Page 4201 of 5135
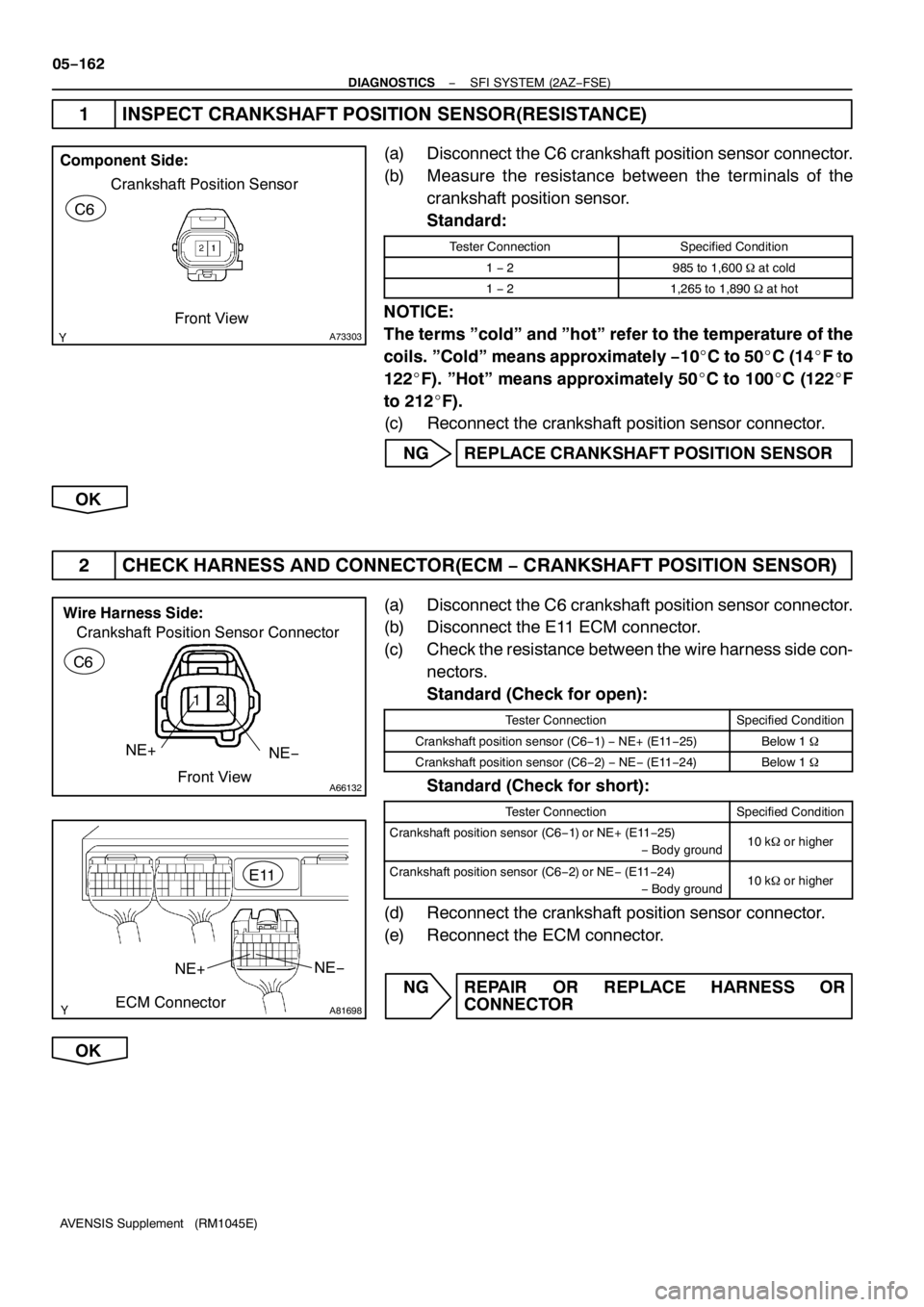
A73303
Component Side:
Front View Crankshaft Position Sensor
C6
12
A66132
Wire Harness Side:
Front View Crankshaft Position Sensor Connector
C6
NE+
NE−
A81698
NE+NE−
ECM ConnectorE11
05−162
− DIAGNOSTICSSFI SYSTEM (2AZ−FSE)
AVENSIS Supplement (RM1045E)
1INSPECT CRANKSHAFT POSITION SENSOR(RESISTANCE)
(a) Disconnect the C6 crankshaft position sensor connector.
(b) Measure the resistance between the terminals of the
crankshaft position sensor.
Standard:
Tester ConnectionSpecified Condition
1−2985 to 1,600at cold
1−21,265 to 1,890at hot
NOTICE:
The terms ”cold” and ”hot” refer to the temperature of the
coils. ”Cold” means approximately−10_Cto50_C(14_Fto
122_F). ”Hot” means approximately 50_Cto100_C(122_F
to 212_F).
(c) Reconnect the crankshaft position sensor connector.
NG REPLACE CRANKSHAFT POSITION SENSOR
OK
2 CHECK HARNESS AND CONNECTOR(ECM−CRANKSHAFT POSITION SENSOR)
(a) Disconnect the C6 crankshaft position sensor connector.
(b) Disconnect the E11 ECM connector.
(c) Check the resistance between the wire harness side con-
nectors.
Standard (Check for open):
Tester ConnectionSpecified Condition
Crankshaft position sensor (C6−1)−NE+ (E11−25)Below 1
Crankshaft position sensor (C6−2)−NE−(E11−24)Below 1
Standard (Check for short):
Tester ConnectionSpecified Condition
Crankshaft position sensor (C6−1) or NE+ (E11−25)
−Body ground10 kor higher
Crankshaft position sensor (C6−2) or NE−(E11−24)
−Body ground10 kor higher
(d) Reconnect the crankshaft position sensor connector.
(e) Reconnect the ECM connector.
NG REPAIR OR REPLACE HARNESS OR
CONNECTOR
OK
Page 4202 of 5135
− DIAGNOSTICSSFI SYSTEM (2AZ−FSE)
05−163
AVENSIS Supplement (RM1045E)
3 CHECK SENSOR INSTALLATION(CRANKSHAFT POSITION SENSOR)
(a) Check the crankshaft position sensor installation.
NG TIGHTEN SENSOR
OK
4 INSPECT CRANKSHAFT POSITION SENSOR PLATE NO.1(TOOTH OF SIGNAL
PLATE)
(a) Remove the crankshaft position sensor plate No. 1.
(b) Check the teeth of the signal plate.
NG REPLACE CRANKSHAFT POSITION SENSOR
PLATE NO.1
OK
REPLACE ECM (See page10−65 of Pub. No. RM1018E AVENSIS)
Page 4203 of 5135
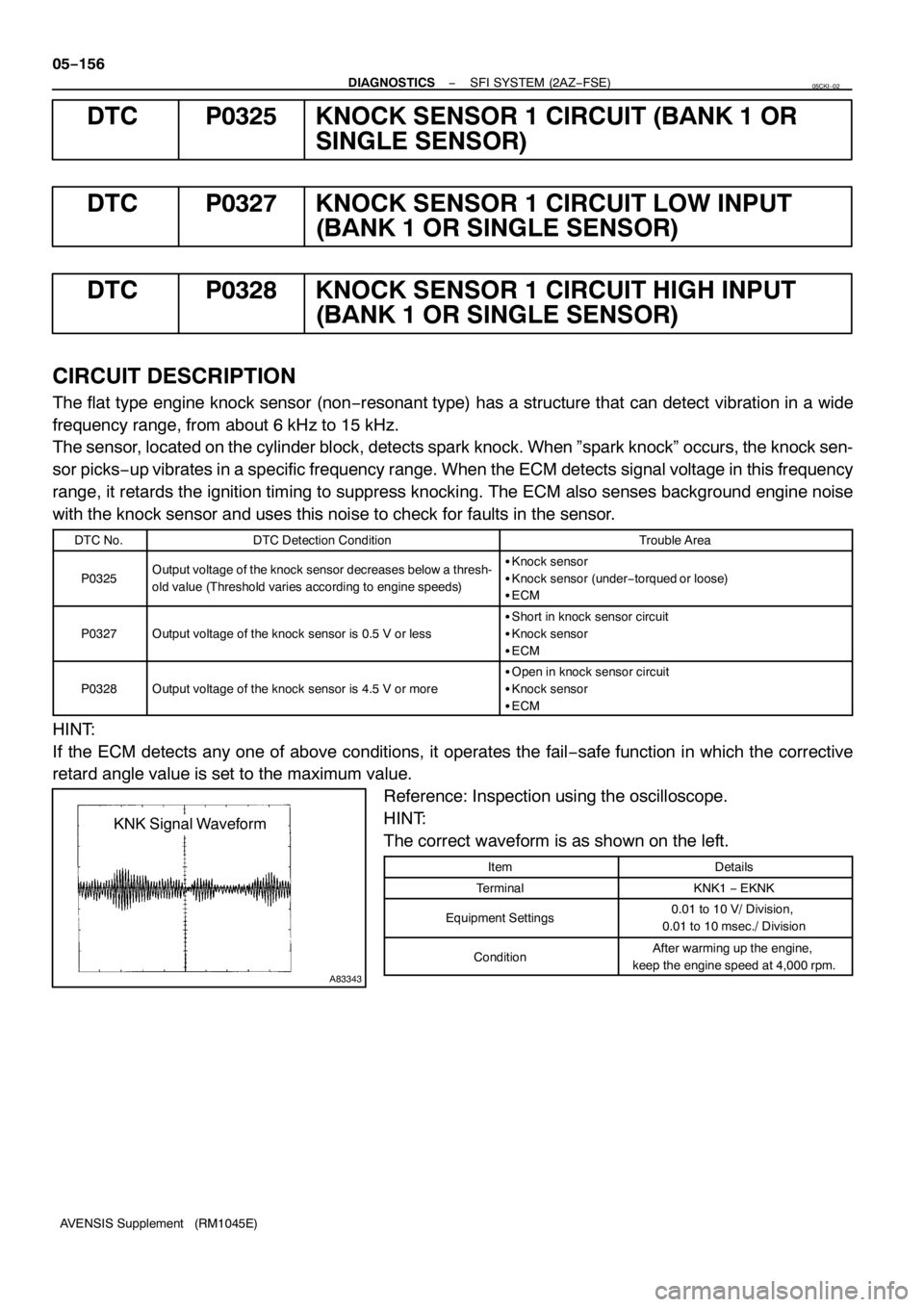
A83343
KNK Signal Waveform 05−156
− DIAGNOSTICSSFI SYSTEM (2AZ−FSE)
AVENSIS Supplement (RM1045E)
DTC P0325 KNOCK SENSOR1CIRCUIT (BANK1OR
SINGLE SENSOR)
DTC P0327 KNOCK SENSOR1CIRCUIT LOW INPUT
(BANK1OR SINGLE SENSOR)
DTC P0328 KNOCK SENSOR1CIRCUIT HIGH INPUT
(BANK1OR SINGLE SENSOR)
CIRCUIT DESCRIPTION
The flat type engine knock sensor (non−resonant type) has a structure that can detect vibration in a wide
frequency range, from about 6 kHz to15 kHz.
The sensor, located on the cylinder block, detects spark knock. When ”spark knock” occurs, the knock sen-
sor picks−up vibrates in a specific frequency range. When the ECM detects signal voltage in this frequency
range, it retards the ignition timing to suppress knocking. The ECM also senses background engine noise
with the knock sensor and uses this noise to check for faults in the sensor.
DTC No.DTC Detection ConditionTrouble Area
P0325Output voltage of the knock sensor decreases below a thresh-
old value (Threshold varies according to engine speeds)SKnock sensor
SKnock sensor (under−torqued or loose)
SECM
P0327Output voltage of the knock sensor is 0.5 V or less
SShort in knock sensor circuit
SKnock sensor
SECM
P0328Output voltage of the knock sensor is 4.5 V or more
SOpen in knock sensor circuit
SKnock sensor
SECM
HINT:
If the ECM detects any one of above conditions, it operates the fail−safe function in which the corrective
retard angle value is set to the maximum value.
Reference: Inspection using the oscilloscope.
HINT:
The correct waveform is as shown on the left.
ItemDetails
TerminalKNK1−EKNK
Equipment Settings0.01to10 V/ Division,
0.01to10 msec./ Division
ConditionAfter warming up the engine,
keep the engine speed at 4,000 rpm.
05CKI−02
Page 4204 of 5135
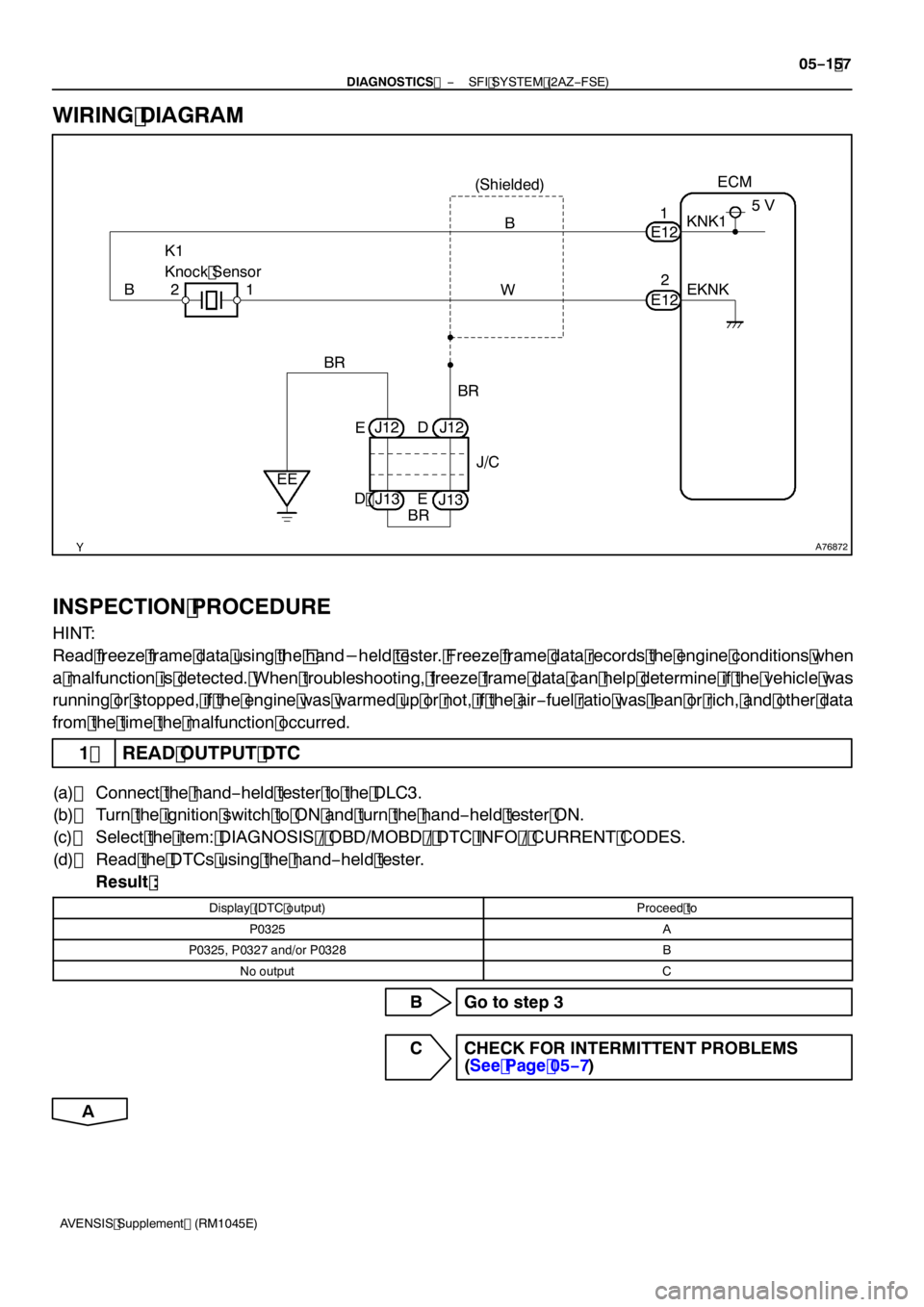
A76872
K1
Knock Sensor ECM
KNK 1
E 12
(Shielded)
1 BR D
E
J1 3 J
1 2 1
B B
J/C EKNK
E 12
2
W
2
EEJ
1 2
J1 3
D
E
BR BR 5V
−
DIAGNOSTICS SFI SYSTEM (2AZ−FSE)
05 −1 57
AVENSIS Supplement (RM 1045E)
WIRING DIAGRAM
INSPECTION PROCEDURE
HINT:
Read freeze frame data using the hand−held tester . Freeze frame data records the engine conditions when
a malfunction is detected. When troubleshooting, freeze frame data can help determine if the vehicle was
running or stopped, if the engine was warmed up or not, if the air −fuel ratio was lean or rich, and other data
from the time the malfunction occurred.
1 READ OUTPUT DTC
(a) Connect the hand −held tester to the DLC3.
(b) Turn the ignition switch to ON and turn the hand −held tester ON.
(c) Select the item: DIAGNOSIS / OBD/MOBD / DTC INFO / CURRENT CODES.
(d) Read the DTCs using the hand −held tester.
Result :
Display (DTC output)Proceed to
P0325A
P0325, P0327 and/or P0328B
No outputC
B Go to step 3
C CHECK FOR INTERMITTENT PROBLEMS (See Page 05 −7)
A
Page 4205 of 5135
A79596
A81695
KNK1 E12
ECM ConnectorEKNK
A76969
KNK1(+)EKNK (−)
E12
ECM Connector 05−158
− DIAGNOSTICSSFI SYSTEM (2AZ−FSE)
AVENSIS Supplement (RM1045E)
2 CHECK KNOCK SENSOR
(a) Check the knock sensor installation.
Torque: 20 Nm (204 kgfcm,15ftlbf)
NG TIGHTEN SENSOR
OK
REPLACE KNOCK SENSOR
3 CHECK HARNESS AND CONNECTOR(ECM−KNOCK SENSOR)
(a) Disconnect the E12 ECM connector.
(b) Check the resistance between the wire harness side con-
nector.
Standard:
Tester ConnectionSpecified Condition
KNK1(E12−1)−EKNK (E12−2)120 to 280 kat 20_C (68_F)
(c) Reconnect the ECM connector.
NG Go to step 5
OK
4 INSPECT ECM(KNK1VOLTAGE)
(a) Disconnect the E12 ECM connector.
(b) Turn the ignition switch to ON.
(c) Measure the voltage between the applicable terminals of
the ECM connector.
Standard:
Tester ConnectionSpecified Condition
KNK1(E12−1)−EKNK (E12−2)4.5 to 5.5 V
(d) Reconnect the ECM connector.
Page 4206 of 5135
A65174
Ohmmeter
−
DIAGNOSTICS SFI SYSTEM (2AZ−FSE)
05 −1 59
AVENSIS Supplement (RM 1045E)
NG REPLACE ECM (See page 10 − 65 of Pub. No.
RM 1018E AVENSIS)
OK
CHECK FOR INTERMITTENT PROBLEMS (See Page 05 −7)
NOTICE:
Fault may be intermittent. Check harness and connectors carefully and its result.
5 INSPECT KNOCK SENSOR
(a) Remove the knock sensor.
(b) Measure the resistance between the terminals. Standard: 120 to 280 k at 20 _C (68 _F)
(c) Reinstall the knock sensor. Torque: 20 N m (204 kgf cm, 15ft lbf)
NG REPLACE KNOCK SENSOR
OK
REPAIR OR REPLACE HARNESS OR CONNECTOR
Page 4207 of 5135
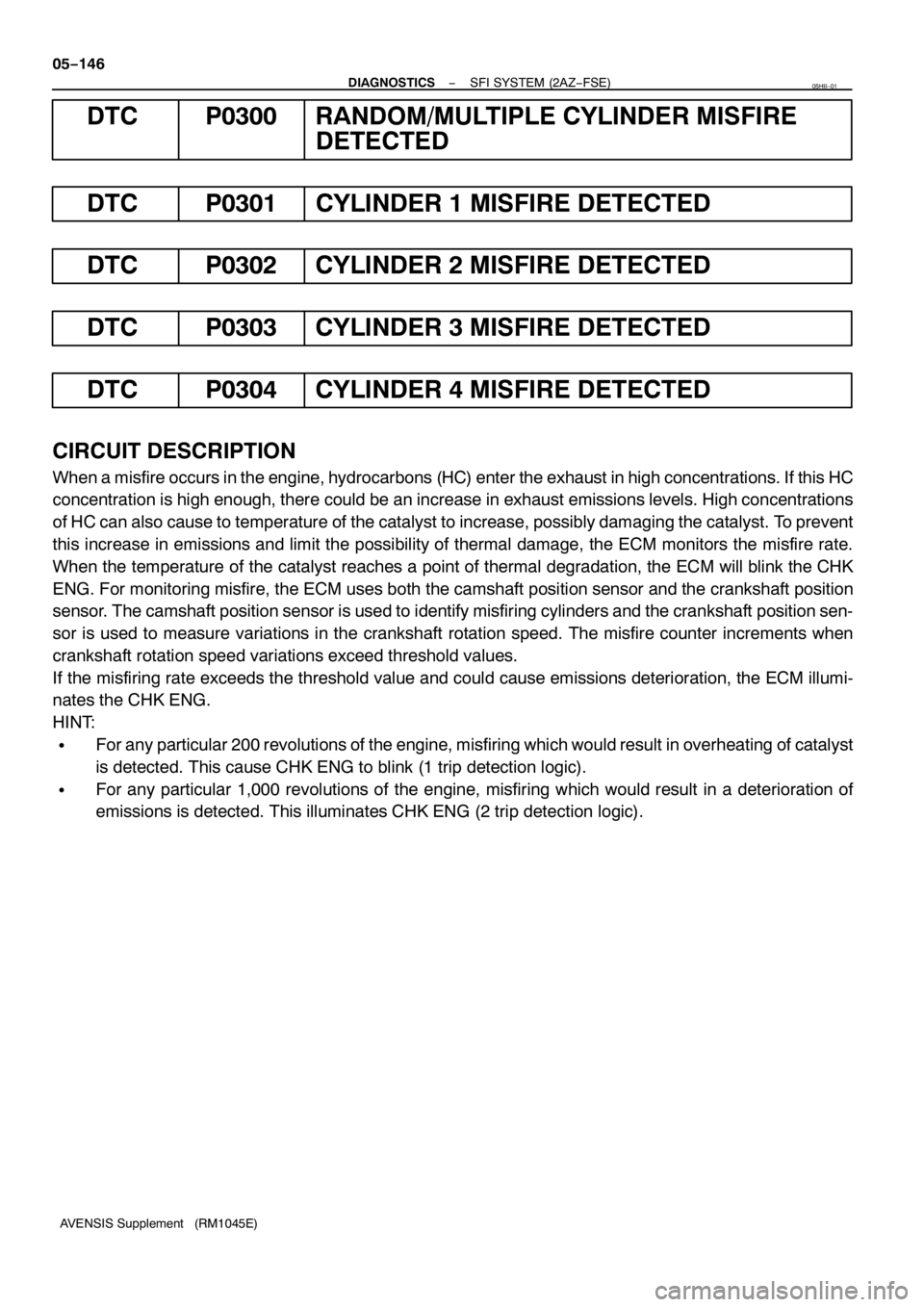
05−146
− DIAGNOSTICSSFI SYSTEM (2AZ−FSE)
AVENSIS Supplement (RM1045E)
DTC P0300 RANDOM/MULTIPLE CYLINDER MISFIRE
DETECTED
DTC P0301CYLINDER1MISFIRE DETECTED
DTC P0302 CYLINDER 2 MISFIRE DETECTED
DTC P0303 CYLINDER 3 MISFIRE DETECTED
DTC P0304 CYLINDER 4 MISFIRE DETECTED
CIRCUIT DESCRIPTION
When a misfire occurs in the engine, hydrocarbons (HC) enter the exhaust in high concentrations. If this HC
concentration is high enough, there could be an increase in exhaust emissions levels. High concentrations
of HC can also cause to temperature of the catalyst to increase, possibly damaging the catalyst. To prevent
this increase in emissions and limit the possibility of thermal damage, the ECM monitors the misfire rate.
When the temperature of the catalyst reaches a point of thermal degradation, the ECM will blink the CHK
ENG. For monitoring misfire, the ECM uses both the camshaft position sensor and the crankshaft position
sensor. The camshaft position sensor is used to identify misfiring cylinders and the crankshaft position sen-
sor is used to measure variations in the crankshaft rotation speed. The misfire counter increments when
crankshaft rotation speed variations exceed threshold values.
If the misfiring rate exceeds the threshold value and could cause emissions deterioration, the ECM illumi-
nates the CHK ENG.
HINT:
SFor any particular 200 revolutions of the engine, misfiring which would result in overheating of catalyst
is detected. This cause CHK ENG to blink (1trip detection logic).
SFor any particular1,000 revolutions of the engine, misfiring which would result in a deterioration of
emissions is detected. This illuminates CHK ENG (2 trip detection logic).
05HII−01
Page 4208 of 5135
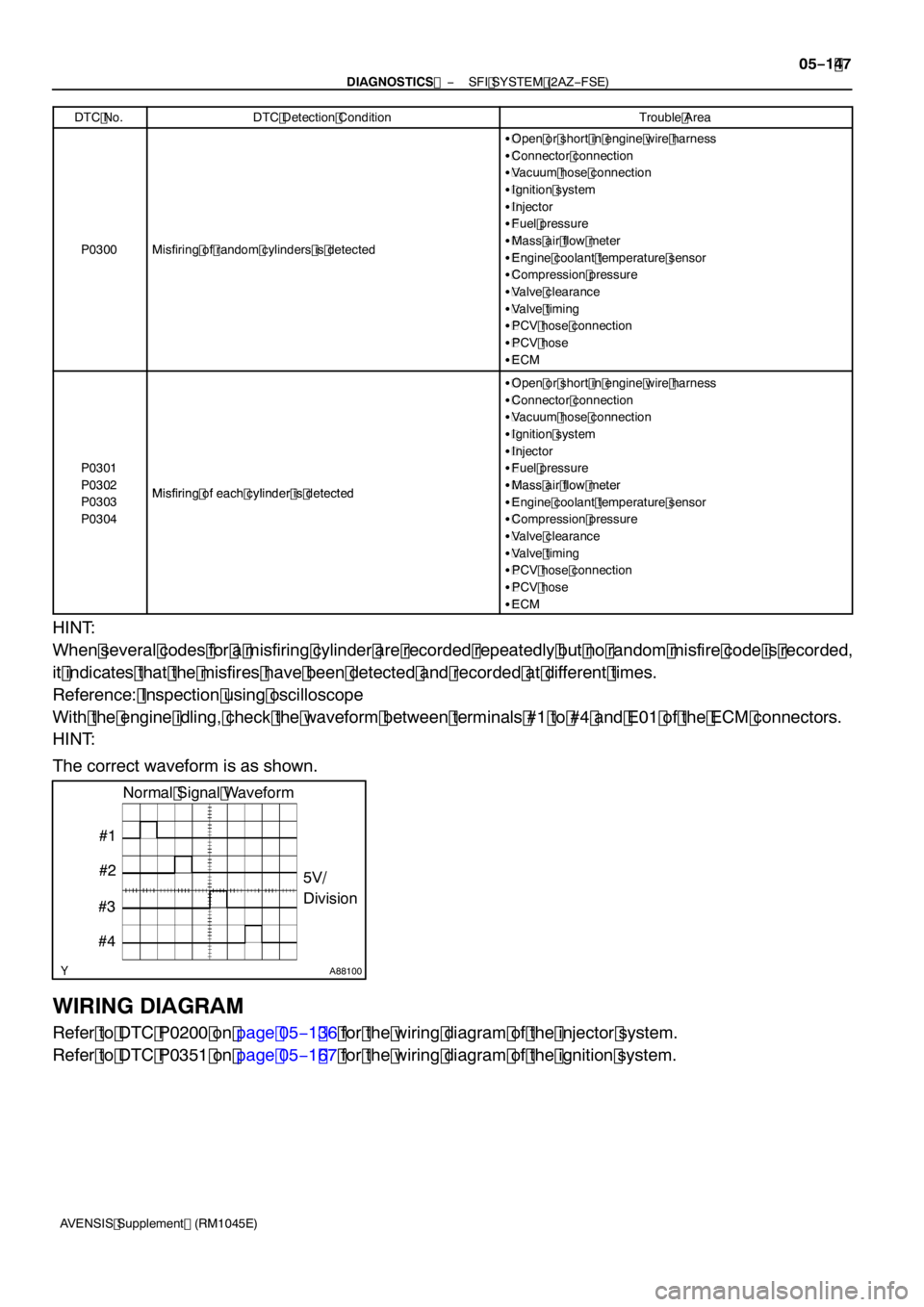
A88100
Normal Signal Waveform
5V/
Division
#
1
#2
#3
#4
−
DIAGNOSTICS SFI SYSTEM (2AZ−FSE)
05 −1 47
AVENSIS Supplement (RM 1045E)
DTC No.
DTC Detection ConditionTrouble Area
P0300Misfiring of random cylinders is detected
S
Open or short in engine wire harness
S Connector connection
S Vacuum hose connection
S Ignition system
S Injector
S Fuel pressure
S Mass air flow meter
S Engine coolant temperature sensor
S Compression pressure
S Valve clearance
S Valve timing
S PCV hose connection
S PCV hose
S ECM
P030 1
P0302
Misfiring of each cylinder is detected
S Open or short in engine wire harness
S Connector connection
S Vacuum hose connection
S Ignition system
S Injector
S Fuel pressure
S Mass air flow meter
P0302
P0303
P0304Misfiring of each cylinder is detectedMass air flow meter
S Engine coolant temperature sensor
S Compression pressure
S Valve clearance
S Valve timing
S PCV hose connection
S PCV hose
S ECM
HINT:
When several codes for a misfiring cylinder are recorded repeatedly but no random misfire code is recorded,
it indicates that the misfires have been detected and recorded at different times.
Reference: Inspection using oscilloscope
With the engine idling, check the waveform between terminals # 1 to #4 and E0 1 of the ECM connectors.
HINT:
The correct waveform is as shown.
WIRING DIAGRAM
Refer to DTC P0200 on page 05 −1 36 for the wiring diagram of the injector system.
Refer to DTC P035 1 on page 05 −1 67 for the wiring diagram of the ignition system.