Page 793 of 5135
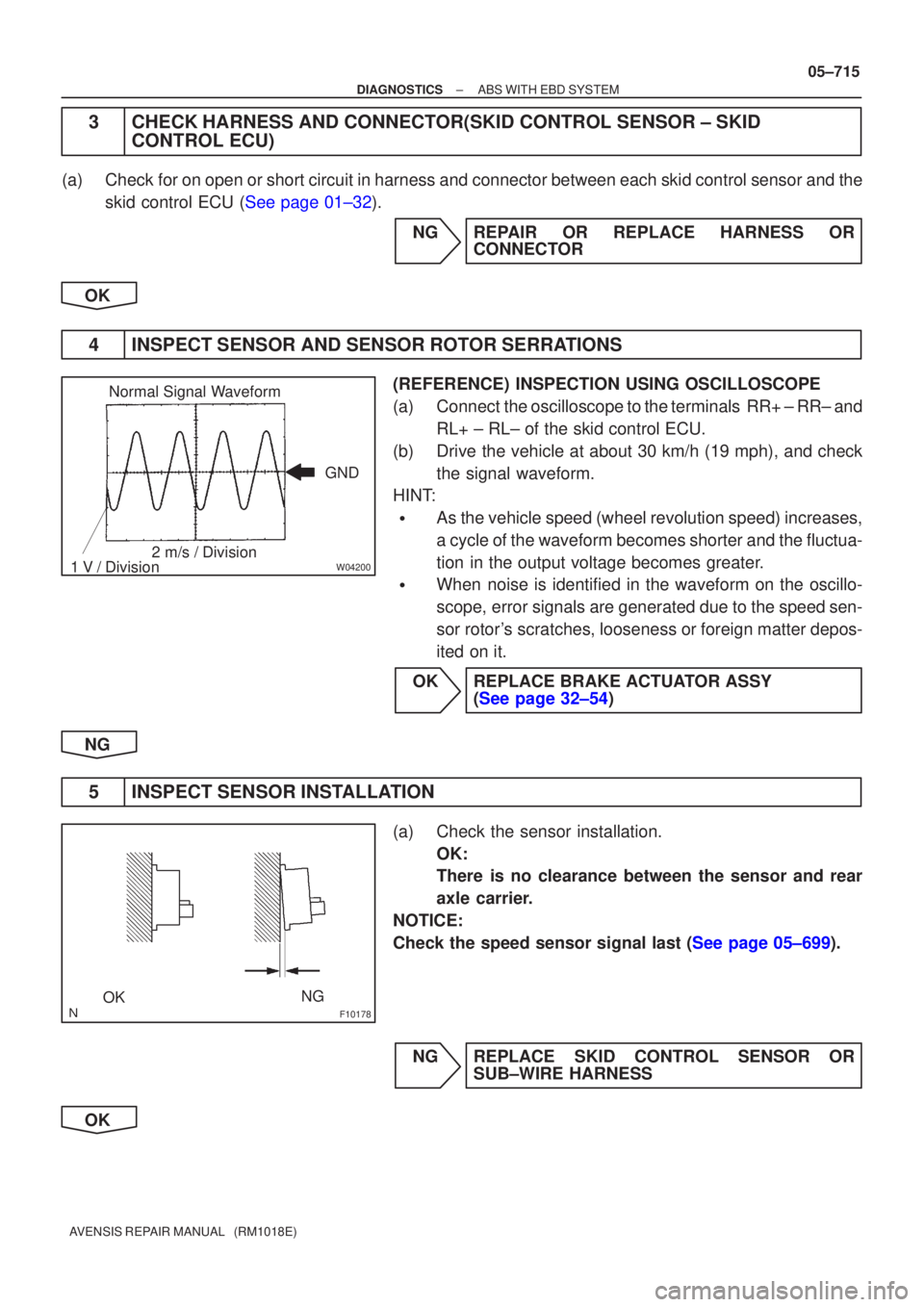
W04200
Normal Signal Waveform
1 V / Division 2 m/s / Division GND
F10178OK
NG
±
DIAGNOSTICS ABS WITH EBD SYSTEM
05±715
AVENSIS REPAIR MANUAL (RM1018E)
3CHECK HARNESS AND CONNECTOR(SKID CONTROL SENSOR ± SKID
CONTROL ECU)
(a)Check for on open or short circuit in harness and connector between each skid\
control sensor and the
skid control ECU (See page 01±32).
NGREPAIR OR REPLACE HARNESS ORCONNECTOR
OK
4INSPECT SENSOR AND SENSOR ROTOR SERRATIONS
(REFERENCE) INSPECTION USING OSCILLOSCOPE
(a)Connect the oscilloscope to the terminals RR+ ± RR± and RL+ ± RL± of the skid control ECU.
(b)Drive the vehicle at about 30 km/h (19 mph), and check the signal waveform.
HINT:
As the vehicle speed (wheel revolution speed) increases,
a cycle of the waveform becomes shorter and the fluctua-
tion in the output voltage becomes greater.
When noise is identified in the waveform on the oscillo-
scope, error signals are generated due to the speed sen-
sor rotor's scratches, looseness or foreign matter depos-
ited on it.
OKREPLACE BRAKE ACTUATOR ASSY (See page 32±54)
NG
5 INSPECT SENSOR INSTALLATION
(a) Check the sensor installation. OK:
There is no clearance between the sensor and rear
axle carrier.
NOTICE:
Check the speed sensor signal last (See page 05±699).
NG REPLACE SKID CONTROL SENSOR OR SUB±WIRE HARNESS
OK
Page 794 of 5135
W04846
05±716
±
DIAGNOSTICS ABS WITH EBD SYSTEM
AVENSIS REPAIR MANUAL (RM1018E)
6INSPECT SPEED SENSOR TIP
(a)Remove the skid control sensor (See page 32±61).
(b)Check the sensor tip. OK:
No scratches or foreign objects on the sensor tip. NOTICE:
Check the speed sensor signal last (See page 05±699).
NGCLEAN OR REPAIR SKID CONTORL SENSOR
OK
7INSPECT SENSOR ROTOR
(a)Check the sensor rotor serrations. OK:
No scratches, missing teeth or foreign objects.
NOTICE:
Check the speed sensor signal last (See page 05±699).
NGREPLACE REAR AXLE HUB & BEARING ASSY RH
NGREPLACE REAR AXLE HUB & BEARING ASSY LH
OK
REPLACE BRAKE ACTUATOR ASSY(See page 32±54)
Page 795 of 5135
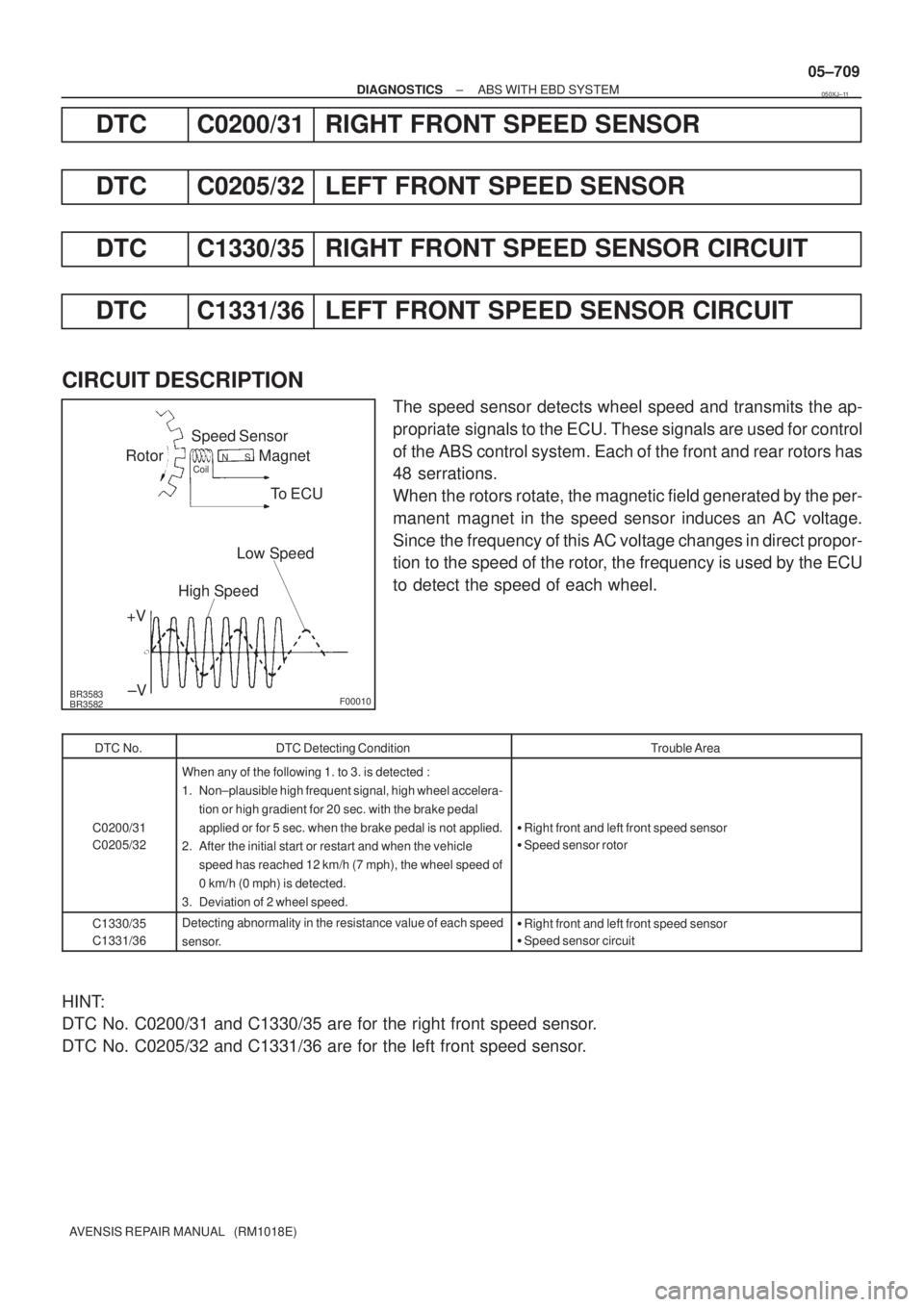
BR3583
BR3582F00010
Rotor
+VSpeed Sensor
MagnetCoilNS
To ECU
Low Speed
High Speed
±V
± DIAGNOSTICSABS WITH EBD SYSTEM
05±709
AVENSIS REPAIR MANUAL (RM1018E)
DTC C0200/31 RIGHT FRONT SPEED SENSOR
DTC C0205/32 LEFT FRONT SPEED SENSOR
DTC C1330/35 RIGHT FRONT SPEED SENSOR CIRCUIT
DTC C1331/36 LEFT FRONT SPEED SENSOR CIRCUIT
CIRCUIT DESCRIPTION
The speed sensor detects wheel speed and transmits the ap-
propriate signals to the ECU. These signals are used for control
of the ABS control system. Each of the front and rear rotors has
48 serrations.
When the rotors rotate, the magnetic field generated by the per-
manent magnet in the speed sensor induces an AC voltage.
Since the frequency of this AC voltage changes in direct propor-
tion to the speed of the rotor, the frequency is used by the ECU
to detect the speed of each wheel.
DTC No.DTC Detecting ConditionTrouble Area
C0200/31
C0205/32
When any of the following 1. to 3. is detected :
1. Non±plausible high frequent signal, high wheel accelera-
tion or high gradient for 20 sec. with the brake pedal
applied or for 5 sec. when the brake pedal is not applied.
2. After the initial start or restart and when the vehicle
speed has reached 12 km/h (7 mph), the wheel speed of
0 km/h (0 mph) is detected.
3. Deviation of 2 wheel speed.
Right front and left front speed sensor
Speed sensor rotor
C1330/35
C1331/36Detecting abnormality in the resistance value of each speed
sensor.Right front and left front speed sensor
Speed sensor circuit
HINT:
DTC No. C0200/31 and C1330/35 are for the right front speed sensor.
DTC No. C0205/32 and C1331/36 are for the left front speed sensor.
050XJ±11
Page 796 of 5135
F40884
2
1
W
B10
9FR+
FR± S2 A4
ABS Speed Sensor
Front LH
A5
ABS Speed Sensor
Front RH2
16
S25
S2
S2FL+
FL± L±Y
R±LSkid Control ECU
with Actuator
05±710
± DIAGNOSTICSABS WITH EBD SYSTEM
AVENSIS REPAIR MANUAL (RM1018E)
WIRING DIAGRAM
INSPECTION PROCEDURE
HINT:
Start the inspection from step 1 if you are using the hand±held tester and start from step 2 if you are not using
the hand±held tester.
1 READ VALUE OF HAND±HELD TESTER(FRONT SPEED SENSOR)
(a) Select the item ºWHEEL SPEED FL (FR)º in the DATA LIST and read the value displayed on the hand±
held tester.
(b) Check that there is no difference between the speed value output from the speed sensor displayed
on the hand±held tester and the speed value displayed on the speedometer when driving the vehicle.
OK:
There is almost no difference in the displayed speed value.
HINT:
There is tolerance of 10 % in the speedometer indication.
OK Go to step 5
NG
Page 797 of 5135
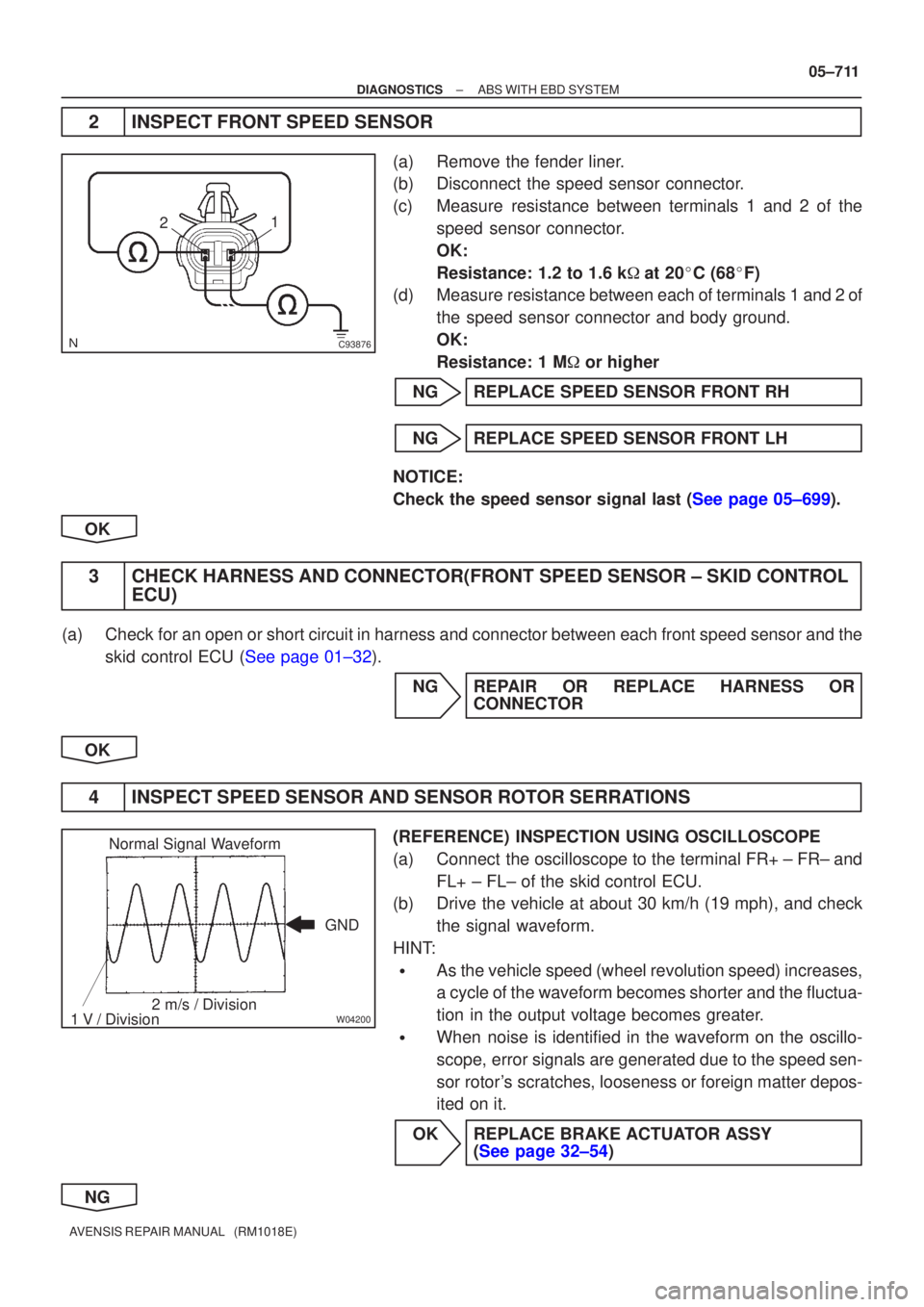
C93876
21
W04200
Normal Signal Waveform
1 V / Division 2 m/s / Division GND
±
DIAGNOSTICS ABS WITH EBD SYSTEM
05±711
AVENSIS REPAIR MANUAL (RM1018E)
2INSPECT FRONT SPEED SENSOR
(a)Remove the fender liner.
(b)Disconnect the speed sensor connector.
(c)Measure resistance between terminals 1 and 2 of the
speed sensor connector.
OK:
Resistance: 1.2 to 1.6 k at 20 C (68 F)
(d)Measure resistance between each of terminals 1 and 2 of
the speed sensor connector and body ground.
OK:
Resistance: 1 M or higher
NGREPLACE SPEED SENSOR FRONT RH
NGREPLACE SPEED SENSOR FRONT LH
NOTICE:
Check the speed sensor signal last (See page 05±699).
OK
3CHECK HARNESS AND CONNECTOR(FRONT SPEED SENSOR ± SKID CONTROL ECU)
(a)Check for an open or short circuit in harness and connector between each front speed sensor and the
skid control ECU (See page 01±32).
NGREPAIR OR REPLACE HARNESS ORCONNECTOR
OK
4INSPECT SPEED SENSOR AND SENSOR ROTOR SERRATIONS
(REFERENCE) INSPECTION USING OSCILLOSCOPE
(a)Connect the oscilloscope to the terminal FR+ ± FR± and FL+ ± FL± of the skid control ECU.
(b)Drive the vehicle at about 30 km/h (19 mph), and check
the signal waveform.
HINT:
As the vehicle speed (wheel revolution speed) increases,
a cycle of the waveform becomes shorter and the fluctua-
tion in the output voltage becomes greater.
When noise is identified in the waveform on the oscillo-
scope, error signals are generated due to the speed sen-
sor rotor's scratches, looseness or foreign matter depos-
ited on it.
OKREPLACE BRAKE ACTUATOR ASSY (See page 32±54)
NG
Page 798 of 5135
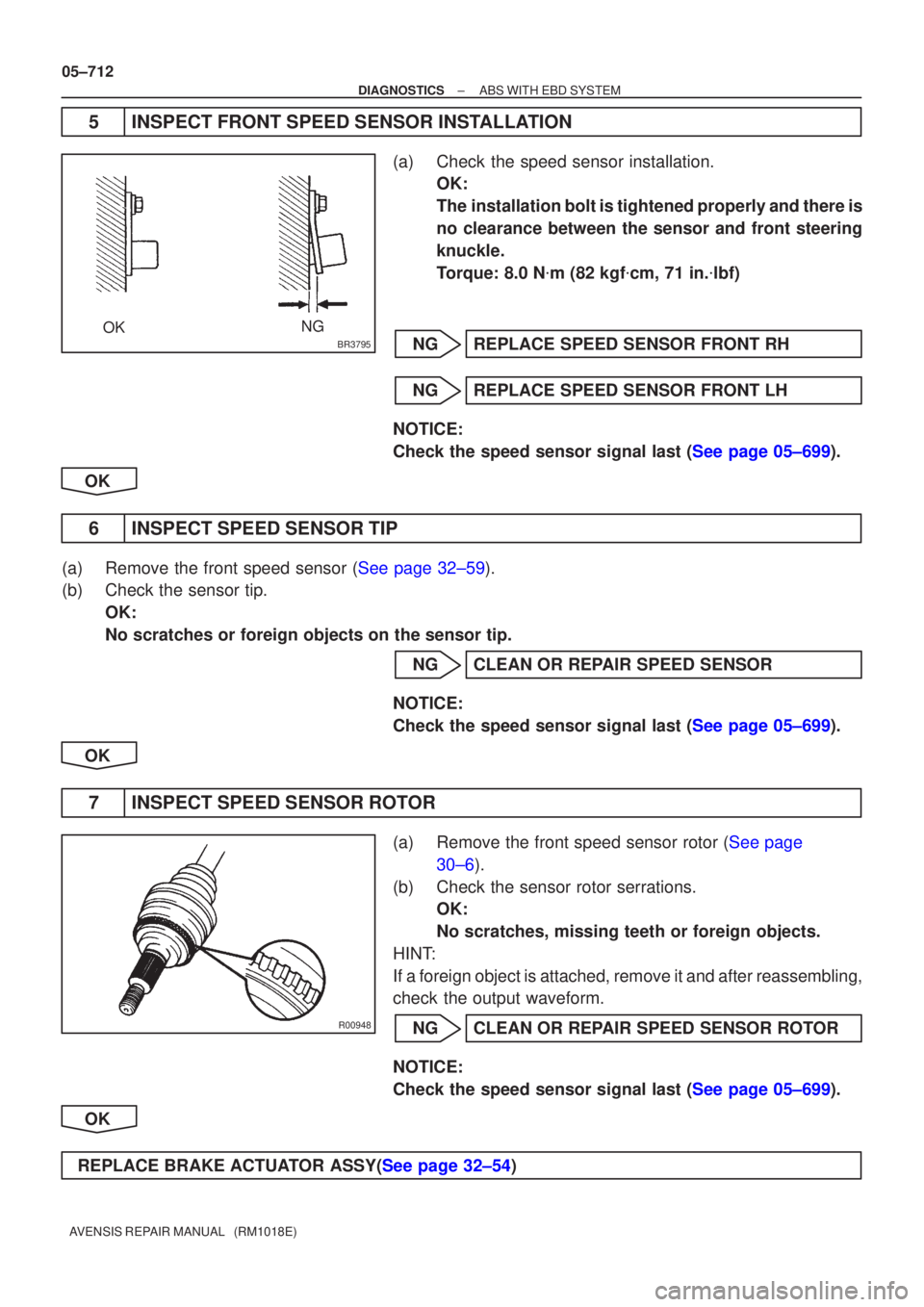
BR3795OKNG
R00948
05±712
±
DIAGNOSTICS ABS WITH EBD SYSTEM
AVENSIS REPAIR MANUAL (RM1018E)
5INSPECT FRONT SPEED SENSOR INSTALLATION
(a)Check the speed sensor installation. OK:
The installation bolt is tightened properly and there is
no clearance between the sensor and front steering
knuckle.
Torque: 8.0 N m (82 kgf cm, 71 in. lbf)
NGREPLACE SPEED SENSOR FRONT RH
NGREPLACE SPEED SENSOR FRONT LH
NOTICE:
Check the speed sensor signal last (See page 05±699).
OK
6INSPECT SPEED SENSOR TIP
(a)Remove the front speed sensor (See page 32±59).
(b)Check the sensor tip. OK:
No scratches or foreign objects on the sensor tip.
NGCLEAN OR REPAIR SPEED SENSOR
NOTICE:
Check the speed sensor signal last (See page 05±699).
OK
7INSPECT SPEED SENSOR ROTOR
(a)Remove the front speed sensor rotor (See page 30±6).
(b)Check the sensor rotor serrations. OK:
No scratches, missing teeth or foreign objects.
HINT:
If a foreign object is attached, remove it and after reassembling,
check the output waveform.
NGCLEAN OR REPAIR SPEED SENSOR ROTOR
NOTICE:
Check the speed sensor signal last (See page 05±699).
OK
REPLACE BRAKE ACTUATOR ASSY(See page 32±54)
Page 799 of 5135
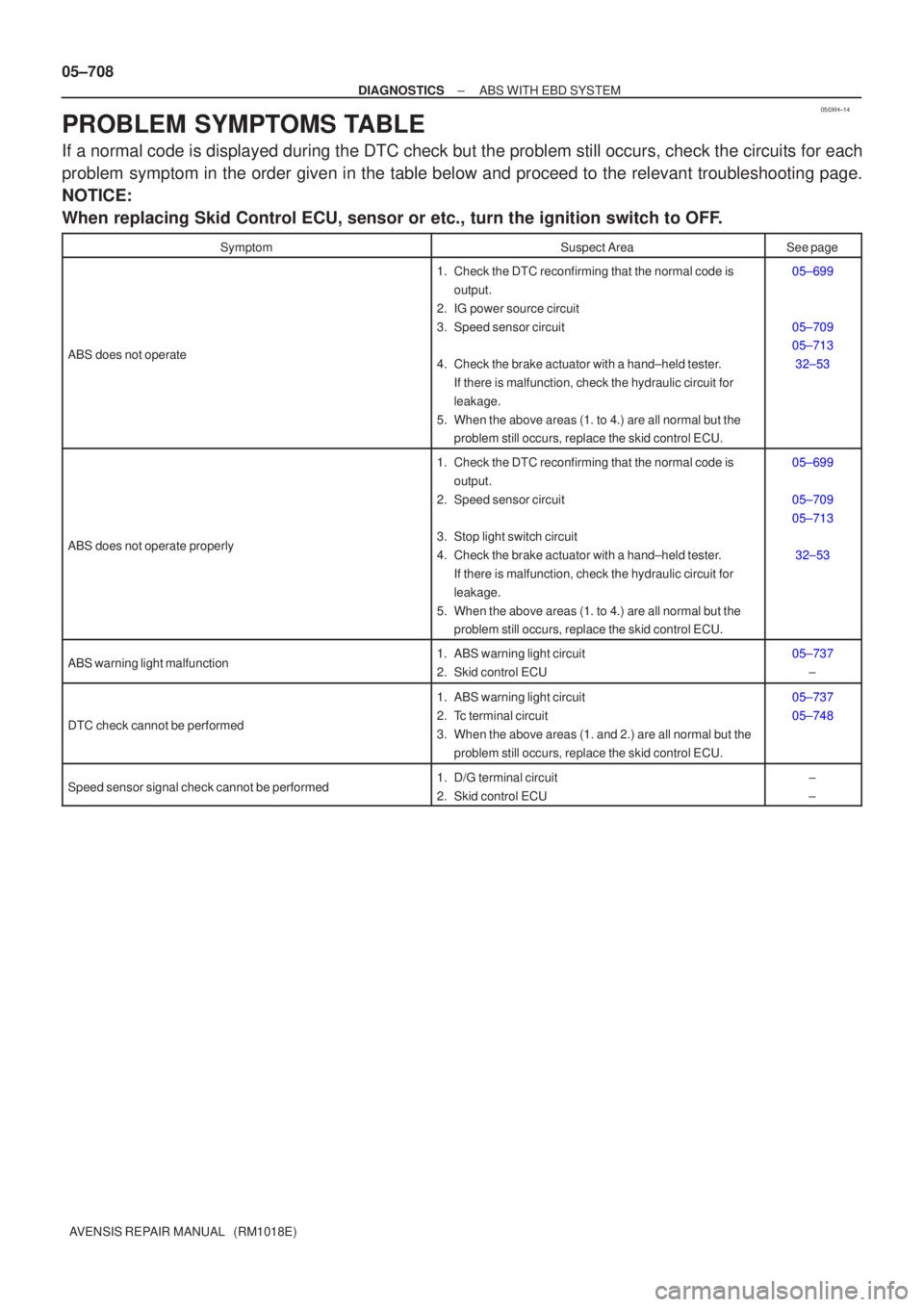
050XH±14
05±708
±
DIAGNOSTICS ABS WITH EBD SYSTEM
AVENSIS REPAIR MANUAL (RM1018E)
PROBLEM SYMPTOMS TABLE
If a normal code is displayed during the DTC check but the problem still o\
ccurs, check the circuits for each
problem symptom in the order given in the table below and proceed to the releva\
nt troubleshooting page.
NOTICE:
When replacing Skid Control ECU, sensor or etc., turn the ignition switc\
h to OFF.
SymptomSuspect AreaSee page
ABS does not operate
1. Check the DTC reconfirming that the normal code is output.
2. IG power source circuit
3. Speed sensor circuit
4. Check the brake actuator with a hand±held tester. If there is malfunction, check the hydraulic circuit for
leakage.
5. When the above areas (1. to 4.) are all normal but the problem still occurs, replace the skid control ECU.05±699
05±709
05±713
32±53
ABS does not operate properly
1. Check the DTC reconfirming that the normal code is output.
2. Speed sensor circuit
3. Stop light switch circuit
4. Check the brake actuator with a hand±held tester. If there is malfunction, check the hydraulic circuit for
leakage.
5. When the above areas (1. to 4.) are all normal but the problem still occurs, replace the skid control ECU.05±699
05±709
05±713
32±53
ABS warning light malfunction1. ABS warning light circuit
2. Skid control ECU05±737 ±
DTC check cannot be performed
1. ABS warning light circuit
2. Tc terminal circuit
3. When the above areas (1. and 2.) are all normal but the problem still occurs, replace the skid control ECU.05±737
05±748
Speed sensor signal check cannot be performed1. D/G terminal circuit
2. Skid control ECU±
±
Page 800 of 5135
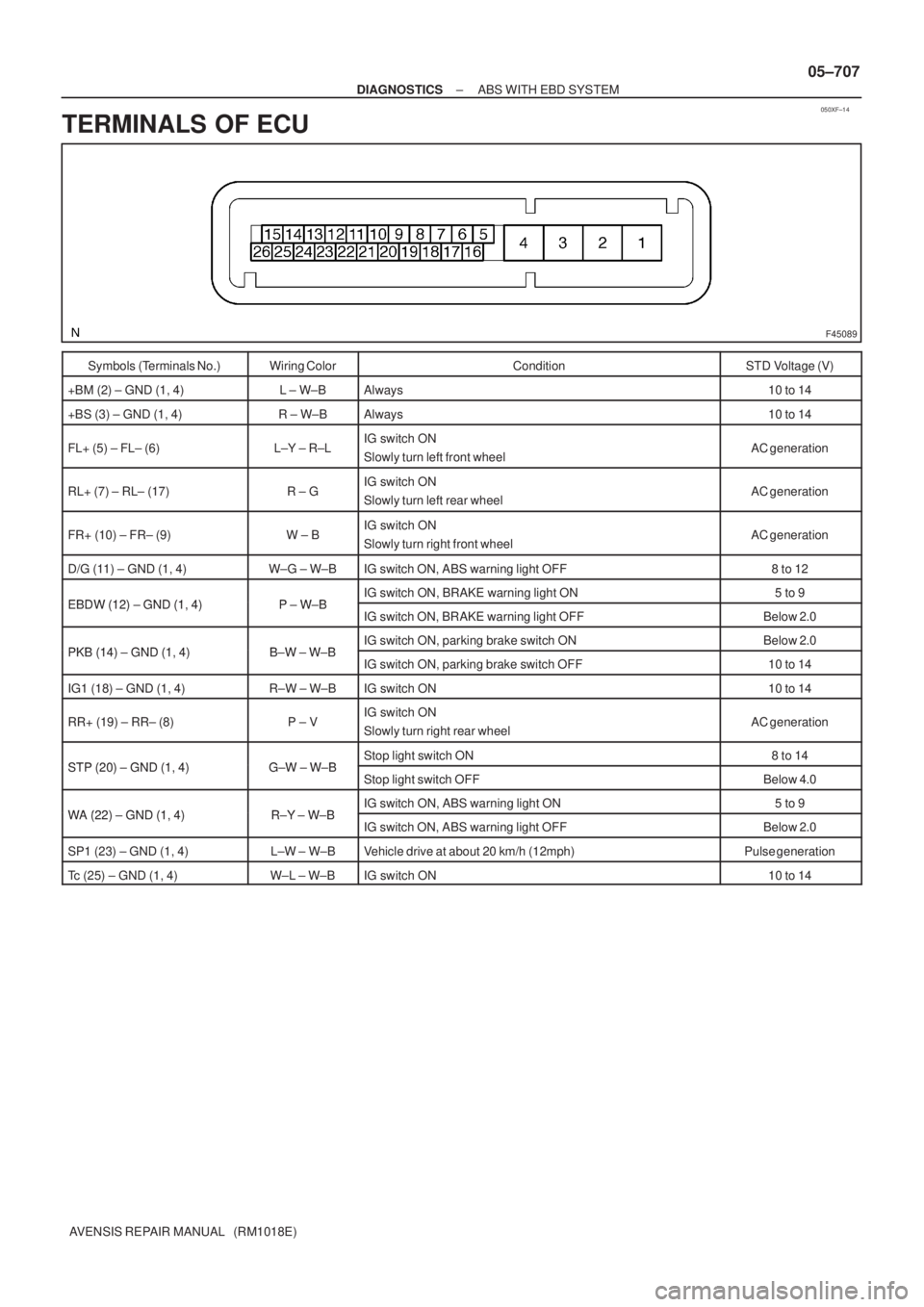
050XF±14
F45089
± DIAGNOSTICSABS WITH EBD SYSTEM
05±707
AVENSIS REPAIR MANUAL (RM1018E)
TERMINALS OF ECU
Symbols (Terminals No.)Wiring ColorConditionSTD Voltage (V)
+BM (2) ± GND (1, 4)L ± W±BAlways10 to 14
+BS (3) ± GND (1, 4)R ± W±BAlways10 to 14
FL+ (5) ± FL± (6)L±Y ± R±LIG switch ON
Slowly turn left front wheelAC generation
RL+ (7) ± RL± (17)R ± GIG switch ON
Slowly turn left rear wheelAC generation
FR+ (10) ± FR± (9)W ± BIG switch ON
Slowly turn right front wheelAC generation
D/G (11) ± GND (1, 4)W±G ± W±BIG switch ON, ABS warning light OFF8 to 12
EBDW (12) GND (1 4)PWBIG switch ON, BRAKE warning light ON5 to 9EBDW (12) ± GND (1, 4)P ± W±BIG switch ON, BRAKE warning light OFFBelow 2.0
PKB (14) GND (1 4)BW WBIG switch ON, parking brake switch ONBelow 2.0PKB (14) ± GND (1, 4)B±W ± W±BIG switch ON, parking brake switch OFF10 to 14
IG1 (18) ± GND (1, 4)R±W ± W±BIG switch ON10 to 14
RR+ (19) ± RR± (8)P ± VIG switch ON
Slowly turn right rear wheelAC generation
STP (20) GND (1 4)GW WBStop light switch ON8 to 14STP (20) ± GND (1, 4)G±W ± W±BStop light switch OFFBelow 4.0
WA (22) GND (1 4)RY WBIG switch ON, ABS warning light ON5 to 9WA (22) ± GND (1, 4)R±Y ± W±BIG switch ON, ABS warning light OFFBelow 2.0
SP1 (23) ± GND (1, 4)L±W ± W±BVehicle drive at about 20 km/h (12mph)Pulse generation
Tc (25) ± GND (1, 4)W±L ± W±BIG switch ON10 to 14