Page 33 of 5135
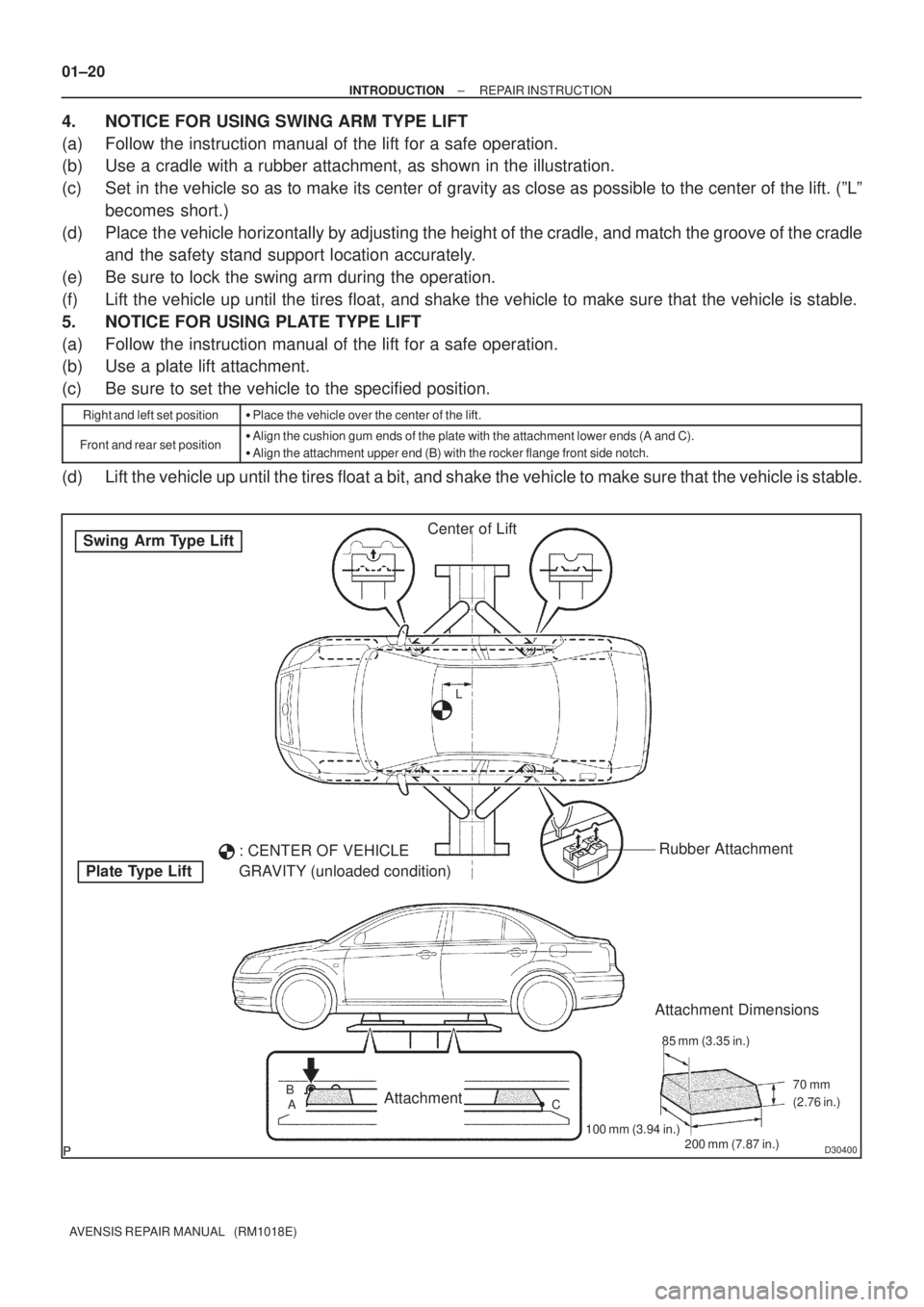
D30400
Swing Arm Type Lift
Plate Type LiftCenter of Lift
: CENTER OF VEHICLE
GRAVITY (unloaded condition)Rubber Attachment
AttachmentBAL
Attachment Dimensions
85 mm (3.35 in.)
200 mm (7.87 in.) 100 mm (3.94 in.)70 mm
(2.76 in.)
C
01±20
± INTRODUCTIONREPAIR INSTRUCTION
AVENSIS REPAIR MANUAL (RM1018E)
4. NOTICE FOR USING SWING ARM TYPE LIFT
(a) Follow the instruction manual of the lift for a safe operation.
(b) Use a cradle with a rubber attachment, as shown in the illustration.
(c) Set in the vehicle so as to make its center of gravity as close as possible to the center of the lift. (ºLº
becomes short.)
(d) Place the vehicle horizontally by adjusting the height of the cradle, and match the groove of the cradle
and the safety stand support location accurately.
(e) Be sure to lock the swing arm during the operation.
(f) Lift the vehicle up until the tires float, and shake the vehicle to make sure that the vehicle is stable.
5. NOTICE FOR USING PLATE TYPE LIFT
(a) Follow the instruction manual of the lift for a safe operation.
(b) Use a plate lift attachment.
(c) Be sure to set the vehicle to the specified position.
Right and left set positionPlace the vehicle over the center of the lift.
Front and rear set positionAlign the cushion gum ends of the plate with the attachment lower ends (A and C).
Align the attachment upper end (B) with the rocker flange front side notch.
(d) Lift the vehicle up until the tires float a bit, and shake the vehicle to make sure that the vehicle is stable.
Page 34 of 5135
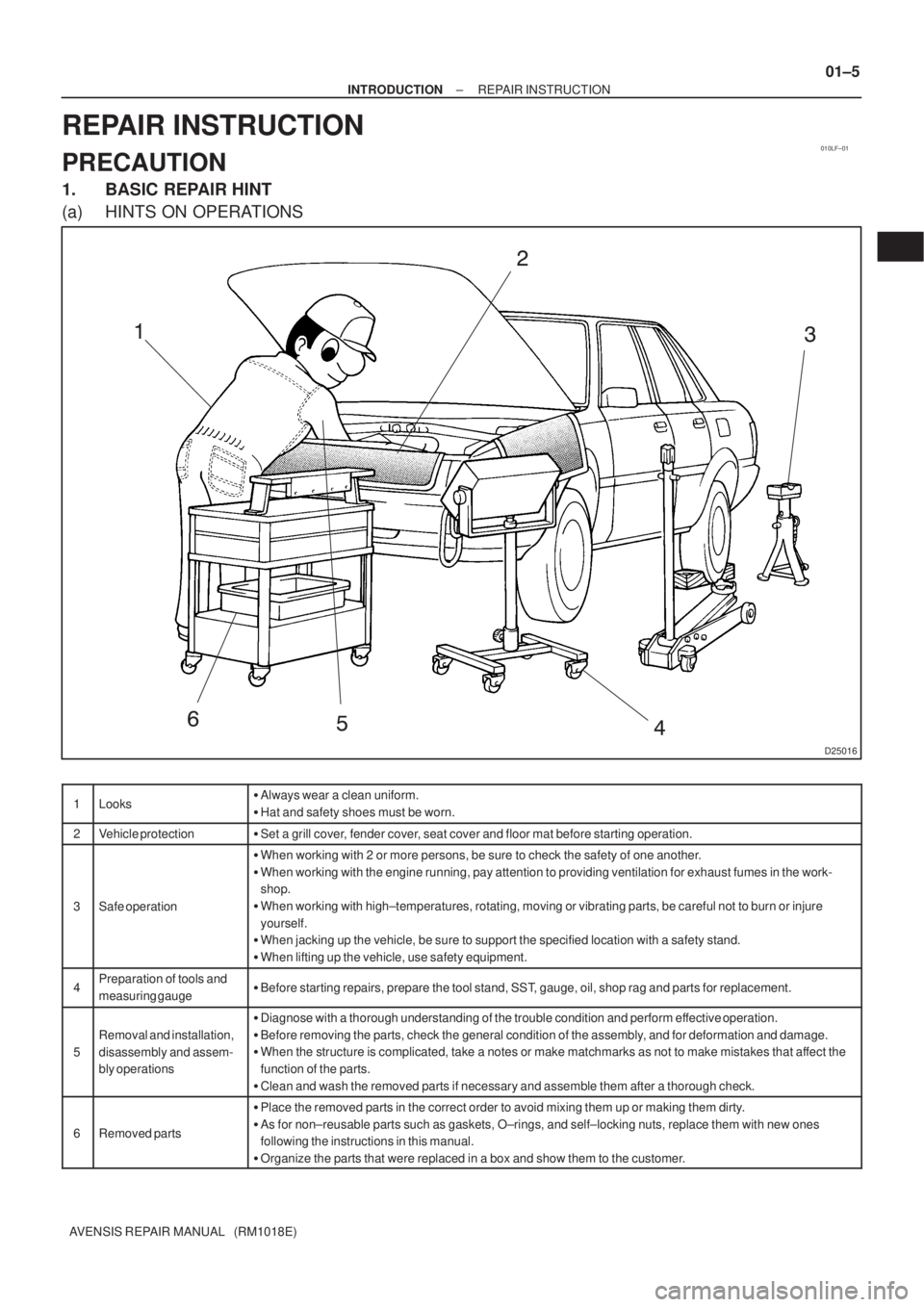
010LF±01
D25016
± INTRODUCTIONREPAIR INSTRUCTION
01±5
AVENSIS REPAIR MANUAL (RM1018E)
REPAIR INSTRUCTION
PRECAUTION
1. BASIC REPAIR HINT
(a) HINTS ON OPERATIONS
1LooksAlways wear a clean uniform.
Hat and safety shoes must be worn.
2Vehicle protectionSet a grill cover, fender cover, seat cover and floor mat before starting operation.
3Safe operation
When working with 2 or more persons, be sure to check the safety of one another.
When working with the engine running, pay attention to providing ventilation for exhaust fumes in the work-
shop.
When working with high±temperatures, rotating, moving or vibrating parts, be careful not to burn or injure
yourself.
When jacking up the vehicle, be sure to support the specified location with a safety stand.
When lifting up the vehicle, use safety equipment.
4Preparation of tools and
measuring gaugeBefore starting repairs, prepare the tool stand, SST, gauge, oil, shop rag and parts for replacement.
5
Removal and installation,
disassembly and assem-
bly operations
Diagnose with a thorough understanding of the trouble condition and perform effective operation.
Before removing the parts, check the general condition of the assembly, and for deformation and damage.
When the structure is complicated, take a notes or make matchmarks as not to make mistakes that affect the
function of the parts.
Clean and wash the removed parts if necessary and assemble them after a thorough check.
6Removed parts
Place the removed parts in the correct order to avoid mixing them up or making them dirty.
As for non±reusable parts such as gaskets, O±rings, and self±locking nuts, replace them with new ones
following the instructions in this manual.
Organize the parts that were replaced in a box and show them to the customer.
Page 35 of 5135
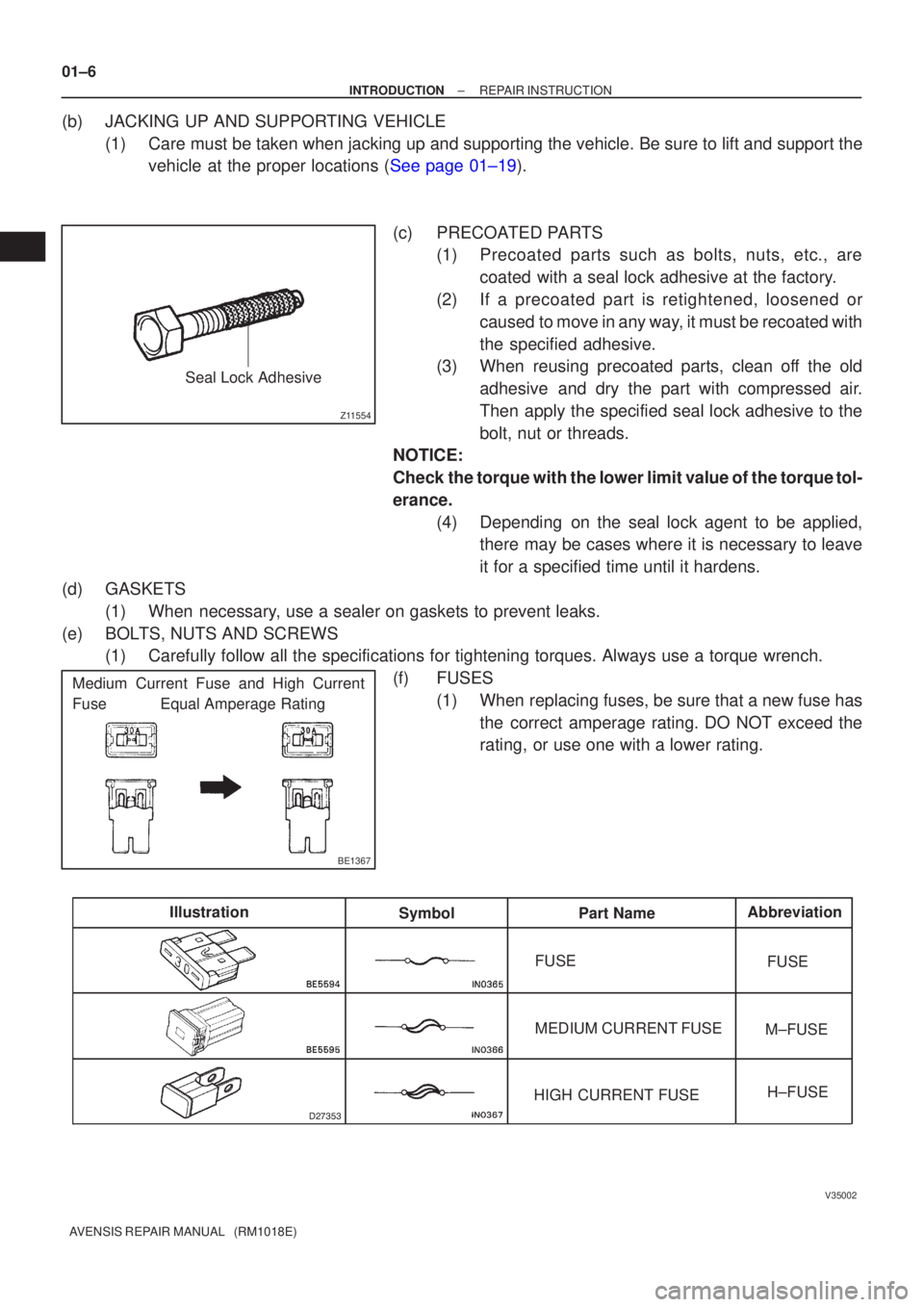
Z11554
Seal Lock Adhesive
BE1367
Medium Current Fuse and High Current
Fuse Equal Amperage Rating
V35002
IllustrationSymbol Part Name Abbreviation
FUSE
MEDIUM CURRENT FUSE
HIGH CURRENT FUSE FUSE
M±FUSE H±FUSE
01±6
±
INTRODUCTION REPAIR INSTRUCTION
AVENSIS REPAIR MANUAL (RM1018E)
(b) JACKING UP AND SUPPORTING VEHICLE (1) Care must be taken when jacking up and supporting the vehicle. Be sure to li\
ft and support thevehicle at the proper locations (See page 01±19).
(c) PRECOATED PARTS(1) Precoated parts such as bolts, nuts, etc., are
coated with a seal lock adhesive at the factory.
(2) If a precoated part is retightened, loosened or caused to move in any way, it must be recoated with
the specified adhesive.
(3) When reusing precoated parts, clean off the old
adhesive and dry the part with compressed air.
Then apply the specified seal lock adhesive to the
bolt, nut or threads.
NOTICE:
Check the torque with the lower limit value of the torque tol-
erance.
(4) Depending on the seal lock agent to be applied,there may be cases where it is necessary to leave
it for a specified time until it hardens.
(d) GASKETS (1) When necessary, use a sealer on gaskets to prevent leaks.
(e) BOLTS, NUTS AND SCREWS (1) Carefully follow all the specifications for tightening torques. Always u\
se a torque wrench.
(f) FUSES(1) When replacing fuses, be sure that a new fuse hasthe correct amperage rating. DO NOT exceed the
rating, or use one with a lower rating.
Page 36 of 5135
D25786
Shape (Example)Removal/Installation
Clip Remover
Pliers
Screwdriver
Scraper
Protective Tape
Clip
Protective Tape
± INTRODUCTIONREPAIR INSTRUCTION
01±7
AVENSIS REPAIR MANUAL (RM1018E)
(g) CLIPS
(1) The removal and installation methods of typical clips used in body parts are shown in the table
below.
HINT:
If the clip is damaged during the operation, always replace it with a new clip.
Page 37 of 5135
V00012
Shape (Example)
Removal/Installation
Removal
Installation Removal Installation
D25063
CORRECT
WRONG
D25064
01±8
± INTRODUCTIONREPAIR INSTRUCTION
AVENSIS REPAIR MANUAL (RM1018E)
(h) REMOVAL AND INSTALLATION OF VACUUM HOSES
(1) To disconnect vacuum hoses, pull them by holding
the end, not the middle of the hose.
(2) When disconnecting vacuum hoses, use tags to
identify where they should be reconnected.
(3) After completing the job, make a double check
whether the vacuum hoses are properly connected.
A label under the hood shows the proper layout.
(4) When using a vacuum gauge, never force the hose
onto a connector that is too large. Use a step±down
adapter for adjustment. Once the hose has been
stretched, it may leak air.
Page 38 of 5135
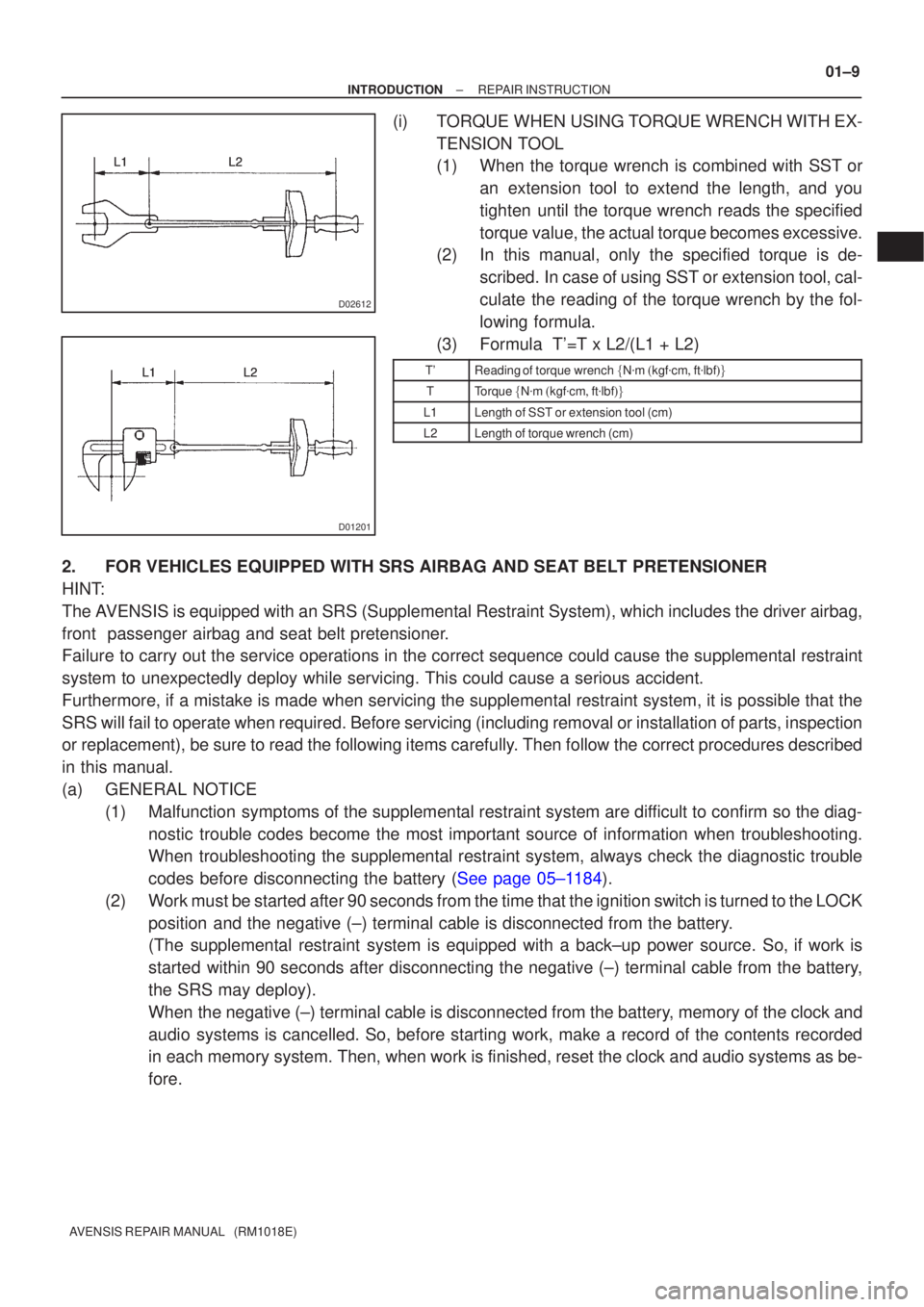
L1L2L1L2L1L2
D02612
L2
L1L2
L1L2
L1
D01201
±
INTRODUCTION REPAIR INSTRUCTION
01±9
AVENSIS REPAIR MANUAL (RM1018E)
(i)TORQUE WHEN USING TORQUE WRENCH WITH EX-
TENSION TOOL
(1)When the torque wrench is combined with SST oran extension tool to extend the length, and you
tighten until the torque wrench reads the specified
torque value, the actual torque becomes excessive.
(2)In this manual, only the specified torque is de-
scribed. In case of using SST or extension tool, cal-
culate the reading of the torque wrench by the fol-
lowing formula.
(3)Formula T'=T x L2/(L1 + L2)
T'Reading of torque wrench N m kgf cm ft lbf
TTorque N m kgf cm ft lbf
L1Length of SST or extension tool (cm)
L2Length of torque wrench (cm)
2.FOR VEHICLES EQUIPPED WITH SRS AIRBAG AND SEAT BELT PRETENSIONER
HINT:
The AVENSIS is equipped with an SRS (Supplemental Restraint System), which \
includes the driver airbag,
front passenger airbag and seat belt pretensioner.
Failure to carry out the service operations in the correct sequence could cause\
the supplemental restraint
system to unexpectedly deploy while servicing. This could cause a seriou\
s accident.
Furthermore, if a mistake is made when servicing the supplemental restra\
int system, it is possible that the
SRS will fail to operate when required. Before servicing (including remova\
l or installation of parts, inspection
or replacement), be sure to read the following items carefully. Then follow the correct procedures described
in this manual.
(a)GENERAL NOTICE
(1)Malfunction symptoms of the supplemental restraint system are difficult to confirm so the diag-nostic trouble codes become the most important source of information when trou\
bleshooting.
When troubleshooting the supplemental restraint system, always check the dia\
gnostic trouble
codes before disconnecting the battery (See page 05±1184).
(2) Work must be started after 90 seconds from the time that the ignition switch\
is turned to the LOCK position and the negative (±) terminal cable is disconnected from the batte\
ry.
(The supplemental restraint system is equipped with a back±up power sourc\
e. So, if work is
started within 90 seconds after disconnecting the negative (±) terminal ca\
ble from the battery,
the SRS may deploy).
When the negative (±) terminal cable is disconnected from the battery, memory of the clock and
audio systems is cancelled. So, before starting work, make a record of the contents recorded
in each memory system. Then, when work is finished, reset the clock and audio systems as be-
fore.
Page 39 of 5135
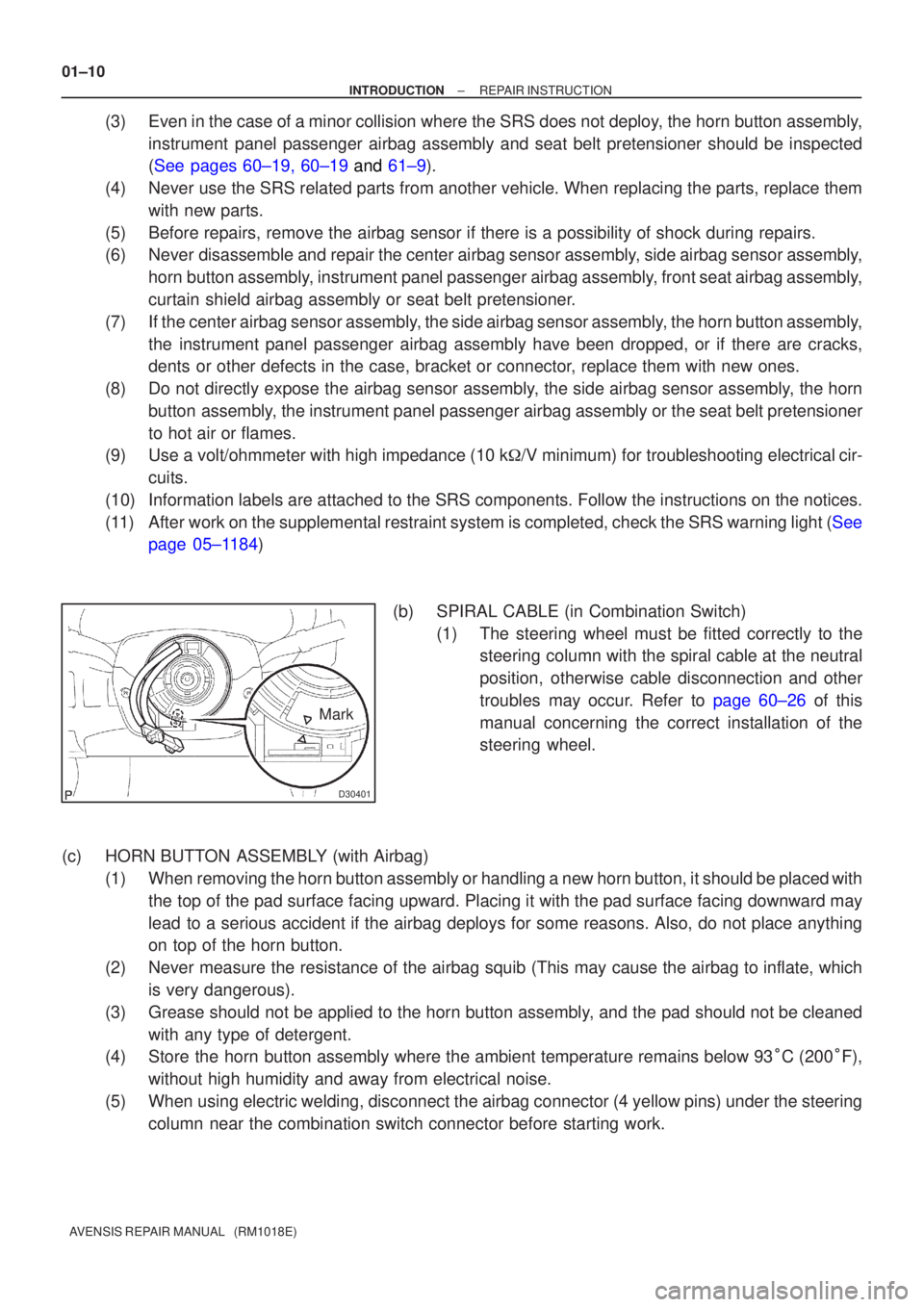
D30401
Mark
01±10
±
INTRODUCTION REPAIR INSTRUCTION
AVENSIS REPAIR MANUAL (RM1018E)
(3)Even in the case of a minor collision where the SRS does not deploy, the horn button assembly, instrument panel passenger airbag assembly and seat belt pretensioner should be in\
spected
(See pages 60±19, 60±19 and 61±9).
(4)Never use the SRS related parts from another vehicle. When replacing the part\
s, replace them with new parts.
(5)Before repairs, remove the airbag sensor if there is a possibility of sh\
ock during repairs.
(6)Never disassemble and repair the center airbag sensor assembly, side airbag sensor assembly, horn button assembly, instrument panel passenger airbag assembly, front seat airbag assembly,
curtain shield airbag assembly or seat belt pretensioner.
(7)If the center airbag sensor assembly, the side airbag sensor assembly, the horn button assembly, the instrument panel passenger airbag assembly have been dropped, or if the\
re are cracks,
dents or other defects in the case, bracket or connector, replace them with new ones.
(8)Do not directly expose the airbag sensor assembly, the side airbag sensor assembly, the horn button assembly, the instrument panel passenger airbag assembly or the seat belt pretensioner
to hot air or flames.
(9)Use a volt/ohmmeter with high impedance (10 k /V minimum) for troubleshooting electrical cir-
cuits.
(10)Information labels are attached to the SRS components. Follow the instru\
ctions on the notices.
(11)After work on the supplemental restraint system is completed, check the SRS w\
arning light (See page 05±1184)
(b)SPIRAL CABLE (in Combination Switch)(1)The steering wheel must be fitted correctly to thesteering column with the spiral cable at the neutral
position, otherwise cable disconnection and other
troubles may occur. Refer to page 60±26 of this
manual concerning the correct installation of the
steering wheel.
(c) HORN BUTTON ASSEMBLY (with Airbag) (1) When removing the horn button assembly or handling a new horn button, it sho\
uld be placed withthe top of the pad surface facing upward. Placing it with the pad surface facing downward may
lead to a serious accident if the airbag deploys for some reasons. Also, do \
not place anything
on top of the horn button.
(2) Never measure the resistance of the airbag squib (This may cause the airbag to inflate, which is very dangerous).
(3) Grease should not be applied to the horn button assembly, and the pad should not be cleaned with any type of detergent.
(4) Store the horn button assembly where the ambient temperature remains below 93 C (200 F),
without high humidity and away from electrical noise.
(5) When using electric welding, disconnect the airbag connector (4 yellow pins\
) under the steering column near the combination switch connector before starting work.
Page 40 of 5135
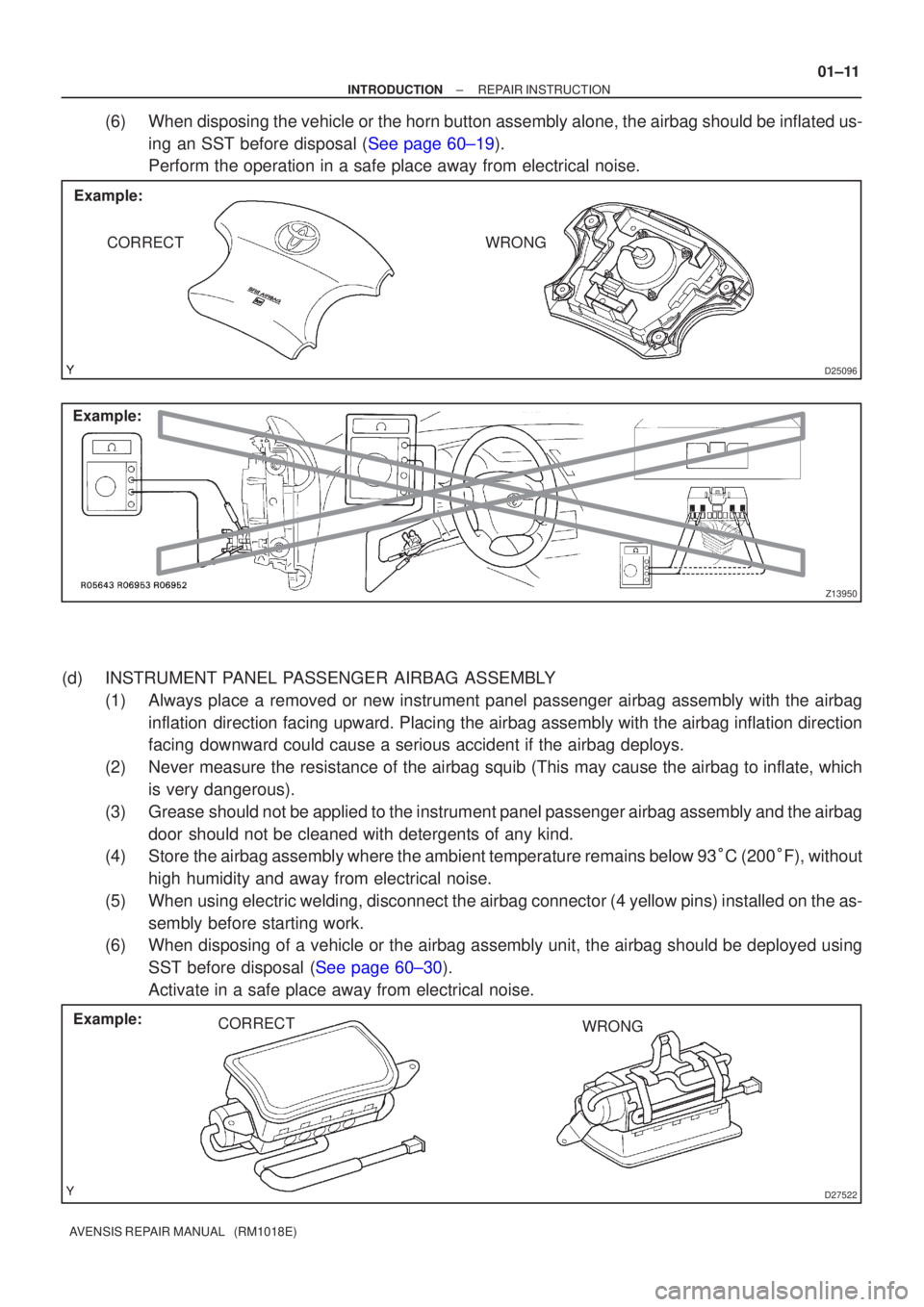
D25096
Example:CORRECTWRONG
Z13950
Example:
D27522
Example: CORRECT WRONG
±
INTRODUCTION REPAIR INSTRUCTION
01±11
AVENSIS REPAIR MANUAL (RM1018E)
(6)When disposing the vehicle or the horn button assembly alone, the airbag\
should be inflated us-
ing an SST before disposal (See page 60±19).
Perform the operation in a safe place away from electrical noise.
(d)INSTRUMENT PANEL PASSENGER AIRBAG ASSEMBLY (1)Always place a removed or new instrument panel passenger airbag assembly\
with the airbaginflation direction facing upward. Placing the airbag assembly with the airbag inflation direction
facing downward could cause a serious accident if the airbag deploys.
(2)Never measure the resistance of the airbag squib (This may cause the airbag to inflate, which is very dangerous).
(3)Grease should not be applied to the instrument panel passenger airbag assembly\
and the airbag door should not be cleaned with detergents of any kind.
(4)Store the airbag assembly where the ambient temperature remains below 93 C (200 F), without
high humidity and away from electrical noise.
(5)When using electric welding, disconnect the airbag connector (4 yellow pins\
) installed on the as- sembly before starting work.
(6)When disposing of a vehicle or the airbag assembly unit, the airbag should be deployed using\
SST before disposal (See page 60±30).
Activate in a safe place away from electrical noise.