Page 2553 of 5135
F45575Non±reusable parts Front Axle Outboard Joint Boot RH No.2 Clamp
Drive Shaft Outboard Joint Boot
Front Axle Out board Joint Boot RH Clamp
Drive Shaft DamperFront Axle Inboard Joint Boot RH Clamp
Drive Shaft Inboard Joint Boot
Front Axle Inboard Joint
Boot RH No.2 Clamp
Front Drive Outboard Joint Shaft Assy RH
RH:
3ZZ±FE/
1ZZ±FE:1AZ±FSE/
1AZ±FE/
1CD±FTV:
Front Drive Inboard
Joint Assy RH
Front Drive Shaft
Dust Cover RHTripod Joint Assy
Front Drive Inner
Shaft Inner RH
Shaft Snap Ring Drive Shaft Bearing
Case Snap Ring
Front Drive Shaft Bearing
Straight Pin
Drive Shaft Bearing Case
Front Drive Shaft
Hole Snap Ring
Front Drive Shaft
Dust Cover
Front Drive Shaft
Dust Cover RH
3ZZ±FE/
1ZZ±FE:
1AZ±FSE/
1AZ±FE/
1CD±FTV:
Front Drive Inboard
Joint Assy RH
± DRIVE SHAFT / PROPELLER SHAFTFRONT DRIVE SHAFT
30±5
AVENSIS REPAIR MANUAL (RM1018E)
Page 2554 of 5135
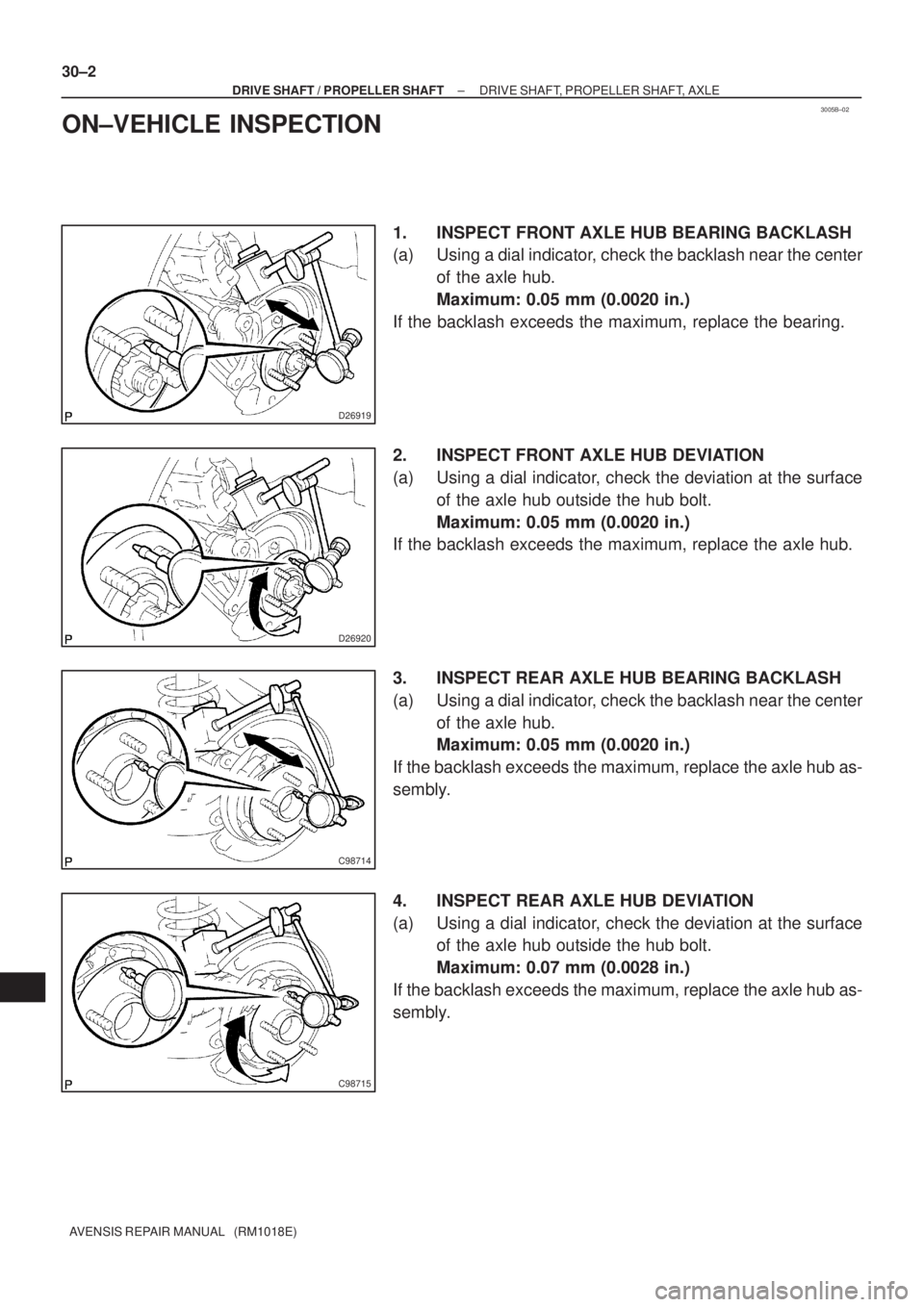
3005B±02
D26919
D26920
C98714
C98715
30±2
± DRIVE SHAFT / PROPELLER SHAFTDRIVE SHAFT, PROPELLER SHAFT, AXLE
AVENSIS REPAIR MANUAL (RM1018E)
ON±VEHICLE INSPECTION
1. INSPECT FRONT AXLE HUB BEARING BACKLASH
(a) Using a dial indicator, check the backlash near the center
of the axle hub.
Maximum: 0.05 mm (0.0020 in.)
If the backlash exceeds the maximum, replace the bearing.
2. INSPECT FRONT AXLE HUB DEVIATION
(a) Using a dial indicator, check the deviation at the surface
of the axle hub outside the hub bolt.
Maximum: 0.05 mm (0.0020 in.)
If the backlash exceeds the maximum, replace the axle hub.
3. INSPECT REAR AXLE HUB BEARING BACKLASH
(a) Using a dial indicator, check the backlash near the center
of the axle hub.
Maximum: 0.05 mm (0.0020 in.)
If the backlash exceeds the maximum, replace the axle hub as-
sembly.
4. INSPECT REAR AXLE HUB DEVIATION
(a) Using a dial indicator, check the deviation at the surface
of the axle hub outside the hub bolt.
Maximum: 0.07 mm (0.0028 in.)
If the backlash exceeds the maximum, replace the axle hub as-
sembly.
Page 2555 of 5135
3005C±02
±
DRIVE SHAFT / PROPELLER SHAFT DRIVE SHAFT, PROPELLER SHAFT, AXLE
30±1
AVENSIS REPAIR MANUAL (RM1018E)
DRIVE SHAFT, PROPELLER SHAFT, AXLE
PROBLEM SYMPTOMS TABLE
Use the table below to help you find the cause of the problem. The numbers \
indicate the priority of
the likely cause of the problem. Check each part in order. If necessary, replace these parts.
SymptomSuspect AreaSee page
Wander
5. Wheel
6. Front wheel alignment
7. Rear wheel alignment
8. Hub bearing (Worn)
9. Front shock absorber
10.Rear shock absorber28±1
26±6
27±4
30±2
26±10
27±8
Front wheel shimmy
1. Wheel (Imbalance)
2. Hub bearing (Worn)
3. Lower suspension arm ATM:
4. Lower suspension arm MTM:
5. Lower ball joint (Worm)
6. Front shock absorber28±1
30±2
26±16
26±21
26±24
26±10
Noise (Front)
1. Front drive shaft
2. Front shock absorber
3. Hub bearing (Worn)
4. Lower ball joint (Worm)30±6
26±10 30±2
26±24
Noise (Rear)1. Hub bearing (Worn)
2. Rear shock absorber30±2
27±8
Page 2556 of 5135
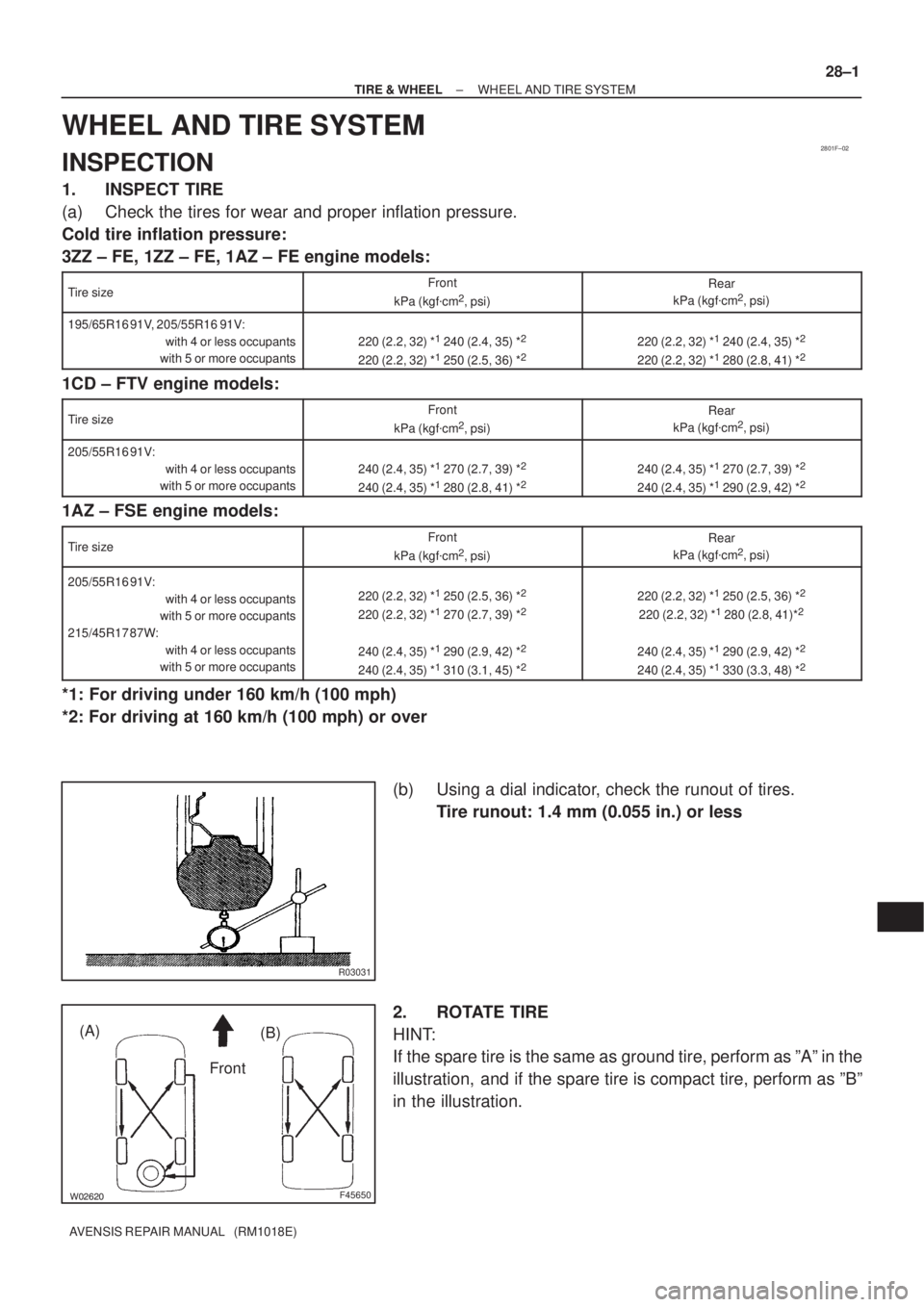
2801F±02
R03031
F45650
Front (A)
(B)
± TIRE & WHEELWHEEL AND TIRE SYSTEM
28±1
AVENSIS REPAIR MANUAL (RM1018E)
WHEEL AND TIRE SYSTEM
INSPECTION
1. INSPECT TIRE
(a) Check the tires for wear and proper inflation pressure.
Cold tire inflation pressure:
3ZZ ± FE, 1ZZ ± FE, 1AZ ± FE engine models:
Tire sizeFront
kPa (kgfcm2, psi)
Rear
kPa (kgfcm2, psi)
195/65R16 91V, 205/55R16 91V:
with 4 or less occupants
with 5 or more occupants
220 (2.2, 32) *1 240 (2.4, 35) *2
220 (2.2, 32) *1 250 (2.5, 36) *2220 (2.2, 32) *1 240 (2.4, 35) *2
220 (2.2, 32) *1 280 (2.8, 41) *2
1CD ± FTV engine models:
Tire sizeFront
kPa (kgfcm2, psi)
Rear
kPa (kgfcm2, psi)
205/55R16 91V:
with 4 or less occupants
with 5 or more occupants
240 (2.4, 35) *1 270 (2.7, 39) *2
240 (2.4, 35) *1 280 (2.8, 41) *2240 (2.4, 35) *1 270 (2.7, 39) *2
240 (2.4, 35) *1 290 (2.9, 42) *2
1AZ ± FSE engine models:
Tire sizeFront
kPa (kgfcm2, psi)
Rear
kPa (kgfcm2, psi)
205/55R16 91V:
with 4 or less occupants
with 5 or more occupants
215/45R17 87W:
with 4 or less occupants
with 5 or more occupants220 (2.2, 32) *1 250 (2.5, 36) *2
220 (2.2, 32) *1 270 (2.7, 39) *2
240 (2.4, 35) *1 290 (2.9, 42) *2
240 (2.4, 35) *1 310 (3.1, 45) *2
220 (2.2, 32) *1 250 (2.5, 36) *2
220 (2.2, 32) *1 280 (2.8, 41)*2
240 (2.4, 35) *1 290 (2.9, 42) *2
240 (2.4, 35) *1 330 (3.3, 48) *2
*1: For driving under 160 km/h (100 mph)
*2: For driving at 160 km/h (100 mph) or over
(b) Using a dial indicator, check the runout of tires.
Tire runout: 1.4 mm (0.055 in.) or less
2. ROTATE TIRE
HINT:
If the spare tire is the same as ground tire, perform as ºAº in the
illustration, and if the spare tire is compact tire, perform as ºBº
in the illustration.
Page 2557 of 5135
C80976
28±2
±
TIRE & WHEEL WHEEL AND TIRE SYSTEM
AVENSIS REPAIR MANUAL (RM1018E)
3. INSPECT WHEEL BALANCE
(a) Check and adjust the Off±the±car balance.
(b) If required, check and adjust the On±the±car balance. Imbalance after adjustment: 8.0 g (0.018 lb) or less
4.INSPECT BEARING BACKLASH (See page 30±2)
5.INSPECT AXLE HUB DEVIATION (See page 30±2)
6.INSPECT BEARING BACKLASH (See page 30±2)
7.INSPECT AXLE HUB DEVIATION (See page 30±2)
Page 2558 of 5135
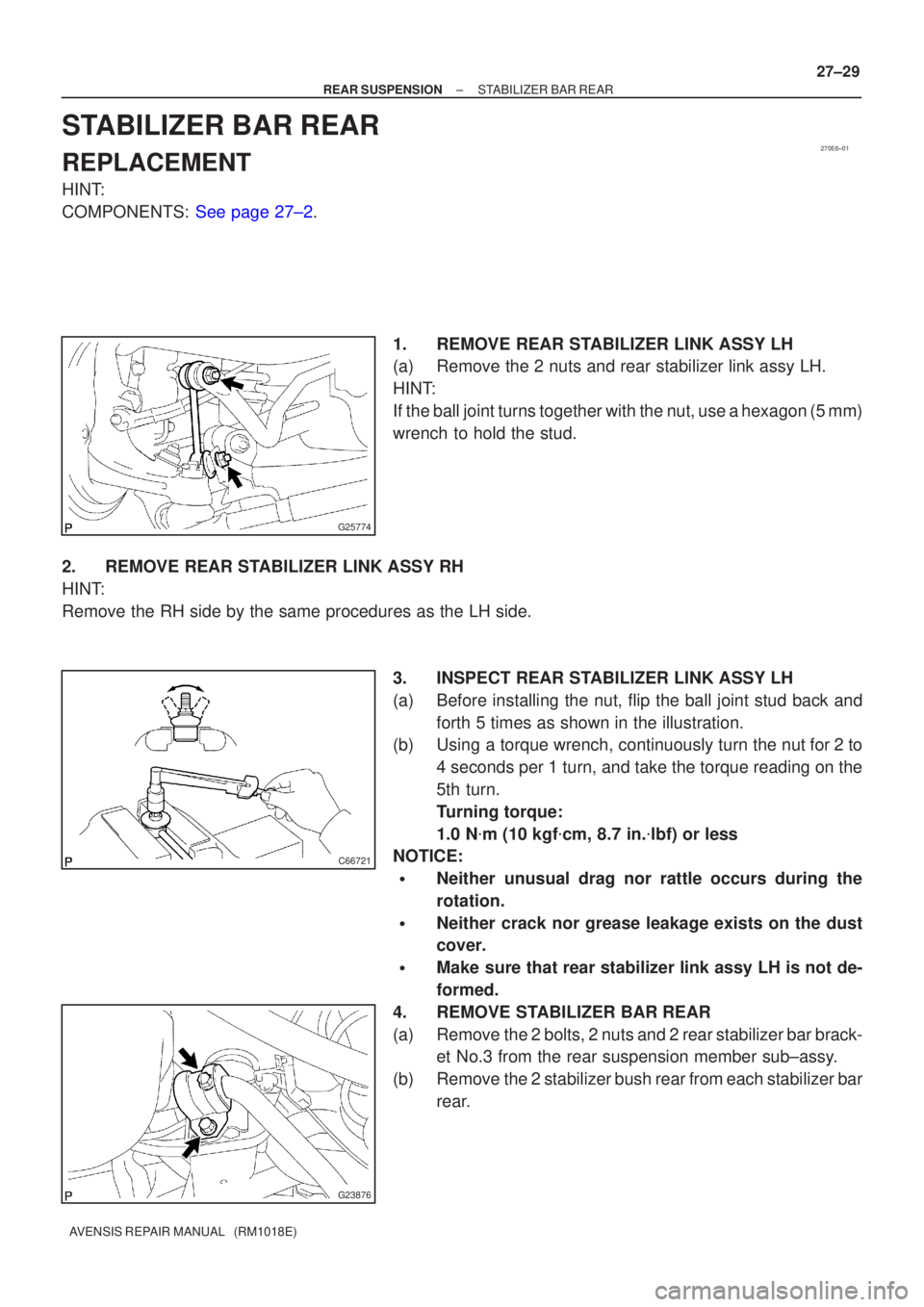
270E6±01
G25774
C66721
G23876
±
REAR SUSPENSION STABILIZER BAR REAR
27±29
AVENSIS REPAIR MANUAL (RM1018E)
STABILIZER BAR REAR
REPLACEMENT
HINT:
COMPONENTS: See page 27±2.
1. REMOVE REAR STABILIZER LINK ASSY LH
(a) Remove the 2 nuts and rear stabilizer link assy LH.
HINT:
If the ball joint turns together with the nut, use a hexagon (5 mm)
wrench to hold the stud.
2. REMOVE REAR STABILIZER LINK ASSY RH
HINT:
Remove the RH side by the same procedures as the LH side. 3. INSPECT REAR STABILIZER LINK ASSY LH
(a) Before installing the nut, flip the ball joint stud back andforth 5 times as shown in the illustration.
(b) Using a torque wrench, continuously turn the nut for 2 to
4 seconds per 1 turn, and take the torque reading on the
5th turn.
Turning torque:
1.0 Nm (10 kgf cm, 8.7 in. lbf) or less
NOTICE:
Neither unusual drag nor rattle occurs during the
rotation.
Neither crack nor grease leakage exists on the dust
cover.
Make sure that rear stabilizer link assy LH is not de-
formed.
4. REMOVE STABILIZER BAR REAR
(a) Remove the 2 bolts, 2 nuts and 2 rear stabilizer bar brack- et No.3 from the rear suspension member sub±assy.
(b) Remove the 2 stabilizer bush rear from each stabilizer bar rear.
Page 2559 of 5135
G23878
Inner side
Stopper Ring
G23876
G25774
27±30
±
REAR SUSPENSION STABILIZER BAR REAR
AVENSIS REPAIR MANUAL (RM1018E)
5. INSTALL STABILIZER BAR REAR
(a) Install the 2 stabilizer bush rear to each stabilizer bar rear.
HINT:
Install the stabilizer bush rear to the outer side of the stopper
ring on the stabilizer bar.
(b) Install the stabilizer bar rear and 2 rear stabilizer bar bracket No.3 with 2 bolts and 2 nuts.
Torque: 35 N m (357 kgf cm, 26 ft lbf)
6. INSTALL REAR STABILIZER LINK ASSY LH
(a) Install the rear stabilizer link assy LH with the 2 nuts. Torque: 44 N m (449 kgf cm, 32 ft lbf)
HINT:
If the ball joint turns together with the nut, use a hexagon (5 mm)
wrench to hold the stud.
7. INSTALL REAR STABILIZER LINK ASSY RH
HINT:
Install the RH side by the same procedures as the LH side.
8.INSPECT AND ADJUST REAR WHEEL ALIGNMENT (See page 27±4)
Page 2560 of 5135
270E5±01
G25775
G21542
G23879
Matchmarks
G23879
Matchmarks
±
REAR SUSPENSION UPPER CONTROL ARM ASSY
27±27
AVENSIS REPAIR MANUAL (RM1018E)
UPPER CONTROL ARM ASSY
REPLACEMENT
HINT:
COMPONENTS: See page 27±2.
1. REMOVE REAR WHEEL
2. REMOVE UPPER CONTROL ARM ASSY
(a) Support the rear suspension arm assy No.1 LH.
(b) Remove the bolt and nut, separate the upper control armassy.
NOTICE:
When removing the bolt, hold the nut not to rotate.
(c) Place matchmarks on the camber adjust cam assy, cam- ber adjust cam No.2 and rear suspension member sub±
assy.
(d) Remove the nut, camber adjust cam assy and camber ad-
just cam No.2.
3. INSTALL UPPER CONTROL ARM ASSY
(a) Install the camber adjust cam assy from the front side of the vehicle, and temporarily fix it with the nut and the cam-
ber adjust cam No.2.