Page 1977 of 2893
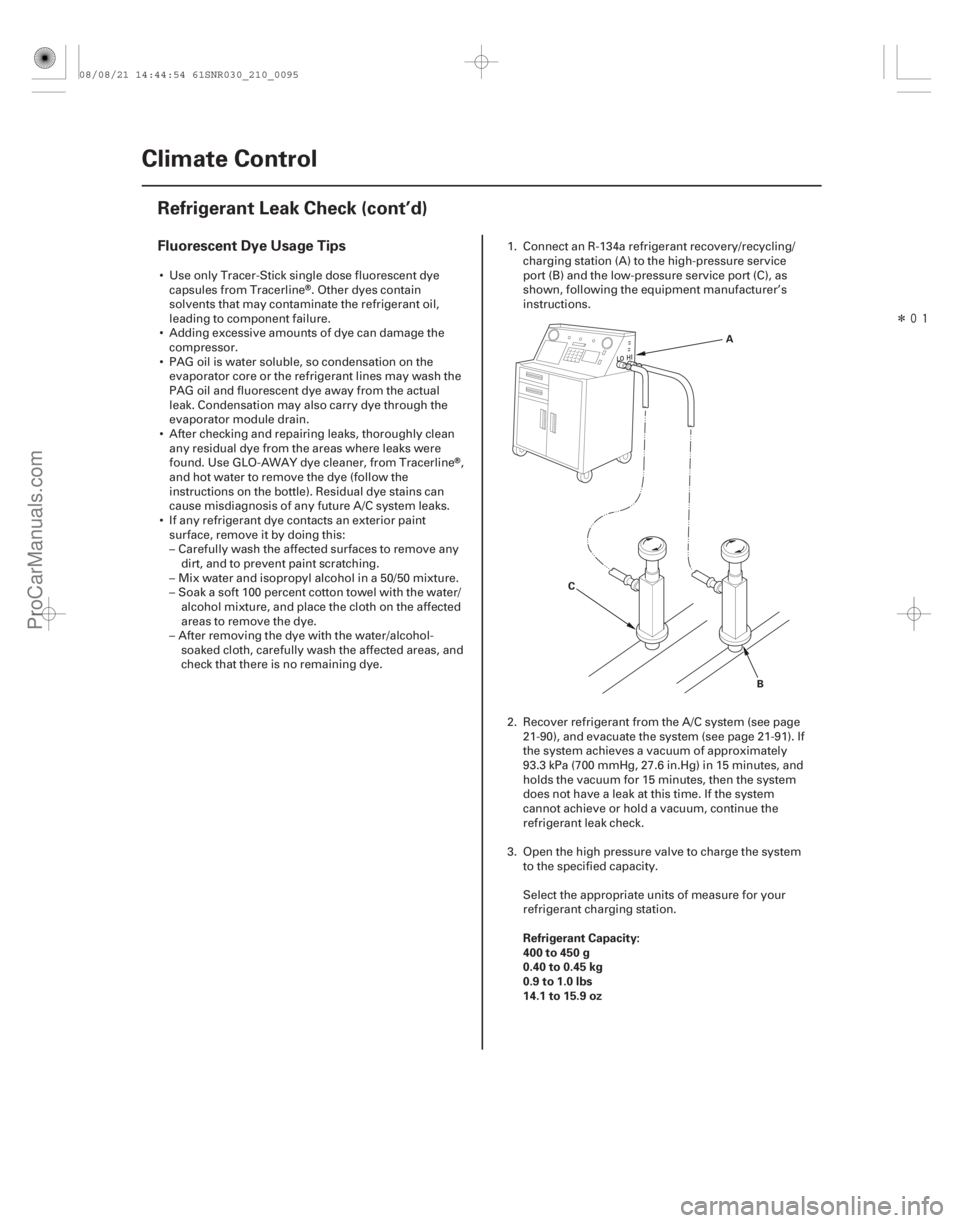
Î
Fluorescent Dye Usage Tips
Refrigerant Capacity:
400 to 450 g
0.40 to 0.45 kg
0.9 to 1.0 lbs
14.1 to 15.9 oz
21-94Climate Control
Refrigerant Leak Check (cont’d)
A
C B
Use only Tracer-Stick single dose fluorescent dyecapsules from Tracerline
. Other dyes contain
solvents that may contaminate the refrigerant oil,
leading to component failure.
Adding excessive amounts of dye can damage the compressor.
PAG oil is water soluble, so condensation on the evaporator core or the refrigerant lines may wash the
PAG oil and fluorescent dye away from the actual
leak. Condensation may also carry dye through the
evaporator module drain.
After checking and repairing leaks, thoroughly clean any residual dye from the areas where leaks were
found. Use GLO-AWAY dye cleaner, from Tracerline
,
and hot water to remove the dye (follow the
instructions on the bottle). Residual dye stains can
cause misdiagnosis of any future A/C system leaks.
If any refrigerant dye contacts an exterior paint surface, remove it by doing this:
– Carefully wash the affected surfaces to remove any dirt, and to prevent paint scratching.
– Mix water and isopropyl alcohol in a 50/50 mixture.
– Soak a soft 100 percent cotton towel with the water/ alcohol mixture, and place the cloth on the affected
areas to remove the dye.
– After removing the dye with the water/alcohol- soaked cloth, carefully wash the affected areas, and
check that there is no remaining dye. 1. Connect an R-134a refrigerant recovery/recycling/
charging station (A) to the high-pressure service
port (B) and the low-pressure service port (C), as
shown, following the equipment manufacturer’s
instructions.
2. Recover refrigerant from the A/C system (see page 21-90), and evacuate the system (see page 21-91). If
the system achieves a vacuum of approximately
93.3 kPa (700 mmHg, 27.6 in.Hg) in 15 minutes, and
holds the vacuum for 15 minutes, then the system
does not have a leak at this time. If the system
cannot achieve or hold a vacuum, continue the
refrigerant leak check.
3. Open the high pressure valve to charge the system to the specified capacity.
Select the appropriate units of measure for your
refrigerant charging station.
08/08/21 14:44:54 61SNR030_210_0095
ProCarManuals.com
DYNOMITE -2009-
Page 1978 of 2893
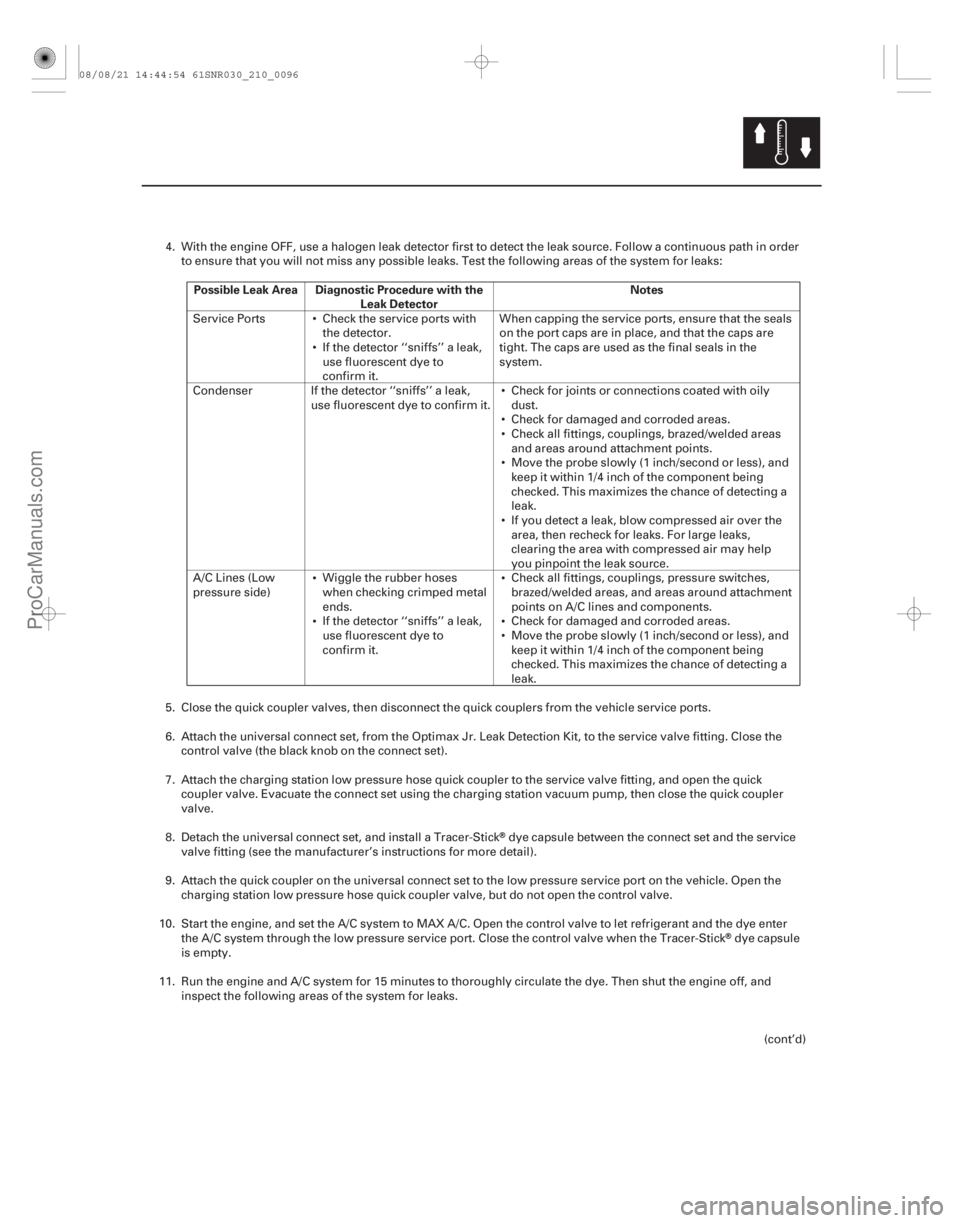
Possible Leak Area Diagnostic Procedure with theLeak Detector Notes
21-95
4. With the engine OFF, use a halogen leak detector first to detect the leak source. Follow a continuous path in order
to ensure that you will not miss any possible leaks. Test the following areas of the system for leaks:
Service Ports Check the service ports with
the detector.
If the detector ‘‘sniffs’’ a leak,
use fluorescent dye to
confirm it. When capping the service ports, ensure that the seals
on the port caps are in place, and that the caps are
tight. The caps are used as the final seals in the
system.
Condenser If the detector ‘‘sniffs’’ a leak, use fluorescent dye to confirm it. Check for joints or connections coated with oily
dust.
Check for damaged and corroded areas.
Check all fittings, couplings, brazed/welded areas
and areas around attachment points.
Move the probe slowly (1 inch/second or less), and
keep it within 1/4 inch of the component being
checked. This maximizes the chance of detecting a
leak.
If you detect a leak, blow compressed air over the
area, then recheck for leaks. For large leaks,
clearing the area with compressed air may help
you pinpoint the leak source.
A/C Lines (Low
pressure side) Wiggle the rubber hoses
when checking crimped metal
ends.
If the detector ‘‘sniffs’’ a leak,
use fluorescent dye to
confirm it. Check all fittings, couplings, pressure switches,
brazed/welded areas, and areas around attachment
points on A/C lines and components.
Check for damaged and corroded areas.
Move the probe slowly (1 inch/second or less), and
keep it within 1/4 inch of the component being
checked. This maximizes the chance of detecting a
leak.
5. Close the quick coupler valves, then disconnect the quick couplers from the vehicle service ports.
6. Attach the universal connect set, from the Optimax Jr. Leak Detection Kit, to the service valve fitting. Close the control valve (the black knob on the connect set).
7. Attach the charging station low pressure hose quick coupler to the service valve fitting, and open the quick coupler valve. Evacuate the connect set using the charging station vacuum pump, then close the quick coupler
valve.
8. Detach the universal connect set, and install a Tracer-Stick
dye capsule between the connect set and the service
valve fitting (see the manufacturer’s instructions for more detail).
9. Attach the quick coupler on the universal connect set to the low pressure service port on the vehicle. Open the charging station low pressure hose quick coupler valve, but do not open the control valve.
10. Start the engine, and set the A/C system to MAX A/C. Open the control valve to let refrigerant and the dye enter the A/C system through the low pressure service port. Close the control valve when the Tracer-Stick
dye capsule
is empty.
11. Run the engine and A/C system for 15 minutes to thoroughly circulate the dye. Then shut the engine off, and inspect the following areas of the system for leaks.
(cont’d)
08/08/21 14:44:54 61SNR030_210_0096
ProCarManuals.com
DYNOMITE -2009-
Page 1979 of 2893
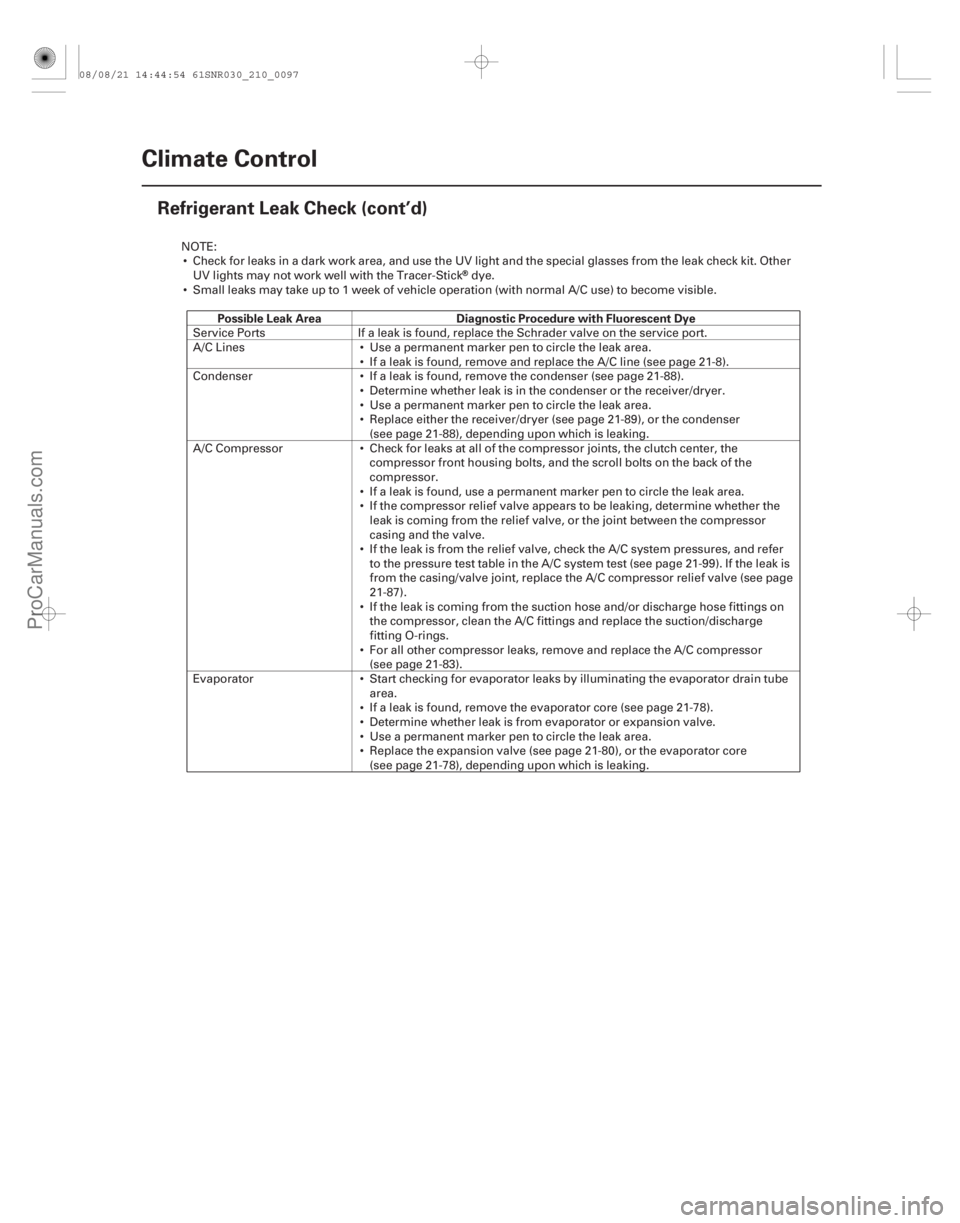
Possible Leak AreaDiagnostic Procedure with Fluorescent Dye
21-96Climate Control
Refrigerant Leak Check (cont’d)
NOTE:
Check for leaks in a dark work area, and use the UV light and the special glasses from the leak check kit. Other UV lights may not work well with the Tracer-Stick
dye.
Small leaks may take up to 1 week of vehicle operation (with normal A/C use) to become visible.
Service Ports If a leak is found, replace the Schrader valve on the service port.
A/C Lines Use a permanent marker pen to circle the leak area.
If a leak is found, remove and replace the A/C line (see page 21-8).
Condenser If a leak is found, remove the condenser (see page 21-88). Determine whether leak is in the condenser or the receiver/dryer.
Use a permanent marker pen to circle the leak area.
Replace either the receiver/dryer (see page 21-89), or the condenser
(see page 21-88), depending upon which is leaking.
A/C Compressor Check for leaks at all of the compressor joints, the clutch center, the compressor front housing bolts, and the scroll bolts on the back of the
compressor.
If a leak is found, use a permanent marker pen to circle the leak area.
If the compressor relief valve appears to be leaking, determine whether the
leak is coming from the relief valve, or the joint between the compressor
casing and the valve.
If the leak is from the relief valve, check the A/C system pressures, and refer
to the pressure test table in the A/C system test (see page 21-99). If the leak is
from the casing/valve joint, replace the A/C compressor relief valve (see page
21-87).
If the leak is coming from the suction hose and/or discharge hose fittings on
the compressor, clean the A/C fittings and replace the suction/discharge
fitting O-rings.
For all other compressor leaks, remove and replace the A/C compressor
(see page 21-83).
Evaporator Start checking for evaporator leaks by illuminating the evaporator drain tube area.
If a leak is found, remove theevaporator core (see page 21-78).
Determine whether leak is from evaporator or expansion valve.
Use a permanent marker pen to circle the leak area.
Replace the expansion valve (see page 21-80), or the evaporator core
(see page 21-78), depending upon which is leaking.
08/08/21 14:44:54 61SNR030_210_0097
ProCarManuals.com
DYNOMITE -2009-
Page 1980 of 2893
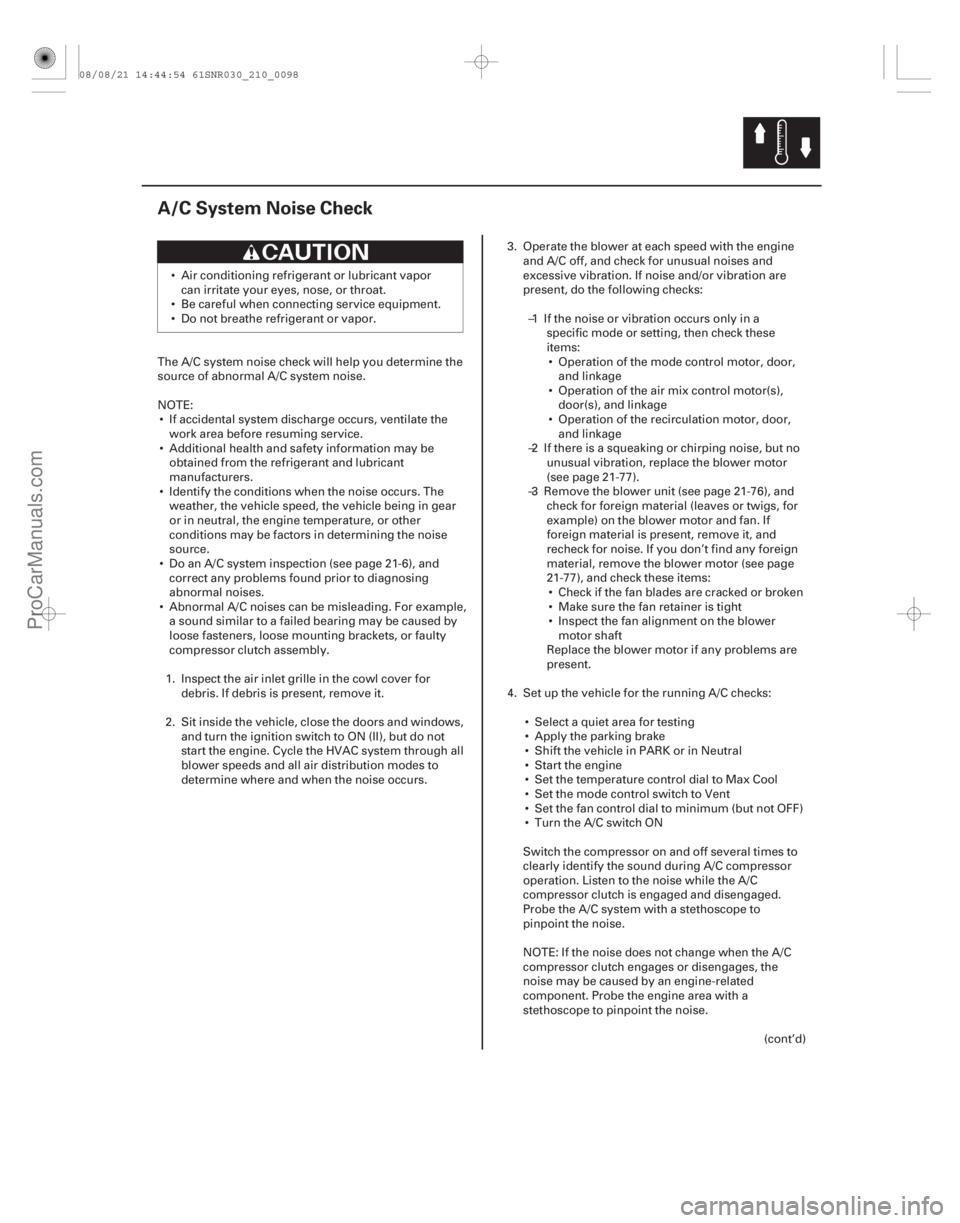
(#'
")
21-97
A/C System Noise Check
Air conditioning refrigerant or lubricant vaporcan irritate your eyes, nose, or throat.
Be careful when connecting service equipment.
Do not breathe refrigerant or vapor.
The A/C system noise check will help you determine the
source of abnormal A/C system noise.
NOTE: If accidental system discharge occurs, ventilate the work area before resuming service.
Additional health and safety information may be obtained from the refrigerant and lubricant
manufacturers.
Identify the conditions when the noise occurs. The weather, the vehicle speed, the vehicle being in gear
or in neutral, the engine temperature, or other
conditions may be factors in determining the noise
source.
Do an A/C system inspection (see page 21-6), and correct any problems found prior to diagnosing
abnormal noises.
Abnormal A/C noises can be misleading. For example,
a sound similar to a failed bearing may be caused by
loose fasteners, loose mounting brackets, or faulty
compressor clutch assembly.
1. Inspect the air inlet grille in the cowl cover for debris. If debris is present, remove it.
2. Sit inside the vehicle, close the doors and windows, and turn the ignition switch to ON (II), but do not
start the engine. Cycle the HVAC system through all
blower speeds and all air distribution modes to
determine where and when the noise occurs. 3. Operate the blower at each speed with the engine
and A/C off, and check for unusual noises and
excessive vibration. If noise and/or vibration are
present, do the following checks:
–1 If the noise or vibration occurs only in a specific mode or setting, then check these
items: Operation of the mode control motor, door, and linkage
Operation of the air mix control motor(s), door(s), and linkage
Operation of the recirculation motor, door, and linkage
–2 If there is a squeaking or chirping noise, but no unusual vibration, replace the blower motor
(see page 21-77).
–3 Remove the blower unit (see page 21-76), and check for foreign material (leaves or twigs, for
example) on the blower motor and fan. If
foreign material is present, remove it, and
recheck for noise. If you don’t find any foreign
material, remove the blower motor (see page
21-77), and check these items: Check if the fan blades are cracked or broken
Make sure the fan retainer is tight
Inspect the fan alignment on the blower motor shaft
Replace the blower motor if any problems are
present.
4. Set up the vehicle for the running A/C che cks:
Select a quiet area for testing
Apply the parking brake
Shift the vehicle in PARK or in Neutral
Start the engine
Set the temperature control dial to Max Cool
Set the mode control switch to Vent
Set the fan control dial to minimum (but not OFF)
Turn the A/C switch ON
Switch the compressor on and off several times to
clearly identify the sound during A/C compressor
operation. Listen to the noise while the A/C
compressor clutch is engaged and disengaged.
Probe the A/C system with a stethoscope to
pinpoint the noise.
NOTE: If the noise does not change when the A/C
compressor clutch engages or disengages, the
noise may be caused by an engine-related
component. Probe the engine area with a
stethoscope to pinpoint the noise. (cont’d)
08/08/21 14:44:54 61SNR030_210_0098
ProCarManuals.com
DYNOMITE -2009-
Page 1981 of 2893
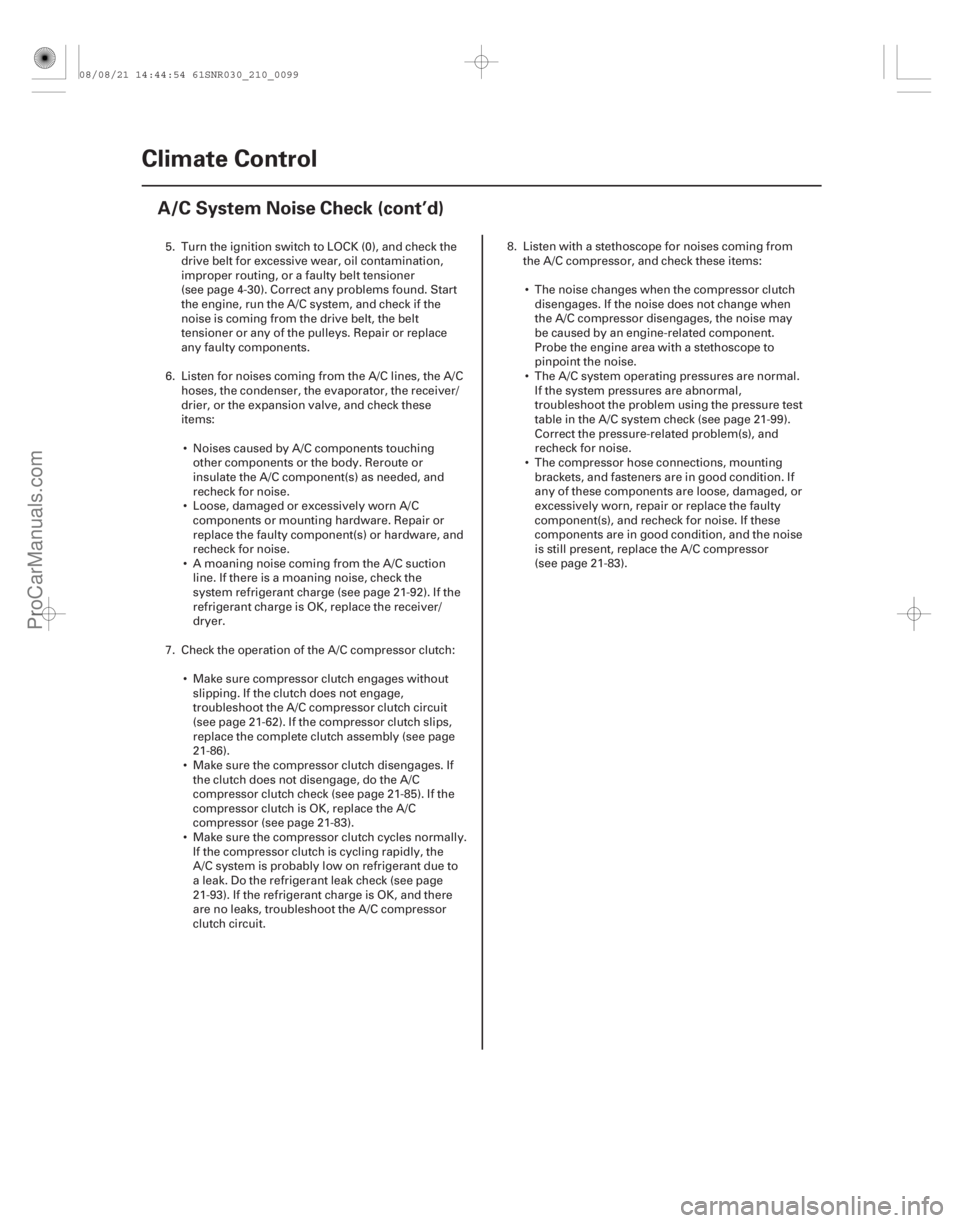
21-98Climate Control
A/C System Noise Check (cont’d)
5. Turn the ignition switch to LOCK (0), and check the
drive belt for excessive wear, oil contamination,
improper routing, or a faulty belt tensioner
(see page 4-30). Correct any problems found. Start
the engine, run the A/C system, and check if the
noise is coming from the drive belt, the belt
tensioner or any of the pulleys. Repair or replace
any faulty components.
6. Listen for noises coming from the A/C lines, the A/C hoses, the condenser, the evaporator, the receiver/
drier, or the expansion valve, and check these
items:
Noises caused by A/C components touching other components or the body. Reroute or
insulate the A/C component(s) as needed, and
recheck for noise.
Loose, damaged or excessively worn A/C components or mounting hardware. Repair or
replace the faulty component(s) or hardware, and
recheck for noise.
A moaning noise coming from the A/C suction line. If there is a moaning noise, check the
system refrigerant charge (see page 21-92). If the
refrigerant charge is OK, replace the receiver/
dryer.
7. Check the operation of the A/C compressor clutch: Make sure compressor clutch engages withoutslipping. If the clutch does not engage,
troubleshoot the A/C compressor clutch circuit
(see page 21-62). If the compressor clutch slips,
replace the complete clutch assembly (see page
21-86).
Make sure the compressor clutch disengages. If the clutch does not disengage, do the A/C
compressor clutch check (see page 21-85). If the
compressor clutch is OK, replace the A/C
compressor (see page 21-83).
Make sure the compressor clutch cycles normally. If the compressor clutch is cycling rapidly, the
A/C system is probably low on refrigerant due to
a leak. Do the refrigerant leak check (see page
21-93). If the refrigerant charge is OK, and there
are no leaks, troubleshoot the A/C compressor
clutch circuit. 8. Listen with a stethoscope for noises coming from
the A/C compressor, and check these items:
The noise changes when the compressor clutch disengages. If the noise does not change when
the A/C compressor disengages, the noise may
be caused by an engine-related component.
Probe the engine area with a stethoscope to
pinpoint the noise.
The A/C system operating pressures are normal. If the system pressures are abnormal,
troubleshoot the problem using the pressure test
table in the A/C system check (see page 21-99).
Correct the pressure-related problem(s), and
recheck for noise.
The compressor hose connections, mounting brackets, and fasteners are in good condition. If
any of these components are loose, damaged, or
excessively worn, repair or replace the faulty
component(s), and recheck for noise. If these
components are in good condition, and the noise
is still present, replace the A/C compressor
(see page 21-83).
08/08/21 14:44:54 61SNR030_210_0099
ProCarManuals.com
DYNOMITE -2009-
Page 1982 of 2893
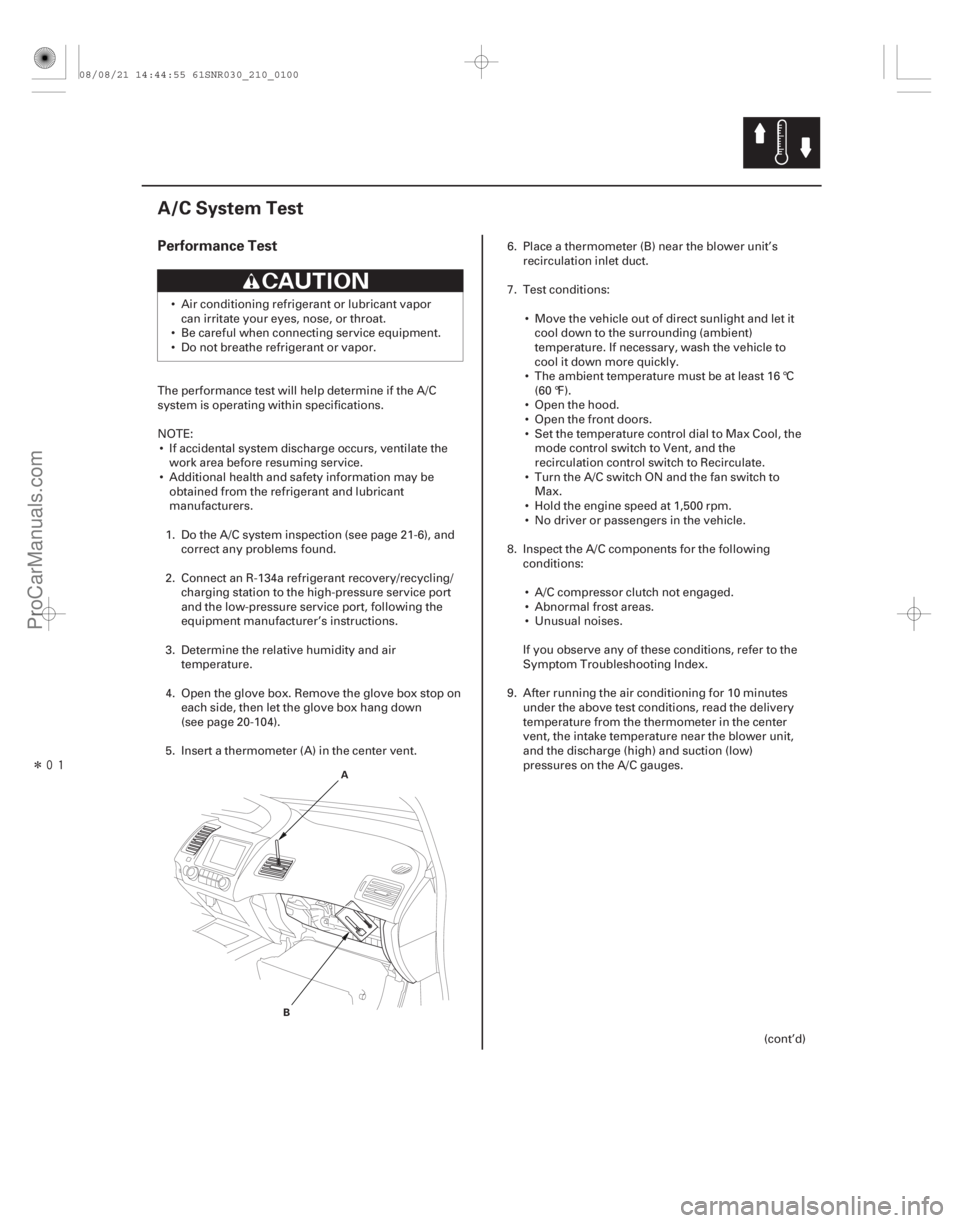
Î
(#'
)
Performance Test
21-99
A/C System Test
A
B
Air conditioning refrigerant or lubricant vapor can irritate your eyes, nose, or throat.
Be careful when connecting service equipment.
Do not breathe refrigerant or vapor.
The performance test will help determine if the A/C
system is operating within specifications.
NOTE: If accidental system discharge occurs, ventilate the work area before resuming service.
Additional health and safety information may be obtained from the refrigerant and lubricant
manufacturers.
1. Do the A/C system inspection (see page 21-6), and correct any problems found.
2. Connect an R-134a refrigerant recovery/recycling/ charging station to the high-pressure service port
and the low-pressure service port, following the
equipment manufacturer’s instructions.
3. Determine the relative humidity and air temperature.
4. Open the glove box. Remove the glove box stop on each side, then let the glove box hang down
(see page 20-104).
5. Insert a thermometer (A) in the center vent. 6. Place a thermometer (B) near the blower unit’s
recirculation inlet duct.
7. Test conditions: Move the vehicle out of direct sunlight and let itcool down to the surrounding (ambient)
temperature. If necessary, wash the vehicle to
cool it down more quickly.
The ambient temperature must be at least 16 °C (60 °F).
Open the hood.
Open the front doors.
Set the temperature control dial to Max Cool, the mode control switch to Vent, and the
recirculation control switch to Recirculate.
Turn the A/C switch ON and the fan switch to Max.
Hold the engine speed at 1,500 rpm.
No driver or passengers in the vehicle.
8. Inspect the A/C components for the following conditions:
A/C compressor clutch not engaged.
Abnormal frost areas.
Unusual noises.
If you observe any of these conditions, refer to the
Symptom Troubleshooting Index.
9. After running the air conditioning for 10 minutes under the above test conditions, read the delivery
temperature from the thermometer in the center
vent, the intake temperature near the blower unit,
and the discharge (high) and suction (low)
pressures on the A/C gauges.
(cont’d)
08/08/21 14:44:55 61SNR030_210_0100
ProCarManuals.com
DYNOMITE -2009-
Page 1983 of 2893
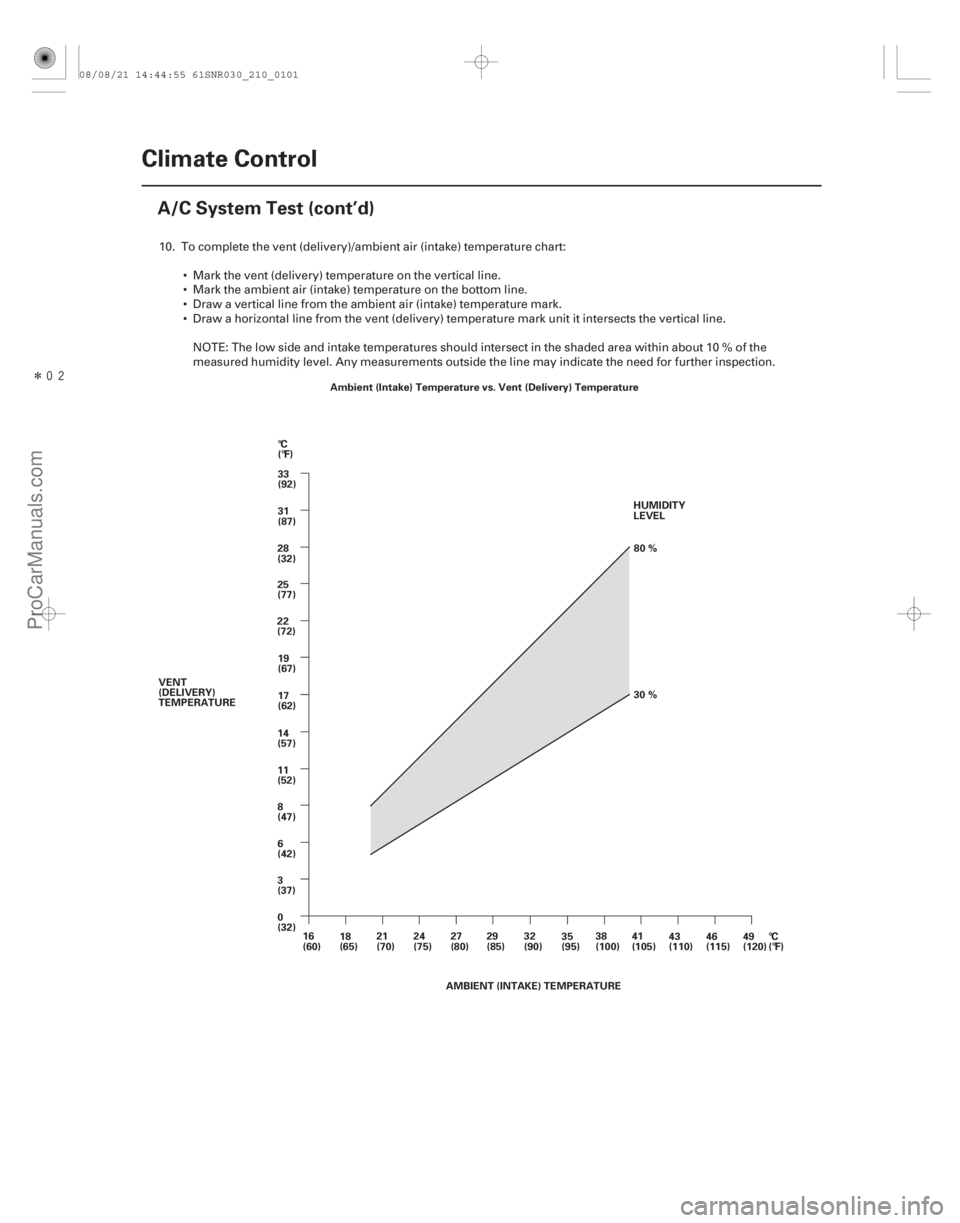
Î
21-100Climate Control
A/C System Test (cont’d)
80 %
HUMIDITY
LEVEL
°C
(°F)
49
(120)
°C
(°F)
33
(92)
25
(77)
14
(57)
VENT
(DELIVERY)
TEMPERATURE
35
(95)
Ambient (Intake) Temperature vs. Vent (Delivery) Temperature
AMBIENT (INTAKE) TEMPERATURE 30 %
28
(32)
17
(62)
8
(47) 31
(87)
22
(72) 19
(67)
11
(52)
6
(42)
3
(37)
0
(32) 46
(115)
43
(110)
41
(105)
38
(100)
32
(90)
29
(85)
27
(80)
24
(75)
21
(70)
18
(65)
16
(60)
10. To complete the vent (delivery)/ambient air (intake) temperature chart:
Mark the vent (delivery) temperature on the vertical line.
Mark the ambient air (intake) temperature on the bottom line.
Draw a vertical line from the ambient air (intake) temperature mark.
Draw a horizontal line from the vent (delivery) temperature mark unit it intersects the vertical line.NOTE: The low side and intake temperatures should intersect in the shaded area within about 10 % of the
measured humidity level. Any measurements outside the line may indicate the need for further inspection.
08/08/21 14:44:55 61SNR030_210_0101
ProCarManuals.com
DYNOMITE -2009-
Page 1984 of 2893
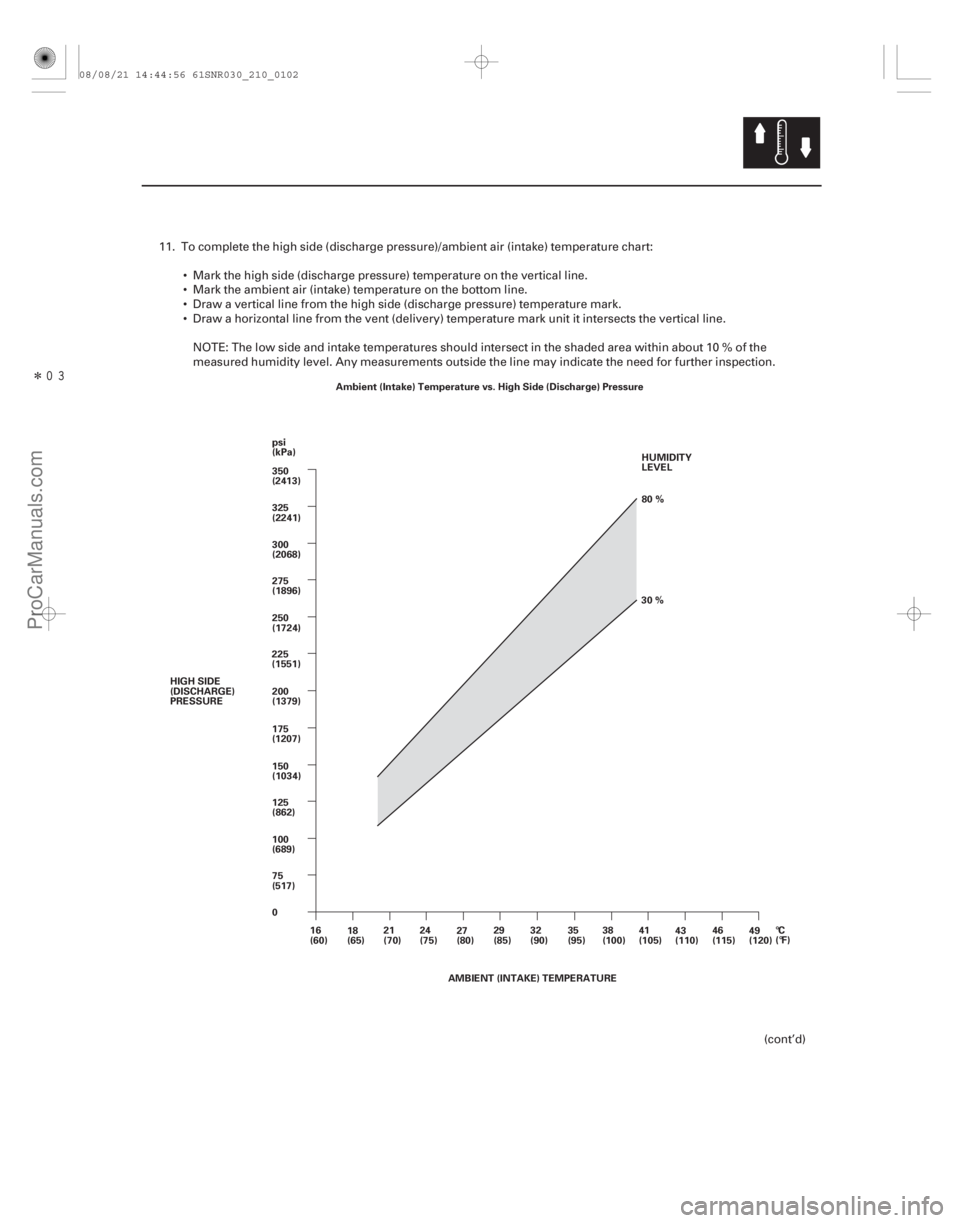
Î
21-101
80 %HUMIDITY
LEVEL
°C
(°F)
49
(120)
psi
(kPa)
350
(2413)
275
(1896)
175
(1207)
HIGH SIDE
(DISCHARGE)
PRESSURE
35
(95)
Ambient (Intake) Temperature vs. High Side (Discharge) Pressure
AMBIENT (INTAKE) TEMPERATURE 30 %
300
(2068)
200
(1379)
125
(862) 325
(2241)
250
(1724)
225
(1551)
150
(1034)
100
(689)
75
(517) 0 46
(115)
43
(110)
41
(105)
38
(100)
32
(90)
29
(85)
27
(80)
24
(75)
21
(70)
18
(65)
16
(60)
11. To complete the high side (discharge pressure)/ambient air (intake) temperature chart:
Mark the high side (discharge pressure) temperature on the vertical line.
Mark the ambient air (intake) temperature on the bottom line.
Draw a vertical line from the high side (discharge pressure) temperature mark.
Draw a horizontal line from the vent (delivery) temperature mark unit it intersects the vertical line.NOTE: The low side and intake temperatures should intersect in the shaded area within about 10 % of the
measured humidity level. Any measurements outside the line may indicate the need for further inspection.
(cont’d)
08/08/21 14:44:56 61SNR030_210_0102
ProCarManuals.com
DYNOMITE -2009-