Page 1905 of 4264
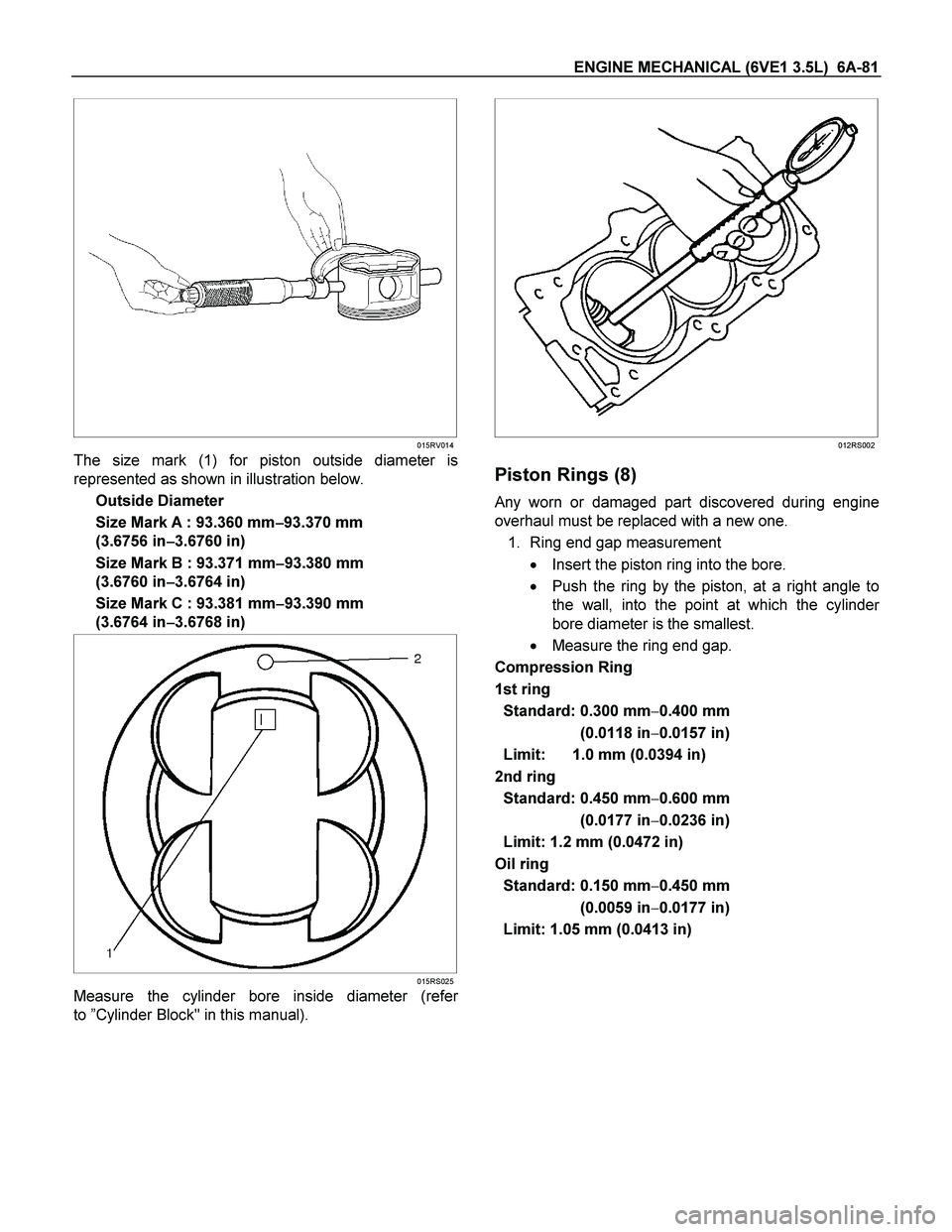
ENGINE MECHANICAL (6VE1 3.5L) 6A-81
015RV014
The size mark (1) for piston outside diameter is
represented as shown in illustration below.
Outside Diameter
Size Mark A : 93.360 mm
93.370 mm
(3.6756 in
3.6760 in)
Size Mark B : 93.371 mm
93.380 mm
(3.6760 in
3.6764 in)
Size Mark C : 93.381 mm
93.390 mm
(3.6764 in
3.6768 in)
015RS025
Measure the cylinder bore inside diameter (refer
to ”Cylinder Block" in this manual).
012RS002
Piston Rings (8)
Any worn or damaged part discovered during engine
overhaul must be replaced with a new one.
1. Ring end gap measurement
Insert the piston ring into the bore.
Push the ring by the piston, at a right angle to
the wall, into the point at which the cylinde
r
bore diameter is the smallest.
Measure the ring end gap.
Compression Ring
1st ring
Standard: 0.300 mm0.400 mm
(0.0118 in0.0157 in)
Limit: 1.0 mm (0.0394 in)
2nd ring
Standard: 0.450 mm0.600 mm
(0.0177 in0.0236 in)
Limit: 1.2 mm (0.0472 in)
Oil ring
Standard: 0.150 mm0.450 mm
(0.0059 in0.0177 in)
Limit: 1.05 mm (0.0413 in)
Page 1906 of 4264
6A-82 ENGINE MECHANICAL (6VE1 3.5L)
015RS026
The No.1 compression ring must be set with
direction of origin.
No.2 compression ring: Positioning mark (1) is
painted as shown in the illustration.
015RS027
2. Measure the clearance between the piston ring
groove and the piston ring with a feeler gauge. I
f
the piston ring groove / piston ring clearance
exceeds the specified limit, the piston must be
replaced.
Compression Ring Clearance
Standard : 0.016 mm
0.038 mm
(0.0006 in.
0.0015 in)
Limit : 0.15mm (0.0059 in)
015RS028
Piston Pin (9)
NOTE: Do not reuse the old piston pin.
1. Use a micrometer to measure the new piston pin
outside diameter in both directions at three
different positions.
2. Measure the inside diameter of the connecting rod
small end. If the fitting interference between the
small end and pin does not conform to the
specified value, the connecting rod must be
replaced.
Standard : 0.023 mm
0.038 mm
(0.0009 in
0.0015 in)
015RS029
Page 1907 of 4264
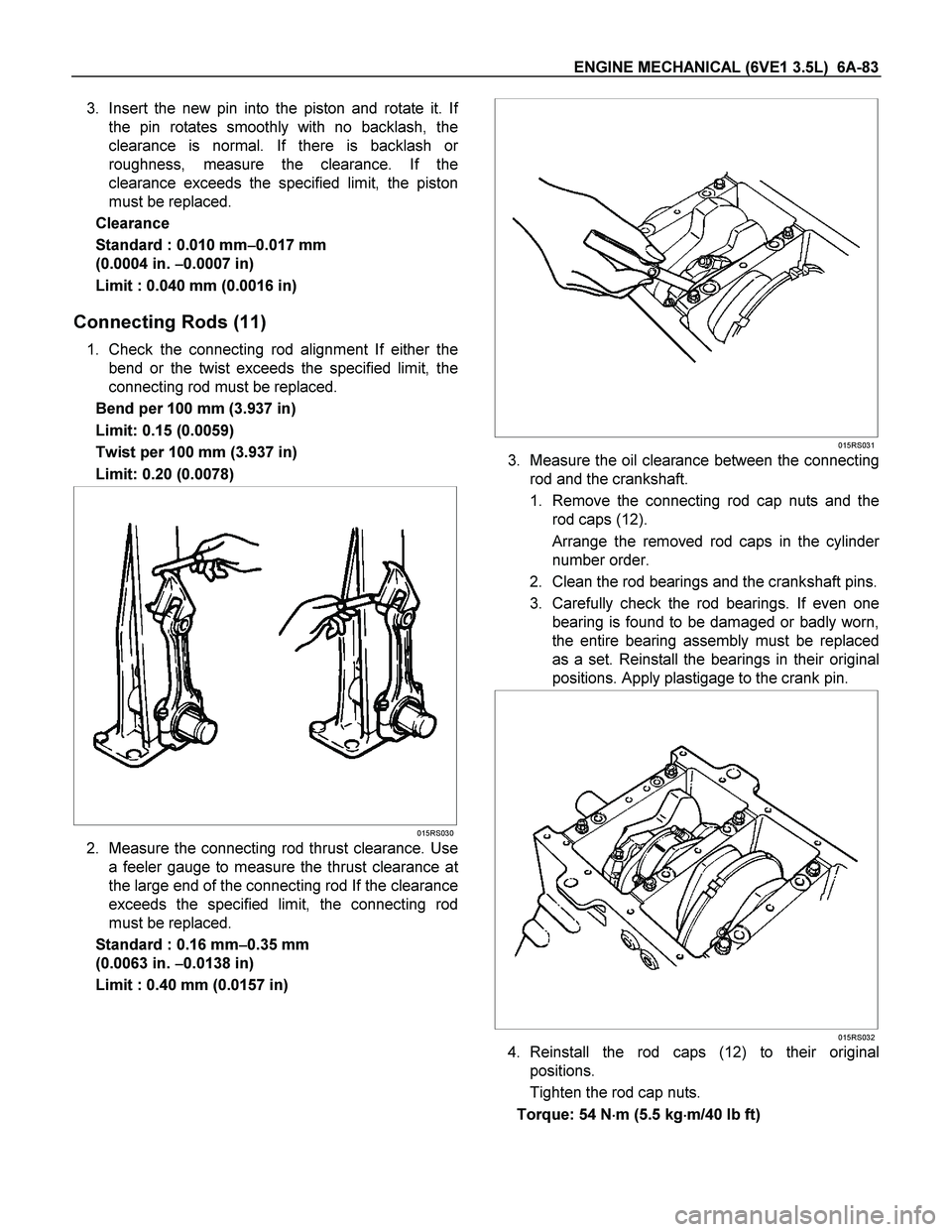
ENGINE MECHANICAL (6VE1 3.5L) 6A-83
3. Insert the new pin into the piston and rotate it. If
the pin rotates smoothly with no backlash, the
clearance is normal. If there is backlash o
r
roughness, measure the clearance. If the
clearance exceeds the specified limit, the piston
must be replaced.
Clearance
Standard : 0.010 mm
0.017 mm
(0.0004 in.
0.0007 in)
Limit : 0.040 mm (0.0016 in)
Connecting Rods (11)
1. Check the connecting rod alignment If either the
bend or the twist exceeds the specified limit, the
connecting rod must be replaced.
Bend per 100 mm (3.937 in)
Limit: 0.15 (0.0059)
Twist per 100 mm (3.937 in)
Limit: 0.20 (0.0078)
015RS030
2. Measure the connecting rod thrust clearance. Use
a feeler gauge to measure the thrust clearance a
t
the large end of the connecting rod If the clearance
exceeds the specified limit, the connecting rod
must be replaced.
Standard : 0.16 mm
0.35 mm
(0.0063 in.
0.0138 in)
Limit : 0.40 mm (0.0157 in)
015RS031
3. Measure the oil clearance between the connecting
rod and the crankshaft.
1. Remove the connecting rod cap nuts and the
rod caps (12).
Arrange the removed rod caps in the cylinder
number order.
2. Clean the rod bearings and the crankshaft pins.
3. Carefully check the rod bearings. If even one
bearing is found to be damaged or badly worn,
the entire bearing assembly must be replaced
as a set. Reinstall the bearings in their original
positions. Apply plastigage to the crank pin.
015RS032
4. Reinstall the rod caps (12) to their original
positions.
Tighten the rod cap nuts.
Torque: 54 N
m (5.5 kg
m/40 lb ft)
Page 1908 of 4264
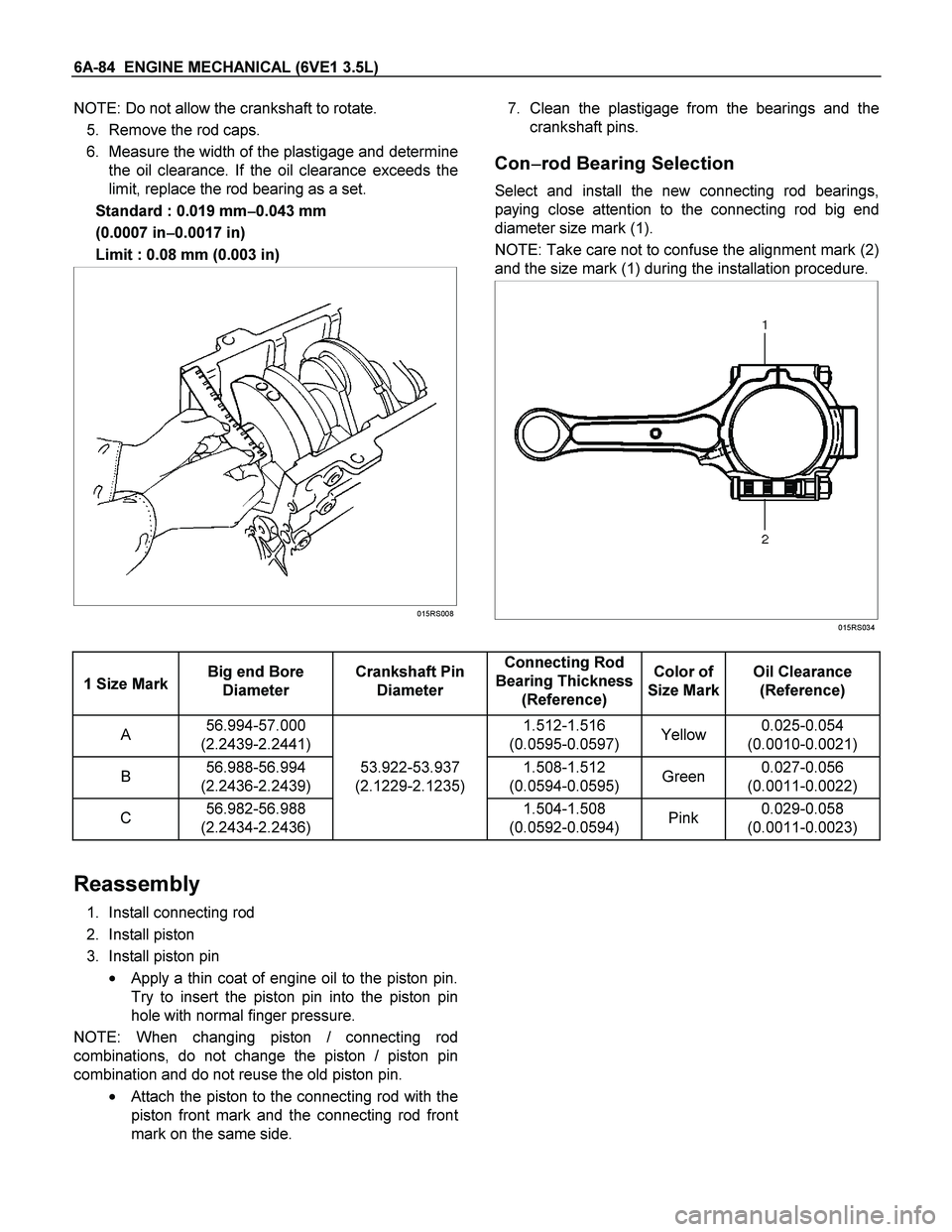
6A-84 ENGINE MECHANICAL (6VE1 3.5L)
NOTE: Do not allow the crankshaft to rotate.
5. Remove the rod caps.
6. Measure the width of the plastigage and determine
the oil clearance. If the oil clearance exceeds the
limit, replace the rod bearing as a set.
Standard : 0.019 mm
0.043 mm
(0.0007 in
0.0017 in)
Limit : 0.08 mm (0.003 in)
015RS008
7. Clean the plastigage from the bearings and the
crankshaft pins.
Con
rod Bearing Selection
Select and install the new connecting rod bearings,
paying close attention to the connecting rod big end
diameter size mark (1).
NOTE: Take care not to confuse the alignment mark (2)
and the size mark (1) during the installation procedure.
015RS034
1 Size Mark Big end Bore
Diameter Crankshaft Pin
Diameter Connecting Rod
Bearing Thickness
(Reference) Color of
Size Mark Oil Clearance
(Reference)
A 56.994-57.000
(2.2439-2.2441) 1.512-1.516
(0.0595-0.0597) Yellow 0.025-0.054
(0.0010-0.0021)
B 56.988-56.994
(2.2436-2.2439) 53.922-53.937
(2.1229-2.1235) 1.508-1.512
(0.0594-0.0595) Green 0.027-0.056
(0.0011-0.0022)
C 56.982-56.988
(2.2434-2.2436) 1.504-1.508
(0.0592-0.0594) Pink 0.029-0.058
(0.0011-0.0023)
Reassembly
1. Install connecting rod
2. Install piston
3. Install piston pin
Apply a thin coat of engine oil to the piston pin.
Try to insert the piston pin into the piston pin
hole with normal finger pressure.
NOTE: When changing piston / connecting rod
combinations, do not change the piston / piston pin
combination and do not reuse the old piston pin.
Attach the piston to the connecting rod with the
piston front mark and the connecting rod fron
t
mark on the same side.
Page 1909 of 4264
ENGINE MECHANICAL (6VE1 3.5L) 6A-85
RUW36ASH000501
With 5884005510 Piston pin service set
and a press, press fit the piston pin.
NOTE: Heat the connecting rod small end to a suitable
temperature to ensure smooth installation.
015RX001
Legend
(1) Press Ram
(2) Piston
(3) Connecting Rod
(4) Piston Pin
4. Install piston ring with the piston ring expander.
The No.2 compression ring must be set with the
T2 mark (1) facing up.
015RS027
Install piston rings in the following sequence.
1. Oil ring
1. Expander ring
2. Upper side rail
3. Lower side rail
2. 2nd compression ring
The 2nd compression ring must be set with the
T2 mark facing up.
3. 1st compression ring
The compression ring must be set with
direction of origin.
After installation, apply engine oil to the entire
circumference of the piston rings. Check to see
that all the rings rotate smoothly.
015RS038
Page 1910 of 4264
6A-86 ENGINE MECHANICAL (6VE1 3.5L)
5. Install piston and connecting rod assembly.
Insert the bearings into the connecting rods and
caps. Apply new engine oil to the bearing faces
and nuts.
Tighten the connecting rod cap nuts
Torque : 54 N
m (5.5 kg
m/40 lb ft)
NOTE: Do not apply engine oil to the bearing back
faces.
6. Oil gallery, refer to “Crankshaft and main bearing"
in this manual.
7. Oil strainer and O-ring.
8. Oil pipe and O-ring.
9. Install crankcase with oil pan, refer to “Oil pan and
Crankcase" in this manual.
10. Install cylinder head gasket.
11. Install Cylinder head assembly.
Refer to “Cylinder head" in this manual.
Page 1911 of 4264
ENGINE MECHANICAL (6VE1 3.5L) 6A-87
Cylinder Block
Cylinder Block and Associated Parts
012RW010
Legend
(1) Cylinder Head Assembly
(2) Cylinder Head Gasket
(3) Crankcase with Oil Pan
(4) Oil Pipe and O-Ring
(5) Oil Strainer and O-Ring
(6) Oil Pump Assembly
(7) Cylinder Block Side Bolts
(8) Oil Gallery
(9) Piston and Connecting Rod Assembly
(10) Flywheel
(11) Rear Oil Seal Retainer Assembly
(12) Main Bearing Cap
(13) Crankshaft
(14) Cylinder Block
Page 1912 of 4264
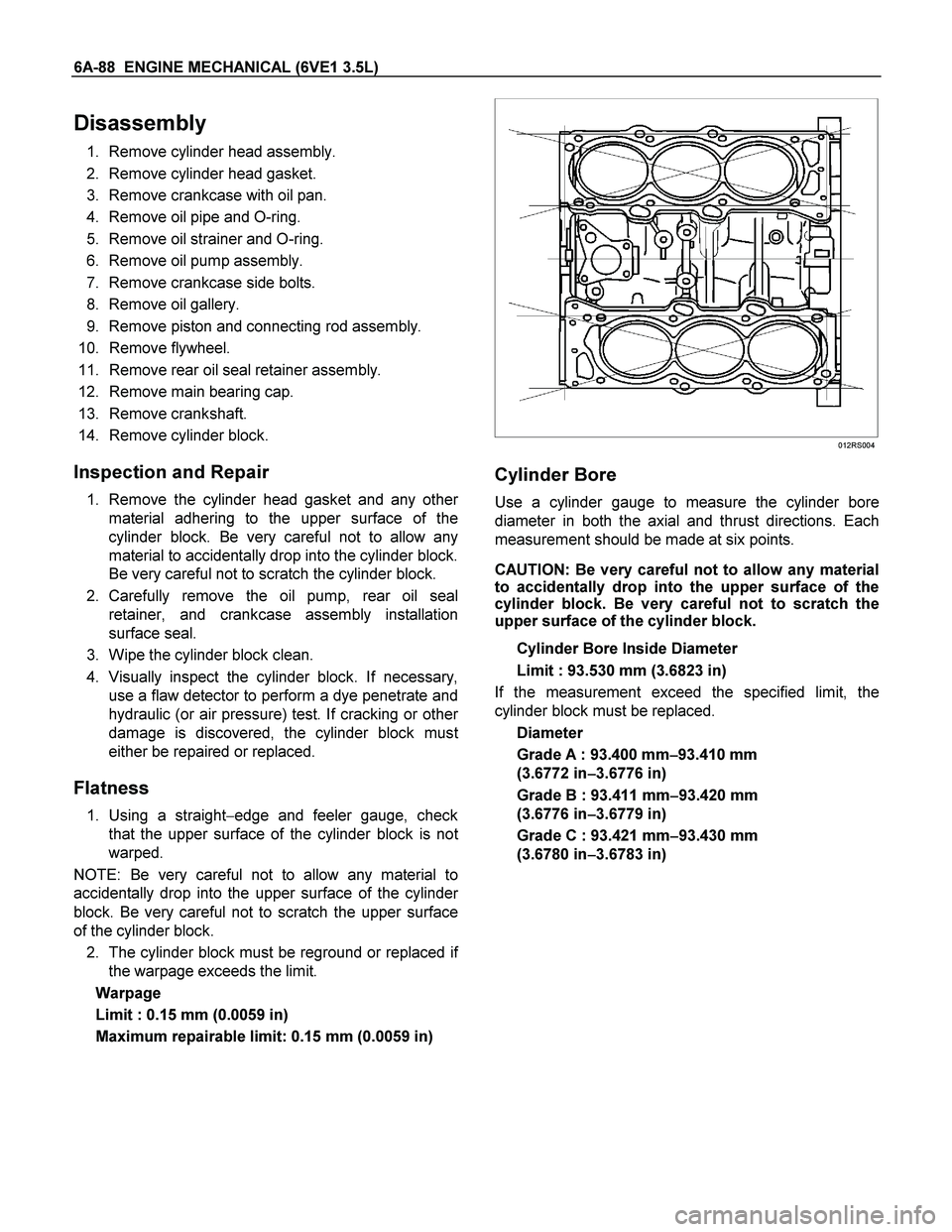
6A-88 ENGINE MECHANICAL (6VE1 3.5L)
Disassembly
1. Remove cylinder head assembly.
2. Remove cylinder head gasket.
3. Remove crankcase with oil pan.
4. Remove oil pipe and O-ring.
5. Remove oil strainer and O-ring.
6. Remove oil pump assembly.
7. Remove crankcase side bolts.
8. Remove oil gallery.
9. Remove piston and connecting rod assembly.
10. Remove flywheel.
11. Remove rear oil seal retainer assembly.
12. Remove main bearing cap.
13. Remove crankshaft.
14. Remove cylinder block.
Inspection and Repair
1. Remove the cylinder head gasket and any other
material adhering to the upper surface of the
cylinder block. Be very careful not to allow any
material to accidentally drop into the cylinder block.
Be very careful not to scratch the cylinder block.
2. Carefully remove the oil pump, rear oil seal
retainer, and crankcase assembly installation
surface seal.
3. Wipe the cylinder block clean.
4. Visually inspect the cylinder block. If necessary,
use a flaw detector to perform a dye penetrate and
hydraulic (or air pressure) test. If cracking or othe
r
damage is discovered, the cylinder block must
either be repaired or replaced.
Flatness
1. Using a straightedge and feeler gauge, check
that the upper surface of the cylinder block is no
t
warped.
NOTE: Be very careful not to allow any material to
accidentally drop into the upper surface of the cylinde
r
block. Be very careful not to scratch the upper surface
of the cylinder block.
2. The cylinder block must be reground or replaced i
f
the warpage exceeds the limit.
Warpage
Limit : 0.15 mm (0.0059 in)
Maximum repairable limit: 0.15 mm (0.0059 in)
012RS004
Cylinder Bore
Use a cylinder gauge to measure the cylinder bore
diameter in both the axial and thrust directions. Each
measurement should be made at six points.
CAUTION: Be very careful not to allow any material
to accidentally drop into the upper surface of the
cylinder block. Be very careful not to scratch the
upper surface of the cylinder block.
Cylinder Bore Inside Diameter
Limit : 93.530 mm (3.6823 in)
If the measurement exceed the specified limit, the
cylinder block must be replaced.
Diameter
Grade A : 93.400 mm
93.410 mm
(3.6772 in
3.6776 in)
Grade B : 93.411 mm
93.420 mm
(3.6776 in
3.6779 in)
Grade C : 93.421 mm
93.430 mm
(3.6780 in
3.6783 in)