Page 2817 of 5135
F44779
Horn Button Assy
Steering Wheel Assy
Headlamp Dimmer Switcn Assy
Spiral Cable
Windshield Wiper Switch Steering Column Cover
Steering Column Assy
Steering
Intermediate
Shaft Assy
No.2
Steering Sliding
Yoke sub−assy
Column Hole Cover Silencer Sheet
N m (kgf cm, ftlbf): Specified torque Steering Sliding
Yoke sub
−assy
Steering Intermediate
Shaft Assy No.2
LHD Steering Position Type:
Electric Power Steering:
35 (360, 26)
35 (360, 26)
35 (360, 26)
Column Hole Cover Silencer Sheet
Steering Column Cover
LW R
Floor Shift Parking Lock
Cable Assy (A/T Transaxle)
Instrument Panel Airbag Assy
18 (184, 13)
Steering
Column
Protector
No.1
Instrument
Panel
Hole Cover
18 (184, 13)
18 (184, 13)
5 (51, 44 in.
lbf)
25 (255, 18)
18 (184, 13)
18 (184, 13)
LHD Steering Position Type: w/ Instrument Cluster
Finish Panel Assy
50 (510, 37)
25 (255, 18)
Steering Column
Protector No.1
35 (360, 26)
M/T Transaxle:25 (255, 18)
−
STEERING COLUMN STEERING COLUMN ASSY
50−7
Page 2818 of 5135
F44780
Transponder Key Amplifier AssyTapered±head Bolt
Ignition or Starter Switch Assy Steering Column Assy
Non±reusable part Steering Column Clamp Upper
Un±lock Warning
Switch Assy
Steering Column Upper w/ Switch Bracket Assy Ignition Switch Lock Cylinder Assy
50±8
± STEERING COLUMNSTEERING COLUMN ASSY
AVENSIS REPAIR MANUAL (RM1018E)
Page 2819 of 5135
5000E±04
F44778
Maximum
Freeplay
30 mm (1.18 in.) 50±4
± STEERING COLUMNSTEERING SYSTEM
AVENSIS REPAIR MANUAL (RM1018E)
ON±VEHICLE INSPECTION
1. CHECK STEERING WHEEL FREEPLAY
(a) Stop the vehicle and face the tires straight ahead.
(b) Rock the steering wheel gently up and down with a finger
lightly, check the steering wheel freeplay.
Maximum freeplay: 30 mm (1.18 in.)
Page 2820 of 5135
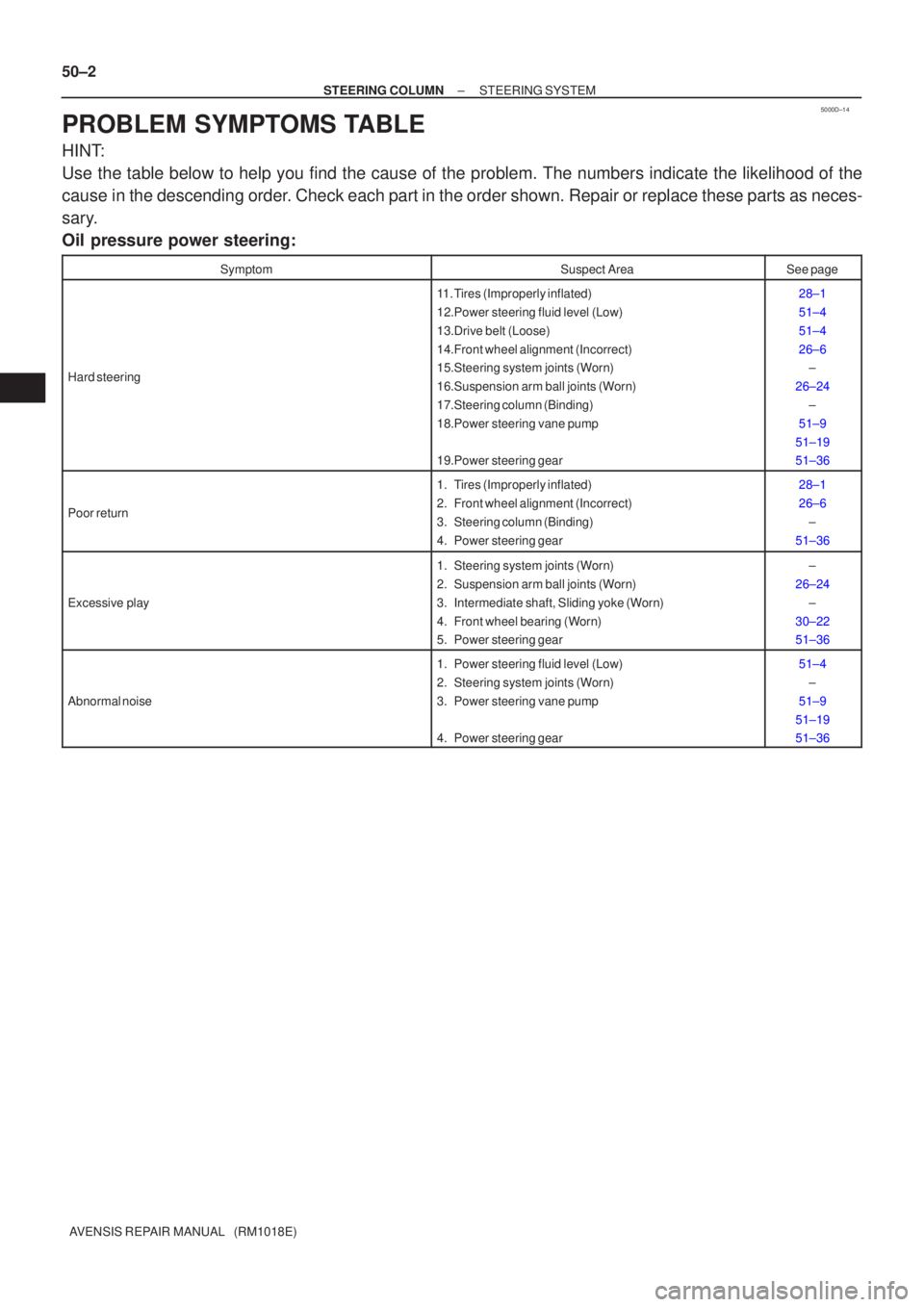
5000D±14
50±2
±
STEERING COLUMN STEERING SYSTEM
AVENSIS REPAIR MANUAL (RM1018E)
PROBLEM SYMPTOMS TABLE
HINT:
Use the table below to help you find the cause of the problem. The numbers \
indicate the likelihood of the
cause in the descending order. Check each part in the order shown. Repair or replace these parts as n\
eces-
sary.
Oil pressure power steering:
SymptomSuspect AreaSee page
Hard steering
11. Tires (Improperly inflated)
12.Power steering fluid level (Low)
13.Drive belt (Loose)
14.Front wheel alignment (Incorrect)
15.Steering system joints (Worn)
16.Suspension arm ball joints (Worn)
17.Steering column (Binding)
18.Power steering vane pump
19.Power steering gear28±1
51±4
51±4
26±6 ±
26±24 ±
51±9
51±19
51±36
Poor return
1. Tires (Improperly inflated)
2. Front wheel alignment (Incorrect)
3. Steering column (Binding)
4. Power steering gear28±1
26±6 ±
51±36
Excessive play
1. Steering system joints (Worn)
2. Suspension arm ball joints (Worn)
3. Intermediate shaft, Sliding yoke (Worn)
4. Front wheel bearing (Worn)
5. Power steering gear±
26±24 ±
30±22
51±36
Abnormal noise
1. Power steering fluid level (Low)
2. Steering system joints (Worn)
3. Power steering vane pump
4. Power steering gear51±4 ±
51±9
51±19
51±36
Page 2821 of 5135
±
STEERING COLUMN STEERING SYSTEM
50±3
AVENSIS REPAIR MANUAL (RM1018E)
Electric power steering:
SymptomSuspect AreaSee page
Hard steering
1. Tires (Improperly inflated)
2. Front wheel alignment (Incorrect)
3. Steering system joints (Worn)
4. Suspension arm ball joints (Worn)
5. Steering column (Binding)
6. Steering column (Electric power steering)28±1
26±6
±
26±24 ±
50±9
Poor return
1. Tires (Improperly inflated)
2. Front wheel alignment (Incorrect)
3. Steering column (Binding)
4. Steering column (Electric power steering)28±1
26±6 ±
50±9
Excessive play
1. Steering system joints (Worn)
2. Suspension arm ball joints (Worn)
3. Intermediate shaft, Sliding yoke (Worn)
4. Front wheel bearing (Worn)
5. Steering column (Electric power steering)±
26±24 ±
30±22 50±9
Abnormal noise1. Steering system joints (Worn)
2. Steering column (Electric power steering)±
50±9
HINT:
When the problem occurs on the Electric Power Steering system, refer to \
the DI section (See page 05±1042
).
Page 2822 of 5135
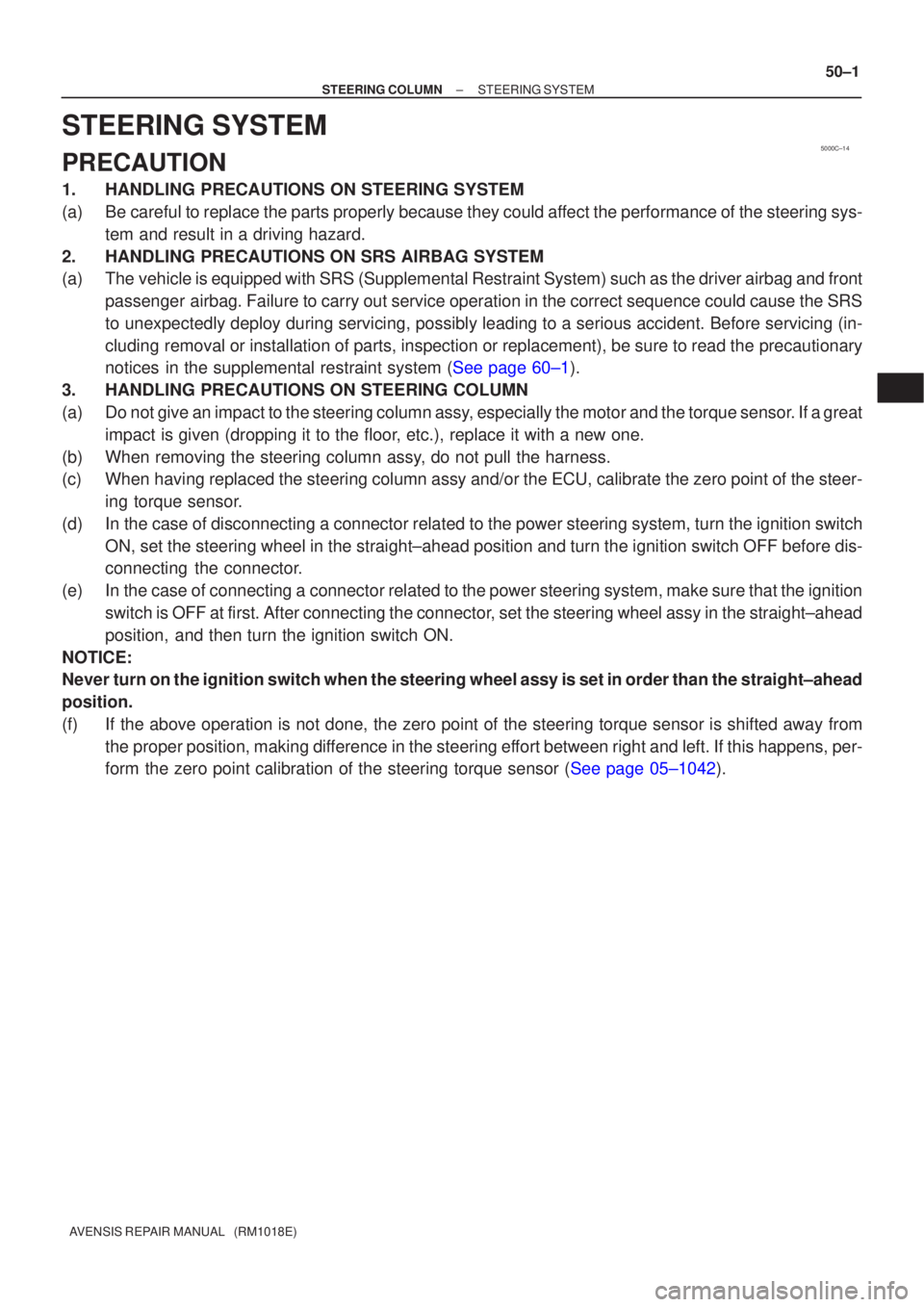
5000C±14
±
STEERING COLUMN STEERING SYSTEM
50±1
AVENSIS REPAIR MANUAL (RM1018E)
STEERING SYSTEM
PRECAUTION
1. HANDLING PRECAUTIONS ON STEERING SYSTEM
(a) Be careful to replace the parts properly because they could affect the performance of the steering sys-
tem and result in a driving hazard.
2. HANDLING PRECAUTIONS ON SRS AIRBAG SYSTEM
(a) The vehicle is equipped with SRS (Supplemental Restraint System) such as \
the driver airbag and front passenger airbag. Failure to carry out service operation in the correct sequence \
could cause the SRS
to unexpectedly deploy during servicing, possibly leading to a serious acc\
ident. Before servicing (in-
cluding removal or installation of parts, inspection or replacement), be sure \
to read the precautionary
notices in the supplemental restraint system (See page 60±1).
3. HANDLING PRECAUTIONS ON STEERING COLUMN
(a) Do not give an impact to the steering column assy, especially the motor and the torque sensor. If a great impact is given (dropping it to the floor, etc.), replace it with a new one.
(b) When removing the steering column assy, do not pull the harness.
(c) When having replaced the steering column assy and/or the ECU, calibrate the \
zero point of the steer- ing torque sensor.
(d) In the case of disconnecting a connector related to the power steering sys\
tem, turn the ignition switch ON, set the steering wheel in the straight±ahead position and turn th\
e ignition switch OFF before dis-
connecting the connector.
(e) In the case of connecting a connector related to the power steering system, make sure that the ignit\
ion switch is OFF at first. After connecting the connector, set the steering wheel assy in the straight±ahead
position, and then turn the ignition switch ON.
NOTICE:
Never turn on the ignition switch when the steering wheel assy is set in orde\
r than the straight±ahead
position.
(f) If the above operation is not done, the zero point of the steering torque \
sensor is shifted away from the proper position, making difference in the steering effort between right and left. If this happens, per-
form the zero point calibration of the steering torque sensor (See page 05±1042).
Page 2823 of 5135
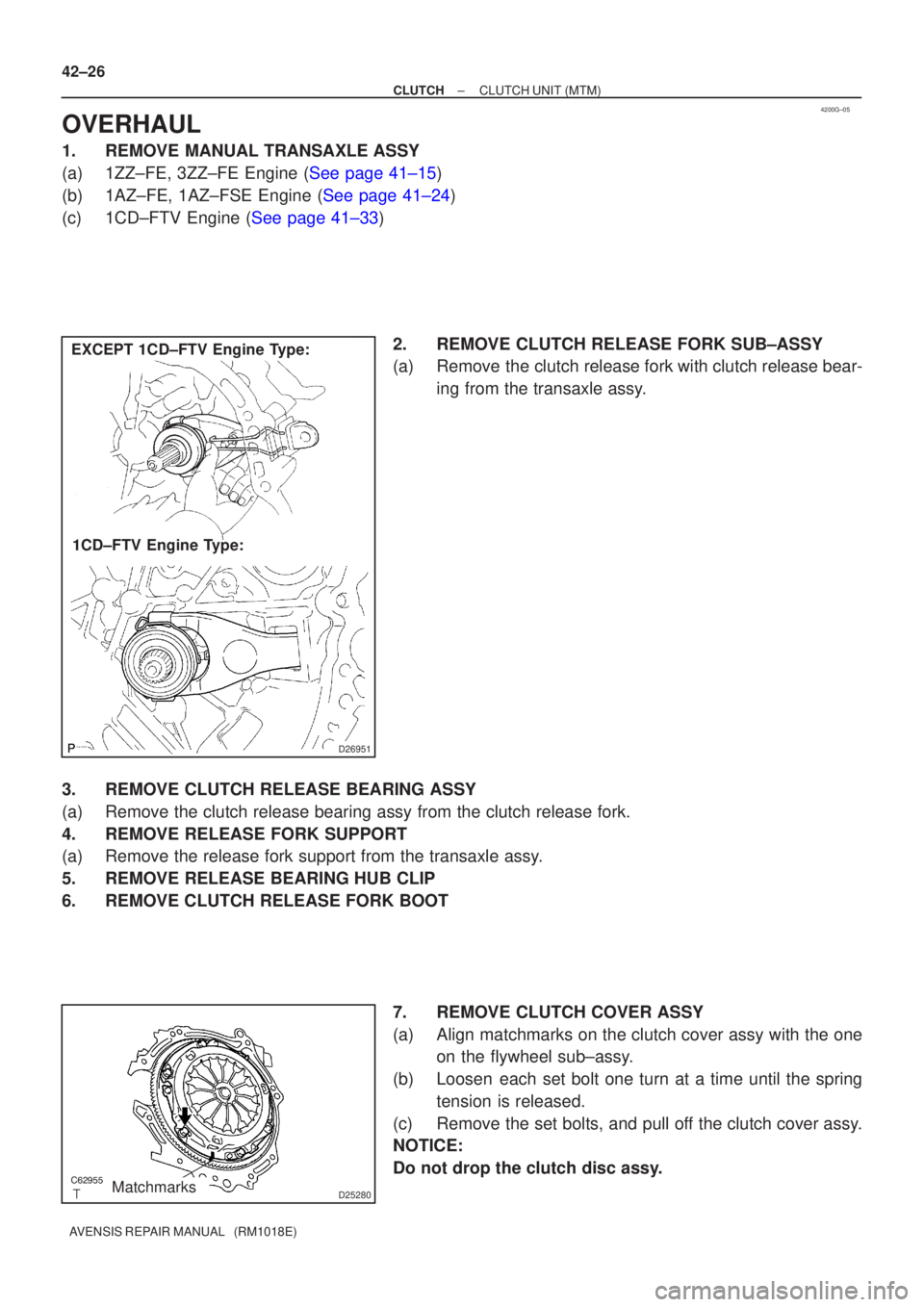
4200G±05
D26951
EXCEPT 1CD±FTV Engine Type:1CD±FTV Engine Type:
D25280Matchmarks
42±26
±
CLUTCH CLUTCH UNIT (MTM)
AVENSIS REPAIR MANUAL (RM1018E)
OVERHAUL
1. REMOVE MANUAL TRANSAXLE ASSY
(a)1ZZ±FE, 3ZZ±FE Engine (See page 41±15)
(b)1AZ±FE, 1AZ±FSE Engine (See page 41±24)
(c)1CD±FTV Engine (See page 41±33) 2. REMOVE CLUTCH RELEASE FORK SUB±ASSY
(a) Remove the clutch release fork with clutch release bear-ing from the transaxle assy.
3. REMOVE CLUTCH RELEASE BEARING ASSY
(a) Remove the clutch release bearing assy from the clutch release fork.
4. REMOVE RELEASE FORK SUPPORT
(a) Remove the release fork support from the transaxle assy.
5. REMOVE RELEASE BEARING HUB CLIP
6. REMOVE CLUTCH RELEASE FORK BOOT 7. REMOVE CLUTCH COVER ASSY
(a) Align matchmarks on the clutch cover assy with the oneon the flywheel sub±assy.
(b) Loosen each set bolt one turn at a time until the spring tension is released.
(c) Remove the set bolts, and pull off the clutch cover assy.
NOTICE:
Do not drop the clutch disc assy.
Page 2824 of 5135
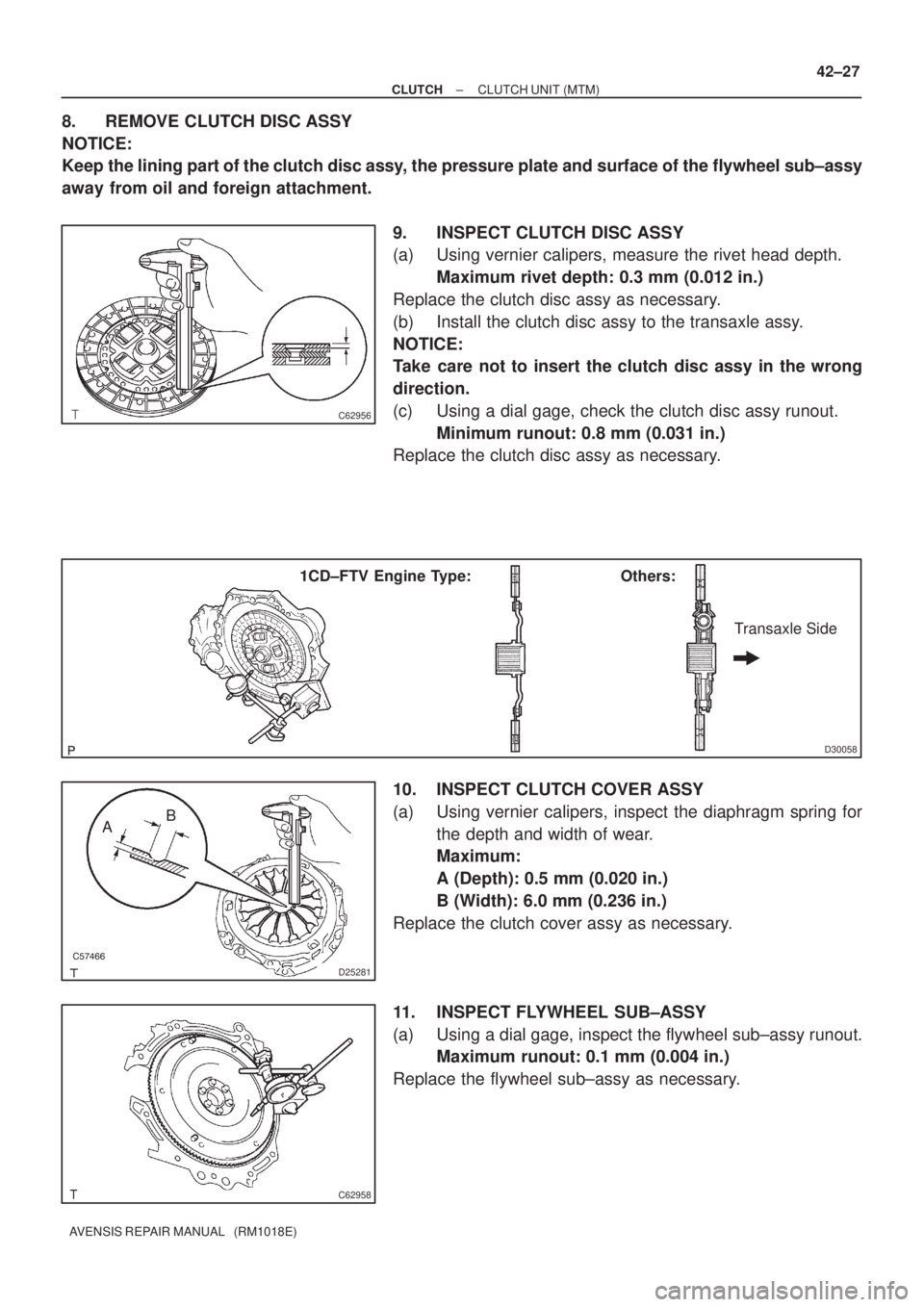
C62956
D30058
1CD±FTV Engine Type: Others:
Transaxle Side
D25281
AB
C62958
± CLUTCHCLUTCH UNIT (MTM)
42±27
AVENSIS REPAIR MANUAL (RM1018E)
8. REMOVE CLUTCH DISC ASSY
NOTICE:
Keep the lining part of the clutch disc assy, the pressure plate and surface of the flywheel sub±assy
away from oil and foreign attachment.
9. INSPECT CLUTCH DISC ASSY
(a) Using vernier calipers, measure the rivet head depth.
Maximum rivet depth: 0.3 mm (0.012 in.)
Replace the clutch disc assy as necessary.
(b) Install the clutch disc assy to the transaxle assy.
NOTICE:
Take care not to insert the clutch disc assy in the wrong
direction.
(c) Using a dial gage, check the clutch disc assy runout.
Minimum runout: 0.8 mm (0.031 in.)
Replace the clutch disc assy as necessary.
10. INSPECT CLUTCH COVER ASSY
(a) Using vernier calipers, inspect the diaphragm spring for
the depth and width of wear.
Maximum:
A (Depth): 0.5 mm (0.020 in.)
B (Width): 6.0 mm (0.236 in.)
Replace the clutch cover assy as necessary.
11. INSPECT FLYWHEEL SUB±ASSY
(a) Using a dial gage, inspect the flywheel sub±assy runout.
Maximum runout: 0.1 mm (0.004 in.)
Replace the flywheel sub±assy as necessary.