Page 2569 of 5598
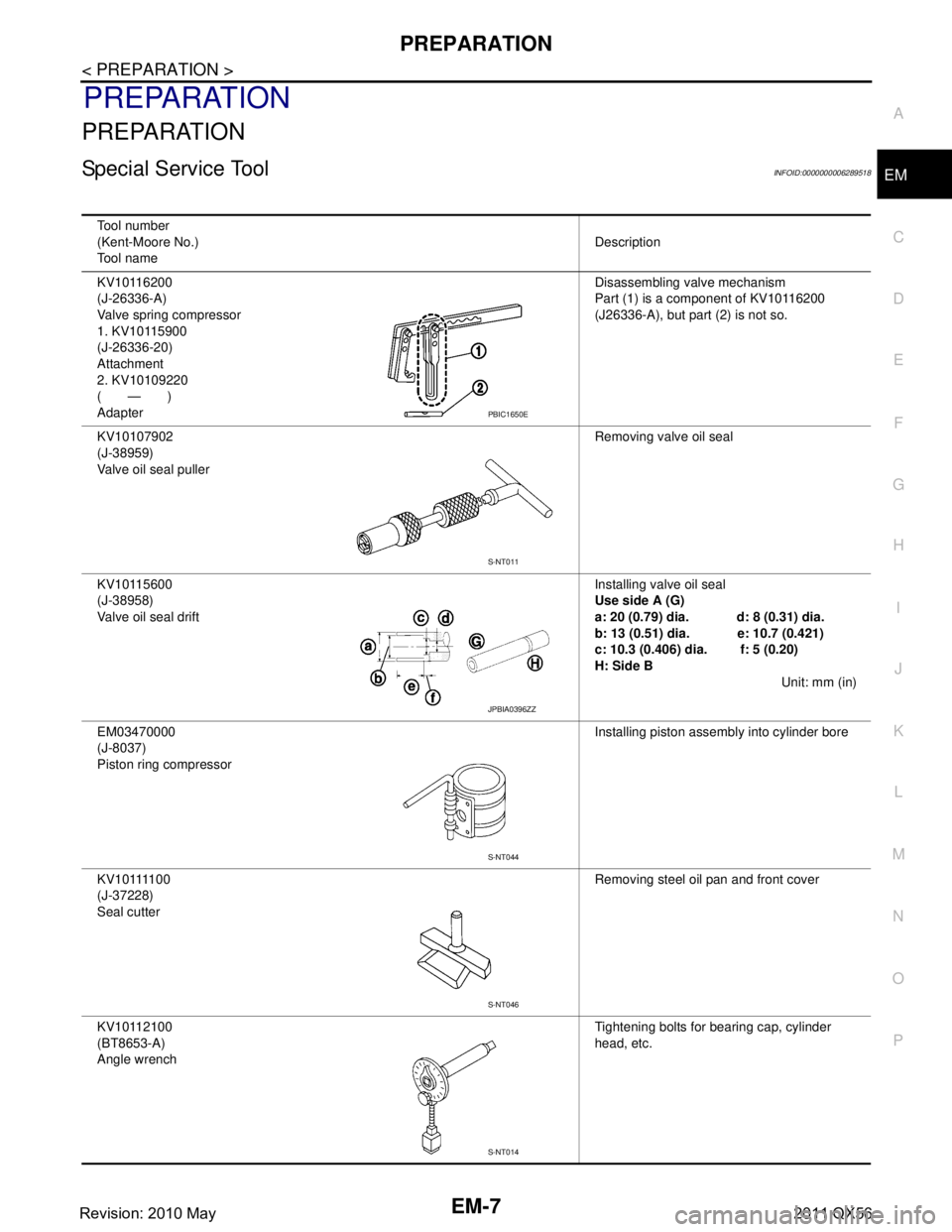
PREPARATIONEM-7
< PREPARATION >
C
DE
F
G H
I
J
K L
M A
EM
NP
O
PREPARATION
PREPARATION
Special Service ToolINFOID:0000000006289518
Tool number
(Kent-Moore No.)
Tool name
Description
KV10116200
(J-26336-A)
Valve spring compressor
1. KV10115900
(J-26336-20)
Attachment
2. KV10109220
(—)
Adapter Disassembling valve mechanism
Part (1) is a component of KV10116200
(J26336-A), but part (2) is not so.
KV10107902
(J-38959)
Valve oil seal puller Removing valve oil seal
KV10115600
(J-38958)
Valve oil seal drift Installing valve oil seal
Use side A (G)
a: 20 (0.79) dia. d: 8 (0.31) dia.
b: 13 (0.51) dia. e: 10.7 (0.421)
c: 10.3 (0.406) dia. f: 5 (0.20)
H: Side B
Unit: mm (in)
EM03470000
(J-8037)
Piston ring compressor Installing piston assembly into cylinder bore
K V 1 0 1111 0 0
(J-37228)
Seal cutter Removing steel oil pan and front cover
KV10112100
(BT8653-A)
Angle wrench Tightening bolts for bearing cap, cylinder
head, etc.
PBIC1650E
S-NT011
JPBIA0396ZZ
S-NT044
S-NT046
S-NT014
Revision: 2010 May2011 QX56
Page 2570 of 5598
EM-8
< PREPARATION >
PREPARATION
KV10114400
(J-38365)
Heated oxygen sensor wrenchLoosening or tightening heated oxygen sen-
sor 2
a: 22 mm (0.87 in)
KV10117100
(J-44626)
Heated oxygen sensor wrench Loosening or tightening air fuel ratio sensor 1
a: 22 mm (0.87 in)
KV10120100
(J-47245)
Ring gear stopper Removing and installing crankshaft pulley
—
(J-45488)
Quick connector release Removing fuel tube quick connectors in en-
gine room
(Available in SEC. 164 of PARTS CATA-
LOG:Part No. 16441 6N210)
KV10119300
(—)
Adapter and torque wrench assembly Tightening rocker cover mounting bolts.
(specified torque)
KV10119600
(—)
Injector remover Removing fuel injector
Tool number
(Kent-Moore No.)
Tool name
Description
JPBIA0397ZZ
NT379
LBIA0451E
PBIC0198E
JPBIA2623ZZ
JPBIA3746ZZ
Revision: 2010 May2011 QX56
Page 2571 of 5598
PREPARATIONEM-9
< PREPARATION >
C
DE
F
G H
I
J
K L
M A
EM
NP
O
Commercial Service ToolINFOID:0000000006289519
KV101197S0
(—)
Injector seal drift set
Installing fuel injector seal ring
EG15050500
(J-45402)
Compression gauge adapter Checking compresion pressure
Tool number
(Kent-Moore No.)
Tool name
Description
JPBIA3281ZZ
ZZA1225D
(Kent-Moore No.)
Tool name
Description
(—)
Tube presser Pressing the tube of liquid gasket
(—)
Power tool Loosening nuts and bolts
(—)
Spark plug wrench Removing and installing spark plug
a: 14 mm (0.55 in)
(—)
Manual lift table caddy Removing and installing engine
S-NT052
PBIC0190E
JPBIA0399ZZ
ZZA1210D
Revision: 2010 May2011 QX56
Page 2572 of 5598
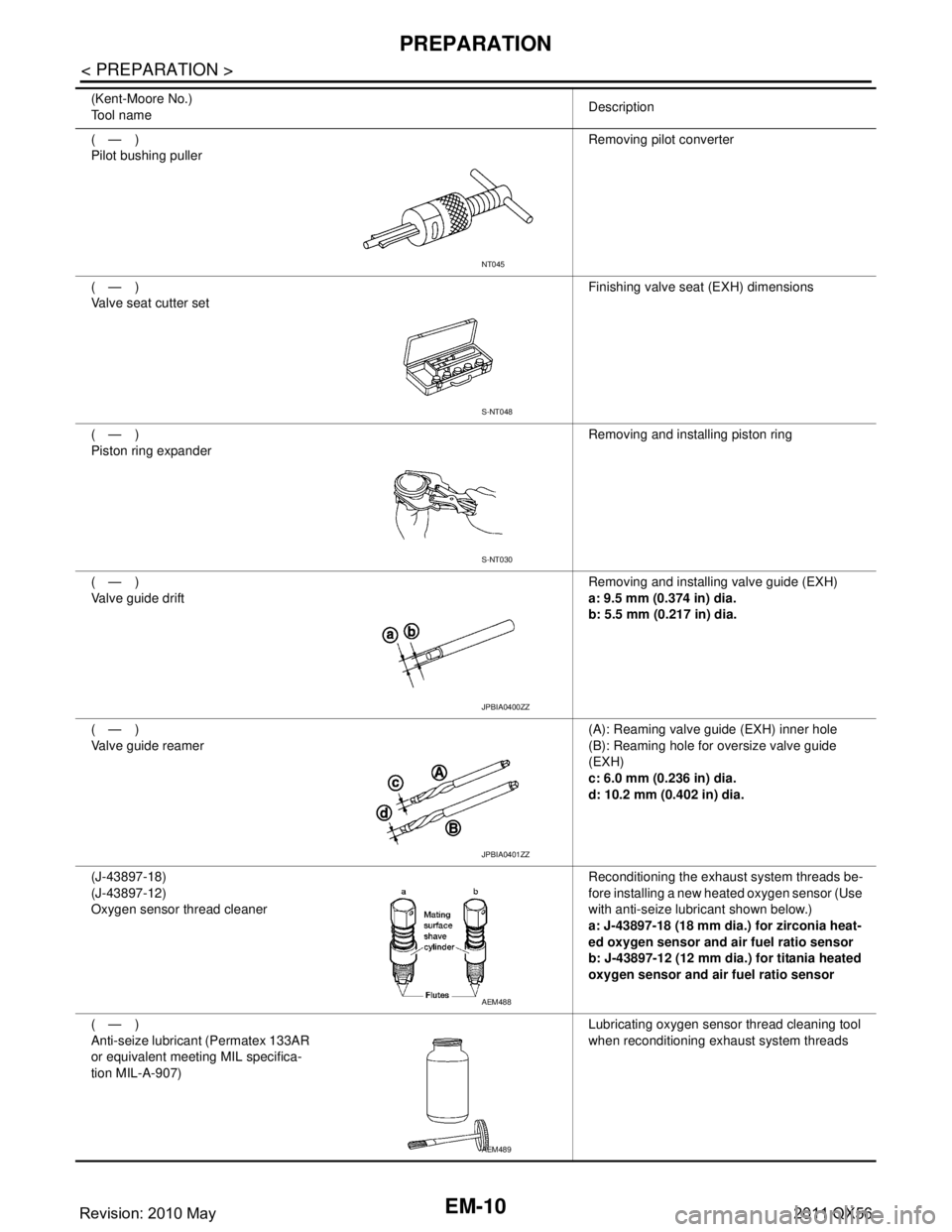
EM-10
< PREPARATION >
PREPARATION
(—)
Pilot bushing pullerRemoving pilot converter
(—)
Valve seat cutter set Finishing valve seat (EXH) dimensions
(—)
Piston ring expander Removing and installing piston ring
(—)
Valve guide drift Removing and installing valve guide (EXH)
a: 9.5 mm (0.374 in) dia.
b: 5.5 mm (0.217 in) dia.
(—)
Valve guide reamer (A): Reaming valve guide (EXH) inner hole
(B): Reaming hole for oversize valve guide
(EXH)
c: 6.0 mm (0.236 in) dia.
d: 10.2 mm (0.402 in) dia.
(J-43897-18)
(J-43897-12)
Oxygen sensor thread cleaner Reconditioning the exhaust system threads be-
fore installing a new heated oxygen sensor (Use
with anti-seize lubricant shown below.)
a: J-43897-18 (18 mm dia.) for zirconia heat-
ed oxygen sensor and air fuel ratio sensor
b: J-43897-12 (12 mm dia.) for titania heated
oxygen sensor and air fuel ratio sensor
(—)
Anti-seize lubricant (Permatex 133AR
or equivalent meeting MIL specifica-
tion MIL-A-907) Lubricating oxygen sensor thread cleaning tool
when reconditioning exhaust system threads
(Kent-Moore No.)
Tool name
Description
NT045
S-NT048
S-NT030
JPBIA0400ZZ
JPBIA0401ZZ
AEM488
AEM489
Revision: 2010 May2011 QX56
Page 2573 of 5598
PREPARATIONEM-11
< PREPARATION >
C
DE
F
G H
I
J
K L
M A
EM
NP
O
(—)
Feeler gauge
Inspection valve clearance (use a curved-tip
gauge)
(—)
Compression gauge with flexible type
adapter Checking compression pressure
(Kent-Moore No.)
Tool name
Description
JPBIA1362ZZ
Revision: 2010 May2011 QX56
Page 2574 of 5598
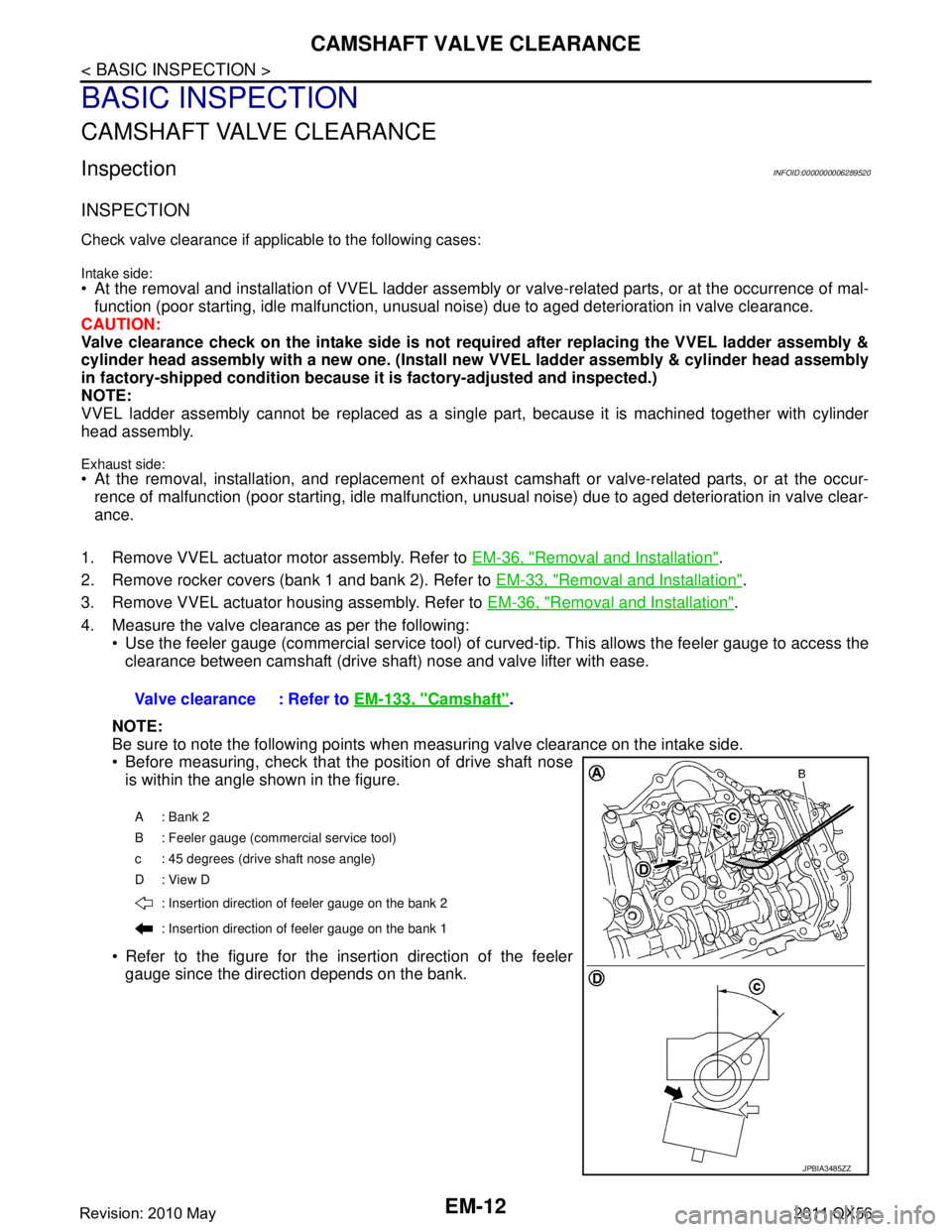
EM-12
< BASIC INSPECTION >
CAMSHAFT VALVE CLEARANCE
BASIC INSPECTION
CAMSHAFT VALVE CLEARANCE
InspectionINFOID:0000000006289520
INSPECTION
Check valve clearance if applicable to the following cases:
Intake side:
At the removal and installation of VVEL ladder assembly or valve-related parts, or at the occurrence of mal-
function (poor starting, idle malfunction, unusual noise) due to aged deterioration in valve clearance.
CAUTION:
Valve clearance check on the intake side is not required after replacing the VVEL ladder assembly &
cylinder head assembly with a new one. (Install new VVEL ladder assembly & cylinder head assembly
in factory-shipped condition because it is factory-adjusted and inspected.)
NOTE:
VVEL ladder assembly cannot be replaced as a singl e part, because it is machined together with cylinder
head assembly.
Exhaust side: At the removal, installation, and replacement of exhaus t camshaft or valve-related parts, or at the occur-
rence of malfunction (poor starting, idle malfunction, unusual noise) due to aged deterioration in valve clear-
ance.
1. Remove VVEL actuator motor assembly. Refer to EM-36, "
Removal and Installation".
2. Remove rocker covers (bank 1 and bank 2). Refer to EM-33, "
Removal and Installation".
3. Remove VVEL actuator housing assembly. Refer to EM-36, "
Removal and Installation".
4. Measure the valve clearance as per the following: Use the feeler gauge (commercial service tool) of cu rved-tip. This allows the feeler gauge to access the
clearance between camshaft (drive shaft) nose and valve lifter with ease.
NOTE:
Be sure to note the following points when measuring valve clearance on the intake side.
Before measuring, check that the position of drive shaft nose
is within the angle shown in the figure.
Refer to the figure for the insertion direction of the feeler gauge since the direction depends on the bank.Valve clearance : Refer to
EM-133, "
Camshaft".
A: Bank 2
B : Feeler gauge (commercial service tool)
c : 45 degrees (drive shaft nose angle)
D: View D
: Insertion direction of feeler gauge on the bank 2
: Insertion direction of feeler gauge on the bank 1
JPBIA3485ZZ
Revision: 2010 May2011 QX56
Page 2575 of 5598
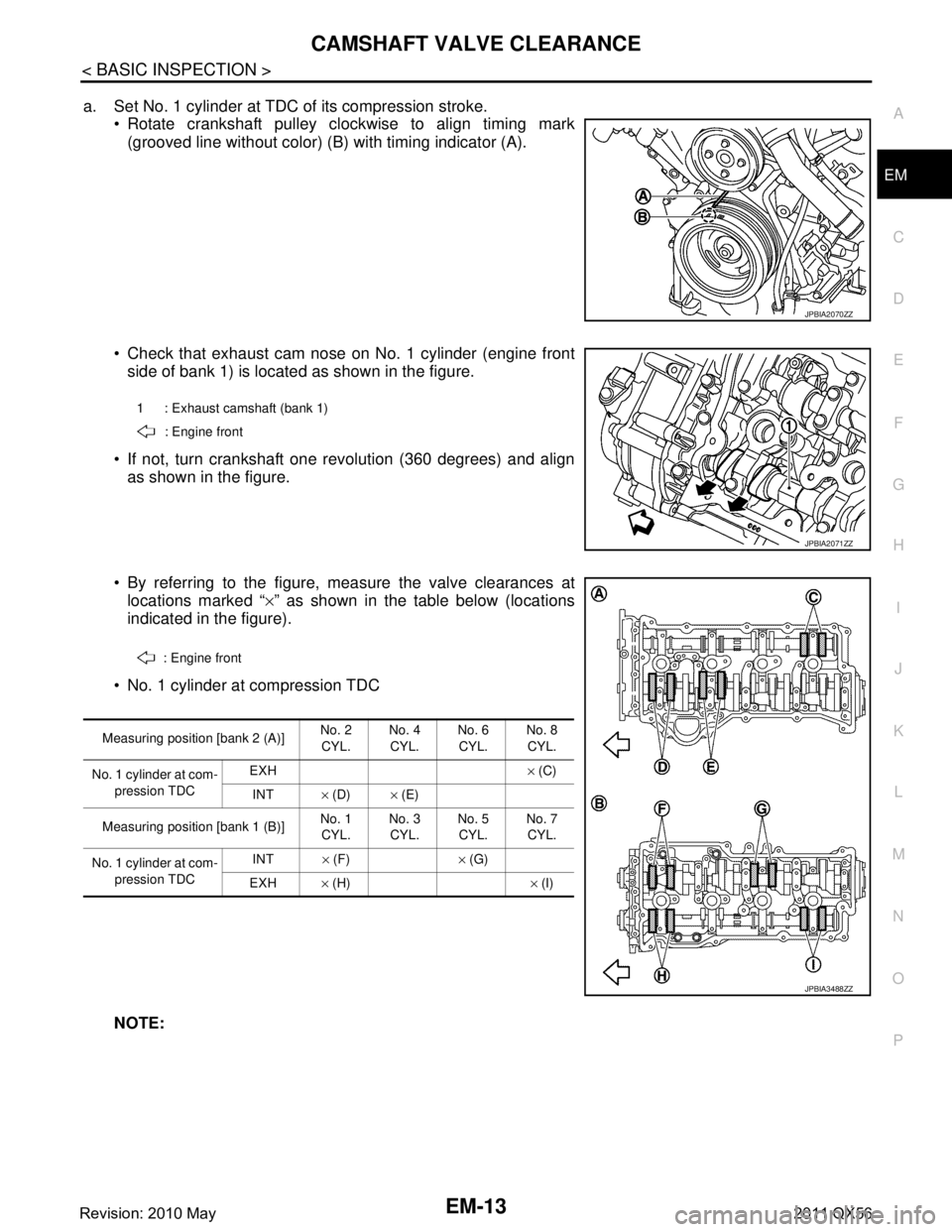
CAMSHAFT VALVE CLEARANCEEM-13
< BASIC INSPECTION >
C
DE
F
G H
I
J
K L
M A
EM
NP
O
a. Set No. 1 cylinder at TDC of its compression stroke.
Rotate crankshaft pulley clockwise to align timing mark
(grooved line without color) (B) with timing indicator (A).
Check that exhaust cam nose on No. 1 cylinder (engine front side of bank 1) is located as shown in the figure.
If not, turn crankshaft one revolution (360 degrees) and align as shown in the figure.
By referring to the figure, measure the valve clearances at locations marked “ ×” as shown in the table below (locations
indicated in the figure).
No. 1 cylinder at compression TDC
NOTE:
JPBIA2070ZZ
1 : Exhaust camshaft (bank 1) : Engine front
JPBIA2071ZZ
: Engine front
Measuring position [bank 2 (A)] No. 2
CYL. No. 4
CYL. No. 6
CYL. No. 8
CYL.
No. 1 cylinder at com- pression TDC EXH
× (C)
INT × (D) × (E)
Measuring position [bank 1 (B)] No. 1
CYL. No. 3
CYL. No. 5
CYL. No. 7
CYL.
No. 1 cylinder at com- pression TDC INT
× (F) × (G)
EXH × (H) × (I)
JPBIA3488ZZ
Revision: 2010 May2011 QX56
Page 2576 of 5598
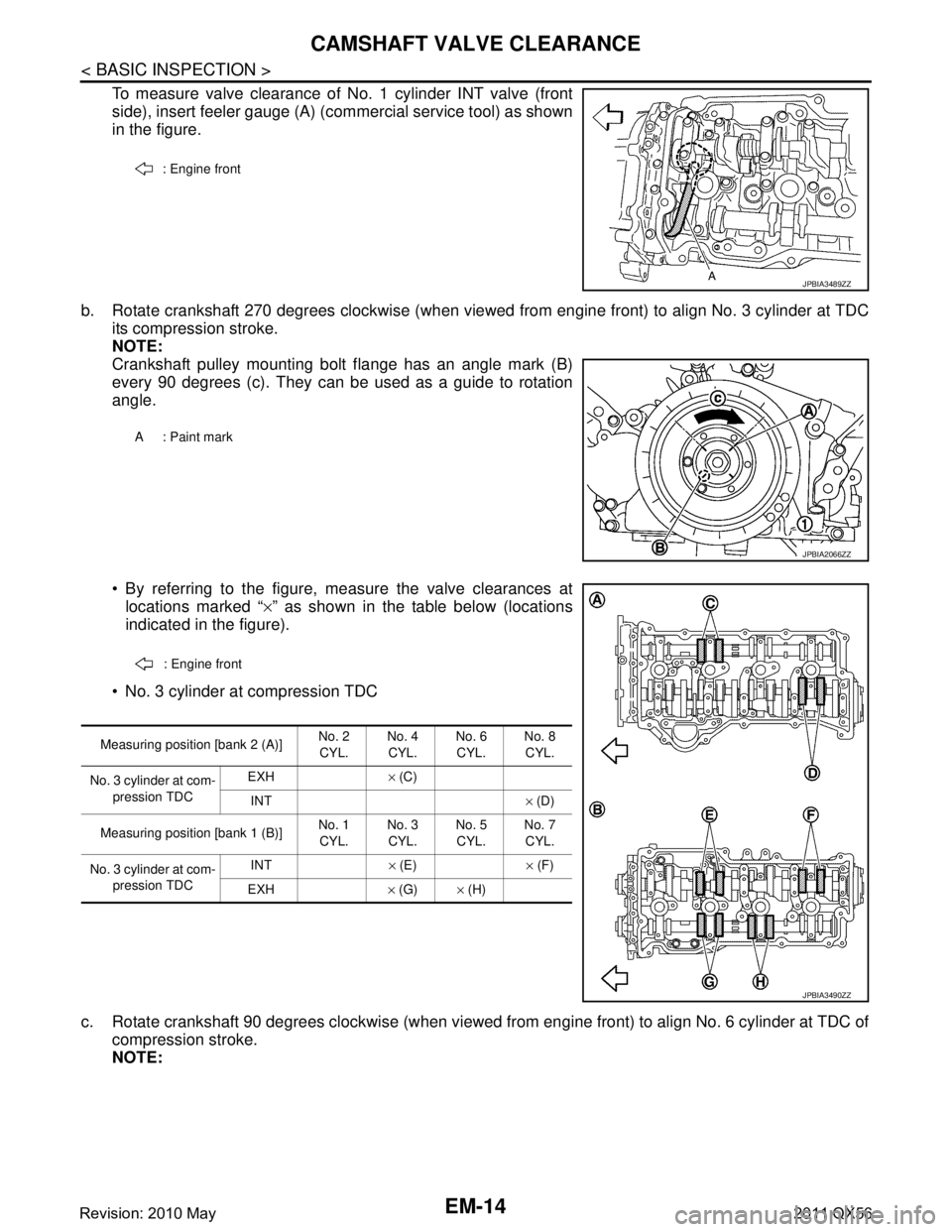
EM-14
< BASIC INSPECTION >
CAMSHAFT VALVE CLEARANCE
To measure valve clearance of No. 1 cylinder INT valve (front
side), insert feeler gauge (A) (commercial service tool) as shown
in the figure.
b. Rotate crankshaft 270 degrees clockwise (when viewed from engine front) to align No. 3 cylinder at TDC its compression stroke.
NOTE:
Crankshaft pulley mounting bolt flange has an angle mark (B)
every 90 degrees (c). They can be used as a guide to rotation
angle.
By referring to the figure, measure the valve clearances atlocations marked “ ×” as shown in the table below (locations
indicated in the figure).
No. 3 cylinder at compression TDC
c. Rotate crankshaft 90 degrees clockwise (when viewed from engine front) to align No. 6 cylinder at TDC of compression stroke.
NOTE:
: Engine front
JPBIA3489ZZ
A : Paint mark
JPBIA2066ZZ
: Engine front
Measuring position [bank 2 (A)] No. 2
CYL. No. 4
CYL. No. 6
CYL. No. 8
CYL.
No. 3 cylinder at com- pression TDC EXH
× (C)
INT × (D)
Measuring position [bank 1 (B)] No. 1
CYL. No. 3
CYL. No. 5
CYL. No. 7
CYL.
No. 3 cylinder at com- pression TDC INT
× (E) × (F)
EXH × (G) × (H)
JPBIA3490ZZ
Revision: 2010 May2011 QX56