Page 5121 of 5135
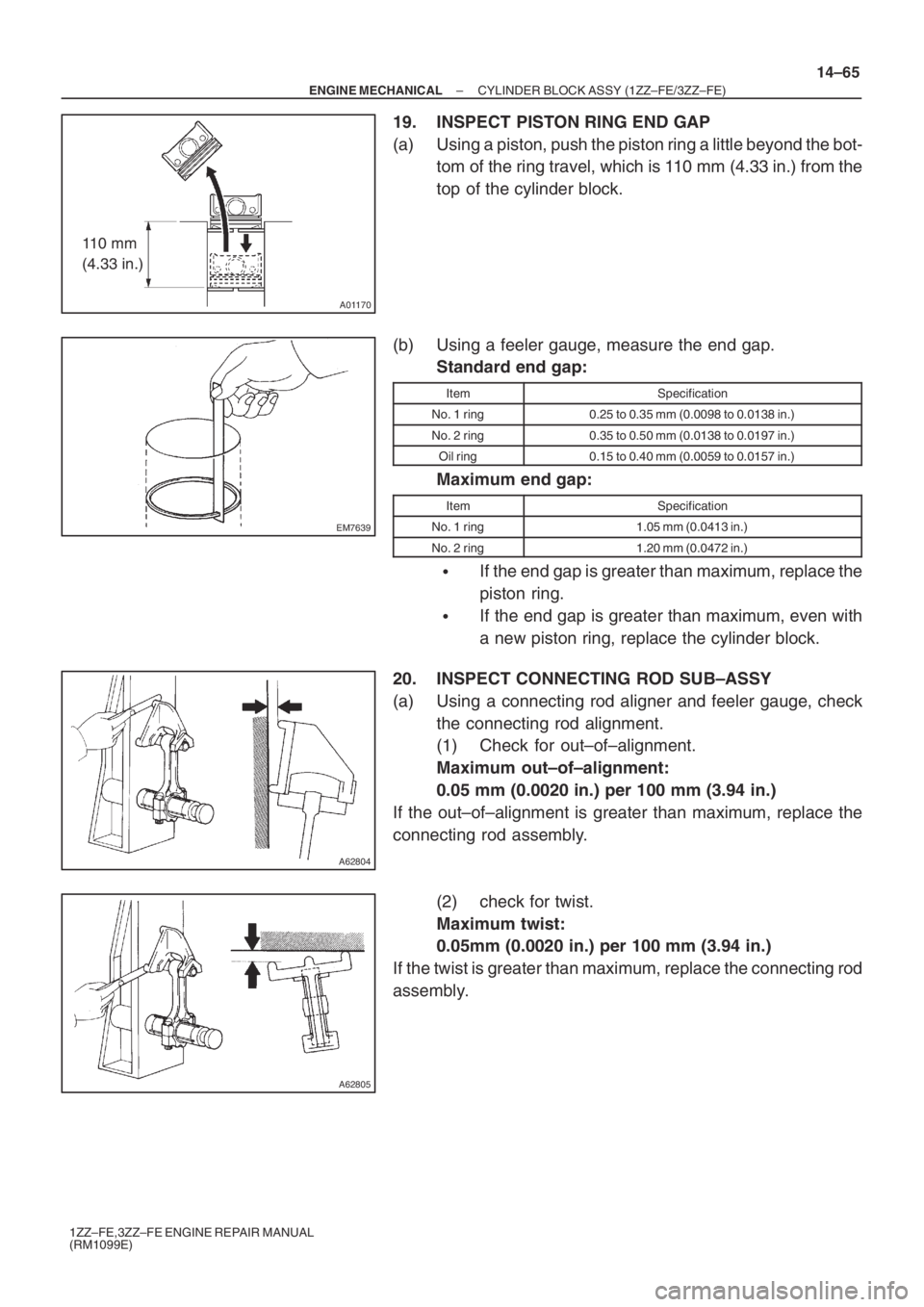
A01170
11 0 m m
(4.33 in.)
EM7639
A62804
A62805
– ENGINE MECHANICALCYLINDER BLOCK ASSY (1ZZ–FE/3ZZ–FE)
14–65
1ZZ–FE,3ZZ–FE ENGINE REPAIR MANUAL
(RM1099E)
19. INSPECT PISTON RING END GAP
(a) Using a piston, push the piston ring a little beyond the bot-
tom of the ring travel, which is 110 mm (4.33 in.) from the
top of the cylinder block.
(b) Using a feeler gauge, measure the end gap.
Standard end gap:
ItemSpecification
No. 1 ring0.25 to 0.35 mm (0.0098 to 0.0138 in.)
No. 2 ring0.35 to 0.50 mm (0.0138 to 0.0197 in.)
Oil ring0.15 to 0.40 mm (0.0059 to 0.0157 in.)
Maximum end gap:
ItemSpecification
No. 1 ring1.05 mm (0.0413 in.)
No. 2 ring1.20 mm (0.0472 in.)
If the end gap is greater than maximum, replace the
piston ring.
If the end gap is greater than maximum, even with
a new piston ring, replace the cylinder block.
20. INSPECT CONNECTING ROD SUB–ASSY
(a) Using a connecting rod aligner and feeler gauge, check
the connecting rod alignment.
(1) Check for out–of–alignment.
Maximum out–of–alignment:
0.05 mm (0.0020 in.) per 100 mm (3.94 in.)
If the out–of–alignment is greater than maximum, replace the
connecting rod assembly.
(2) check for twist.
Maximum twist:
0.05mm (0.0020 in.) per 100 mm (3.94 in.)
If the twist is greater than maximum, replace the connecting rod
assembly.
Page 5122 of 5135
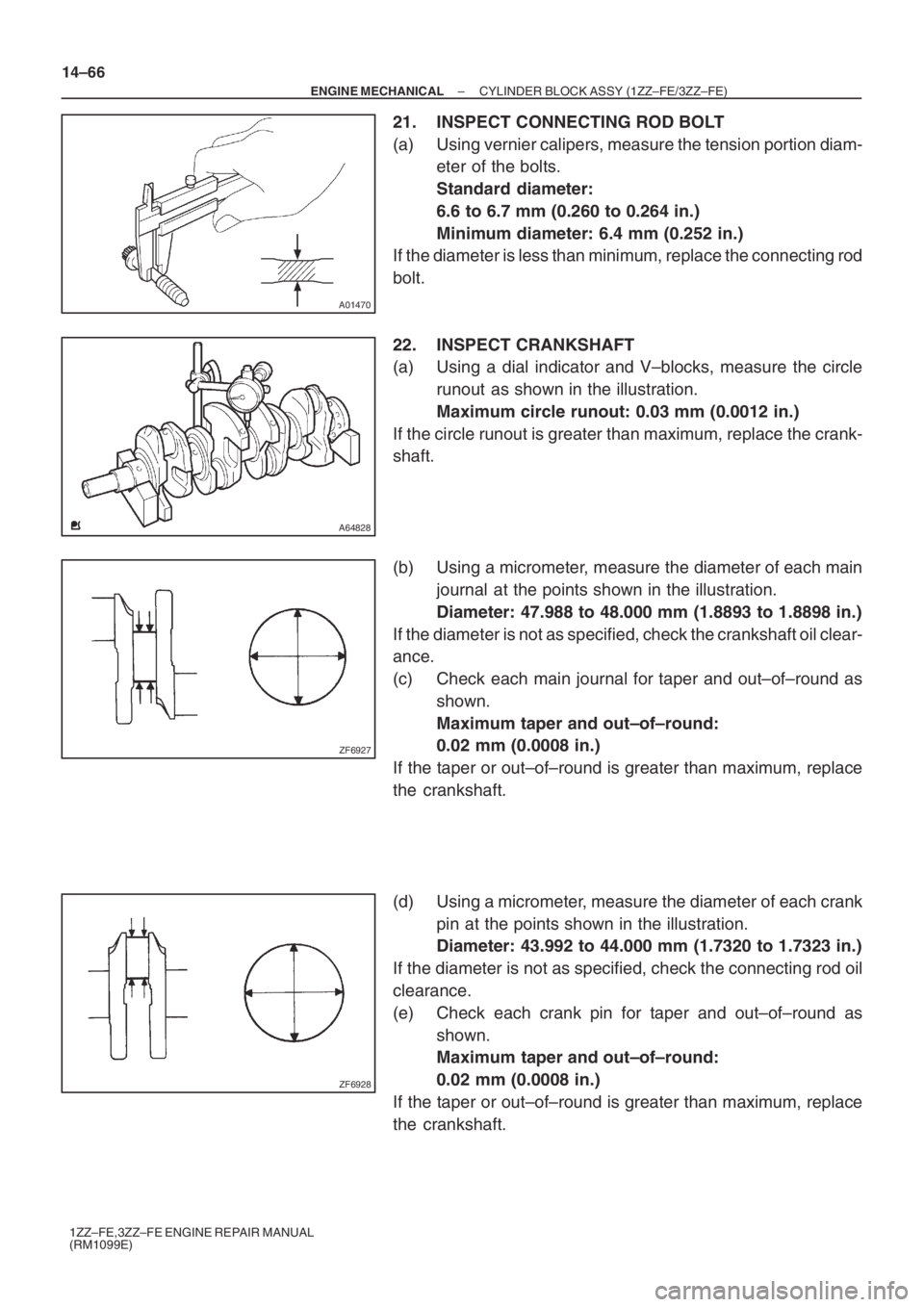
A01470
A64828
ZF6927
ZF6928
14–66
– ENGINE MECHANICALCYLINDER BLOCK ASSY (1ZZ–FE/3ZZ–FE)
1ZZ–FE,3ZZ–FE ENGINE REPAIR MANUAL
(RM1099E)
21. INSPECT CONNECTING ROD BOLT
(a) Using vernier calipers, measure the tension portion diam-
eter of the bolts.
Standard diameter:
6.6 to 6.7 mm (0.260 to 0.264 in.)
Minimum diameter: 6.4 mm (0.252 in.)
If the diameter is less than minimum, replace the connecting rod
bolt.
22. INSPECT CRANKSHAFT
(a) Using a dial indicator and V–blocks, measure the circle
runout as shown in the illustration.
Maximum circle runout: 0.03 mm (0.0012 in.)
If the circle runout is greater than maximum, replace the crank-
shaft.
(b) Using a micrometer, measure the diameter of each main
journal at the points shown in the illustration.
Diameter: 47.988 to 48.000 mm (1.8893 to 1.8898 in.)
If the diameter is not as specified, check the crankshaft oil clear-
ance.
(c) Check each main journal for taper and out–of–round as
shown.
Maximum taper and out–of–round:
0.02 mm (0.0008 in.)
If the taper or out–of–round is greater than maximum, replace
the crankshaft.
(d) Using a micrometer, measure the diameter of each crank
pin at the points shown in the illustration.
Diameter: 43.992 to 44.000 mm (1.7320 to 1.7323 in.)
If the diameter is not as specified, check the connecting rod oil
clearance.
(e) Check each crank pin for taper and out–of–round as
shown.
Maximum taper and out–of–round:
0.02 mm (0.0008 in.)
If the taper or out–of–round is greater than maximum, replace
the crankshaft.
Page 5123 of 5135
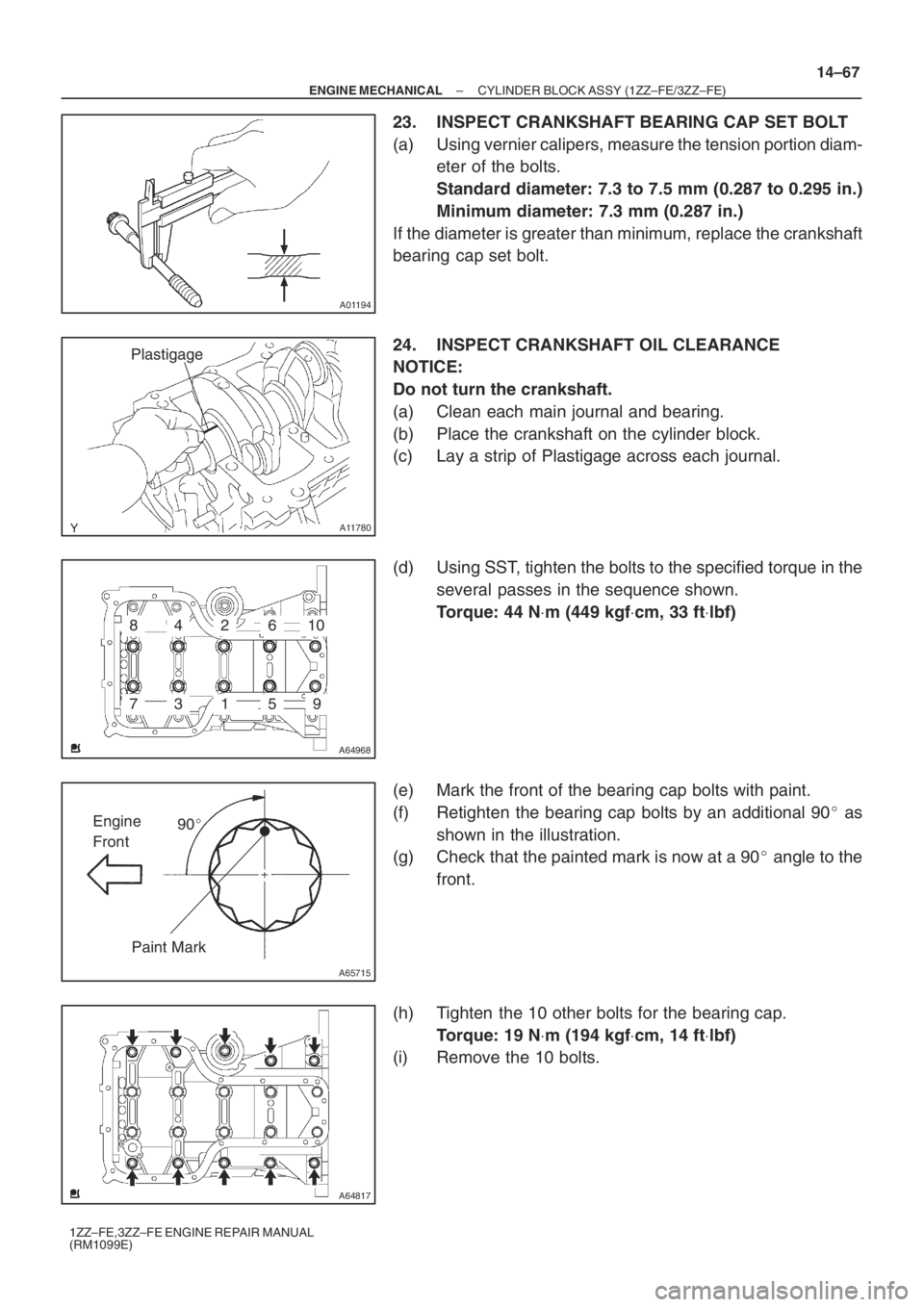
A01194
A11780
Plastigage
A64968
793
481062
15
A65715
Paint Mark90 Engine
Front
A64817
– ENGINE MECHANICALCYLINDER BLOCK ASSY (1ZZ–FE/3ZZ–FE)
14–67
1ZZ–FE,3ZZ–FE ENGINE REPAIR MANUAL
(RM1099E)
23. INSPECT CRANKSHAFT BEARING CAP SET BOLT
(a) Using vernier calipers, measure the tension portion diam-
eter of the bolts.
Standard diameter: 7.3 to 7.5 mm (0.287 to 0.295 in.)
Minimum diameter: 7.3 mm (0.287 in.)
If the diameter is greater than minimum, replace the crankshaft
bearing cap set bolt.
24. INSPECT CRANKSHAFT OIL CLEARANCE
NOTICE:
Do not turn the crankshaft.
(a) Clean each main journal and bearing.
(b) Place the crankshaft on the cylinder block.
(c) Lay a strip of Plastigage across each journal.
(d) Using SST, tighten the bolts to the specified torque in the
several passes in the sequence shown.
Torque: 44 N⋅m (449 kgf⋅cm, 33 ft⋅lbf)
(e) Mark the front of the bearing cap bolts with paint.
(f) Retighten the bearing cap bolts by an additional 90 as
shown in the illustration.
(g) Check that the painted mark is now at a 90 angle to the
front.
(h) Tighten the 10 other bolts for the bearing cap.
Torque: 19 N⋅m (194 kgf⋅cm, 14 ft⋅lbf)
(i) Remove the 10 bolts.
Page 5124 of 5135
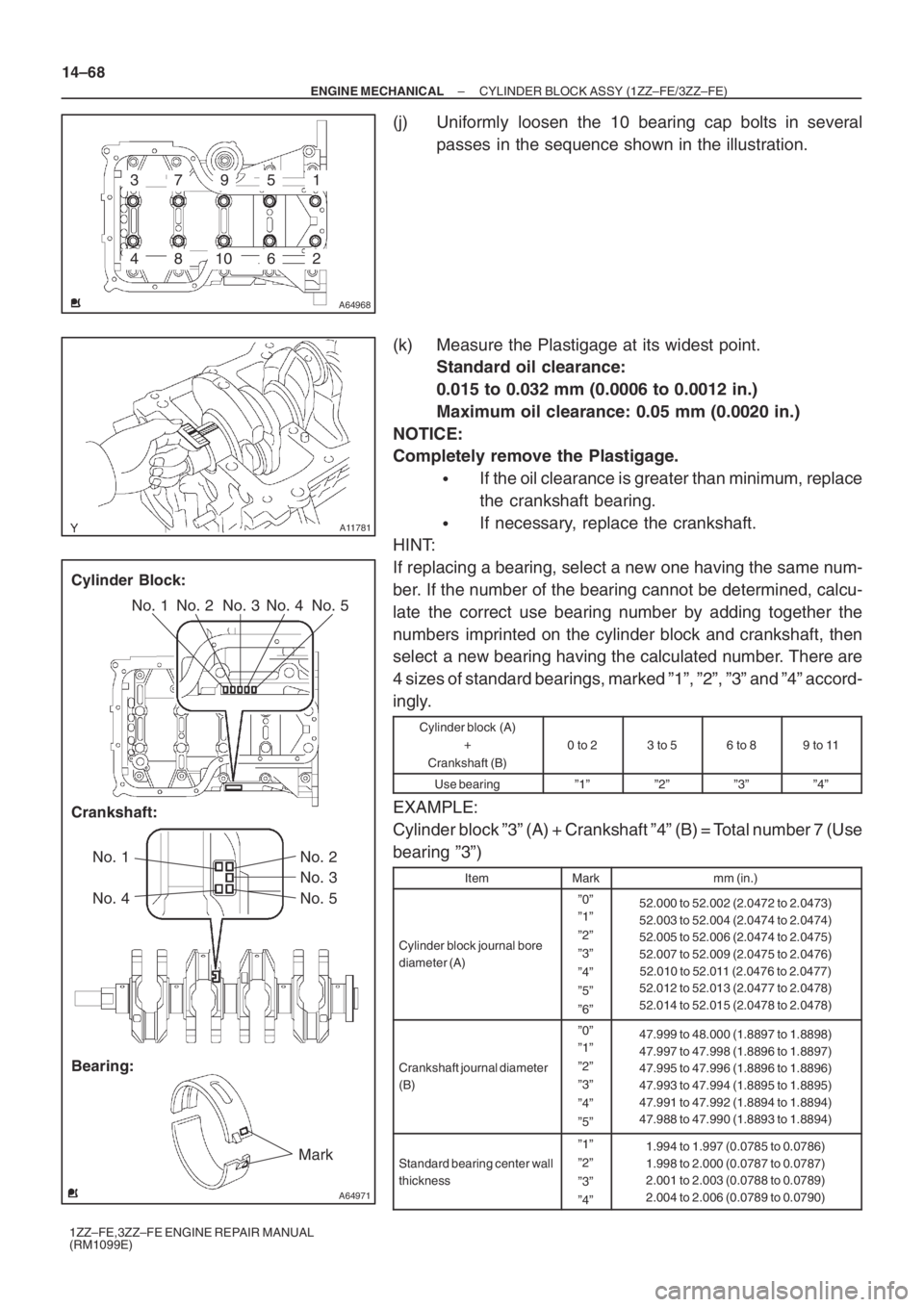
A64968
793
481062
15
A11781
A64971
Cylinder Block:
Crankshaft:
Bearing:No. 1 No. 2 No. 3 No. 4 No. 5
No. 2
No. 3
No. 5 No. 1
No. 4
Mark
14–68
– ENGINE MECHANICALCYLINDER BLOCK ASSY (1ZZ–FE/3ZZ–FE)
1ZZ–FE,3ZZ–FE ENGINE REPAIR MANUAL
(RM1099E)
(j) Uniformly loosen the 10 bearing cap bolts in several
passes in the sequence shown in the illustration.
(k) Measure the Plastigage at its widest point.
Standard oil clearance:
0.015 to 0.032 mm (0.0006 to 0.0012 in.)
Maximum oil clearance: 0.05 mm (0.0020 in.)
NOTICE:
Completely remove the Plastigage.
If the oil clearance is greater than minimum, replace
the crankshaft bearing.
If necessary, replace the crankshaft.
HINT:
If replacing a bearing, select a new one having the same num-
ber. If the number of the bearing cannot be determined, calcu-
late the correct use bearing number by adding together the
numbers imprinted on the cylinder block and crankshaft, then
select a new bearing having the calculated number. There are
4 sizes of standard bearings, marked ”1”, ”2”, ”3” and ”4” accord-
ingly.
Cylinder block (A)
+
Crankshaft (B)
0 to 23 to 56 to 89 to 11
Use bearing”1””2””3””4”
EXAMPLE:
Cylinder block ”3” (A) + Crankshaft ”4” (B) = Total number 7 (Use
bearing ”3”)
ItemMarkmm (in.)
Cylinder block journal bore
diameter (A)
”0”
”1”
”2”
”3”
”4”
”5”
”6”52.000 to 52.002 (2.0472 to 2.0473)
52.003 to 52.004 (2.0474 to 2.0474)
52.005 to 52.006 (2.0474 to 2.0475)
52.007 to 52.009 (2.0475 to 2.0476)
52.010 to 52.011 (2.0476 to 2.0477)
52.012 to 52.013 (2.0477 to 2.0478)
52.014 to 52.015 (2.0478 to 2.0478)
Crankshaft journal diameter
(B)
”0”
”1”
”2”
”3”
”4”
”5”47.999 to 48.000 (1.8897 to 1.8898)
47.997 to 47.998 (1.8896 to 1.8897)
47.995 to 47.996 (1.8896 to 1.8896)
47.993 to 47.994 (1.8895 to 1.8895)
47.991 to 47.992 (1.8894 to 1.8894)
47.988 to 47.990 (1.8893 to 1.8894)
Standard bearing center wall
thickness
”1”
”2”
”3”
”4”1.994 to 1.997 (0.0785 to 0.0786)
1.998 to 2.000 (0.0787 to 0.0787)
2.001 to 2.003 (0.0788 to 0.0789)
2.004 to 2.006 (0.0789 to 0.0790)
Page 5125 of 5135
A64972
8
155
(0.197)
(mm (in.))12
(0.472) 7.5
(0.295)8
(0.315) Front Side:
Bearing Cap Lower Side:Lower Side: Rear Side:
10
22
1510
146
ABCD A
BC
D
– ENGINE MECHANICALCYLINDER BLOCK ASSY (1ZZ–FE/3ZZ–FE)
14–69
1ZZ–FE,3ZZ–FE ENGINE REPAIR MANUAL
(RM1099E)
25. INSTALL STRAIGHT PIN
(a) Using a plastic hammer, install 9 new straight pins into the
cylinder block.
Standard protrusion:
ItemSpecification
A5.0 mm (0.197 in.)
B7.5 mm (0.295 in.)
C12.0 mm (0.472 in.)
D8.0 mm (0.315 in.)
Page 5126 of 5135
A64973
Front Side: Upper Side:
AB
B
ABC6
(0.236)7
(0.276)10
(0.394)
C
(mm (in.)) Bearing Cap Front Side:
14
1213
129
15 14–70
– ENGINE MECHANICALCYLINDER BLOCK ASSY (1ZZ–FE/3ZZ–FE)
1ZZ–FE,3ZZ–FE ENGINE REPAIR MANUAL
(RM1099E)
26. INSTALL RING PIN
(a) Using a plastic hammer, install 5 new ring pins into the cyl-
inder block.
Standard protrusion:
ItemSpecification
A6.0 mm (0.236 in.)
B7.0 mm (0.276 in.)
C10.0 mm (0.394 in.)
Page 5127 of 5135
A64974
Intake Side:
Bearing Cap Lower Side:Upper Side:
A
D
E
DC B
ABCDE
(mm)15
1238.515
1052.5
14
931.512
927.5 10
822.5
A64975
End Gap
End Gap
Pin Hole
Cutout Portion
– ENGINE MECHANICALCYLINDER BLOCK ASSY (1ZZ–FE/3ZZ–FE)
14–71
1ZZ–FE,3ZZ–FE ENGINE REPAIR MANUAL
(RM1099E)
27. INSTALL STUD BOLT
(a) Using Torx socket wrenches E5 and E7, install the 9 stud
bolts into the cylinder block.
Torque:
5.0 N⋅m (51 kgf⋅cm, 44 in.⋅lbf) for A
11 N⋅m (112 kgf⋅cm, 8 ft⋅lbf) for B
5.0 N⋅m (51 kgf⋅cm, 44 in.⋅lbf) for C
5.0 N⋅m (51 kgf⋅cm, 44 in.⋅lbf) for D
5.0 N⋅m (51 kgf⋅cm, 44 in.⋅lbf) for E
28. INSTALL W/PIN PISTON SUB–ASSY
(a) Using a small screwdriver, install a new snap ring onto
one end of the piston pin hole.
HINT:
Be sure that the end gap of the snap ring is aligned with the pin
hole cutout portion of the piston.
Page 5128 of 5135
A01187
A64976
Front
Mark
A96654
End Gap
End Gap
Pin Hole
Cutout Portion
A62811
Cord Mark
Piston Ring
Expander
14–72
– ENGINE MECHANICALCYLINDER BLOCK ASSY (1ZZ–FE/3ZZ–FE)
1ZZ–FE,3ZZ–FE ENGINE REPAIR MANUAL
(RM1099E)
(b) Gradually heat the piston up to 80 to 90C (176 to 194F).
(c) Align the front marks on the piston with the connecting
rod, then push in the piston with your thumb.
(d) Using a small screwdriver, install a new snap ring onto
one end of the piston pin hole.
HINT:
Be sure that the end gap of the snap ring is aligned with the pin
hole cutout portion of the piston.
29. INSTALL PISTON RING SET
HINT:
In case of reusing the piston rings, install them onto the
matched pistons with the surfaces facing upward correctly.
(a) Install the oil ring expander and 2 side rails by hand.
(b) Using a piston ring expander, install the 2 compression
rings with the code mark facing upward.
Code mark (No. 2 only): 2R