Page 3217 of 4731
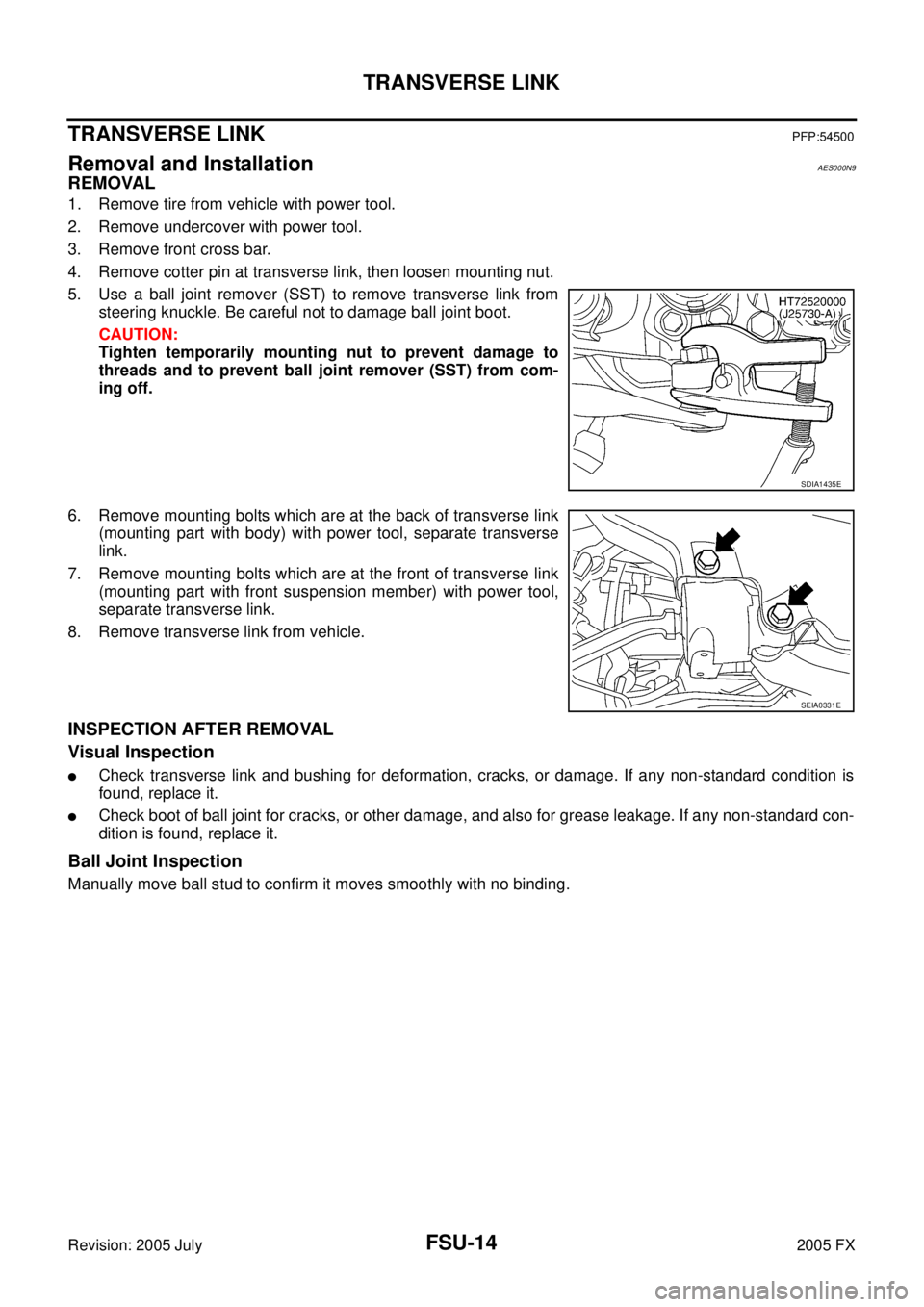
FSU-14
TRANSVERSE LINK
Revision: 2005 July 2005 FX
TRANSVERSE LINKPFP:54500
Removal and InstallationAES000N9
REMOVAL
1. Remove tire from vehicle with power tool.
2. Remove undercover with power tool.
3. Remove front cross bar.
4. Remove cotter pin at transverse link, then loosen mounting nut.
5. Use a ball joint remover (SST) to remove transverse link from steering knuckle. Be careful not to damage ball joint boot.
CAUTION:
Tighten temporarily mounting nut to prevent damage to
threads and to prevent ball joint remover (SST) from com-
ing off.
6. Remove mounting bolts which are at the back of transverse link (mounting part with body) with power tool, separate transverse
link.
7. Remove mounting bolts which are at the front of transverse link (mounting part with front suspension member) with power tool,
separate transverse link.
8. Remove transverse link from vehicle.
INSPECTION AFTER REMOVAL
Visual Inspection
Check transverse link and bushing for deformation, cracks, or damage. If any non-standard condition is
found, replace it.
Check boot of ball joint for cracks, or other damage, and also for grease leakage. If any non-standard con-
dition is found, replace it.
Ball Joint Inspection
Manually move ball stud to confirm it moves smoothly with no binding.
SDIA1435E
SEIA0331E
Page 3218 of 4731
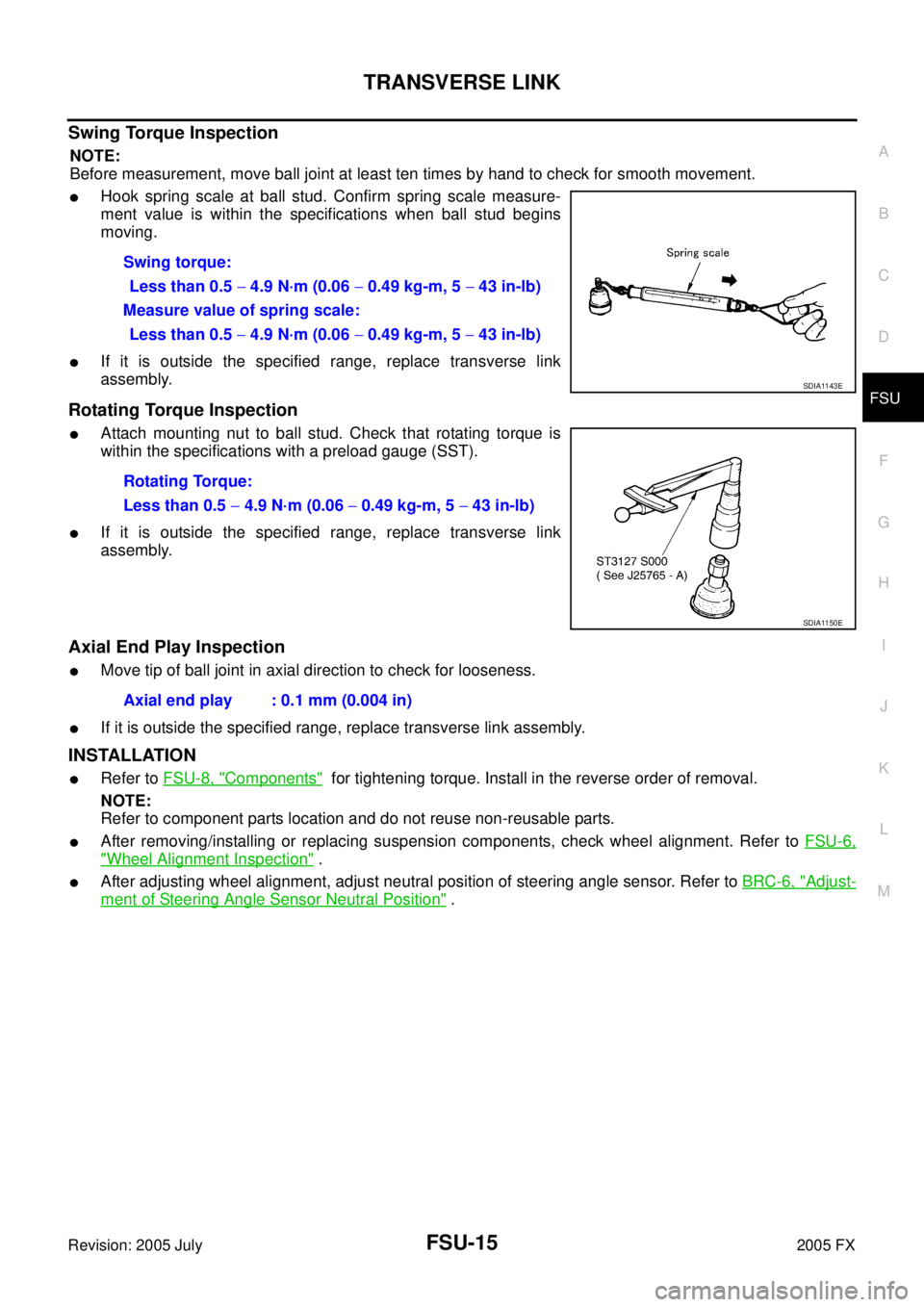
TRANSVERSE LINK FSU-15
C
D
F
G H
I
J
K L
M A
B
FSU
Revision: 2005 July 2005 FX
Swing Torque Inspection
NOTE:
Before measurement, move ball joint at least ten times by hand to check for smooth movement.
Hook spring scale at ball stud. Confirm spring scale measure-
ment value is within the specifications when ball stud begins
moving.
If it is outside the specified range, replace transverse link
assembly.
Rotating Torque Inspection
Attach mounting nut to ball stud. Check that rotating torque is
within the specifications with a preload gauge (SST).
If it is outside the specified range, replace transverse link
assembly.
Axial End Play Inspection
Move tip of ball joint in axial direction to check for looseness.
If it is outside the specified range, replace transverse link assembly.
INSTALLATION
Refer to FSU-8, "Components" for tightening torque. Install in the reverse order of removal.
NOTE:
Refer to component parts location and do not reuse non-reusable parts.
After removing/installing or replacing suspension components, check wheel alignment. Refer to FSU-6,
"Wheel Alignment Inspection" .
After adjusting wheel alignment, adjust neutral position of steering angle sensor. Refer to BRC-6, "Adjust-
ment of Steering Angle Sensor Neutral Position" .
Swing torque:
Less than 0.5 − 4.9 N·m (0.06 − 0.49 kg-m, 5 − 43 in-lb)
Measure value of spring scale: Less than 0.5 − 4.9 N·m (0.06 − 0.49 kg-m, 5 − 43 in-lb)
SDIA1143E
Rotating Torque:
Less than 0.5 − 4.9 N·m (0.06 − 0.49 kg-m, 5 − 43 in-lb)
SDIA1150E
Axial end play : 0.1 mm (0.004 in)
Page 3219 of 4731
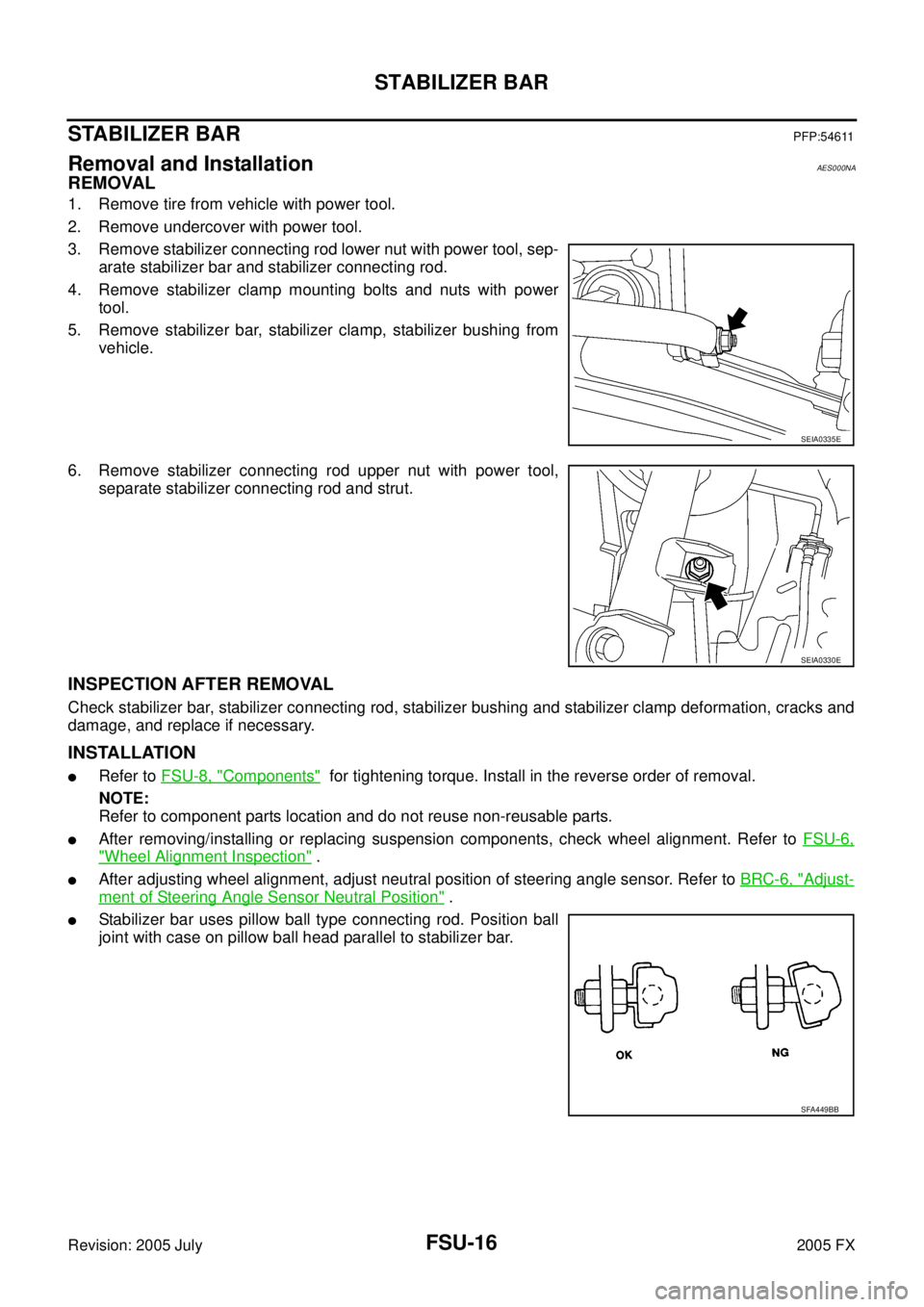
FSU-16
STABILIZER BAR
Revision: 2005 July 2005 FX
STABILIZER BARPFP:54611
Removal and InstallationAES000NA
REMOVAL
1. Remove tire from vehicle with power tool.
2. Remove undercover with power tool.
3. Remove stabilizer connecting rod lower nut with power tool, sep- arate stabilizer bar and stabilizer connecting rod.
4. Remove stabilizer clamp mounting bolts and nuts with power tool.
5. Remove stabilizer bar, stabilizer clamp, stabilizer bushing from vehicle.
6. Remove stabilizer connecting rod upper nut with power tool, separate stabilizer connecting rod and strut.
INSPECTION AFTER REMOVAL
Check stabilizer bar, stabilizer connecting rod, stabilizer bushing and stabilizer clamp deformation, cracks and
damage, and replace if necessary.
INSTALLATION
Refer to FSU-8, "Components" for tightening torque. Install in the reverse order of removal.
NOTE:
Refer to component parts location and do not reuse non-reusable parts.
After removing/installing or replacing suspension components, check wheel alignment. Refer to FSU-6,
"Wheel Alignment Inspection" .
After adjusting wheel alignment, adjust neutral position of steering angle sensor. Refer to BRC-6, "Adjust-
ment of Steering Angle Sensor Neutral Position" .
Stabilizer bar uses pillow ball type connecting rod. Position ball
joint with case on pillow ball head parallel to stabilizer bar.
SEIA0335E
SEIA0330E
SFA449BB
Page 3220 of 4731
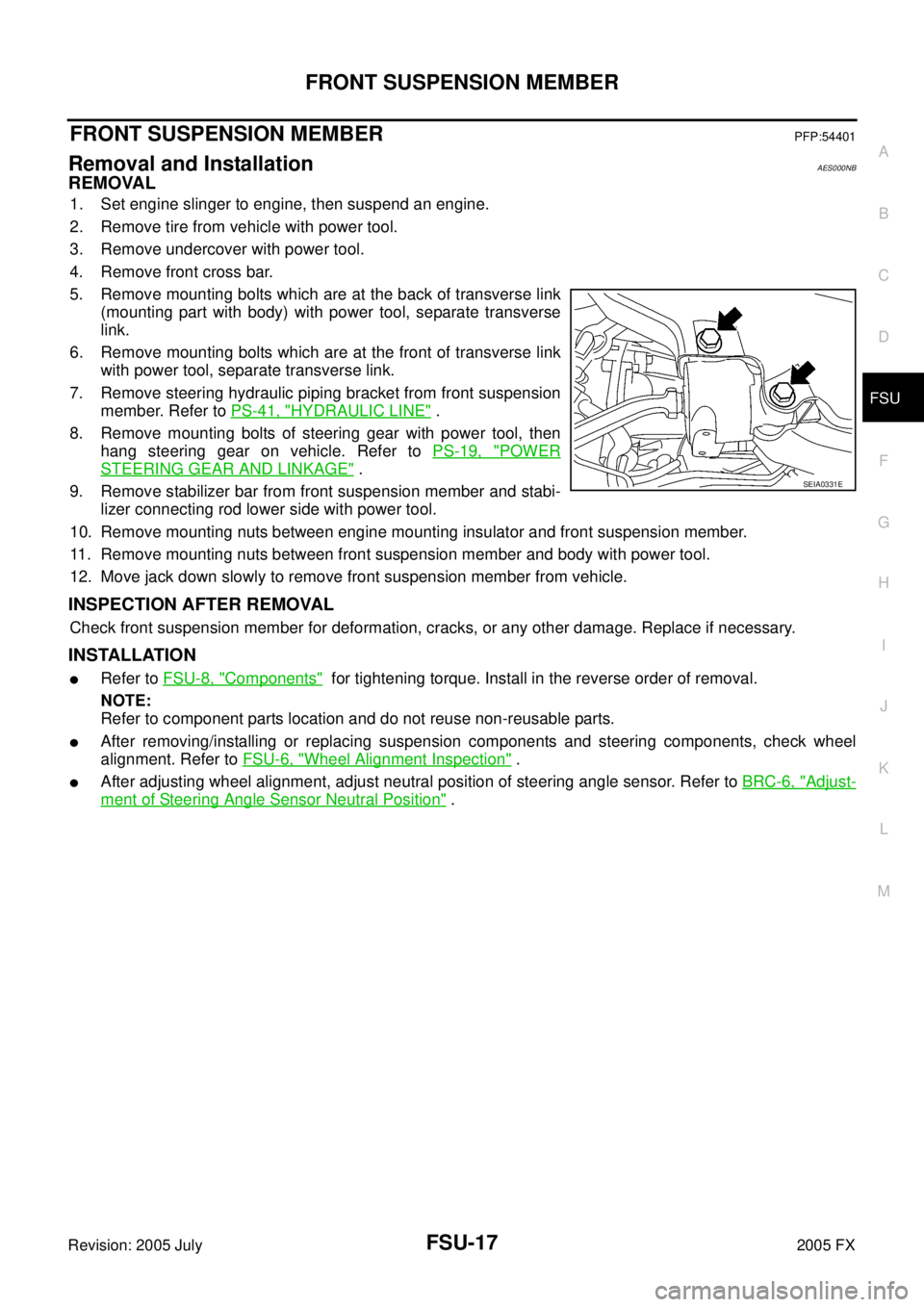
FRONT SUSPENSION MEMBER FSU-17
C
D
F
G H
I
J
K L
M A
B
FSU
Revision: 2005 July 2005 FX
FRONT SUSPENSION MEMBERPFP:54401
Removal and InstallationAES000NB
REMOVAL
1. Set engine slinger to engine, then suspend an engine.
2. Remove tire from vehicle with power tool.
3. Remove undercover with power tool.
4. Remove front cross bar.
5. Remove mounting bolts which are at the back of transverse link (mounting part with body) with power tool, separate transverse
link.
6. Remove mounting bolts which are at the front of transverse link with power tool, separate transverse link.
7. Remove steering hydraulic piping bracket from front suspension member. Refer to PS-41, "
HYDRAULIC LINE" .
8. Remove mounting bolts of steering gear with power tool, then hang steering gear on vehicle. Refer to PS-19, "
POWER
STEERING GEAR AND LINKAGE" .
9. Remove stabilizer bar from front suspension member and stabi- lizer connecting rod lower side with power tool.
10. Remove mounting nuts between engine mounting insulator and front suspension member.
11. Remove mounting nuts between front suspension member and body with power tool.
12. Move jack down slowly to remove front suspension member from vehicle.
INSPECTION AFTER REMOVAL
Check front suspension member for deformation, cracks, or any other damage. Replace if necessary.
INSTALLATION
Refer to FSU-8, "Components" for tightening torque. Install in the reverse order of removal.
NOTE:
Refer to component parts location and do not reuse non-reusable parts.
After removing/installing or replacing suspension components and steering components, check wheel
alignment. Refer to FSU-6, "
Wheel Alignment Inspection" .
After adjusting wheel alignment, adjust neutral position of steering angle sensor. Refer to BRC-6, "Adjust-
ment of Steering Angle Sensor Neutral Position" .
SEIA0331E
Page 3221 of 4731
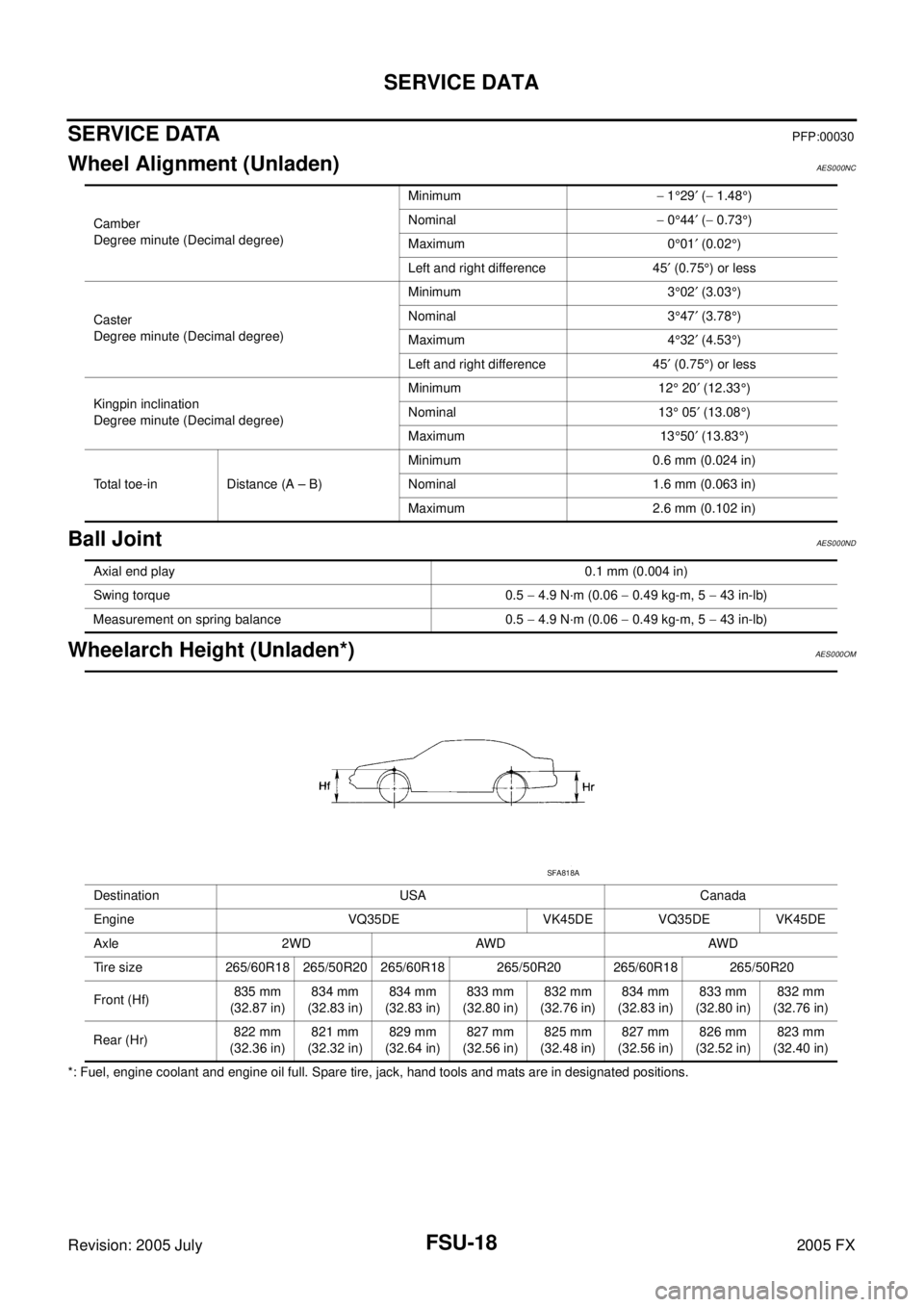
FSU-18
SERVICE DATA
Revision: 2005 July 2005 FX
SERVICE DATAPFP:00030
Wheel Alignment (Unladen)AES000NC
Ball JointAES000ND
Wheelarch Height (Unladen*)AES000OM
*: Fuel, engine coolant and engine oil full. Spare tire, jack, hand tools and mats are in designated positions. Camber
Degree minute (Decimal degree) Minimum
− 1 °29 ′ ( − 1.48 °)
Nominal − 0 °44 ′ ( − 0.73 °)
Maximum 0 °01 ′ (0.02 °)
Left and right difference 45 ′ (0.75 °) or less
Caster
Degree minute (Decimal degree) Minimum 3
°02 ′ (3.03 °)
Nominal 3 °47 ′ (3.78 °)
Maximum 4 °32 ′ (4.53 °)
Left and right difference 45 ′ (0.75 °) or less
Kingpin inclination
Degree minute (Decimal degree) Minimum 12
° 20 ′ (12.33 °)
Nominal 13 ° 05 ′ (13.08 °)
Maximum 13 °50 ′ (13.83 °)
Total toe-in Distance (A – B) Minimum 0.6 mm (0.024 in)
Nominal 1.6 mm (0.063 in)
Maximum 2.6 mm (0.102 in)
Axial end play 0.1 mm (0.004 in)
Swing torque 0.5 − 4.9 N·m (0.06 − 0.49 kg-m, 5 − 43 in-lb)
Measurement on spring balance 0.5 − 4.9 N·m (0.06 − 0.49 kg-m, 5 − 43 in-lb)
Destination USA Canada
Engine VQ35DE VK45DE VQ35DE VK45DE
Axle 2WD AWD AWD
Tire size 265/60R18 265/50R20 265/60R18 265/50R20 265/60R18 265/50R20
Front (Hf) 835 mm
(32.87 in) 834 mm
(32.83 in) 834 mm
(32.83 in) 833 mm
(32.80 in) 832 mm
(32.76 in) 834 mm
(32.83 in) 833 mm
(32.80 in) 832 mm
(32.76 in)
Rear (Hr) 822 mm
(32.36 in) 821 mm
(32.32 in) 829 mm
(32.64 in) 827 mm
(32.56 in) 825 mm
(32.48 in) 827 mm
(32.56 in) 826 mm
(32.52 in) 823 mm
(32.40 in)
SFA818A
Page 3222 of 4731
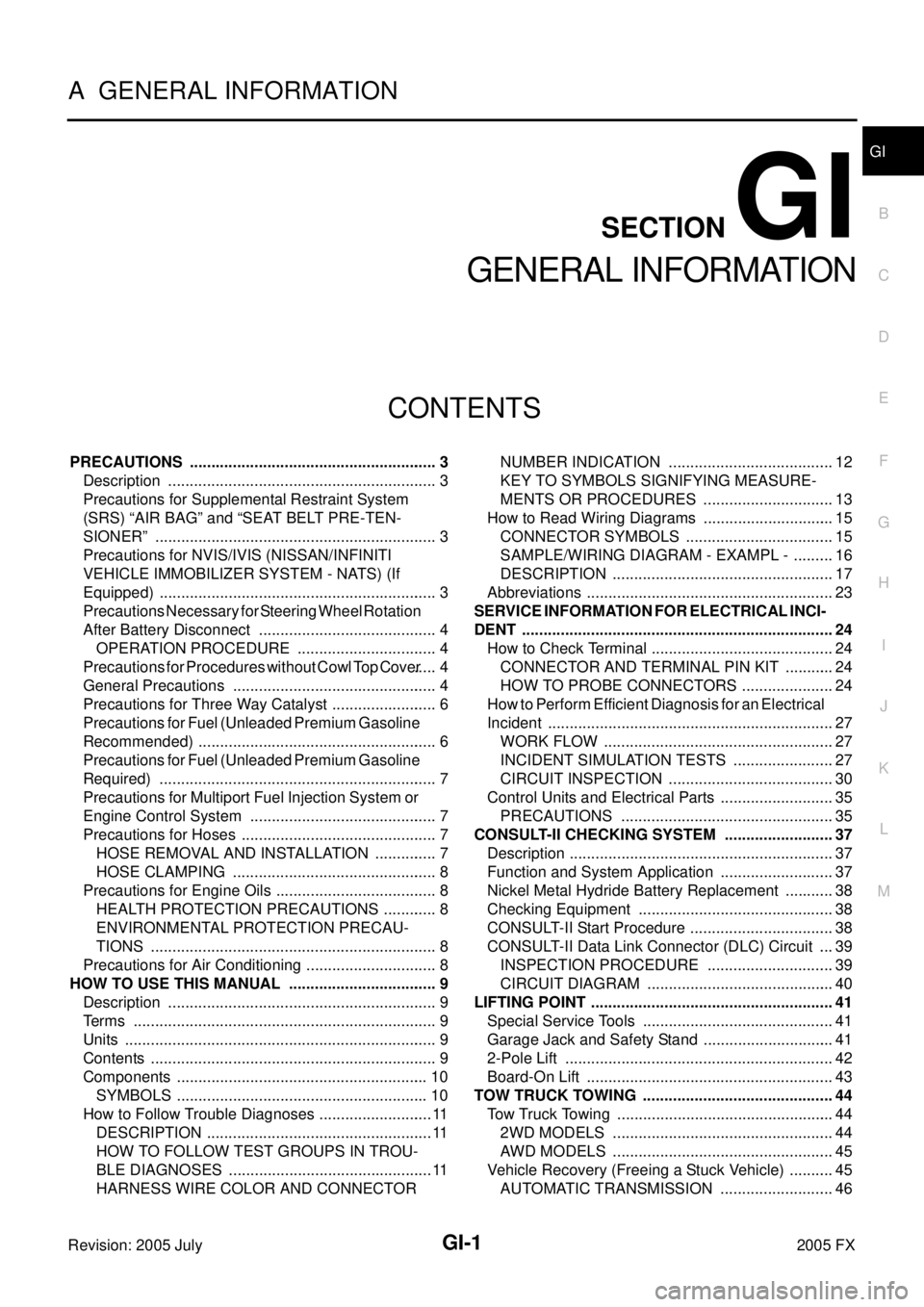
GI-1
GENERAL INFORMATION
A GENERAL INFORMATION
CONTENTS
C
D E
F
G H
I
J
K L
M B
GI
SECTION GI
Revision: 2005 July
2005 FX
GENERAL INFORMATION
PRECAUTIONS .......................................................... 3
Description .......................................................... ..... 3
Precautions for Supplemental Restraint System
(SRS) “AIR BAG” and “SEAT BELT PRE-TEN-
SIONER” ............................................................. ..... 3
Precautions for NVIS/IVIS (NISSAN/INFINITI
VEHICLE IMMOBILIZER SYSTEM - NATS) (If
Equipped) ............................................................ ..... 3
Precautions Necessary for Steering Wheel Rotation
After Battery Disconnect ..................................... ..... 4
OPERATION PROCEDURE ............................ ..... 4
Precautions for Procedures without Cowl Top Cover ..... 4
General Precautions ........................................... ..... 4
Precautions for Three Way Catalyst .................... ..... 6
Precautions for Fuel (Unleaded Premium Gasoline
Recommended) ................................................... ..... 6
Precautions for Fuel (Unleaded Premium Gasoline
Required) ............................................................ ..... 7
Precautions for Multiport Fuel Injection System or
Engine Control System ....................................... ..... 7
Precautions for Hoses ......................................... ..... 7
HOSE REMOVAL AND INSTALLATION .......... ..... 7
HOSE CLAMPING ........................................... ..... 8
Precautions for Engine Oils ................................. ..... 8
HEALTH PROTECTION PRECAUTIONS ........ ..... 8
ENVIRONMENTAL PROTECTION PRECAU-
TIONS .............................................................. ..... 8
Precautions for Air Conditioning .......................... ..... 8
HOW TO USE THIS MANUAL .............................. ..... 9
Description .......................................................... ..... 9
Terms .................................................................. ..... 9
Units .................................................................... ..... 9
Contents .............................................................. ..... 9
Components ........................................................ ... 10
SYMBOLS ........................................................ ... 10
How to Follow Trouble Diagnoses ....................... .... 11
DESCRIPTION ................................................. .... 11
HOW TO FOLLOW TEST GROUPS IN TROU-
BLE DIAGNOSES ............................................ .... 11
HARNESS WIRE COLOR AND CONNECTOR NUMBER INDICATION ....................................
... 12
KEY TO SYMBOLS SIGNIFYING MEASURE-
MENTS OR PROCEDURES ............................ ... 13
How to Read Wiring Diagrams ............................ ... 15
CONNECTOR SYMBOLS ................................ ... 15
SAMPLE/WIRING DIAGRAM - EXAMPL - ....... ... 16
DESCRIPTION ................................................. ... 17
Abbreviations ....................................................... ... 23
SERVICE INFORMATION FOR ELECTRICAL INCI-
DENT ...................................................................... ... 24
How to Check Terminal ........................................ ... 24
CONNECTOR AND TERMINAL PIN KIT ......... ... 24
HOW TO PROBE CONNECTORS ................... ... 24
How to Perform Efficient Diagnosis for an Electrical
Incident ................................................................ ... 27
WORK FLOW ................................................... ... 27
INCIDENT SIMULATION TESTS ..................... ... 27
CIRCUIT INSPECTION .................................... ... 30
Control Units and Electrical Parts ........................ ... 35
PRECAUTIONS ............................................... ... 35
CONSULT-II CHECKING SYSTEM ....................... ... 37
Description ........................................................... ... 37
Function and System Application ........................ ... 37
Nickel Metal Hydride Battery Replacement ......... ... 38
Checking Equipment ........................................... ... 38
CONSULT-II Start Procedure ............................... ... 38
CONSULT-II Data Link Connector (DLC) Circuit . ... 39
INSPECTION PROCEDURE ........................... ... 39
CIRCUIT DIAGRAM ......................................... ... 40
LIFTING POINT ...................................................... ... 41
Special Service Tools .......................................... ... 41
Garage Jack and Safety Stand ............................ ... 41
2-Pole Lift ............................................................ ... 42
Board-On Lift ....................................................... ... 43
TOW TRUCK TOWING .......................................... ... 44
Tow Truck Towing ................................................ ... 44
2WD MODELS ................................................. ... 44
AWD MODELS ................................................. ... 45
Vehicle Recovery (Freeing a Stuck Vehicle) ........ ... 45
AUTOMATIC TRANSMISSION ........................ ... 46
Page 3223 of 4731
GI-2Revision: 2005 July 2005 FX
TIGHTENING TORQUE OF STANDARD BOLTS .
... 47
Tightening Torque Table ...................................... ... 47
RECOMMENDED CHEMICAL PRODUCTS AND
SEALANTS ............................................................ ... 48
Recommended Chemical Products and Sealants ... 48
IDENTIFICATION INFORMATION ......................... ... 49
Model Variation .................................................... ... 49
IDENTIFICATION NUMBER ............................. ... 50 IDENTIFICATION PLATE .................................
... 50
ENGINE SERIAL NUMBER .............................. ... 51
AUTOMATIC TRANSMISSION NUMBER ........ ... 51
Dimensions .......................................................... ... 51
Wheels & Tires ..................................................... ... 51
TERMINOLOGY ..................................................... ... 52
SAE J1930 Terminology List ................................ ... 52
Page 3224 of 4731
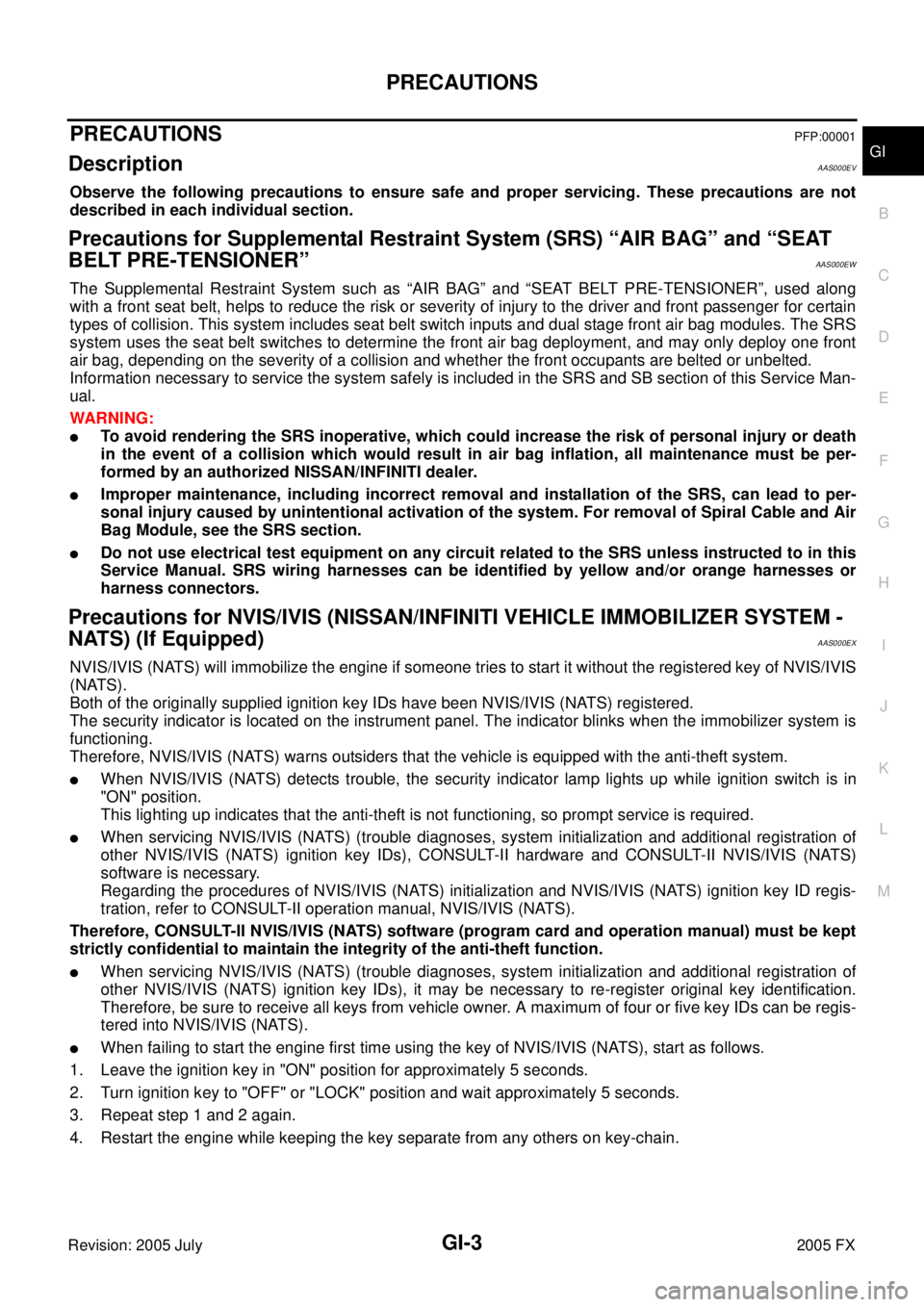
PRECAUTIONS GI-3
C
D E
F
G H
I
J
K L
M B
GI
Revision: 2005 July 2005 FX
PRECAUTIONSPFP:00001
DescriptionAAS000EV
Observe the following precautions to ensure safe and proper servicing. These precautions are not
described in each individual section.
Precautions for Supplemental Restraint System (SRS) “AIR BAG” and “SEAT
BELT PRE-TENSIONER”
AAS000EW
The Supplemental Restraint System such as “AIR BAG” and “SEAT BELT PRE-TENSIONER”, used along
with a front seat belt, helps to reduce the risk or severity of injury to the driver and front passenger for certain
types of collision. This system includes seat belt switch inputs and dual stage front air bag modules. The SRS
system uses the seat belt switches to determine the front air bag deployment, and may only deploy one front
air bag, depending on the severity of a collision and whether the front occupants are belted or unbelted.
Information necessary to service the system safely is included in the SRS and SB section of this Service Man-
ual.
WARNING:
To avoid rendering the SRS inoperative, which could increase the risk of personal injury or death
in the event of a collision which would result in air bag inflation, all maintenance must be per-
formed by an authorized NISSAN/INFINITI dealer.
Improper maintenance, including incorrect removal and installation of the SRS, can lead to per-
sonal injury caused by unintentional activation of the system. For removal of Spiral Cable and Air
Bag Module, see the SRS section.
Do not use electrical test equipment on any circuit related to the SRS unless instructed to in this
Service Manual. SRS wiring harnesses can be identified by yellow and/or orange harnesses or
harness connectors.
Precautions for NVIS/IVIS (NISSAN/INFINITI VEHICLE IMMOBILIZER SYSTEM -
NATS) (If Equipped)
AAS000EX
NVIS/IVIS (NATS) will immobilize the engine if someone tries to start it without the registered key of NVIS/IVIS
(NATS).
Both of the originally supplied ignition key IDs have been NVIS/IVIS (NATS) registered.
The security indicator is located on the instrument panel. The indicator blinks when the immobilizer system is
functioning.
Therefore, NVIS/IVIS (NATS) warns outsiders that the vehicle is equipped with the anti-theft system.
When NVIS/IVIS (NATS) detects trouble, the security indicator lamp lights up while ignition switch is in
"ON" position.
This lighting up indicates that the anti-theft is not functioning, so prompt service is required.
When servicing NVIS/IVIS (NATS) (trouble diagnoses, system initialization and additional registration of
other NVIS/IVIS (NATS) ignition key IDs), CONSULT-II hardware and CONSULT-II NVIS/IVIS (NATS)
software is necessary.
Regarding the procedures of NVIS/IVIS (NATS) initialization and NVIS/IVIS (NATS) ignition key ID regis-
tration, refer to CONSULT-II operation manual, NVIS/IVIS (NATS).
Therefore, CONSULT-II NVIS/IVIS (NATS) software (program card and operation manual) must be kept
strictly confidential to maintain the integrity of the anti-theft function.
When servicing NVIS/IVIS (NATS) (trouble diagnoses, system initialization and additional registration of
other NVIS/IVIS (NATS) ignition key IDs), it may be necessary to re-register original key identification.
Therefore, be sure to receive all keys from vehicle owner. A maximum of four or five key IDs can be regis-
tered into NVIS/IVIS (NATS).
When failing to start the engine first time using the key of NVIS/IVIS (NATS), start as follows.
1. Leave the ignition key in "ON" position for approximately 5 seconds.
2. Turn ignition key to "OFF" or "LOCK" position and wait approximately 5 seconds.
3. Repeat step 1 and 2 again.
4. Restart the engine while keeping the key separate from any others on key-chain.