Page 3929 of 5135
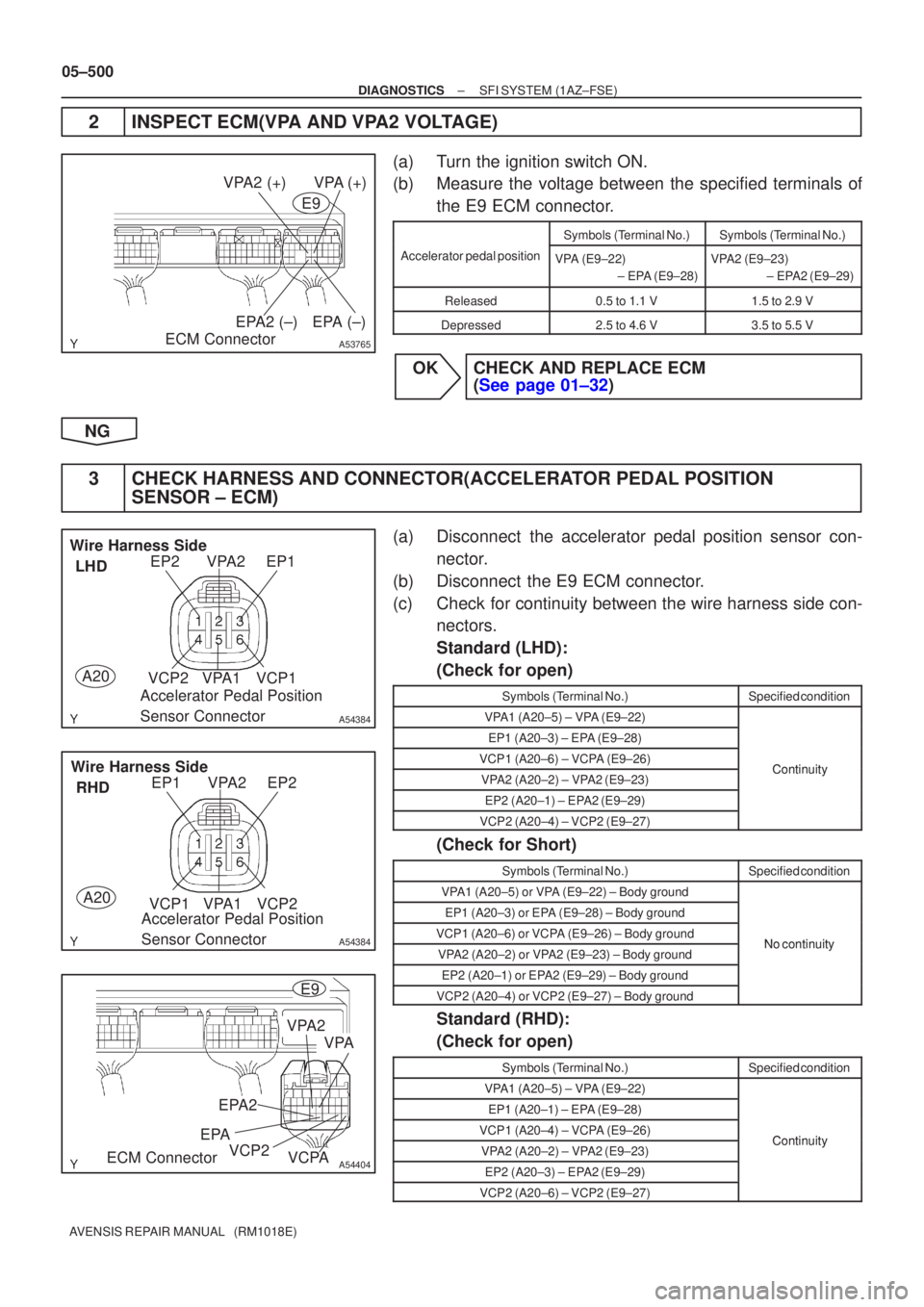
A53765
VPA2 (+)VPA (+)EPA (±)
EPA2 (±)
ECM Connector
E9
A54384
EP2EP1VPA2
VCP2VPA1VCP1
Wire Harness Side
LHD
A20 Accelerator Pedal Position
Sensor Connector
A54384
EP1EP2VPA2
VCP1VPA1VCP2
Wire Harness Side
RHD
A20 Accelerator Pedal Position
Sensor Connector
A54404
EPA2
EPA
E9
VCPA
VCP2
VPA2
VPA
ECM Connector
05±500
±
DIAGNOSTICS SFI SYSTEM(1AZ±FSE)
AVENSIS REPAIR MANUAL (RM1018E)
2INSPECT ECM(VPA AND VPA2 VOLTAGE)
(a)Turn the ignition switch ON.
(b)Measure the voltage between the specified terminals of the E9 ECM connector.
Symbols (Terminal No.)Symbols (Terminal No.)
Accelerator pedal positionVPA (E9±22)
± EPA (E9±28)VPA2 (E9±23) ± EPA2 (E9±29)
Released0.5 to 1.1 V1.5 to 2.9 V
Depressed2.5 to 4.6 V3.5 to 5.5 V
OKCHECK AND REPLACE ECM(See page 01±32)
NG
3 CHECK HARNESS AND CONNECTOR(ACCELERATOR PEDAL POSITION SENSOR ± ECM)
(a) Disconnect the accelerator pedal position sensor con-
nector.
(b) Disconnect the E9 ECM connector.
(c) Check for continuity between the wire harness side con- nectors.
Standard (LHD):
(Check for open)
Symbols (Terminal No.)Specified condition
VPA1 (A20±5) ± VPA (E9±22)
EP1 (A20±3) ± EPA (E9±28)
VCP1 (A20±6) ± VCPA (E9±26)ContinuityVPA2 (A20±2) ± VPA2 (E9±23)Continuity
EP2 (A20±1) ± EPA2 (E9±29)
VCP2 (A20±4) ± VCP2 (E9±27)
(Check for Short)
Symbols (Terminal No.)Specified condition
VPA1 (A20±5) or VPA (E9±22) ± Body ground
EP1 (A20±3) or EPA (E9±28) ± Body ground
VCP1 (A20±6) or VCPA (E9±26) ± Body groundNo continuityVPA2 (A20±2) or VPA2 (E9±23) ± Body groundNo continuity
EP2 (A20±1) or EPA2 (E9±29) ± Body ground
VCP2 (A20±4) or VCP2 (E9±27) ± Body ground
Standard (RHD):
(Check for open)
Symbols (Terminal No.)Specified condition
VPA1 (A20±5) ± VPA (E9±22)
EP1 (A20±1) ± EPA (E9±28)
VCP1 (A20±4) ± VCPA (E9±26)ContinuityVPA2 (A20±2) ± VPA2 (E9±23)Continuity
EP2 (A20±3) ± EPA2 (E9±29)
VCP2 (A20±6) ± VCP2 (E9±27)
Page 3930 of 5135
±
DIAGNOSTICS SFI SYSTEM(1AZ±FSE)
05±501
AVENSIS REPAIR MANUAL (RM1018E)
(Check for Short)
Symbols (Terminal No.)Specified condition
VPA1 (A20±5) or VPA (E9±22) ± Body ground
EP1 (A20±1) or EPA (E9±28) ± Body ground
VCP1 (A20±4) or VCPA (E9±26) ± Body groundNocontinuityVPA2 (A20±2) or VPA2 (E9±23) ± Body groundNo continuity
EP2 (A20±3) or EPA2 (E9±29) ± Body ground
VCP2 (A20±6) or VCP2 (E9±27) ± Body ground
NGREPAIR OR REPLACE HARNESS OR
CONNECTOR
OK
REPLACE ACCELERATOR PEDAL ASSY (See page 10±66)
Page 3931 of 5135
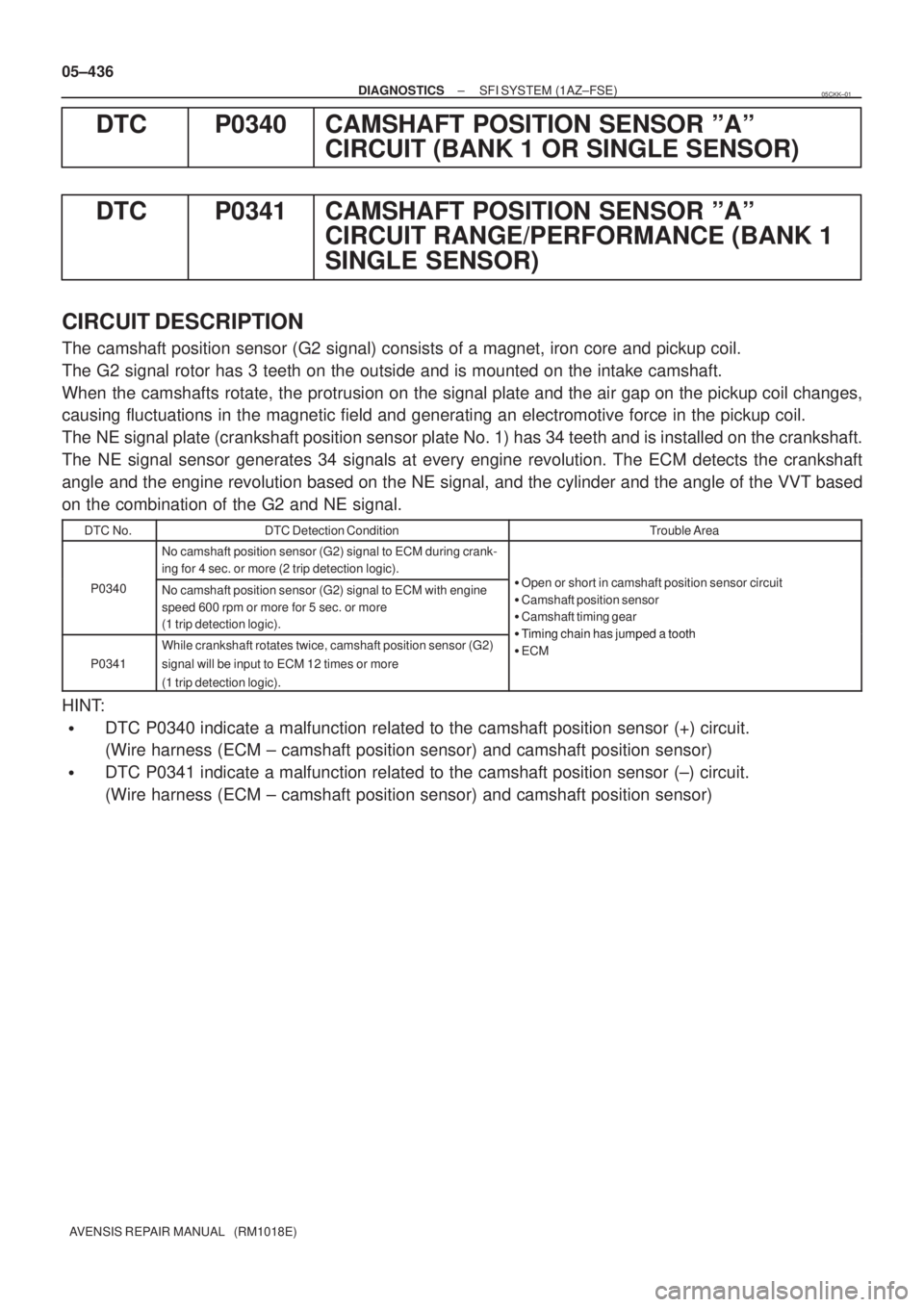
05±436
± DIAGNOSTICSSFI SYSTEM (1AZ±FSE)
AVENSIS REPAIR MANUAL (RM1018E)
DTC P0340 CAMSHAFT POSITION SENSOR ºAº
CIRCUIT (BANK 1 OR SINGLE SENSOR)
DTC P0341 CAMSHAFT POSITION SENSOR ºAº
CIRCUIT RANGE/PERFORMANCE (BANK 1
SINGLE SENSOR)
CIRCUIT DESCRIPTION
The camshaft position sensor (G2 signal) consists of a magnet, iron core and pickup coil.
The G2 signal rotor has 3 teeth on the outside and is mounted on the intake camshaft.
When the camshafts rotate, the protrusion on the signal plate and the air gap on the pickup coil changes,
causing fluctuations in the magnetic field and generating an electromotive force in the pickup coil.
The NE signal plate (crankshaft position sensor plate No. 1) has 34 teeth and is installed on the crankshaft.
The NE signal sensor generates 34 signals at every engine revolution. The ECM detects the crankshaft
angle and the engine revolution based on the NE signal, and the cylinder and the angle of the VVT based
on the combination of the G2 and NE signal.
DTC No.DTC Detection ConditionTrouble Area
No camshaft position sensor (G2) signal to ECM during crank-
ing for 4 sec. or more (2 trip detection logic).
O h t i h ft iti i itP0340No camshaft position sensor (G2) signal to ECM with engine
speed 600 rpm or more for 5 sec. or more
(1 trip detection logic).Open or short in camshaft position sensor circuit
Camshaft position sensor
Camshaft timing gear
Timing chain has jumped a tooth
P0341
While crankshaft rotates twice, camshaft position sensor (G2)
signal will be input to ECM 12 times or more
(1 trip detection logic).Timing chain has jumped a tooth
ECM
HINT:
DTC P0340 indicate a malfunction related to the camshaft position sensor (+) circuit.
(Wire harness (ECM ± camshaft position sensor) and camshaft position sensor)
DTC P0341 indicate a malfunction related to the camshaft position sensor (±) circuit.
(Wire harness (ECM ± camshaft position sensor) and camshaft position sensor)
05CKK±01
Page 3932 of 5135

A76903
NE+
G2+
NE±ECM Connector E11
A59781
A64984Camshaft Position Sensor
Component Side
C1
±
DIAGNOSTICS SFI SYSTEM(1AZ±FSE)
05±437
AVENSIS REPAIR MANUAL (RM1018E)
Reference: Inspection using the oscilloscope.
(1)During cranking or idling, check the waveform be-tween the terminals of the ECM connector.
ItemDetails
TerminalCH1: G2+ ± NE±
CH2: NE+ ± NE±
Equipment Setting5 V/Division, 20 ms/Division
ConditionDuring Cranking or idling
HINT:
The correct waveforms are as shown in the left.
WIRING DIAGRAM
Refer to DTC P0335 on page 05±433.
INSPECTION PROCEDURE
HINT:
Read freeze frame data using the hand±held tester. Freeze frame data records the engine conditions when
a malfunction is detected. When troubleshooting, it is useful for determi\
ning whether the vehicle was running
or stopped, the engine was warmed up or not, the air±fuel ratio was lea\
n or rich, etc. at the time of the mal-
function.
1 INSPECT CAMSHAFT POSITION SENSOR(RESISTANCE)
(a) Disconnect the C1 camshaft position sensor connector.
(b) Measure the resistance between the terminals of the camshaft position sensor.
Resistance:
835 to 1,400 at cold
1,060 to 1,645 at hot
NOTICE:
ºColdº and ºHotº shown above mean the temperature of
the coils themselves. ºColdº is from ±10 C (14 F) to 50 C
(122 F) and ºHotº is from 50 C (122 F) to 100 C (212 F).
NG REPLACE CAMSHAFT POSITION SENSOR
OK
Page 3933 of 5135
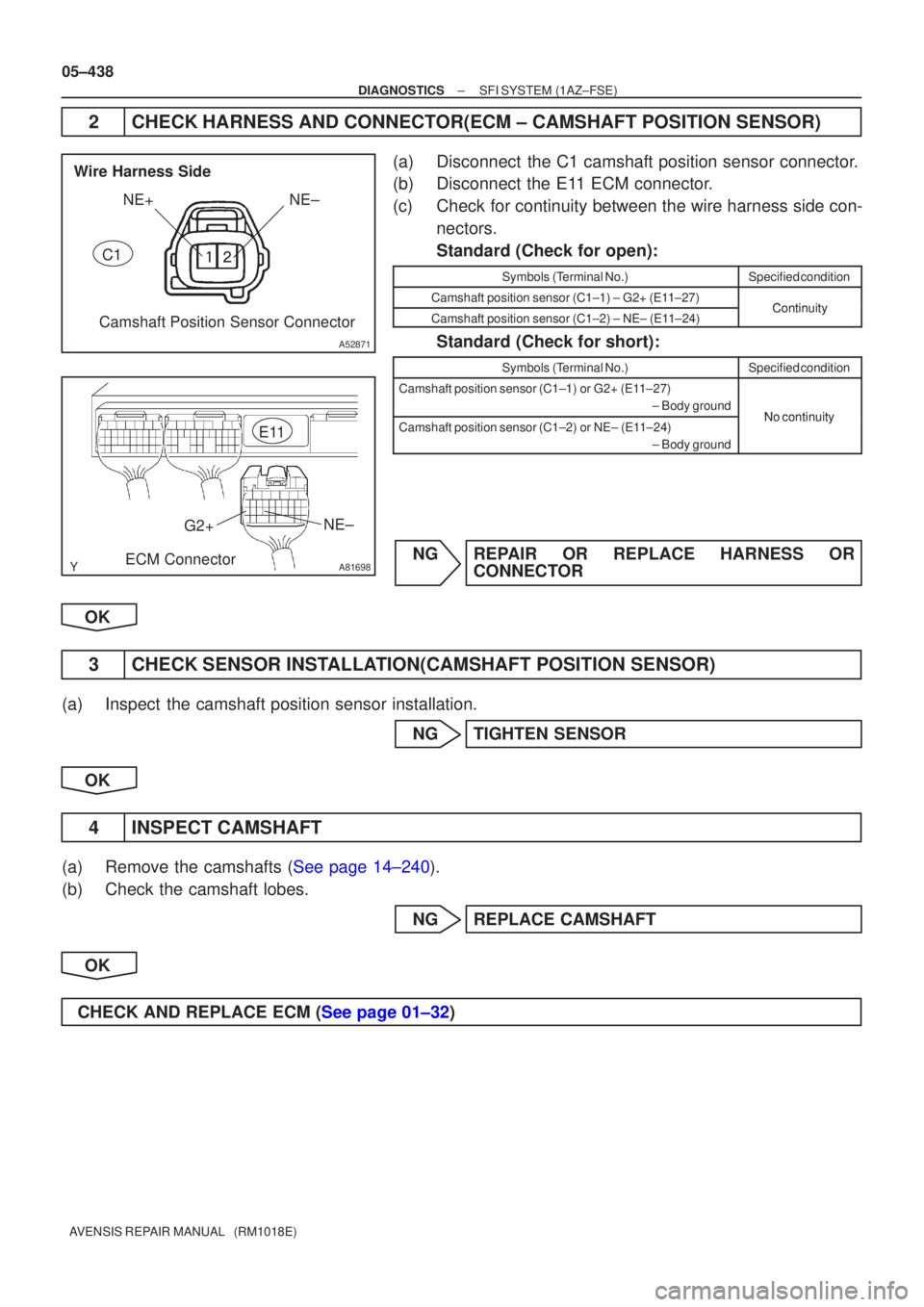
NE+NE±
A52871
Camshaft Position Sensor Connector
Wire Harness Side
C1
A81698
G2+ NE±
ECM Connector E11
05±438
±
DIAGNOSTICS SFI SYSTEM(1AZ±FSE)
AVENSIS REPAIR MANUAL (RM1018E)
2CHECK HARNESS AND CONNECTOR(ECM ± CAMSHAFT POSITION SENSOR)
(a)Disconnect the C1 camshaft position sensor connector.
(b)Disconnect the E11 ECM connector.
(c)Check for continuity between the wire harness side con- nectors.
Standard (Check for open):
Symbols (Terminal No.)Specified condition
Camshaft position sensor (C1±1) ± G2+ (E11±27)ContinuityCamshaft position sensor (C1±2) ± NE± (E11±24)Continuity
Standard (Check for short):
Symbols (Terminal No.)Specified condition
Camshaft position sensor (C1±1)or G2+ (E11±27)
± Body ground
NocontinuityCamshaft position sensor (C1±2)or NE± (E11±24) ± Body groundNo continuity
NGREPAIR OR REPLACE HARNESS ORCONNECTOR
OK
3CHECK SENSOR INSTALLATION(CAMSHAFT POSITION SENSOR)
(a)Inspect the camshaft position sensor installation. NGTIGHTEN SENSOR
OK
4INSPECT CAMSHAFT
(a)Remove the camshafts (See page 14±240).
(b) Check the camshaft lobes. NG REPLACE CAMSHAFT
OK
CHECK AND REPLACE ECM (See page 01±32)
Page 3934 of 5135
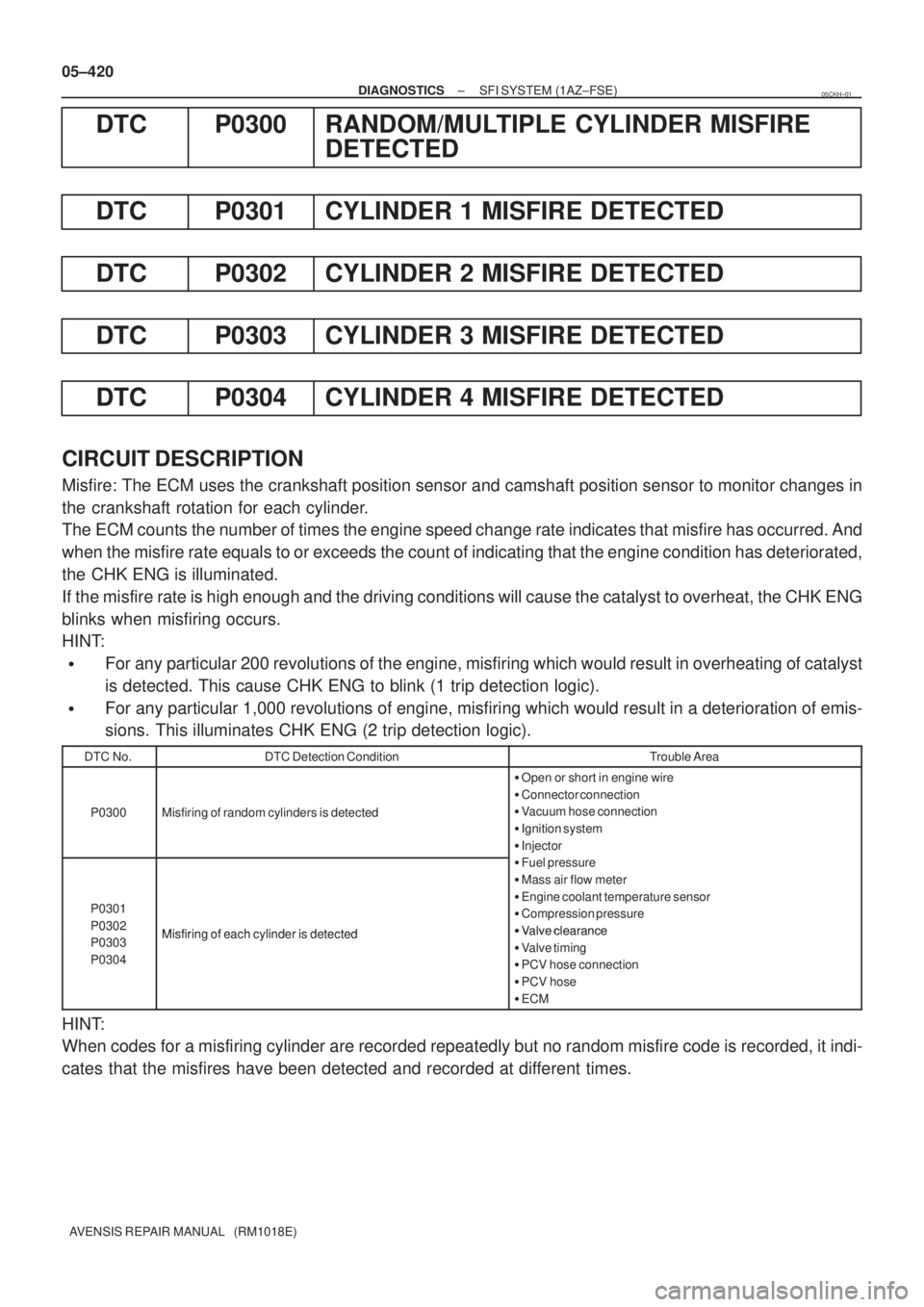
05±420
± DIAGNOSTICSSFI SYSTEM (1AZ±FSE)
AVENSIS REPAIR MANUAL (RM1018E)
DTC P0300 RANDOM/MULTIPLE CYLINDER MISFIRE
DETECTED
DTC P0301 CYLINDER 1 MISFIRE DETECTED
DTC P0302 CYLINDER 2 MISFIRE DETECTED
DTC P0303 CYLINDER 3 MISFIRE DETECTED
DTC P0304 CYLINDER 4 MISFIRE DETECTED
CIRCUIT DESCRIPTION
Misfire: The ECM uses the crankshaft position sensor and camshaft position sensor to monitor changes in
the crankshaft rotation for each cylinder.
The ECM counts the number of times the engine speed change rate indicates that misfire has occurred. And
when the misfire rate equals to or exceeds the count of indicating that the engine condition has deteriorated,
the CHK ENG is illuminated.
If the misfire rate is high enough and the driving conditions will cause the catalyst to overheat, the CHK ENG
blinks when misfiring occurs.
HINT:
For any particular 200 revolutions of the engine, misfiring which would result in overheating of catalyst
is detected. This cause CHK ENG to blink (1 trip detection logic).
For any particular 1,000 revolutions of engine, misfiring which would result in a deterioration of emis-
sions. This illuminates CHK ENG (2 trip detection logic).
DTC No.DTC Detection ConditionTrouble Area
P0300Misfiring of random cylinders is detected
Open or short in engine wire
Connector connection
Vacuum hose connection
Ignition system
Injector
P0301
P0302
Misfiring of each cylinder is detected
Fuel pressure
Mass air flow meter
Engine coolant temperature sensor
Compression pressure
Valve clearanceP0302
P0303
P0304Misfiring of each cylinder is detectedValve clearance
Valve timing
PCV hose connection
PCV hose
ECM
HINT:
When codes for a misfiring cylinder are recorded repeatedly but no random misfire code is recorded, it indi-
cates that the misfires have been detected and recorded at different times.
05CKH±01
Page 3935 of 5135
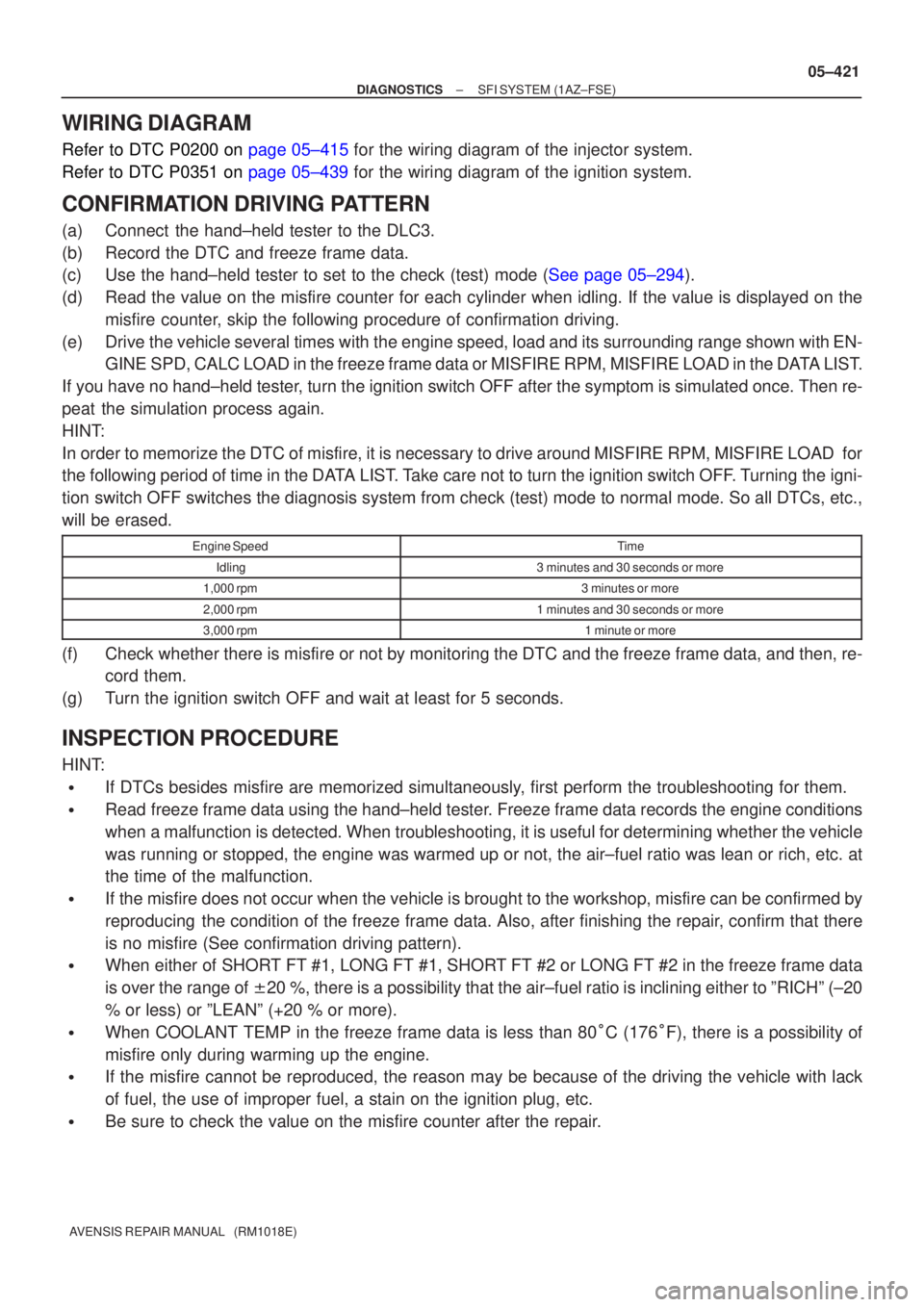
±
DIAGNOSTICS SFI SYSTEM(1AZ±FSE)
05±421
AVENSIS REPAIR MANUAL (RM1018E)
WIRING DIAGRAM
Refer to DTC P0200 on page 05±415 for the wiring diagram of the injector system.
Refer to DTC P0351 on page 05±439 for the wiring diagram of the ignition system.
CONFIRMATION DRIVING PATTERN
(a)Connect the hand±held tester to the DLC3.
(b)Record the DTC and freeze frame data.
(c)Use the hand±held tester to set to the check (test) mode (See page 05±294).
(d) Read the value on the misfire counter for each cylinder when idling. If \
the value is displayed on the
misfire counter, skip the following procedure of confirmation driving.
(e) Drive the vehicle several times with the engine speed, load and its surr\
ounding range shown with EN- GINE SPD, CALC LOAD in the freeze frame data or MISFIRE RPM, MISFIRE LOAD in\
the DATA LIST.
If you have no hand±held tester, turn the ignition switch OFF after the symptom is simulated once. Then\
re-
peat the simulation process again.
HINT:
In order to memorize the DTC of misfire, it is necessary to drive around M\
ISFIRE RPM, MISFIRE LOAD for
the following period of time in the DATA LIST. Take care not to turn the ignition switch OFF. Turning the igni-
tion switch OFF switches the diagnosis system from check (test) mode to no\
rmal mode. So all DTCs, etc.,
will be erased.
Engine SpeedTime
Idling3 minutes and 30 seconds or more
1,000 rpm3 minutes or more
2,000 rpm1 minutes and 30 seconds or more
3,000 rpm1 minute or more
(f) Check whether there is misfire or not by monitoring the DTC and the freeze fr\
ame data, and then, re- cord them.
(g) Turn the ignition switch OFF and wait at least for 5 seconds.
INSPECTION PROCEDURE
HINT:
If DTCs besides misfire are memorized simultaneously, first perform the troubleshooting for them.
Read freeze frame data using the hand±held tester. Freeze frame data records the engine conditions
when a malfunction is detected. When troubleshooting, it is useful for deter\
mining whether the vehicle
was running or stopped, the engine was warmed up or not, the air±fuel ra\
tio was lean or rich, etc. at
the time of the malfunction.
If the misfire does not occur when the vehicle is brought to the workshop,\
misfire can be confirmed by
reproducing the condition of the freeze frame data. Also, after finishing the repai\
r, confirm that there
is no misfire (See confirmation driving pattern).
When either of SHORT FT #1, LONG FT #1, SHORT FT #2 or LONG FT #2 in the freeze frame data
is over the range of 20 %, there is a possibility that the air±fuel ratio is inclining eit\
her to ºRICHº (±20
% or less) or ºLEANº (+20 % or more).
When COOLANT TEMP in the freeze frame data is less than 80 C (176 F), there is a possibility of
misfire only during warming up the engine.
If the misfire cannot be reproduced, the reason may be because of the dr\
iving the vehicle with lack
of fuel, the use of improper fuel, a stain on the ignition plug, etc.
Be sure to check the value on the misfire counter after the repair.
Page 3936 of 5135
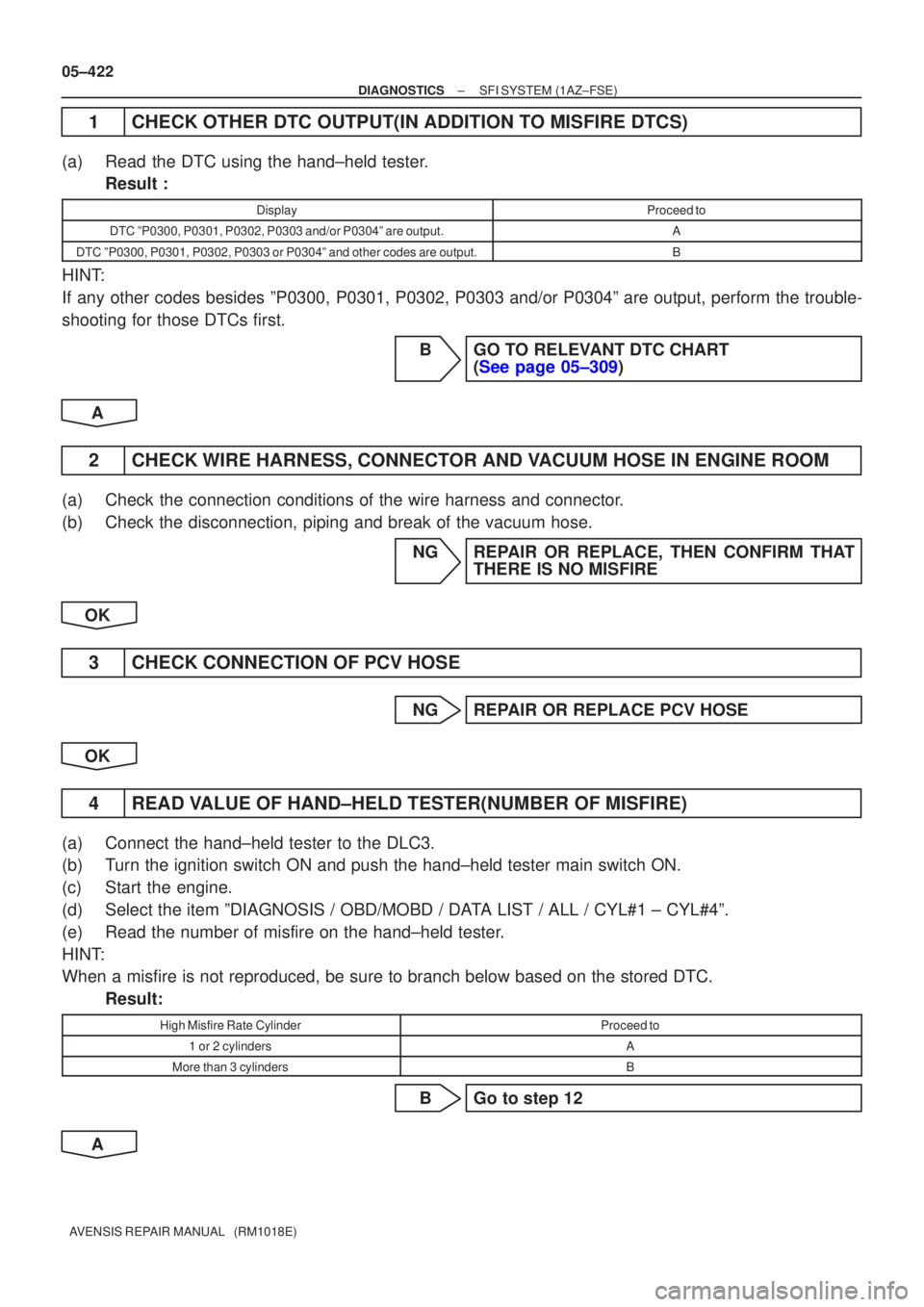
05±422
±
DIAGNOSTICS SFI SYSTEM(1AZ±FSE)
AVENSIS REPAIR MANUAL (RM1018E)
1CHECK OTHER DTC OUTPUT(IN ADDITION TO MISFIRE DTCS)
(a)Read the DTC using the hand±held tester. Result :
DisplayProceed to
DTC ºP0300, P0301, P0302, P0303 and/or P0304º are output.A
DTC ºP0300, P0301, P0302, P0303 or P0304º and other codes are outp\
ut.B
HINT:
If any other codes besides ºP0300, P0301, P0302, P0303 and/or P0304º are output, perform the trouble-
shooting for those DTCs first.
BGO TO RELEVANT DTC CHART (See page 05±309)
A
2 CHECK WIRE HARNESS, CONNECTOR AND VACUUM HOSE IN ENGINE ROOM
(a) Check the connection conditions of the wire harness and connector.
(b) Check the disconnection, piping and break of the vacuum hose. NG REPAIR OR REPLACE, THEN CONFIRM THATTHERE IS NO MISFIRE
OK
3 CHECK CONNECTION OF PCV HOSE
NG REPAIR OR REPLACE PCV HOSE
OK
4 READ VALUE OF HAND±HELD TESTER(NUMBER OF MISFIRE)
(a) Connect the hand±held tester to the DLC3.
(b) Turn the ignition switch ON and push the hand±held tester main switch \
ON.
(c) Start the engine.
(d) Select the item ºDIAGNOSIS / OBD/MOBD / DATA LIST / ALL / CYL#1 ± CYL#4º.
(e) Read the number of misfire on the hand±held tester.
HINT:
When a misfire is not reproduced, be sure to branch below based on the s\
tored DTC. Result:
High Misfire Rate CylinderProceed to
1 or 2 cylindersA
More than 3 cylindersB
B Go to step 12
A