Page 1801 of 5135
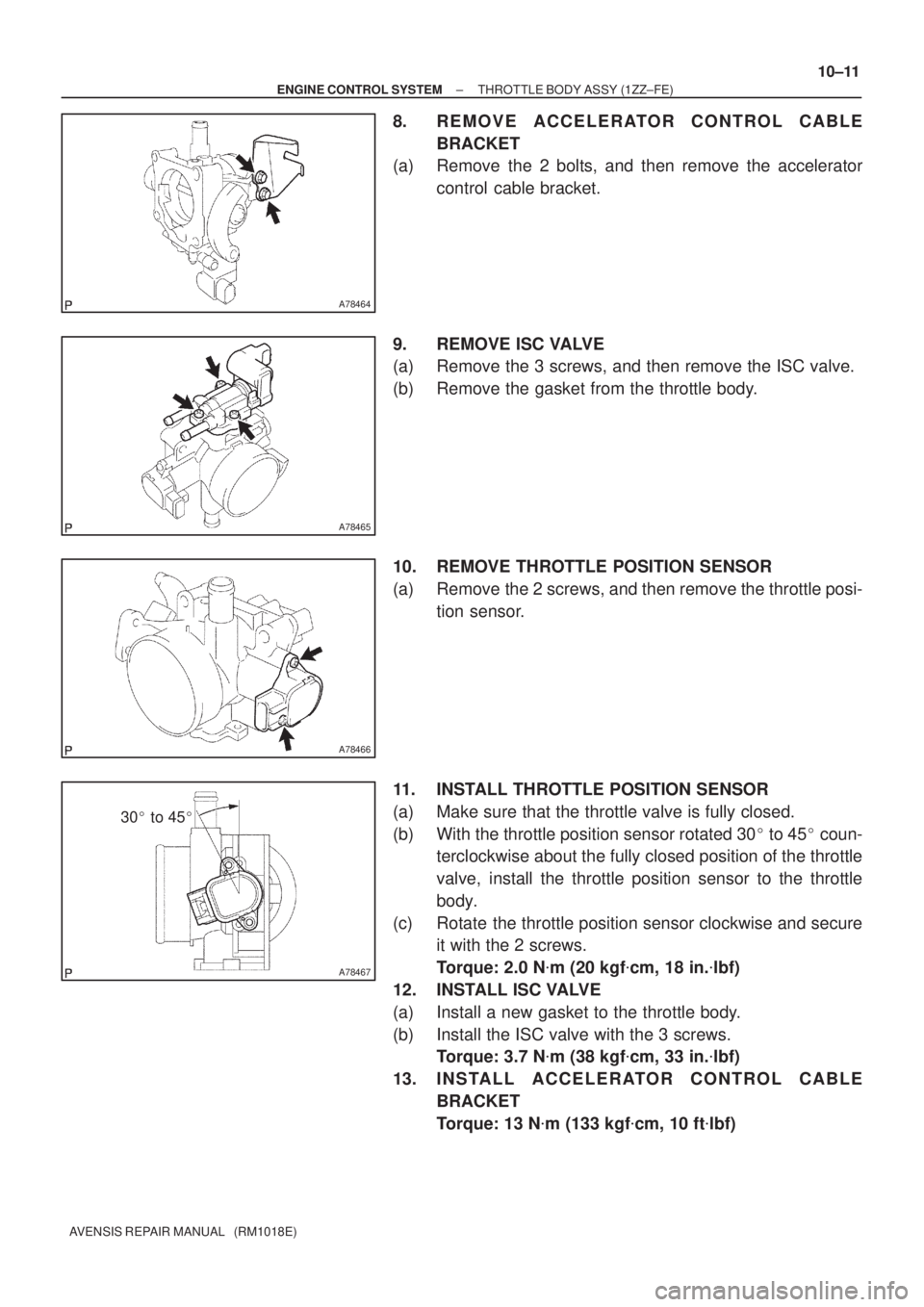
A78464
A78465
A78466
A78467
30 to 45
± ENGINE CONTROL SYSTEMTHROTTLE BODY ASSY (1ZZ±FE)
10±11
AVENSIS REPAIR MANUAL (RM1018E)
8. REMOVE ACCELERATOR CONTROL CABLE
BRACKET
(a) Remove the 2 bolts, and then remove the accelerator
control cable bracket.
9. REMOVE ISC VALVE
(a) Remove the 3 screws, and then remove the ISC valve.
(b) Remove the gasket from the throttle body.
10. REMOVE THROTTLE POSITION SENSOR
(a) Remove the 2 screws, and then remove the throttle posi-
tion sensor.
11. INSTALL THROTTLE POSITION SENSOR
(a) Make sure that the throttle valve is fully closed.
(b) With the throttle position sensor rotated 30 to 45 coun-
terclockwise about the fully closed position of the throttle
valve, install the throttle position sensor to the throttle
body.
(c) Rotate the throttle position sensor clockwise and secure
it with the 2 screws.
Torque: 2.0 Nm (20 kgfcm, 18 in.lbf)
12. INSTALL ISC VALVE
(a) Install a new gasket to the throttle body.
(b) Install the ISC valve with the 3 screws.
Torque: 3.7 Nm (38 kgfcm, 33 in.lbf)
13. INSTALL ACCELERATOR CONTROL CABLE
BRACKET
Torque: 13 Nm (133 kgfcm, 10 ftlbf)
Page 1802 of 5135
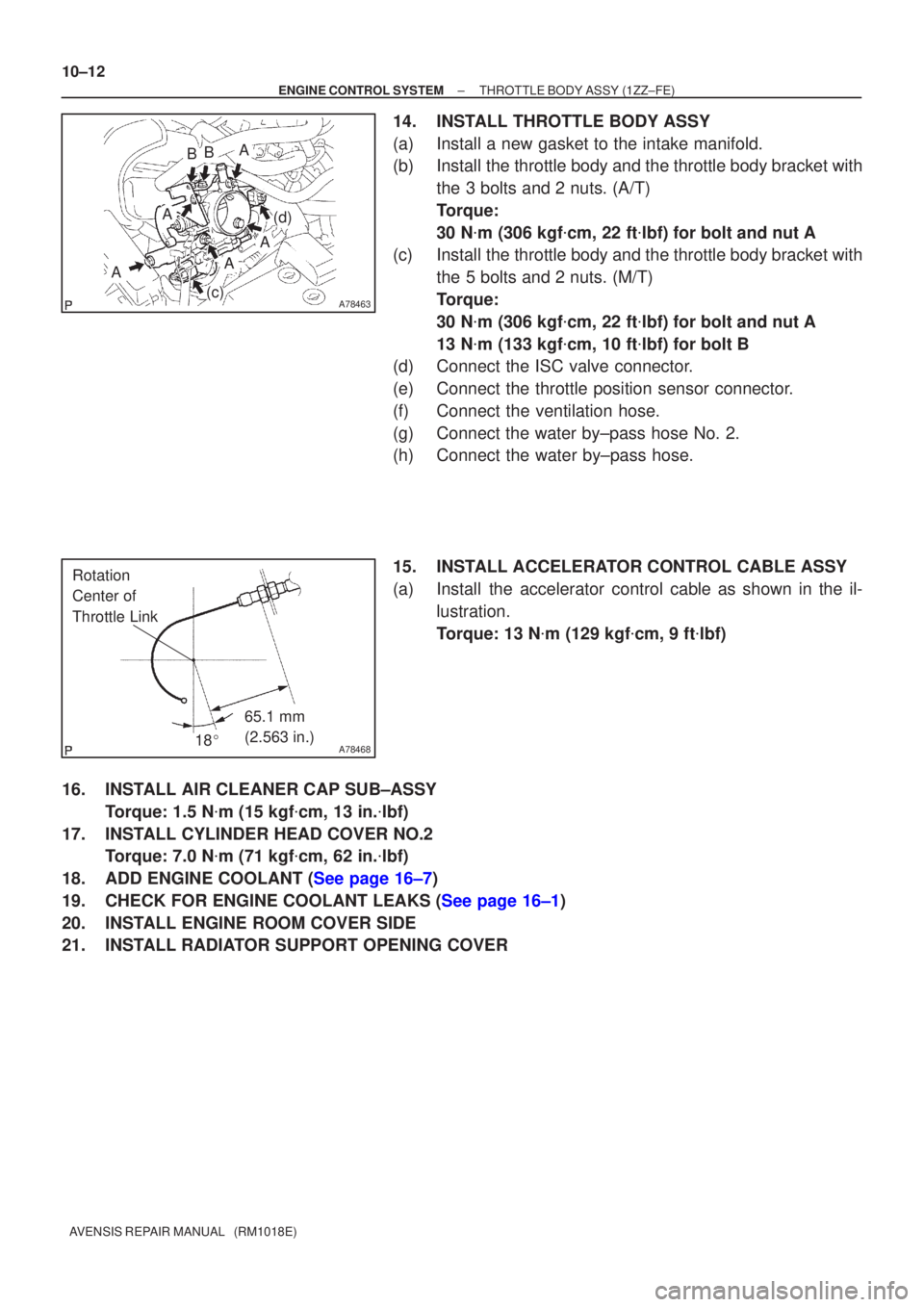
A78463
A
A
A
A
BB
A
(d)
(c)
A78468
65.1 mm
(2.563 in.)
Rotation
Center of
Throttle Link
18
10±12
±
ENGINE CONTROL SYSTEM THROTTLE BODY ASSY(1ZZ±FE)
AVENSIS REPAIR MANUAL (RM1018E)
14.INSTALL THROTTLE BODY ASSY
(a)Install a new gasket to the intake manifold.
(b)Install the throttle body and the throttle body bracket with the 3 bolts and 2 nuts. (A/T)
Torque:
30 Nm (306 kgf cm, 22 ft lbf) for bolt and nut A
(c)Install the throttle body and the throttle body bracket with
the 5 bolts and 2 nuts. (M/T)
Torque:
30 Nm (306 kgf cm, 22 ft lbf) for bolt and nut A
13 N m (133 kgf cm, 10 ft lbf) for bolt B
(d)Connect the ISC valve connector.
(e)Connect the throttle position sensor connector.
(f)Connect the ventilation hose.
(g)Connect the water by±pass hose No. 2.
(h)Connect the water by±pass hose.
15.INSTALL ACCELERATOR CONTROL CABLE ASSY
(a)Install the accelerator control cable as shown in the il-
lustration.
Torque: 13 N m (129 kgf cm, 9 ft lbf)
16.INSTALL AIR CLEANER CAP SUB±ASSY Torque: 1.5 N m (15 kgf cm, 13 in. lbf)
17.INSTALL CYLINDER HEAD COVER NO.2 Torque: 7.0 N m (71 kgf cm, 62 in. lbf)
18.ADD ENGINE COOLANT (See page 16±7)
19.CHECK FOR ENGINE COOLANT LEAKS (See page 16±1)
20. INSTALL ENGINE ROOM COVER SIDE
21. INSTALL RADIATOR SUPPORT OPENING COVER
Page 1803 of 5135
100FB±01
A78454
N´m (kgf´cm, ft´lbf) : Specified torqueClip
Cylinder Head Cover No.2
Fuel
Vapor Feed Hose No.1
VSV
Connector
Mass Air Flow
Meter Connector Accelerator Control
Cable Assy
Fuel Vapor Feed Hose
No.3 Engine Room Cover Side
Radiator Support Opening Cover
Clip
Retainer
7.0 (71, 62 in.´lbf)
Clip
1.5 (15, 13 in.´lbf)
13 (129, 9)
Air Cleaner Cap
Sub±assy
x2
x4
± ENGINE CONTROL SYSTEMTHROTTLE BODY ASSY (1ZZ±FE)
10±7
AVENSIS REPAIR MANUAL (RM1018E)
THROTTLE BODY ASSY (1ZZ±FE)
COMPONENTS
Page 1804 of 5135
A78455
Throttle Body Gasket
Non±reusable part
N´m (kgf´cm, ft´lbf) : Specified torqueISC Valve Throttle Body Cover Gasket Accelerator
Control Cable BracketThrottle Position
SensorWater By±pass
Hose Water By±pass
Hose No.2
Throttle Body Bracket ISC Valve ConnectorThrottle Body Assy
M/T:
Manifold Stay No.2Ventilation Hose
Throttle Position
Sensor Connector
13 (133, 10)
30 (306, 22)
30 (306, 22)
3.7 (38, 33 in.´lbf)
2.0 (20, 18 in.´lbf)
13 (133, 10)
x3 x2x2 x2 10±8
± ENGINE CONTROL SYSTEMTHROTTLE BODY ASSY (1ZZ±FE)
AVENSIS REPAIR MANUAL (RM1018E)
Page 1805 of 5135
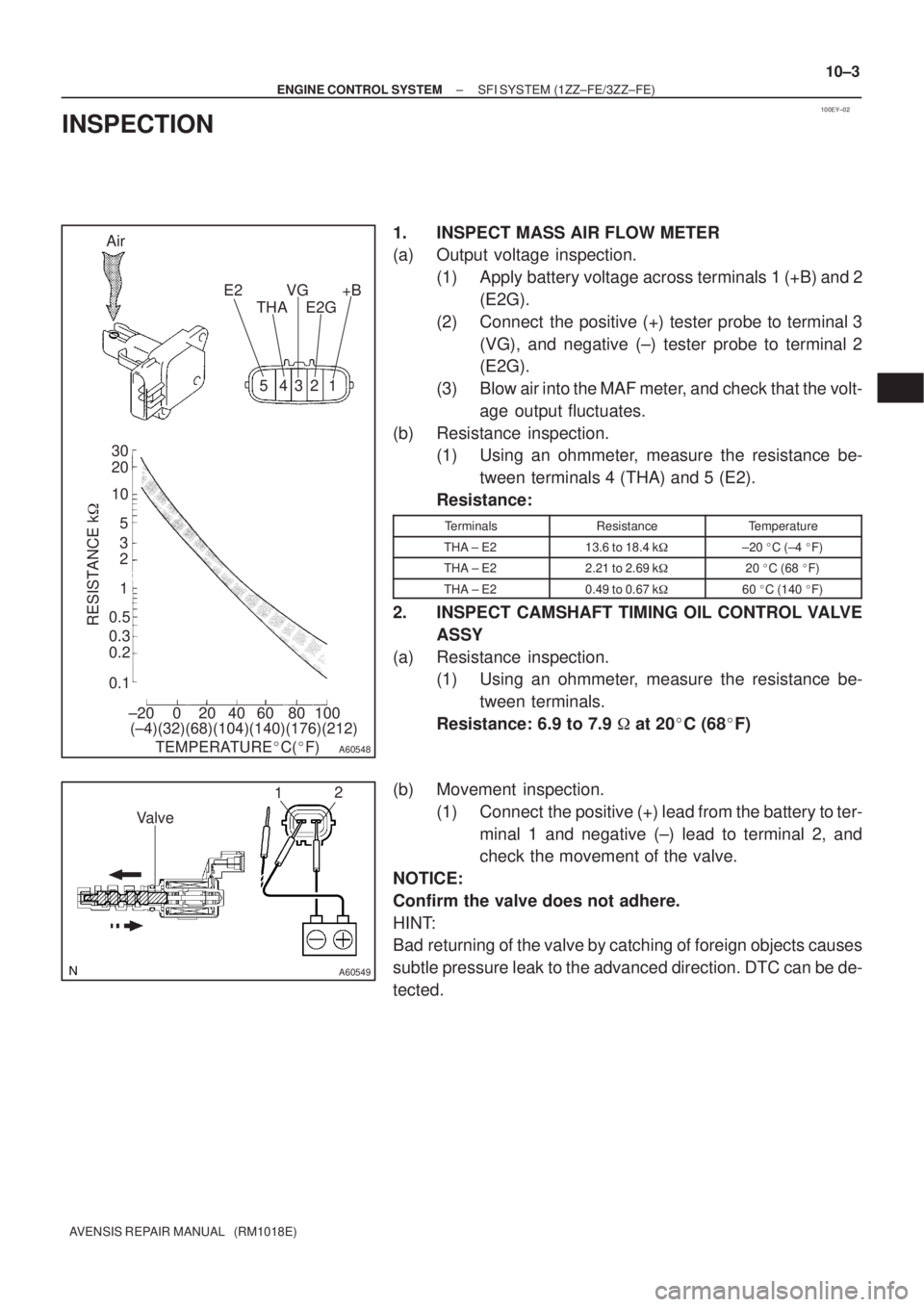
100EY±02
A60548
Air
E2
THAVG
E2G+B
30
20
10
5
3
2
1
0.5
0.3
0.2
0.1
RESISTANCE k
±20 0 20 40 60 80 10054321
(±4)(32)(68)(104)(140)(176)(212)
TEMPERATUREC(F)
A60549
12
Valve
± ENGINE CONTROL SYSTEMSFI SYSTEM (1ZZ±FE/3ZZ±FE)
10±3
AVENSIS REPAIR MANUAL (RM1018E)
INSPECTION
1. INSPECT MASS AIR FLOW METER
(a) Output voltage inspection.
(1) Apply battery voltage across terminals 1 (+B) and 2
(E2G).
(2) Connect the positive (+) tester probe to terminal 3
(VG), and negative (±) tester probe to terminal 2
(E2G).
(3) Blow air into the MAF meter, and check that the volt-
age output fluctuates.
(b) Resistance inspection.
(1) Using an ohmmeter, measure the resistance be-
tween terminals 4 (THA) and 5 (E2).
Resistance:
TerminalsResistanceTemperature
THA ± E213.6 to 18.4 k±20 C (±4 F)
THA ± E22.21 to 2.69 k20 C (68 F)
THA ± E20.49 to 0.67 k60 C (140 F)
2. INSPECT CAMSHAFT TIMING OIL CONTROL VALVE
ASSY
(a) Resistance inspection.
(1) Using an ohmmeter, measure the resistance be-
tween terminals.
Resistance: 6.9 to 7.9 at 20C (68F)
(b) Movement inspection.
(1) Connect the positive (+) lead from the battery to ter-
minal 1 and negative (±) lead to terminal 2, and
check the movement of the valve.
NOTICE:
Confirm the valve does not adhere.
HINT:
Bad returning of the valve by catching of foreign objects causes
subtle pressure leak to the advanced direction. DTC can be de-
tected.
Page 1806 of 5135
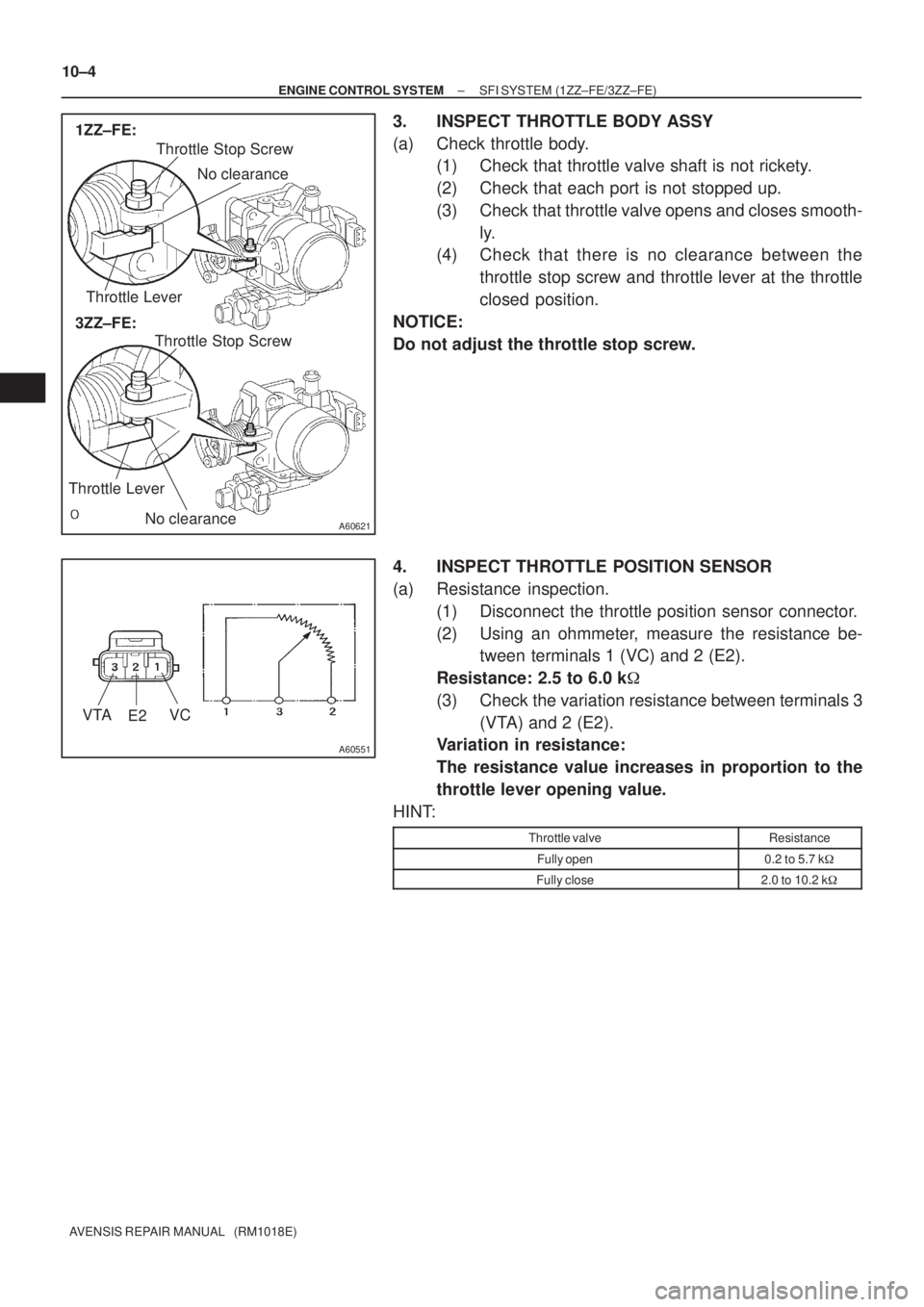
A60621
3ZZ±FE: 1ZZ±FE:
Throttle Stop Screw
Throttle Lever
Throttle Stop Screw
Throttle Lever
No clearance
No clearance
A60551
VTA
E2VC
10±4
± ENGINE CONTROL SYSTEMSFI SYSTEM (1ZZ±FE/3ZZ±FE)
AVENSIS REPAIR MANUAL (RM1018E)
3. INSPECT THROTTLE BODY ASSY
(a) Check throttle body.
(1) Check that throttle valve shaft is not rickety.
(2) Check that each port is not stopped up.
(3) Check that throttle valve opens and closes smooth-
ly.
(4) Check that there is no clearance between the
throttle stop screw and throttle lever at the throttle
closed position.
NOTICE:
Do not adjust the throttle stop screw.
4. INSPECT THROTTLE POSITION SENSOR
(a) Resistance inspection.
(1) Disconnect the throttle position sensor connector.
(2) Using an ohmmeter, measure the resistance be-
tween terminals 1 (VC) and 2 (E2).
Resistance: 2.5 to 6.0 k
(3) Check the variation resistance between terminals 3
(VTA) and 2 (E2).
Variation in resistance:
The resistance value increases in proportion to the
throttle lever opening value.
HINT:
Throttle valveResistance
Fully open0.2 to 5.7 k
Fully close2.0 to 10.2 k
Page 1807 of 5135
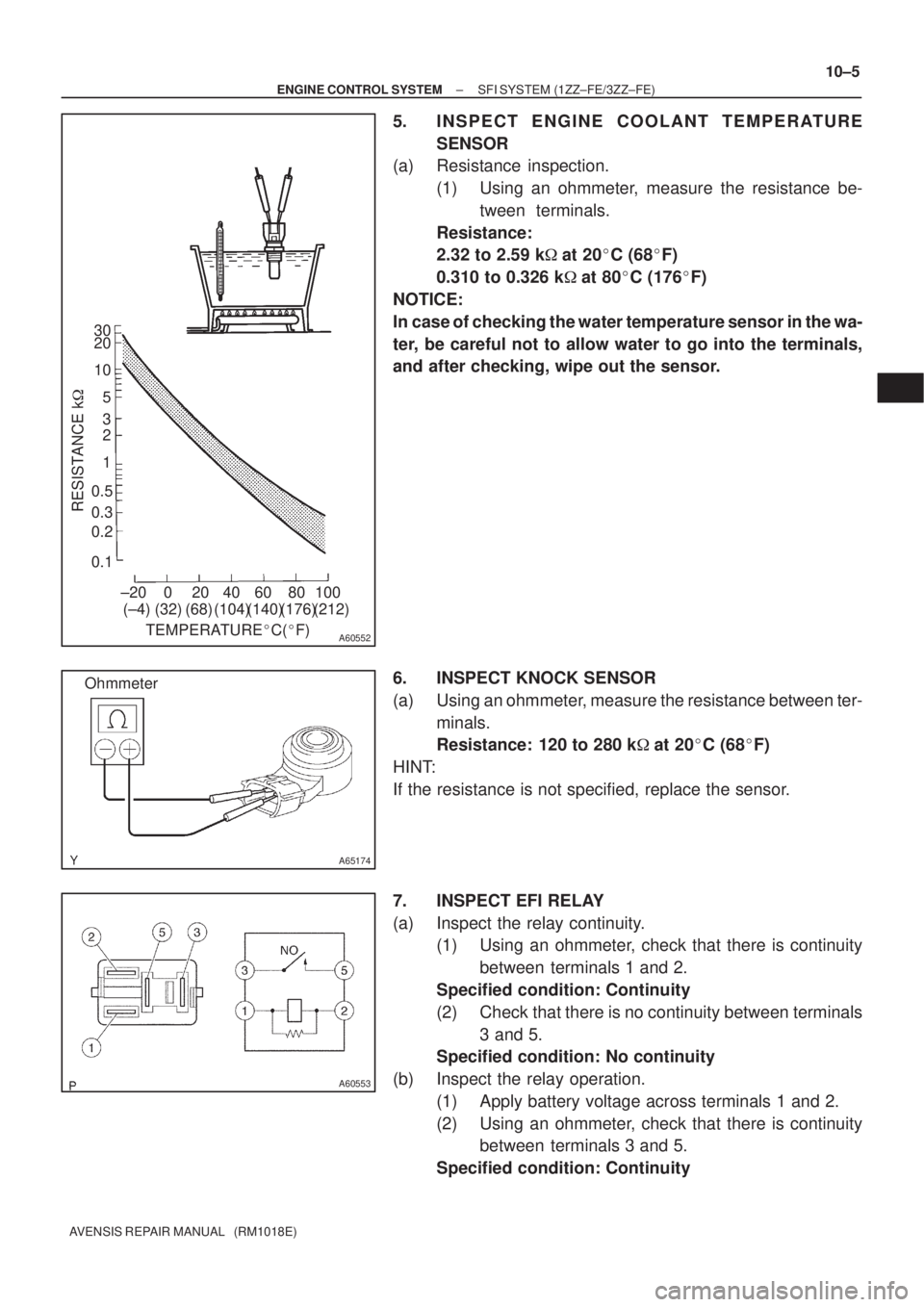
A60552
30
20
10
5
3
2
1
0.5
0.3
0.2
0.1
RESISTANCE k
±20 0 20 40 60 80 100
(±4)
TEMPERATUREC(F) (32) (68) (104)(140)(176)(212)
A65174
Ohmmeter
A60553
± ENGINE CONTROL SYSTEMSFI SYSTEM (1ZZ±FE/3ZZ±FE)
10±5
AVENSIS REPAIR MANUAL (RM1018E)
5. INSPECT ENGINE COOLANT TEMPERATURE
SENSOR
(a) Resistance inspection.
(1) Using an ohmmeter, measure the resistance be-
tween terminals.
Resistance:
2.32 to 2.59 kat 20C (68F)
0.310 to 0.326 kat 80C (176F)
NOTICE:
In case of checking the water temperature sensor in the wa-
ter, be careful not to allow water to go into the terminals,
and after checking, wipe out the sensor.
6. INSPECT KNOCK SENSOR
(a) Using an ohmmeter, measure the resistance between ter-
minals.
Resistance: 120 to 280 kat 20C (68F)
HINT:
If the resistance is not specified, replace the sensor.
7. INSPECT EFI RELAY
(a) Inspect the relay continuity.
(1) Using an ohmmeter, check that there is continuity
between terminals 1 and 2.
Specified condition: Continuity
(2) Check that there is no continuity between terminals
3 and 5.
Specified condition: No continuity
(b) Inspect the relay operation.
(1) Apply battery voltage across terminals 1 and 2.
(2) Using an ohmmeter, check that there is continuity
between terminals 3 and 5.
Specified condition: Continuity
Page 1808 of 5135
A60553
10±6
± ENGINE CONTROL SYSTEMSFI SYSTEM (1ZZ±FE/3ZZ±FE)
AVENSIS REPAIR MANUAL (RM1018E)
8. INSPECT CIRCUIT OPENING RELAY
(a) Inspect the relay continuity.
(1) Using an ohmmeter, check that there is continuity
between terminals 1 and 2.
Specified condition: Continuity
(2) Check that there is no continuity between terminals
3 and 5.
Specified condition: No continuity
(b) Inspect the relay operation.
(1) Apply battery voltage across terminals 1 and 2.
(2) Using an ohmmeter, check that there is continuity
between terminals 3 and 5.
Specified condition: Continuity