Page 1209 of 4264
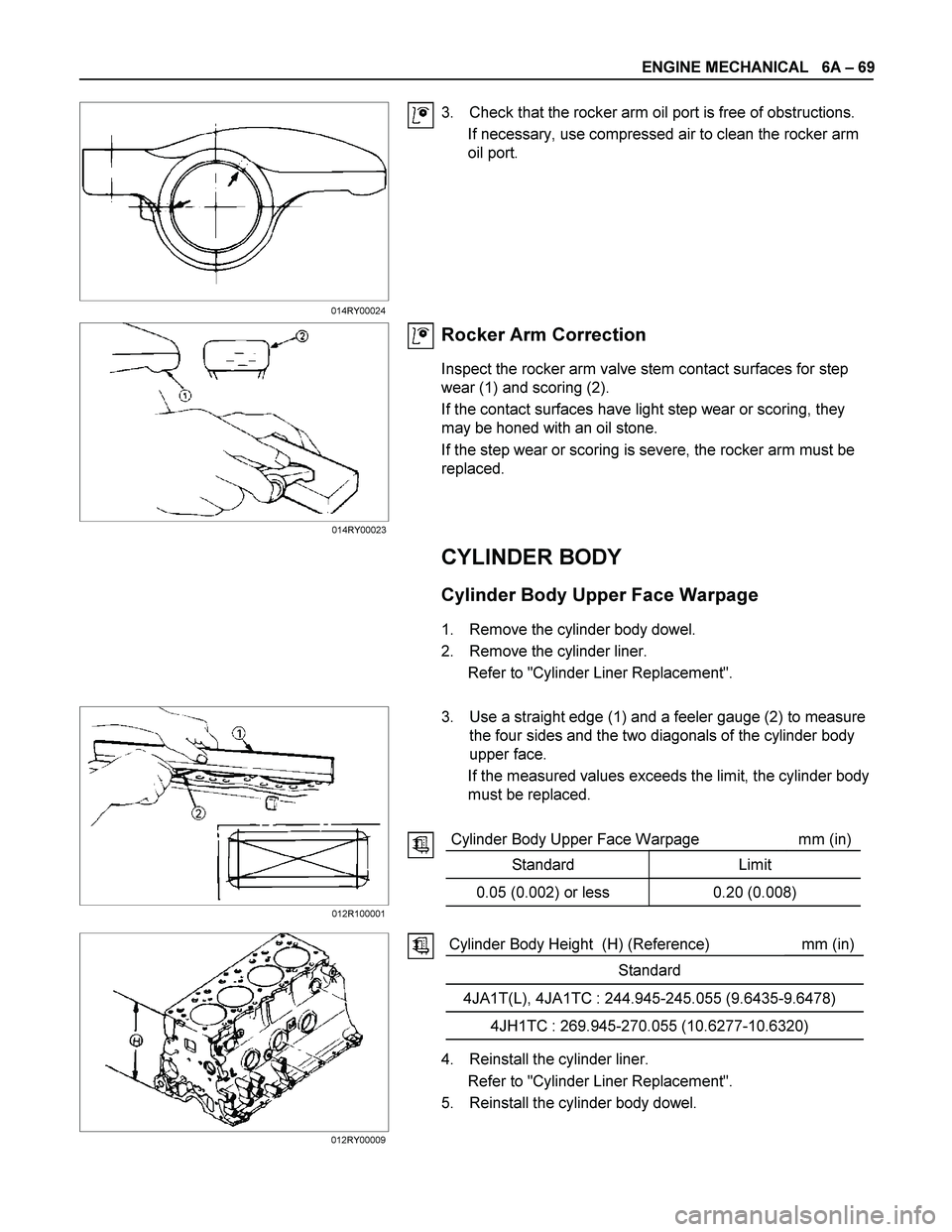
ENGINE MECHANICAL 6A – 69
3. Check that the rocker arm oil port is free of obstructions.
If necessary, use compressed air to clean the rocker arm
oil port.
Rocker Arm Correction
Inspect the rocker arm valve stem contact surfaces for step
wear (1) and scoring (2).
If the contact surfaces have light step wear or scoring, they
may be honed with an oil stone.
If the step wear or scoring is severe, the rocker arm must be
replaced.
CYLINDER BODY
Cylinder Body Upper Face Warpage
1. Remove the cylinder body dowel.
2. Remove the cylinder liner.
Refer to "Cylinder Liner Replacement".
3. Use a straight edge (1) and a feeler gauge (2) to measure
the four sides and the two diagonals of the cylinder body
upper face.
If the measured values exceeds the limit, the cylinder body
must be replaced.
Cylinder Body Upper Face Warpage mm (in)
Standard Limit
0.05 (0.002) or less 0.20 (0.008)
Cylinder Body Height (H) (Reference) mm (in)
Standard
4JA1T(L), 4JA1TC : 244.945-245.055 (9.6435-9.6478)
4JH1TC : 269.945-270.055 (10.6277-10.6320)
4. Reinstall the cylinder liner.
Refer to "Cylinder Liner Replacement".
5. Reinstall the cylinder body dowel.
014RY00024
012R100001
012RY00009014RY00023
Page 1210 of 4264
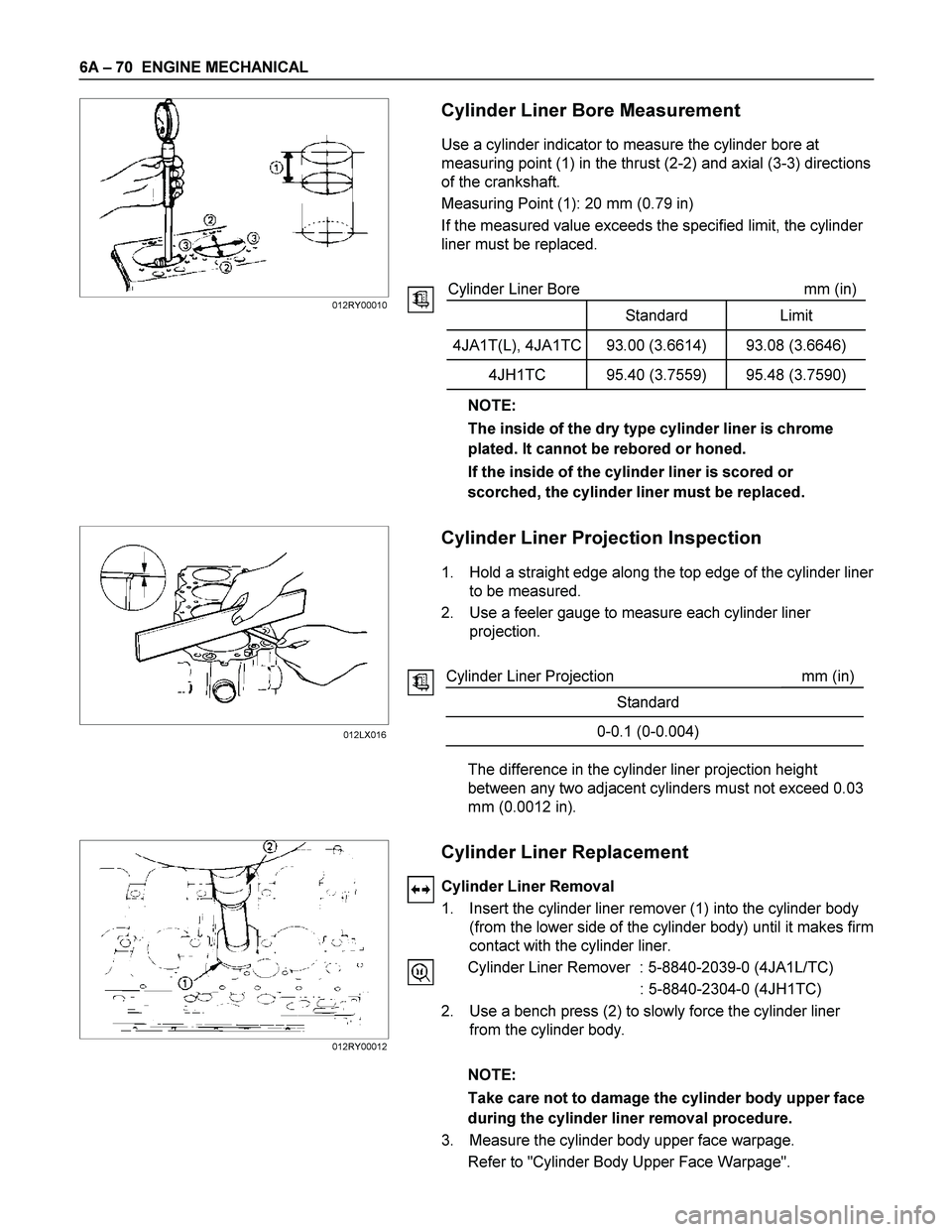
6A – 70 ENGINE MECHANICAL
Cylinder Liner Bore Measurement
Use a cylinder indicator to measure the cylinder bore at
measuring point (1) in the thrust (2-2) and axial (3-3) directions
of the crankshaft.
Measuring Point (1): 20 mm (0.79 in)
If the measured value exceeds the specified limit, the cylinder
liner must be replaced.
Cylinder Liner Bore mm (in)
Standard Limit
4JA1T(L), 4JA1TC 93.00 (3.6614) 93.08 (3.6646)
4JH1TC 95.40 (3.7559) 95.48 (3.7590)
NOTE:
The inside of the dry type cylinder liner is chrome
plated. It cannot be rebored or honed.
If the inside of the cylinder liner is scored or
scorched, the cylinder liner must be replaced.
Cylinder Liner Projection Inspection
1. Hold a straight edge along the top edge of the cylinder liner
to be measured.
2. Use a feeler gauge to measure each cylinder liner
projection.
Cylinder Liner Projection mm (in)
Standard
0-0.1 (0-0.004)
The difference in the cylinder liner projection height
between any two adjacent cylinders must not exceed 0.03
mm (0.0012 in).
Cylinder Liner Replacement
Cylinder Liner Removal
1. Insert the cylinder liner remover (1) into the cylinder body
(from the lower side of the cylinder body) until it makes firm
contact with the cylinder liner.
Cylinder Liner Remover : 5-8840-2039-0 (4JA1L/TC)
: 5-8840-2304-0 (4JH1TC)
2. Use a bench press (2) to slowly force the cylinder liner
from the cylinder body.
NOTE:
Take care not to damage the cylinder body upper face
during the cylinder liner removal procedure.
3. Measure the cylinder body upper face warpage.
Refer to "Cylinder Body Upper Face Warpage".
012RY00010
012LX016
012RY00012
Page 1211 of 4264
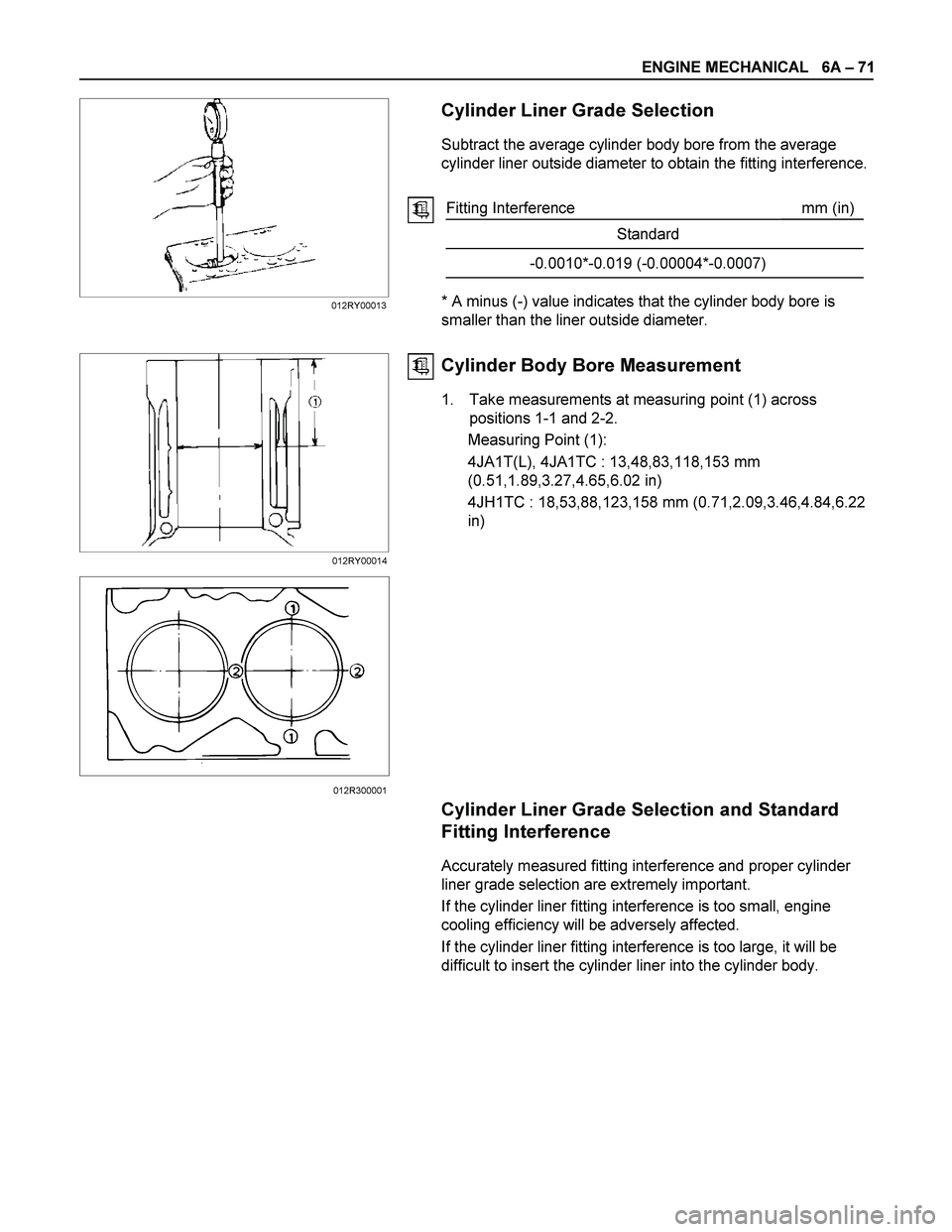
ENGINE MECHANICAL 6A – 71
Cylinder Liner Grade Selection
Subtract the average cylinder body bore from the average
cylinder liner outside diameter to obtain the fitting interference.
Fitting Interference mm (in)
Standard
-0.0010*-0.019 (-0.00004*-0.0007)
* A minus (-) value indicates that the cylinder body bore is
smaller than the liner outside diameter.
Cylinder Body Bore Measurement
1. Take measurements at measuring point (1) across
positions 1-1 and 2-2.
Measuring Point (1):
4JA1T(L), 4JA1TC : 13,48,83,118,153 mm
(0.51,1.89,3.27,4.65,6.02 in)
4JH1TC : 18,53,88,123,158 mm (0.71,2.09,3.46,4.84,6.22
in)
Cylinder Liner Grade Selection and Standard
Fitting Interference
Accurately measured fitting interference and proper cylinder
liner grade selection are extremely important.
If the cylinder liner fitting interference is too small, engine
cooling efficiency will be adversely affected.
If the cylinder liner fitting interference is too large, it will be
difficult to insert the cylinder liner into the cylinder body.
012RY00013
012RY00014
012R300001
Page 1212 of 4264
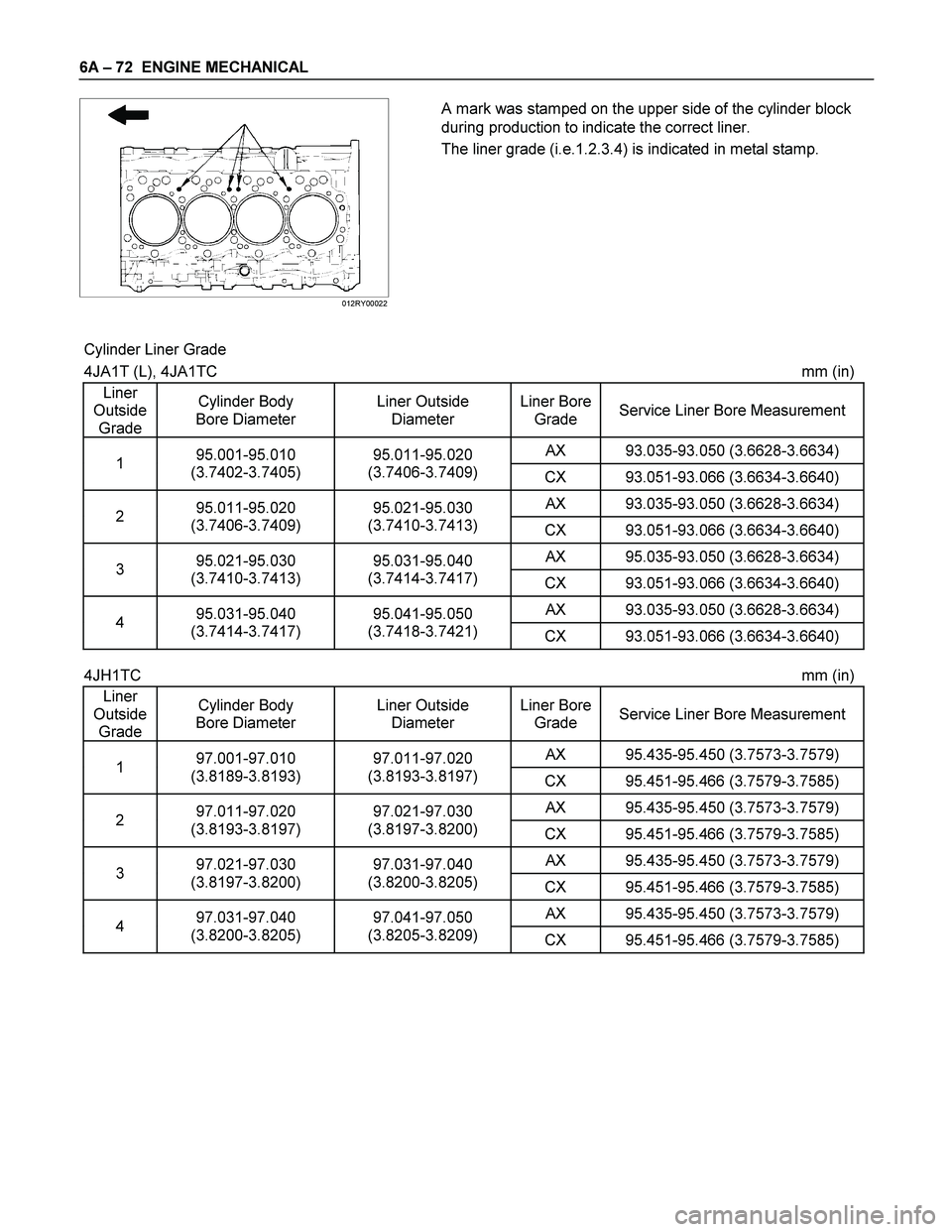
6A – 72 ENGINE MECHANICAL
012RY00022
A mark was stamped on the upper side of the cylinder block
during production to indicate the correct liner.
The liner grade (i.e.1.2.3.4) is indicated in metal stamp.
Cylinder Liner Grade
4JA1T (L), 4JA1TC mm (in)
Liner
Outside
Grade Cylinder Body
Bore Diameter Liner Outside
Diameter Liner Bore
Grade Service Liner Bore Measurement
AX 93.035-93.050 (3.6628-3.6634) 1 95.001-95.010
(3.7402-3.7405) 95.011-95.020
(3.7406-3.7409)
CX 93.051-93.066 (3.6634-3.6640)
AX 93.035-93.050 (3.6628-3.6634) 2 95.011-95.020
(3.7406-3.7409) 95.021-95.030
(3.7410-3.7413)
CX 93.051-93.066 (3.6634-3.6640)
AX 95.035-93.050 (3.6628-3.6634) 3 95.021-95.030
(3.7410-3.7413) 95.031-95.040
(3.7414-3.7417)
CX 93.051-93.066 (3.6634-3.6640)
AX 93.035-93.050 (3.6628-3.6634) 4 95.031-95.040
(3.7414-3.7417) 95.041-95.050
(3.7418-3.7421)
CX 93.051-93.066 (3.6634-3.6640)
4JH1TC mm (in)
Liner
Outside
Grade Cylinder Body
Bore Diameter Liner Outside
Diameter Liner Bore
Grade Service Liner Bore Measurement
AX 95.435-95.450 (3.7573-3.7579) 1 97.001-97.010
(3.8189-3.8193) 97.011-97.020
(3.8193-3.8197)
CX 95.451-95.466 (3.7579-3.7585)
AX 95.435-95.450 (3.7573-3.7579) 2 97.011-97.020
(3.8193-3.8197) 97.021-97.030
(3.8197-3.8200)
CX 95.451-95.466 (3.7579-3.7585)
AX 95.435-95.450 (3.7573-3.7579) 3 97.021-97.030
(3.8197-3.8200) 97.031-97.040
(3.8200-3.8205)
CX 95.451-95.466 (3.7579-3.7585)
AX 95.435-95.450 (3.7573-3.7579) 4 97.031-97.040
(3.8200-3.8205) 97.041-97.050
(3.8205-3.8209)
CX 95.451-95.466 (3.7579-3.7585)
Page 1213 of 4264
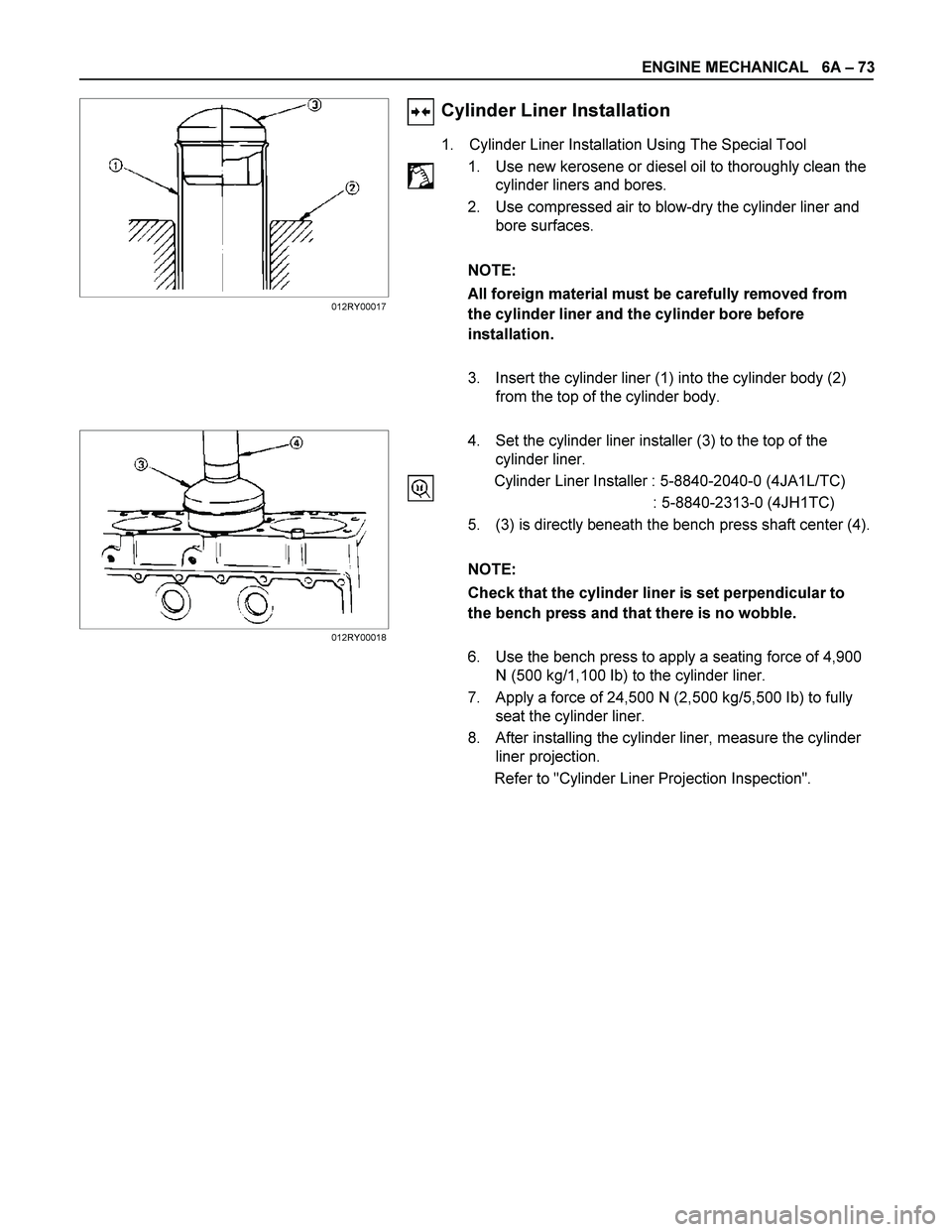
ENGINE MECHANICAL 6A – 73
Cylinder Liner Installation
1. Cylinder Liner Installation Using The Special Tool
1. Use new kerosene or diesel oil to thoroughly clean the
cylinder liners and bores.
2. Use compressed air to blow-dry the cylinder liner and
bore surfaces.
NOTE:
All foreign material must be carefully removed from
the cylinder liner and the cylinder bore before
installation.
3. Insert the cylinder liner (1) into the cylinder body (2)
from the top of the cylinder body.
4. Set the cylinder liner installer (3) to the top of the
cylinder liner.
Cylinder Liner Installer : 5-8840-2040-0 (4JA1L/TC)
: 5-8840-2313-0 (4JH1TC)
5. (3) is directly beneath the bench press shaft center (4).
NOTE:
Check that the cylinder liner is set perpendicular to
the bench press and that there is no wobble.
6. Use the bench press to apply a seating force of 4,900
N (500 kg/1,100 Ib) to the cylinder liner.
7. Apply a force of 24,500 N (2,500 kg/5,500 Ib) to fully
seat the cylinder liner.
8. After installing the cylinder liner, measure the cylinder
liner projection.
Refer to "Cylinder Liner Projection Inspection".
012RY00017
012RY00018
Page 1214 of 4264
6A – 74 ENGINE MECHANICAL
Piston Grade Selection
Measure the cylinder liner bore after installing the cylinder liner.
Then select the appropriate piston grade for the installed
cylinder liner.
1. Measure the cylinder liner bore.
Refer to "Cylinder Liner Bore Measurement"
Cylinder Liner Bore (Service Part) Grade mm (in)
Grade Bore measurement
AX 93.035-95.050
(3.6628-3.6634) 4JA1T(L)
4JA1TC
CX 93.051-95.066
(3.6634-3.6640)
AX 95.435-95.450
(3.7573-3.7579)
4JH1TC
CX 95.451-95.466
(3.7579-3.7585)
NOTE:
It is most important that the correct piston grade be
used. Failure to select the correct piston grade will
result in engine failure. Always measure the cylinder
bore and select the correct piston grade.
Page 1215 of 4264
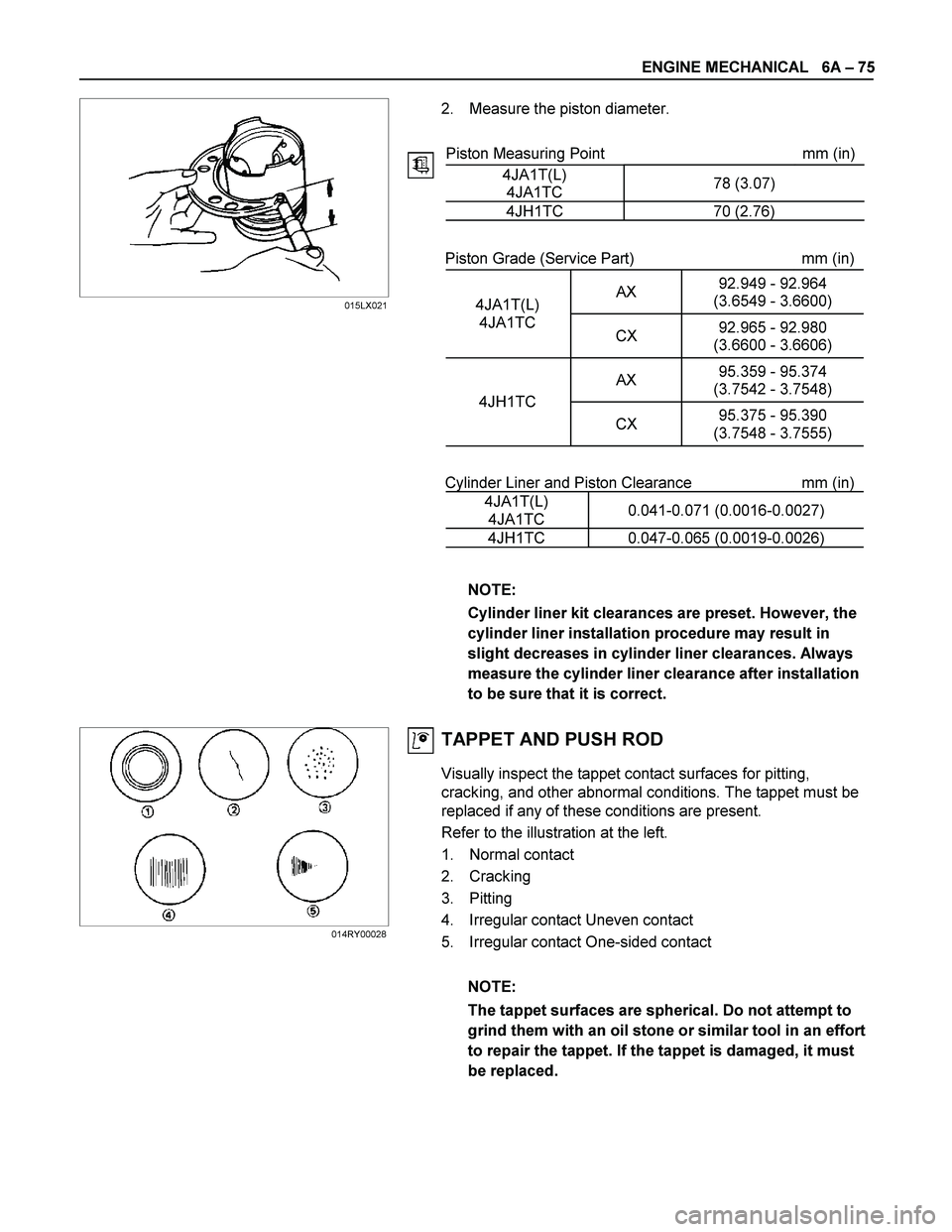
ENGINE MECHANICAL 6A – 75
2. Measure the piston diameter.
Piston Measuring Point mm (in)
4JA1T(L)
4JA1TC 78 (3.07)
4JH1TC 70 (2.76)
Piston Grade (Service Part) mm (in)
AX 92.949 - 92.964
(3.6549 - 3.6600)
4JA1T(L)
4JA1TC
CX 92.965 - 92.980
(3.6600 - 3.6606)
AX 95.359 - 95.374
(3.7542 - 3.7548)
4JH1TC
CX 95.375 - 95.390
(3.7548 - 3.7555)
Cylinder Liner and Piston Clearance mm (in)
4JA1T(L)
4JA1TC 0.041-0.071 (0.0016-0.0027)
4JH1TC 0.047-0.065 (0.0019-0.0026)
NOTE:
Cylinder liner kit clearances are preset. However, the
cylinder liner installation procedure may result in
slight decreases in cylinder liner clearances. Always
measure the cylinder liner clearance after installation
to be sure that it is correct.
TAPPET AND PUSH ROD
Visually inspect the tappet contact surfaces for pitting,
cracking, and other abnormal conditions. The tappet must be
replaced if any of these conditions are present.
Refer to the illustration at the left.
1. Normal contact
2. Cracking
3. Pitting
4. Irregular contact Uneven contact
5. Irregular contact One-sided contact
NOTE:
The tappet surfaces are spherical. Do not attempt to
grind them with an oil stone or similar tool in an effort
to repair the tappet. If the tappet is damaged, it must
be replaced.
015LX021
014RY00028
Page 1216 of 4264
6A – 76 ENGINE MECHANICAL
Tappet Outside Diameter
Measure the tappet outside diameter with a micrometer.
If the measured value is less than the specified limit, the tappet
must be replaced.
Tappet Outside Diameter mm (in)
Standard Limit
12.97 - 12.99
(0.510 - 0.511) 12.95 (0.510)
Tappet and Cylinder Body Clearance mm (in)
Standard Limit
0.01 - 0.046
(0.0004 - 0.0018) 0.10 (0.004)
Push Rod Curvature
1. Lay the push rod on a surface plate.
2. Roll the push rod along the surface plate and measure the
push rod curvature with a thickness gauge.
If the measured value exceeds the specified limit, the push
rod must be replaced.
Pushrod Curvature mm (in)
Limit
0.3 (0.012)
3. Visually inspect both ends of the push rod for excessive
wear and damage. The push rod must be replaced if these
conditions are discovered during inspection.
014RY00029
012LX014
014RY00031