Page 1921 of 5135
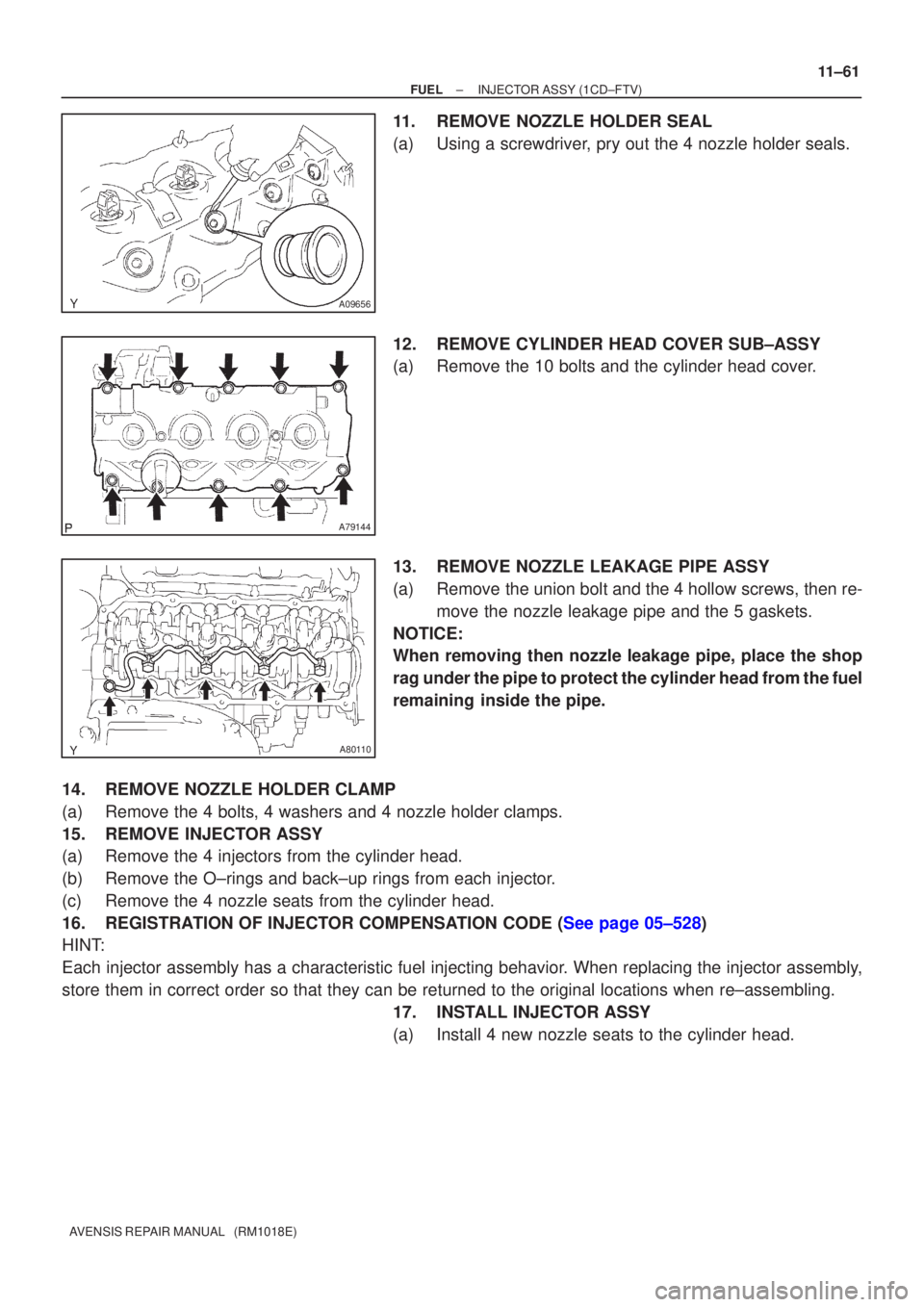
A09656
A79144
A80110
±
FUEL INJECTOR ASSY(1CD±FTV)
11±61
AVENSIS REPAIR MANUAL (RM1018E)
11.REMOVE NOZZLE HOLDER SEAL
(a)Using a screwdriver, pry out the 4 nozzle holder seals.
12.REMOVE CYLINDER HEAD COVER SUB±ASSY
(a)Remove the 10 bolts and the cylinder head cover.
13.REMOVE NOZZLE LEAKAGE PIPE ASSY
(a)Remove the union bolt and the 4 hollow screws, then re-
move the nozzle leakage pipe and the 5 gaskets.
NOTICE:
When removing then nozzle leakage pipe, place the shop
rag under the pipe to protect the cylinder head from the fuel
remaining inside the pipe.
14.REMOVE NOZZLE HOLDER CLAMP
(a)Remove the 4 bolts, 4 washers and 4 nozzle holder clamps.
15.REMOVE INJECTOR ASSY
(a)Remove the 4 injectors from the cylinder head.
(b)Remove the O±rings and back±up rings from each injector.
(c)Remove the 4 nozzle seats from the cylinder head.
16.REGISTRATION OF INJECTOR COMPENSATION CODE (See page 05±528)
HINT:
Each injector assembly has a characteristic fuel injecting behavior. When replacing the injector assembly,
store them in correct order so that they can be returned to the original\
locations when re±assembling. 17. INSTALL INJECTOR ASSY
(a) Install 4 new nozzle seats to the cylinder head.
Page 1922 of 5135
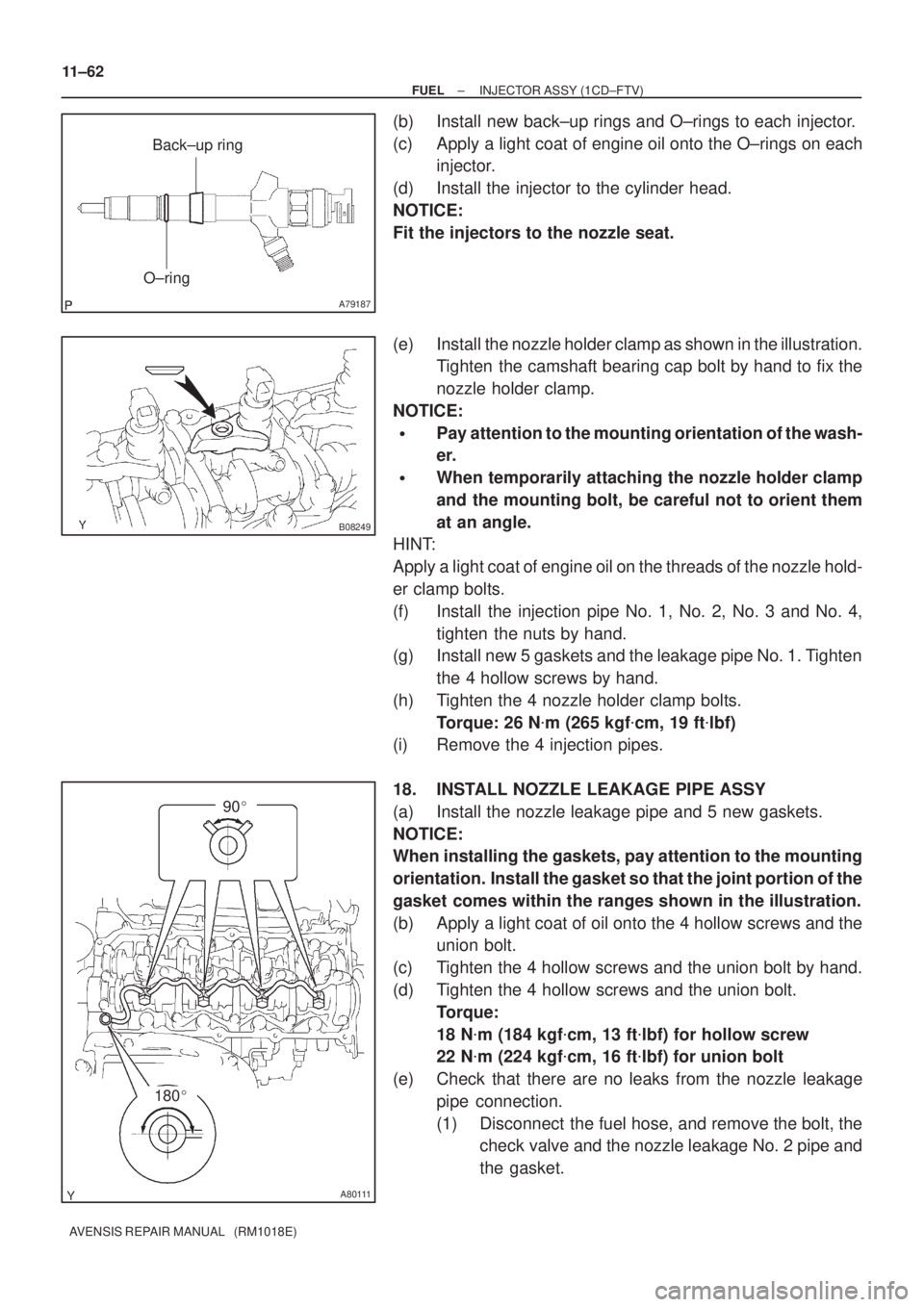
A79187
O±ringBack±up ring
B08249
A80111
180
90 11±62
± FUELINJECTOR ASSY (1CD±FTV)
AVENSIS REPAIR MANUAL (RM1018E)
(b) Install new back±up rings and O±rings to each injector.
(c) Apply a light coat of engine oil onto the O±rings on each
injector.
(d) Install the injector to the cylinder head.
NOTICE:
Fit the injectors to the nozzle seat.
(e) Install the nozzle holder clamp as shown in the illustration.
Tighten the camshaft bearing cap bolt by hand to fix the
nozzle holder clamp.
NOTICE:
Pay attention to the mounting orientation of the wash-
er.
When temporarily attaching the nozzle holder clamp
and the mounting bolt, be careful not to orient them
at an angle.
HINT:
Apply a light coat of engine oil on the threads of the nozzle hold-
er clamp bolts.
(f) Install the injection pipe No. 1, No. 2, No. 3 and No. 4,
tighten the nuts by hand.
(g) Install new 5 gaskets and the leakage pipe No. 1. Tighten
the 4 hollow screws by hand.
(h) Tighten the 4 nozzle holder clamp bolts.
Torque: 26 Nm (265 kgfcm, 19 ftlbf)
(i) Remove the 4 injection pipes.
18. INSTALL NOZZLE LEAKAGE PIPE ASSY
(a) Install the nozzle leakage pipe and 5 new gaskets.
NOTICE:
When installing the gaskets, pay attention to the mounting
orientation. Install the gasket so that the joint portion of the
gasket comes within the ranges shown in the illustration.
(b) Apply a light coat of oil onto the 4 hollow screws and the
union bolt.
(c) Tighten the 4 hollow screws and the union bolt by hand.
(d) Tighten the 4 hollow screws and the union bolt.
Torque:
18 Nm (184 kgfcm, 13 ftlbf) for hollow screw
22 Nm (224 kgfcm, 16 ftlbf) for union bolt
(e) Check that there are no leaks from the nozzle leakage
pipe connection.
(1) Disconnect the fuel hose, and remove the bolt, the
check valve and the nozzle leakage No. 2 pipe and
the gasket.
Page 1923 of 5135
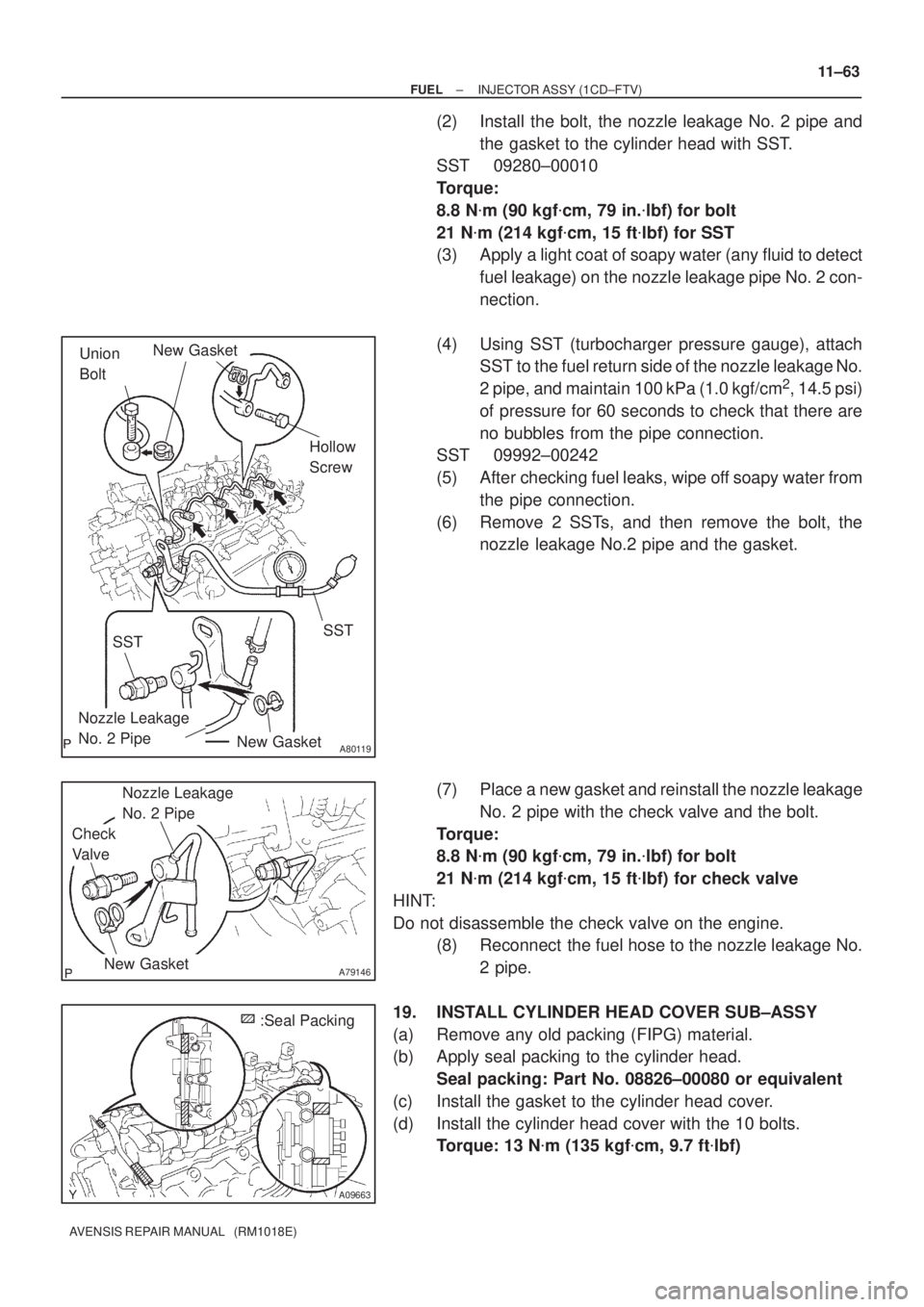
A80119
New Gasket
Hollow
Screw
Union
Bolt
SST
Nozzle Leakage
No. 2 Pipe
New Gasket
SST
A79146
Check
Valve
Nozzle Leakage
No. 2 Pipe
New Gasket
A09663
:Seal Packing
± FUELINJECTOR ASSY (1CD±FTV)
11±63
AVENSIS REPAIR MANUAL (RM1018E)
(2) Install the bolt, the nozzle leakage No. 2 pipe and
the gasket to the cylinder head with SST.
SST 09280±00010
Torque:
8.8 Nm (90 kgfcm, 79 in.lbf) for bolt
21 Nm (214 kgfcm, 15 ftlbf) for SST
(3) Apply a light coat of soapy water (any fluid to detect
fuel leakage) on the nozzle leakage pipe No. 2 con-
nection.
(4) Using SST (turbocharger pressure gauge), attach
SST to the fuel return side of the nozzle leakage No.
2 pipe, and maintain 100 kPa (1.0 kgf/cm
2, 14.5 psi)
of pressure for 60 seconds to check that there are
no bubbles from the pipe connection.
SST 09992±00242
(5) After checking fuel leaks, wipe off soapy water from
the pipe connection.
(6) Remove 2 SSTs, and then remove the bolt, the
nozzle leakage No.2 pipe and the gasket.
(7) Place a new gasket and reinstall the nozzle leakage
No. 2 pipe with the check valve and the bolt.
Torque:
8.8 Nm (90 kgfcm, 79 in.lbf) for bolt
21 Nm (214 kgfcm, 15 ftlbf) for check valve
HINT:
Do not disassemble the check valve on the engine.
(8) Reconnect the fuel hose to the nozzle leakage No.
2 pipe.
19. INSTALL CYLINDER HEAD COVER SUB±ASSY
(a) Remove any old packing (FIPG) material.
(b) Apply seal packing to the cylinder head.
Seal packing: Part No. 08826±00080 or equivalent
(c) Install the gasket to the cylinder head cover.
(d) Install the cylinder head cover with the 10 bolts.
Torque: 13 Nm (135 kgfcm, 9.7 ftlbf)
Page 1924 of 5135
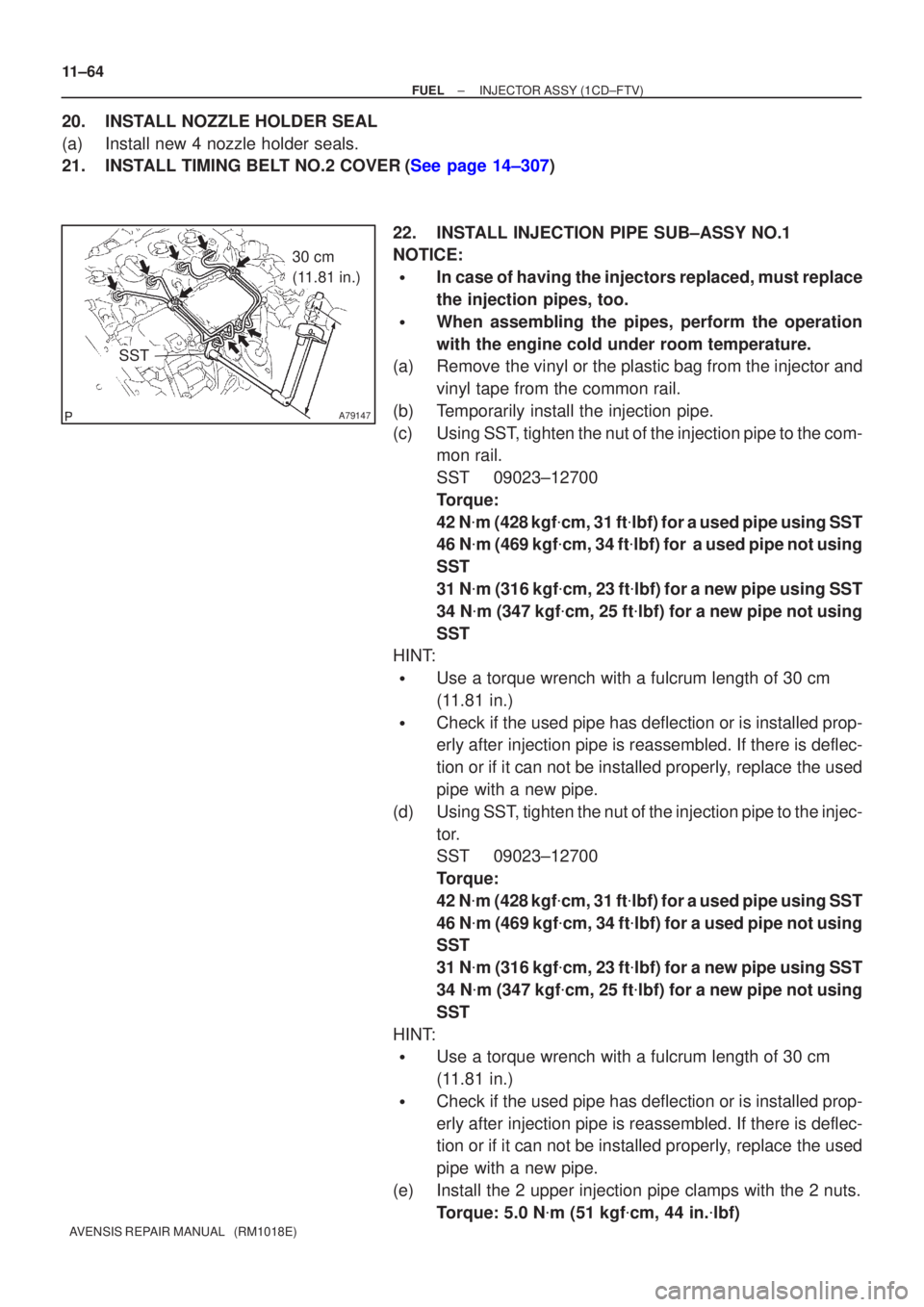
A79147
SST
30 cm
(11.81 in.)
11±64
±
FUEL INJECTOR ASSY(1CD±FTV)
AVENSIS REPAIR MANUAL (RM1018E)
20.INSTALL NOZZLE HOLDER SEAL
(a)Install new 4 nozzle holder seals.
21.INSTALL TIMING BELT NO.2 COVER(See page 14±307) 22. INSTALL INJECTION PIPE SUB±ASSY NO.1
NOTICE:
In case of having the injectors replaced, must replace
the injection pipes, too.
When assembling the pipes, perform the operation
with the engine cold under room temperature.
(a) Remove the vinyl or the plastic bag from the injector and
vinyl tape from the common rail.
(b) Temporarily install the injection pipe.
(c) Using SST, tighten the nut of the injection pipe to the com- mon rail.
SST 09023±12700
Torque:
42 Nm (428 kgf cm, 31 ft lbf) for a used pipe using SST
46 N m (469 kgf cm, 34 ft lbf) for a used pipe not using
SST
31 N m (316 kgf cm, 23 ft lbf) for a new pipe using SST
34 N m (347 kgf cm, 25 ft lbf) for a new pipe not using
SST
HINT:
Use a torque wrench with a fulcrum length of 30 cm
(11.81 in.)
Check if the used pipe has deflection or is installed prop-
erly after injection pipe is reassembled. If there is deflec-
tion or if it can not be installed properly, replace the used
pipe with a new pipe.
(d) Using SST, tighten the nut of the injection pipe to the injec- tor.
SST 09023±12700
Torque:
42 Nm (428 kgf cm, 31 ft lbf) for a used pipe using SST
46 N m (469 kgf cm, 34 ft lbf) for a used pipe not using
SST
31 N m (316 kgf cm, 23 ft lbf) for a new pipe using SST
34 N m (347 kgf cm, 25 ft lbf) for a new pipe not using
SST
HINT:
Use a torque wrench with a fulcrum length of 30 cm
(11.81 in.)
Check if the used pipe has deflection or is installed prop-
erly after injection pipe is reassembled. If there is deflec-
tion or if it can not be installed properly, replace the used
pipe with a new pipe.
(e) Install the 2 upper injection pipe clamps with the 2 nuts. Torque: 5.0 N m (51 kgf cm, 44 in. lbf)
Page 1925 of 5135
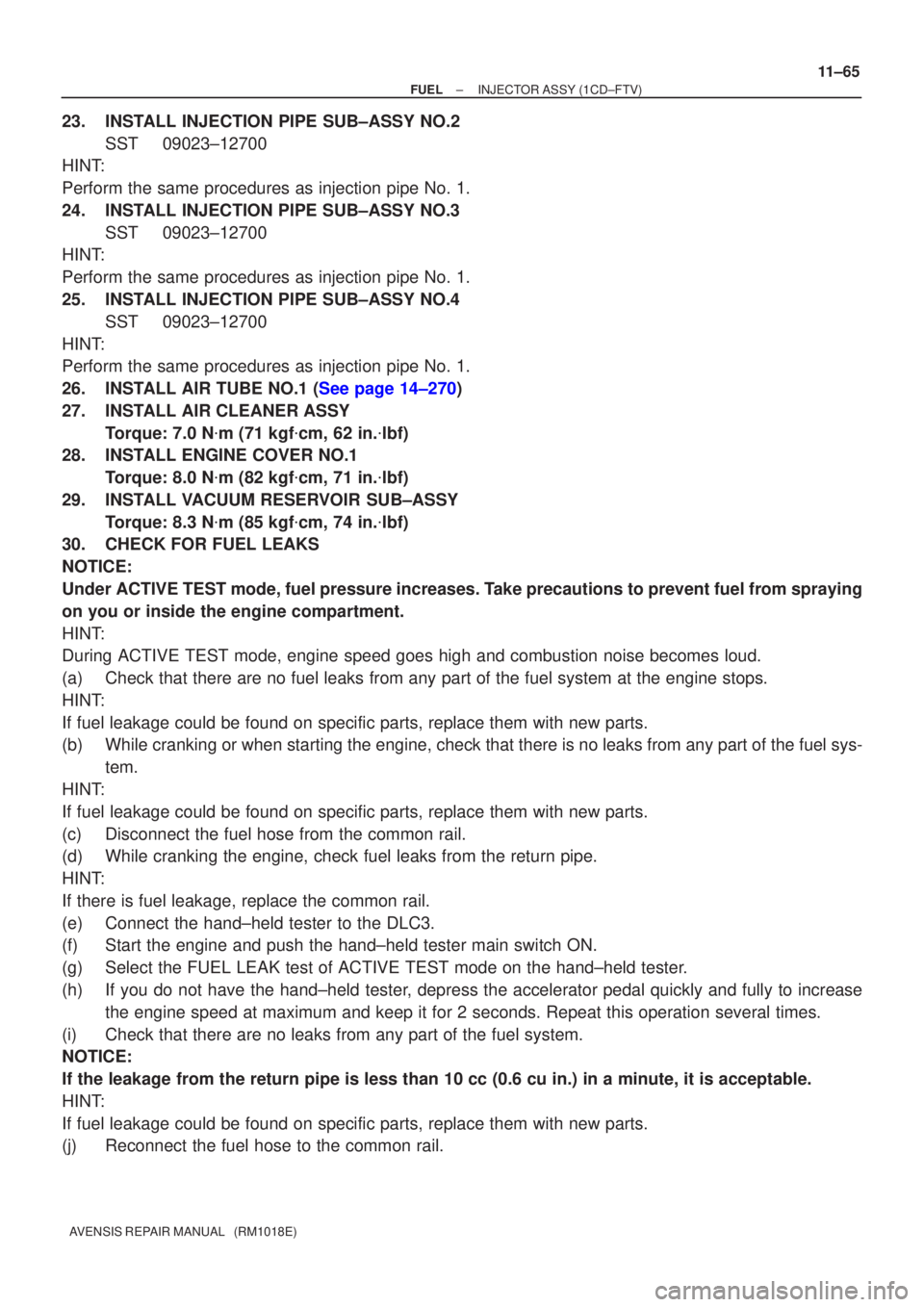
±
FUEL INJECTOR ASSY(1CD±FTV)
11±65
AVENSIS REPAIR MANUAL (RM1018E)
23.INSTALL INJECTION PIPE SUB±ASSY NO.2
SST09023±12700
HINT:
Perform the same procedures as injection pipe No. 1.
24.INSTALL INJECTION PIPE SUB±ASSY NO.3
SST09023±12700
HINT:
Perform the same procedures as injection pipe No. 1.
25.INSTALL INJECTION PIPE SUB±ASSY NO.4
SST09023±12700
HINT:
Perform the same procedures as injection pipe No. 1.
26.INSTALL AIR TUBE NO.1 (See page 14±270)
27. INSTALL AIR CLEANER ASSY Torque: 7.0 N m (71 kgf cm, 62 in. lbf)
28. INSTALL ENGINE COVER NO.1
Torque: 8.0 N m (82 kgf cm, 71 in. lbf)
29. INSTALL VACUUM RESERVOIR SUB±ASSY Torque: 8.3 N m (85 kgf cm, 74 in. lbf)
30. CHECK FOR FUEL LEAKS
NOTICE:
Under ACTIVE TEST mode, fuel pressure increases. Take precautions to prevent fuel from spraying
on you or inside the engine compartment.
HINT:
During ACTIVE TEST mode, engine speed goes high and combustion noise bec\
omes loud.
(a) Check that there are no fuel leaks from any part of the fuel system at t\
he engine stops.
HINT:
If fuel leakage could be found on specific parts, replace them with new \
parts.
(b) While cranking or when starting the engine, check that there is no leaks from\
any part of the fuel sys-
tem.
HINT:
If fuel leakage could be found on specific parts, replace them with new pa\
rts.
(c) Disconnect the fuel hose from the common rail.
(d) While cranking the engine, check fuel leaks from the return pipe.
HINT:
If there is fuel leakage, replace the common rail.
(e) Connect the hand±held tester to the DLC3.
(f) Start the engine and push the hand±held tester main switch ON.
(g) Select the FUEL LEAK test of ACTIVE TEST mode on the hand±held tester\
.
(h) If you do not have the hand±held tester, depress the accelerator pedal quickly and fully to increase the engine speed at maximum and keep it for 2 seconds. Repeat this opera\
tion several times.
(i) Check that there are no leaks from any part of the fuel system.
NOTICE:
If the leakage from the return pipe is less than 10 cc (0.6 cu in.) in\
a minute, it is acceptable.
HINT:
If fuel leakage could be found on specific parts, replace them with new \
parts.
(j) Reconnect the fuel hose to the common rail.
Page 1926 of 5135
110U7±01
A79434
Radiator Support Opening Cover
Engine Cover No. 1
Vacuum Reservoir Sub±assy
Union To Connector Tube Hose
Air Cleaner Cap w/ Hose
Air Cleaner Element
Air Cleaner Case
N´m (kgf´cm, ft´lbf)
: Specified torque
8.0 (82, 71 in.lbf)
8.3 (85, 73 in.lbf)
7.0 (71, 62 in.lbf)
Clip
Retainer
25 (255, 18)
Air Tube No. 1
25 (255, 18)
11±58
± FUELINJECTOR ASSY (1CD±FTV)
AVENSIS REPAIR MANUAL (RM1018E)
INJECTOR ASSY (1CD±FTV)
COMPONENTS
Page 1927 of 5135
A79442
Timing Belt No. 2 Cover
Seal Washer *
2 Gasket
Injection Pipe
Clamp No. 2
Injection
Pipe Sub±assy
13 (135, 9.7)
Cylinder Head Cover Sub±assy
Gasket
Nozzle Holder Seal
Gasket
O±ring Fuel Injector Back±up Ring No. 1
Injection Nozzle Seat Washer
Nozzle Holder ClampNozzle Leakage
Pipe Assy
Injector Assy
N´m (kgf´cm, ft´lbf)
: Specified torque
Non±reusable part
7.4 (75, 65 in.´lbf)
*1 31 (316, 23)
34 (347, 25)
Gasket
22 (224, 16)
18 (184, 13)
27 (270, 20)
Nozzle
Leakage
Pipe No. 2
*1 Use SST
*2 Replace only if damaged
*1 31 (316, 23)
34 (347, 25)
5.0 (51, 44 in.´lbf)
Gasket
21 (214, 15)
8.8 (90, 79 in.´lbf)
± FUELINJECTOR ASSY (1CD±FTV)
11±59
AVENSIS REPAIR MANUAL (RM1018E)
Page 1928 of 5135
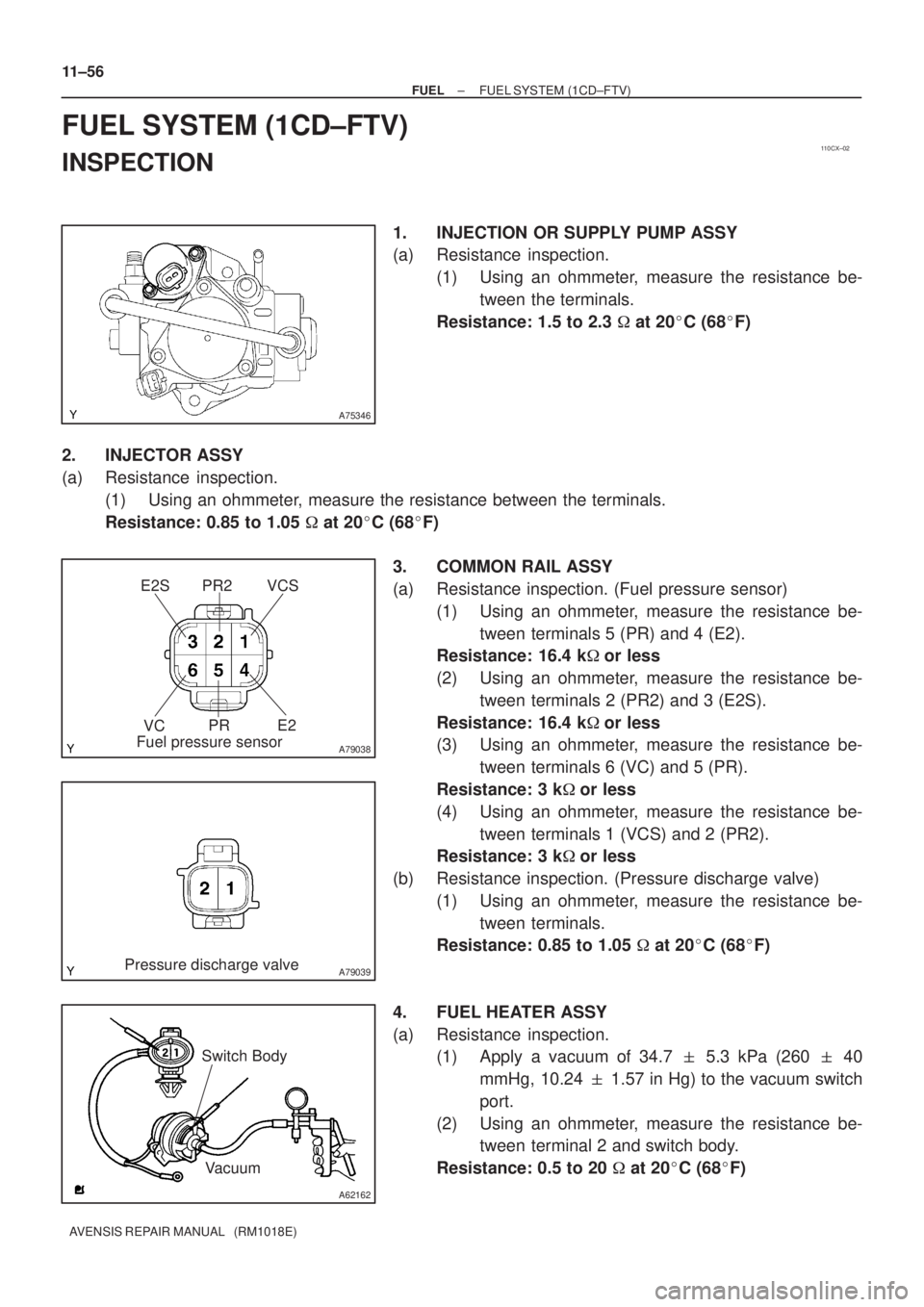
110CX±02
A75346
A79038
E2S PR2 VCS
VCPR E2
Fuel pressure sensor
A79039Pressure discharge valve
A62162
Vacuum Switch Body
11±56
± FUELFUEL SYSTEM (1CD±FTV)
AVENSIS REPAIR MANUAL (RM1018E)
FUEL SYSTEM (1CD±FTV)
INSPECTION
1. INJECTION OR SUPPLY PUMP ASSY
(a) Resistance inspection.
(1) Using an ohmmeter, measure the resistance be-
tween the terminals.
Resistance: 1.5 to 2.3 at 20C (68F)
2. INJECTOR ASSY
(a) Resistance inspection.
(1) Using an ohmmeter, measure the resistance between the terminals.
Resistance: 0.85 to 1.05 at 20C (68F)
3. COMMON RAIL ASSY
(a) Resistance inspection. (Fuel pressure sensor)
(1) Using an ohmmeter, measure the resistance be-
tween terminals 5 (PR) and 4 (E2).
Resistance: 16.4 kor less
(2) Using an ohmmeter, measure the resistance be-
tween terminals 2 (PR2) and 3 (E2S).
Resistance: 16.4 kor less
(3) Using an ohmmeter, measure the resistance be-
tween terminals 6 (VC) and 5 (PR).
Resistance: 3 kor less
(4) Using an ohmmeter, measure the resistance be-
tween terminals 1 (VCS) and 2 (PR2).
Resistance: 3 kor less
(b) Resistance inspection. (Pressure discharge valve)
(1) Using an ohmmeter, measure the resistance be-
tween terminals.
Resistance: 0.85 to 1.05 at 20C (68F)
4. FUEL HEATER ASSY
(a) Resistance inspection.
(1) Apply a vacuum of 34.7 5.3 kPa (260 40
mmHg, 10.24 1.57 in Hg) to the vacuum switch
port.
(2) Using an ohmmeter, measure the resistance be-
tween terminal 2 and switch body.
Resistance: 0.5 to 20 at 20C (68F)