Page 73 of 2893
Î
(#'
)
4-25
Circuit Diagram
6
3
191 F5
17 D2
A3
A2 H1
ELD
CANL
CANH
ALTF ALTC ALTL
5V
ALTERNATOR DRIVER
YEL
FR L C IG BRN
ELD
A23 GAUGE CONTROL MODULE (TACH)
IGNITION SWITCH
BATIG1
B43 B42 B41 A37
A36 RED
WHT CPU
YEL
1
BLK/YEL
No. 2 (50 A)
BLK
RECTIFIER
BATTERY
VOLTAGE REGULATOR2
3
4
B
BLK
G301
UNDER-HOOD FUSE/RELAY BOX
No. 1 (100 A)
ORN
WHT/RED WHT/GRNWHT/BLU UNDER-DASH
FUSE/RELAY BOX
CHARGING
SYSTEM
INDICATOR
IG1 HOT in ON (II)
and START (III)
A1
ECM/PCM BLU
Q9
WHT
22
17C101
CANH
CANL
YEL
No. 10
(7.5 A)
No. 3
(10 A)
08/08/21 14:10:10 61SNR030_040_0026
ProCarManuals.com
DYNOMITE -2009-
Page 74 of 2893
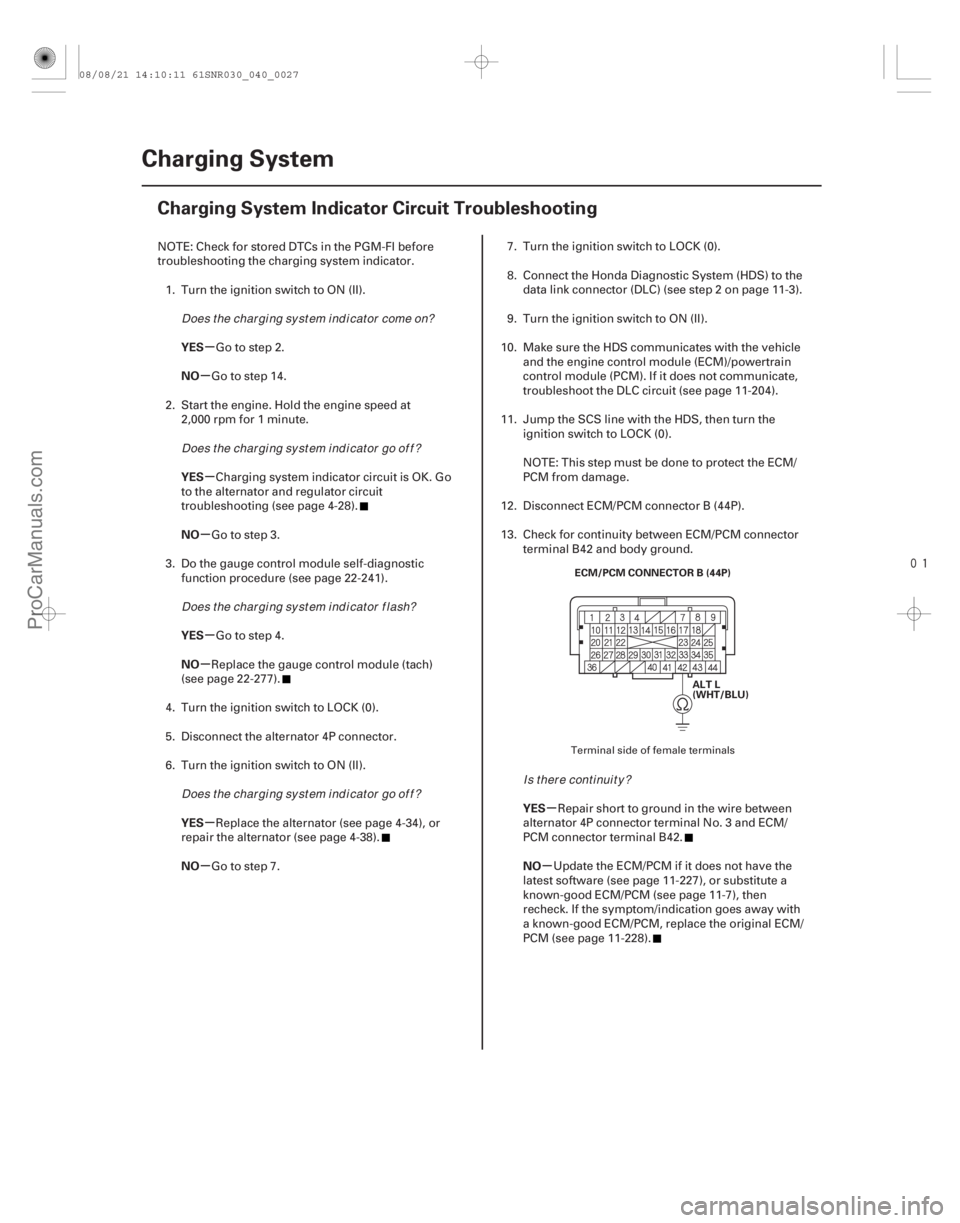
(#'
)
µ
µ
µ
µ
µ
µ
µ
µ µ
µ
YES
NO
YES
NO
YES
NO
YES
NO
YES
NO
4-26Charging System
Charging System Indicator Circuit Troubleshooting
ALT L
(WHT/BLU)
ECM/PCM CONNECTOR B (44P)
NOTE: Check for stored DTCs in the PGM-FI before
troubleshooting the charging system indicator.
1. Turn the ignition switch to ON (II).
Go to step 2.
Go to step 14.
2. Start the engine. Hold the engine speed at 2,000 rpm for 1 minute.
Charging system indicator circuit is OK. Go
to the alternator and regulator circuit
troubleshooting (see page 4-28).
Go to step 3.
3. Do the gauge control module self-diagnostic function procedure (see page 22-241).
Go to step 4.
Replace the gauge control module (tach)
(see page 22-277).
4. Turn the ignition switch to LOCK (0).
5. Disconnect the alternator 4P connector.
6. Turn the ignition switch to ON (II).
Replace the alternator (see page 4-34), or
repair the alternator (see page 4-38).
Go to step 7. 7. Turn the ignition switch to LOCK (0).
8. Connect the Honda Diagnostic System (HDS) to the
data link connector (DLC) (see step 2 on page 11-3).
9. Turn the ignition switch to ON (II).
10. Make sure the HDS communicates with the vehicle and the engine control module (ECM)/powertrain
control module (PCM). If it does not communicate,
troubleshoot the DLC circuit (see page 11-204).
11. Jump the SCS line with the HDS, then turn the ignition switch to LOCK (0).
NOTE: This step must be done to protect the ECM/
PCMfromdamage.
12. Disconnect ECM/PCM connector B (44P).
13. Check for continuity between ECM/PCM connector terminal B42 and body ground.
Repair short to ground in the wire between
alternator 4P connector terminal No. 3 and ECM/
PCM connector terminal B42.
Update the ECM/PCM if it does not have the
latest software (see page 11-227), or substitute a
known-good ECM/PCM (see page 11-7), then
recheck. If the symptom/indication goes away with
a known-good ECM/PCM, replace the original ECM/
PCM (see page 11-228).
Terminal side of female terminals
Does t he char gi ng sy st em i nd i cat or come on?
Does t he char gi ng sy st em i nd i cat or go of f ?
Does t he char gi ng sy st em i nd i cat or f l ash?
Does t he char gi ng sy st em i nd i cat or go of f ? Is there continuity?
08/08/21 14:10:11 61SNR030_040_0027
ProCarManuals.com
DYNOMITE -2009-
Page 75 of 2893
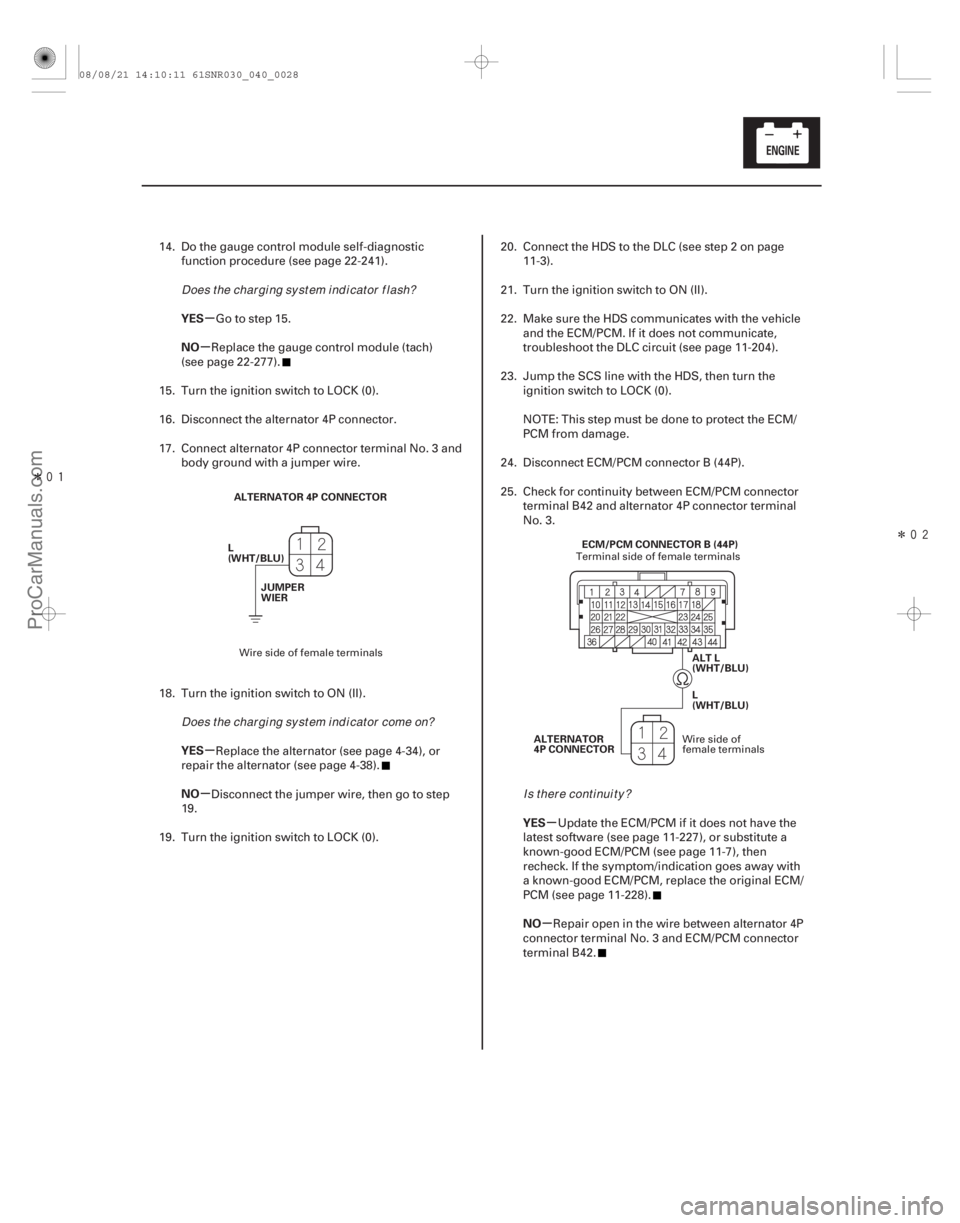
Î
Î
µ
µ
µ
µ µ
µ
YES
NO
YES
NO
YES
NO
4-27
ALTERNATOR 4P CONNECTOR
L
(WHT/BLU) JUMPER
WIER
ALT L
(WHT/BLU)
ECM/PCM CONNECTOR B (44P)
L
(WHT/BLU)
ALTERNATOR
4P CONNECTOR
14. Do the gauge control module self-diagnostic function procedure (see page 22-241).
Go to step 15.
Replace the gauge control module (tach)
(see page 22-277).
15. Turn the ignition switch to LOCK (0).
16. Disconnect the alternator 4P connector.
17. Connect alternator 4P connector terminal No. 3 and body ground with a jumper wire.
18. Turn the ignition switch to ON (II). Replace the alternator (see page 4-34), or
repair the alternator (see page 4-38).
Disconnect the jumper wire, then go to step
19.
19. Turn the ignition switch to LOCK (0). 20. Connect the HDS to the DLC (see step 2 on page
11-3).
21. Turn the ignition switch to ON (II).
22. Make sure the HDS communicates with the vehicle and the ECM/PCM. If it does not communicate,
troubleshoot the DLC circuit (see page 11-204).
23. Jump the SCS line with the HDS, then turn the ignition switch to LOCK (0).
NOTE: This step must be done to protect the ECM/
PCMfromdamage.
24. Disconnect ECM/PCM connector B (44P).
25. Check for continuity between ECM/PCM connector terminal B42 and alternator 4P connector terminal
No. 3.
Update the ECM/PCM if it does not have the
latest software (see page 11-227), or substitute a
known-good ECM/PCM (see page 11-7), then
recheck. If the symptom/indication goes away with
a known-good ECM/PCM, replace the original ECM/
PCM (see page 11-228).
Repair open in the wire between alternator 4P
connector terminal No. 3 and ECM/PCM connector
terminal B42.
Wire side of female terminals Terminal side of female terminals
Wire side of
female terminals
Does t he char gi ng sy st em i nd i cat or f l ash?
Does t he char gi ng sy st em i nd i cat or come on? Is there continuity?
08/08/21 14:10:11 61SNR030_040_0028
ProCarManuals.com
DYNOMITE -2009-
Page 76 of 2893
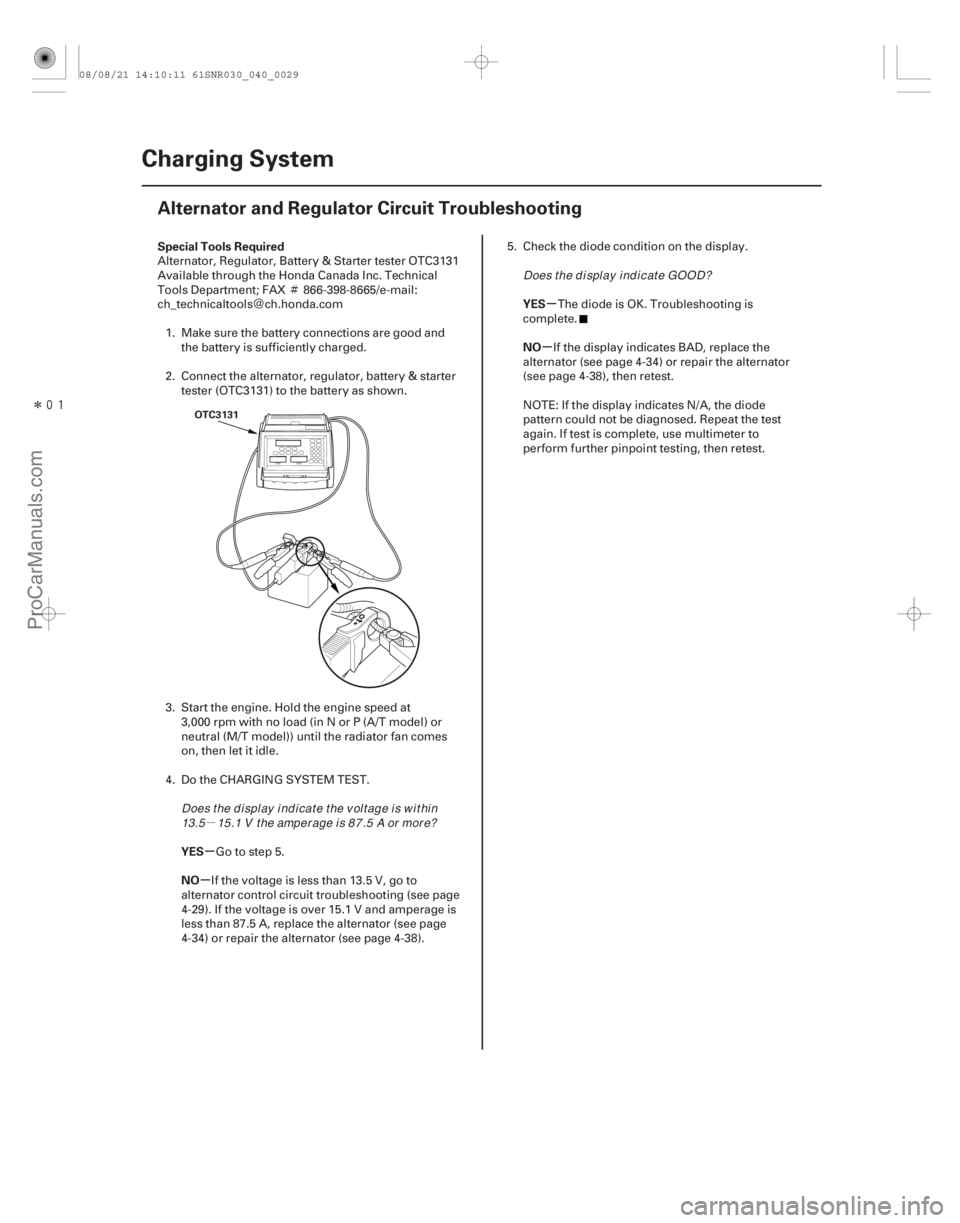
µÌ
Ï
Î
(#'
)
µ
µ µ
µ
Special Tools Required
YES
NO YES
NO
4-28
Charging System
Alternator and Regulator Circuit Troubleshooting
OTC3131
Alternator, Regulator, Battery & Starter tester OTC3131
Available through the Honda Canada Inc. Technical
Tools Department; FAX
866-398-8665/e-mail:
ch_technicaltools ch.honda.com
1. Make sure the battery connections are good and the battery is sufficiently charged.
2. Connect the alternator, regulator, battery & starter tester (OTC3131) to the battery as shown.
3. Start the engine. Hold the engine speed at 3,000 rpm with no load (in N or P (A/T model) or
neutral (M/T model)) until the radiator fan comes
on, then let it idle.
4. Do the CHARGING SYSTEM TEST.
Go to step 5.
If the voltage is less than 13.5 V, go to
alternator control circuit troubleshooting (see page
4-29). If the voltage is over 15.1 V and amperage is
less than 87.5 A, replace the alternator (see page
4-34) or repair the alternator (see page 4-38). 5. Check the diode condition on the display.
The diode is OK. Troubleshooting is
complete.
If the display indicates BAD, replace the
alternator (see page 4-34) or repair the alternator
(see page 4-38), then retest.
NOTE: If the display indicates N/A, the diode
pattern could not be diagnosed. Repeat the test
again. If test is complete, use multimeter to
perform further pinpoint testing, then retest.
Does the display indicate the voltage is within 13.5 15 .1 V t he amper age i s 87 .5 A or mor e? Does t he d i spl ay i nd i cat e GOOD?
08/08/21 14:10:11 61SNR030_040_0029
ProCarManuals.com
DYNOMITE -2009-
Page 77 of 2893
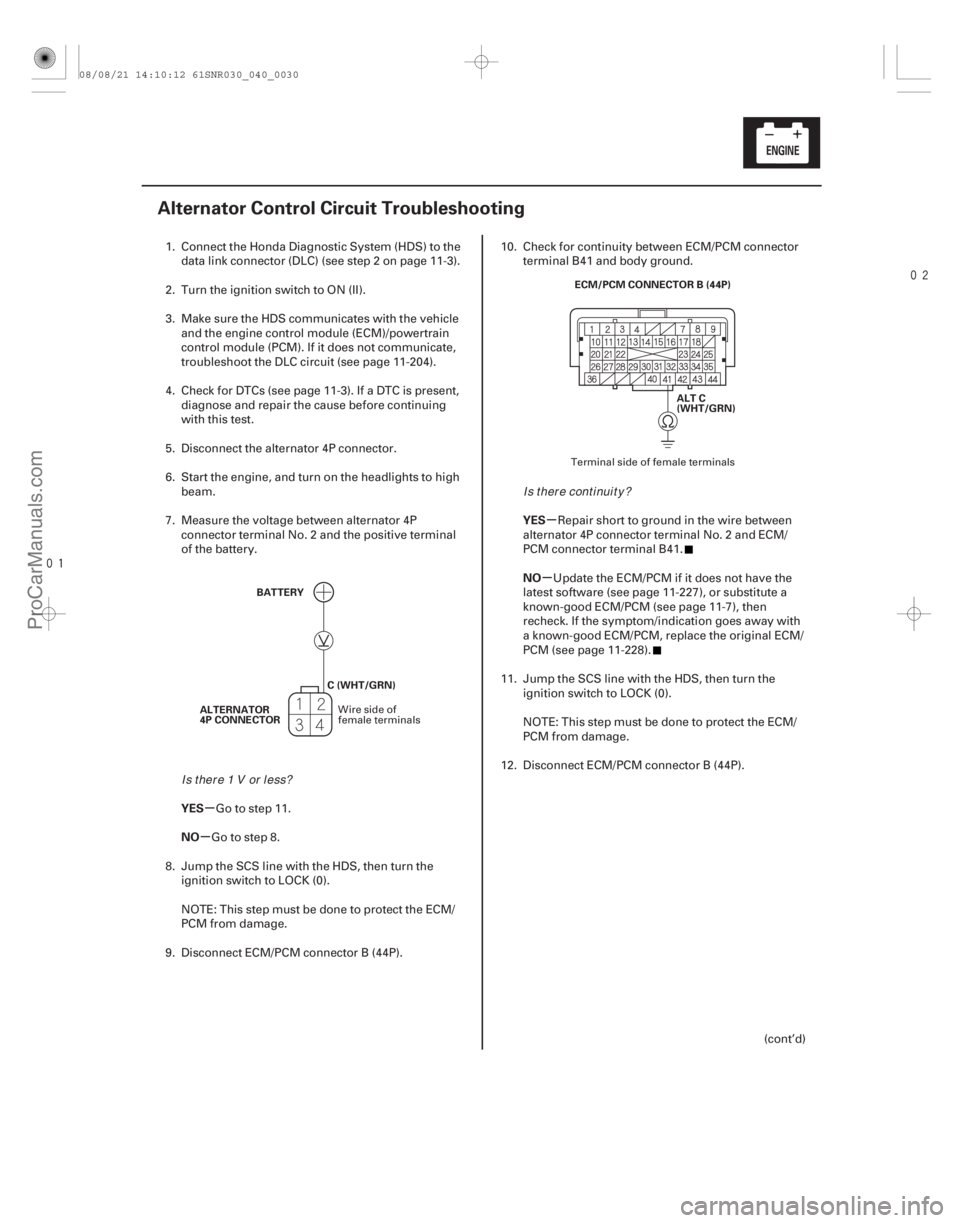
(#'
)
µ
µ µ
µ
YES
NO YES
NO
4-29
Alternator Control Circuit Troubleshooting
BATTERY
ALTERNATOR
4P CONNECTOR C (WHT/GRN) ALT C
(WHT/GRN)
ECM/PCM CONNECTOR B (44P)
1. Connect the Honda Diagnostic System (HDS) to the
data link connector (DLC) (see step 2 on page 11-3).
2. Turn the ignition switch to ON (II).
3. Make sure the HDS communicates with the vehicle and the engine control module (ECM)/powertrain
control module (PCM). If it does not communicate,
troubleshoot the DLC circuit (see page 11- 204).
4. Check for DTCs (see page 11-3). If a DTC is present, diagnose and repair the cause before continuing
with this test.
5. Disconnect the alternator 4P connector.
6. Start the engine, and turn on the headlights to high beam.
7. Measure the voltage between alternator 4P connector terminal No. 2 and the positive terminal
of the battery.
Go to step 11.
Go to step 8.
8. Jump the SCS line with the HDS, then turn the ignition switch to LOCK (0).
NOTE: This step must be done to protect the ECM/
PCM from damage.
9. Disconnect ECM/PCM connector B (44P). 10. Check for continuity between ECM/PCM connector
terminal B41 and body ground.
Repair short to ground in the wire between
alternator 4P connector terminal No. 2 and ECM/
PCM connector terminal B41.
Update the ECM/PCM if it does not have the
latest software (see page 11-227), or substitute a
known-good ECM/PCM (see page 11-7), then
recheck. If the symptom/indication goes away with
a known-good ECM/PCM, replace the original ECM/
PCM (see page 11-228).
11. Jump the SCS line with the HDS, then turn the ignition switch to LOCK (0).
NOTE: This step must be done to protect the ECM/
PCMfromdamage.
12. Disconnect ECM/PCM connector B (44P).
(cont’d)
Wire side of
female terminals Terminal side of female terminals
Is t her e 1 V or l ess?
Is there continuity?
08/08/21 14:10:12 61SNR030_040_0030
ProCarManuals.com
DYNOMITE -2009-
Page 78 of 2893
Î
(#'
")
µ
µ
YES
NO
4-304-30 Charging System
Alternator Control Circuit
Troubleshooting (cont’d)
Drive Belt Inspection
C (WHT/GRN)
ALTERNATOR
4P CONNECTOR ALT C
(WHT/GRN)
ECM/PCM CONNECTOR B (44P)
A
B
13. Check for continuity between ECM/PCM connector terminal B41 and alternator 4P connector terminal
No. 2.
Replace the alternator (see page 4-34), or
repair the alternator (see page 4-38).
Repair open in the wire between alternator 4P
connector terminal No. 2 and ECM/PCM connector
terminal B41. 1. Inspect the belt for cracks or damage. If the belt is
cracked or damaged, replace it (see page 4-31).
2. Check the position of the auto-tensioner indicator (A) is within the standard range (B) as shown. If it is
out of the standard range, replace the drive belt
(see page 4-31).
Wire side of
female terminals
Terminal side of female terminals
Is there continuity?
08/08/21 14:10:12 61SNR030_040_0031
ProCarManuals.com
DYNOMITE -2009-
Page 79 of 2893
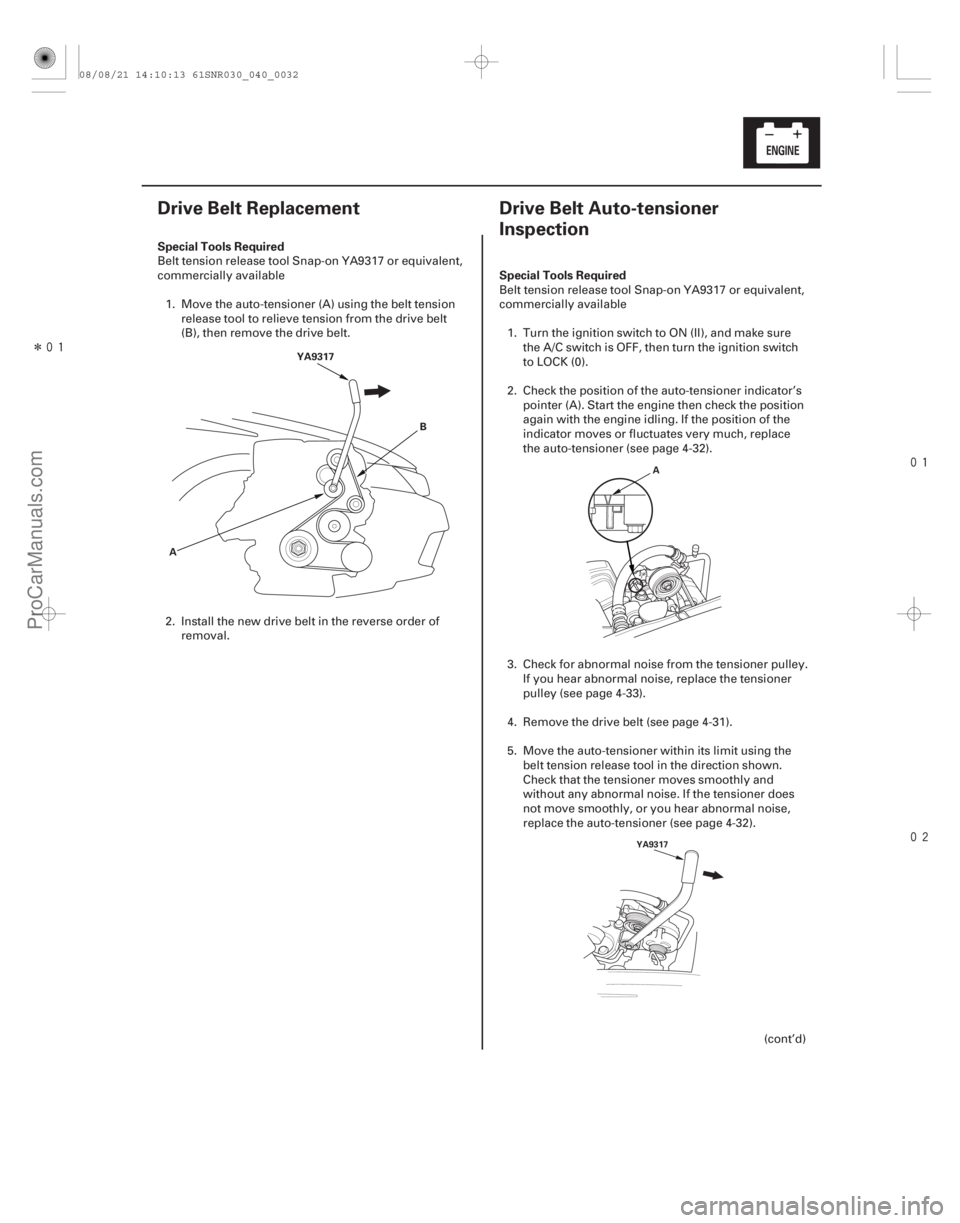
Î
(#'
)
(#'
")
Special Tools Required
Special Tools Required
4-314-31
Drive Belt ReplacementDrive Belt Auto-tensioner
Inspection
YA9317
A B
A
YA9317
Belt tension release tool Snap-on YA9317 or equivalent,
commercially available
1. Move the auto-tensioner (A) using the belt tension release tool to relieve tension from the drive belt
(B), then remove the drive belt.
2. Install the new drive belt in the reverse order of removal. Belt tension release tool Snap-on YA9317 or equivalent,
commercially available
1. Turn the ignition switch to ON (II), and make sure the A/C switch is OFF, then turn the ignition switch
to LOCK (0).
2. Check the position of the auto-tensioner indicator’s pointer (A). Start the engine then check the position
again with the engine idling. If the position of the
indicator moves or fluctuates very much, replace
the auto-tensioner (see page 4-32).
3. Check for abnormal noise from the tensioner pulley. If you hear abnormal noise, replace the tensioner
pulley(seepage4-33).
4. Remove the drive belt (see page 4-31).
5. Move the auto-tensioner within its limit using the belt tension release tool in the direction shown.
Check that the tensioner moves smoothly and
without any abnormal noise. If the tensioner does
not move smoothly, or you hear abnormal noise,
replace the auto-tensioner (see page 4-32).
(cont’d)
08/08/21 14:10:13 61SNR030_040_0032
ProCarManuals.com
DYNOMITE -2009-
Page 80 of 2893
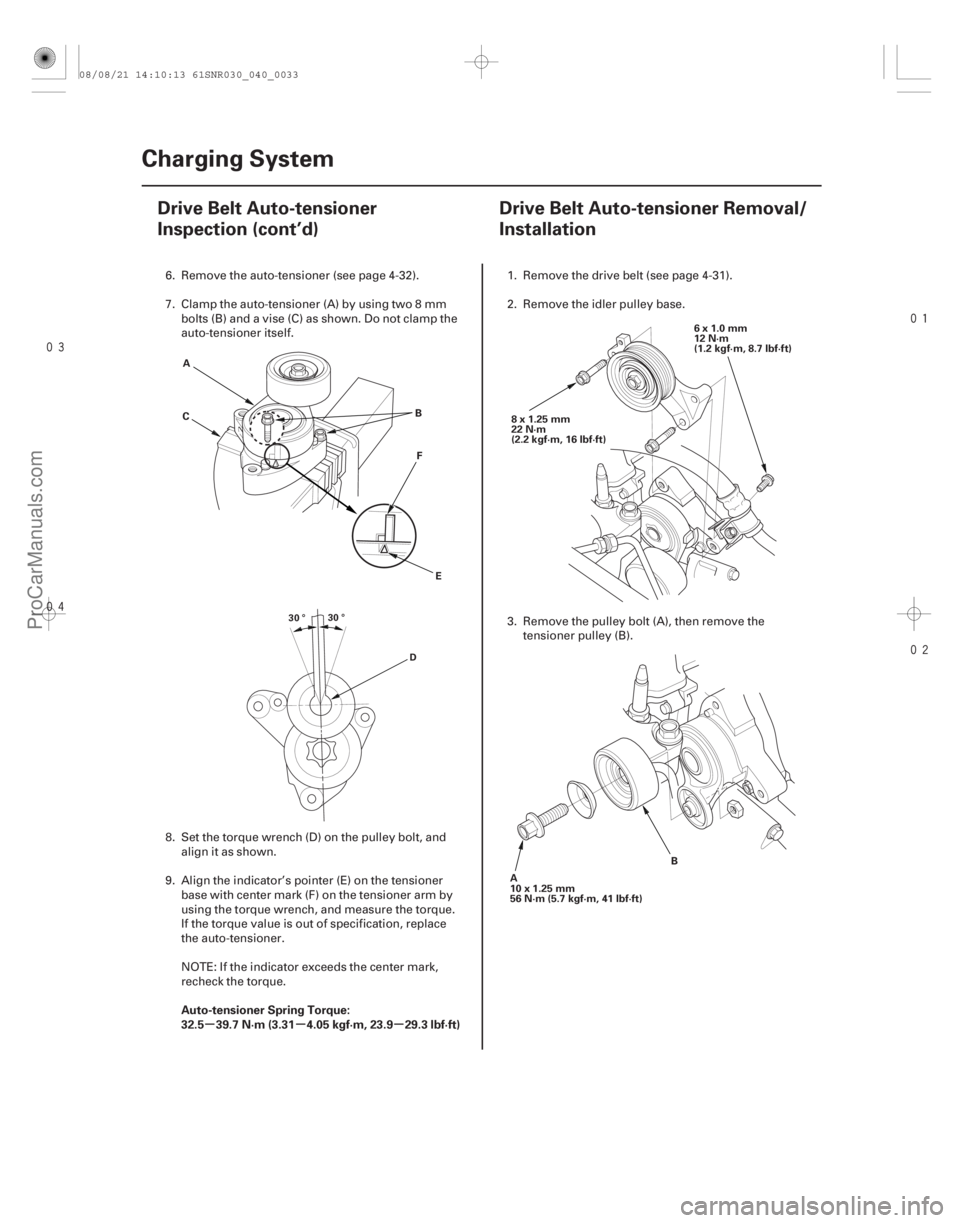
(#'
)
µµ µ
Auto-tensioner Spring Torque:
32.5 39.7 N·m (3.31 4.05 kgf·m, 23.9 29.3 lbf·ft)
4-324-32 Charging System
Drive Belt Auto-tensioner
Inspection (cont’d)
Drive Belt Auto-tensioner Removal/
Installation
A
B
C
E
F
8x1.25mm
22 N·m
(2.2 kgf·m, 16 lbf·ft) 6x1.0mm
12 N·m
(1.2 kgf·m, 8.7 lbf·ft)
A
10x1.25mm
56 N·m (5.7 kgf·m, 41 lbf·ft) B
30 °
30 °
D
6. Remove the auto-tensioner (see page 4-32).
7. Clamp the auto-tensioner (A) by using two 8 mmbolts (B) and a vise (C) as shown. Do not clamp the
auto-tensioner itself.
8. Set the torque wrench (D) on the pulley bolt, and align it as shown.
9. Align the indicator’s pointer (E) on the tensioner base with center mark (F) on the tensioner arm by
using the torque wrench, and measure the torque.
If the torque value is out of specification, replace
the auto-tensioner.
NOTE: If the indicator exceeds the center mark,
recheck the torque. 1. Remove the drive belt (see page 4-31).
2. Remove the idler pulley base.
3. Remove the pulley bolt (A), then remove the
tensioner pulley (B).
08/08/21 14:10:13 61SNR030_040_0033
ProCarManuals.com
DYNOMITE -2009-