Page 3689 of 5598
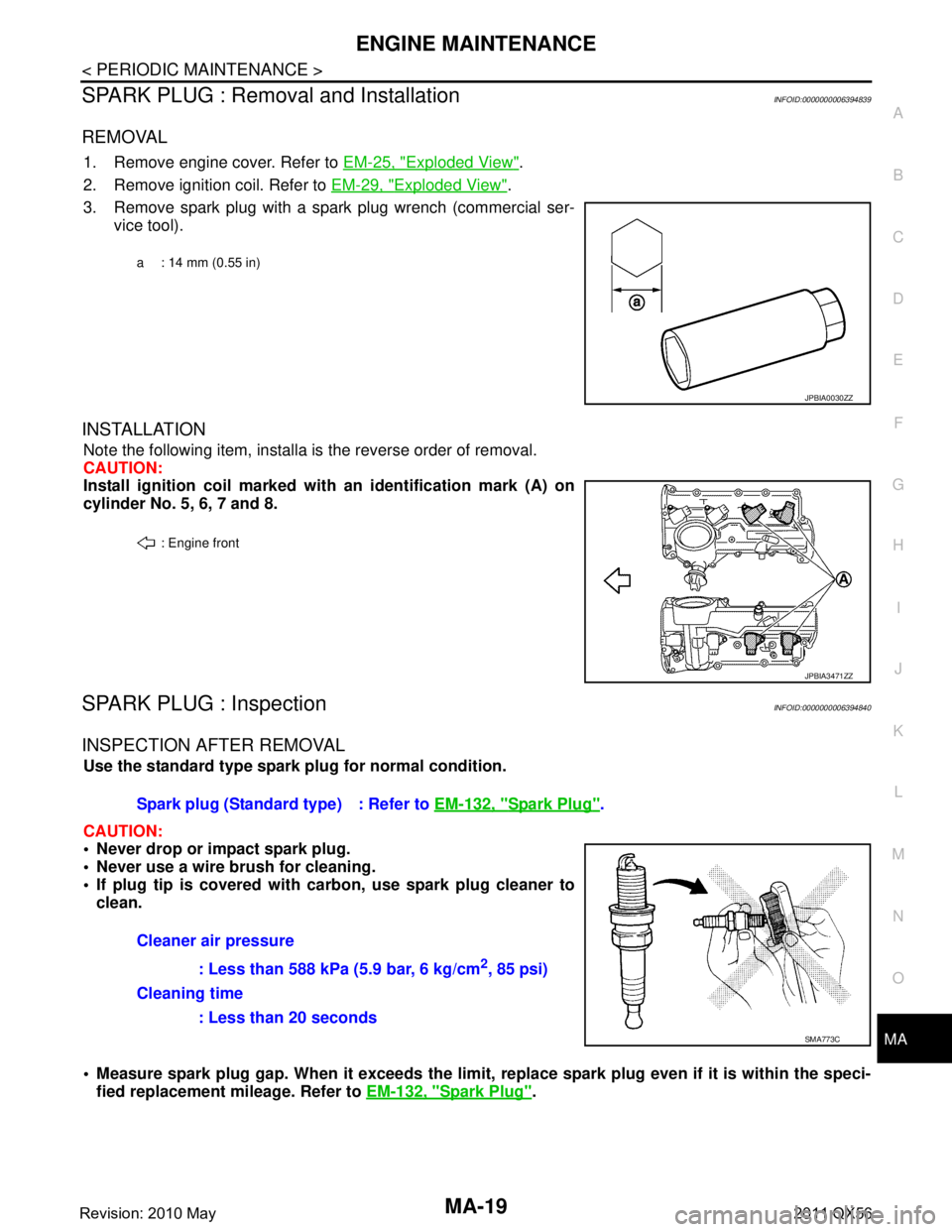
ENGINE MAINTENANCEMA-19
< PERIODIC MAINTENANCE >
C
DE
F
G H
I
J
K L
M B
MA
N
O A
SPARK PLUG : Removal and InstallationINFOID:0000000006394839
REMOVAL
1. Remove engine cover. Refer to
EM-25, "Exploded View".
2. Remove ignition coil. Refer to EM-29, "
Exploded View".
3. Remove spark plug with a spark plug wrench (commercial ser- vice tool).
INSTALLATION
Note the following item, installa is the reverse order of removal.
CAUTION:
Install ignition coil marked wi th an identification mark (A) on
cylinder No. 5, 6, 7 and 8.
SPARK PLUG : InspectionINFOID:0000000006394840
INSPECTION AFTER REMOVAL
Use the standard type spark plug for normal condition.
CAUTION:
Never drop or impact spark plug.
Never use a wire brush for cleaning.
If plug tip is covered with carbon, use spark plug cleaner to
clean.
Measure spark plug gap. When it exceeds the limit, replace spark plug even if it is within the speci-
fied replacement mileage. Refer to EM-132, "
Spark Plug".
a : 14 mm (0.55 in)
JPBIA0030ZZ
: Engine front
JPBIA3471ZZ
Spark plug (Standard type) : Refer to EM-132, "Spark Plug".
Cleaner air pressure : Less than 588 kPa (5.9 bar, 6 kg/cm
2, 85 psi)
Cleaning time
: Less than 20 seconds
SMA773C
Revision: 2010 May2011 QX56
Page 3690 of 5598
MA-20
< PERIODIC MAINTENANCE >
ENGINE MAINTENANCE
Spark plug gap adjustment is not required between replace-ment intervals.
EVAP VAPOR LINES
EVAP VAPOR LINES : InspectionINFOID:0000000006220923
1. Visually inspect EVAP vapor lines for improper attachment and for cracks, damage, loose connections,
chafing and deterioration.
2. Inspect fuel tank filler cap vacuum relief valve for clogging, sticking, etc.
Refer to EC-532, "
Inspection".
JPBIA0031ZZ
Revision: 2010 May2011 QX56
Page 3691 of 5598
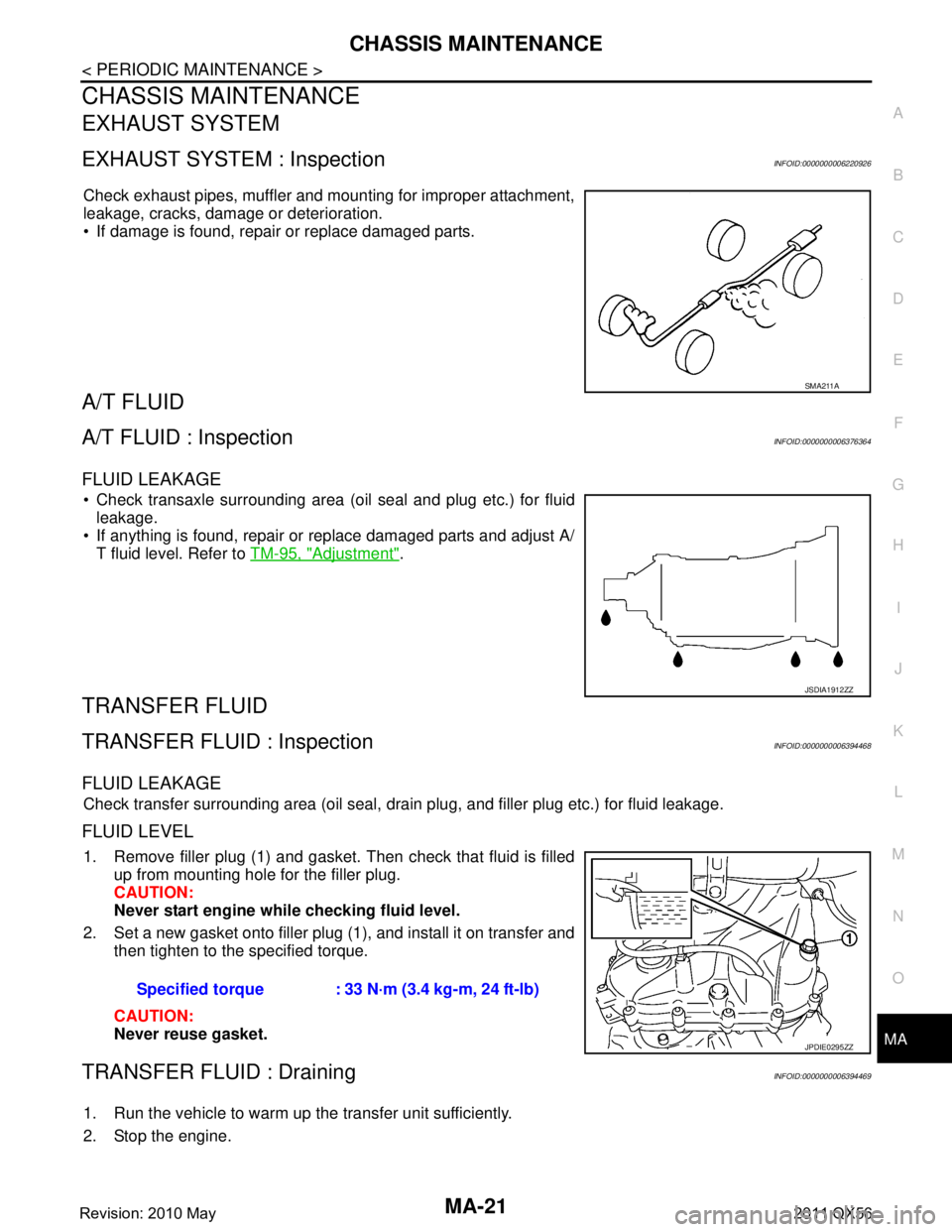
CHASSIS MAINTENANCEMA-21
< PERIODIC MAINTENANCE >
C
DE
F
G H
I
J
K L
M B
MA
N
O A
CHASSIS MAINTENANCE
EXHAUST SYSTEM
EXHAUST SYSTEM : InspectionINFOID:0000000006220926
Check exhaust pipes, muffler and mounting for improper attachment,
leakage, cracks, damage or deterioration.
If damage is found, repair or replace damaged parts.
A/T FLUID
A/T FLUID : InspectionINFOID:0000000006376364
FLUID LEAKAGE
Check transaxle surrounding area (oil seal and plug etc.) for fluid
leakage.
If anything is found, repair or replace damaged parts and adjust A/ T fluid level. Refer to TM-95, "
Adjustment".
TRANSFER FLUID
TRANSFER FLUID : InspectionINFOID:0000000006394468
FLUID LEAKAGE
Check transfer surrounding area (oil seal, drain plug, and filler plug etc.) for fluid leakage.
FLUID LEVEL
1. Remove filler plug (1) and gasket. Then check that fluid is filled
up from mounting hole for the filler plug.
CAUTION:
Never start engine whil e checking fluid level.
2. Set a new gasket onto filler plug (1), and install it on transfer and then tighten to the specified torque.
CAUTION:
Never reuse gasket.
TRANSFER FLUID : DrainingINFOID:0000000006394469
1. Run the vehicle to warm up the transfer unit sufficiently.
2. Stop the engine.
SMA211A
JSDIA1912ZZ
Specified torque : 33 N·m (3.4 kg-m, 24 ft-lb)
JPDIE0295ZZ
Revision: 2010 May2011 QX56
Page 3692 of 5598
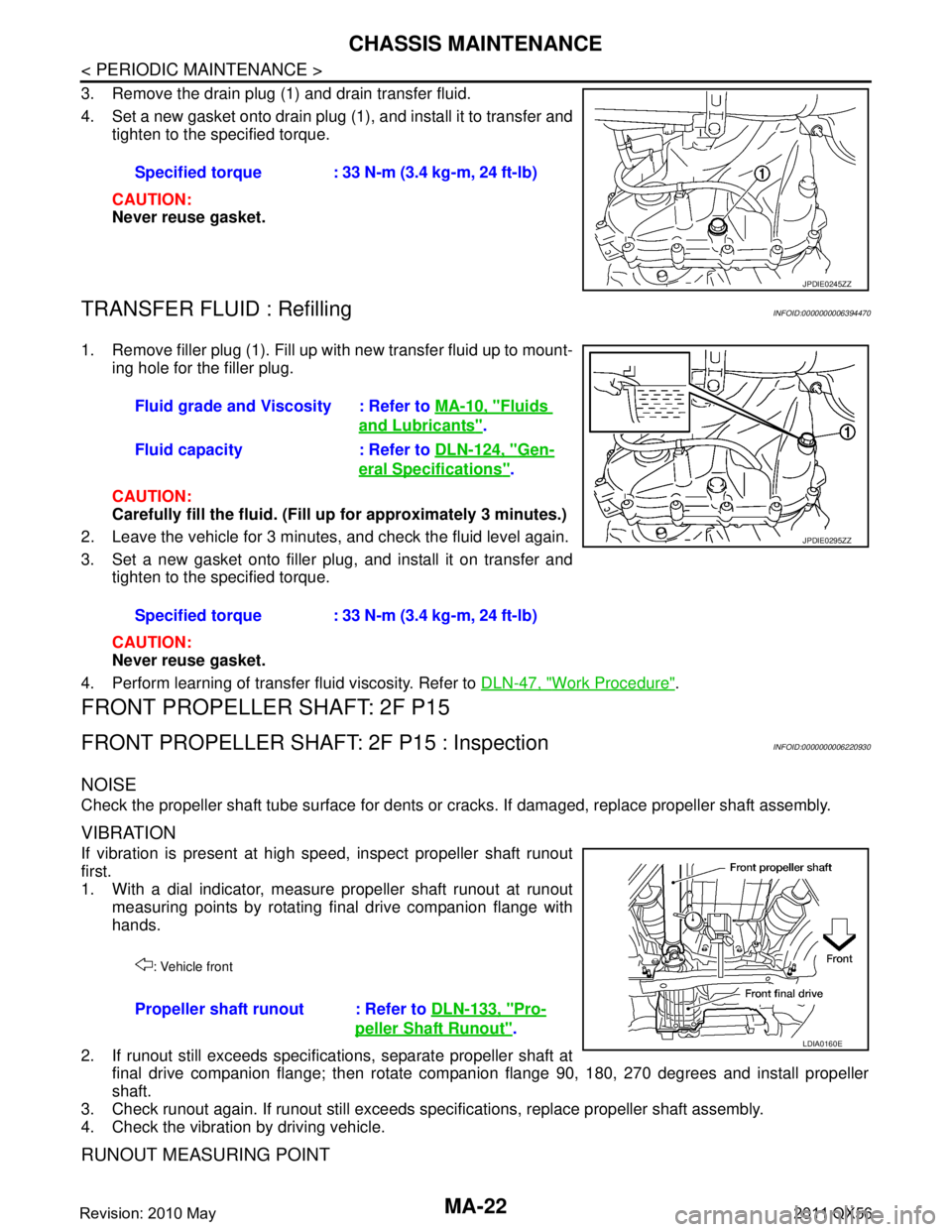
MA-22
< PERIODIC MAINTENANCE >
CHASSIS MAINTENANCE
3. Remove the drain plug (1) and drain transfer fluid.
4. Set a new gasket onto drain plug (1), and install it to transfer andtighten to the specified torque.
CAUTION:
Never reuse gasket.
TRANSFER FLUID : RefillingINFOID:0000000006394470
1. Remove filler plug (1). Fill up with new transfer fluid up to mount-
ing hole for the filler plug.
CAUTION:
Carefully fill the fluid. (Fill up for approximately 3 minutes.)
2. Leave the vehicle for 3 minutes, and check the fluid level again.
3. Set a new gasket onto filler plug, and install it on transfer and tighten to the specified torque.
CAUTION:
Never reuse gasket.
4. Perform learning of transfer fluid viscosity. Refer to DLN-47, "
Work Procedure".
FRONT PROPELLER SHAFT: 2F P15
FRONT PROPELLER SHAFT: 2F P15 : InspectionINFOID:0000000006220930
NOISE
Check the propeller shaft tube surface for dents or cr acks. If damaged, replace propeller shaft assembly.
VIBRATION
If vibration is present at high speed, inspect propeller shaft runout
first.
1. With a dial indicator, measure propeller shaft runout at runout
measuring points by rotating final drive companion flange with
hands.
2. If runout still exceeds specifications, separate propeller shaft at final drive companion flange; then rotate companion flange 90, 180, 270 degrees and install propeller
shaft.
3. Check runout again. If runout still exceeds s pecifications, replace propeller shaft assembly.
4. Check the vibration by driving vehicle.
RUNOUT MEASURING POINT
Specified torque : 33 N-m (3.4 kg-m, 24 ft-lb)
JPDIE0245ZZ
Fluid grade and Viscosity : Refer to MA-10, "Fluids
and Lubricants".
Fluid capacity : Refer to DLN-124, "
Gen-
eral Specifications".
Specified torque : 33 N-m (3.4 kg-m, 24 ft-lb)
JPDIE0295ZZ
: Vehicle front
Propeller shaft runout : Refer to DLN-133, "Pro-
peller Shaft Runout".LDIA0160E
Revision: 2010 May2011 QX56
Page 3693 of 5598
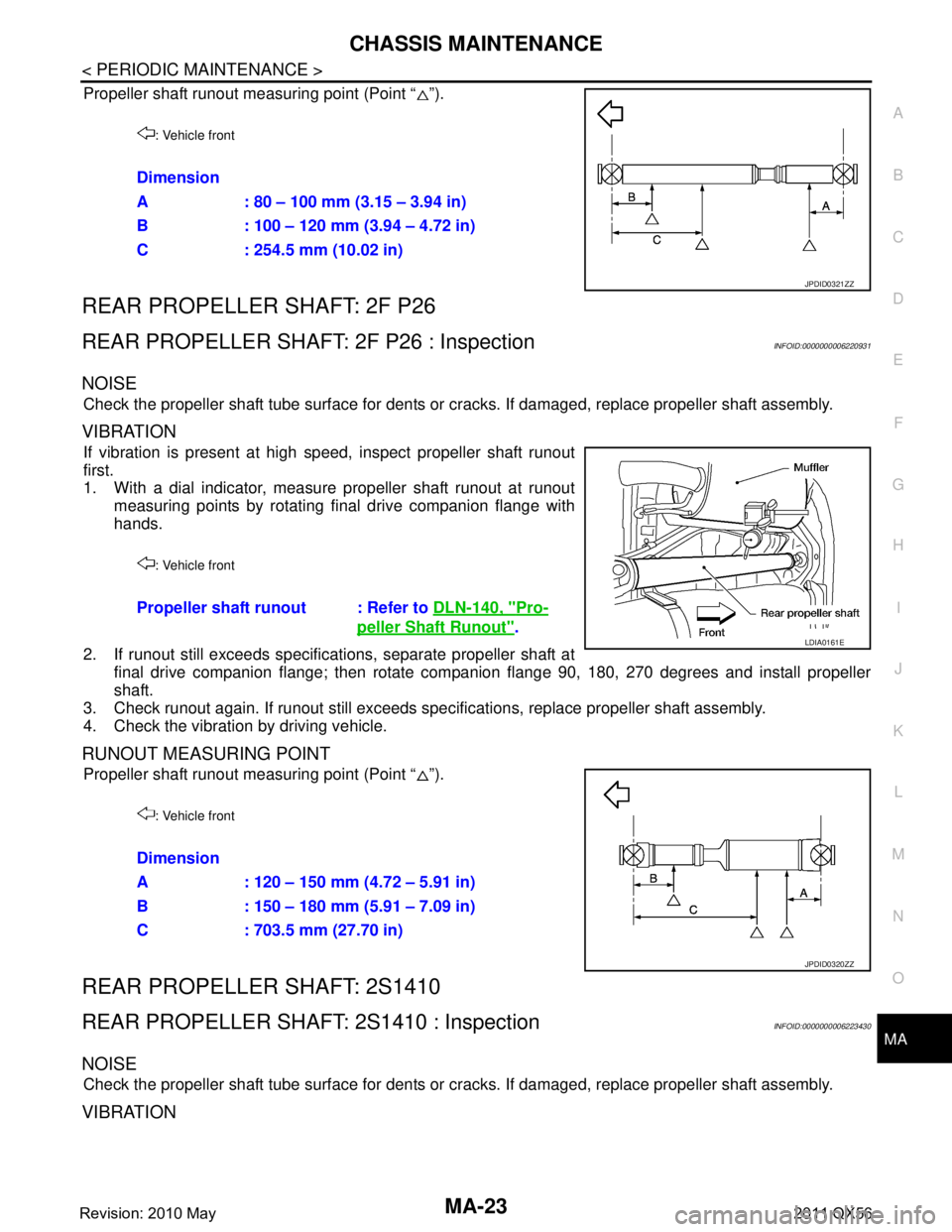
CHASSIS MAINTENANCEMA-23
< PERIODIC MAINTENANCE >
C
DE
F
G H
I
J
K L
M B
MA
N
O A
Propeller shaft runout measuring point (Point “ ”).
REAR PROPELLER SHAFT: 2F P26
REAR PROPELLER SHAFT: 2F P26 : InspectionINFOID:0000000006220931
NOISE
Check the propeller shaft tube surface for dents or cr
acks. If damaged, replace propeller shaft assembly.
VIBRATION
If vibration is present at high speed, inspect propeller shaft runout
first.
1. With a dial indicator, measure propeller shaft runout at runout measuring points by rotating final drive companion flange with
hands.
2. If runout still exceeds specifications, separate propeller shaft at final drive companion flange; then rotate companion flange 90, 180, 270 degrees and install propeller
shaft.
3. Check runout again. If runout still exceeds spec ifications, replace propeller shaft assembly.
4. Check the vibration by driving vehicle.
RUNOUT MEASURING POINT
Propeller shaft runout measuring point (Point “ ”).
REAR PROPELLER SHAFT: 2S1410
REAR PROPELLER SHAFT: 2S1410 : InspectionINFOID:0000000006223430
NOISE
Check the propeller shaft tube surface for dents or cr acks. If damaged, replace propeller shaft assembly.
VIBRATION
: Vehicle front
Dimension
A : 80 – 100 mm (3.15 – 3.94 in)
B : 100 – 120 mm (3.94 – 4.72 in)
C : 254.5 mm (10.02 in)
JPDID0321ZZ
: Vehicle front
Propeller shaft runout : Refer to DLN-140, "Pro-
peller Shaft Runout".LDIA0161E
: Vehicle front
Dimension
A : 120 – 150 mm (4.72 – 5.91 in)
B : 150 – 180 mm (5.91 – 7.09 in)
C : 703.5 mm (27.70 in)
JPDID0320ZZ
Revision: 2010 May2011 QX56
Page 3694 of 5598
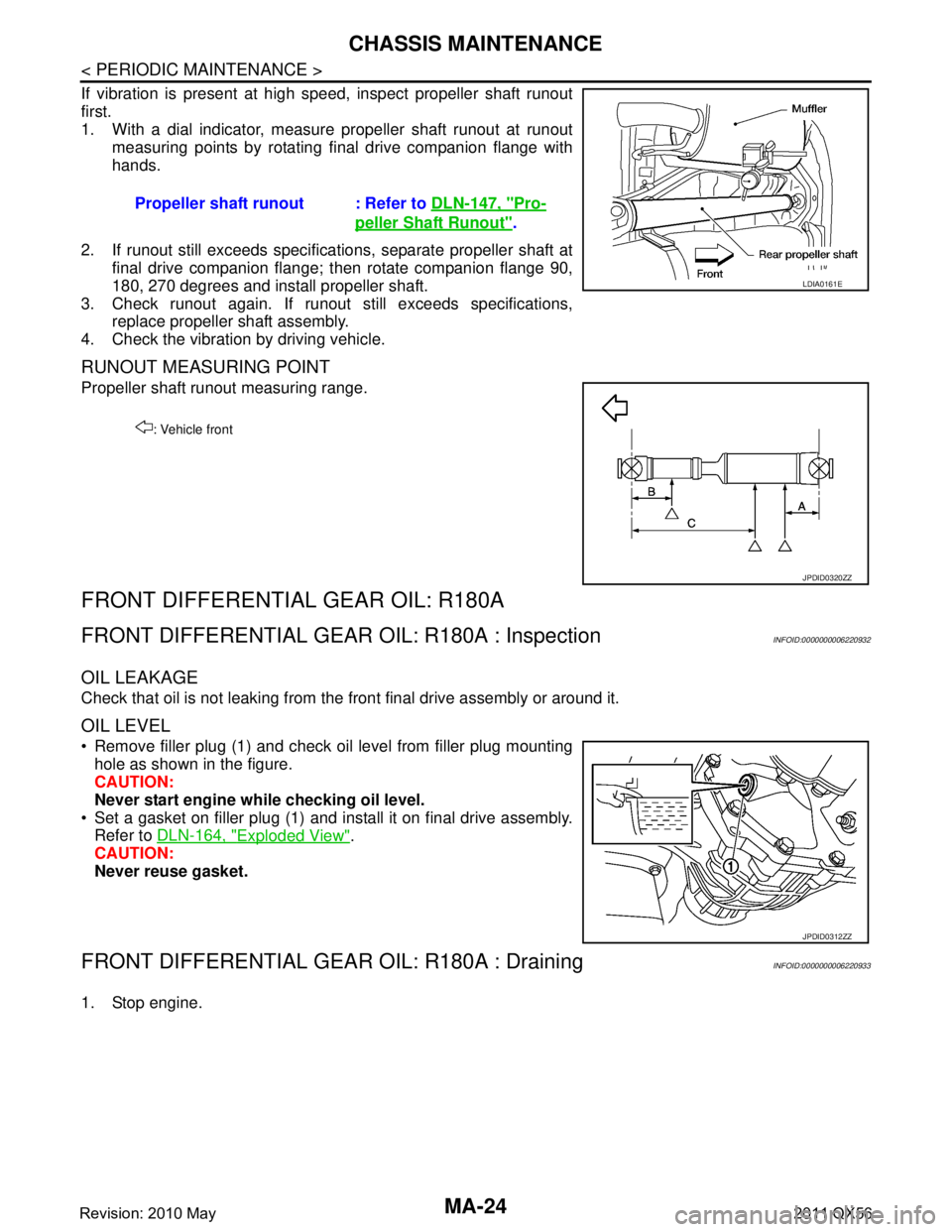
MA-24
< PERIODIC MAINTENANCE >
CHASSIS MAINTENANCE
If vibration is present at high speed, inspect propeller shaft runout
first.
1. With a dial indicator, measure propeller shaft runout at runoutmeasuring points by rotating final drive companion flange with
hands.
2. If runout still exceeds specifications, separate propeller shaft at final drive companion flange; then rotate companion flange 90,
180, 270 degrees and install propeller shaft.
3. Check runout again. If runout still exceeds specifications, replace propeller shaft assembly.
4. Check the vibration by driving vehicle.
RUNOUT MEASURING POINT
Propeller shaft runout measuring range.
FRONT DIFFERENTIAL GEAR OIL: R180A
FRONT DIFFERENTIAL GEAR OIL: R180A : InspectionINFOID:0000000006220932
OIL LEAKAGE
Check that oil is not leaking from the front final drive assembly or around it.
OIL LEVEL
Remove filler plug (1) and check oil level from filler plug mounting
hole as shown in the figure.
CAUTION:
Never start engine while checking oil level.
Set a gasket on filler plug (1) and install it on final drive assembly. Refer to DLN-164, "
Exploded View".
CAUTION:
Never reuse gasket.
FRONT DIFFERENTIAL GEAR OIL: R180A : DrainingINFOID:0000000006220933
1. Stop engine.Propeller shaft runout : Refer to
DLN-147, "
Pro-
peller Shaft Runout".
LDIA0161E
: Vehicle front
JPDID0320ZZ
JPDID0312ZZ
Revision: 2010 May2011 QX56
Page 3695 of 5598
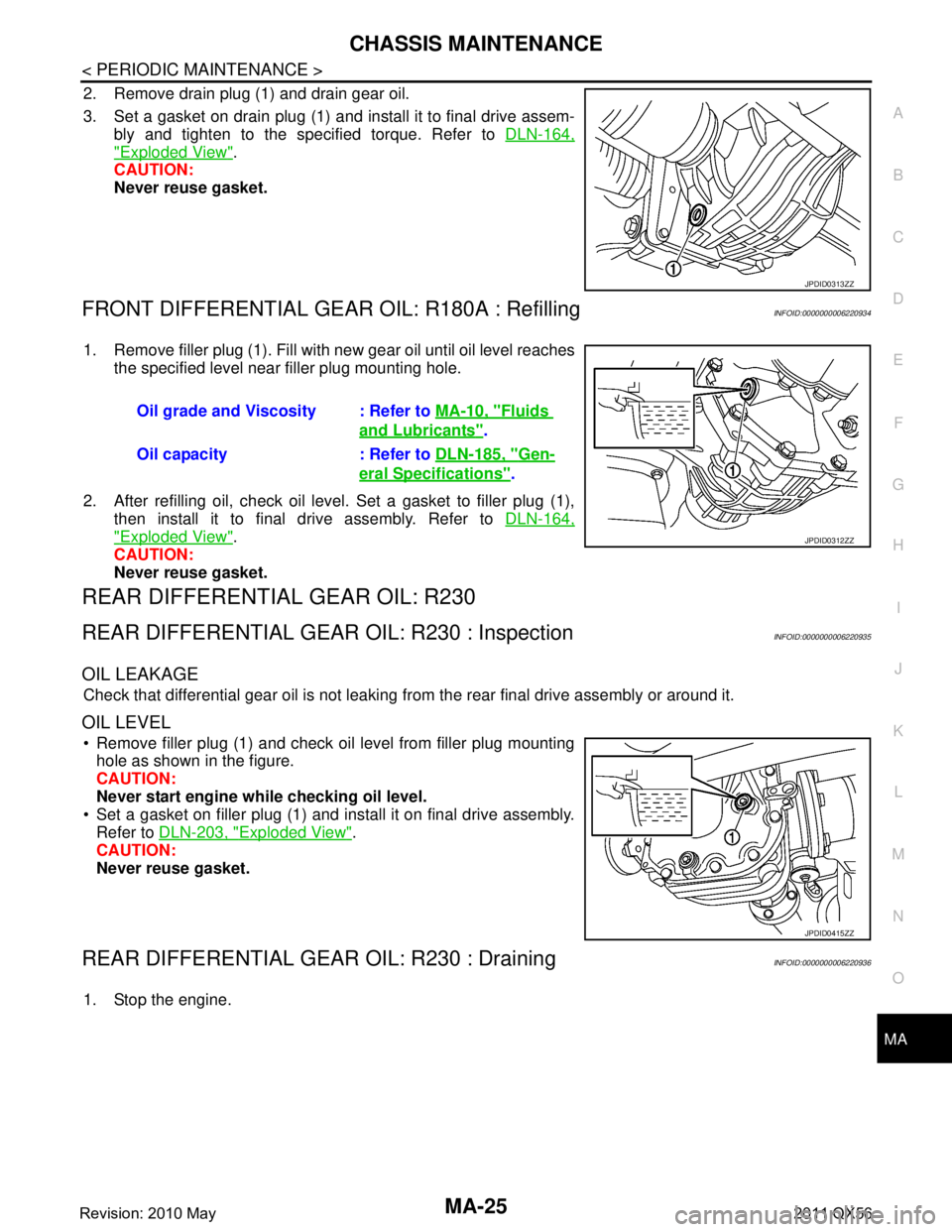
CHASSIS MAINTENANCEMA-25
< PERIODIC MAINTENANCE >
C
DE
F
G H
I
J
K L
M B
MA
N
O A
2. Remove drain plug (1) and drain gear oil.
3. Set a gasket on drain plug (1) and install it to final drive assem-
bly and tighten to the specified torque. Refer to DLN-164,
"Exploded View".
CAUTION:
Never reuse gasket.
FRONT DIFFERENTIAL GEAR OIL: R180A : RefillingINFOID:0000000006220934
1. Remove filler plug (1). Fill with new gear oil until oil level reaches
the specified level near filler plug mounting hole.
2. After refilling oil, check oil level. Set a gasket to filler plug (1), then install it to final drive assembly. Refer to DLN-164,
"Exploded View".
CAUTION:
Never reuse gasket.
REAR DIFFERENTIAL GEAR OIL: R230
REAR DIFFERENTIAL GEAR OIL: R230 : InspectionINFOID:0000000006220935
OIL LEAKAGE
Check that differential gear oil is not leaking fr om the rear final drive assembly or around it.
OIL LEVEL
Remove filler plug (1) and check oil level from filler plug mounting
hole as shown in the figure.
CAUTION:
Never start engine while checking oil level.
Set a gasket on filler plug (1) and install it on final drive assembly. Refer to DLN-203, "
Exploded View".
CAUTION:
Never reuse gasket.
REAR DIFFERENTIAL GEAR OIL: R230 : DrainingINFOID:0000000006220936
1. Stop the engine.
JPDID0313ZZ
Oil grade and Viscosity : Refer to MA-10, "Fluids
and Lubricants".
Oil capacity : Refer to DLN-185, "
Gen-
eral Specifications".
JPDID0312ZZ
JPDID0415ZZ
Revision: 2010 May2011 QX56
Page 3696 of 5598
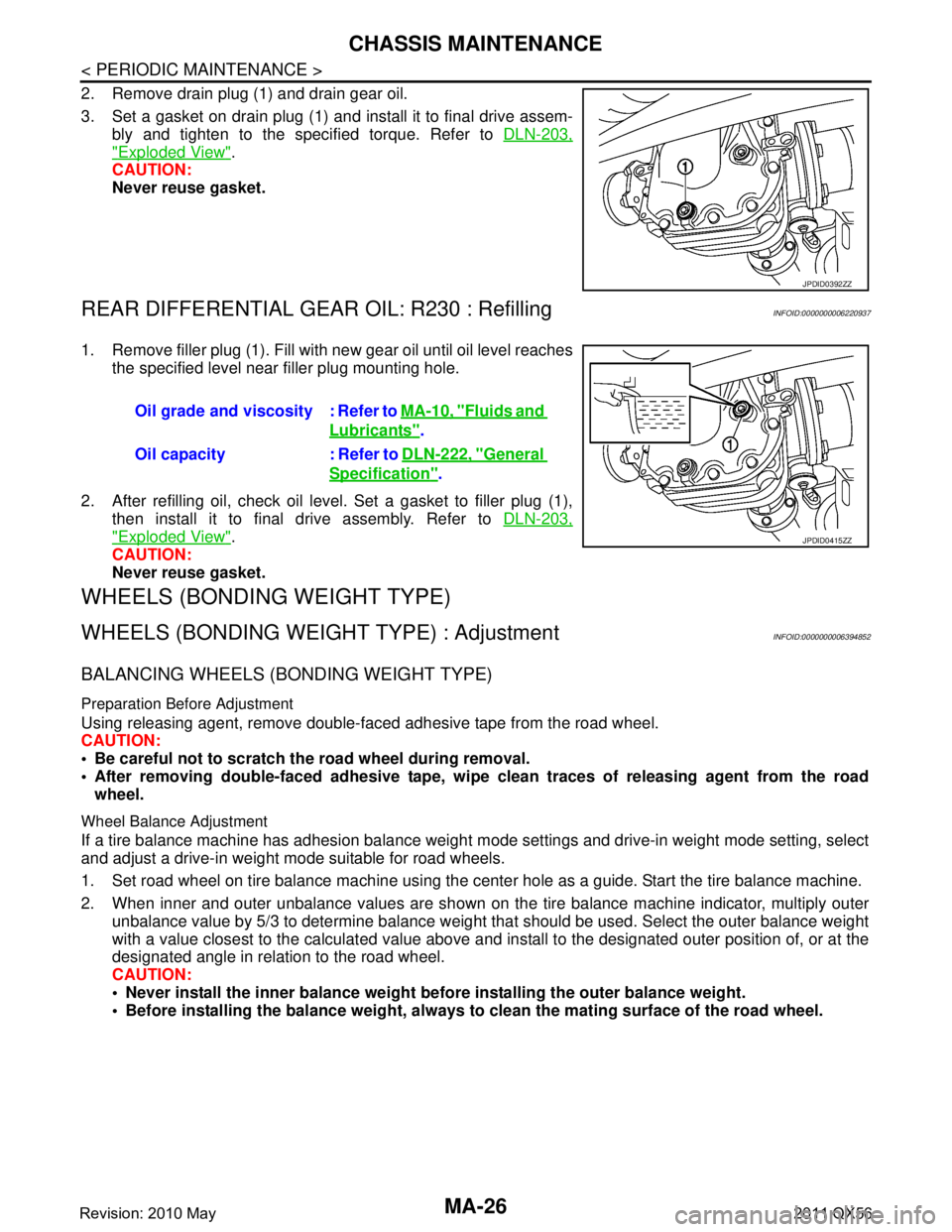
MA-26
< PERIODIC MAINTENANCE >
CHASSIS MAINTENANCE
2. Remove drain plug (1) and drain gear oil.
3. Set a gasket on drain plug (1) and install it to final drive assem-bly and tighten to the specified torque. Refer to DLN-203,
"Exploded View".
CAUTION:
Never reuse gasket.
REAR DIFFERENTIAL GEAR OIL: R230 : RefillingINFOID:0000000006220937
1. Remove filler plug (1). Fill with new gear oil until oil level reaches
the specified level near filler plug mounting hole.
2. After refilling oil, check oil level. Set a gasket to filler plug (1), then install it to final drive assembly. Refer to DLN-203,
"Exploded View".
CAUTION:
Never reuse gasket.
WHEELS (BONDING WEIGHT TYPE)
WHEELS (BONDING WEIG HT TYPE) : AdjustmentINFOID:0000000006394852
BALANCING WHEELS (BONDING WEIGHT TYPE)
Preparation Before Adjustment
Using releasing agent, remove double-faced adhesive tape from the road wheel.
CAUTION:
Be careful not to scratch th e road wheel during removal.
After removing double-faced adhesive tape, wi pe clean traces of releasing agent from the road
wheel.
Wheel Balance Adjustment
If a tire balance machine has adhesion balance weight m ode settings and drive-in weight mode setting, select
and adjust a drive-in weight mode suitable for road wheels.
1. Set road wheel on tire balance machine using the center hole as a guide. Start the tire balance machine.
2. When inner and outer unbalance values are shown on the tire balance machine indicator, multiply outer unbalance value by 5/3 to determine balance weight t hat should be used. Select the outer balance weight
with a value closest to the calculated value above and in stall to the designated outer position of, or at the
designated angle in relation to the road wheel.
CAUTION:
Never install the inner balance weight be fore installing the outer balance weight.
Before installing the balance weight, always to clean the mating surface of the road wheel.
JPDID0392ZZ
Oil grade and viscosity : Refer to MA-10, "Fluids and
Lubricants".
Oil capacity : Refer to DLN-222, "
General
Specification".
JPDID0415ZZ
Revision: 2010 May2011 QX56