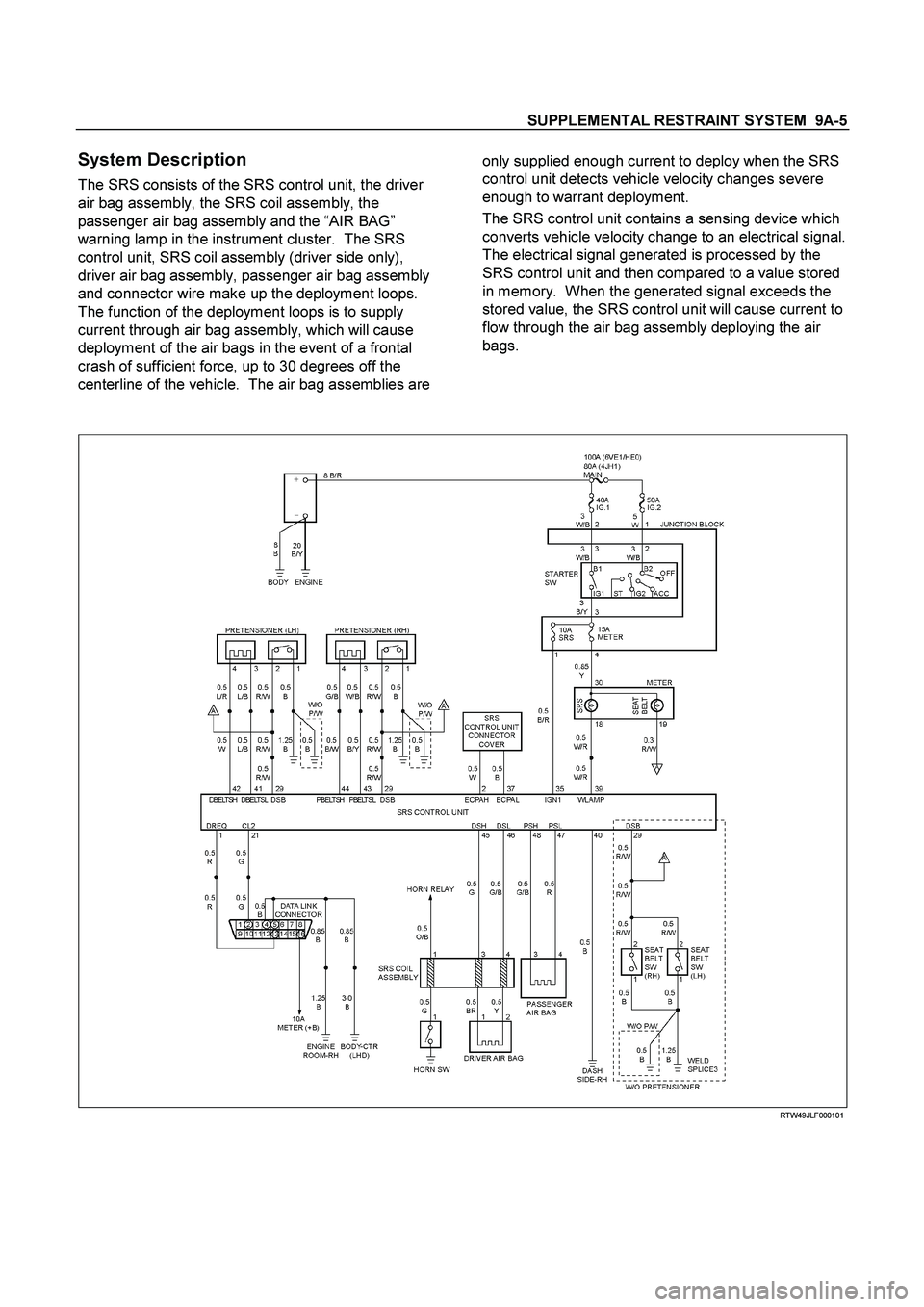
SUPPLEMENTAL RESTRAINT SYSTEM 9A-5
System Description
The SRS consists of the SRS control unit, the driver
air bag assembly, the SRS coil assembly, the
passenger air bag assembly and the “AIR BAG”
warning lamp in the instrument cluster. The SRS
control unit, SRS coil assembly (driver side only),
driver air bag assembly, passenger air bag assembly
and connector wire make up the deployment loops.
The function of the deployment loops is to supply
current through air bag assembly, which will cause
deployment of the air bags in the event of a frontal
crash of sufficient force, up to 30 degrees off the
centerline of the vehicle. The air bag assemblies are
only supplied enough current to deploy when the SRS
control unit detects vehicle velocity changes severe
enough to warrant deployment.
The SRS control unit contains a sensing device which
converts vehicle velocity change to an electrical signal.
The electrical signal generated is processed by the
SRS control unit and then compared to a value stored
in memory. When the generated signal exceeds the
stored value, the SRS control unit will cause current to
flow through the air bag assembly deploying the air
bags.
RTW49JLF000101
Page 26 of 4264
9A-6 SUPPLEMENTAL RESTRAINT SYSTEM
SRS Component And Wiring Location View - RHD
RTW49JMF000301
Page 27 of 4264
SUPPLEMENTAL RESTRAINT SYSTEM 9A-7
SRS Component And Wiring Location View - LHD
RTW49JMF000401
Page 28 of 4264
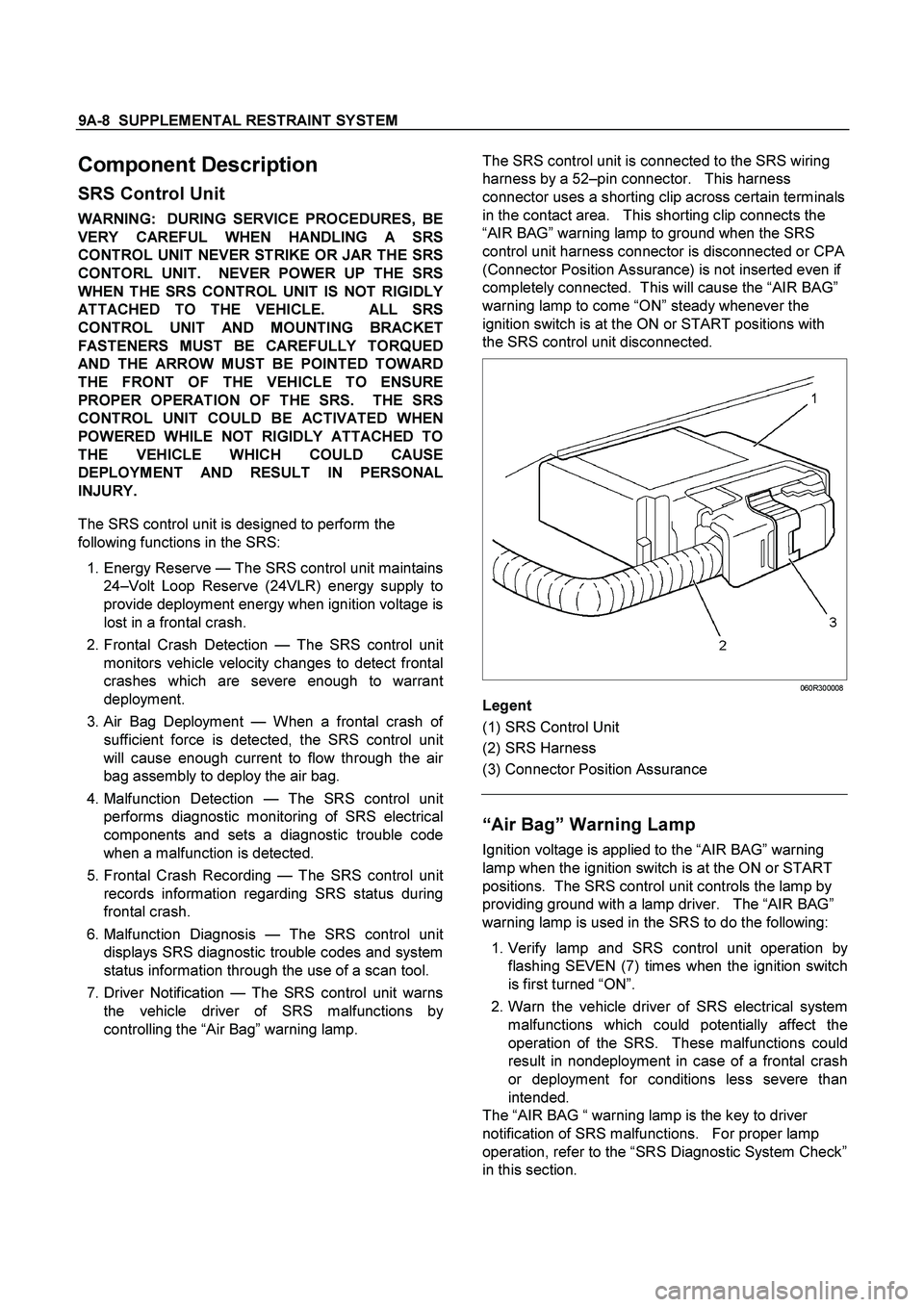
9A-8 SUPPLEMENTAL RESTRAINT SYSTEM
The SRS control unit is connected to the SRS wiring
harness by a 52–pin connector. This harness
connector uses a shorting clip across certain terminals
in the contact area. This shorting clip connects the
“AIR BAG” warning lamp to ground when the SRS
control unit harness connector is disconnected or CPA
(Connector Position Assurance) is not inserted even if
completely connected. This will cause the “AIR BAG”
warning lamp to come “ON” steady whenever the
ignition switch is at the ON or START positions with
the SRS control unit disconnected.
060R300008
Legent
(1) SRS Control Unit
(2) SRS Harness
(3) Connector Position Assurance
Component Description
SRS Control Unit
WARNING: DURING SERVICE PROCEDURES, BE
VERY CAREFUL WHEN HANDLING A SRS
CONTROL UNIT NEVER STRIKE OR JAR THE SRS
CONTORL UNIT. NEVER POWER UP THE SRS
WHEN THE SRS CONTROL UNIT IS NOT RIGIDLY
ATTACHED TO THE VEHICLE. ALL SRS
CONTROL UNIT AND MOUNTING BRACKET
FASTENERS MUST BE CAREFULLY TORQUED
AND THE ARROW MUST BE POINTED TOWARD
THE FRONT OF THE VEHICLE TO ENSURE
PROPER OPERATION OF THE SRS. THE SRS
CONTROL UNIT COULD BE ACTIVATED WHEN
POWERED WHILE NOT RIGIDLY ATTACHED TO
THE VEHICLE WHICH COULD CAUSE
DEPLOYMENT AND RESULT IN PERSONAL
INJURY.
The SRS control unit is designed to perform the
following functions in the SRS:
1. Energy Reserve — The SRS control unit maintains
24–
Volt Loop Reserve (24VLR) energy supply to
provide deployment energy when ignition voltage is
lost in a frontal crash.
2. Frontal Crash Detection — The SRS control uni
t
monitors vehicle velocity changes to detect frontal
crashes which are severe enough to warran
t
deployment.
3. Air Bag Deployment — When a frontal crash o
f
sufficient force is detected, the SRS control unit
will cause enough current to flow through the air
bag assembly to deploy the air bag.
4. Malfunction Detection —The SRS control uni
t
performs diagnostic monitoring of SRS electrical
components and sets a diagnostic trouble code
when a malfunction is detected.
5. Frontal Crash Recording — The SRS control uni
t
records information regarding SRS status during
frontal crash.
6. Malfunction Diagnosis —The SRS control uni
t
displays SRS diagnostic trouble codes and system
status information through the use of a scan tool.
7. Driver Notification — The SRS control unit warns
the vehicle driver of SRS malfunctions b
y
controlling the “Air Bag” warning lamp.
“Air Bag” Warning Lamp
Ignition voltage is applied to the “AIR BAG” warning
lamp when the ignition switch is at the ON or START
positions. The SRS control unit controls the lamp by
providing ground with a lamp driver. The “AIR BAG”
warning lamp is used in the SRS to do the following:
1.
Verify lamp and SRS control unit operation by
flashing SEVEN (7) times when the ignition switch
is first turned “ON”.
2. Warn the vehicle driver of SRS electrical system
malfunctions which could potentially affect the
operation of the SRS. These malfunctions could
result in nondeployment in case of a frontal crash
or deployment for conditions less severe than
intended.
The “AIR BAG “ warning lamp is the key to driver
notification of SRS malfunctions. For proper lamp
operation, refer to the “SRS Diagnostic System Check”
in this section.
Page 29 of 4264
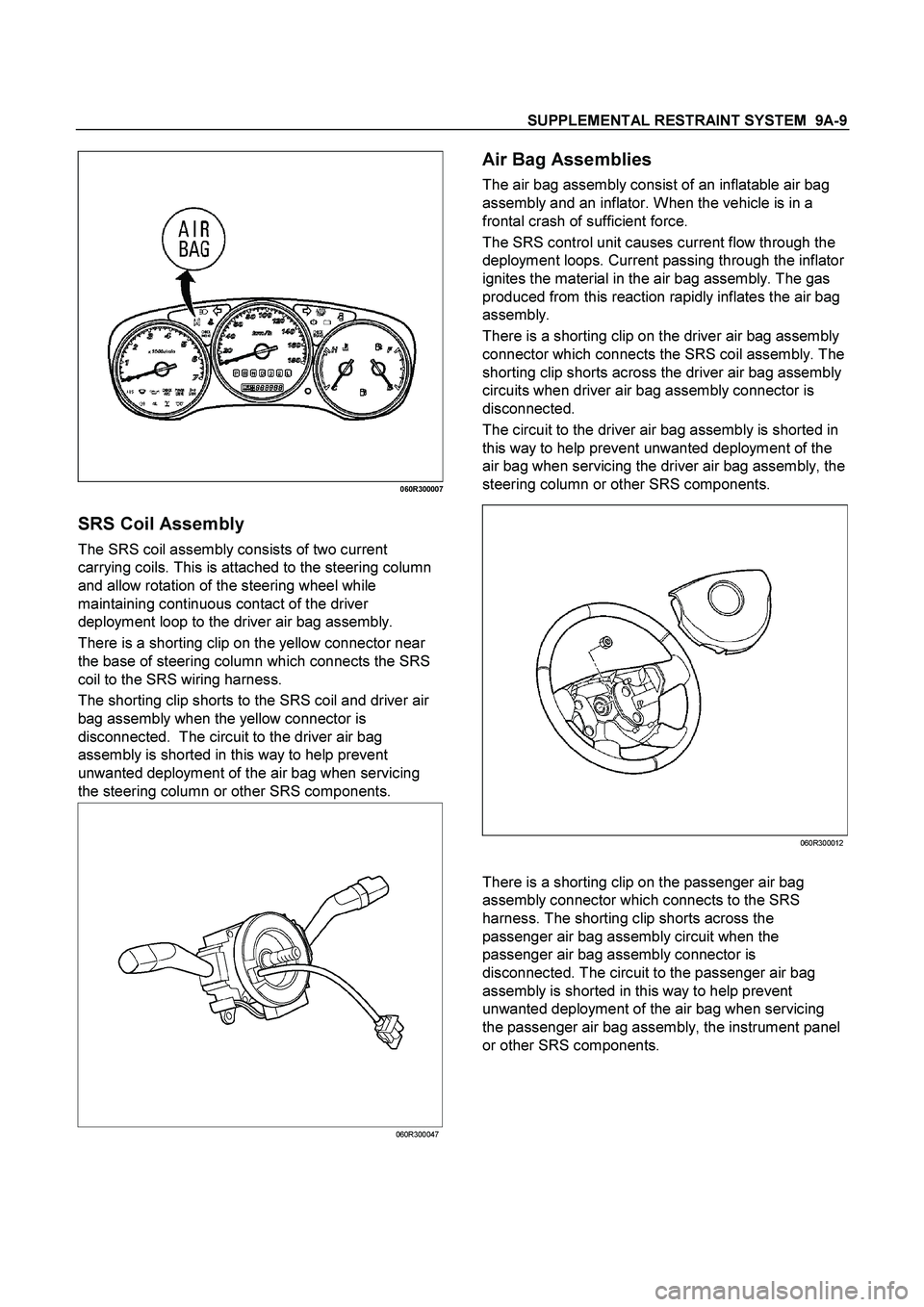
SUPPLEMENTAL RESTRAINT SYSTEM 9A-9
060R300007
SRS Coil Assembly
The SRS coil assembly consists of two current
carrying coils. This is attached to the steering column
and allow rotation of the steering wheel while
maintaining continuous contact of the driver
deployment loop to the driver air bag assembly.
There is a shorting clip on the yellow connector near
the base of steering column which connects the SRS
coil to the SRS wiring harness.
The shorting clip shorts to the SRS coil and driver air
bag assembly when the yellow connector is
disconnected. The circuit to the driver air bag
assembly is shorted in this way to help prevent
unwanted deployment of the air bag when servicing
the steering column or other SRS components.
060R300047
Air Bag Assemblies
The air bag assembly consist of an inflatable air bag
assembly and an inflator. When the vehicle is in a
frontal crash of sufficient force.
The SRS control unit causes current flow through the
deployment loops. Current passing through the inflator
ignites the material in the air bag assembly. The gas
produced from this reaction rapidly inflates the air bag
assembly.
There is a shorting clip on the driver air bag assembly
connector which connects the SRS coil assembly. The
shorting clip shorts across the driver air bag assembly
circuits when driver air bag assembly connector is
disconnected.
The circuit to the driver air bag assembly is shorted in
this way to help prevent unwanted deployment of the
air bag when servicing the driver air bag assembly, the
steering column or other SRS components.
060R300012
There is a shorting clip on the passenger air bag
assembly connector which connects to the SRS
harness. The shorting clip shorts across the
passenger air bag assembly circuit when the
passenger air bag assembly connector is
disconnected. The circuit to the passenger air bag
assembly is shorted in this way to help prevent
unwanted deployment of the air bag when servicing
the passenger air bag assembly, the instrument panel
or other SRS components.
Page 30 of 4264
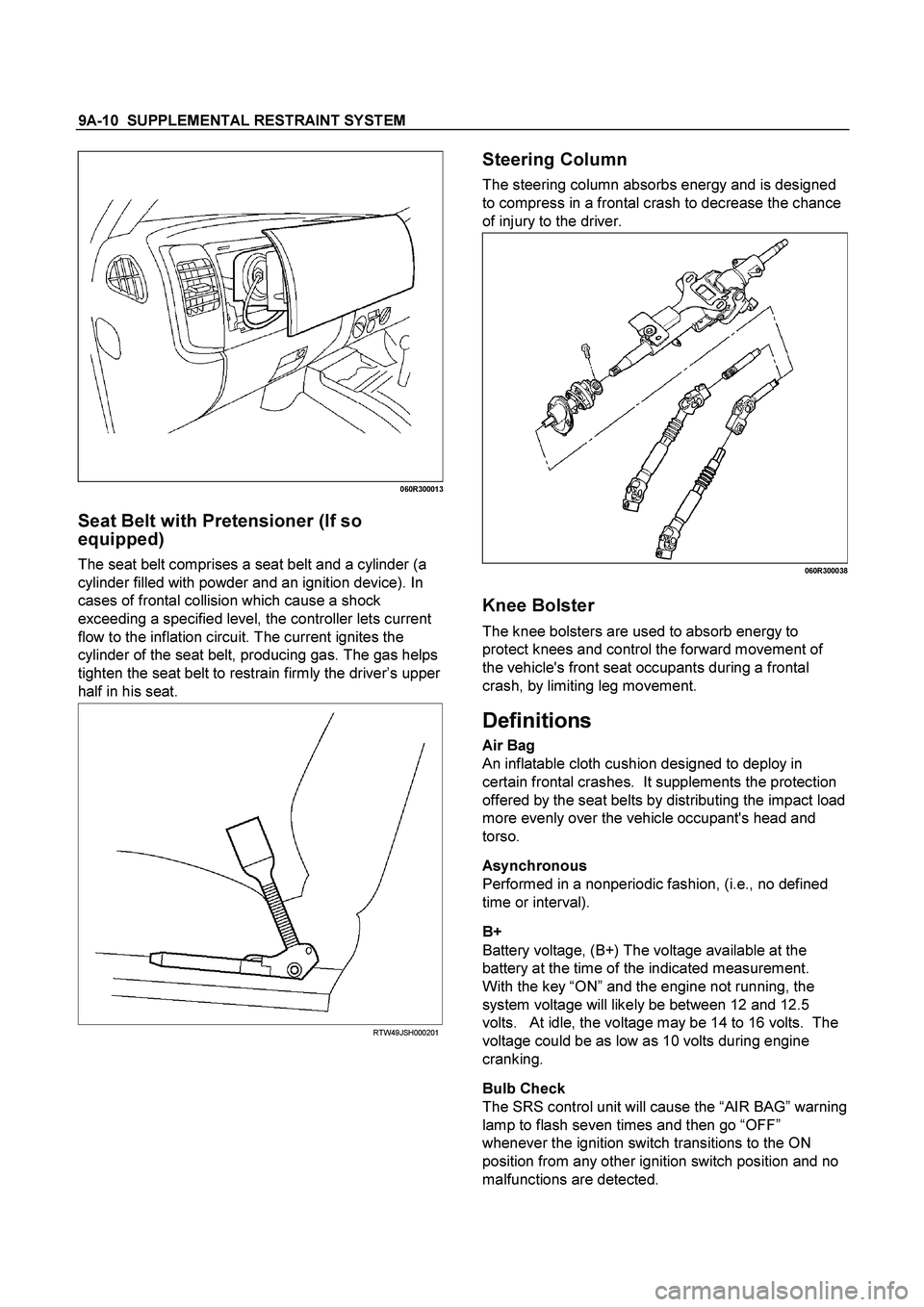
9A-10 SUPPLEMENTAL RESTRAINT SYSTEM
060R300013
Seat Belt with Pretensioner (If so
equipped)
The seat belt comprises a seat belt and a cylinder (a
cylinder filled with powder and an ignition device). In
cases of frontal collision which cause a shock
exceeding a specified level, the controller lets current
flow to the inflation circuit. The current ignites the
cylinder of the seat belt, producing gas. The gas helps
tighten the seat belt to restrain firmly the driver’s upper
half in his seat.
RTW49JSH000201
Steering Column
The steering column absorbs energy and is designed
to compress in a frontal crash to decrease the chance
of injury to the driver.
060R300038
Knee Bolster
The knee bolsters are used to absorb energy to
protect knees and control the forward movement of
the vehicle's front seat occupants during a frontal
crash, by limiting leg movement.
Definitions
Air Bag
An inflatable cloth cushion designed to deploy in
certain frontal crashes. It supplements the protection
offered by the seat belts by distributing the impact load
more evenly over the vehicle occupant's head and
torso.
Asynchronous
Performed in a nonperiodic fashion, (i.e., no defined
time or interval).
B+
Battery voltage, (B+) The voltage available at the
battery at the time of the indicated measurement.
With the key “ON” and the engine not running, the
system voltage will likely be between 12 and 12.5
volts. At idle, the voltage may be 14 to 16 volts. The
voltage could be as low as 10 volts during engine
cranking.
Bulb Check
The SRS control unit will cause the “AIR BAG” warning
lamp to flash seven times and then go “OFF”
whenever the ignition switch transitions to the ON
position from any other ignition switch position and no
malfunctions are detected.
Page 31 of 4264
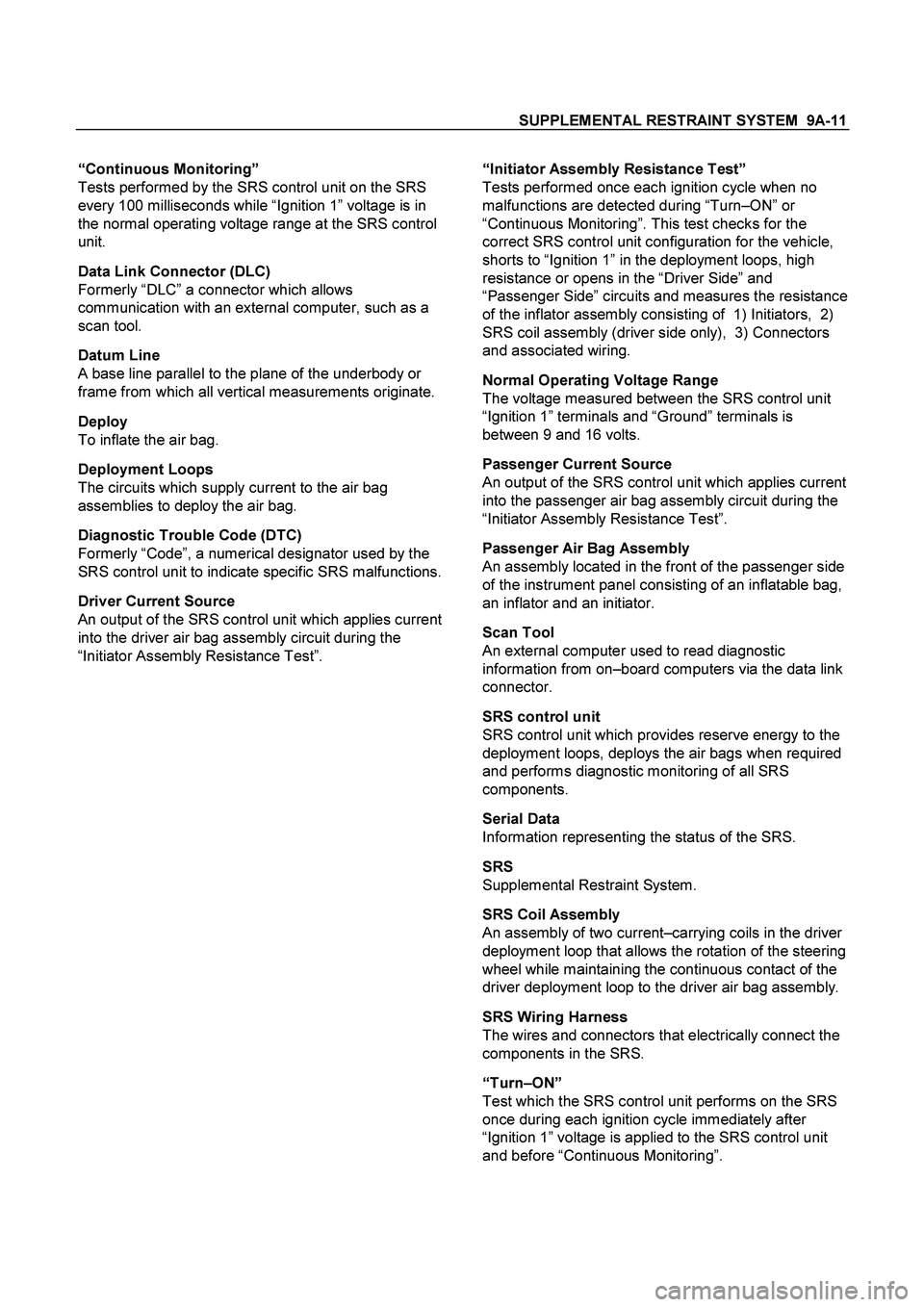
SUPPLEMENTAL RESTRAINT SYSTEM 9A-11
“Continuous Monitoring”
Tests performed by the SRS control unit on the SRS
every 100 milliseconds while “Ignition 1” voltage is in
the normal operating voltage range at the SRS control
unit.
Data Link Connector (DLC)
Formerly “DLC” a connector which allows
communication with an external computer, such as a
scan tool.
Datum Line
A base line parallel to the plane of the underbody or
frame from which all vertical measurements originate.
Deploy
To inflate the air bag.
Deployment Loops
The circuits which supply current to the air bag
assemblies to deploy the air bag.
Diagnostic Trouble Code (DTC)
Formerly “Code”, a numerical designator used by the
SRS control unit to indicate specific SRS malfunctions.
Driver Current Source
An output of the SRS control unit which applies current
into the driver air bag assembly circuit during the
“Initiator Assembly Resistance Test”.
“Initiator Assembly Resistance Test”
Tests performed once each ignition cycle when no
malfunctions are detected during “Turn–ON” or
“Continuous Monitoring”. This test checks for the
correct SRS control unit configuration for the vehicle,
shorts to “Ignition 1” in the deployment loops, high
resistance or opens in the “Driver Side” and
“Passenger Side” circuits and measures the resistance
of the inflator assembly consisting of 1) Initiators, 2)
SRS coil assembly (driver side only), 3) Connectors
and associated wiring.
Normal Operating Voltage Range
The voltage measured between the SRS control unit
“Ignition 1” terminals and “Ground” terminals is
between 9 and 16 volts.
Passenger Current Source
An output of the SRS control unit which applies current
into the passenger air bag assembly circuit during the
“Initiator Assembly Resistance Test”.
Passenger Air Bag Assembly
An assembly located in the front of the passenger side
of the instrument panel consisting of an inflatable bag,
an inflator and an initiator.
Scan Tool
An external computer used to read diagnostic
information from on–board computers via the data link
connector.
SRS control unit
SRS control unit which provides reserve energy to the
deployment loops, deploys the air bags when required
and performs diagnostic monitoring of all SRS
components.
Serial Data
Information representing the status of the SRS.
SRS
Supplemental Restraint System.
SRS Coil Assembly
An assembly of two current–carrying coils in the driver
deployment loop that allows the rotation of the steering
wheel while maintaining the continuous contact of the
driver deployment loop to the driver air bag assembly.
SRS Wiring Harness
The wires and connectors that electrically connect the
components in the SRS.
“Turn–ON”
Test which the SRS control unit performs on the SRS
once during each ignition cycle immediately after
“Ignition 1” voltage is applied to the SRS control unit
and before “Continuous Monitoring”.
Page 32 of 4264
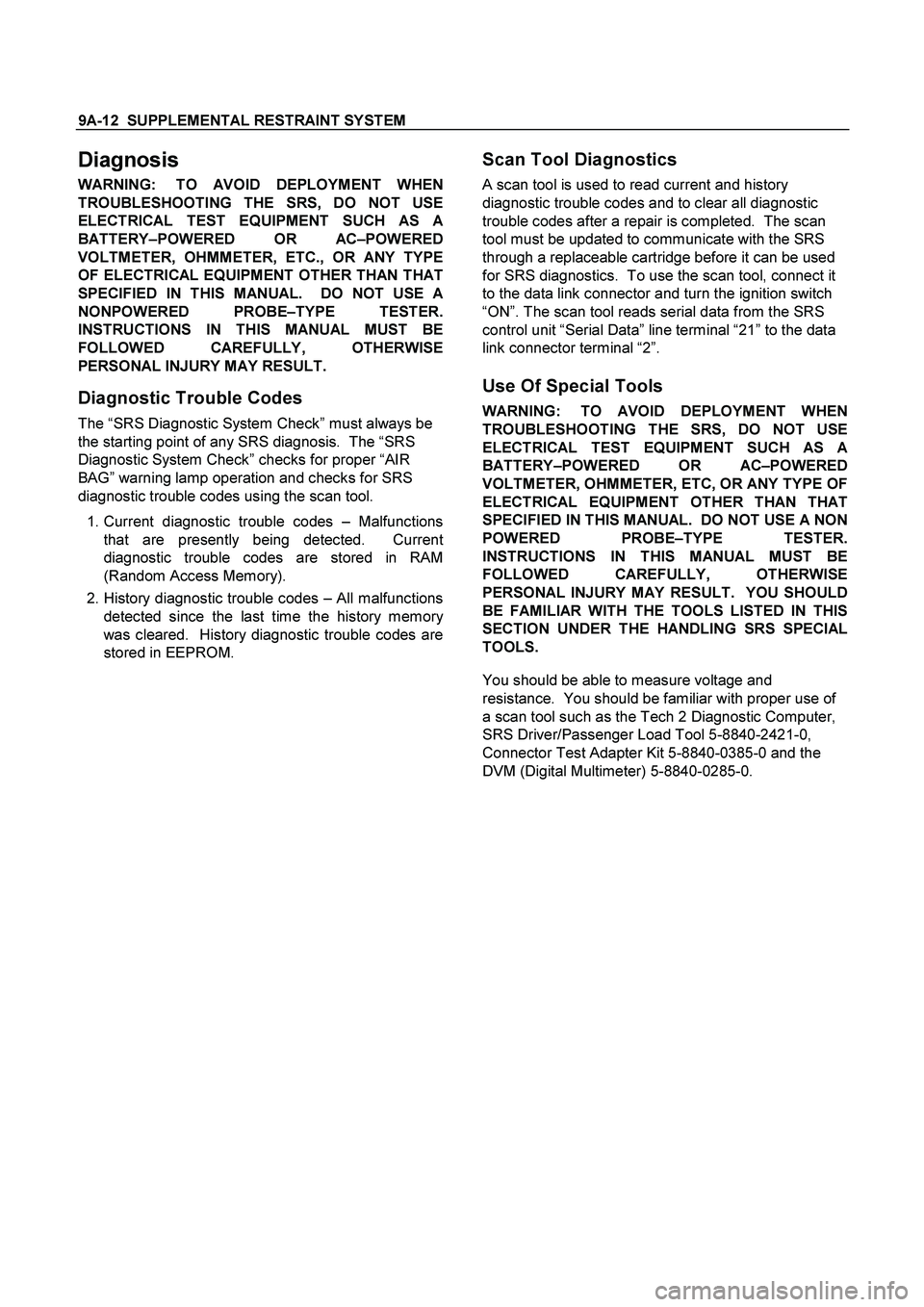
9A-12 SUPPLEMENTAL RESTRAINT SYSTEM
Diagnosis
WARNING: TO AVOID DEPLOYMENT WHEN
TROUBLESHOOTING THE SRS, DO NOT USE
ELECTRICAL TEST EQUIPMENT SUCH AS A
BATTERY–POWERED OR AC–POWERED
VOLTMETER, OHMMETER, ETC., OR ANY TYPE
OF ELECTRICAL EQUIPMENT OTHER THAN THAT
SPECIFIED IN THIS MANUAL. DO NOT USE A
NONPOWERED PROBE–TYPE TESTER.
INSTRUCTIONS IN THIS MANUAL MUST BE
FOLLOWED CAREFULLY, OTHERWISE
PERSONAL INJURY MAY RESULT.
Diagnostic Trouble Codes
The “SRS Diagnostic System Check” must always be
the starting point of any SRS diagnosis. The “SRS
Diagnostic System Check” checks for proper “AIR
BAG” warning lamp operation and checks for SRS
diagnostic trouble codes using the scan tool.
1. Current diagnostic trouble codes – Malfunctions
that are presently being detected. Curren
t
diagnostic trouble codes are stored in RAM
(Random Access Memory).
2. History diagnostic trouble codes – All malfunctions
detected since the last time the history memor
y
was cleared. History diagnostic trouble codes are
stored in EEPROM.
Scan Tool Diagnostics
A scan tool is used to read current and history
diagnostic trouble codes and to clear all diagnostic
trouble codes after a repair is completed. The scan
tool must be updated to communicate with the SRS
through a replaceable cartridge before it can be used
for SRS diagnostics. To use the scan tool, connect it
to the data link connector and turn the ignition switch
“ON”. The scan tool reads serial data from the SRS
control unit “Serial Data” line terminal “21” to the data
link connector terminal “2”.
Use Of Special Tools
WARNING: TO AVOID DEPLOYMENT WHEN
TROUBLESHOOTING THE SRS, DO NOT USE
ELECTRICAL TEST EQUIPMENT SUCH AS A
BATTERY–POWERED OR AC–POWERED
VOLTMETER, OHMMETER, ETC, OR ANY TYPE OF
ELECTRICAL EQUIPMENT OTHER THAN THAT
SPECIFIED IN THIS MANUAL. DO NOT USE A NON
POWERED PROBE–TYPE TESTER.
INSTRUCTIONS IN THIS MANUAL MUST BE
FOLLOWED CAREFULLY, OTHERWISE
PERSONAL INJURY MAY RESULT. YOU SHOULD
BE FAMILIAR WITH THE TOOLS LISTED IN THIS
SECTION UNDER THE HANDLING SRS SPECIAL
TOOLS.
You should be able to measure voltage and
resistance. You should be familiar with proper use of
a scan tool such as the Tech 2 Diagnostic Computer,
SRS Driver/Passenger Load Tool 5-8840-2421-0,
Connector Test Adapter Kit 5-8840-0385-0 and the
DVM (Digital Multimeter) 5-8840-0285-0.