Page 4297 of 4731
PS-22
POWER STEERING GEAR AND LINKAGE
Revision: 2005 July 2005 FX
Disassembly and AssemblyAGS000H1
SGIA1433E
Page 4298 of 4731
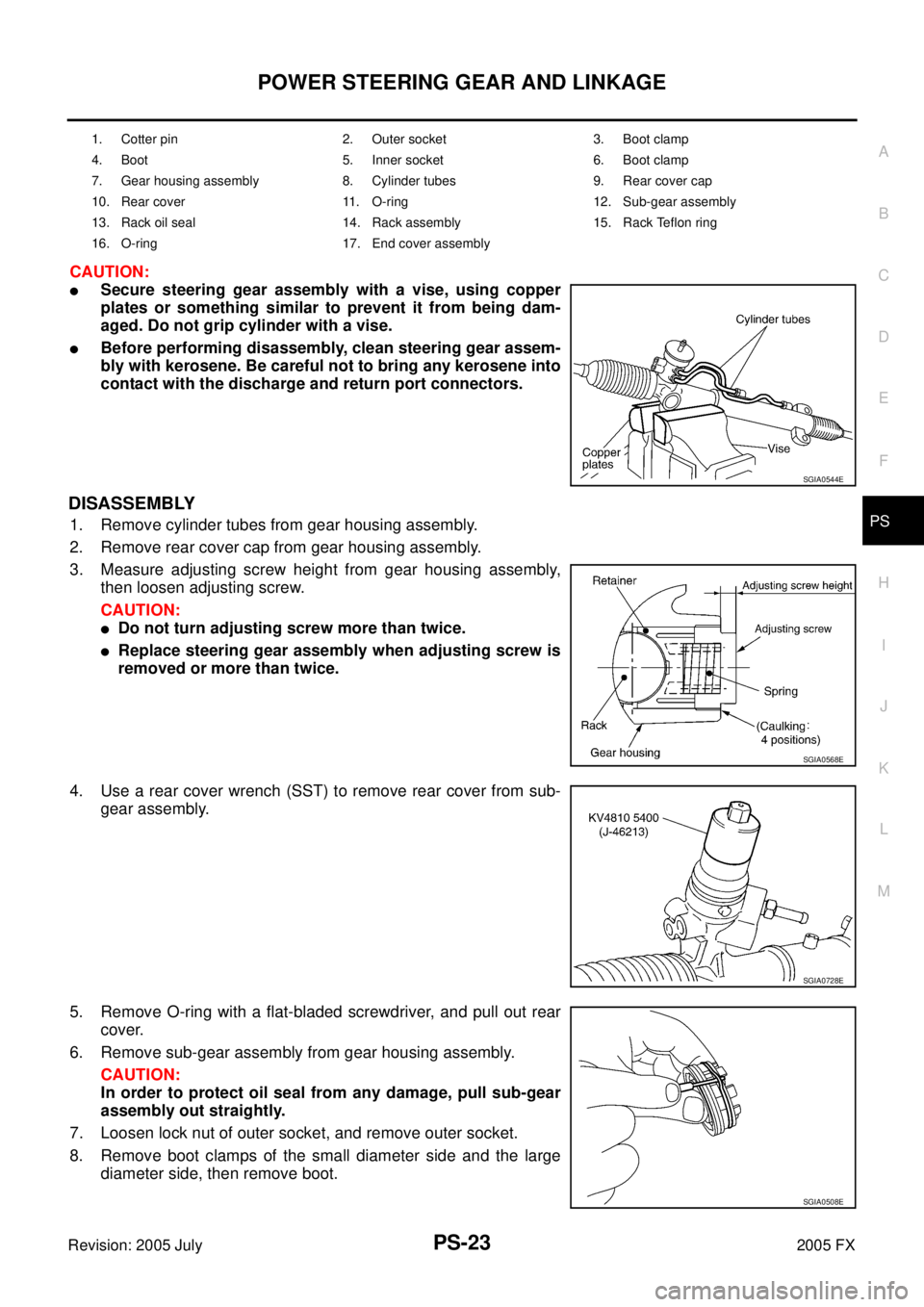
POWER STEERING GEAR AND LINKAGE PS-23
C
D E
F
H I
J
K L
M A
B
PS
Revision: 2005 July 2005 FX
CAUTION:
Secure steering gear assembly with a vise, using copper
plates or something similar to prevent it from being dam-
aged. Do not grip cylinder with a vise.
Before performing disassembly, clean steering gear assem-
bly with kerosene. Be careful not to bring any kerosene into
contact with the discharge and return port connectors.
DISASSEMBLY
1. Remove cylinder tubes from gear housing assembly.
2. Remove rear cover cap from gear housing assembly.
3. Measure adjusting screw height from gear housing assembly, then loosen adjusting screw.
CAUTION:
Do not turn adjusting screw more than twice.
Replace steering gear assembly when adjusting screw is
removed or more than twice.
4. Use a rear cover wrench (SST) to remove rear cover from sub- gear assembly.
5. Remove O-ring with a flat-bladed screwdriver, and pull out rear cover.
6. Remove sub-gear assembly from gear housing assembly. CAUTION:
In order to protect oil seal from any damage, pull sub-gear
assembly out straightly.
7. Loosen lock nut of outer socket, and remove outer socket.
8. Remove boot clamps of the small diameter side and the large diameter side, then remove boot.
1. Cotter pin 2. Outer socket 3. Boot clamp
4. Boot 5. Inner socket 6. Boot clamp
7. Gear housing assembly 8. Cylinder tubes 9. Rear cover cap
10. Rear cover 11. O-ring 12. Sub-gear assembly
13. Rack oil seal 14. Rack assembly 15. Rack Teflon ring
16. O-ring 17. End cover assembly
SGIA0544E
SGIA0568E
SGIA0728E
SGIA0508E
Page 4299 of 4731
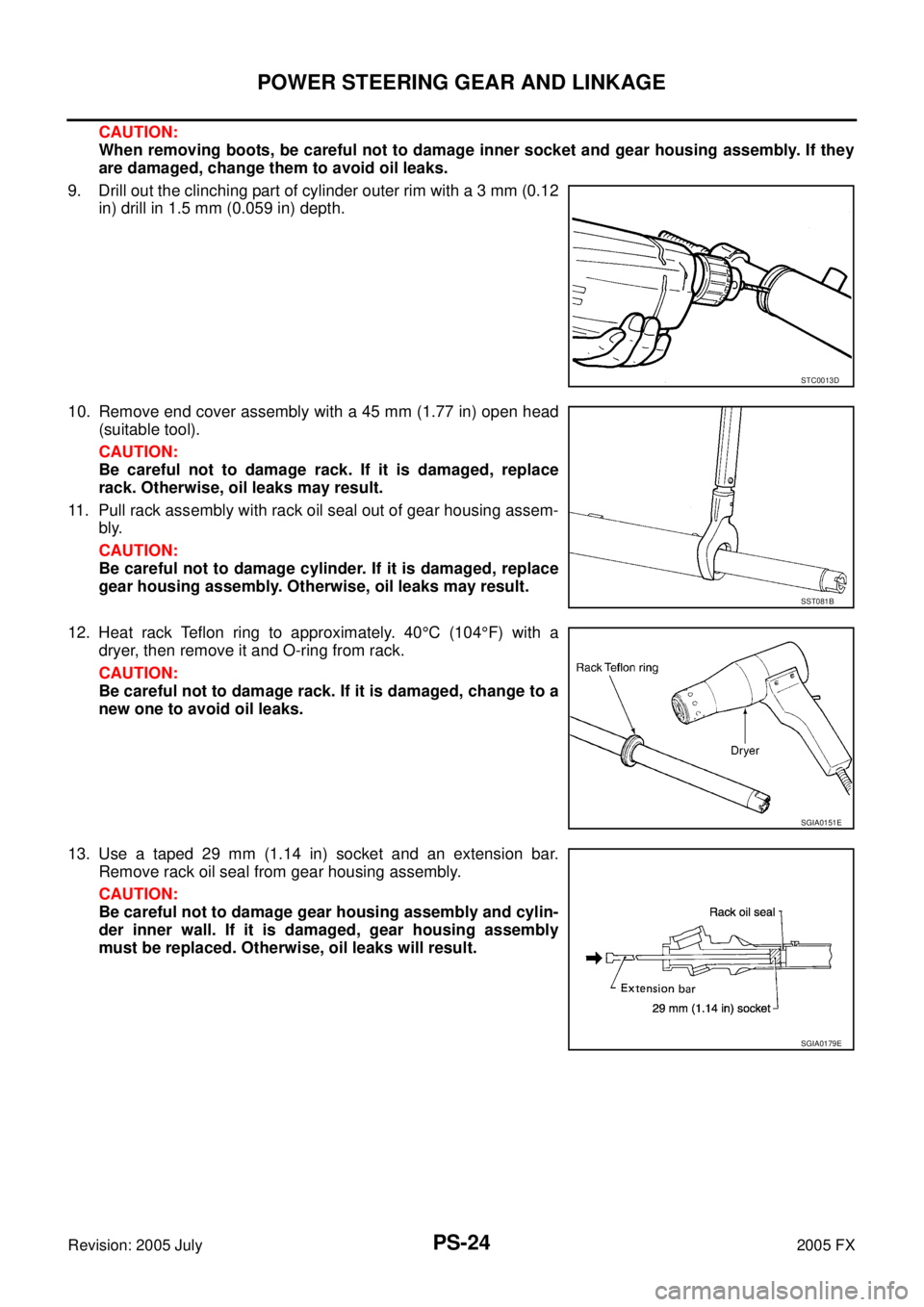
PS-24
POWER STEERING GEAR AND LINKAGE
Revision: 2005 July 2005 FX
CAUTION:
When removing boots, be careful not to damage inner socket and gear housing assembly. If they
are damaged, change them to avoid oil leaks.
9. Drill out the clinching part of cylinder outer rim with a 3 mm (0.12 in) drill in 1.5 mm (0.059 in) depth.
10. Remove end cover assembly with a 45 mm (1.77 in) open head (suitable tool).
CAUTION:
Be careful not to damage rack. If it is damaged, replace
rack. Otherwise, oil leaks may result.
11. Pull rack assembly with rack oil seal out of gear housing assem- bly.
CAUTION:
Be careful not to damage cylinder. If it is damaged, replace
gear housing assembly. Otherwise, oil leaks may result.
12. Heat rack Teflon ring to approximately. 40 °C (104 °F) with a
dryer, then remove it and O-ring from rack.
CAUTION:
Be careful not to damage rack. If it is damaged, change to a
new one to avoid oil leaks.
13. Use a taped 29 mm (1.14 in) socket and an extension bar. Remove rack oil seal from gear housing assembly.
CAUTION:
Be careful not to damage gear housing assembly and cylin-
der inner wall. If it is damaged, gear housing assembly
must be replaced. Otherwise, oil leaks will result.
STC0013D
SST081B
SGIA0151E
SGIA0179E
Page 4300 of 4731
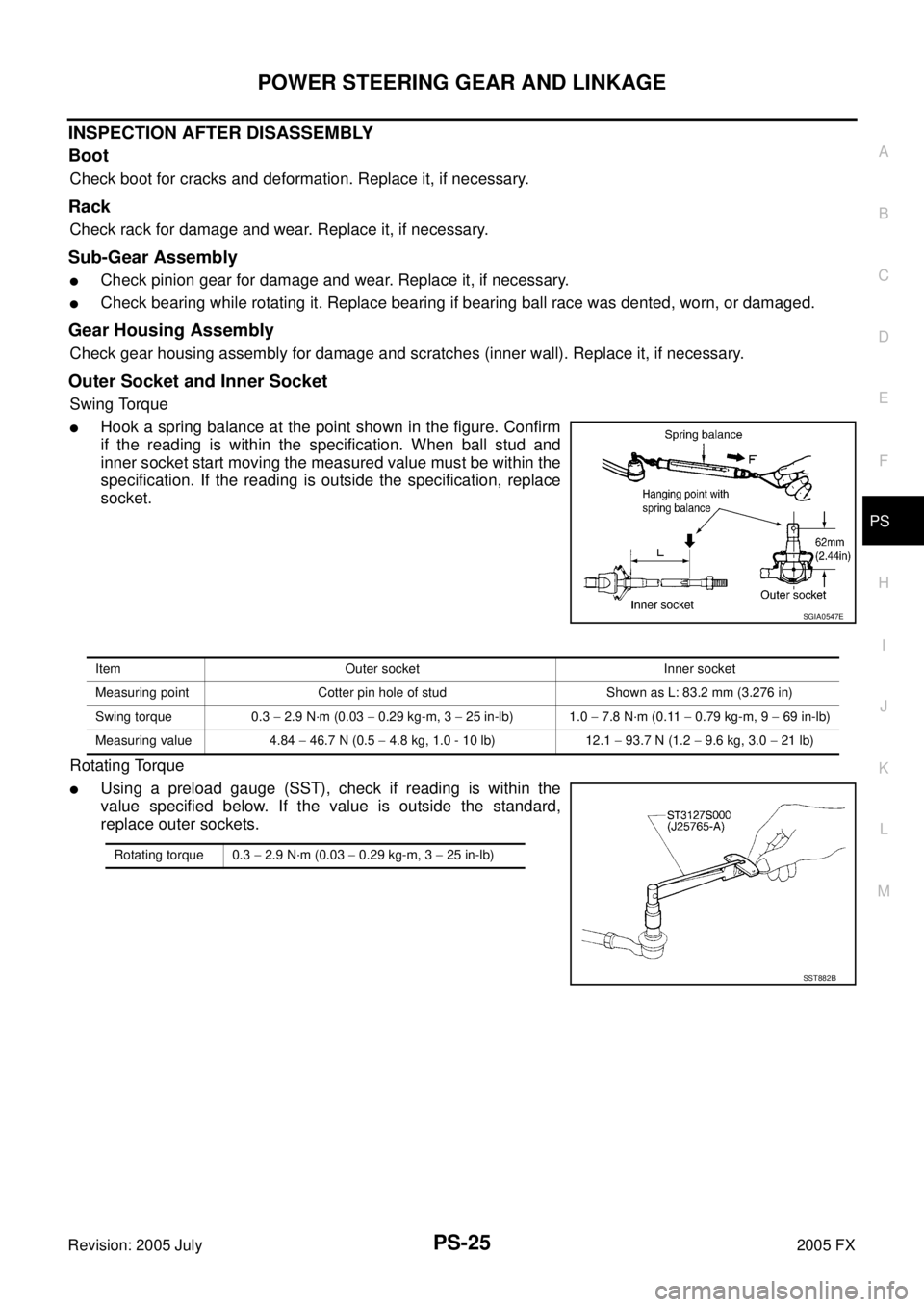
POWER STEERING GEAR AND LINKAGE PS-25
C
D E
F
H I
J
K L
M A
B
PS
Revision: 2005 July 2005 FX
INSPECTION AFTER DISASSEMBLY
Boot
Check boot for cracks and deformation. Replace it, if necessary.
Rack
Check rack for damage and wear. Replace it, if necessary.
Sub-Gear Assembly
Check pinion gear for damage and wear. Replace it, if necessary.
Check bearing while rotating it. Replace bearing if bearing ball race was dented, worn, or damaged.
Gear Housing Assembly
Check gear housing assembly for damage and scratches (inner wall). Replace it, if necessary.
Outer Socket and Inner Socket
Swing Torque
Hook a spring balance at the point shown in the figure. Confirm
if the reading is within the specification. When ball stud and
inner socket start moving the measured value must be within the
specification. If the reading is outside the specification, replace
socket.
Rotating Torque
Using a preload gauge (SST), check if reading is within the
value specified below. If the value is outside the standard,
replace outer sockets.
SGIA0547E
Item Outer socket Inner socket
Measuring point Cotter pin hole of stud Shown as L: 83.2 mm (3.276 in)
Swing torque 0.3 − 2.9 N·m (0.03 − 0.29 kg-m, 3 − 25 in-lb) 1.0 − 7.8 N·m (0.11 − 0.79 kg-m, 9 − 69 in-lb)
Measuring value 4.84 − 46.7 N (0.5 − 4.8 kg, 1.0 - 10 lb) 12.1 − 93.7 N (1.2 − 9.6 kg, 3.0 − 21 lb)
Rotating torque 0.3 − 2.9 N·m (0.03 − 0.29 kg-m, 3 − 25 in-lb)
SST882B
Page 4301 of 4731
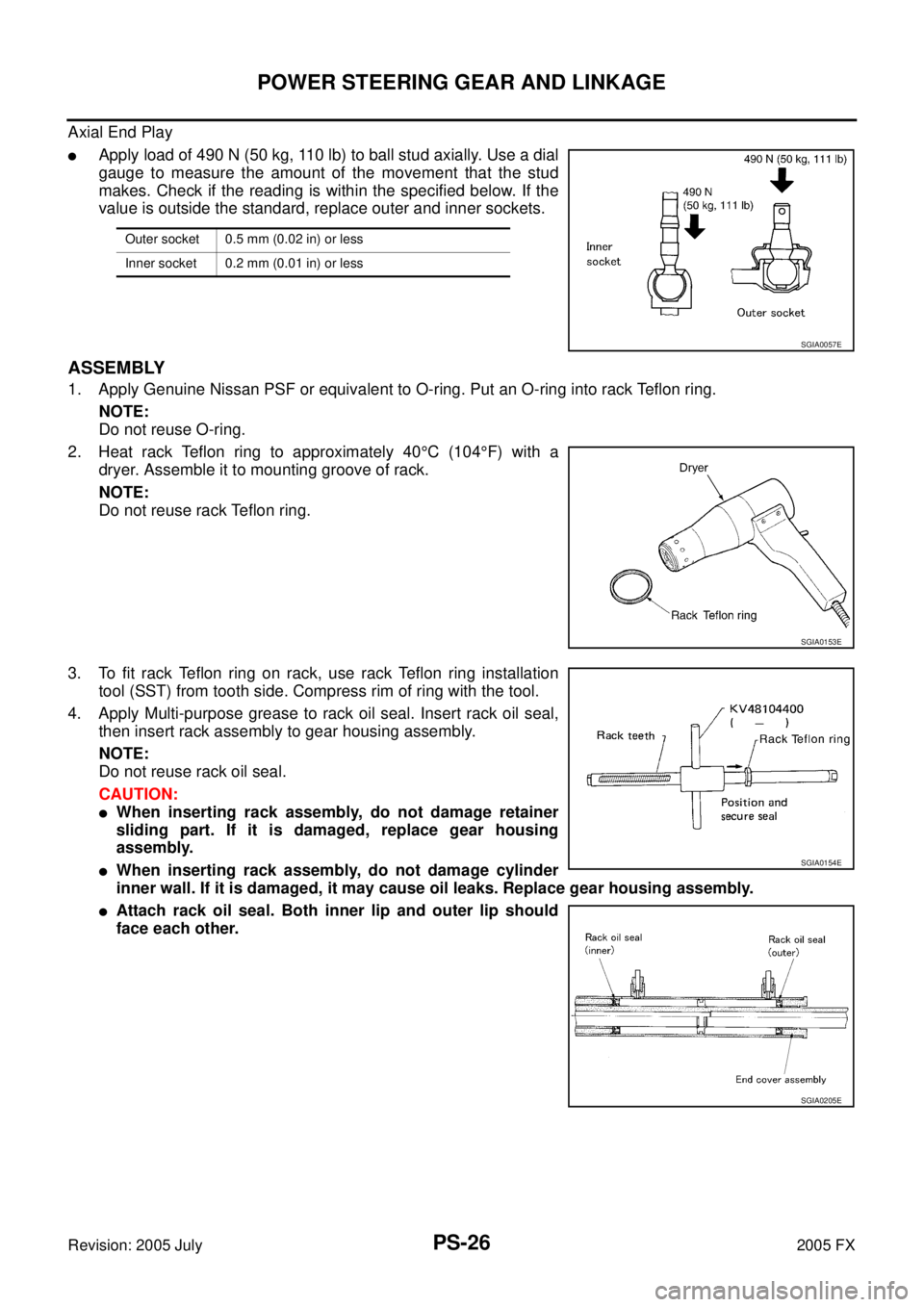
PS-26
POWER STEERING GEAR AND LINKAGE
Revision: 2005 July 2005 FX
Axial End Play
Apply load of 490 N (50 kg, 110 lb) to ball stud axially. Use a dial
gauge to measure the amount of the movement that the stud
makes. Check if the reading is within the specified below. If the
value is outside the standard, replace outer and inner sockets.
ASSEMBLY
1. Apply Genuine Nissan PSF or equivalent to O-ring. Put an O-ring into rack Teflon ring.
NOTE:
Do not reuse O-ring.
2. Heat rack Teflon ring to approximately 40 °C (104 °F) with a
dryer. Assemble it to mounting groove of rack.
NOTE:
Do not reuse rack Teflon ring.
3. To fit rack Teflon ring on rack, use rack Teflon ring installation tool (SST) from tooth side. Compress rim of ring with the tool.
4. Apply Multi-purpose grease to rack oil seal. Insert rack oil seal, then insert rack assembly to gear housing assembly.
NOTE:
Do not reuse rack oil seal.
CAUTION:
When inserting rack assembly, do not damage retainer
sliding part. If it is damaged, replace gear housing
assembly.
When inserting rack assembly, do not damage cylinder
inner wall. If it is damaged, it may cause oil leaks. Replace gear housing assembly.
Attach rack oil seal. Both inner lip and outer lip should
face each other.
Outer socket 0.5 mm (0.02 in) or less
Inner socket 0.2 mm (0.01 in) or less
SGIA0057E
SGIA0153E
SGIA0154E
SGIA0205E
Page 4302 of 4731
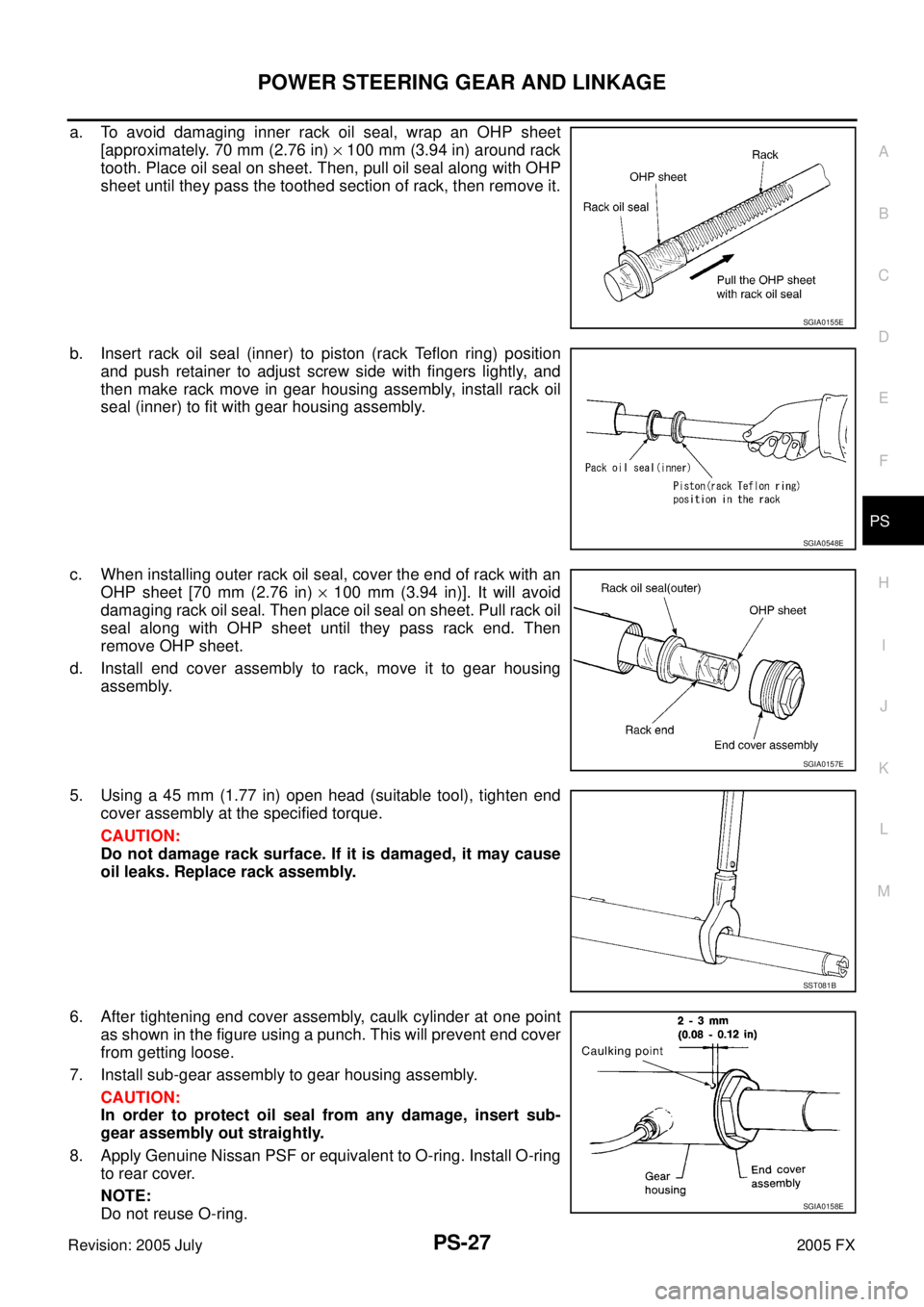
POWER STEERING GEAR AND LINKAGE PS-27
C
D E
F
H I
J
K L
M A
B
PS
Revision: 2005 July 2005 FX
a. To avoid damaging inner rack oil seal, wrap an OHP sheet
[approximately. 70 mm (2.76 in) × 100 mm (3.94 in) around rack
tooth. Place oil seal on sheet. Then, pull oil seal along with OHP
sheet until they pass the toothed section of rack, then remove it.
b. Insert rack oil seal (inner) to piston (rack Teflon ring) position and push retainer to adjust screw side with fingers lightly, and
then make rack move in gear housing assembly, install rack oil
seal (inner) to fit with gear housing assembly.
c. When installing outer rack oil seal, cover the end of rack with an OHP sheet [70 mm (2.76 in) × 100 mm (3.94 in)]. It will avoid
damaging rack oil seal. Then place oil seal on sheet. Pull rack oil
seal along with OHP sheet until they pass rack end. Then
remove OHP sheet.
d. Install end cover assembly to rack, move it to gear housing assembly.
5. Using a 45 mm (1.77 in) open head (suitable tool), tighten end cover assembly at the specified torque.
CAUTION:
Do not damage rack surface. If it is damaged, it may cause
oil leaks. Replace rack assembly.
6. After tightening end cover assembly, caulk cylinder at one point as shown in the figure using a punch. This will prevent end cover
from getting loose.
7. Install sub-gear assembly to gear housing assembly. CAUTION:
In order to protect oil seal from any damage, insert sub-
gear assembly out straightly.
8. Apply Genuine Nissan PSF or equivalent to O-ring. Install O-ring to rear cover.
NOTE:
Do not reuse O-ring.
SGIA0155E
SGIA0548E
SGIA0157E
SST081B
SGIA0158E
Page 4303 of 4731
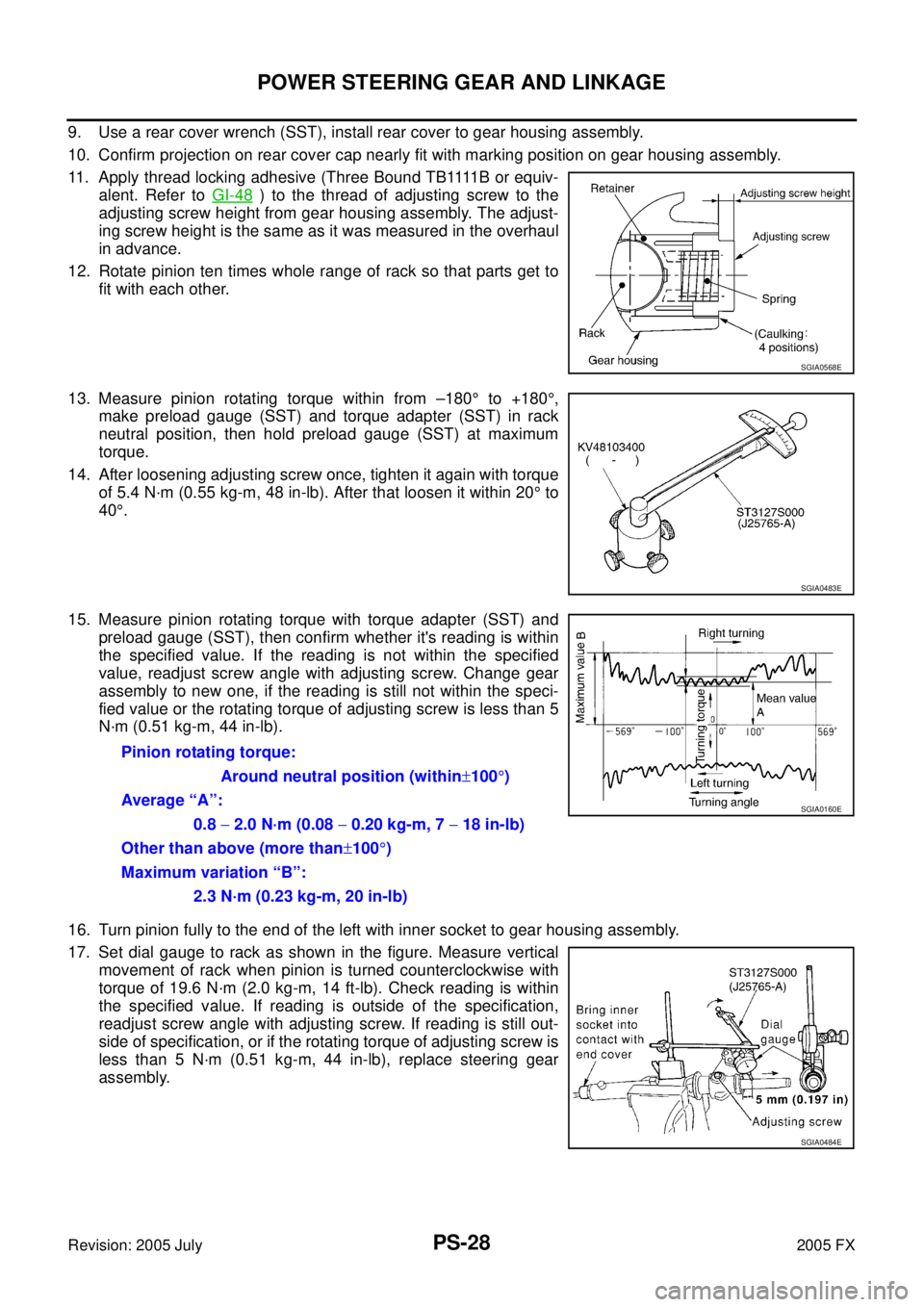
PS-28
POWER STEERING GEAR AND LINKAGE
Revision: 2005 July 2005 FX
9. Use a rear cover wrench (SST), install rear cover to gear housing assembly.
10. Confirm projection on rear cover cap nearly fit with marking position on gear housing assembly.
11 . A p p l y t h r e a d l o c k i n g a d h e s i v e ( T h r e e B o u n d T B 1111 B o r e q u i v - alent. Refer to GI-48
) to the thread of adjusting screw to the
adjusting screw height from gear housing assembly. The adjust-
ing screw height is the same as it was measured in the overhaul
in advance.
12. Rotate pinion ten times whole range of rack so that parts get to fit with each other.
13. Measure pinion rotating torque within from –180 ° to +180 °,
make preload gauge (SST) and torque adapter (SST) in rack
neutral position, then hold preload gauge (SST) at maximum
torque.
14. After loosening adjusting screw once, tighten it again with torque of 5.4 N·m (0.55 kg-m, 48 in-lb). After that loosen it within 20 ° to
40 °.
15. Measure pinion rotating torque with torque adapter (SST) and preload gauge (SST), then confirm whether it's reading is within
the specified value. If the reading is not within the specified
value, readjust screw angle with adjusting screw. Change gear
assembly to new one, if the reading is still not within the speci-
fied value or the rotating torque of adjusting screw is less than 5
N·m (0.51 kg-m, 44 in-lb).
16. Turn pinion fully to the end of the left with inner socket to gear housing assembly.
17. Set dial gauge to rack as shown in the figure. Measure vertical movement of rack when pinion is turned counterclockwise with
torque of 19.6 N·m (2.0 kg-m, 14 ft-lb). Check reading is within
the specified value. If reading is outside of the specification,
readjust screw angle with adjusting screw. If reading is still out-
side of specification, or if the rotating torque of adjusting screw is
less than 5 N·m (0.51 kg-m, 44 in-lb), replace steering gear
assembly.
SGIA0568E
SGIA0483E
Pinion rotating torque:
Around neutral position (within ±100 °)
Average “A”:
0.8 − 2.0 N·m (0.08 − 0.20 kg-m, 7 − 18 in-lb)
Other than above (more than ±100 °)
Maximum variation “B”:
2.3 N·m (0.23 kg-m, 20 in-lb)
SGIA0160E
SGIA0484E
Page 4304 of 4731

POWER STEERING GEAR AND LINKAGE PS-29
C
D E
F
H I
J
K L
M A
B
PS
Revision: 2005 July 2005 FX
18. Install large-diameter side of boot to gear housing assembly.
19. Install small-diameter side of boot to the mounting groove of inner socket boot.
20. Install boot clamp to the small-diameter side of boot.
21. Install boot clamp to the large-diameter side of boot.
NOTE:
Do not reuse boot clamp.
a. Tighten large-diameter side of RH/LH boot with boot clamp (stainless wire).
b. After wrapping clamp around boot groove for two turns, insert screwdriver in loop on both ends of wire. Twist 4 to 4.5 turns
while pulling with a force of approx. 98 N (10 kg, 22 lb).
c. Twist boot clamp as shown in the figure, pay attention to rela- tionship between winding and twisting directions.
22. Install cylinder tubes to gear housing assembly.
23. Install lock nut and outer socket to inner socket. Amount of vertical movement with rack Less than 0.265 mm (0.01 in)
Measuring point Axial direction of rack 5 mm (0.2 in) away from
end of gear housing
Radius direction of rack Shaft direction of adjust- ing screw
SGIA0550E
Wire length “L” : 390 mm (15.35 in)
SGIA0163E
SGIA0164E
SGIA0544E