Page 4017 of 5135
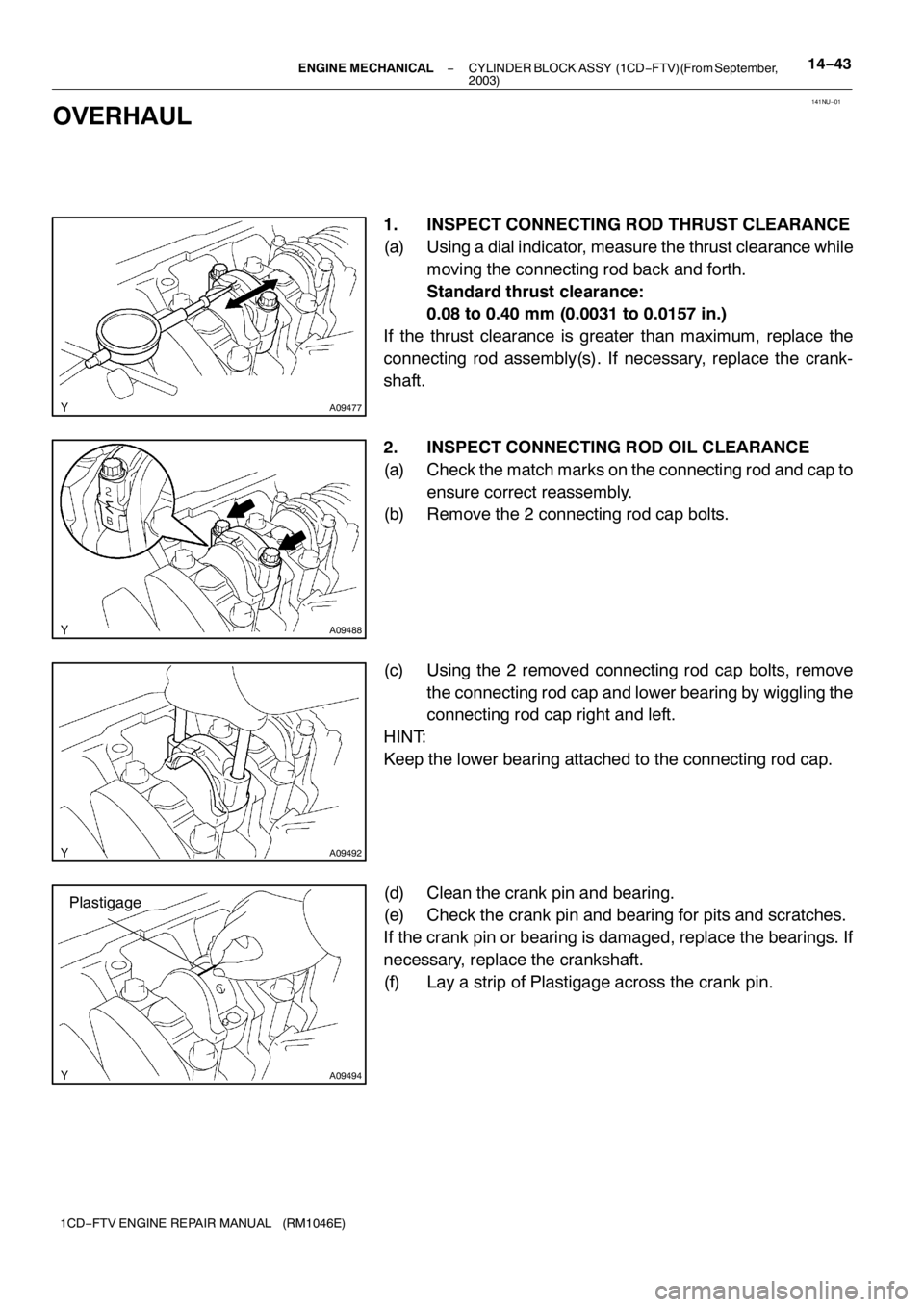
141NU−01
A09477
A09488
A09492
A09494
Plastigage
− ENGINE MECHANICALCYLINDER BLOCK ASSY (1CD−FTV)(From September,
2003)14−43
1CD−FTV ENGINE REPAIR MANUAL (RM1046E)
OVERHAUL
1. INSPECT CONNECTING ROD THRUST CLEARANCE
(a) Using a dial indicator, measure the thrust clearance while
moving the connecting rod back and forth.
Standard thrust clearance:
0.08 to 0.40 mm (0.0031 to 0.0157 in.)
If the thrust clearance is greater than maximum, replace the
connecting rod assembly(s). If necessary, replace the crank-
shaft.
2. INSPECT CONNECTING ROD OIL CLEARANCE
(a) Check the match marks on the connecting rod and cap to
ensure correct reassembly.
(b) Remove the 2 connecting rod cap bolts.
(c) Using the 2 removed connecting rod cap bolts, remove
the connecting rod cap and lower bearing by wiggling the
connecting rod cap right and left.
HINT:
Keep the lower bearing attached to the connecting rod cap.
(d) Clean the crank pin and bearing.
(e) Check the crank pin and bearing for pits and scratches.
If the crank pin or bearing is damaged, replace the bearings. If
necessary, replace the crankshaft.
(f) Lay a strip of Plastigage across the crank pin.
Page 4018 of 5135
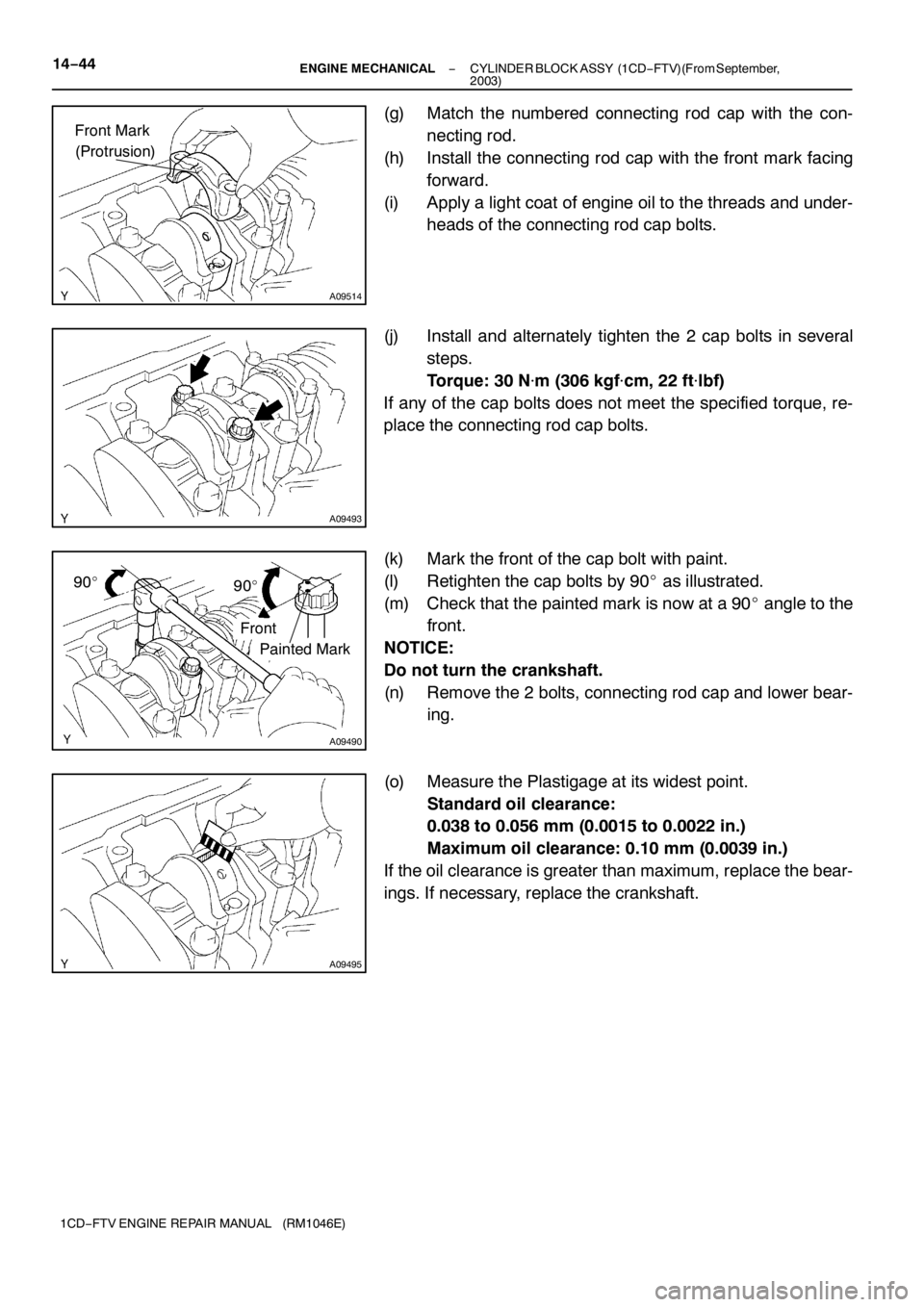
A09514
Front Mark
(Protrusion)
A09493
90_
90_
A09490
Front
Painted Mark
A09495
14−44− ENGINE MECHANICALCYLINDER BLOCK ASSY (1CD−FTV)(From September,
2003)
1CD−FTV ENGINE REPAIR MANUAL (RM1046E)
(g) Match the numbered connecting rod cap with the con-
necting rod.
(h) Install the connecting rod cap with the front mark facing
forward.
(i) Apply a light coat of engine oil to the threads and under-
heads of the connecting rod cap bolts.
(j) Install and alternately tighten the 2 cap bolts in several
steps.
Torque: 30 Nm (306 kgfcm, 22 ftlbf)
If any of the cap bolts does not meet the specified torque, re-
place the connecting rod cap bolts.
(k) Mark the front of the cap bolt with paint.
(l) Retighten the cap bolts by 90_as illustrated.
(m) Check that the painted mark is now at a 90_angle to the
front.
NOTICE:
Do not turn the crankshaft.
(n) Remove the 2 bolts, connecting rod cap and lower bear-
ing.
(o) Measure the Plastigage at its widest point.
Standard oil clearance:
0.038 to 0.056 mm (0.0015 to 0.0022 in.)
Maximum oil clearance: 0.10 mm (0.0039 in.)
If the oil clearance is greater than maximum, replace the bear-
ings. If necessary, replace the crankshaft.
Page 4019 of 5135
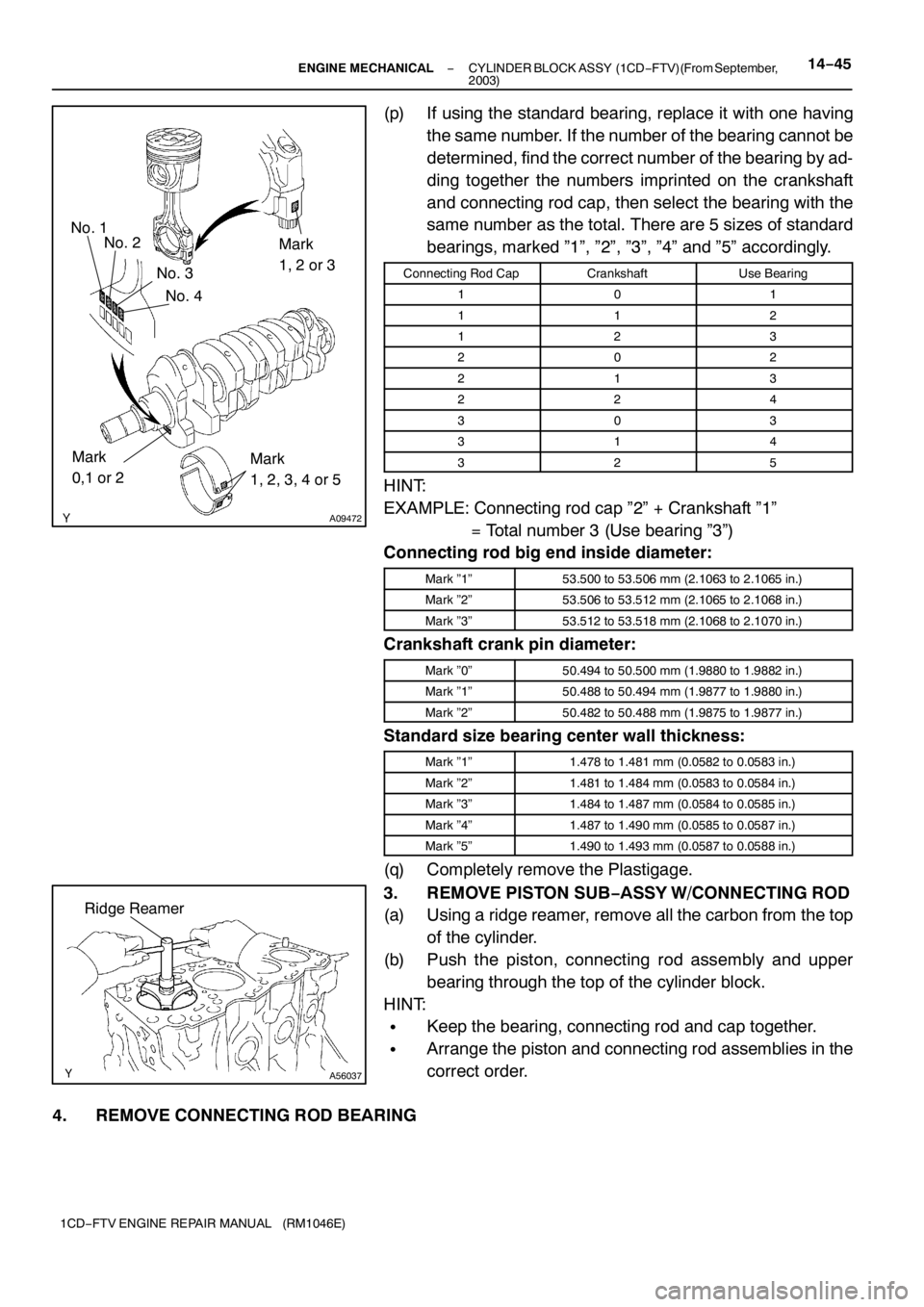
A09472
No. 1
No. 2
No. 3
No. 4
Mark
0,1 or 2Mark
1, 2, 3, 4 or 5Mark
1, 2 or 3
A56037
Ridge Reamer
− ENGINE MECHANICALCYLINDER BLOCK ASSY (1CD−FTV)(From September,
2003)14−45
1CD−FTV ENGINE REPAIR MANUAL (RM1046E)
(p) If using the standard bearing, replace it with one having
the same number. If the number of the bearing cannot be
determined, find the correct number of the bearing by ad-
ding together the numbers imprinted on the crankshaft
and connecting rod cap, then select the bearing with the
same number as the total. There are 5 sizes of standard
bearings, marked ”1”, ”2”, ”3”, ”4” and ”5” accordingly.
Connecting Rod CapCrankshaftUse Bearing
101
112
123
202
213
224
303
314
325
HINT:
EXAMPLE: Connecting rod cap ”2” + Crankshaft ”1”
= Total number 3 (Use bearing ”3”)
Connecting rod big end inside diameter:
Mark ”1”53.500 to 53.506 mm (2.1063 to 2.1065 in.)
Mark ”2”53.506 to 53.512 mm (2.1065 to 2.1068 in.)
Mark ”3”53.512 to 53.518 mm (2.1068 to 2.1070 in.)
Crankshaft crank pin diameter:
Mark ”0”50.494 to 50.500 mm (1.9880 to 1.9882 in.)
Mark ”1”50.488 to 50.494 mm (1.9877 to 1.9880 in.)
Mark ”2”50.482 to 50.488 mm (1.9875 to 1.9877 in.)
Standard size bearing center wall thickness:
Mark ”1”1.478 to 1.481 mm (0.0582 to 0.0583 in.)
Mark ”2”1.481 to 1.484 mm (0.0583 to 0.0584 in.)
Mark ”3”1.484 to 1.487 mm (0.0584 to 0.0585 in.)
Mark ”4”1.487 to 1.490 mm (0.0585 to 0.0587 in.)
Mark ”5”1.490 to 1.493 mm (0.0587 to 0.0588 in.)
(q) Completely remove the Plastigage.
3. REMOVE PISTON SUB−ASSY W/CONNECTING ROD
(a) Using a ridge reamer, remove all the carbon from the top
of the cylinder.
(b) Push the piston, connecting rod assembly and upper
bearing through the top of the cylinder block.
HINT:
SKeep the bearing, connecting rod and cap together.
SArrange the piston and connecting rod assemblies in the
correct order.
4. REMOVE CONNECTING ROD BEARING
Page 4020 of 5135
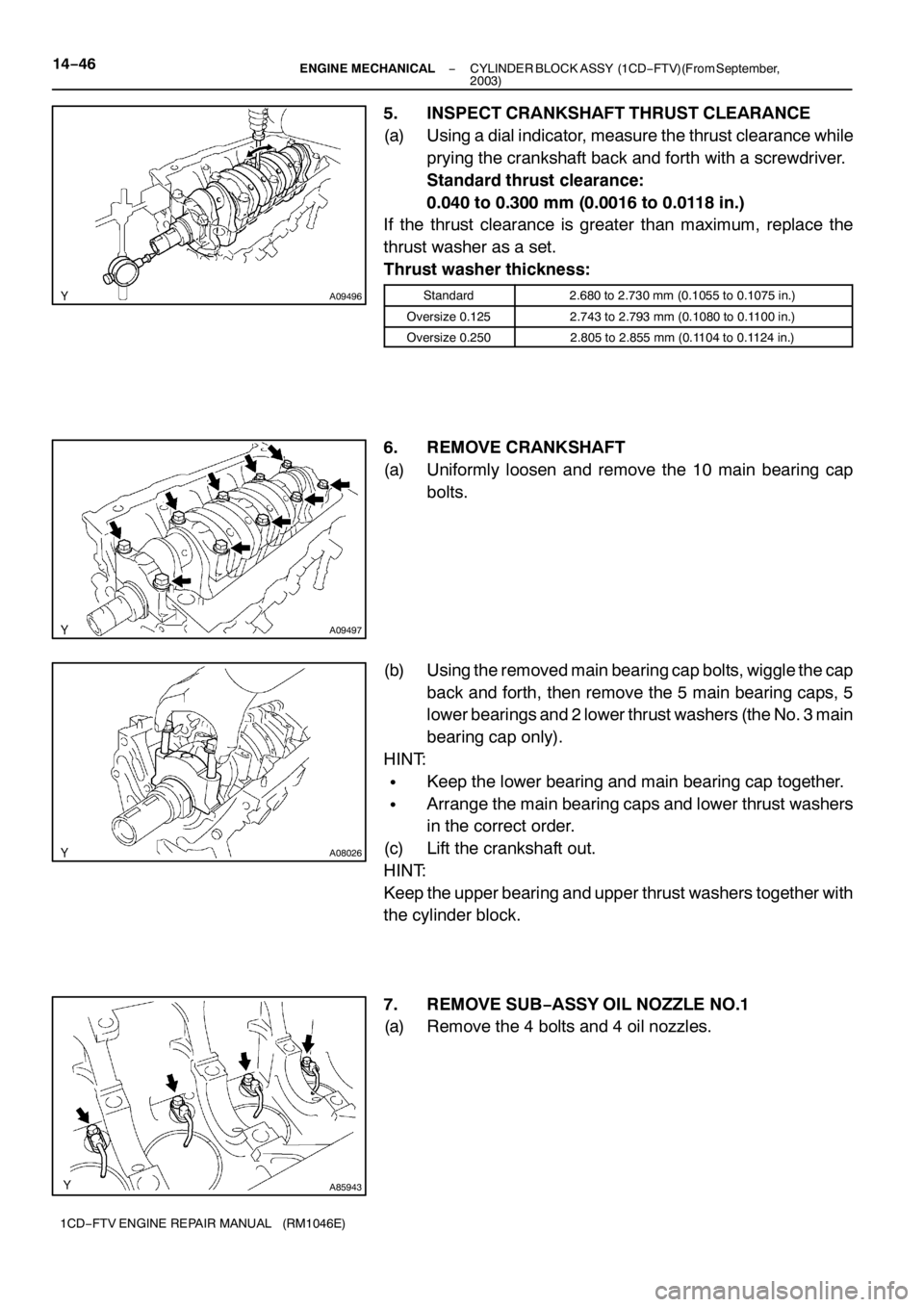
A09496
A09497
A08026
A85943
14−46− ENGINE MECHANICALCYLINDER BLOCK ASSY (1CD−FTV)(From September,
2003)
1CD−FTV ENGINE REPAIR MANUAL (RM1046E)
5. INSPECT CRANKSHAFT THRUST CLEARANCE
(a) Using a dial indicator, measure the thrust clearance while
prying the crankshaft back and forth with a screwdriver.
Standard thrust clearance:
0.040 to 0.300 mm (0.0016 to 0.0118 in.)
If the thrust clearance is greater than maximum, replace the
thrust washer as a set.
Thrust washer thickness:
Standard2.680 to 2.730 mm (0.1055 to 0.1075 in.)
Oversize 0.1252.743 to 2.793 mm (0.1080 to 0.1100 in.)
Oversize 0.2502.805 to 2.855 mm (0.1104 to 0.1124 in.)
6. REMOVE CRANKSHAFT
(a) Uniformly loosen and remove the 10 main bearing cap
bolts.
(b) Using the removed main bearing cap bolts, wiggle the cap
back and forth, then remove the 5 main bearing caps, 5
lower bearings and 2 lower thrust washers (the No. 3 main
bearing cap only).
HINT:
SKeep the lower bearing and main bearing cap together.
SArrange the main bearing caps and lower thrust washers
in the correct order.
(c) Lift the crankshaft out.
HINT:
Keep the upper bearing and upper thrust washers together with
the cylinder block.
7. REMOVE SUB−ASSY OIL NOZZLE NO.1
(a) Remove the 4 bolts and 4 oil nozzles.
Page 4021 of 5135
A87939
6mm
Hexagon
Wrench
A87944
A09502
A09501
− ENGINE MECHANICALCYLINDER BLOCK ASSY (1CD−FTV)(From September,
2003)14−47
1CD−FTV ENGINE REPAIR MANUAL (RM1046E)
8. REMOVE CYLINDER BLOCK OIL ORIFICE
(a) Using a hexagon wrench (6 mm), remove the oil orifice.
9. REMOVE PISTON RING SET
(a) Using a piston ring expander, remove the No. 1 and No.
2 piston ring and oil ring.
NOTICE:
Try to keep the piston ring expansion as small as possible.
(b) Remove the coil by hand.
HINT:
Arrange the piston rings in the correct order.
10. REMOVE W/PIN PISTON SUB−ASSY
(a) Using a small screwdriver, pry the snap rings off the pis-
ton.
(b) Gradually heat the piston up to approximately 60_C
(140_F).
(c) Using a plastic−faced hammer and brass bar, lightly tap
out the piston pin and remove the connecting rod.
HINT:
SThe piston and pin are a matched set.
SArrange the pistons, pins, rings, connecting rods and
bearings in the correct order.
Page 4022 of 5135
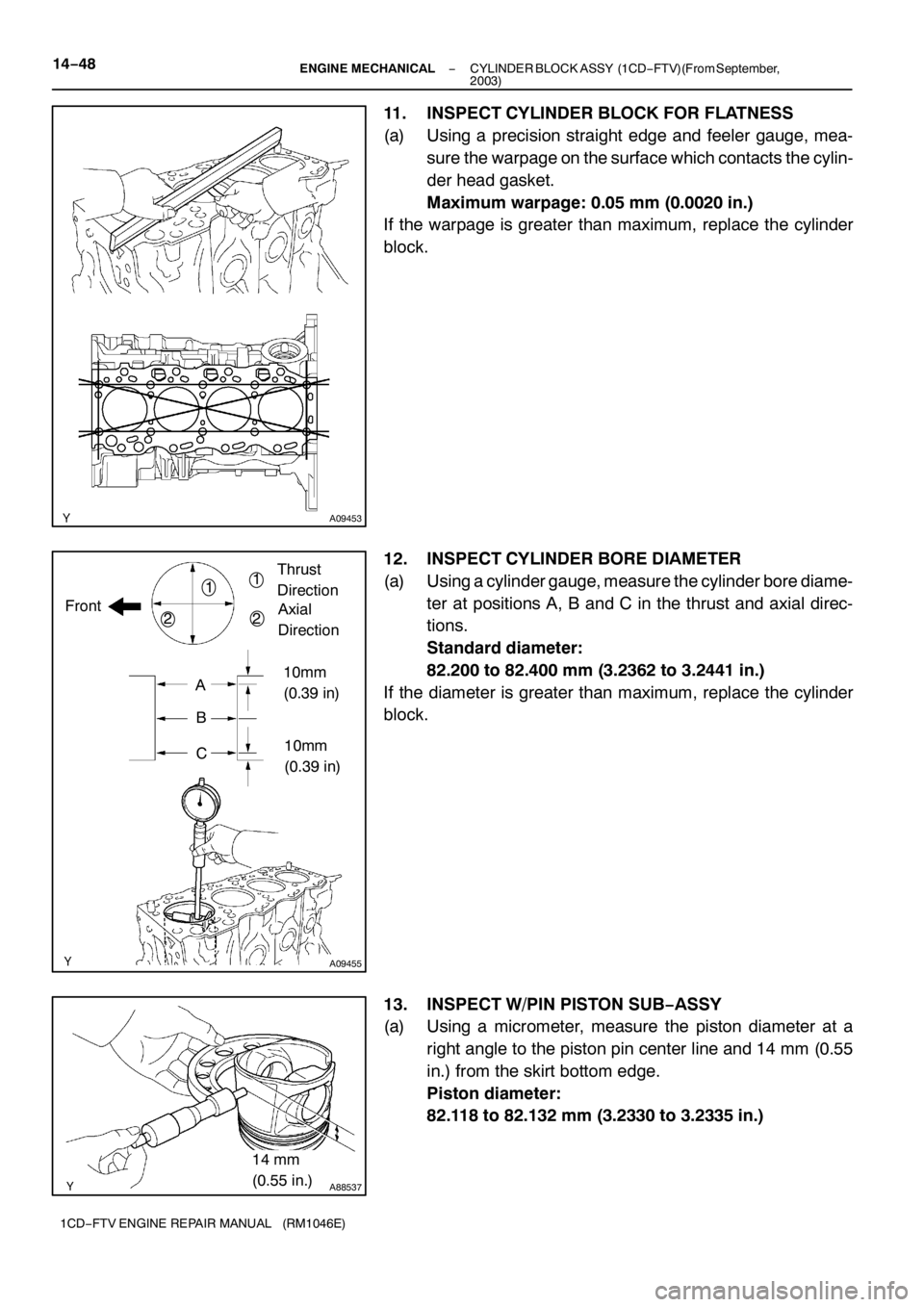
A09453
10mm
(0.39 in)
10mm
(0.39 in)
A09455
1
2 Front
Thrust
Direction
Axial
Direction1
2
A
B
C
A88537
14 mm
(0.55 in.) 14−48
− ENGINE MECHANICALCYLINDER BLOCK ASSY (1CD−FTV)(From September,
2003)
1CD−FTV ENGINE REPAIR MANUAL (RM1046E)
11. INSPECT CYLINDER BLOCK FOR FLATNESS
(a) Using a precision straight edge and feeler gauge, mea-
sure the warpage on the surface which contacts the cylin-
der head gasket.
Maximum warpage: 0.05 mm (0.0020 in.)
If the warpage is greater than maximum, replace the cylinder
block.
12. INSPECT CYLINDER BORE DIAMETER
(a) Using a cylinder gauge, measure the cylinder bore diame-
ter at positions A, B and C in the thrust and axial direc-
tions.
Standard diameter:
82.200 to 82.400 mm (3.2362 to 3.2441 in.)
If the diameter is greater than maximum, replace the cylinder
block.
13. INSPECT W/PIN PISTON SUB−ASSY
(a) Using a micrometer, measure the piston diameter at a
right angle to the piston pin center line and 14 mm (0.55
in.) from the skirt bottom edge.
Piston diameter:
82.118 to 82.132 mm (3.2330 to 3.2335 in.)
Page 4023 of 5135
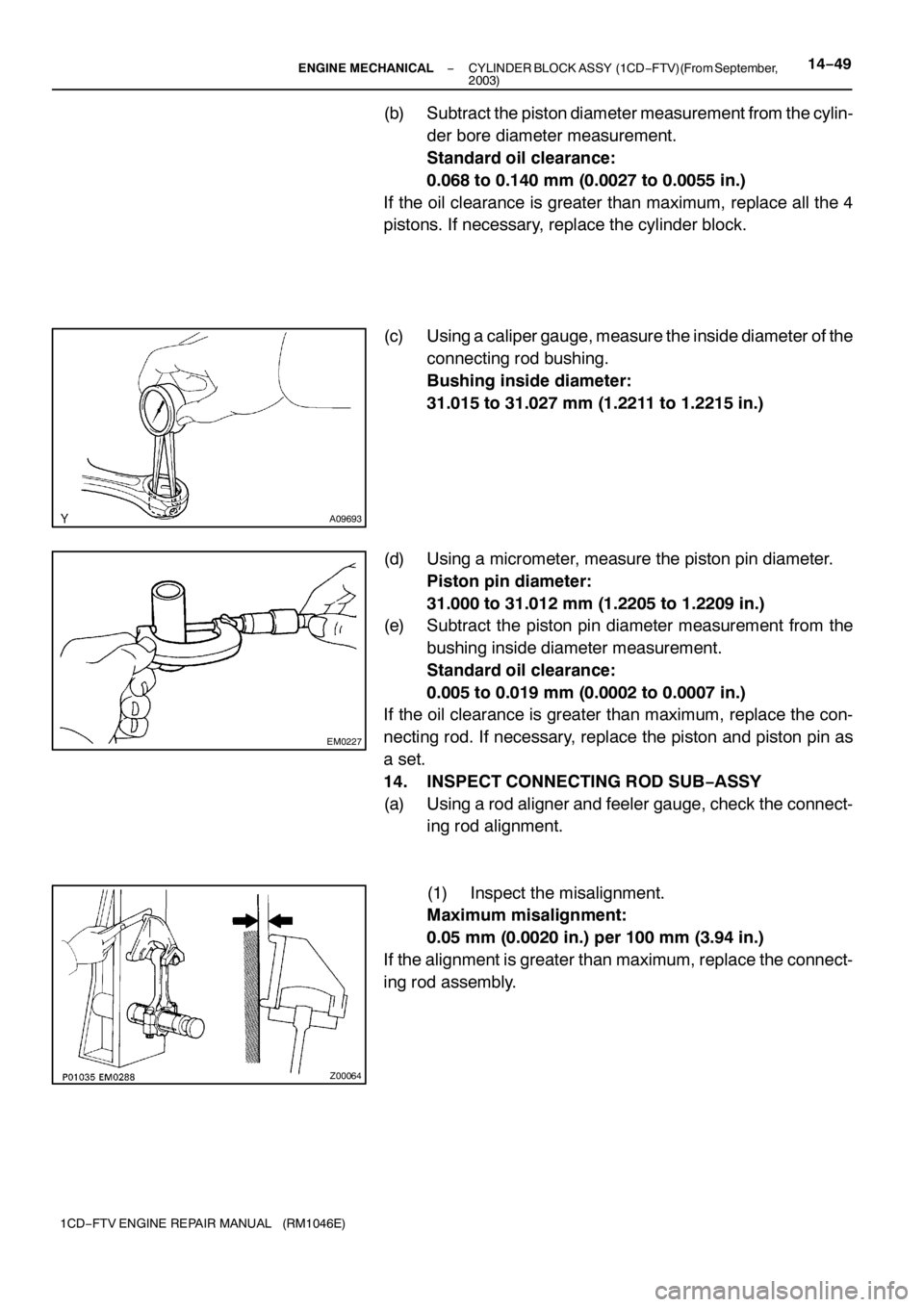
A09693
EM0227
Z00064
− ENGINE MECHANICALCYLINDER BLOCK ASSY (1CD−FTV)(From September,
2003)14−49
1CD−FTV ENGINE REPAIR MANUAL (RM1046E)
(b) Subtract the piston diameter measurement from the cylin-
der bore diameter measurement.
Standard oil clearance:
0.068 to 0.140 mm (0.0027 to 0.0055 in.)
If the oil clearance is greater than maximum, replace all the 4
pistons. If necessary, replace the cylinder block.
(c) Using a caliper gauge, measure the inside diameter of the
connecting rod bushing.
Bushing inside diameter:
31.015 to 31.027 mm (1.2211 to 1.2215 in.)
(d) Using a micrometer, measure the piston pin diameter.
Piston pin diameter:
31.000 to 31.012 mm (1.2205 to 1.2209 in.)
(e) Subtract the piston pin diameter measurement from the
bushing inside diameter measurement.
Standard oil clearance:
0.005 to 0.019 mm (0.0002 to 0.0007 in.)
If the oil clearance is greater than maximum, replace the con-
necting rod. If necessary, replace the piston and piston pin as
a set.
14. INSPECT CONNECTING ROD SUB−ASSY
(a) Using a rod aligner and feeler gauge, check the connect-
ing rod alignment.
(1) Inspect the misalignment.
Maximum misalignment:
0.05 mm (0.0020 in.) per 100 mm (3.94 in.)
If the alignment is greater than maximum, replace the connect-
ing rod assembly.
Page 4024 of 5135
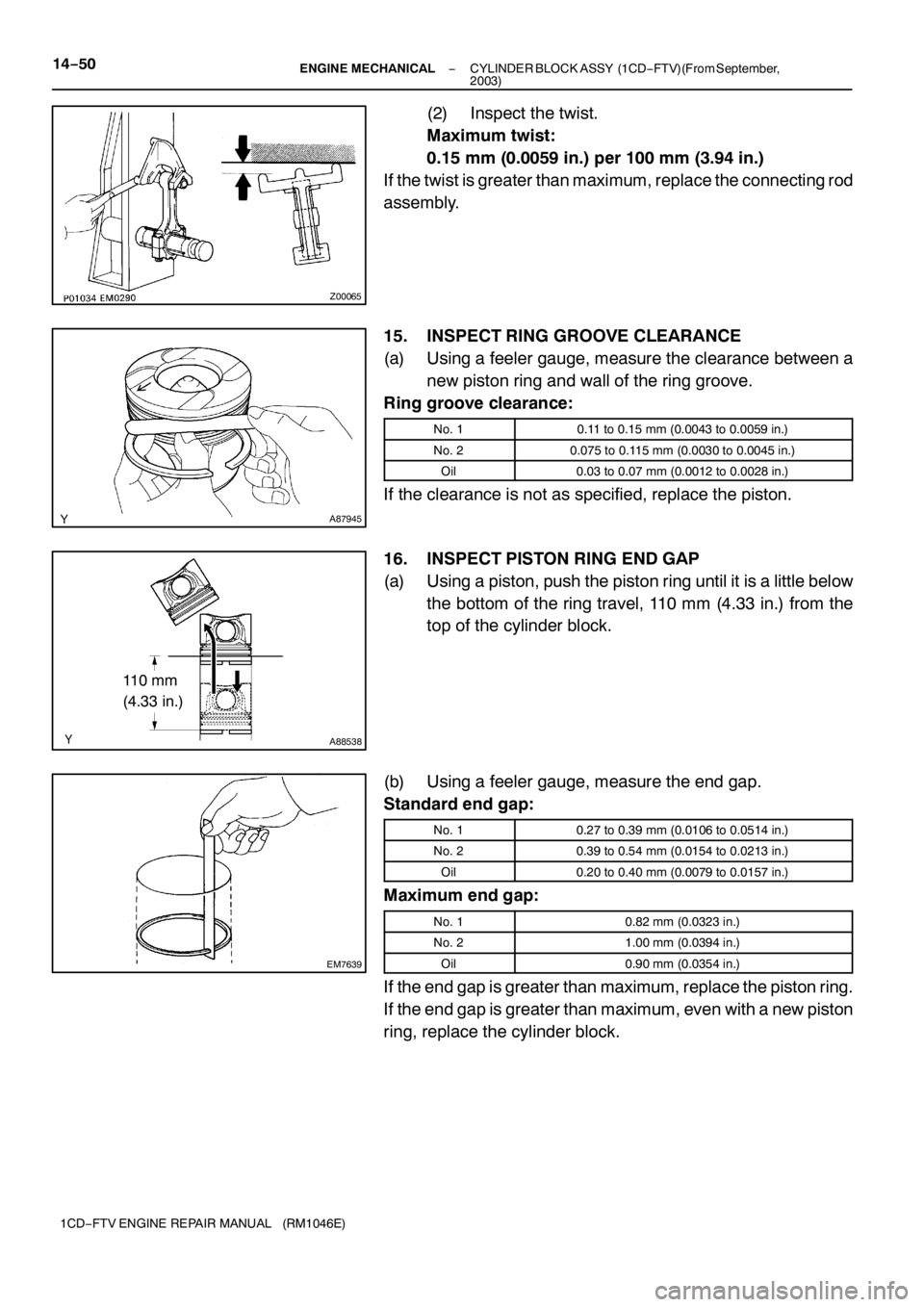
Z00065
A87945
A88538
11 0 m m
(4.33 in.)
EM7639
14−50− ENGINE MECHANICALCYLINDER BLOCK ASSY (1CD−FTV)(From September,
2003)
1CD−FTV ENGINE REPAIR MANUAL (RM1046E)
(2) Inspect the twist.
Maximum twist:
0.15 mm (0.0059 in.) per 100 mm (3.94 in.)
If the twist is greater than maximum, replace the connecting rod
assembly.
15. INSPECT RING GROOVE CLEARANCE
(a) Using a feeler gauge, measure the clearance between a
new piston ring and wall of the ring groove.
Ring groove clearance:
No. 10.11 to 0.15 mm (0.0043 to 0.0059 in.)
No. 20.075 to 0.115 mm (0.0030 to 0.0045 in.)
Oil0.03 to 0.07 mm (0.0012 to 0.0028 in.)
If the clearance is not as specified, replace the piston.
16. INSPECT PISTON RING END GAP
(a) Using a piston, push the piston ring until it is a little below
the bottom of the ring travel, 110 mm (4.33 in.) from the
top of the cylinder block.
(b) Using a feeler gauge, measure the end gap.
Standard end gap:
No. 10.27 to 0.39 mm (0.0106 to 0.0514 in.)
No. 20.39 to 0.54 mm (0.0154 to 0.0213 in.)
Oil0.20 to 0.40 mm (0.0079 to 0.0157 in.)
Maximum end gap:
No. 10.82 mm (0.0323 in.)
No. 21.00 mm (0.0394 in.)
Oil0.90 mm (0.0354 in.)
If the end gap is greater than maximum, replace the piston ring.
If the end gap is greater than maximum, even with a new piston
ring, replace the cylinder block.