Page 65 of 2893
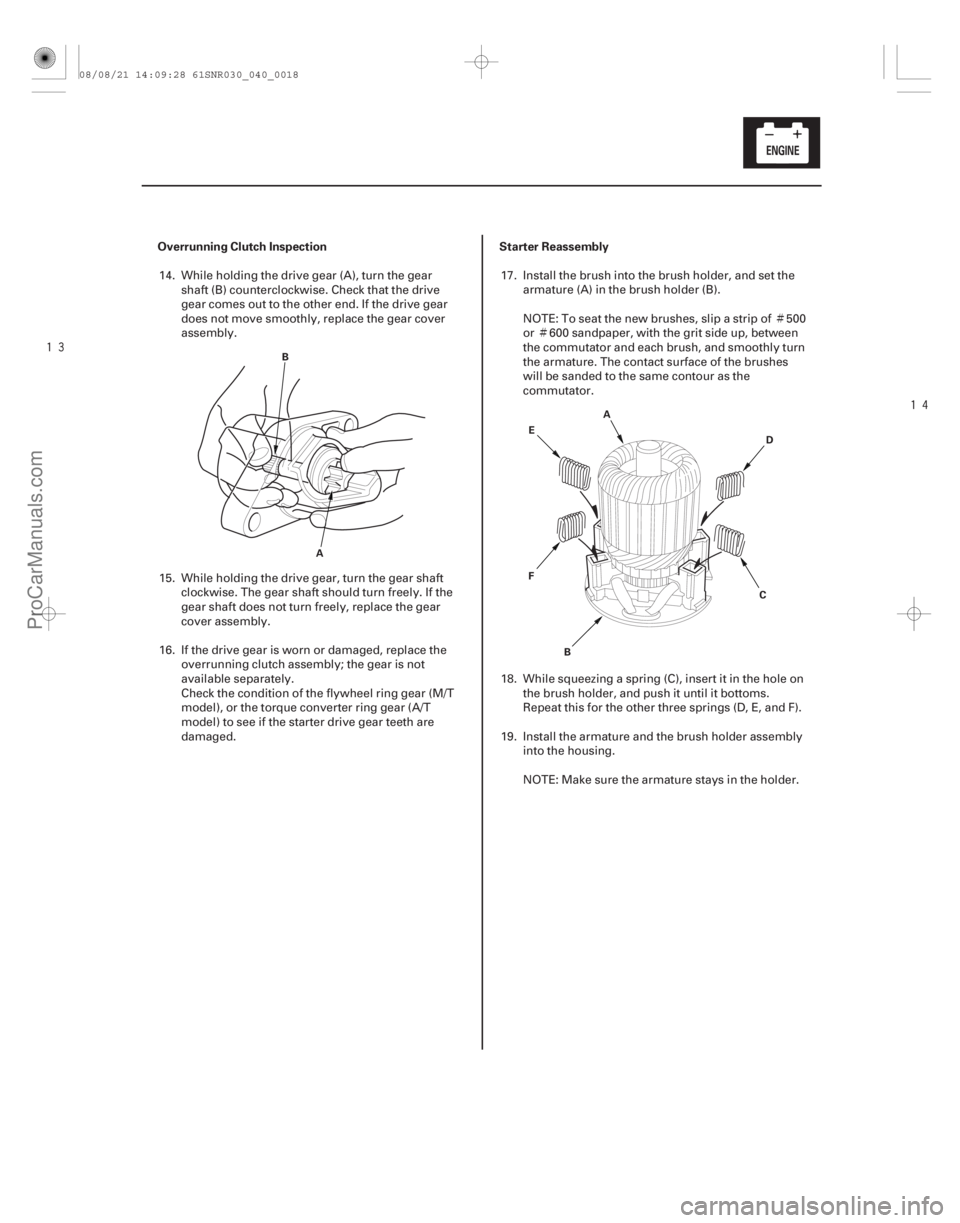
Ì
Ì
Overrunning Clutch Inspection Starter Reassembly
4-17
B
A A
B CD
E
F
14. While holding the drive gear (A), turn the gear shaft (B) counterclockwise. Check that the drive
gear comes out to the other end. If the drive gear
does not move smoothly, replace the gear cover
assembly.
15. While holding the drive gear, turn the gear shaft clockwise. The gear shaft should turn freely. If the
gear shaft does not turn freely, replace the gear
cover assembly.
16. If the drive gear is worn or damaged, replace the overrunning clutch assembly; the gear is not
available separately.
Check the condition of the flywheel ring gear (M/T
model), or the torque converter ring gear (A/T
model) to see if the starter drive gear teeth are
damaged. 17. Install the brush into the brush holder, and set the
armature (A) in the brush holder (B).
NOTE: To seat the new brushes, slip a strip of 500
or 600 sandpaper, with the grit side up, between
the commutator and each brush, and smoothly turn
the armature. The contact surface of the brushes
will be sanded to the same contour as the
commutator.
18. While squeezing a spring (C), insert it in the hole on the brush holder, and push it until it bottoms.
Repeat this for the other three springs (D, E, and F).
19. Install the armature and the brush holder assembly into the housing.
NOTE: Make sure the armature stays in the holder.
08/08/21 14:09:28 61SNR030_040_0018
ProCarManuals.com
DYNOMITE -2009-
Page 66 of 2893
Î
(#'
)
4-18Ignition System
Component Location Index
IGNITION COIL
SPARK PLUG UNDER-HOOD
FUSE/RELAY BOX
IGNITION COIL RELAY
Ignition Timing Inspection, page 4-20
Removal/Installation, page 4-21
Inspection, page 4-21 Test, page 22-70
08/08/21 14:09:29 61SNR030_040_0019
ProCarManuals.com
DYNOMITE -2009-
Page 67 of 2893
Î
(#'
)
4-19
Circuit Diagram
ICM
ICM ICM
ICM: Ignition Conotrol Module BLK BLK BLK
ICM
BLK/WHT BLK/WHT BLK/WHT BLK/WHT
5V
BLU
ECM/PCM
IGPLS4 IGPLS3 IGPLS2 IGPLS1 MRLY BLK/WHT
2 3
1 UNDER-HOOD FUSE/RELAY BOX
1
3 2
4
No. 18 (15 A)
GRN
No. 4 WHT/BLU
No. 3 No. 2 BLU/RED
BATTERY
YEL/GRN
BLK No. 1
BRN
G101G101 IGNITION
COIL
RELAY
IGNITION
COILS
SPARK
PLUGS E7
F9
C18 C17 C16 C15 A6
13 3
1
3
1
2
2
2 23
16
C101
08/08/21 14:09:30 61SNR030_040_0020
ProCarManuals.com
DYNOMITE -2009-
Page 68 of 2893
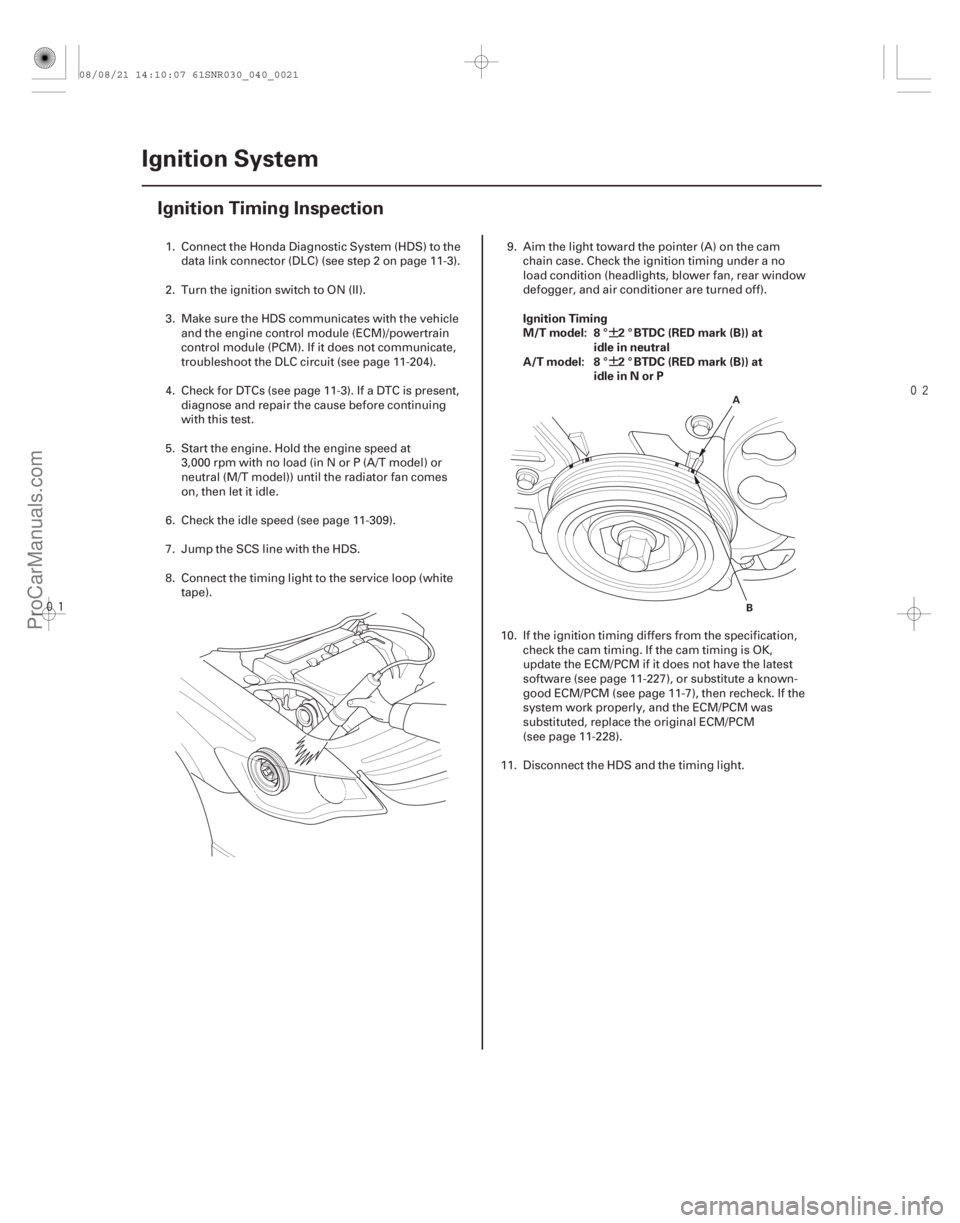
(#'
") ¶
¶
Ignition Timing
M/T model: 8 ° 2 ° BTDC (RED mark (B)) at
idle in neutral
A/T model: 8 ° 2 ° BTDC (RED mark (B)) at idle in N or P
4-20Ignition System
Ignition Timing Inspection
A
B
1. Connect the Honda Diagnostic System (HDS) to the data link connector (DLC) (see step 2 on page 11-3).
2. Turn the ignition switch to ON (II).
3. Make sure the HDS communicates with the vehicle and the engine control module (ECM)/powertrain
control module (PCM). If it does not communicate,
troubleshoot the DLC circuit (see page 11- 204).
4. Check for DTCs (see page 11-3). If a DTC is present, diagnose and repair the cause before continuing
with this test.
5. Start the engine. Hold the engine speed at 3,000 rpm with no load (in N or P (A/T model) or
neutral (M/T model)) until the radiator fan comes
on, then let it idle.
6. Check the idle speed (see page 11-309).
7. Jump the SCS line with the HDS.
8. Connect the timing light to the service loop (white tape). 9. Aim the light toward the pointer (A) on the cam
chain case. Check the ignition timing under a no
load condition (headlights, blower fan, rear window
defogger, and air conditioner are turned off).
10. If the ignition timing differs from the specification, check the cam timing. If the cam timing is OK,
update the ECM/PCM if it does not have the latest
software (see page 11-227), or substitute a known-
good ECM/PCM (see page 11-7), then recheck. If the
system work properly, and the ECM/PCM was
substituted, replace the original ECM/PCM
(see page 11-228).
11. Disconnect the HDS and the timing light.
08/08/21 14:10:07 61SNR030_040_0021
ProCarManuals.com
DYNOMITE -2009-
Page 69 of 2893
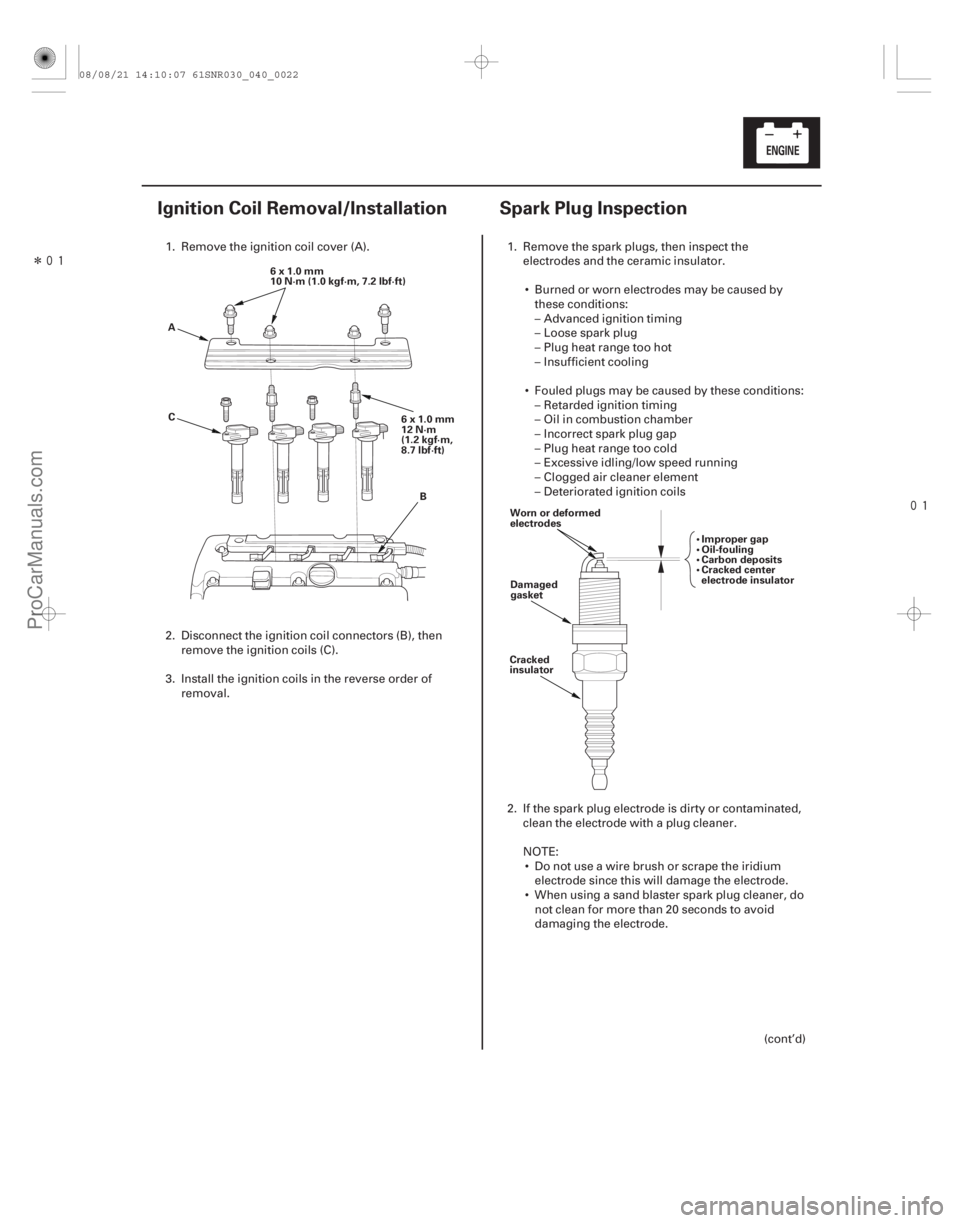
Î
(#'
)
(#'
")
4-214-21
Ignition Coil Removal/Installation Spark Plug Inspection
A B
C 6x1.0mm
10 N·m (1.0 kgf·m, 7.2 lbf·ft)
6x1.0mm
12 N·m
(1.2 kgf·m,
8.7 lbf·ft) Impropergap
Oil-fouling
Carbon deposits
Cracked centerelectrode insulator
Worn or deformed
electrodes
Damaged
gasket
Cracked
insulator
1. Remove the ignition coil cover (A).
2. Disconnect the ignition coil connectors (B), then remove the ignition coils (C).
3. Install the ignition coils in the reverse order of removal. 1. Remove the spark plugs, then inspect the
electrodes and the ceramic insulator.
Burned or worn electrodes may be caused by these conditions:
– Advanced ignition timing
– Loose spark plug
– Plug heat range too hot
– Insufficient cooling
Fouled plugs may be caused by these conditions: – Retarded ignition timing
– Oil in combustion chamber
– Incorrect spark plug gap
– Plug heat range too cold
– Excessive idling/low speed running
– Clogged air cleaner element
– Deteriorated ignition coils
2. If the spark plug electrode is dirty or contaminated, clean the electrode with a plug cleaner.
NOTE: Do not use a wire brush or scrape the iridium electrode since this will damage the electrode.
When using a sand blaster spark plug cleaner, do not clean for more than 20 seconds to avoid
damaging the electrode.
(cont’d)
08/08/21 14:10:07 61SNR030_040_0022
ProCarManuals.com
DYNOMITE -2009-
Page 70 of 2893
µµ
Spark Plugs
K20Z2 engine
DENSO: SKJ20DR-M11
K20Z3 engine
DENSO: SK22PR-M11S
Electrode Gap
Standard(New): 1.0 1.1 mm (0.039 0.043 in.)
4-22 Ignition System
Spark Plug Inspection (cont’d)
B
A
3. Replace the plug at the specified interval or if the
center electrode (A) is rounded, or if the spark plug
gap (B) is out of specification. Use only the listed
spark plugs.
NOTE: Do not adjust the gap of iridium tip plugs.
4. Apply a small amount of anti-seize compound to the plug threads, and screw the plugs into the
cylinder head, finger-tight. Torque them to 18 N·m
(1.8 kgf·m, 13 lbf·ft).
08/08/21 14:10:07 61SNR030_040_0023
ProCarManuals.com
DYNOMITE -2009-
Page 71 of 2893
Î
(#'
)
4-23
Charging System
Component Location Index
BATTERY
DRIVE BELT CHARGING SYSTEM INDICATOR
(In the gauge control module (tach))
UNDER-HOOD FUSE/RELAY BOX
(Has built-in ELECTRICAL LOAD
DETECTOR (ELD))
ALTERNATOR
DRIVE BELT AUTO-TENSIONER
IDLER PULLEY
Test, page 22-67
Inspection, page 4-30
Replacement, page 4-31 Removal and Installation, page 4-34
Overhaul, page 4-38
Inspection, page 4-31
Removal/Installation, page 4-32
Tensioner Pulley Replacement,
page 4-33
Replacement,
page 4-34
08/08/21 14:10:10 61SNR030_040_0024
ProCarManuals.com
DYNOMITE -2009-
Page 72 of 2893
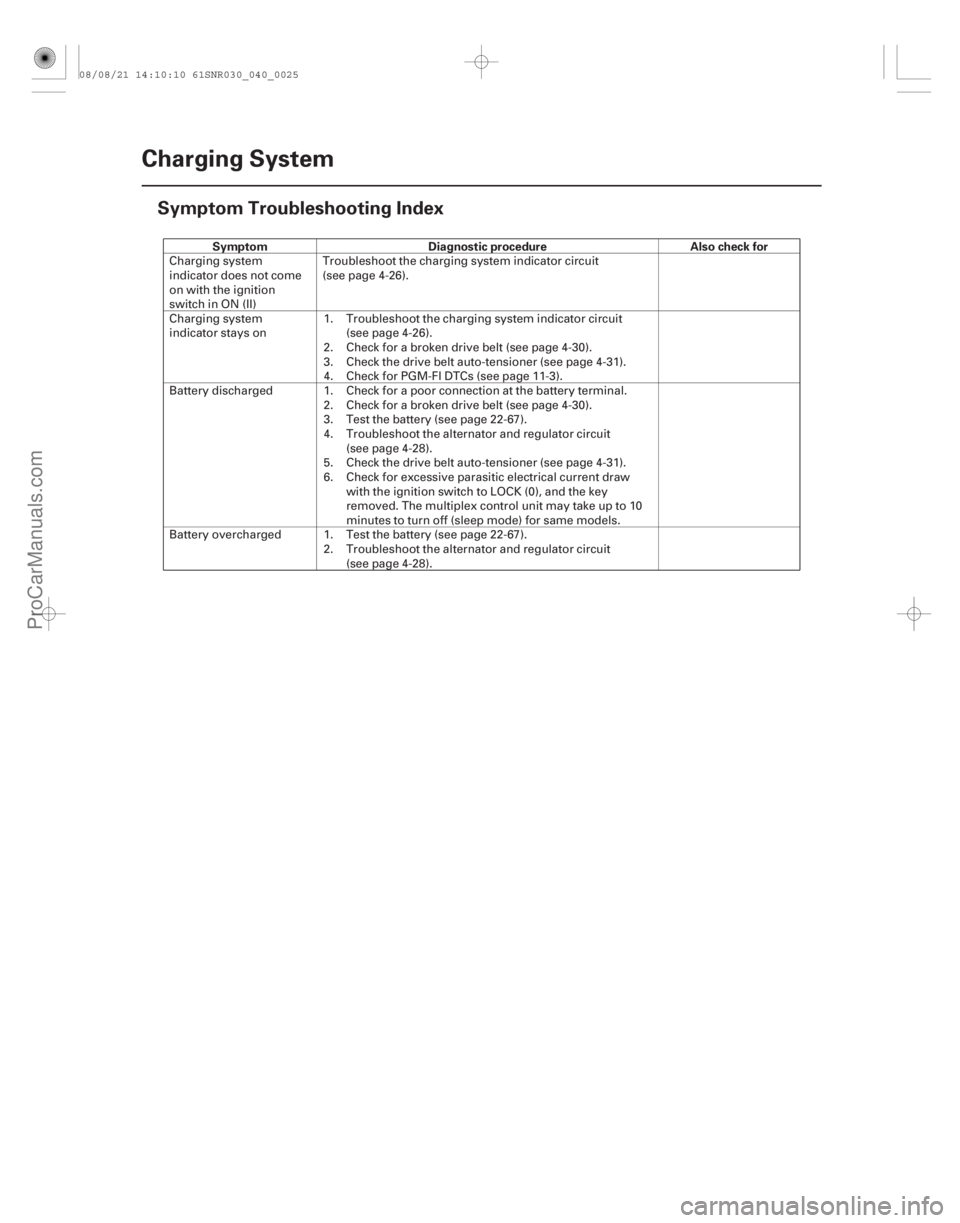
(#'
)
Symptom Diagnostic procedure Also check for
4-24
Charging System
Symptom Troubleshooting Index
Charging system
indicator does not come
on with the ignition
switch in ON (II)
Troubleshoot the charging system indicator circuit
(see page 4-26).
Charging system
indicator stays on 1.
2.
3.
4.Troubleshoot the charging system indicator circuit
(see page 4-26).
Check for a broken drive belt (see page 4-30).
Check the drive belt auto-tensioner (see page 4-31).
Check for PGM-FI DTCs (see page 11-3).
Battery discharged 1. 2.
3.
4.
5.
6.Check for a poor connection at the battery terminal.
Check for a broken drive belt (see page 4-30).
Test the battery (see page 22-67).
Troubleshoot the alternator and regulator circuit
(see page 4-28).
Check the drive belt auto-tensioner (see page 4-31).
Check for excessive parasitic electrical current draw
with the ignition switch to LOCK (0), and the key
removed. The multiplex control unit may take up to 10
minutes to turn off (sleep mode) for same models.
Battery overcharged 1. 2.Test the battery (see page 22-67).
Troubleshoot the alternator and regulator circuit
(see page 4-28).
08/08/21 14:10:10 61SNR030_040_0025
ProCarManuals.com
DYNOMITE -2009-