Page 3897 of 5135
A65743OCV+OCV±
E13
ECM Connector
Camshaft Timing Oil Control Valve
Connector
A53155
Wire Harness Side
C2
±
DIAGNOSTICS SFI SYSTEM(1ZZ±FE/3ZZ±FE)
05±123
AVENSIS REPAIR MANUAL (RM1018E)
4CHECK HARNESS AND CONNECTOR(ECM ± OCV)
(a)Disconnect the camshaft timing oil control valve connec-
tor.
(b)Disconnect the E13 ECM connector.
(c)Check for continuity between the wire harness side con- nectors.
Standard (Check for open):
Symbols (Terminal No.)Specified condition
Oil control valve (C2±1) ± OCV+ (E13±14)ContinuityOil control valve (C2±2) ± OCV± (E13±15)Continuity
Standard (Check for short):
Symbols (Terminal No.)Specified condition
Oil control valve (C2±1)or OCV+ (E13±14) ± Body groundNocontinuityOil control valve (C2±2)or OCV± (E13±15) ± Body groundNo continuity
NGREPAIR OR REPLACE HARNESS OR CONNECTOR
OK
CHECK FOR INTERMITTENT PROBLEMS (See page 05±5)
Page 3898 of 5135
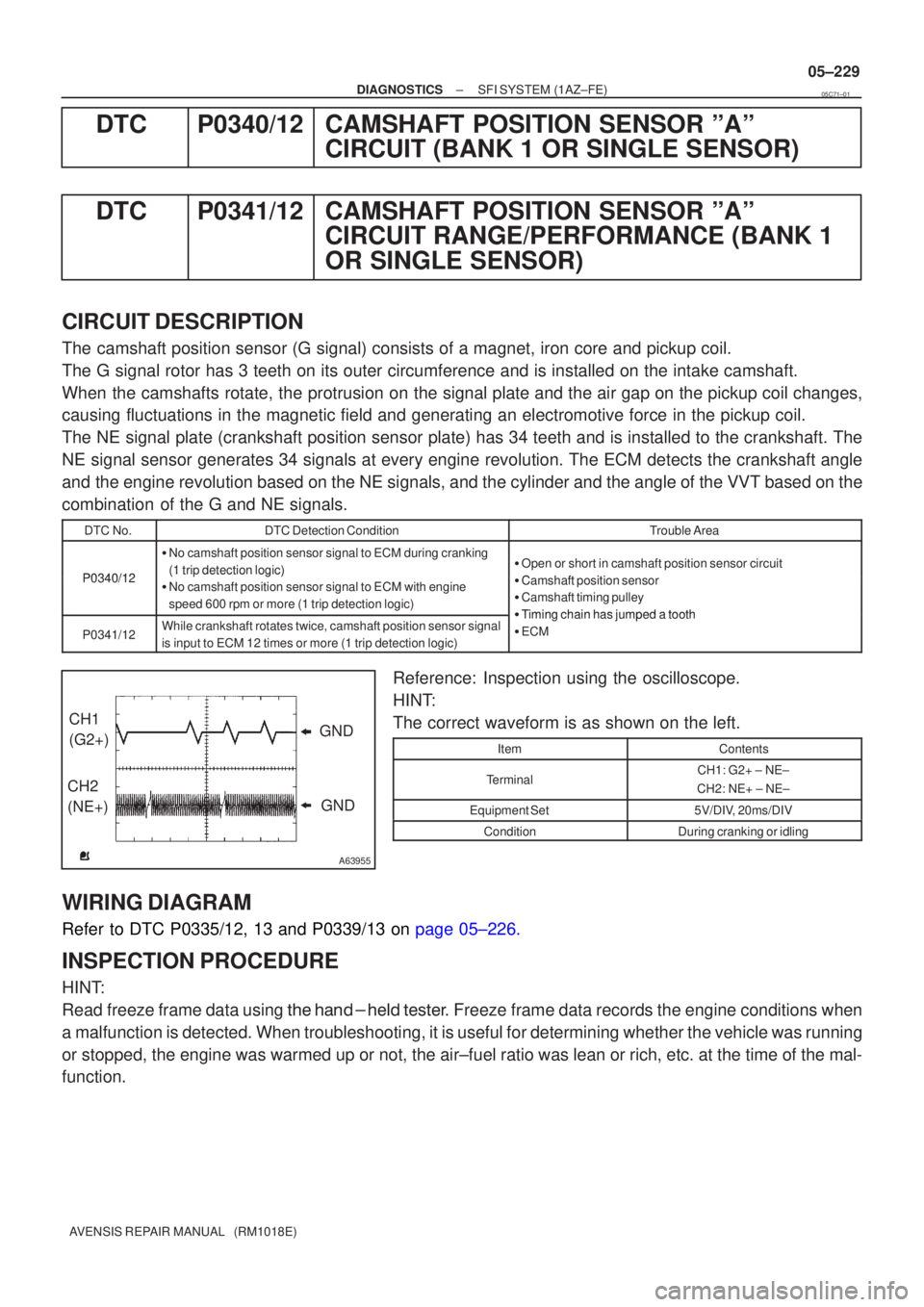
A63955
GND
CH1
(G2+)
CH2
(NE+) GND
±
DIAGNOSTICS SFI SYSTEM(1AZ±FE)
05±229
AVENSIS REPAIR MANUAL (RM1018E)
DTCP0340/12CAMSHAFT POSITION SENSOR ºAº
CIRCUIT (BANK 1 OR SINGLE SENSOR)
DTCP0341/12CAMSHAFT POSITION SENSOR ºAº CIRCUIT RANGE/PERFORMANCE (BANK 1
OR SINGLE SENSOR)
CIRCUIT DESCRIPTION
The camshaft position sensor (G signal) consists of a magnet, iron core a\
nd pickup coil.
The G signal rotor has 3 teeth on its outer circumference and is install\
ed on the intake camshaft.
When the camshafts rotate, the protrusion on the signal plate and the air gap on the pickup coil changes,
causing fluctuations in the magnetic field and generating an electromoti\
ve force in the pickup coil.
The NE signal plate (crankshaft position sensor plate) has 34 teeth an\
d is installed to the crankshaft. The
NE signal sensor generates 34 signals at every engine revolution. The EC\
M detects the crankshaft angle
and the engine revolution based on the NE signals, and the cylinder and the\
angle of the VVT based on the
combination of the G and NE signals.
DTC No.DTC Detection ConditionTrouble Area
P0340/12
No camshaft position sensor signal to ECM during cranking
(1 trip detection logic)Open or short in camshaft position sensor circuit
ChftitiP0340/12(1 tri detection logic)
No camshaft position sensor signal to ECM with engine
speed 600 rpm or more (1 trip detection logic)Camshaft position sensor
Camshaft timing pulley
Timingchainhasjumpedatooth
P0341/12While crankshaft rotates twice, camshaft position sensor signal
is input to ECM 12 times or more (1 trip detection logic)Timing chain has jumped a tooth
ECM
Reference: Inspection using the oscilloscope.
HINT:
The correct waveform is as shown on the left.
ItemContents
TerminalCH1: G2+ ± NE±
CH2: NE+ ± NE±
Equipment Set5V/DIV, 20ms/DIV
ConditionDuring cranking or idling
WIRING DIAGRAM
Refer to DTC P0335/12, 13 and P0339/13 on page 05±226.
INSPECTION PROCEDURE
HINT:
Read freeze frame data using \f \b \f\f
Freeze frame data records the engine conditions when
a malfunction is detected. When troubleshooting, it is useful for determi\
ning whether the vehicle was running
or stopped, the engine was warmed up or not, the air±fuel ratio was lea\
n or rich, etc. at the time of the mal-
function.
05C71±01
Page 3899 of 5135
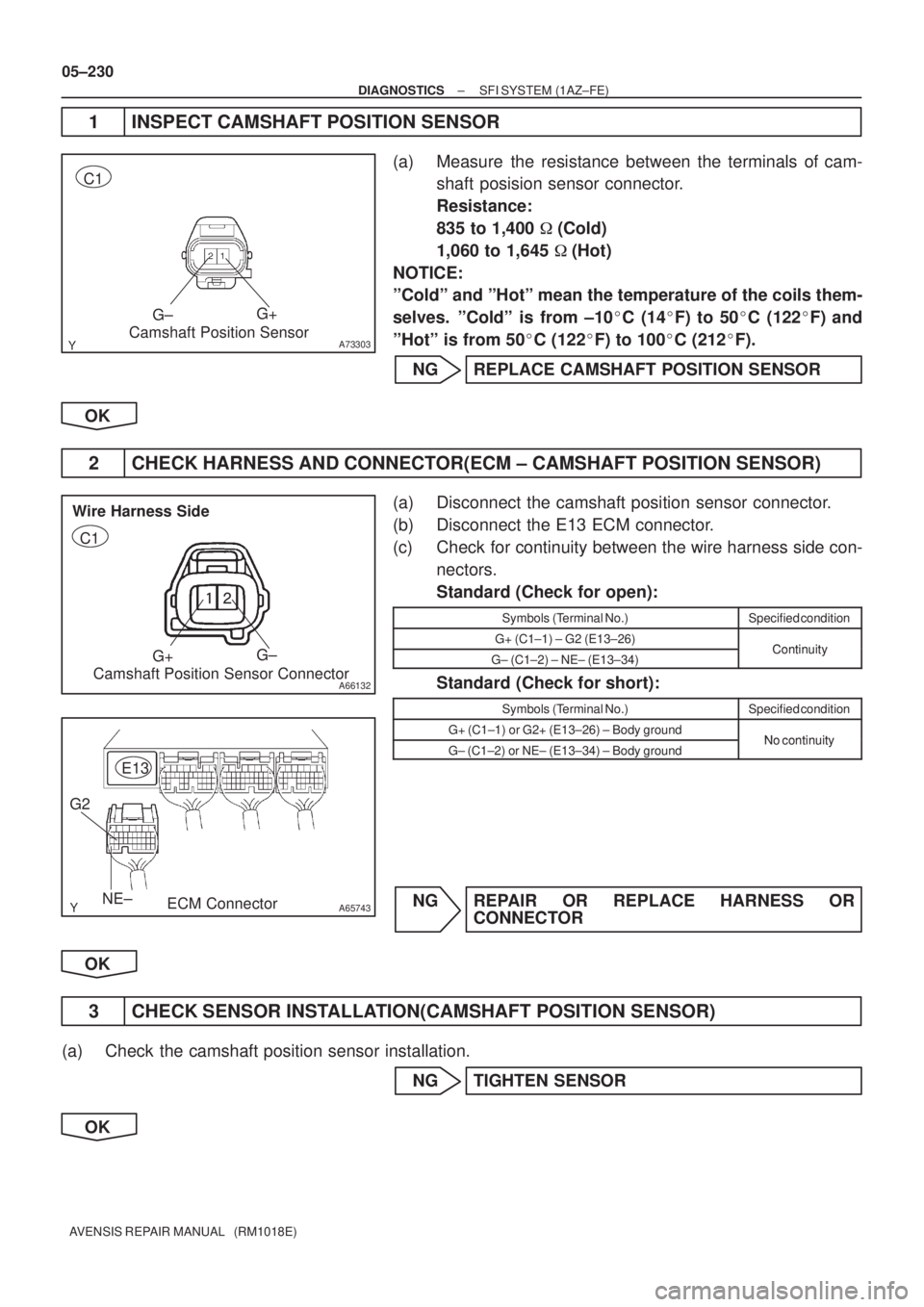
A73303
G±G+
Camshaft Position Sensor C1
A66132
G+G±
Camshaft Position Sensor Connector Wire Harness Side
C1
A65743NE± G2
E13
ECM Connector
05±230
± DIAGNOSTICSSFI SYSTEM (1AZ±FE)
AVENSIS REPAIR MANUAL (RM1018E)
1 INSPECT CAMSHAFT POSITION SENSOR
(a) Measure the resistance between the terminals of cam-
shaft posision sensor connector.
Resistance:
835 to 1,400 (Cold)
1,060 to 1,645 (Hot)
NOTICE:
ºColdº and ºHotº mean the temperature of the coils them-
selves. ºColdº is from ±10C (14F) to 50C (122F) and
ºHotº is from 50C (122F) to 100C (212F).
NG REPLACE CAMSHAFT POSITION SENSOR
OK
2 CHECK HARNESS AND CONNECTOR(ECM ± CAMSHAFT POSITION SENSOR)
(a) Disconnect the camshaft position sensor connector.
(b) Disconnect the E13 ECM connector.
(c) Check for continuity between the wire harness side con-
nectors.
Standard (Check for open):
Symbols (Terminal No.)Specified condition
G+ (C1±1) ± G2 (E13±26)ContinuityG± (C1±2) ± NE± (E13±34)Continuity
Standard (Check for short):
Symbols (Terminal No.)Specified condition
G+ (C1±1) or G2+ (E13±26) ± Body groundNo continuityG± (C1±2) or NE± (E13±34) ± Body groundNo continuity
NG REPAIR OR REPLACE HARNESS OR
CONNECTOR
OK
3 CHECK SENSOR INSTALLATION(CAMSHAFT POSITION SENSOR)
(a) Check the camshaft position sensor installation.
NG TIGHTEN SENSOR
OK
Page 3900 of 5135
±
DIAGNOSTICS SFI SYSTEM(1AZ±FE)
05±231
AVENSIS REPAIR MANUAL (RM1018E)
4INSPECT CAMSHAFT
(a)Check the teeth of the signal plate.
NGREPLACE CAMSHAFT
OK
CHECK AND REPLACE ECM (See page 01±32)
Page 3901 of 5135
±
DIAGNOSTICS SFI SYSTEM(1ZZ±FE/3ZZ±FE)
05±111
AVENSIS REPAIR MANUAL (RM1018E)
DTCP1346VVT SENSOR/CAMSHAFT POSITION
SENSOR CIRCUIT RANGE/PERFORMANCE
PROBLEM (BANK 1)
CIRCUIT DESCRIPTION
Refer to DTC P0335 on page 05±84
DTC No.Detection ItemTrouble Area
P1346Deviation in crankshaft position sensor signal and camshaft
position sensor signal (2 trip detection logic)Mechanical system (Timing chain has jumped a tooth, chain
stretched)
ECM
WIRING DIAGRAM
Refer to DTC P0335 on page 05±84
INSPECTION PROCEDURE
HINT:
Read freeze frame data using the hand±held tester. Freeze frame data records the engine conditions when
the malfunction is detected. When troubleshooting, it is useful for determining whether the vehicle was run-
ning or stopped, the engine was warmed up or not, the air±fuel ratio \
was lean or rich, etc. at the time of the
malfunction.
1CHECK VALVE TIMING (See page 14±49)
NGADJUST VALVE TIMING(See page 14±49)
OK
CHECK AND REPLACE ECM (See page 01±32)
0506C±04
Page 3902 of 5135
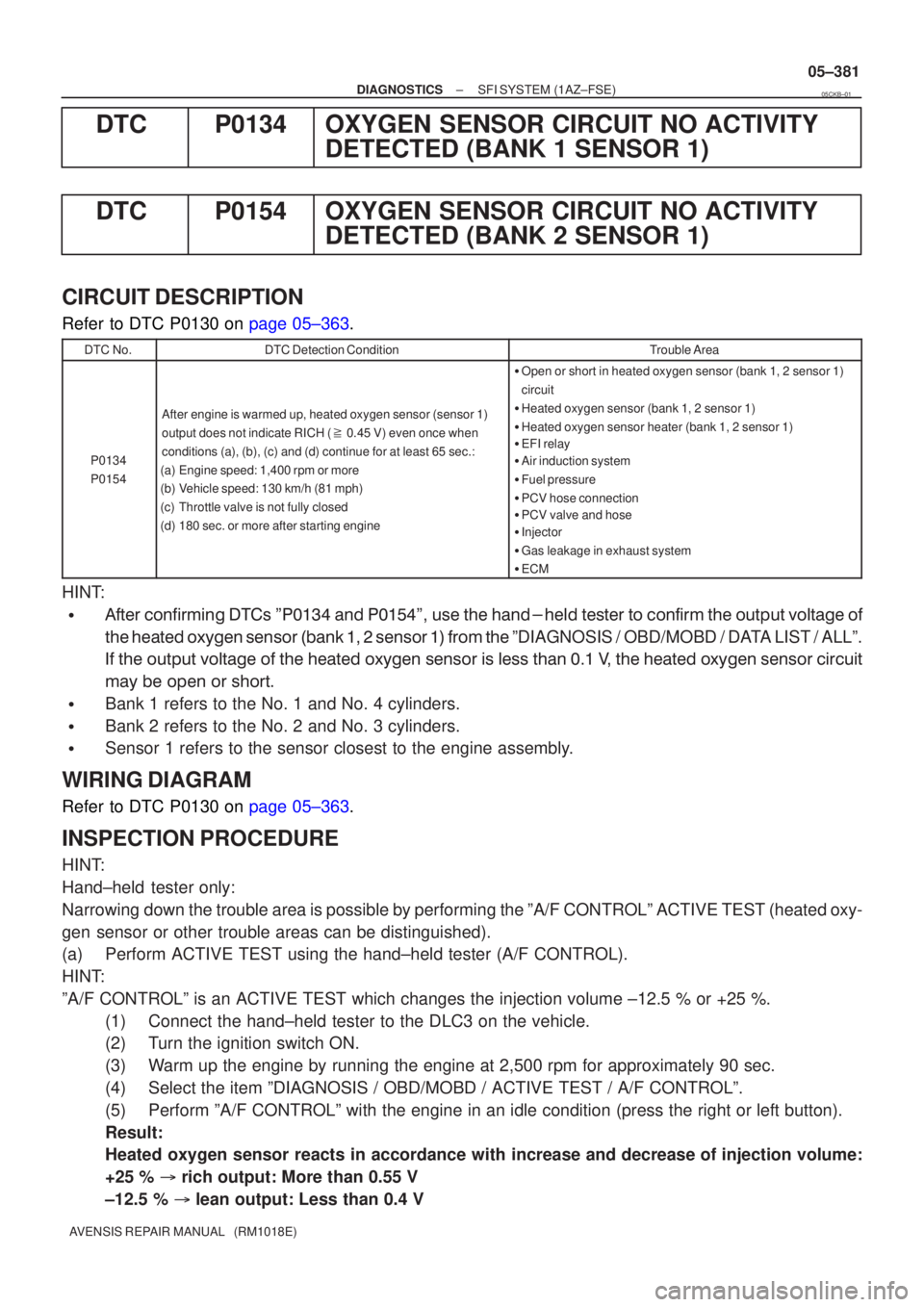
±
DIAGNOSTICS SFI SYSTEM(1AZ±FSE)
05±381
AVENSIS REPAIR MANUAL (RM1018E)
DTCP0134OXYGEN SENSOR CIRCUIT NO ACTIVITY
DETECTED (BANK 1 SENSOR 1)
DTCP0154OXYGEN SENSOR CIRCUIT NO ACTIVITY DETECTED (BANK 2 SENSOR 1)
CIRCUIT DESCRIPTION
Refer to DTC P0130 on page 05±363.
DTC No.DTC Detection ConditionTrouble Area
P0134
P0154
After engine is warmed up, heated oxygen sensor (sensor 1)
output does not indicate RICH ( 0.45 V) even once when
conditions (a), (b), (c) and (d) continue for at least 65 sec.:
(a)Engine speed: 1,400 rpm or more
(b)Vehicle speed: 130 km/h (81 mph)
(c)Throttle valve is not fully closed
(d)180 sec. or more after starting engine
Open or short in heated oxygen sensor (bank 1, 2 sensor 1)
circuit
Heated oxygen sensor (bank 1, 2 sensor 1)
Heated oxygen sensor heater (bank 1, 2 sensor 1)
EFI relay
Air induction system
Fuel pressure
PCV hose connection
PCV valve and hose
Injector
Gas leakage in exhaust system
ECM
HINT:
&$"!$ !%\b \f!\b
\f'%&!&%&$&""!$ &"''&("&"
&&")*!%!%"$!
%!%"$ $" & ºDIAGNOSIS / OBD/MOBD / DATA LIST / ALLº
&"''&("&"&&")*!%!%"$%%%&!\b &&")*!%!%"$$'&
*"#!"$%"$&
Bank 1 refers to the No. 1 and No. 4 cylinders.
Bank 2 refers to the No. 2 and No. 3 cylinders.
Sensor 1 refers to the sensor closest to the engine assembly.
WIRING DIAGRAM
Refer to DTC P0130 on page 05±363.
INSPECTION PROCEDURE
HINT:
Hand±held tester only:
Narrowing down the trouble area is possible by performing the ºA/F CONTROLº ACTIVE TEST (heated oxy-
gen sensor or other trouble areas can be distinguished).
(a) Perform ACTIVE TEST using the hand±held tester (A/F CONTROL).
HINT:
ºA/F CONTROLº is an ACTIVE TEST which changes the injection volume\
±12.5 % or +25 %.
(1) Connect the hand±held tester to the DLC3 on the vehicle.
(2) Turn the ignition switch ON.
(3) Warm up the engine by running the engine at 2,500 rpm for approximately 9\
0 sec.
(4) Select the item ºDIAGNOSIS / OBD/MOBD / ACTIVE TEST / A/F CONTROLº\
.
(5) Perform ºA/F CONTROLº with the engine in an idle condition (press\
the right or left button).
Result:
Heated oxygen sensor reacts in accordance with increase and decrease of injection volume:
+25 % rich output: More than 0.55 V
±12.5 % lean output: Less than 0.4 V
05CKB±01
Page 3903 of 5135
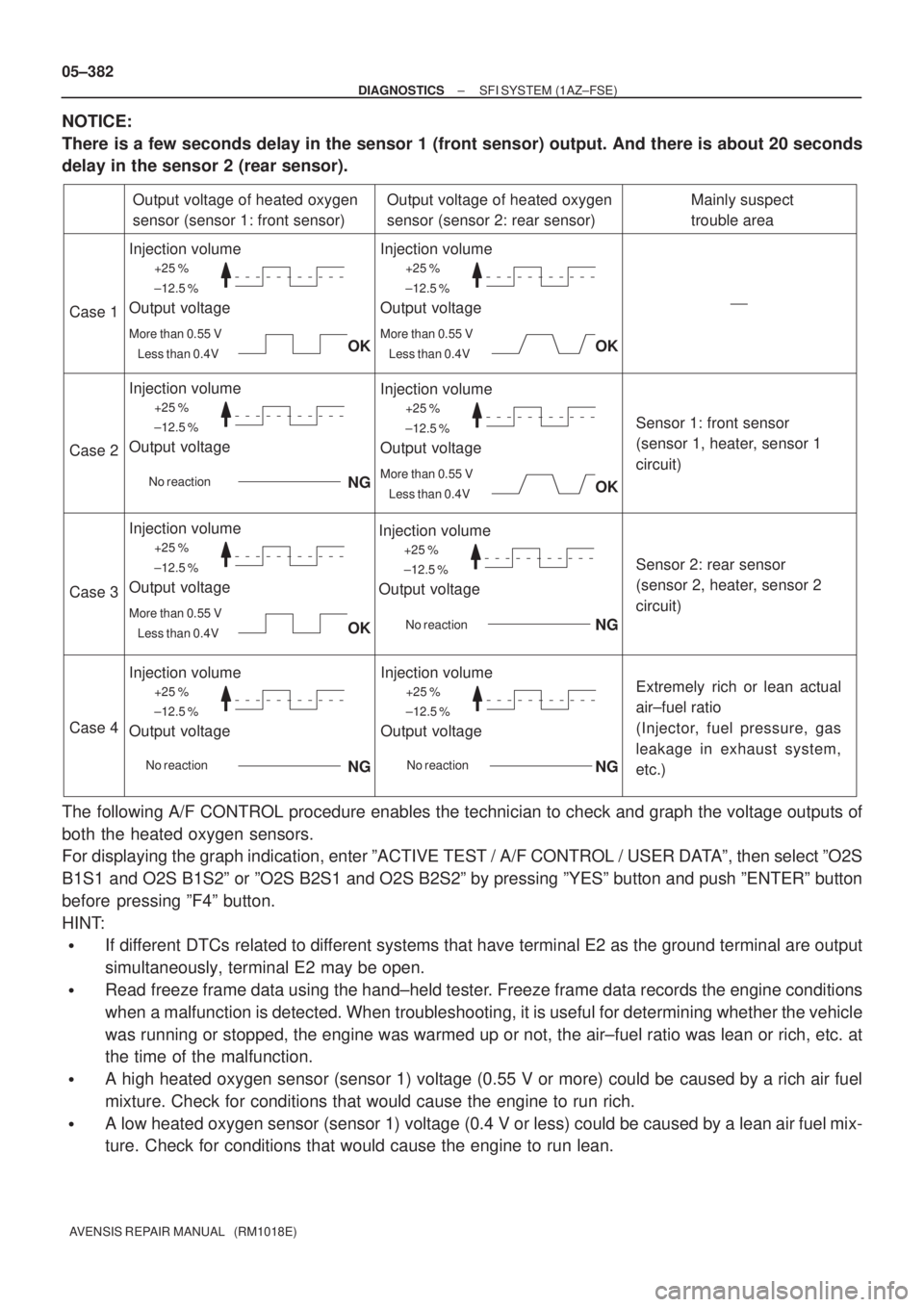
+25 %
±12.5 %
More than 0.55 V
Less than 0.4V
Case 1
Case 2
Case 3
Case 4
Output voltage of heated oxygen
sensor (sensor 1: front sensor)
Injection volume
Output voltage
Output voltage of heated oxygen
sensor (sensor 2: rear sensor)Mainly suspect
trouble area
OK
+25 %
±12.5 %
More than 0.55 V
Less than 0.4V
Injection volume
Output voltage
+25 %
±12.5 %
More than 0.55 V
Less than 0.4V
Injection volume
Output voltage
Sensor 1: front sensor
(sensor 1, heater, sensor 1
circuit)
+25 %
±12.5 %
More than 0.55 V
Less than 0.4V
Injection volume
Output voltage
+25 %
±12.5 %
Injection volume
Output voltage
NG
+25 %
±12.5 %
Injection volume
Output voltage
NG
+25 %
±12.5 %
Injection volume
Output voltage
NG
+25 %
±12.5 %
Injection volume
Output voltage
NGExtremely rich or lean actual
air±fuel ratio
(Injector, fuel pressure, gas
leakage in exhaust system,
etc.) OK
OK
OK
No reaction
No reaction
No reaction No reaction
Sensor 2: rear sensor
(sensor 2, heater, sensor 2
circuit) 05±382
± DIAGNOSTICSSFI SYSTEM (1AZ±FSE)
AVENSIS REPAIR MANUAL (RM1018E)
NOTICE:
There is a few seconds delay in the sensor 1 (front sensor) output. And there is about 20 seconds
delay in the sensor 2 (rear sensor).
The following A/F CONTROL procedure enables the technician to check and graph the voltage outputs of
both the heated oxygen sensors.
For displaying the graph indication, enter ºACTIVE TEST / A/F CONTROL / USER DATAº, then select ºO2S
B1S1 and O2S B1S2º or ºO2S B2S1 and O2S B2S2º by pressing ºYESº button and push ºENTERº button
before pressing ºF4º button.
HINT:
If different DTCs related to different systems that have terminal E2 as the ground terminal are output
simultaneously, terminal E2 may be open.
Read freeze frame data using the hand±held tester. Freeze frame data records the engine conditions
when a malfunction is detected. When troubleshooting, it is useful for determining whether the vehicle
was running or stopped, the engine was warmed up or not, the air±fuel ratio was lean or rich, etc. at
the time of the malfunction.
A high heated oxygen sensor (sensor 1) voltage (0.55 V or more) could be caused by a rich air fuel
mixture. Check for conditions that would cause the engine to run rich.
A low heated oxygen sensor (sensor 1) voltage (0.4 V or less) could be caused by a lean air fuel mix-
ture. Check for conditions that would cause the engine to run lean.
Page 3904 of 5135
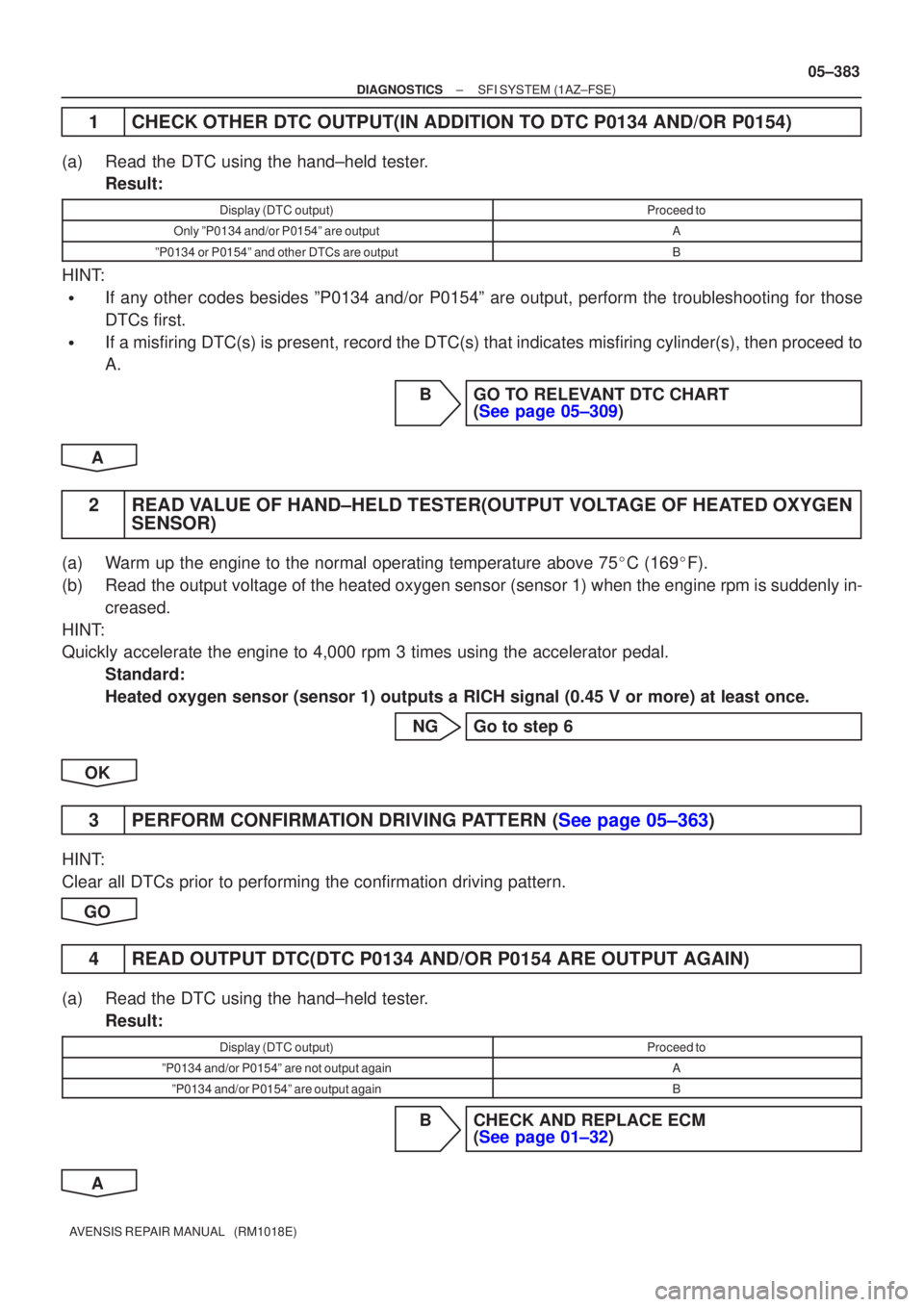
±
DIAGNOSTICS SFI SYSTEM(1AZ±FSE)
05±383
AVENSIS REPAIR MANUAL (RM1018E)
1CHECK OTHER DTC OUTPUT(IN ADDITION TO DTC P0134 AND/OR P0154)
(a)Read the DTC using the hand±held tester.
Result:
Display (DTC output)Proceed to
Only ºP0134 and/or P0154º are outputA
ºP0134 or P0154º and other DTCs are outputB
HINT:
If any other codes besides ºP0134 and/or P0154º are output, perform t\
he troubleshooting for those
DTCs first.
If a misfiring DTC(s) is present, record the DTC(s) that indicates mis\
firing cylinder(s), then proceed to
A.
BGO TO RELEVANT DTC CHART (See page 05±309)
A
2READ VALUE OF HAND±HELD TESTER(OUTPUT VOLTAGE OF HEATED OXYGEN SENSOR)
(a)Warm up the engine to the normal operating temperature above 75 C (169 F).
(b)Read the output voltage of the heated oxygen sensor (sensor 1) when the engine rpm is suddenly\
in- creased.
HINT:
Quickly accelerate the engine to 4,000 rpm 3 times using the accelerator pedal.\
Standard:
Heated oxygen sensor (sensor 1) outputs a RICH signal (0.45 V or more\
) at least once.
NGGo to step 6
OK
3PERFORM CONFIRMATION DRIVING PATTERN (See page 05±363)
HINT:
Clear all DTCs prior to performing the confirmation driving pattern. GO
4READ OUTPUT DTC(DTC P0134 AND/OR P0154 ARE OUTPUT AGAIN)
(a)Read the DTC using the hand±held tester. Result:
Display (DTC output)Proceed to
ºP0134 and/or P0154º are not output againA
ºP0134 and/or P0154º are output againB
BCHECK AND REPLACE ECM (See page 01±32)
A