Page 3081 of 5598
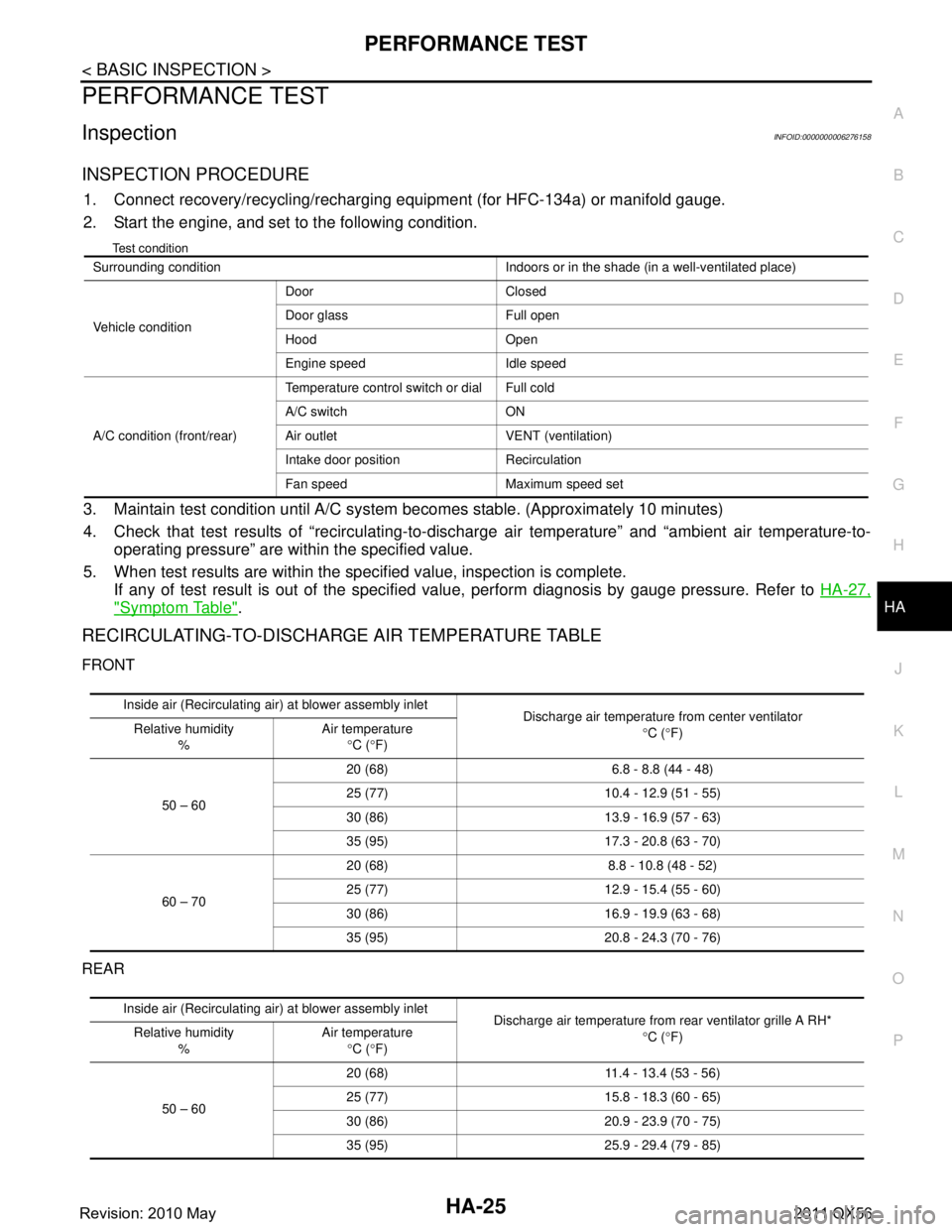
PERFORMANCE TESTHA-25
< BASIC INSPECTION >
C
DE
F
G H
J
K L
M A
B
HA
N
O P
PERFORMANCE TEST
InspectionINFOID:0000000006276158
INSPECTION PROCEDURE
1. Connect recovery/recycling/recharging equipment (for HFC-134a) or manifold gauge.
2. Start the engine, and set to the following condition.
Test condition
3. Maintain test condition until A/C system becomes stable. (Approximately 10 minutes)
4. Check that test results of “recirculating-to-disc harge air temperature” and “ambient air temperature-to-
operating pressure” are within the specified value.
5. When test results are within the specified value, inspection is complete. If any of test result is out of the specified value, perform diagnosis by gauge pressure. Refer to HA-27,
"Symptom Table".
RECIRCULATING-TO-DISCHARGE AIR TEMPERATURE TABLE
FRONT
REAR
Surrounding condition Indoors or in the shade (in a well-ventilated place)
Vehicle conditionDoor Closed
Door glass Full open
Hood Open
Engine speed Idle speed
A/C condition (front/rear) Temperature control switch or dial Full cold
A/C switch ON
Air outlet VENT (ventilation)
Intake door position Recirculation
Fan speed Maximum speed set
Inside air (Recirculating air) at blower assembly inlet
Discharge air temperature from center ventilator
°C ( °F)
Relative humidity
% Air temperature
°C ( °F)
50 – 60 20 (68) 6.8 - 8.8 (44 - 48)
25 (77) 10.4 -
12.9 (51 - 55)
30 (86) 13.9 - 16.9 (57 - 63)
35 (95) 17.3 - 20.8 (63 - 70)
60 – 70 20 (68) 8.8 - 10.8 (48 - 52)
25 (77) 12.9 -
15.4 (55 - 60)
30 (86) 16.9 - 19.9 (63 - 68)
35 (95) 20.8 - 24.3 (70 - 76)
Inside air (Recirculating air) at blower assembly inlet
Discharge air temperature from rear ventilator grille A RH*
°C ( °F)
Relative humidity
% Air temperature
°C ( °F)
50 – 60 20 (68) 11.4 -
13.4 (53 - 56)
25 (77) 15.8 - 18.3 (60 - 65)
30 (86) 20.9 - 23.9 (70 - 75)
35 (95) 25.9 - 29.4 (79 - 85)
Revision: 2010 May2011 QX56
Page 3082 of 5598
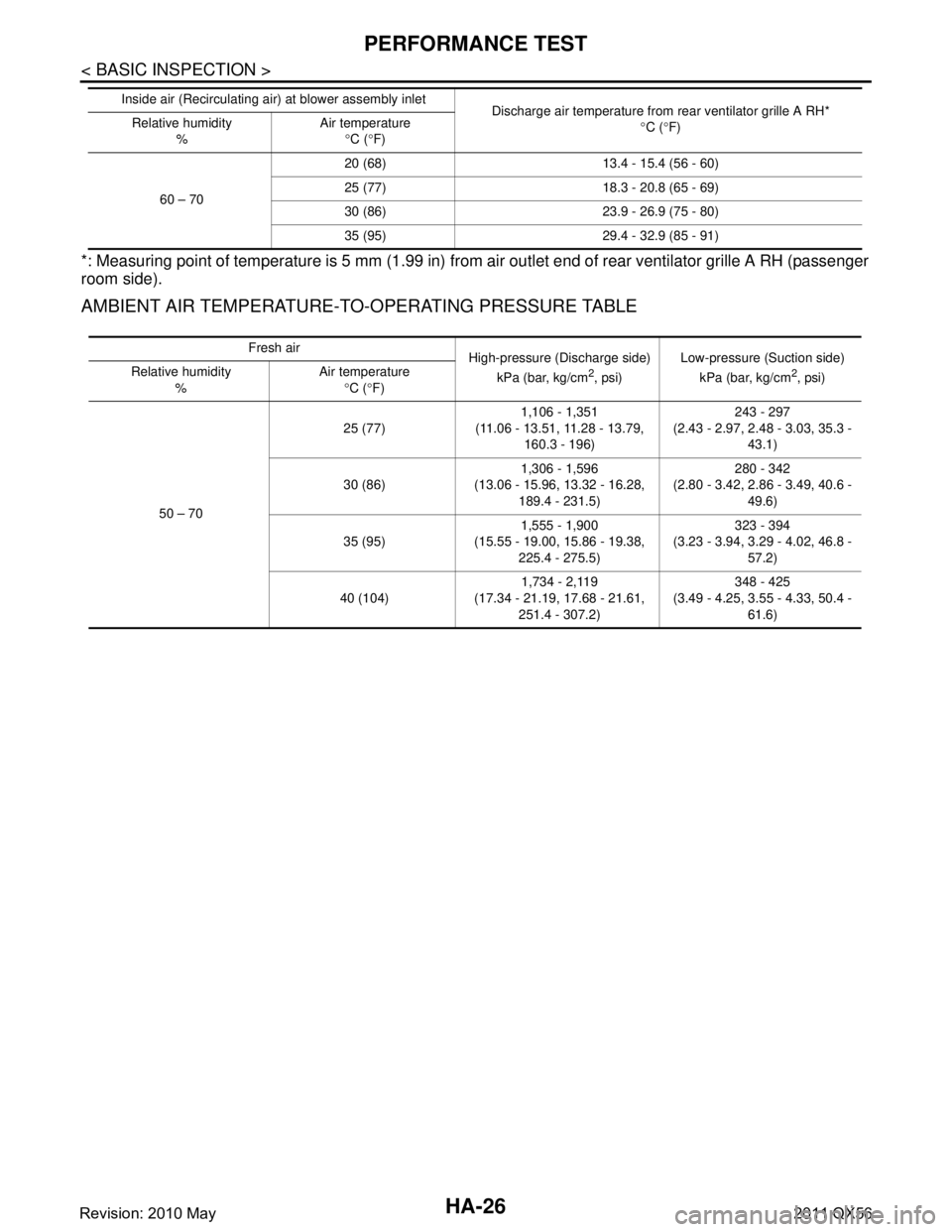
HA-26
< BASIC INSPECTION >
PERFORMANCE TEST
*: Measuring point of temperature is 5 mm (1.99 in) from air outlet end of rear ventilator grille A RH (passenger
room side).
AMBIENT AIR TEMPERATURE-TO-OPERATING PRESSURE TABLE
60 – 70 20 (68) 13.4 - 15.4 (56 - 60)
25 (77) 18.3 - 20.8 (65 - 69)
30 (86) 23.9 - 26.9 (75 - 80)
35 (95) 29.4 - 32.9 (85 - 91)
Inside air (Recirculating air) at blower assembly inlet
Discharge air temperature from rear ventilator grille A RH*
°C ( °F)
Relative humidity
% Air temperature
°C ( °F)
Fresh air
High-pressure (Discharge side)
kPa (bar, kg/cm
2, psi) Low-pressure (Suction side)
kPa (bar, kg/cm2, psi)
Relative humidity
% Air temperature
°C ( °F)
50 – 70 25 (77)
1,106 - 1,351
(11.06 - 13.51, 11.28 - 13.79, 160.3 - 196) 243 - 297
(2.43 - 2.97, 2.48 - 3.03, 35.3 - 43.1)
30 (86) 1,306 - 1,596
(13.06 - 15.96, 13.32 - 16.28,
189.4 - 231.5) 280 - 342
(2.80 - 3.42, 2.86 - 3.49, 40.6 -
49.6)
35 (95) 1,555 - 1,900
(15.55 - 19.00, 15.86 - 19.38, 225.4 - 275.5) 323 - 394
(3.23 - 3.94, 3.29 - 4.02, 46.8 - 57.2)
40 (104) 1,734 - 2,119
(17.34 - 21.19, 17.68 - 21.61, 251.4 - 307.2) 348 - 425
(3.49 - 4.25, 3.55 - 4.33, 50.4 - 61.6)
Revision: 2010 May2011 QX56
Page 3083 of 5598
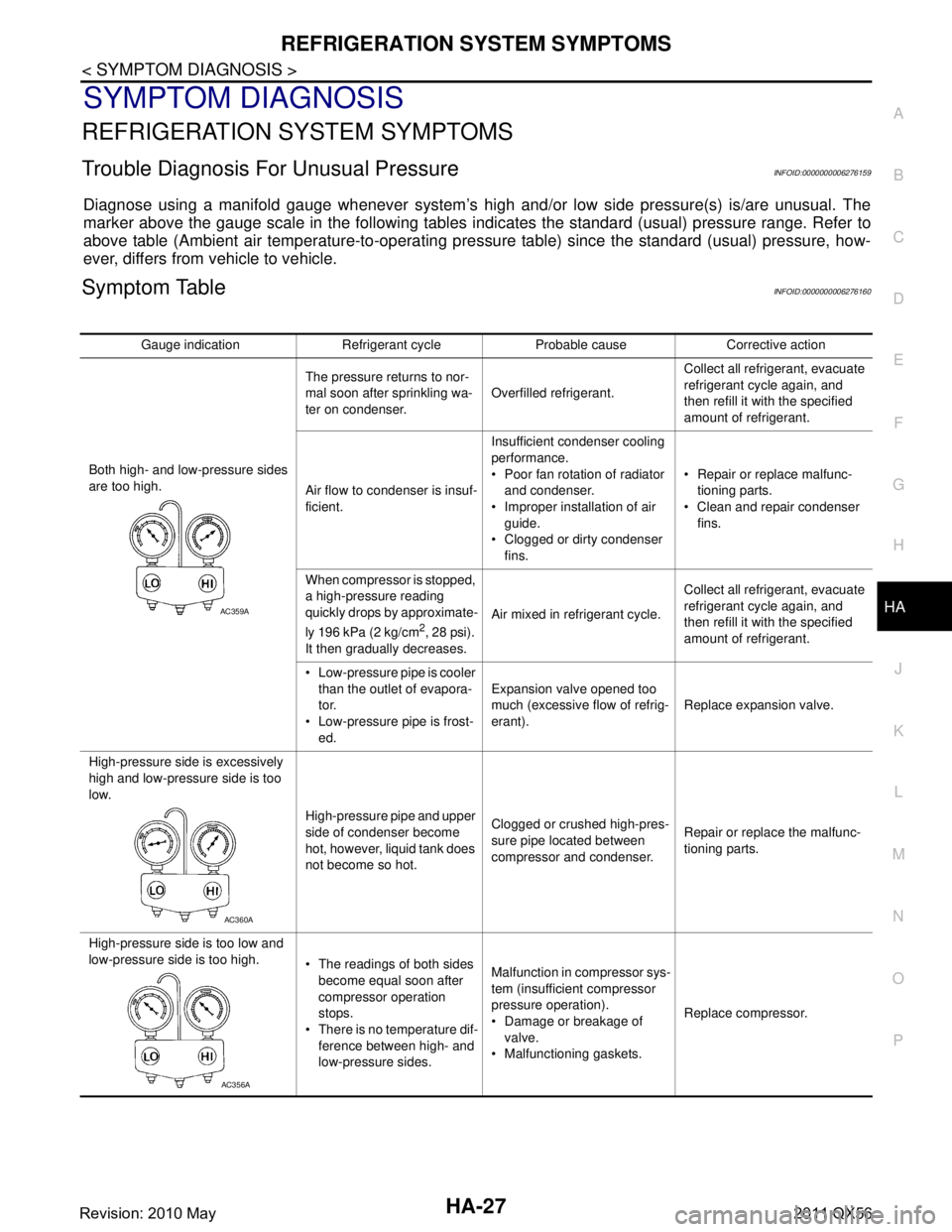
REFRIGERATION SYSTEM SYMPTOMSHA-27
< SYMPTOM DIAGNOSIS >
C
DE
F
G H
J
K L
M A
B
HA
N
O P
SYMPTOM DIAGNOSIS
REFRIGERATION SYSTEM SYMPTOMS
Trouble Diagnosis For Unusual PressureINFOID:0000000006276159
Diagnose using a manifold gauge whenever system’s high and/or low side pressure(s) is/are unusual. The
marker above the gauge scale in the following tables i ndicates the standard (usual) pressure range. Refer to
above table (Ambient air temperature-to-operating pre ssure table) since the standard (usual) pressure, how-
ever, differs from vehicle to vehicle.
Symptom TableINFOID:0000000006276160
Gauge indication Refrigerant cycle Probable cause Corrective action
Both high- and low-pressure sides
are too high. The pressure returns to nor-
mal soon after sprinkling wa-
ter on condenser.
Overfilled refrigerant. Collect all refrigerant, evacuate
refrigerant cycle again, and
then refill it with the specified
amount of refrigerant.
Air flow to condenser is insuf-
ficient. Insufficient condenser cooling
performance.
Poor fan rotation of radiator
and condenser.
Improper installation of air guide.
Clogged or dirty condenser fins. Repair or replace malfunc-
tioning parts.
Clean and repair condenser fins.
When compressor is stopped,
a high-pressure reading
quickly drops by approximate-
ly 196 kPa (2 kg/cm
2, 28 psi).
It then gradually decreases. Air mixed in refrigerant cycle.
Collect all refrigerant, evacuate
refrigerant cycle again, and
then refill it with the specified
amount of refrigerant.
Low-pressure pipe is cooler than the outlet of evapora-
tor.
Low-pressure pipe is frost- ed. Expansion valve opened too
much (excessive flow of refrig-
erant).
Replace expansion valve.
High-pressure side is excessively
high and low-pressure side is too
low. High-pressure pipe and upper
side of condenser become
hot, however, liquid tank does
not become so hot.Clogged or crushed high-pres-
sure pipe located between
compressor and condenser.
Repair or replace the malfunc-
tioning parts.
High-pressure side is too low and
low-pressure side is too high. The readings of both sides
become equal soon after
compressor operation
stops.
There is no temperature dif- ference between high- and
low-pressure sides. Malfunction in compressor sys-
tem (insufficient compressor
pressure operation).
Damage or breakage of
valve.
Malfunctioning gaskets. Replace compressor.
AC359A
AC360A
AC356A
Revision: 2010 May2011 QX56
Page 3084 of 5598
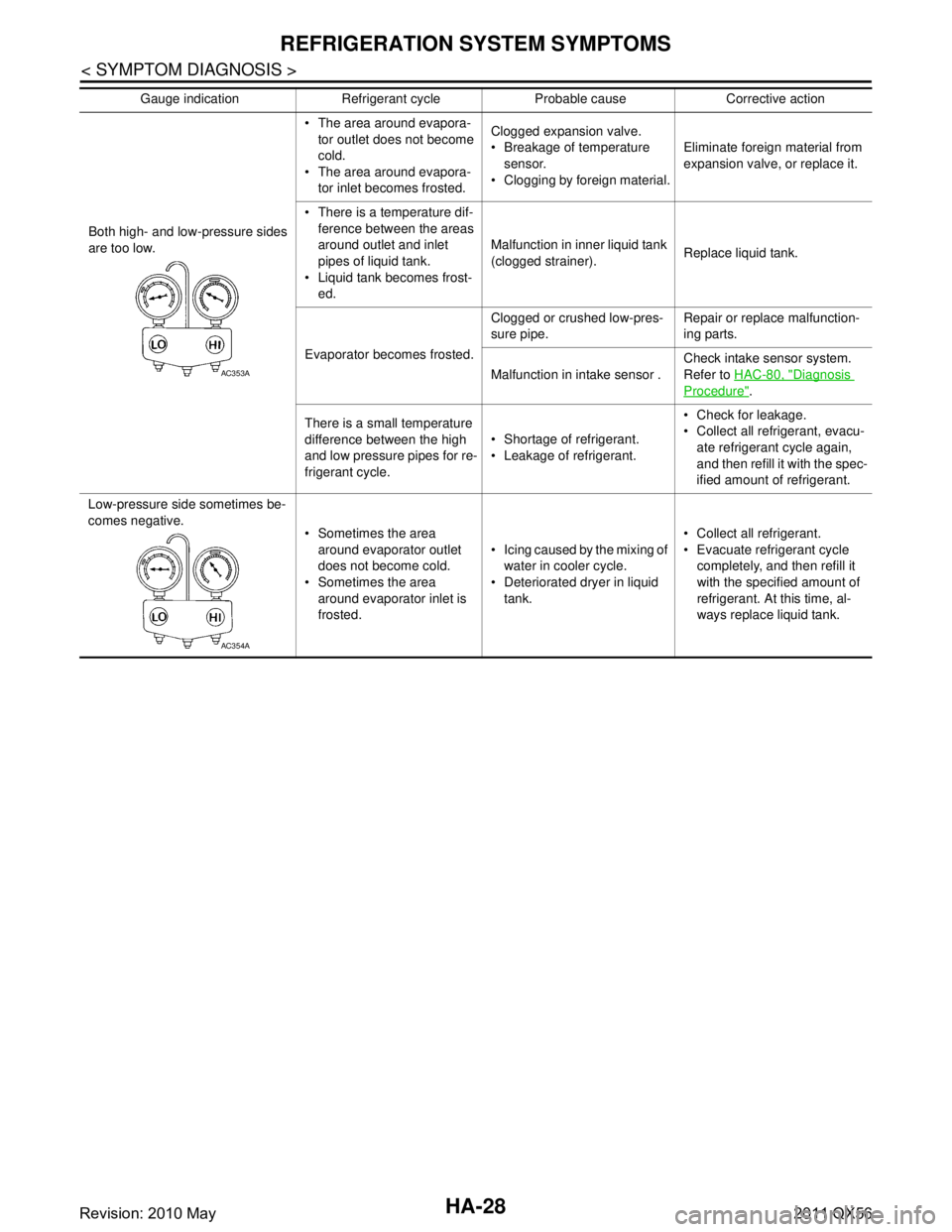
HA-28
< SYMPTOM DIAGNOSIS >
REFRIGERATION SYSTEM SYMPTOMS
Both high- and low-pressure sides
are too low. The area around evapora-
tor outlet does not become
cold.
The area around evapora- tor inlet becomes frosted. Clogged expansion valve.
Breakage of temperature
sensor.
Clogging by foreign material. Eliminate foreign material from
expansion valve, or replace it.
There is a temperature dif- ference between the areas
around outlet and inlet
pipes of liquid tank.
Liquid tank becomes frost- ed. Malfunction in inner liquid tank
(clogged strainer).
Replace liquid tank.
Evaporator becomes frosted. Clogged or crushed low-pres-
sure pipe.
Repair or replace malfunction-
ing parts.
Malfunction in intake sensor . Check intake sensor system.
Refer to
HAC-80, "
Diagnosis
Procedure".
There is a small temperature
difference between the high
and low pressure pipes for re-
frigerant cycle. Shortage of refrigerant.
Leakage of refrigerant. Check for leakage.
Collect all refrigerant, evacu-
ate refrigerant cycle again,
and then refill it with the spec-
ified amount of refrigerant.
Low-pressure side sometimes be-
comes negative. Sometimes the area
around evaporator outlet
does not become cold.
Sometimes the area
around evaporator inlet is
frosted. Icing caused by the mixing of
water in cooler cycle.
Deteriorated dryer in liquid
tank. Collect all refrigerant.
Evacuate refrigerant cycle
completely, and then refill it
with the specified amount of
refrigerant. At this time, al-
ways replace liquid tank.
Gauge indication Refrigerant cycle Probable cause Corrective action
AC353A
AC354A
Revision: 2010 May2011 QX56
Page 3085 of 5598
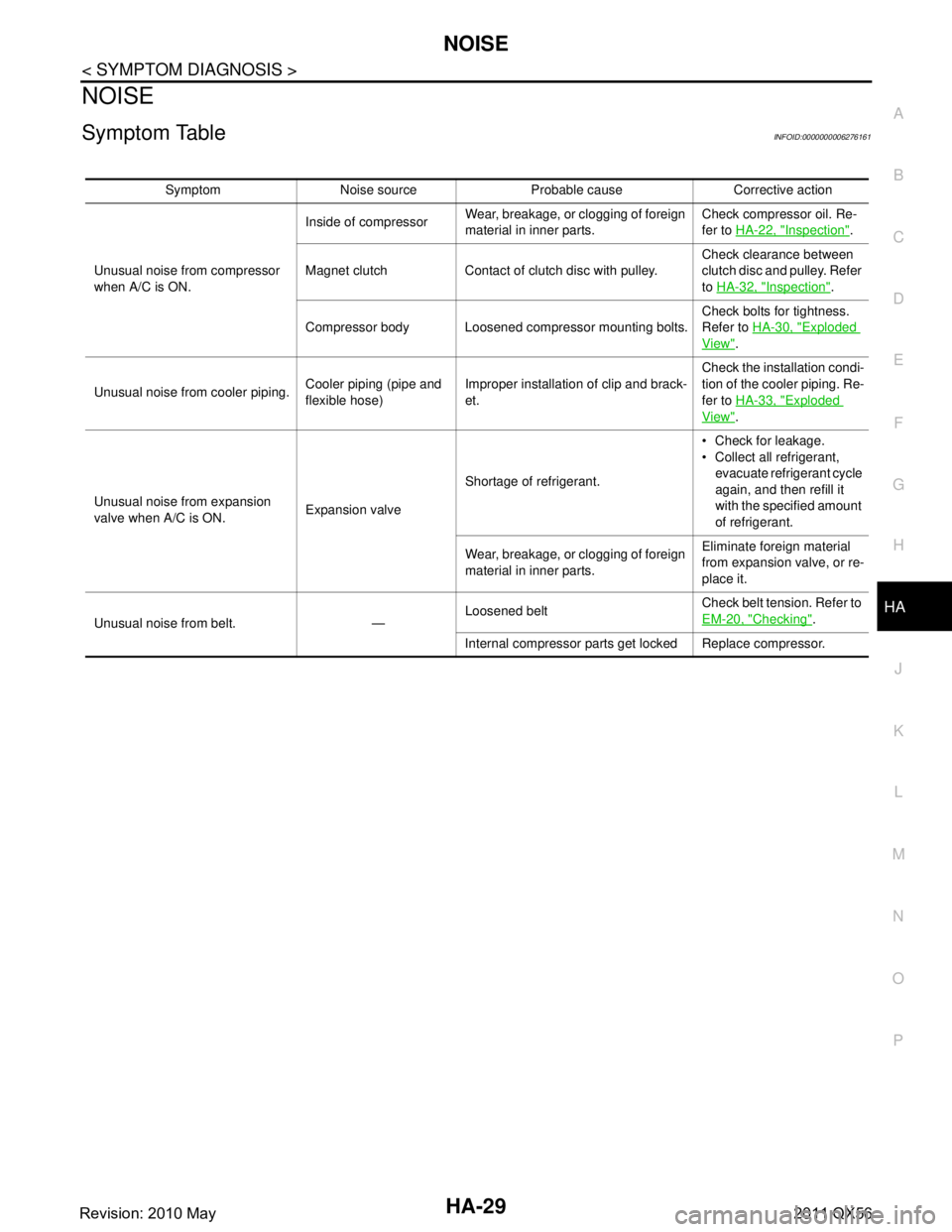
NOISEHA-29
< SYMPTOM DIAGNOSIS >
C
DE
F
G H
J
K L
M A
B
HA
N
O P
NOISE
Symptom TableINFOID:0000000006276161
Symptom Noise source Probable cause Corrective action
Unusual noise from compressor
when A/C is ON. Inside of compressor
Wear, breakage, or clogging of foreign
material in inner parts. Check compressor oil. Re-
fer to
HA-22, "
Inspection".
Magnet clutch Contact of clutch disc with pulley. Check clearance between
clutch disc and pulley. Refer
to
HA-32, "
Inspection".
Compressor body Loosened compressor mounting bolts. Check bolts for tightness.
Refer to
HA-30, "
Exploded
View".
Unusual noise from cooler piping. Cooler piping (pipe and
flexible hose)Improper installation of clip and brack-
et. Check the installation condi-
tion of the cooler piping. Re-
fer to
HA-33, "
Exploded
View".
Unusual noise from expansion
valve when A/C is ON. Expansion valveShortage of refrigerant. Check for leakage.
Collect all refrigerant,
evacuate refrigerant cycle
again, and then refill it
with the specified amount
of refrigerant.
Wear, breakage, or clogging of foreign
material in inner parts. Eliminate foreign material
from expansion valve, or re-
place it.
Unusual noise from belt. — Loosened belt
Check belt tension. Refer to
EM-20, "
Checking".
Internal compressor parts ge t locked Replace compressor.
Revision: 2010 May2011 QX56
Page 3086 of 5598
HA-30
< REMOVAL AND INSTALLATION >
COMPRESSOR
REMOVAL AND INSTALLATION
COMPRESSOR
Exploded ViewINFOID:0000000006276162
REMOVAL
DISASSEMBLY
COMPRESSOR
COMPRESSOR : Removal and InstallationINFOID:0000000006276163
CAUTION:
1. High-pressure flexible hose 2. O-ring 3. Compressor
4. Low-pressure flexible hose
A. To condenser B. To evaporator
Refer to GI-4, "
Components" for symbols in the figure.
JMIIA0622GB
1. Clutch disc 2. Shim 3. Snap ring
4. Pulley assembly 5. Field coil 6. Compressor unit
Refer to GI-4, "
Components" for symbols in the figure.
JMIIA0805GB
Revision: 2010 May2011 QX56
Page 3087 of 5598
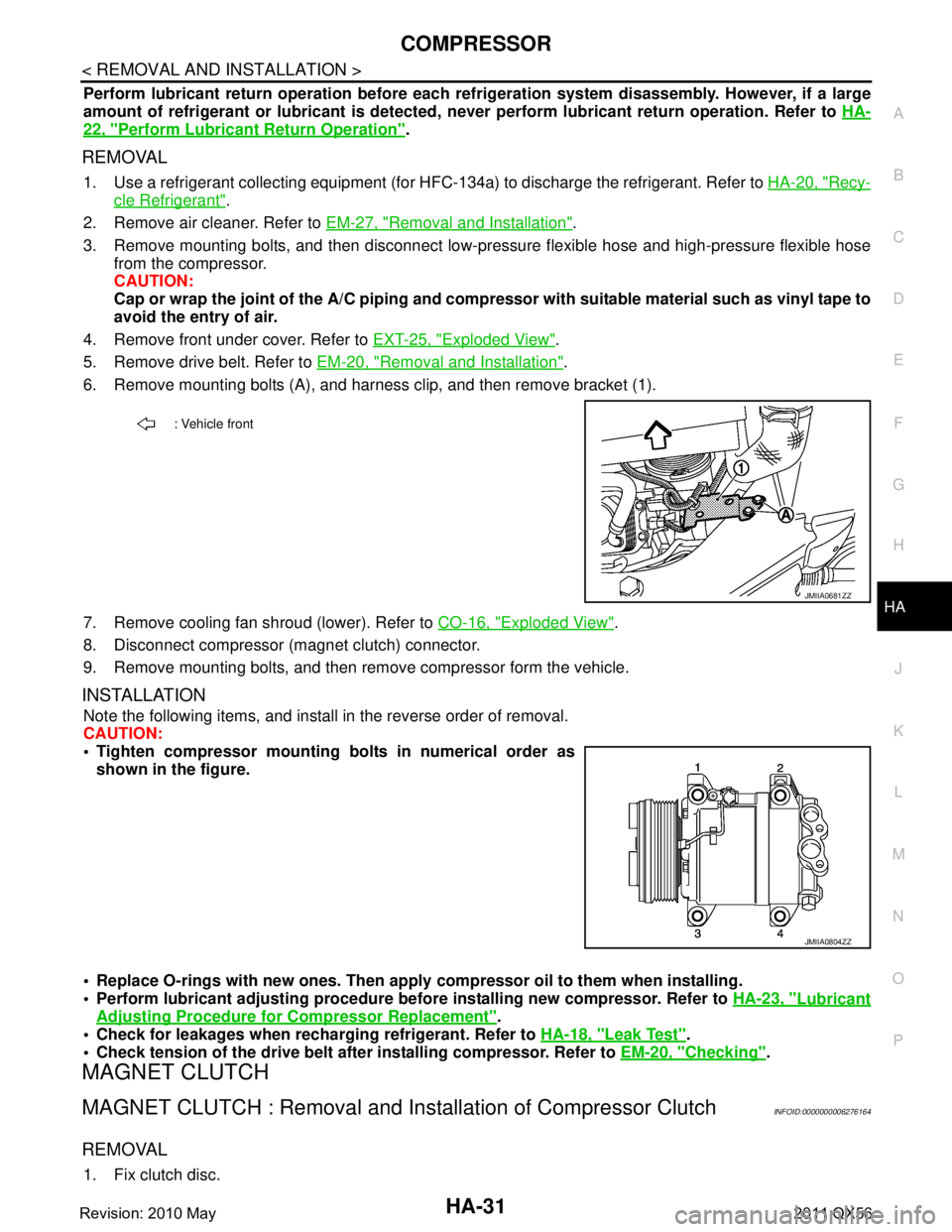
COMPRESSORHA-31
< REMOVAL AND INSTALLATION >
C
DE
F
G H
J
K L
M A
B
HA
N
O P
Perform lubricant return operati on before each refrigeration system disassembly. However, if a large
amount of refrigerant or lubricant is detected, n ever perform lubricant return operation. Refer to HA-
22, "Perform Lubricant Return Operation".
REMOVAL
1. Use a refrigerant collecting equipment (for HF C-134a) to discharge the refrigerant. Refer to HA-20, "Recy-
cle Refrigerant".
2. Remove air cleaner. Refer to EM-27, "
Removal and Installation".
3. Remove mounting bolts, and then disconnect low-pressure flexible hose and high-pressure flexible hose from the compressor.
CAUTION:
Cap or wrap the joint of the A/C piping and comp ressor with suitable material such as vinyl tape to
avoid the entry of air.
4. Remove front under cover. Refer to EXT-25, "
Exploded View".
5. Remove drive belt. Refer to EM-20, "
Removal and Installation".
6. Remove mounting bolts (A), and harness clip, and then remove bracket (1).
7. Remove cooling fan shroud (lower). Refer to CO-16, "
Exploded View".
8. Disconnect compressor (magnet clutch) connector.
9. Remove mounting bolts, and then remove compressor form the vehicle.
INSTALLATION
Note the following items, and install in the reverse order of removal.
CAUTION:
Tighten compressor mounting bolts in numerical order as shown in the figure.
Replace O-rings with new ones. Then apply compressor oil to them when installing.
Perform lubricant adjusting procedure befo re installing new compressor. Refer to HA-23, "
Lubricant
Adjusting Procedure for Compressor Replacement".
Check for leakages when recharging refrigerant. Refer to HA-18, "
Leak Test".
Check tension of the drive belt afte r installing compressor. Refer to EM-20, "
Checking".
MAGNET CLUTCH
MAGNET CLUTCH : Removal and Inst allation of Compressor ClutchINFOID:0000000006276164
REMOVAL
1. Fix clutch disc.
: Vehicle front
JMIIA0681ZZ
JMIIA0804ZZ
Revision: 2010 May2011 QX56
Page 3088 of 5598
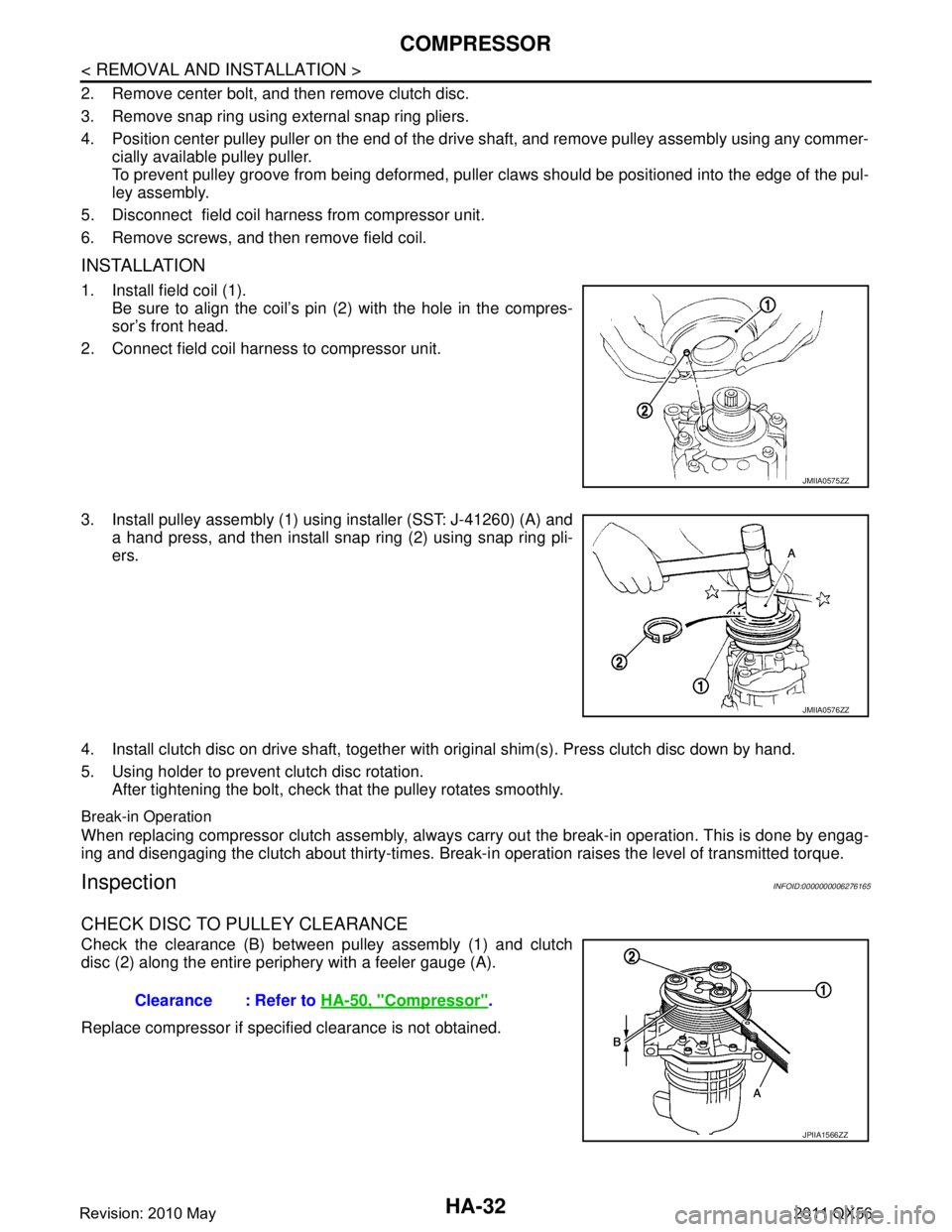
HA-32
< REMOVAL AND INSTALLATION >
COMPRESSOR
2. Remove center bolt, and then remove clutch disc.
3. Remove snap ring using external snap ring pliers.
4. Position center pulley puller on the end of the drive shaft, and remove pulley assembly using any commer-
cially available pulley puller.
To prevent pulley groove from being deformed, pulle r claws should be positioned into the edge of the pul-
ley assembly.
5. Disconnect field coil harness from compressor unit.
6. Remove screws, and then remove field coil.
INSTALLATION
1. Install field coil (1). Be sure to align the coil’s pin (2) with the hole in the compres-
sor’s front head.
2. Connect field coil harness to compressor unit.
3. Install pulley assembly (1) using installer (SST: J-41260) (A) and a hand press, and then install snap ring (2) using snap ring pli-
ers.
4. Install clutch disc on drive shaft, together with original shim(s). Press clutch disc down by hand.
5. Using holder to prevent clutch disc rotation. After tightening the bolt, check that the pulley rotates smoothly.
Break-in Operation
When replacing compressor clutch assembly, always carry out the break-in operation. This is done by engag-
ing and disengaging the clutch about thirty-times. Break-i n operation raises the level of transmitted torque.
InspectionINFOID:0000000006276165
CHECK DISC TO PULLEY CLEARANCE
Check the clearance (B) between pulley assembly (1) and clutch
disc (2) along the entire periphery with a feeler gauge (A).
Replace compressor if specified clearance is not obtained.
JMIIA0575ZZ
JMIIA0576ZZ
Clearance : Refer to HA-50, "Compressor".
JPIIA1566ZZ
Revision: 2010 May2011 QX56