Page 1169 of 4264
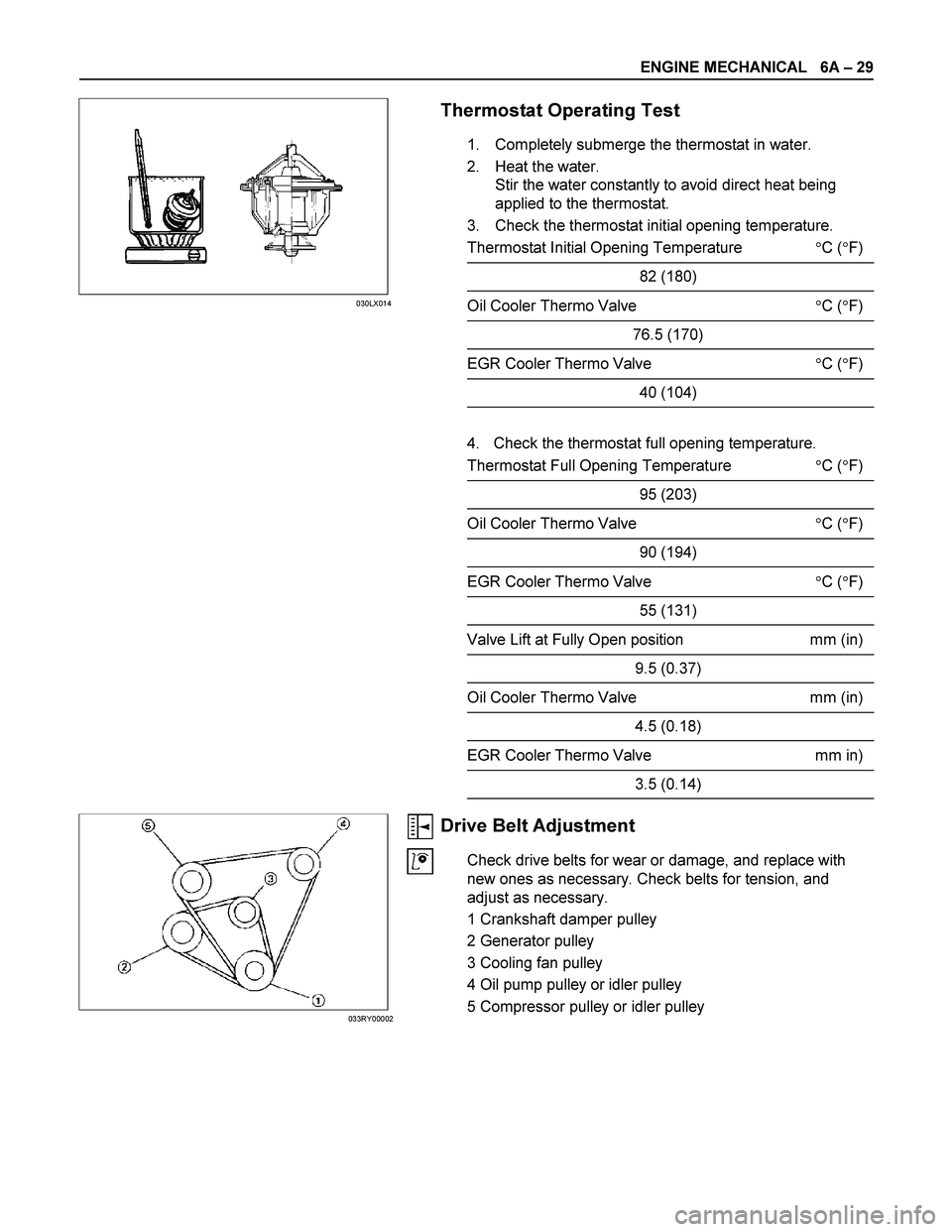
ENGINE MECHANICAL 6A – 29
Thermostat Operating Test
1. Completely submerge the thermostat in water.
2. Heat the water.
Stir the water constantly to avoid direct heat being
applied to the thermostat.
3. Check the thermostat initial opening temperature.
Thermostat Initial Opening Temperature C (F)
82 (180)
Oil Cooler Thermo Valve C (F)
76.5 (170)
EGR Cooler Thermo Valve C (F)
40 (104)
4. Check the thermostat full opening temperature.
Thermostat Full Opening Temperature C (F)
95 (203)
Oil Cooler Thermo Valve C (F)
90 (194)
EGR Cooler Thermo Valve C (F)
55 (131)
Valve Lift at Fully Open position mm (in)
9.5 (0.37)
Oil Cooler Thermo Valve mm (in)
4.5 (0.18)
EGR Cooler Thermo Valve mm in)
3.5 (0.14)
Drive Belt Adjustment
Check drive belts for wear or damage, and replace with
new ones as necessary. Check belts for tension, and
adjust as necessary.
1 Crankshaft damper pulley
2 Generator pulley
3 Cooling fan pulley
4 Oil pump pulley or idler pulley
5 Compressor pulley or idler pulley
030LX014
033RY00002
Page 1170 of 4264
6A – 30 ENGINE MECHANICAL
Cooling Fan Pulley Drive Belt
Fan belt tension is adjusted by moving the generator.
Depress the drive belt mid-portion with a 98N (10 kg/22 lb)
force.
Cooling Fan Drive Belt Deflection mm (in)
New belt 4 - 7 (0.16 - 0.28)
Reuse belt 6 - 9 (0.24 - 0.35)
1 Crankshaft damper pulley
2 Generator pulley
3 Cooling fan pulley
A/C Compressor Drive Belt
Compressor belt tension is adjusted by moving the P/S
pumppulley.
Depress the drive belt mid-portion with a 98N (10 kg/22 Ib)
force.
A/C Compressor Drive Belt Deflection mm (in)
New belt 9 - 10 (0.35 - 0.39)
Reuse belt 12 - 13 (0.47 - 0.51)
1 Crankshaft damper pulley
2 P/S pump pulley
2 A/C Compressor pulley
033RY00003
033RY00004
Page 1171 of 4264
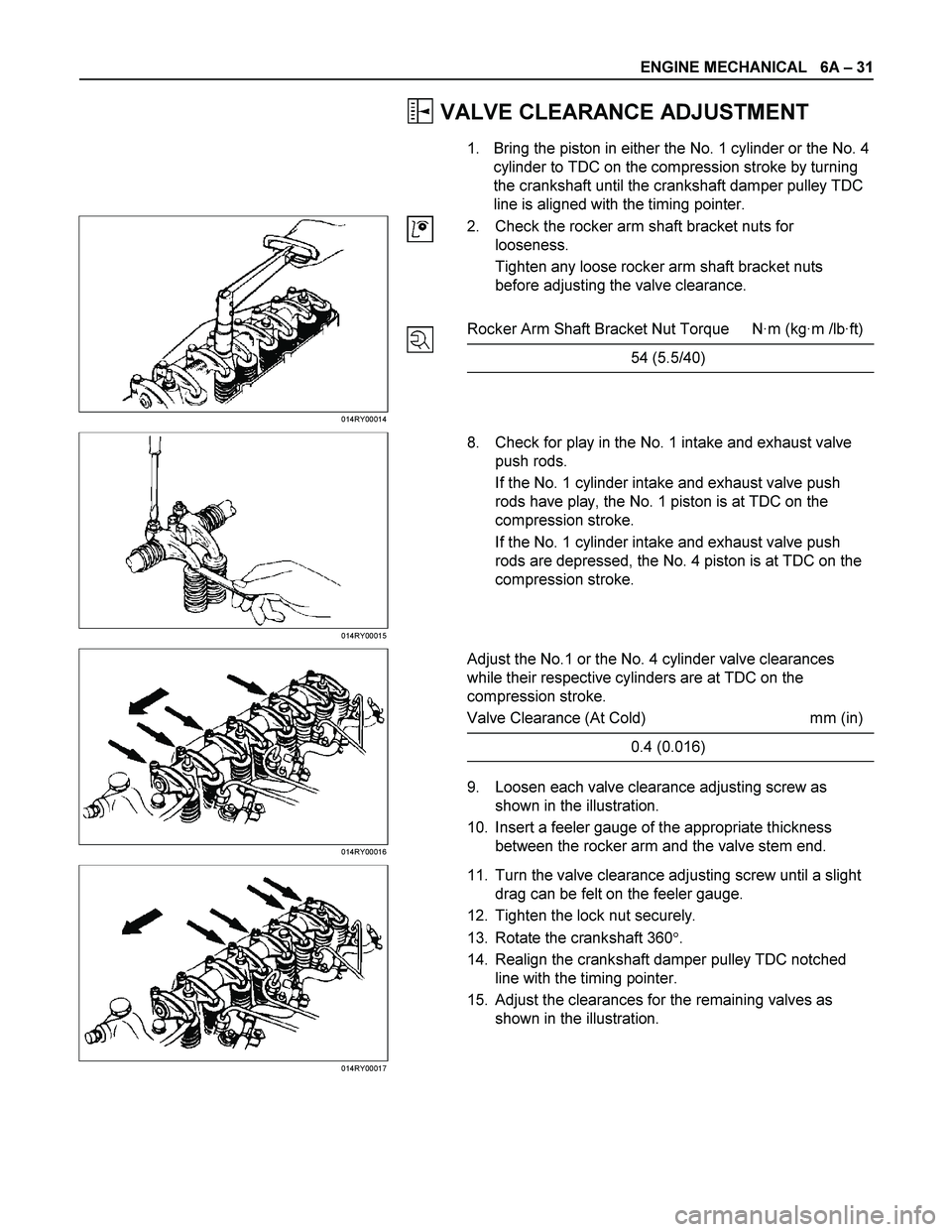
ENGINE MECHANICAL 6A – 31
VALVE CLEARANCE ADJUSTMENT
1. Bring the piston in either the No. 1 cylinder or the No. 4
cylinder to TDC on the compression stroke by turning
the crankshaft until the crankshaft damper pulley TDC
line is aligned with the timing pointer.
014RY00014
2. Check the rocker arm shaft bracket nuts for
looseness.
Tighten any loose rocker arm shaft bracket nuts
before adjusting the valve clearance.
Rocker Arm Shaft Bracket Nut Torque N·m (kg·m /lb·ft)
54 (5.5/40)
014RY00015
8. Check for play in the No. 1 intake and exhaust valve
push rods.
If the No. 1 cylinder intake and exhaust valve push
rods have play, the No. 1 piston is at TDC on the
compression stroke.
If the No. 1 cylinder intake and exhaust valve push
rods are depressed, the No. 4 piston is at TDC on the
compression stroke.
014RY00016
Adjust the No.1 or the No. 4 cylinder valve clearances
while their respective cylinders are at TDC on the
compression stroke.
Valve Clearance (At Cold) mm (in)
0.4 (0.016)
9. Loosen each valve clearance adjusting screw as
shown in the illustration.
10. Insert a feeler gauge of the appropriate thickness
between the rocker arm and the valve stem end.
014RY00017
11. Turn the valve clearance adjusting screw until a slight
drag can be felt on the feeler gauge.
12. Tighten the lock nut securely.
13. Rotate the crankshaft 360.
14. Realign the crankshaft damper pulley TDC notched
line with the timing pointer.
15. Adjust the clearances for the remaining valves as
shown in the illustration.
Page 1172 of 4264
6A – 32 ENGINE MECHANICAL
COMPRESSION PRESSURE
MEASUREMENT
1. Start the engine and allow it to idle until the coolant
temperature reaches 70 – 80 C (158 – 176 F).
2. Remove the following parts.
Leak off pipe
Injection nozzle holder bracket
Injection nozzle holder
3. Install the following parts.
Set the adapter and compression gauge (SST) to
the No.1 cylinder injection nozzle hole.
Injection nozzle holder bracket
Injection nozzle holder bracket Bolt Torque
N·m (kg·m /lb·ft)
37 (3.8/27)
Compression Gauge: 5-8840-2675-0
Adapter; Compression Gauge: 5-8531-7001-0
4. Turn the engine over with the starter motor and take
the compression gauge reading.
Compression Pressure MPa (kg/cm
2 /psi) at 200 rpm
Standard Limit
3.0 (31.0/441) 2.1 (21.7/309)
5. Repeat the procedure (Steps 3 and 4) for the
remaining cylinders.
If the measured value is less than the specified limit,
refer to “Troubleshooting” in this Manual.
F06XL056
901R100003
Page 1173 of 4264
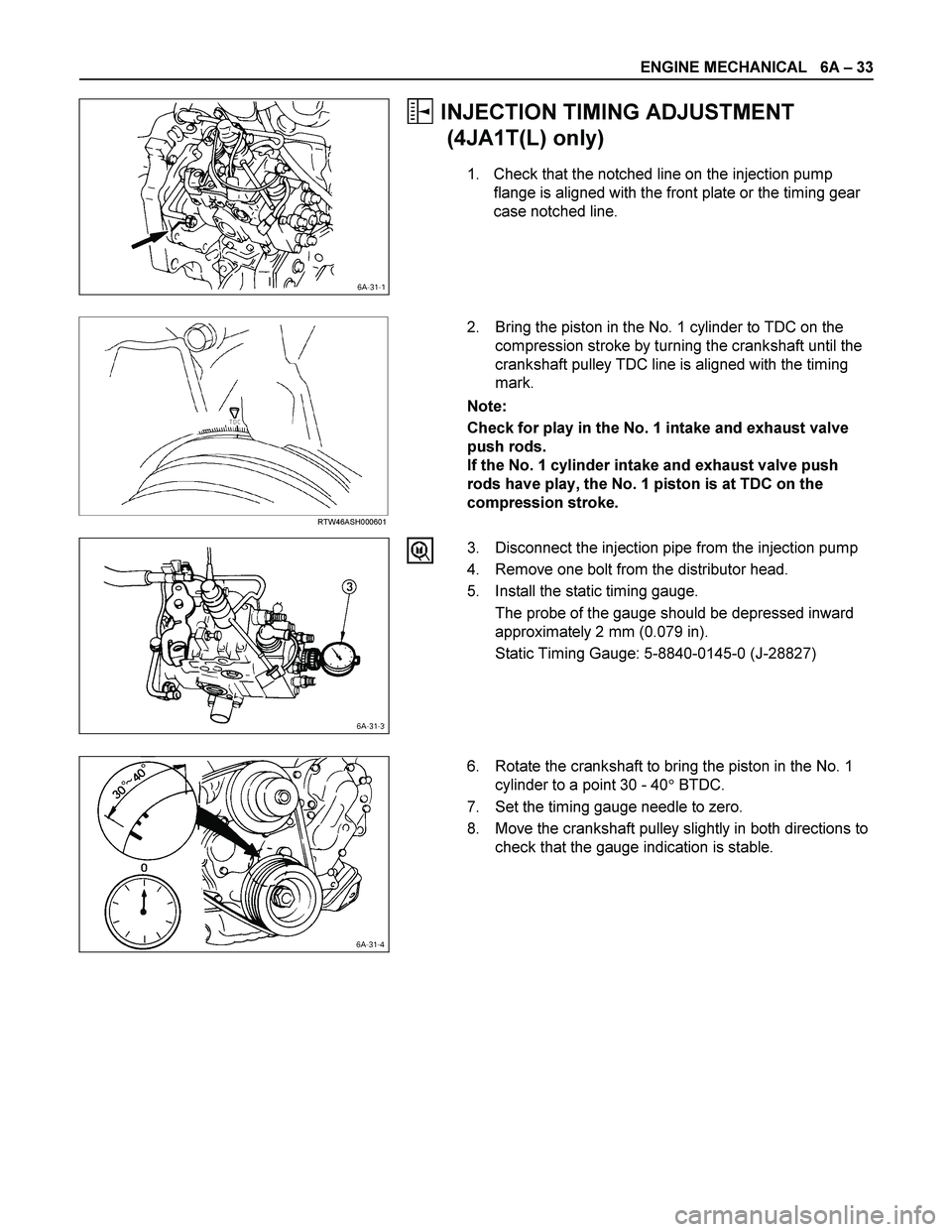
ENGINE MECHANICAL 6A – 33
INJECTION TIMING ADJUSTMENT
(4JA1T(L) only)
1. Check that the notched line on the injection pump
flange is aligned with the front plate or the timing gear
case notched line.
2. Bring the piston in the No. 1 cylinder to TDC on the
compression stroke by turning the crankshaft until the
crankshaft pulley TDC line is aligned with the timing
mark.
Note:
Check for play in the No. 1 intake and exhaust valve
push rods.
If the No. 1 cylinder intake and exhaust valve push
rods have play, the No. 1 piston is at TDC on the
compression stroke.
RTW46ASH000601
3. Disconnect the injection pipe from the injection pump
4. Remove one bolt from the distributor head.
5. Install the static timing gauge.
The probe of the gauge should be depressed inward
approximately 2 mm (0.079 in).
Static Timing Gauge: 5-8840-0145-0 (J-28827)
6. Rotate the crankshaft to bring the piston in the No. 1
cylinder to a point 30 - 40 BTDC.
7. Set the timing gauge needle to zero.
8. Move the crankshaft pulley slightly in both directions to
check that the gauge indication is stable.
Page 1174 of 4264
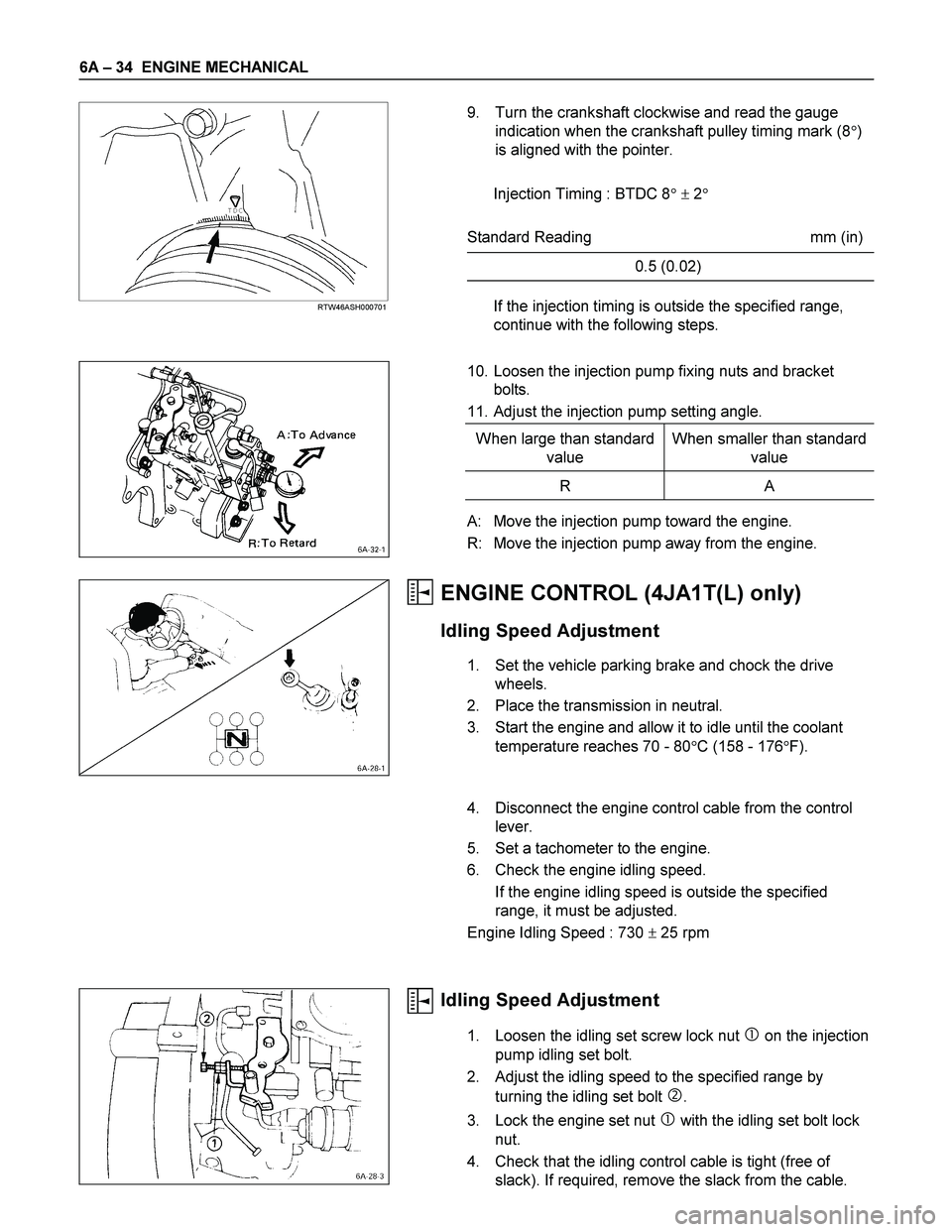
6A – 34 ENGINE MECHANICAL
RTW46ASH000701
9. Turn the crankshaft clockwise and read the gauge
indication when the crankshaft pulley timing mark (8)
is aligned with the pointer.
Injection Timing : BTDC 8 2
Standard Reading mm (in)
0.5 (0.02)
If the injection timing is outside the specified range,
continue with the following steps.
10. Loosen the injection pump fixing nuts and bracket
bolts.
11. Adjust the injection pump setting angle.
When large than standard
value When smaller than standard
value
R A
A: Move the injection pump toward the engine.
R: Move the injection pump away from the engine.
ENGINE CONTROL (4JA1T(L) only)
Idling Speed Adjustment
1. Set the vehicle parking brake and chock the drive
wheels.
2. Place the transmission in neutral.
3. Start the engine and allow it to idle until the coolant
temperature reaches 70 - 80C (158 - 176F).
4. Disconnect the engine control cable from the control
lever.
5. Set a tachometer to the engine.
6. Check the engine idling speed.
If the engine idling speed is outside the specified
range, it must be adjusted.
Engine Idling Speed : 730 25 rpm
Idling Speed Adjustment
1. Loosen the idling set screw lock nut on the injection
pump idling set bolt.
2. Adjust the idling speed to the specified range by
turning the idling set bolt
.
3. Lock the engine set nut
with the idling set bolt lock
nut.
4. Check that the idling control cable is tight (free of
slack). If required, remove the slack from the cable.
Page 1175 of 4264
ENGINE MECHANICAL 6A – 35
Fast Idling Speed Inspection
1. Set tachometer to the engine.
2. Disconnect the vacuum hose
from the fast idle
actuator
on the injection pump.
3. Disconnect the other vacuum hose
from the
vacuum switching valve
and connect it to the fast
idle actuator
.
The vacuum line will now be connected directly from
the vacuum pump
to the fast idle actuator.
4. Check the engine fast idling speed.
If the engine idling speed is outside the specified
range, it must be adjusted.
Fast Idling Speed rpm
850 25
Fast Idling Speed Adjustment
1. Loosen the fast idle actuator bracket bolts.
2. Adjust the fast idling speed by moving the actuator
bracket, so that the clearance “S” can be 1 ~ 2 mm
(0.04 ~ 0.08 in.).
3. Tighten the bracket bolts.
Accelerator Control Cable Adjustment
Refer to Sec. 6H-6 (Accelerator Control)
Page 1176 of 4264
6A – 36 ENGINE MECHANICAL
GENERAL DESCRIPTION
RTW46AMF000401
The 4J series automotive diesel engine has special designed combustion chambers in the piston. This design
provides superior fuel economy over a wide range of driving conditions.
Auto-thermatic pistons with cast steel struts are used to reduce thermal expansion and resulting engine noise when
the engine is cold.
Chrome plated dry type cylinder liners provide the highest durability.
The laminated steel sheet cylinder head gasket is very durable and, to increase the head gasket reliability.
The crankshaft has been tufftrided to provide a longer service life. Because the crankshaft is tufftrided, it cannot be
reground.
The 4JA1T(L) engine is equipped with the BOSCH VE-Type distributor injection pump.
The 4JH1TC and 4JA1TC engine is equipped with the BOSCH VP44-Type distributor injection pump.
The engine is turbocharger equipped.