Page 2633 of 5598
TIMING CHAINEM-71
< REMOVAL AND INSTALLATION >
C
DE
F
G H
I
J
K L
M A
EM
NP
O
Bolt (A) of fuel pump connector protector (1) cannot be
installed after installing valve timing control cover. Therefore,
install fuel pump connector protector in advance, if it is being
removed.
a. Install new O-rings (1) on front cover.
b. Install new seal rings (1) in shaft grooves. CAUTION:
When replacing seal ring, replace all rings with new ones.
c. Apply a continuous bead of liquid gasket with tube presser (commercial service tool) to valve timing control covers as
shown in the figure.
Use Genuine RTV silicone seal ant or equivalent. Refer to
GI-22, "
Recommended Chemical Products and Sealants".
JPBIA3500ZZ
JPBIA3477ZZ
JPBIA3518ZZ
A : Bank 1
B : Bank 2
c: φ3.4 - 4.4 mm (0.134 - 0.173 in)
JPBIA3519ZZ
Revision: 2010 May2011 QX56
Page 2634 of 5598
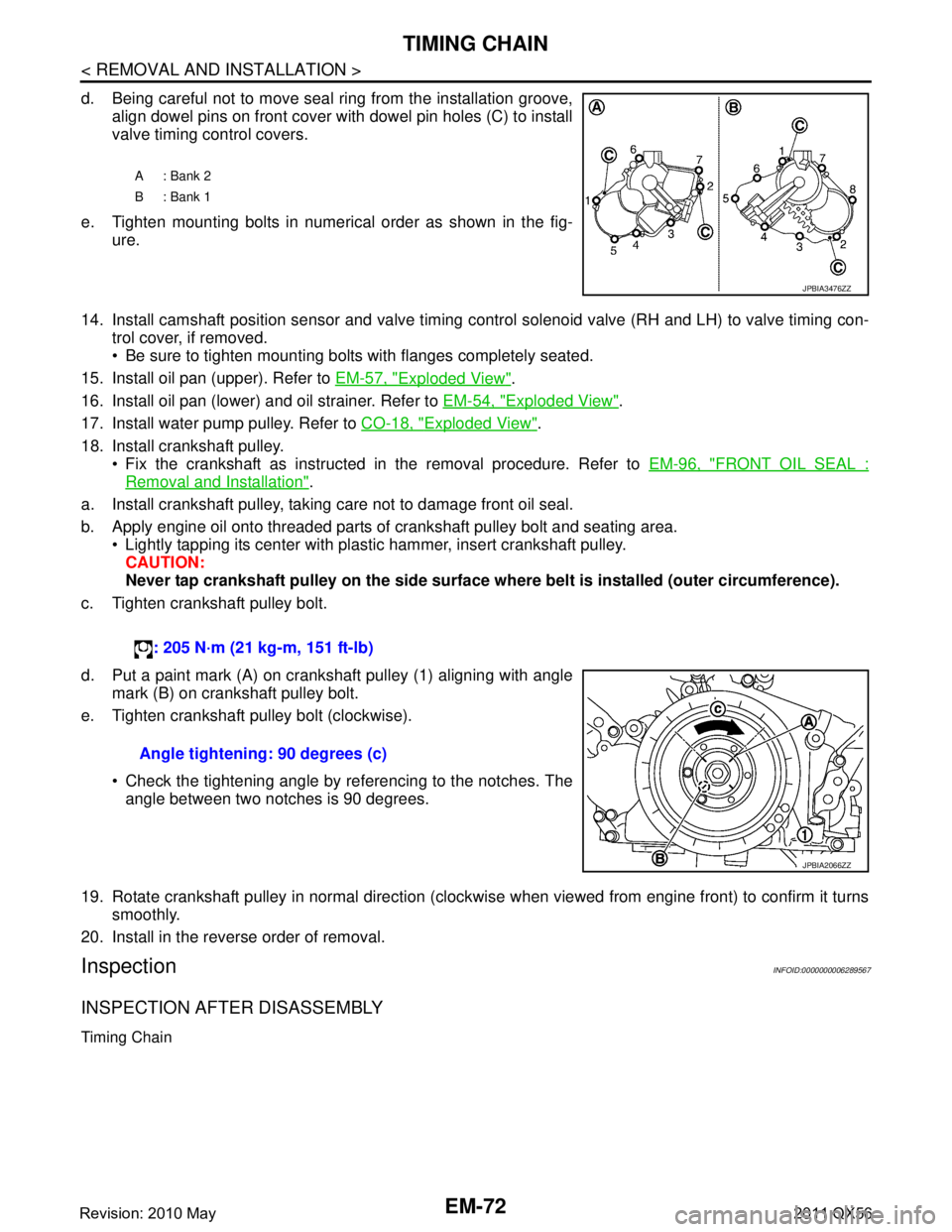
EM-72
< REMOVAL AND INSTALLATION >
TIMING CHAIN
d. Being careful not to move seal ring from the installation groove,align dowel pins on front cover with dowel pin holes (C) to install
valve timing control covers.
e. Tighten mounting bolts in numerical order as shown in the fig- ure.
14. Install camshaft position sensor and valve timing c ontrol solenoid valve (RH and LH) to valve timing con-
trol cover, if removed.
Be sure to tighten mounting bolts with flanges completely seated.
15. Install oil pan (upper). Refer to EM-57, "
Exploded View".
16. Install oil pan (lower) and oil strainer. Refer to EM-54, "
Exploded View".
17. Install water pump pulley. Refer to CO-18, "
Exploded View".
18. Install crankshaft pulley. Fix the crankshaft as instructed in the removal procedure. Refer to EM-96, "
FRONT OIL SEAL :
Removal and Installation".
a. Install crankshaft pulley, taking care not to damage front oil seal.
b. Apply engine oil onto threaded parts of crankshaft pulley bolt and seating area. Lightly tapping its center with plastic hammer, insert crankshaft pulley.
CAUTION:
Never tap crankshaft pulley on the side surface wh ere belt is installed (outer circumference).
c. Tighten crankshaft pulley bolt.
d. Put a paint mark (A) on crankshaft pulley (1) aligning with angle mark (B) on crankshaft pulley bolt.
e. Tighten crankshaft pulley bolt (clockwise).
Check the tightening angle by referencing to the notches. Theangle between two notches is 90 degrees.
19. Rotate crankshaft pulley in normal direction (clockwise when viewed from engine front) to confirm it turns smoothly.
20. Install in the reverse order of removal.
InspectionINFOID:0000000006289567
INSPECTION AFTER DISASSEMBLY
Timing Chain
A: Bank 2
B: Bank 1
JPBIA3476ZZ
: 205 N·m (21 kg-m, 151 ft-lb)
Angle tightening: 90 degrees (c)
JPBIA2066ZZ
Revision: 2010 May2011 QX56
Page 2635 of 5598
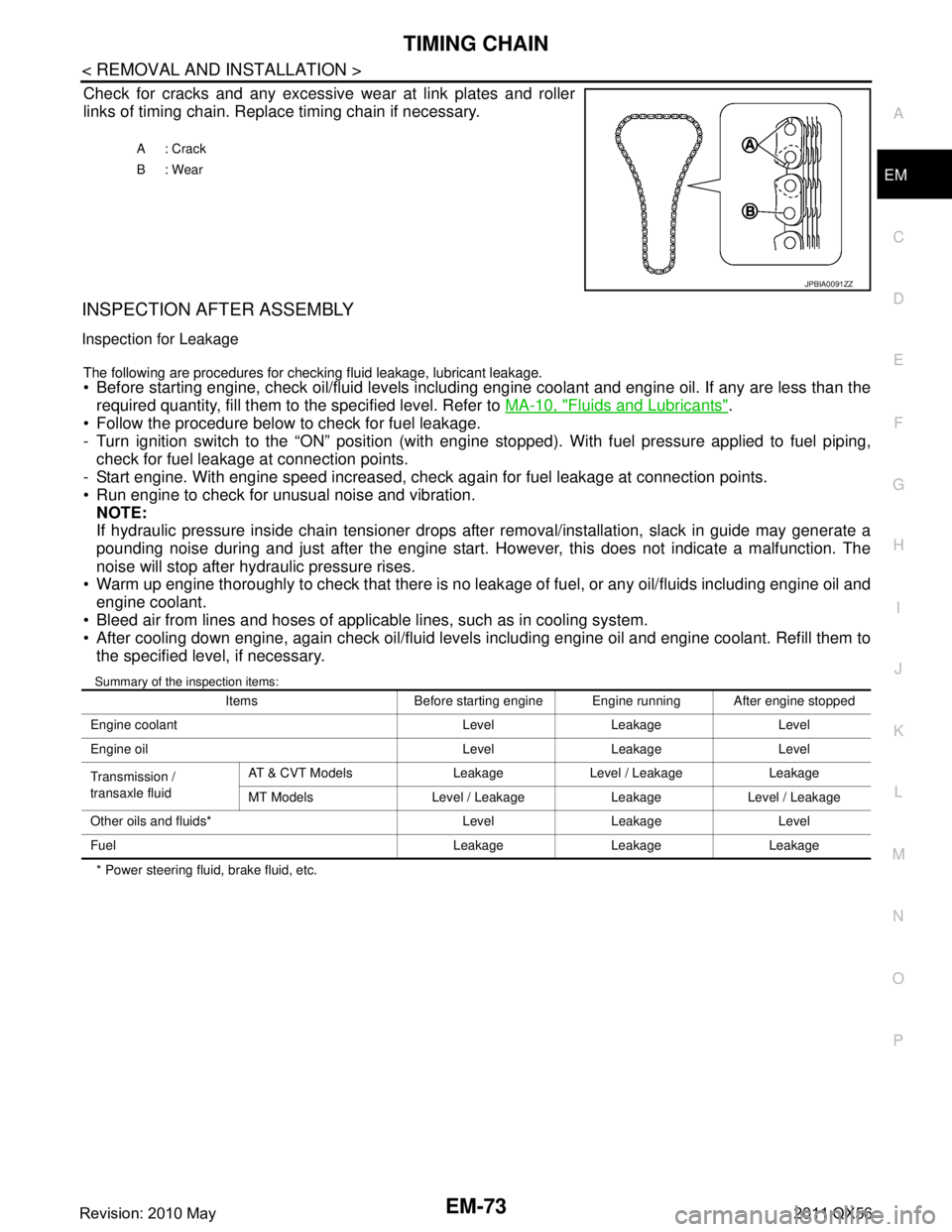
TIMING CHAINEM-73
< REMOVAL AND INSTALLATION >
C
DE
F
G H
I
J
K L
M A
EM
NP
O
Check for cracks and any excessive
wear at link plates and roller
links of timing chain. Replace timing chain if necessary.
INSPECTION AFTER ASSEMBLY
Inspection for Leakage
The following are procedures for chec king fluid leakage, lubricant leakage. Before starting engine, check oil/fluid levels including engine coolant and engine oil. If any are less than the
required quantity, fill them to the specified level. Refer to MA-10, "
Fluids and Lubricants".
Follow the procedure below to check for fuel leakage.
- Turn ignition switch to the “ON” position (with engi ne stopped). With fuel pressure applied to fuel piping,
check for fuel leakage at connection points.
- Start engine. With engine speed increased, check again for fuel leakage at connection points.
Run engine to check for unusual noise and vibration.
NOTE:
If hydraulic pressure inside chain tensioner drops after removal/installation, slack in guide may generate a
pounding noise during and just after the engine start. However, this does not indicate a malfunction. The
noise will stop after hydraulic pressure rises.
Warm up engine thoroughly to check that there is no leak age of fuel, or any oil/fluids including engine oil and
engine coolant.
Bleed air from lines and hoses of applicable lines, such as in cooling system.
After cooling down engine, again check oil/fluid levels including engine oil and engine coolant. Refill them to the specified level, if necessary.
Summary of the inspection items:
* Power steering fluid, brake fluid, etc. A: Crack
B: Wear
JPBIA0091ZZ
Items Before starting engine Engine running After engine stopped
Engine coolant Level Leakage Level
Engine oil Level Leakage Level
Transmission /
transaxle fluid AT & CVT Models Leakage Level / Leakage Leakage
MT Models Level / Leakage Leakage Level / Leakage
Other oils and fluids* Level Leakage Level
Fuel Leakage Leakage Leakage
Revision: 2010 May2011 QX56
Page 2636 of 5598
EM-74
< REMOVAL AND INSTALLATION >
CAMSHAFT
CAMSHAFT
Exploded ViewINFOID:0000000006289568
1.VVEL actuator motor assembly
(bank 2) 2. Gasket 3.
VVEL actuator ho
using assembly
(bank 2)
4. Washer 5. VVEL ladder as sembly (bank 2) 6. Exhaust camshaft (bank 2)
7. Cylinder head (bank 2) 8. Cylinder head (bank 1) 9. Exhaust camshaft (bank 1)
10. VVEL ladder assembly (bank 1) 11. VVEL actuator housing assembly
(bank 1)12. Gasket
13. VVEL actuator motor assembly
(bank 1) 14.
VVEL control shaft
position sensor
(bank 1) 15.
VVEL control shaft
position sensor
(bank 2)
A. Comply with the installation proce-
dure when tightening. Refer to
EM-
75, "Removal and Installation".B. View B C. View C
Refer to GI-4, "
Components" for symbols in the figure.
JSBIA0403GB
Revision: 2010 May2011 QX56
Page 2637 of 5598
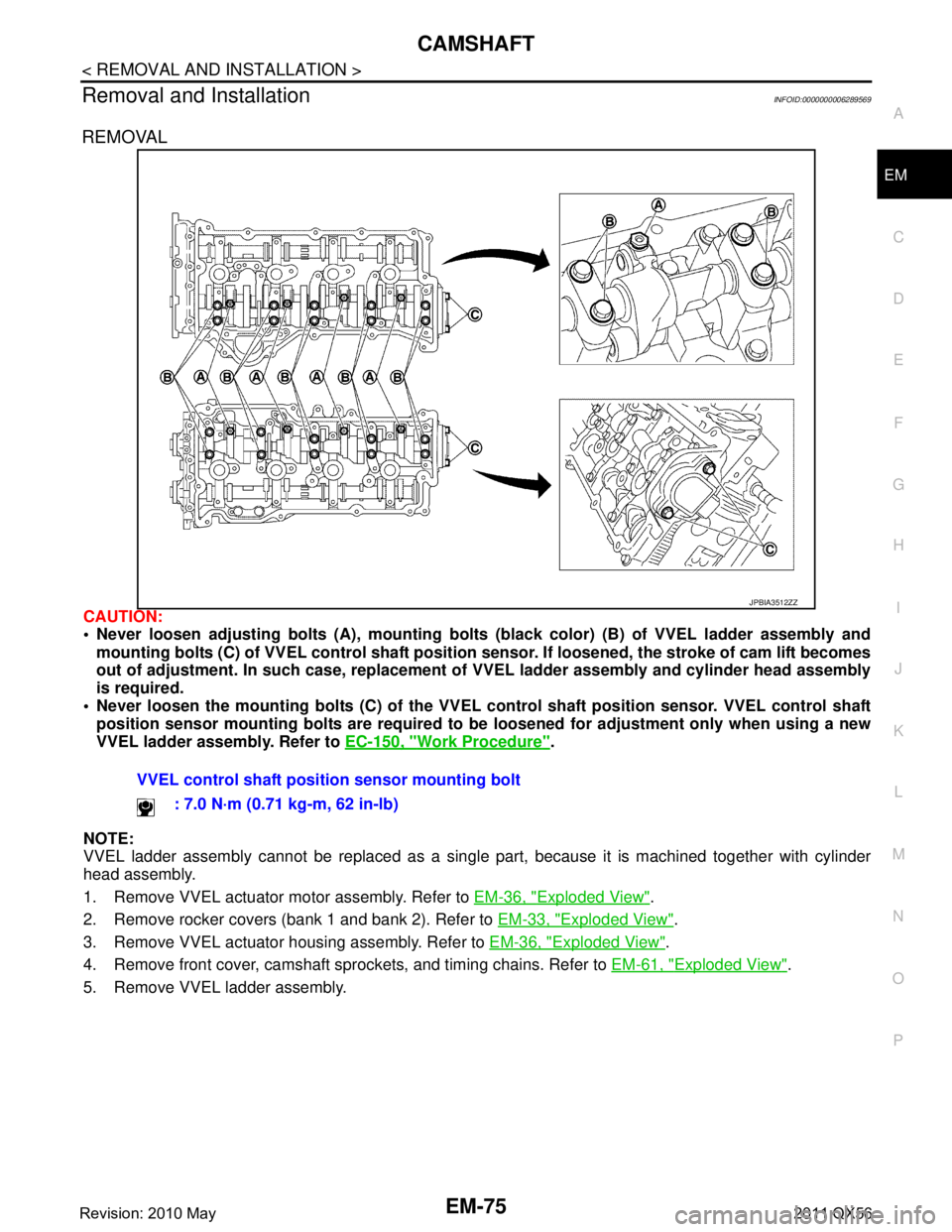
CAMSHAFTEM-75
< REMOVAL AND INSTALLATION >
C
DE
F
G H
I
J
K L
M A
EM
NP
O
Removal and InstallationINFOID:0000000006289569
REMOVAL
CAUTION:
Never loosen adjusting bolts (A), mounting bolt
s (black color) (B) of VVEL ladder assembly and
mounting bolts (C) of VVEL control shaft position sen sor. If loosened, the stroke of cam lift becomes
out of adjustment. In such case, replacement of VVEL ladder assembly and cylinder head assembly
is required.
Never loosen the mounting bolts (C) of the VVEL control shaft position sensor. VVEL control shaft
position sensor mounting bolts are required to be loosened for adjustment only when using a new
VVEL ladder assembly. Refer to EC-150, "
Work Procedure".
NOTE:
VVEL ladder assembly cannot be replaced as a singl e part, because it is machined together with cylinder
head assembly.
1. Remove VVEL actuator motor assembly. Refer to EM-36, "
Exploded View".
2. Remove rocker covers (bank 1 and bank 2). Refer to EM-33, "
Exploded View".
3. Remove VVEL actuator housing assembly. Refer to EM-36, "
Exploded View".
4. Remove front cover, camshaft sprockets, and timing chains. Refer to EM-61, "
Exploded View".
5. Remove VVEL ladder assembly.
JPBIA3512ZZ
VVEL control shaft positi on sensor mounting bolt
: 7.0 N·m (0.71 kg-m, 62 in-lb)
Revision: 2010 May2011 QX56
Page 2638 of 5598
EM-76
< REMOVAL AND INSTALLATION >
CAMSHAFT
Loosen mounting bolts (gold color) in the reverse order asshown in the figure.
CAUTION:
Never loosen adjusting bolts and mounting bolts (black color).
When removing VVEL ladder assembly, hold the drive
shaft from below so as not to drop it.
6. Remove exhaust camshaft.
7. Remove valve lifter, if necessary. Identify installation positions, and store them without mixing them up.
INSTALLATION
1. Install valve lifter. Install it in the original position.
2. Install exhaust camshaft. Distinction between exhaust camshaft is performed with the
identification mark.
3. Install VVEL ladder assembly as per the following:
A: Bank 2
B: Bank 1 : Engine front
JPBIA3513ZZ
: Engine front
Bank Paint marks
Identification rib (E)
M1 (C) M2 (D)
Bank 1 (A) No Purple Yes
Bank 2 (B) No Purple No
JPBIA3514ZZ
Revision: 2010 May2011 QX56
Page 2639 of 5598
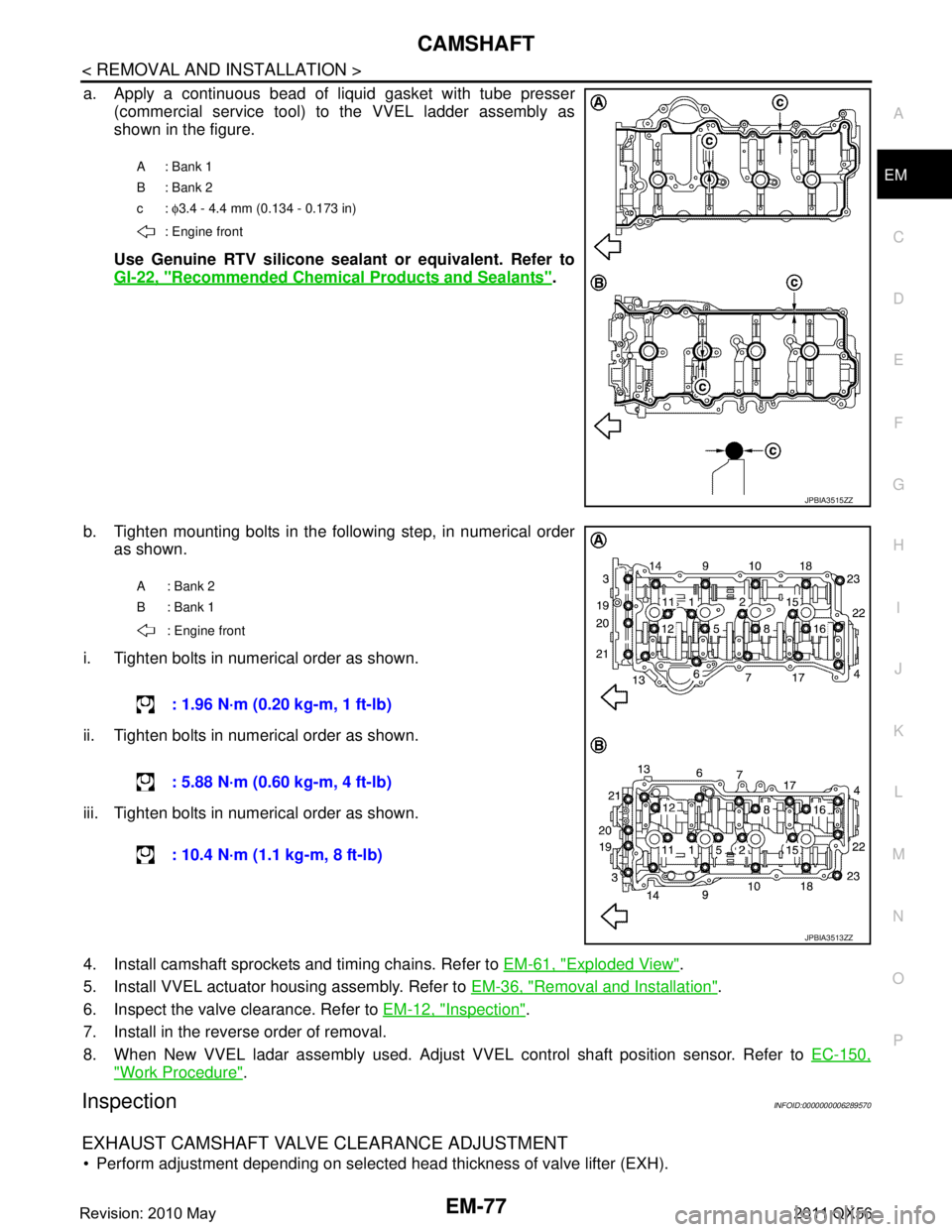
CAMSHAFTEM-77
< REMOVAL AND INSTALLATION >
C
DE
F
G H
I
J
K L
M A
EM
NP
O
a. Apply a continuous bead of liquid gasket with tube presser
(commercial service tool) to the VVEL ladder assembly as
shown in the figure.
Use Genuine RTV silicone seal ant or equivalent. Refer to
GI-22, "
Recommended Chemical Products and Sealants".
b. Tighten mounting bolts in the following step, in numerical order as shown.
i. Tighten bolts in numerical order as shown.
ii. Tighten bolts in numerical order as shown.
iii. Tighten bolts in numerical order as shown.
4. Install camshaft sprockets and timing chains. Refer to EM-61, "
Exploded View".
5. Install VVEL actuator housing assembly. Refer to EM-36, "
Removal and Installation".
6. Inspect the valve clearance. Refer to EM-12, "
Inspection".
7. Install in the reverse order of removal.
8. When New VVEL ladar assembly used. Adjust VVEL control shaft position sensor. Refer to EC-150,
"Work Procedure".
InspectionINFOID:0000000006289570
EXHAUST CAMSHAFT VALVE CLEARANCE ADJUSTMENT
Perform adjustment depending on selected head thickness of valve lifter (EXH).
A: Bank 1
B: Bank 2
c: φ3.4 - 4.4 mm (0.134 - 0.173 in)
: Engine front
JPBIA3515ZZ
A: Bank 2
B: Bank 1
: Engine front
: 1.96 N·m (0.20 kg-m, 1 ft-lb)
: 5.88 N·m (0.60 kg-m, 4 ft-lb)
: 10.4 N·m (1.1 kg-m, 8 ft-lb)
JPBIA3513ZZ
Revision: 2010 May2011 QX56
Page 2640 of 5598
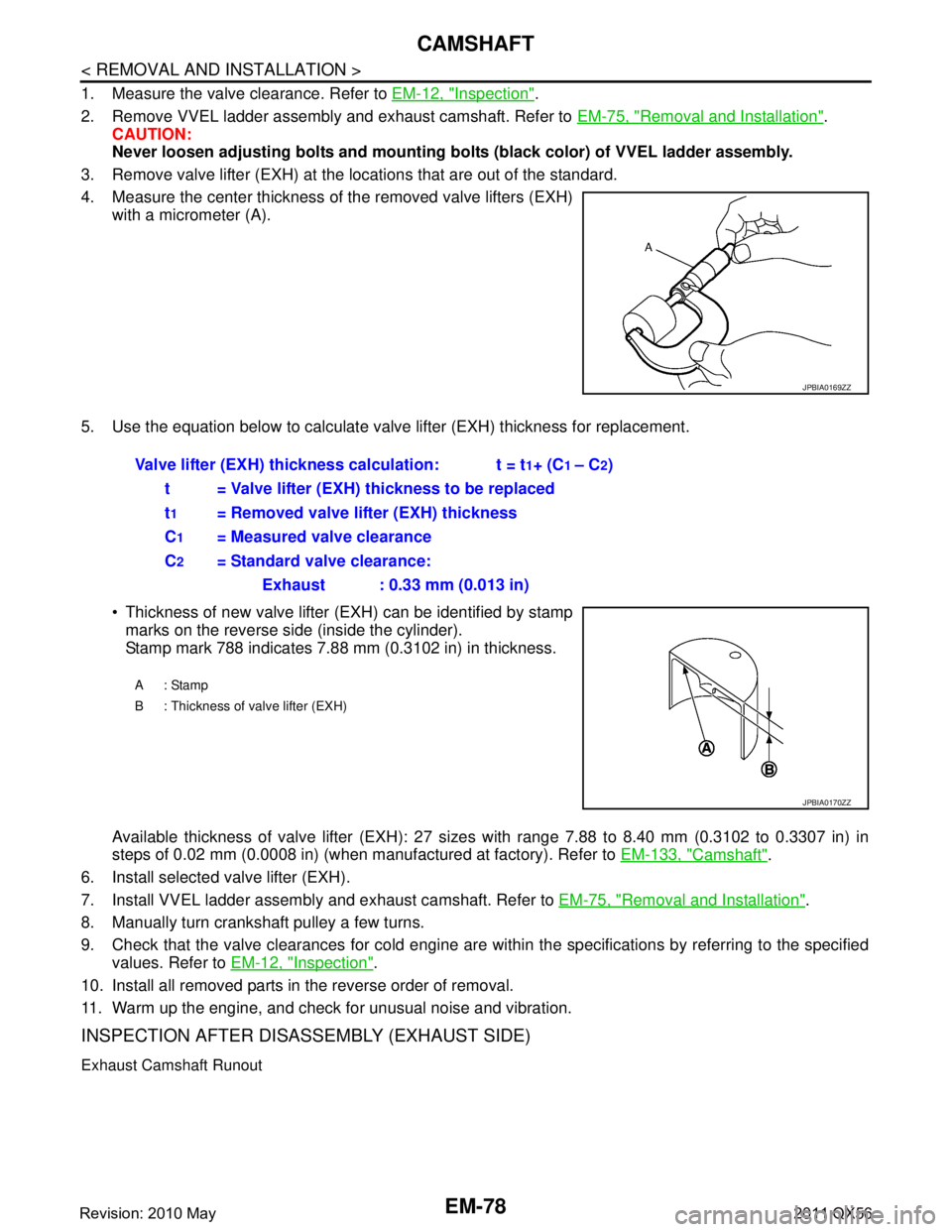
EM-78
< REMOVAL AND INSTALLATION >
CAMSHAFT
1. Measure the valve clearance. Refer to EM-12, "Inspection".
2. Remove VVEL ladder assembly and exhaust camshaft. Refer to EM-75, "
Removal and Installation".
CAUTION:
Never loosen adjusting bolts and mounting bolts (black color) of VVEL ladder assembly.
3. Remove valve lifter (EXH) at the locations that are out of the standard.
4. Measure the center thickness of the removed valve lifters (EXH) with a micrometer (A).
5. Use the equation below to calculate valve lifter (EXH) thickness for replacement. Thickness of new valve lifter (EXH) can be identified by stampmarks on the reverse side (inside the cylinder).
Stamp mark 788 indicates 7.88 mm (0.3102 in) in thickness.
Available thickness of valve lifter (EXH): 27 si zes with range 7.88 to 8.40 mm (0.3102 to 0.3307 in) in
steps of 0.02 mm (0.0008 in) (when m anufactured at factory). Refer to EM-133, "
Camshaft".
6. Install selected valve lifter (EXH).
7. Install VVEL ladder assembly and exhaust camshaft. Refer to EM-75, "
Removal and Installation".
8. Manually turn crankshaft pulley a few turns.
9. Check that the valve clearances for cold engine are wit hin the specifications by referring to the specified
values. Refer to EM-12, "
Inspection".
10. Install all removed parts in the reverse order of removal.
11. Warm up the engine, and check for unusual noise and vibration.
INSPECTION AFTER DISASSEMBLY (EXHAUST SIDE)
Exhaust Camshaft Runout
JPBIA0169ZZ
Valve lifter (EXH) thickness calculation: t = t1+ (C1 – C2)
t = Valve lifter (EXH) thickness to be replaced
t
1= Removed valve lifter (EXH) thickness
C
1= Measured valve clearance
C
2= Standard valve clearance: Exhaust : 0.33 mm (0.013 in)
A: Stamp
B : Thickness of valve lifter (EXH)
JPBIA0170ZZ
Revision: 2010 May2011 QX56