Page 4505 of 4731
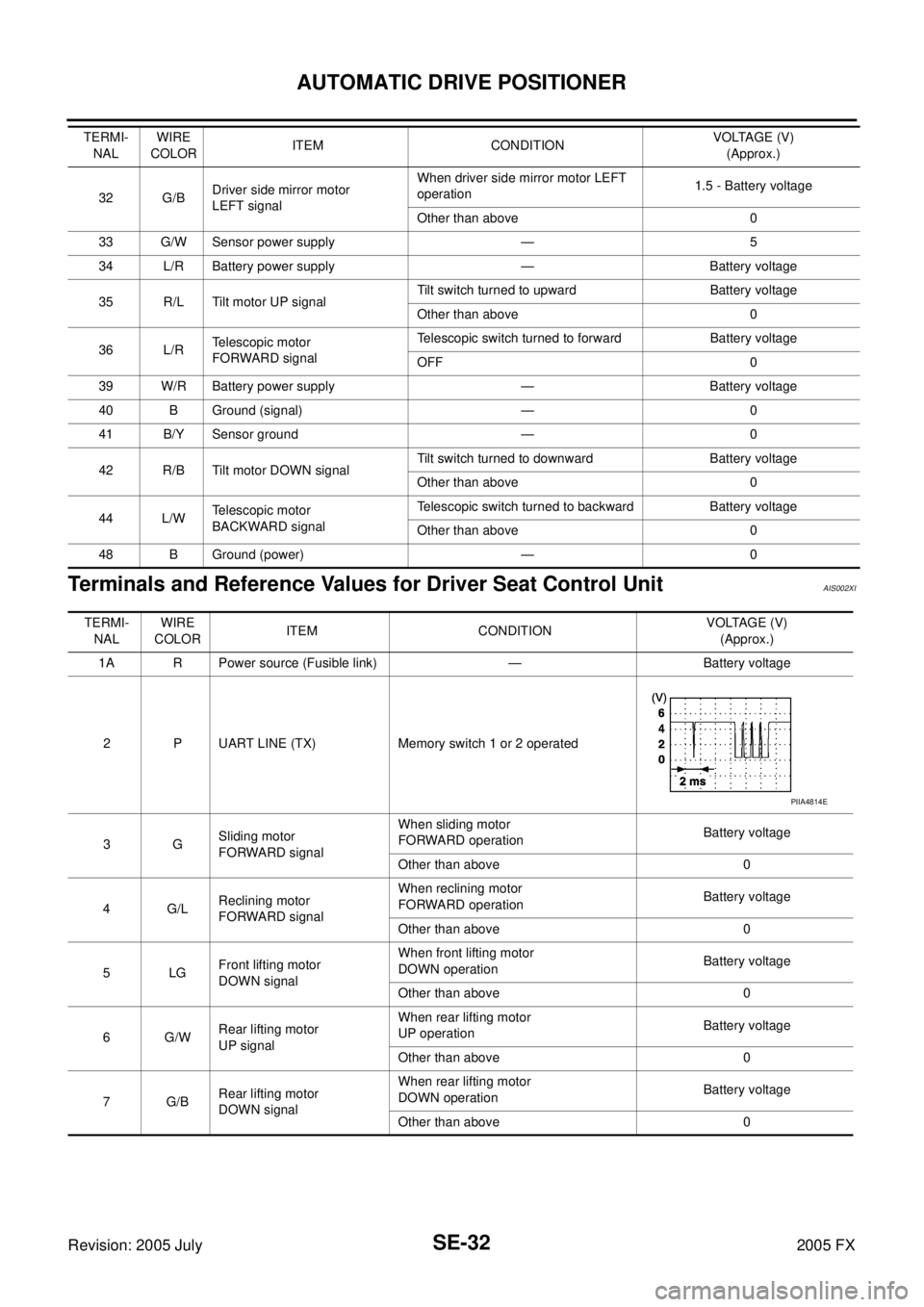
SE-32
AUTOMATIC DRIVE POSITIONER
Revision: 2005 July 2005 FX
Terminals and Reference Values for Driver Seat Control UnitAIS002XI
32 G/B Driver side mirror motor
LEFT signal When driver side mirror motor LEFT
operation 1.5 - Battery voltage
Other than above 0
33 G/W Sensor power supply — 5
34 L/R Battery power supply — Battery voltage
35 R/L Tilt motor UP signal Tilt switch turned to upward Battery voltage
Other than above 0
36 L/R Telescopic motor
FORWARD signal Telescopic switch turned to forward Battery voltage
OFF 0
39 W/R Battery power supply — Battery voltage
40 B Ground (signal) — 0
41 B/Y Sensor ground — 0
42 R/B Tilt motor DOWN signal Tilt switch turned to downward Battery voltage
Other than above 0
44 L/W Telescopic motor
BACKWARD signal Telescopic switch turned to backward Battery voltage
Other than above 0
48 B Ground (power) — 0
TERMI-
NAL WIRE
COLOR ITEM CONDITION VOLTAGE (V)
(Approx.)
TERMI-NAL WIRE
COLOR ITEM CONDITION VOLTAGE (V)
(Approx.)
1A R Power source (Fusible link) — Battery voltage
2 P UART LINE (TX) Memory switch 1 or 2 operated
3G Sliding motor
FORWARD signal When sliding motor
FORWARD operation Battery voltage
Other than above 0
4 G/L Reclining motor
FORWARD signal When reclining motor
FORWARD operation Battery voltage
Other than above 0
5LG Front lifting motor
DOWN signal When front lifting motor
DOWN operation Battery voltage
Other than above 0
6 G/W Rear lifting motor
UP signal When rear lifting motor
UP operation Battery voltage
Other than above 0
7 G/B Rear lifting motor
DOWN signal When rear lifting motor
DOWN operation Battery voltage
Other than above 0
PIIA4814E
Page 4506 of 4731
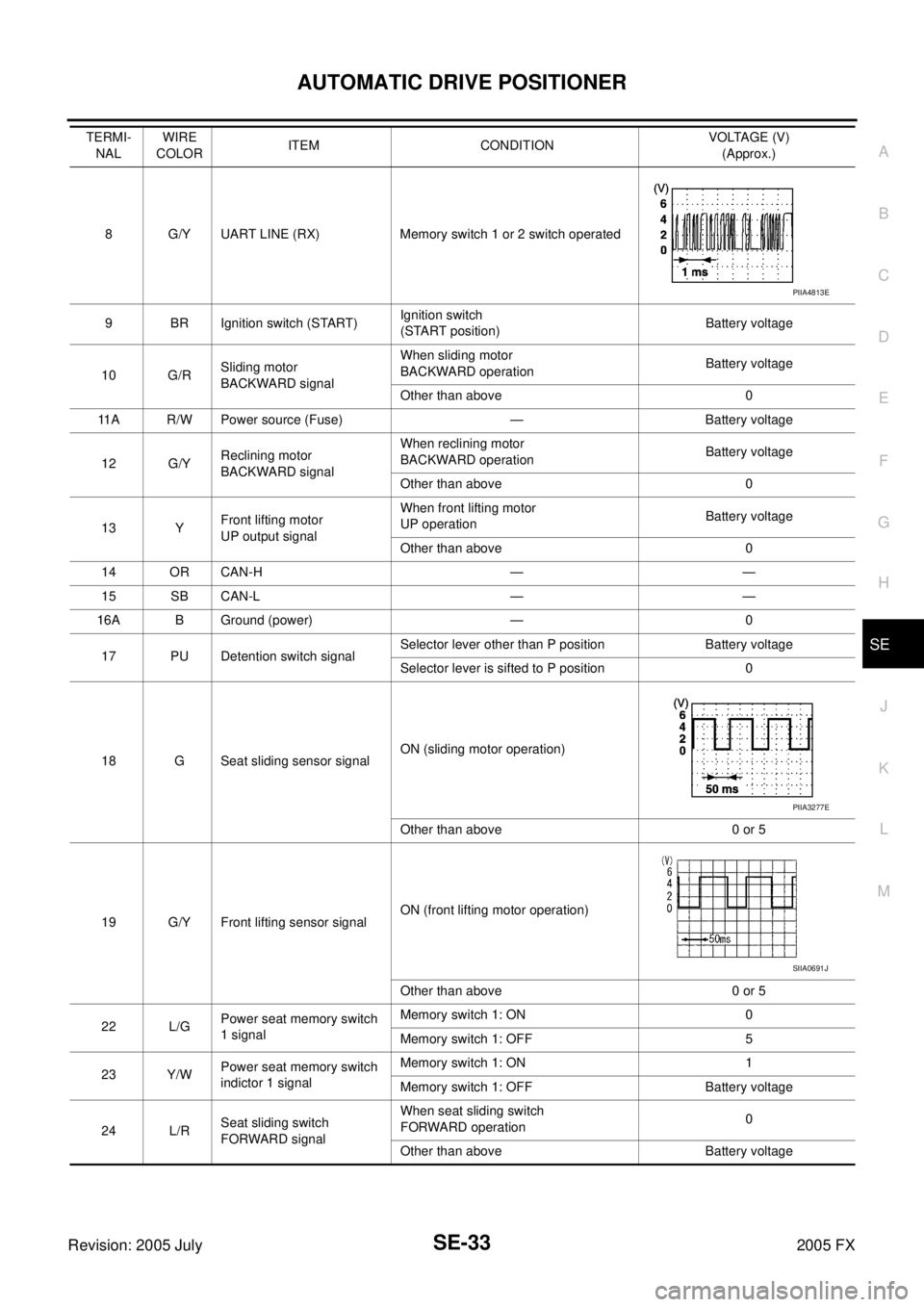
AUTOMATIC DRIVE POSITIONER SE-33
C
D E
F
G H
J
K L
M A
B
SE
Revision: 2005 July 2005 FX
8 G/Y UART LINE (RX) Memory switch 1 or 2 switch operated
9 BR Ignition switch (START) Ignition switch
(START position) Battery voltage
10 G/R Sliding motor
BACKWARD signal When sliding motor
BACKWARD operation Battery voltage
Other than above 0
11A R/W Power source (Fuse) — Battery voltage
12 G/Y Reclining motor
BACKWARD signal When reclining motor
BACKWARD operation Battery voltage
Other than above 0
13 Y Front lifting motor
UP output signal When front lifting motor
UP operation Battery voltage
Other than above 0
14 OR CAN-H — —
15 SB CAN-L — —
16A B Ground (power) — 0
17 PU Detention switch signal Selector lever other than P position Battery voltage
Selector lever is sifted to P position 0
18 G Seat sliding sensor signal ON (sliding motor operation)
Other than above 0 or 5
19 G/Y Front lifting sensor signal ON (front lifting motor operation)
Other than above 0 or 5
22 L/G Power seat memory switch
1 signal Memory switch 1: ON 0
Memory switch 1: OFF 5
23 Y/W Power seat memory switch
indictor 1 signal Memory switch 1: ON 1
Memory switch 1: OFF Battery voltage
24 L/R Seat sliding switch
FORWARD signal When seat sliding switch
FORWARD operation 0
Other than above Battery voltage
TERMI-
NAL WIRE
COLOR ITEM CONDITION VOLTAGE (V)
(Approx.)
PIIA4813E
PIIA3277E
SIIA0691J
Page 4507 of 4731
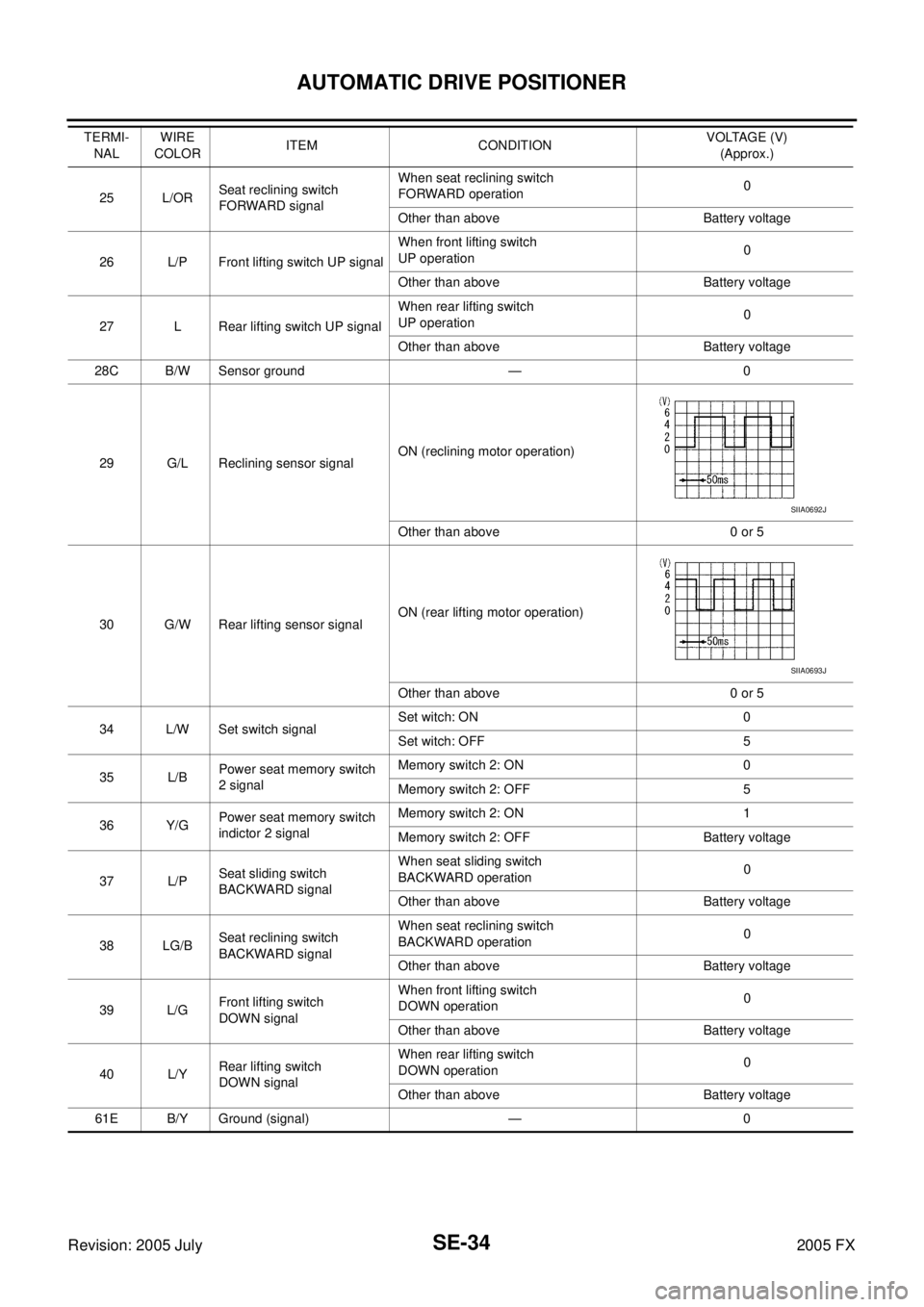
SE-34
AUTOMATIC DRIVE POSITIONER
Revision: 2005 July 2005 FX
25 L/OR Seat reclining switch
FORWARD signal When seat reclining switch
FORWARD operation 0
Other than above Battery voltage
26 L/P Front lifting switch UP signal When front lifting switch
UP operation 0
Other than above Battery voltage
27 L Rear lifting switch UP signal When rear lifting switch
UP operation 0
Other than above Battery voltage
28C B/W Sensor ground — 0
29 G/L Reclining sensor signal ON (reclining motor operation)
Other than above 0 or 5
30 G/W Rear lifting sensor signal ON (rear lifting motor operation)
Other than above 0 or 5
34 L/W Set switch signal Set witch: ON 0
Set witch: OFF 5
35 L/B Power seat memory switch
2 signal Memory switch 2: ON 0
Memory switch 2: OFF 5
36 Y/G Power seat memory switch
indictor 2 signal Memory switch 2: ON 1
Memory switch 2: OFF Battery voltage
37 L/P Seat sliding switch
BACKWARD signal When seat sliding switch
BACKWARD operation 0
Other than above Battery voltage
38 LG/B Seat reclining switch
BACKWARD signal When seat reclining switch
BACKWARD operation 0
Other than above Battery voltage
39 L/G Front lifting switch
DOWN signal When front lifting switch
DOWN operation 0
Other than above Battery voltage
40 L/Y Rear lifting switch
DOWN signal When rear lifting switch
DOWN operation 0
Other than above Battery voltage
61E B/Y Ground (signal) — 0
TERMI-
NAL WIRE
COLOR ITEM CONDITION VOLTAGE (V)
(Approx.)
SIIA0692J
SIIA0693J
Page 4508 of 4731
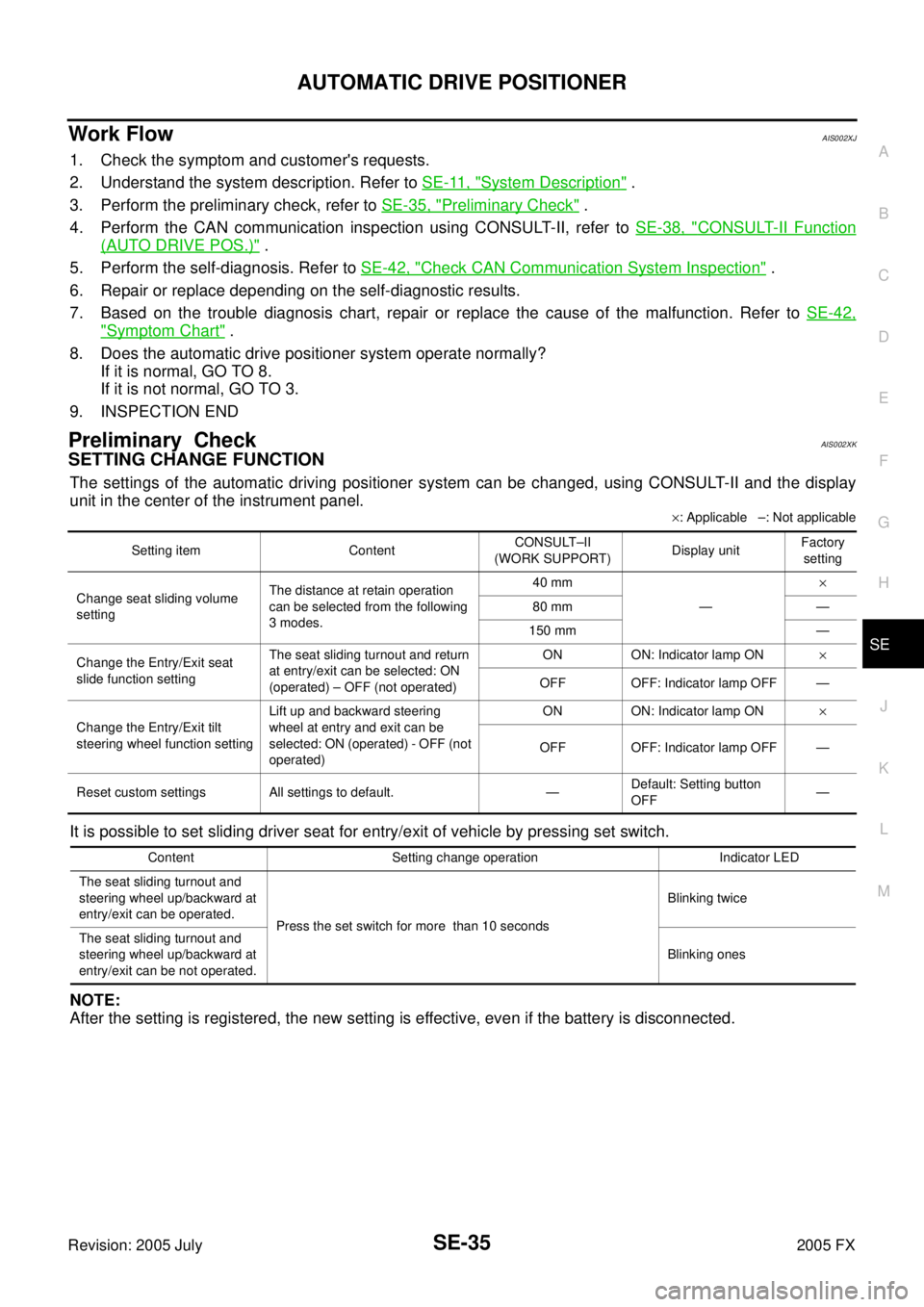
AUTOMATIC DRIVE POSITIONER SE-35
C
D E
F
G H
J
K L
M A
B
SE
Revision: 2005 July 2005 FX
Work Flow AIS002XJ
1. Check the symptom and customer's requests.
2. Understand the system description. Refer to SE-11, "
System Description" .
3. Perform the preliminary check, refer to SE-35, "
Preliminary Check" .
4. Perform the CAN communication inspection using CONSULT-II, refer to SE-38, "
CONSULT-II Function
(AUTO DRIVE POS.)" .
5. Perform the self-diagnosis. Refer to SE-42, "
Check CAN Communication System Inspection" .
6. Repair or replace depending on the self-diagnostic results.
7. Based on the trouble diagnosis chart, repair or replace the cause of the malfunction. Refer to SE-42,
"Symptom Chart" .
8. Does the automatic drive positioner system operate normally? If it is normal, GO TO 8.
If it is not normal, GO TO 3.
9. INSPECTION END
Preliminary CheckAIS002XK
SETTING CHANGE FUNCTION
The settings of the automatic driving positioner system can be changed, using CONSULT-II and the display
unit in the center of the instrument panel.
× : Applicable –: Not applicable
It is possible to set sliding driver seat for entry/exit of vehicle by pressing set switch.
NOTE:
After the setting is registered, the new setting is effective, even if the battery is disconnected.
Setting item Content CONSULT–II
(WORK SUPPORT) Display unitFactory
setting
Change seat sliding volume
setting The distance at retain operation
can be selected from the following
3 modes. 40 mm
— ×
80 mm —
150 mm —
Change the Entry/Exit seat
slide function setting The seat sliding turnout and return
at entry/exit can be selected: ON
(operated) – OFF (not operated) ON ON: Indicator lamp ON
×
OFF OFF: Indicator lamp OFF —
Change the Entry/Exit tilt
steering wheel function setting Lift up and backward steering
wheel at entry and exit can be
selected: ON (operated) - OFF (not
operated) ON ON: Indicator lamp ON
×
OFF OFF: Indicator lamp OFF —
Reset custom settings All settings to default. — Default: Setting button
OFF —
Content Setting change operation Indicator LED
The seat sliding turnout and
steering wheel up/backward at
entry/exit can be operated. Press the set switch for more than 10 seconds Blinking twice
The seat sliding turnout and
steering wheel up/backward at
entry/exit can be not operated. Blinking ones
Page 4509 of 4731
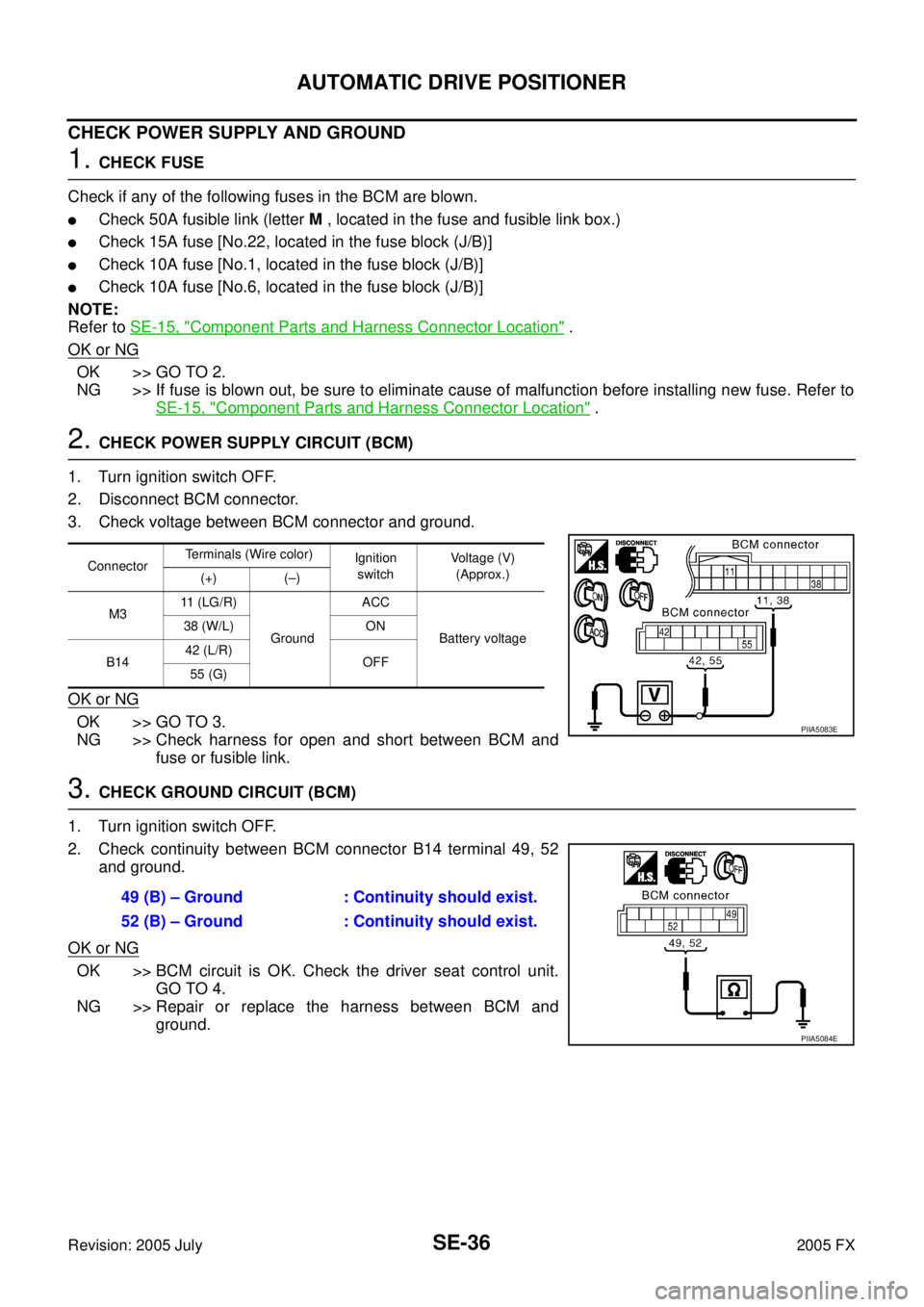
SE-36
AUTOMATIC DRIVE POSITIONER
Revision: 2005 July 2005 FX
CHECK POWER SUPPLY AND GROUND
1. CHECK FUSE
Check if any of the following fuses in the BCM are blown.
Check 50A fusible link (letter M , located in the fuse and fusible link box.)
Check 15A fuse [No.22, located in the fuse block (J/B)]
Check 10A fuse [No.1, located in the fuse block (J/B)]
Check 10A fuse [No.6, located in the fuse block (J/B)]
NOTE:
Refer to SE-15, "
Component Parts and Harness Connector Location" .
OK or NG
OK >> GO TO 2.
NG >> If fuse is blown out, be sure to eliminate cause of malfunction before installing new fuse. Refer to
SE-15, "
Component Parts and Harness Connector Location" .
2. CHECK POWER SUPPLY CIRCUIT (BCM)
1. Turn ignition switch OFF.
2. Disconnect BCM connector.
3. Check voltage between BCM connector and ground.
OK or NG
OK >> GO TO 3.
NG >> Check harness for open and short between BCM and fuse or fusible link.
3. CHECK GROUND CIRCUIT (BCM)
1. Turn ignition switch OFF.
2. Check continuity between BCM connector B14 terminal 49, 52 and ground.
OK or NG
OK >> BCM circuit is OK. Check the driver seat control unit. GO TO 4.
NG >> Repair or replace the harness between BCM and ground.
Connector Terminals (Wire color)
Ignition
switch Voltage (V)
(Approx.)
(+) (–)
M3 11 (LG/R)
Ground ACC
Battery voltage
38 (W/L) ON
B14 42 (L/R)
OFF
55 (G)
PIIA5083E
49 (B) – Ground : Continuity should exist.
52 (B) – Ground : Continuity should exist.
PIIA5084E
Page 4510 of 4731
![INFINITI FX35 2005 Service Manual AUTOMATIC DRIVE POSITIONER SE-37
C
D E
F
G H
J
K L
M A
B
SE
Revision: 2005 July 2005 FX
4. CHECK FUSE
Check 10A fuse [No.9, located in fuse block (J/B)].
NOTE:
Refer to SE-15, "
Comp INFINITI FX35 2005 Service Manual AUTOMATIC DRIVE POSITIONER SE-37
C
D E
F
G H
J
K L
M A
B
SE
Revision: 2005 July 2005 FX
4. CHECK FUSE
Check 10A fuse [No.9, located in fuse block (J/B)].
NOTE:
Refer to SE-15, "
Comp](/manual-img/42/57020/w960_57020-4509.png)
AUTOMATIC DRIVE POSITIONER SE-37
C
D E
F
G H
J
K L
M A
B
SE
Revision: 2005 July 2005 FX
4. CHECK FUSE
Check 10A fuse [No.9, located in fuse block (J/B)].
NOTE:
Refer to SE-15, "
Component Parts and Harness Connector Location" .
OK or NG
OK >> GO TO 5.
NG >> If fuse is blown out, be sure to eliminate cause of malfunction before installing new fuse. Refer to
SE-15, "
Component Parts and Harness Connector Location" .
5. CHECK POWER SUPPLY CIRCUIT (DRIVER SEAT CONTROL UNIT)
1. Disconnect driver seat control unit connector.
2. Check voltage between driver seat control unit and ground.
OK or NG
OK >> GO TO 6.
NG >> Repair or replace harness between driver seat control
unit and fuse block (J/B).
6. CHECK GROUND CIRCUIT (DRIVER SEAT CONTROL UNIT)
1. Turn ignition switch OFF.
2. Check continuity between the driver seat control unit connector B152, B153 terminal16A, 61E and ground.
OK or NG
OK >> GO TO 7.
NG >> Repair or replace harness between driver seat control unit and ground.
7. CHECK POWER SUPPLY CIRCUIT (AUTOMATIC DRIVE POSITIONER CONTROL UNIT)
1. Disconnect automatic drive positioner control unit connector.
2. Check voltage between automatic drive positioner control unit and ground.
OK or NG
OK >> GO TO 8.
NG >> Repair or replace harness between automatic drive positioner control unit and fuse block (J/B).
Connector Terminals (Wire color)
Ignition
switch Voltage (V)
(Approx.)
(+) (–)
B152 9 (BR)
Ground START
Battery voltage
B153 1A (R)
OFF
11 A ( R / W )
PIIA5085E
16A (B) – Ground : Continuity should exist.
61E (B/Y) – Ground : Continuity should exist.
PIIA5087E
Connector Terminals (Wire color)
Ignition
switch Voltage (V)
(Approx.)
(+) (–)
M49 28 (SB) Ground START
Battery voltage
M50 34 (L/R)
M50 39 (W/R) OFF
PIIA5086E
Page 4511 of 4731
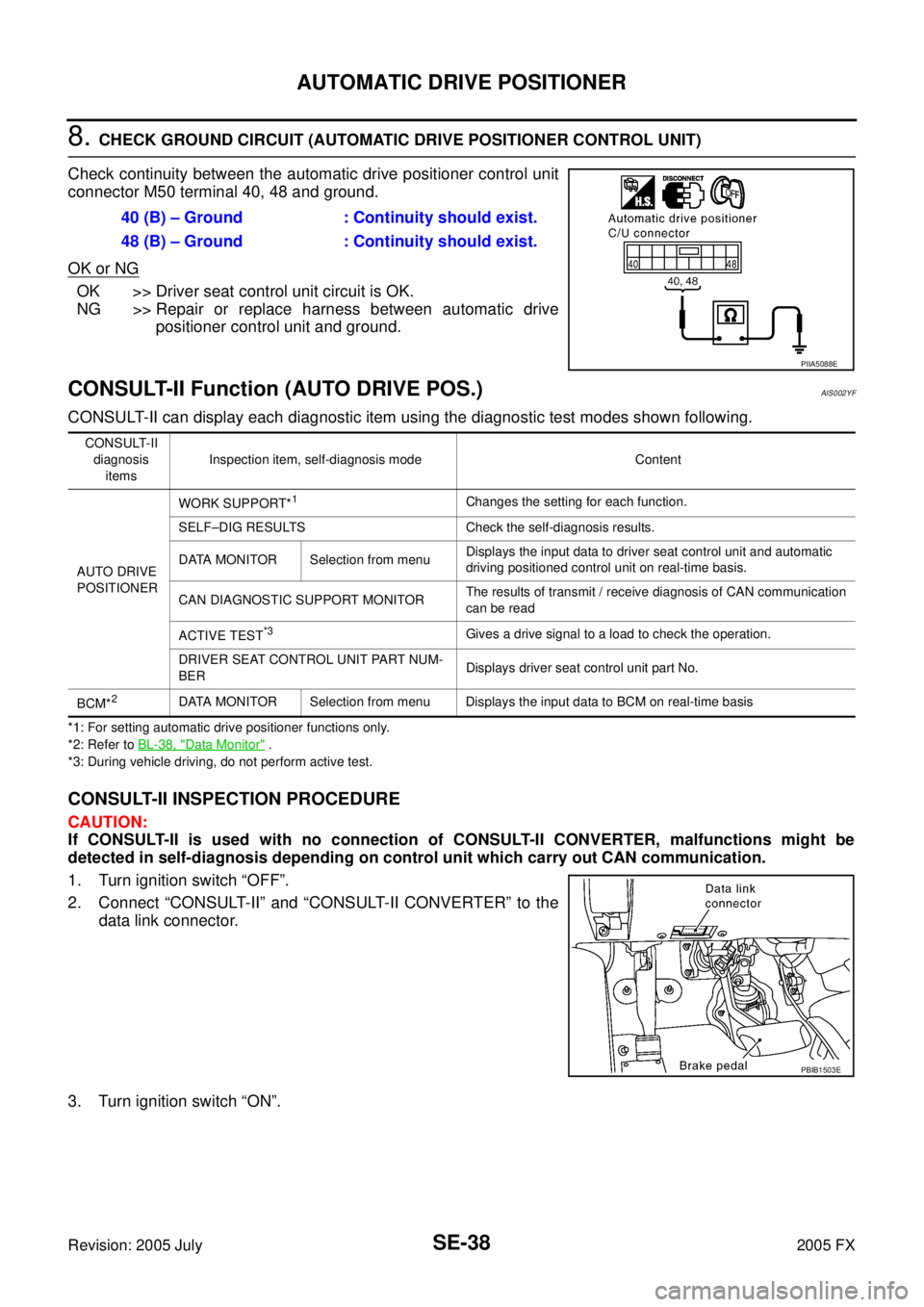
SE-38
AUTOMATIC DRIVE POSITIONER
Revision: 2005 July 2005 FX
8. CHECK GROUND CIRCUIT (AUTOMATIC DRIVE POSITIONER CONTROL UNIT)
Check continuity between the automatic drive positioner control unit
connector M50 terminal 40, 48 and ground.
OK or NG
OK >> Driver seat control unit circuit is OK.
NG >> Repair or replace harness between automatic drive positioner control unit and ground.
CONSULT-II Function (AUTO DRIVE POS.)AIS002YF
CONSULT-II can display each diagnostic item using the diagnostic test modes shown following.
*1: For setting automatic drive positioner functions only.
*2: Refer to BL-38, "
Data Monitor" .
*3: During vehicle driving, do not perform active test.
CONSULT-II INSPECTION PROCEDURE
CAUTION:
If CONSULT-II is used with no connection of CONSULT-II CONVERTER, malfunctions might be
detected in self-diagnosis depending on control unit which carry out CAN communication.
1. Turn ignition switch “OFF”.
2. Connect “CONSULT-II” and “CONSULT-II CONVERTER” to the data link connector.
3. Turn ignition switch “ON”. 40 (B) – Ground : Continuity should exist.
48 (B) – Ground : Continuity should exist.
PIIA5088E
CONSULT-II diagnosis items Inspection item, self-diagnosis mode Content
AUTO DRIVE
POSITIONER WORK SUPPORT*
1Changes the setting for each function.
SELF–DIG RESULTS Check the self-diagnosis results.
DATA MONITOR Selection from menu Displays the input data to driver seat control unit and automatic
driving positioned control unit on real-time basis.
CAN DIAGNOSTIC SUPPORT MONITOR The results of transmit / receive diagnosis of CAN communication
can be read
ACTIVE TEST
*3Gives a drive signal to a load to check the operation.
DRIVER SEAT CONTROL UNIT PART NUM-
BER Displays driver seat control unit part No.
BCM*
2DATA MONITOR Selection from menu Displays the input data to BCM on real-time basis
PBIB1503E
Page 4512 of 4731
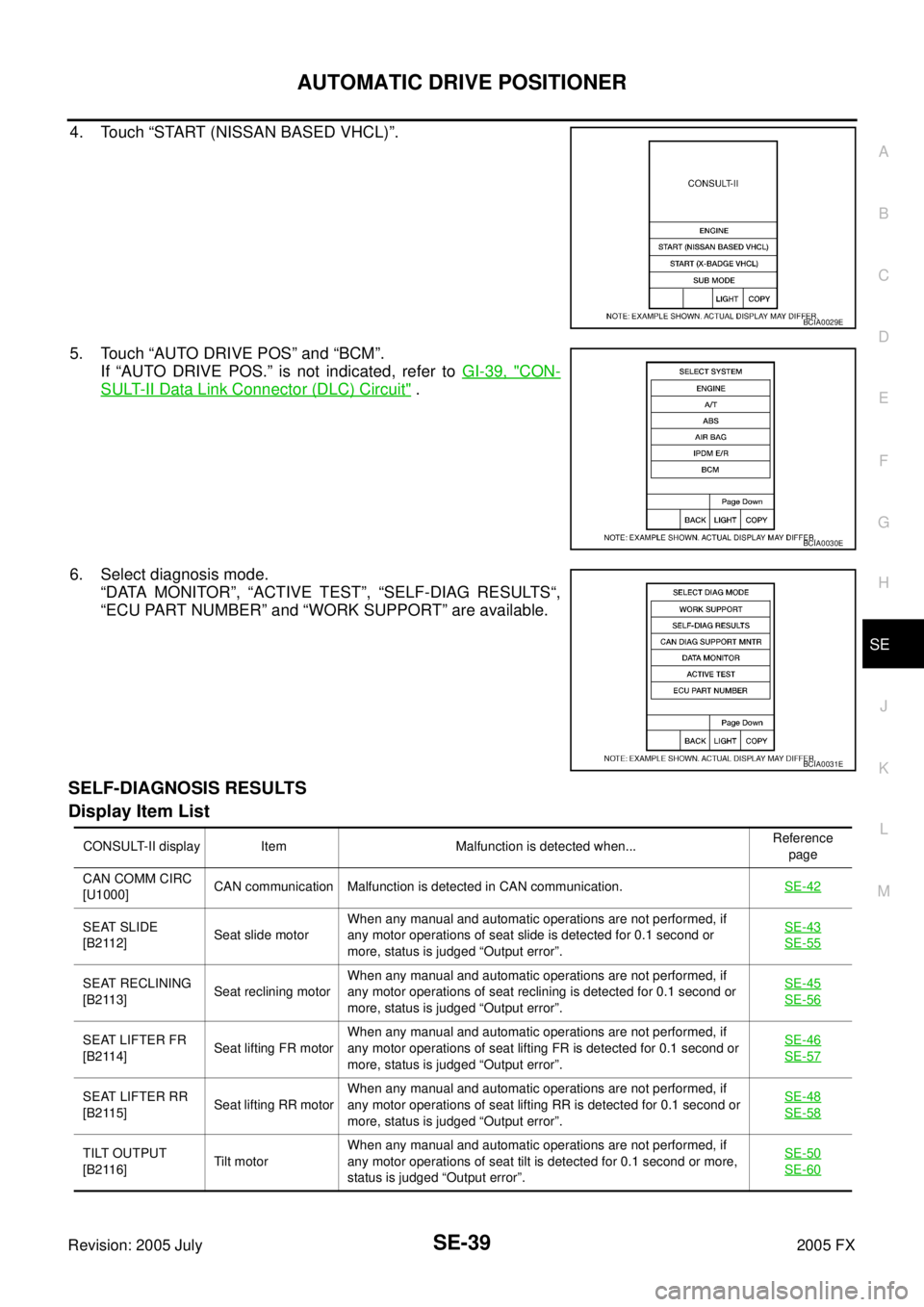
AUTOMATIC DRIVE POSITIONER SE-39
C
D E
F
G H
J
K L
M A
B
SE
Revision: 2005 July 2005 FX
4. Touch “START (NISSAN BASED VHCL)”.
5. Touch “AUTO DRIVE POS” and “BCM”.
If “AUTO DRIVE POS.” is not indicated, refer to GI-39, "
CON-
SULT-II Data Link Connector (DLC) Circuit" .
6. Select diagnosis mode. “DATA MONITOR”, “ACTIVE TEST”, “SELF-DIAG RESULTS“,
“ECU PART NUMBER” and “WORK SUPPORT” are available.
SELF-DIAGNOSIS RESULTS
Display Item List
BCIA0029E
BCIA0030E
BCIA0031E
CONSULT-II display Item Malfunction is detected when... Reference
page
CAN COMM CIRC
[U1000] CAN communication Malfunction is detected in CAN communication.
SE-42
SEAT SLIDE
[B2112] Seat slide motor When any manual and automatic operations are not performed, if
any motor operations of seat slide is detected for 0.1 second or
more, status is judged “Output error”. SE-43
SE-55
SEAT RECLINING
[B2113] Seat reclining motor When any manual and automatic operations are not performed, if
any motor operations of seat reclining is detected for 0.1 second or
more, status is judged “Output error”. SE-45
SE-56
SEAT LIFTER FR
[B2114] Seat lifting FR motor When any manual and automatic operations are not performed, if
any motor operations of seat lifting FR is detected for 0.1 second or
more, status is judged “Output error”. SE-46
SE-57
SEAT LIFTER RR
[B2115] Seat lifting RR motor When any manual and automatic operations are not performed, if
any motor operations of seat lifting RR is detected for 0.1 second or
more, status is judged “Output error”. SE-48
SE-58
TILT OUTPUT
[B2116] Tilt motor When any manual and automatic operations are not performed, if
any motor operations of seat tilt is detected for 0.1 second or more,
status is judged “Output error”. SE-50
SE-60