Page 1345 of 2893
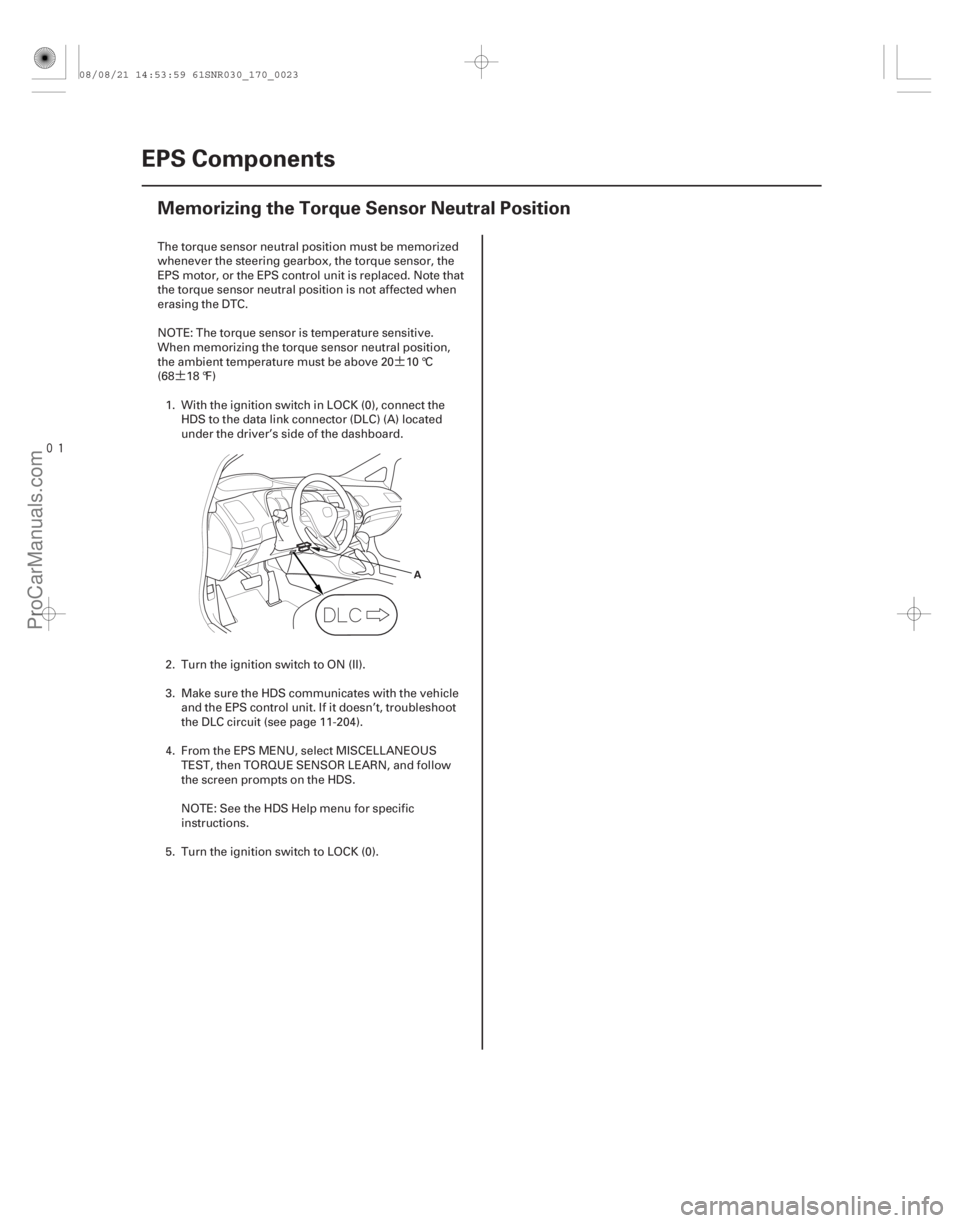
¶
¶
(#'
")
17-22EPS Components
Memorizing the Torque Sensor Neutral Position
A
The torque sensor neutral position must be memorized
whenever the steering gearbox, the torque sensor, the
EPS motor, or the EPS control unit is replaced. Note that
the torque sensor neutral position is not affected when
erasing the DTC.
NOTE: The torque sensor is temperature sensitive.
When memorizing the torque sensor neutral position,
theambienttemperaturemustbeabove20 10°C
(68 18 °F)
1. With the ignition switch in LOCK (0), connect the HDS to the data link connector (DLC) (A) located
under the driver’s side of the dashboard.
2. Turn the ignition switch to ON (II).
3. Make sure the HDS communicates with the vehicle and the EPS control unit. If it doesn’t, troubleshoot
the DLC circuit (see page 11-204).
4. From the EPS MENU, select MISCELLANEOUS TEST, then TORQUE SENSOR LEARN, and follow
the screen prompts on the HDS.
NOTE: See the HDS Help menu for specific
instructions.
5. Turn the ignition switch to LOCK (0).
08/08/21 14:53:59 61SNR030_170_0023
ProCarManuals.com
DYNOMITE -2009-
Page 1346 of 2893
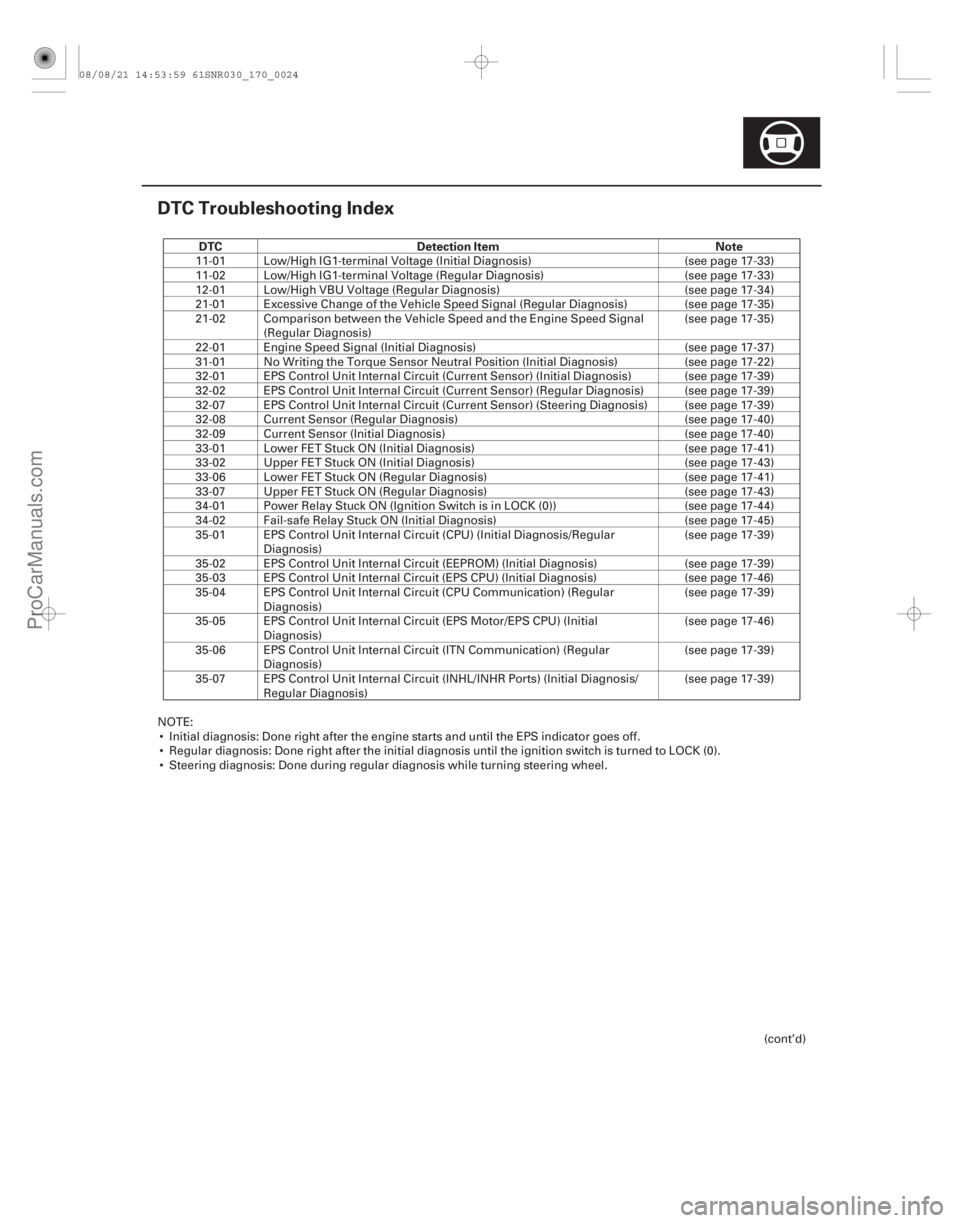
(#'
)
DTC Detection Item Note
17-23
DTC Troubleshooting Index
11-01 Low/High IG1-terminal Voltage (Initial Diagnosis)
(see page 17-33)
11-02 Low/High IG1-terminal Voltage (Regular Diagnosis) (see page 17-33)
12-01 Low/High VBU Voltage (Regular Diagnosis) (see page 17-34)
21-01 Excessive Change of the Vehicle Speed Signal (Regular Diagnosis) (see page 17-35)
21-02 Comparison between the Vehicle Speed and the Engine Speed Signal (Regular Diagnosis) (see page 17-35)
22-01 Engine Speed Signal (Initial Diagnosis) (see page 17-37)
31-01 No Writing the Torque Sensor Neutral Position (Initial Diagnosis) (see page 17-22)
32-01 EPS Control Unit Internal Circuit (Current Sensor) (Initial Diagnosis) (see page 17-39)
32-02 EPS Control Unit Internal Circuit (Current Sensor) (Regular Diagnosis) (see page 17-39)
32-07 EPS Control Unit Internal Circuit (Current Sensor) (Steering Diagnosis) (see page 17-39)
32-08 Current Sensor (Regular Diagnosis) (see page 17-40)
32-09 Current Sensor (Initial Diagnosis) (see page 17-40)
33-01 Lower FET Stuck ON (Initial Diagnosis) (see page 17-41)
33-02 Upper FET Stuck ON (Initial Diagnosis) (see page 17-43)
33-06 Lower FET Stuck ON (Regular Diagnosis) (see page 17-41)
33-07 Upper FET Stuck ON (Regular Diagnosis) (see page 17-43)
34-01 Power Relay Stuck ON (Ignition Switch is in LOCK (0)) (see page 17-44)
34-02 Fail-safe Relay Stuck ON (Initial Diagnosis) (see page 17-45)
35-01 EPS Control Unit Internal Circuit (CPU) (Initial Diagnosis/Regular Diagnosis) (see page 17-39)
35-02 EPS Control Unit Internal Circuit (EEPROM) (Initial Diagnosis) (see page 17-39)
35-03 EPS Control Unit Internal Circuit (EPS CPU) (Initial Diagnosis) (see page 17-46)
35-04 EPS Control Unit Internal Circuit (CPU Communication) (Regular Diagnosis) (see page 17-39)
35-05 EPS Control Unit Internal Circuit (EPS Motor/EPS CPU) (Initial Diagnosis) (see page 17-46)
35-06 EPS Control Unit Internal Circuit (ITN Communication) (Regular Diagnosis) (see page 17-39)
35-07 EPS Control Unit Internal Circuit (INHL/INHR Ports) (Initial Diagnosis/ Regular Diagnosis) (see page 17-39)
NOTE: Initial diagnosis: Done right after the engine starts and until the EPS indicator goes off.
Regular diagnosis: Done right after the initial diagnosis until the ignition switch is turned to LOCK (0).
Steering diagnosis: Done during regular diagnosis while turning steering wheel.
(cont’d)
08/08/21 14:53:59 61SNR030_170_0024
ProCarManuals.com
DYNOMITE -2009-
Page 1347 of 2893
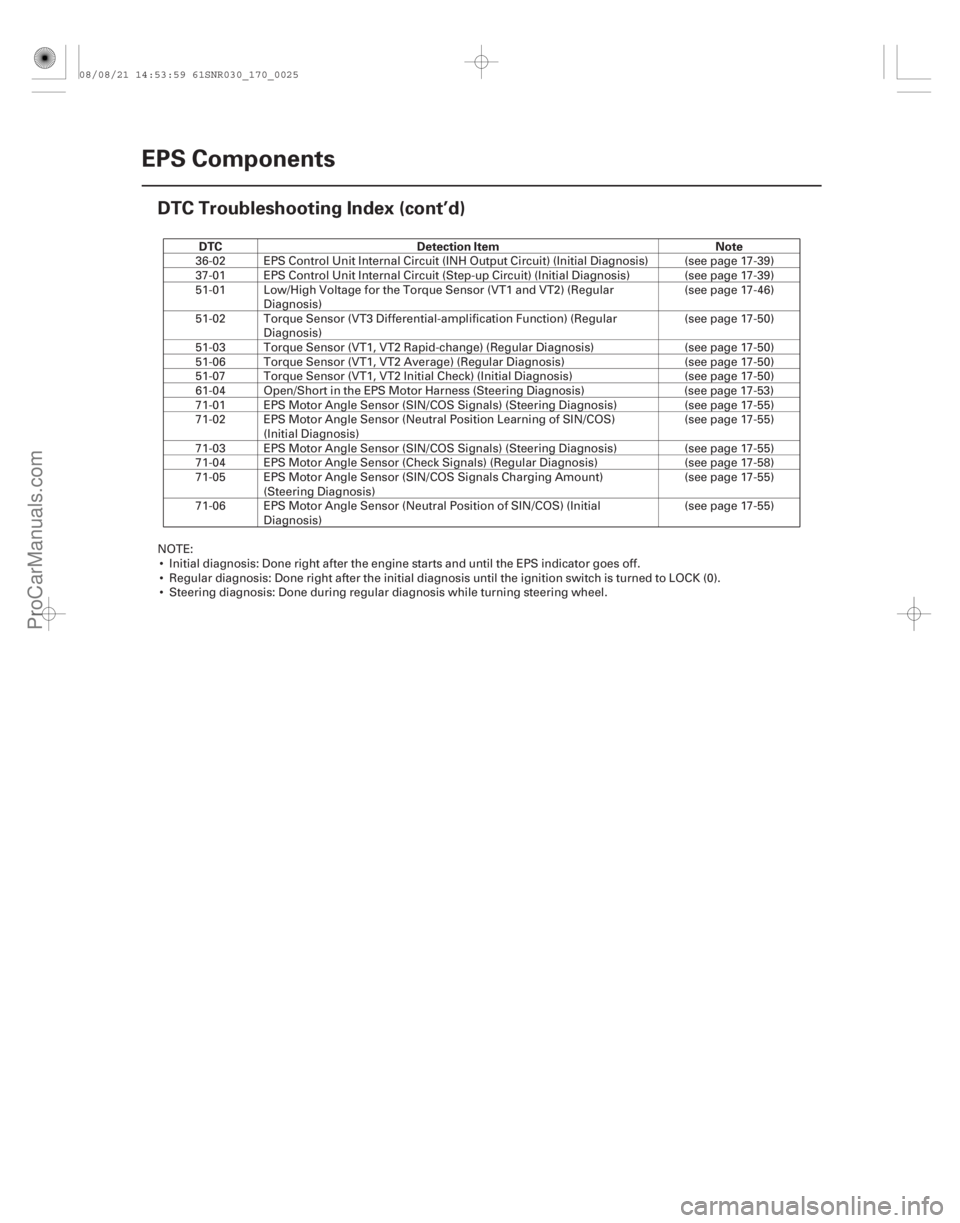
DTCDetection Item Note
17-24EPS Components
DTC Troubleshooting Index (cont’d)
36-02 EPS Control Unit Internal Circuit (INH Output Circuit) (Initial Diagnosis) (see page 17-39)
37-01 EPS Control Unit Internal Circuit (Step-up Circuit) (Initial Diagnosis) (see page 17-39)
51-01 Low/High Voltage for the Torque Sensor (VT1 and VT2) (Regular
Diagnosis) (see page 17-46)
51-02 Torque Sensor (VT3 Differential-amplification Function) (Regular Diagnosis) (see page 17-50)
51-03 Torque Sensor (VT1, VT2 Rapid-change) (Regular Diagnosis) (see page 17-50)
51-06 Torque Sensor (VT1, VT2 Average) (Regular Diagnosis) (see page 17-50)
51-07 Torque Sensor (VT1, VT2 Initial Check) (Initial Diagnosis) (see page 17-50)
61-04 Open/Short in the EPS Motor Harness (Steering Diagnosis) (see page 17-53)
71-01 EPS Motor Angle Sensor (SIN/COS Signals) (Steering Diagnosis) (see page 17-55)
71-02 EPS Motor Angle Sensor (Neutral Position Learning of SIN/COS) (Initial Diagnosis) (see page 17-55)
71-03 EPS Motor Angle Sensor (SIN/COS Signals) (Steering Diagnosis) (see page 17-55)
71-04 EPS Motor Angle Sensor (Check Signals) (Regular Diagnosis) (see page 17-58)
71-05 EPS Motor Angle Sensor (SIN/COS Signals Charging Amount) (Steering Diagnosis) (see page 17-55)
71-06 EPS Motor Angle Sensor (Neutral Position of SIN/COS) (Initial Diagnosis) (see page 17-55)
NOTE: Initial diagnosis: Done right after the engine starts and until the EPS indicator goes off.
Regular diagnosis: Done right after the initial diagnosis until the ignition switch is turned to LOCK (0).
Steering diagnosis: Done during regular diagnosis while turning steering wheel.
08/08/21 14:53:59 61SNR030_170_0025
ProCarManuals.com
DYNOMITE -2009-
Page 1348 of 2893
(#'
)
Symptom Diagnostic procedure
17-25
Symptom Troubleshooting Index
HDS does not communicate with the
EPS control unit or the vehicle
Troubleshoot the DLC circuit (see page 11-
204)
EPS indicator does not come on Symptom Troubleshooting (see page 17-60)
EPS indicator does not go off, and no
DTCs are stored Symptom Troubleshooting (see page 17-60)
EPS indicator is not on, no DTCs are
stored, but there is no power assist or
power assist is reduced 1.
2.
3.Check the EPS motor power wires between the EPS control unit
and the EPS motor for a short to body ground. Repair as needed.
If the EPS motor power wires are OK, replace the EPS motor (short
in the EPS motor) (see page 17-63).
Check the power and body ground connections at the EPS control
unit.
08/08/21 14:53:59 61SNR030_170_0026
ProCarManuals.com
DYNOMITE -2009-
Page 1349 of 2893
´•••
•••
•••
(#'
)EPS Control Unit Inputs and Outputs for Connector A (2P) (Connector disconnected)
EPS Control Unit Inputs and Outputs for Connector B (2P) (Connector disconnected)
EPS Control Unit Inputs and Outputs for Connector C (2P) (Connector disconnected)
Terminalnumber Wire color Terminal sign Description Signal
Terminal number Wire color Terminal sign Description Signal
Terminal number Wire color Terminal sign Description Signal
17-26EPS Components
System Description
NOTE: Standard battery voltage is 12 V.
1BLKPG (Power ground) Ground for the actuator EPS
motor Continuity to ground
2WHTB (Plus battery) Power source for the
actuator EPS motor Battery voltage at all times
1 GRN H-W Drives the actuator EPS motor
1 RED H-U Drives the actuator EPS motor
2 BLU H-V Drives the actuator EPS motor
Wire side of female terminals
Wire side of female terminals
Wire side of female terminals
08/08/21 14:54:00 61SNR030_170_0027
ProCarManuals.com
DYNOMITE -2009-
Page 1350 of 2893
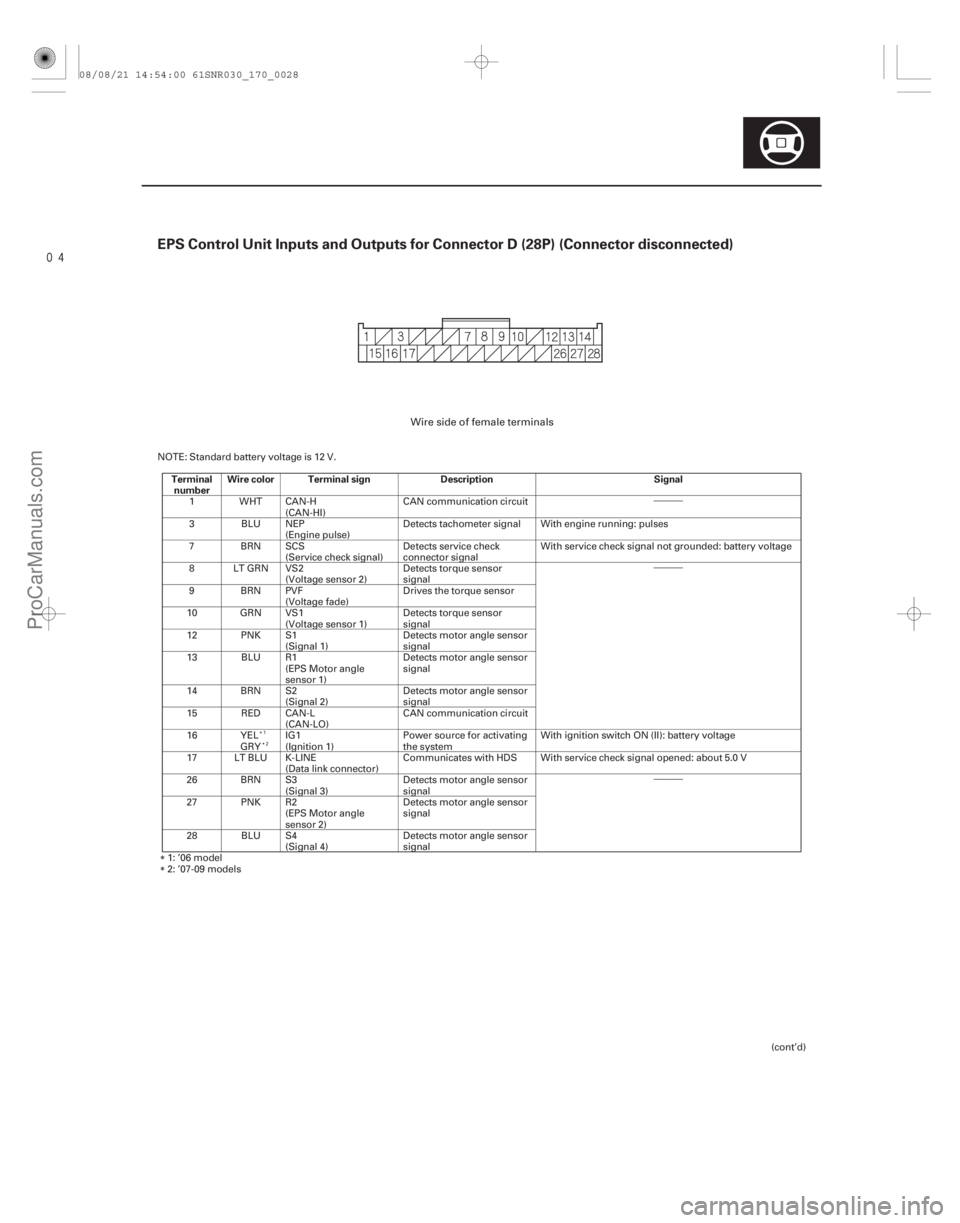
•••
•••
•••
EPS Control Unit Inputs and Outputs for Connector D (28P) (Connector disconnected)
Terminalnumber Wire color Terminal sign Description Signal
17-27
NOTE: Standard battery voltage is 12 V.
1WHTCAN-H (CAN-HI) CAN communication circuit
3BLUNEP (Engine pulse) Detects tachometer signal With engine running: pulses
7 BRN SCS (Service check signal) Detects service check
connector signal With service check signal not grounded: battery voltage
8 LT GRN VS2 (Voltage sensor 2) Detects torque sensor
signal
9 BRN PVF (Voltage fade) Drives the torque sensor
10 GRN VS1 (Voltage sensor 1) Detects torque sensor
signal
12 PNK S1 (Signal 1) Detects motor angle sensor
signal
13 BLU R1 (EPS Motor angle
sensor 1) Detects motor angle sensor
signal
14 BRN S2 (Signal 2) Detects motor angle sensor
signal
15 RED CAN-L (CAN-LO) CAN communication circuit
16 YEL GRYIG1
(Ignition 1) Power source for activating
the system With ignition switch ON (II): battery voltage
17 LT BLU K-LINE (Data link connector) Communicates with HDS With service check signal opened: about 5.0 V
26 BRN S3 (Signal 3) Detects motor angle sensor
signal
27 PNK R2 (EPS Motor angle
sensor 2) Detects motor angle sensor
signal
28 BLU S4 (Signal 4) Detects motor angle sensor
signal
1: ’06 model
2: ’07-09 models
(cont’d)
12
Wire side of female terminals
08/08/21 14:54:00 61SNR030_170_0028
ProCarManuals.com
DYNOMITE -2009-
Page 1351 of 2893
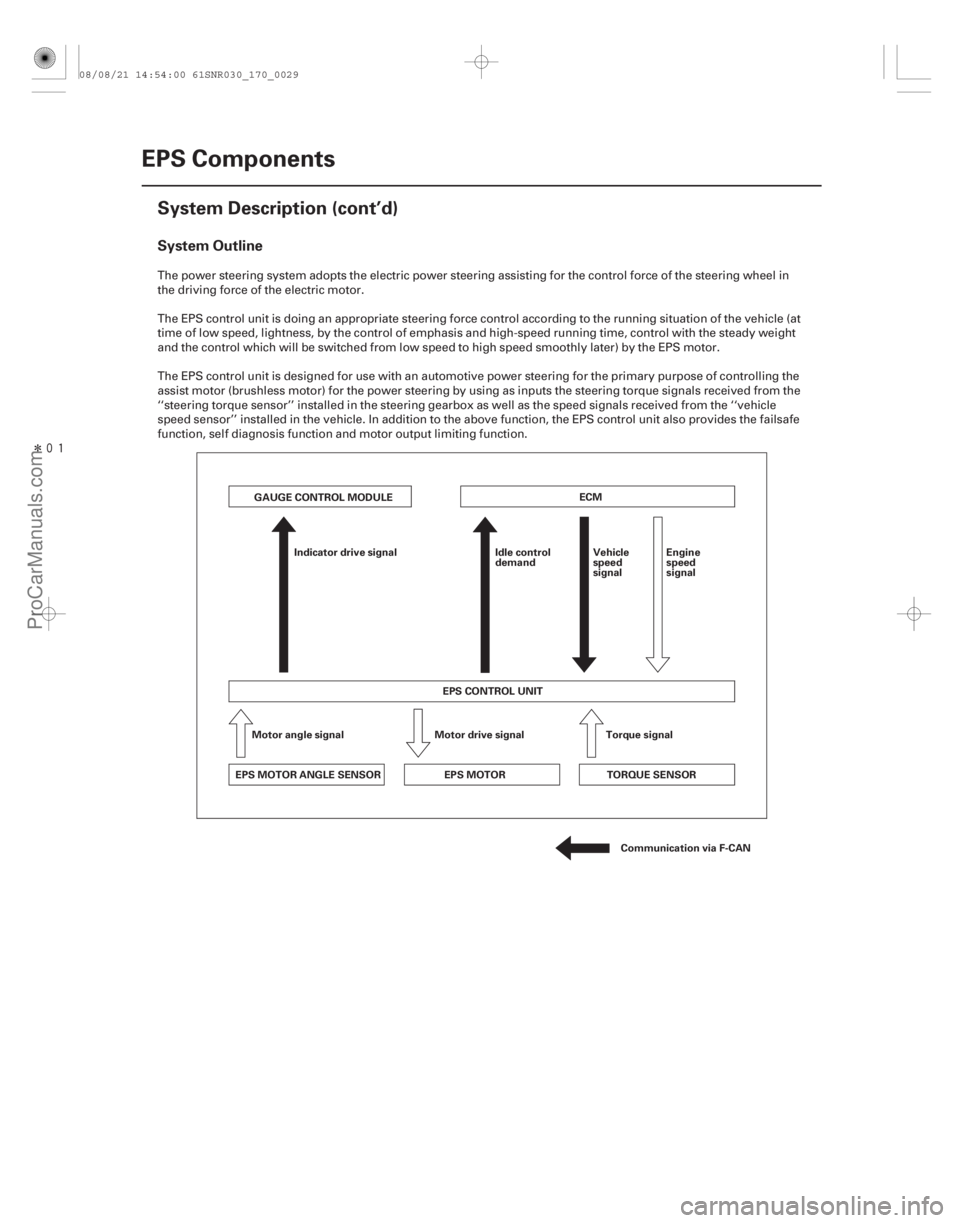
Î
System Outline
17-28EPS Components
System Description (cont’d)
GAUGE CONTROL MODULE
ECM
Indicator drive signal
EPS CONTROL UNITEPS MOTOR
EPS MOTOR ANGLE SENSOR TORQUE SENSOR Motor drive signal
Motor angle signal Torque signal Idle control
demand
Communication via F-CAN
Vehicle
speed
signal
Engine
speed
signal
The power steering system adopts the electric power steering assisting for the control force of the steering wheel in
the driving force of the electric motor.
The EPS control unit is doing an appropriate steering force control according to the running situation of the vehicle (at
time of low speed, lightness, by the control of emphasis and high-speed running time, control with the steady weight
and the control which will be switched from low speed to high speed smoothly later) by the EPS motor.
The EPS control unit is designed for use with an automotive power steering for the primary purpose of controlling the
assist motor (brushless motor) for the power steering by using as inputs the steering torque signals received from the
‘‘steering torque sensor’’ installed in the steering gearbox as well as the speed signals received from the ‘‘vehicle
speed sensor’’ installed in the vehicle. In addition to the above function, the EPS control unit also provides the failsafe
function, self diagnosis function and motor output limiting function.
08/08/21 14:54:00 61SNR030_170_0029
ProCarManuals.com
DYNOMITE -2009-
Page 1352 of 2893
Î
ÎSteering Gearbox
Torque Sensor
17-29
Worm wheel gear
Worm gear
EPS motor
Torque sensor
Steered to right Center Steered to left Steered to left
Steered to right
0 VT1
VT3
VT2
Input voltage (V)
Core
Coil
The EPS motor engages with a pinion and one worm wheel gear, which is transmitted to a direct pinion, to move a
rack.
When the steering wheel is turned, twist occurs in the torsion bar between the steering side of the input shaft and the
output shaft on the road reaction force side. Inductance is changed by the movement of the core. The amount this
voltage changes (varies with the amount of movement, and direction of the core) is amplified with the interface
circuitry of the sensor coil, and output to the EPS control unit as a steer signal.
08/08/21 14:54:01 61SNR030_170_0030
ProCarManuals.com
DYNOMITE -2009-