Page 3601 of 4770
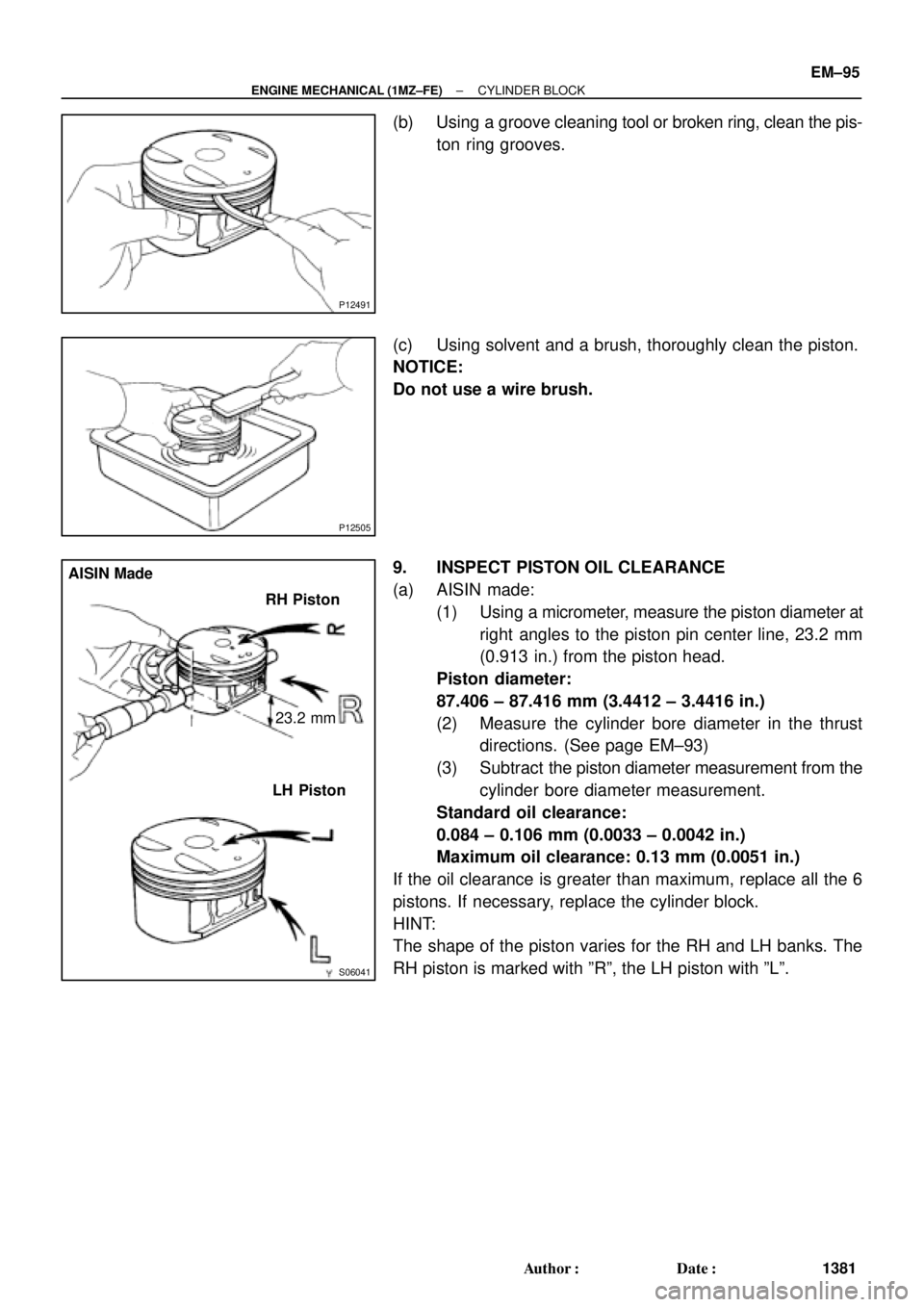
P12491
P12505
S06041
AISIN Made
RH Piston
LH Piston23.2 mm
± ENGINE MECHANICAL (1MZ±FE)CYLINDER BLOCK
EM±95
1381 Author: Date:
(b) Using a groove cleaning tool or broken ring, clean the pis-
ton ring grooves.
(c) Using solvent and a brush, thoroughly clean the piston.
NOTICE:
Do not use a wire brush.
9. INSPECT PISTON OIL CLEARANCE
(a) AISIN made:
(1) Using a micrometer, measure the piston diameter at
right angles to the piston pin center line, 23.2 mm
(0.913 in.) from the piston head.
Piston diameter:
87.406 ± 87.416 mm (3.4412 ± 3.4416 in.)
(2) Measure the cylinder bore diameter in the thrust
directions. (See page EM±93)
(3) Subtract the piston diameter measurement from the
cylinder bore diameter measurement.
Standard oil clearance:
0.084 ± 0.106 mm (0.0033 ± 0.0042 in.)
Maximum oil clearance: 0.13 mm (0.0051 in.)
If the oil clearance is greater than maximum, replace all the 6
pistons. If necessary, replace the cylinder block.
HINT:
The shape of the piston varies for the RH and LH banks. The
RH piston is marked with ºRº, the LH piston with ºLº.
Page 3602 of 4770
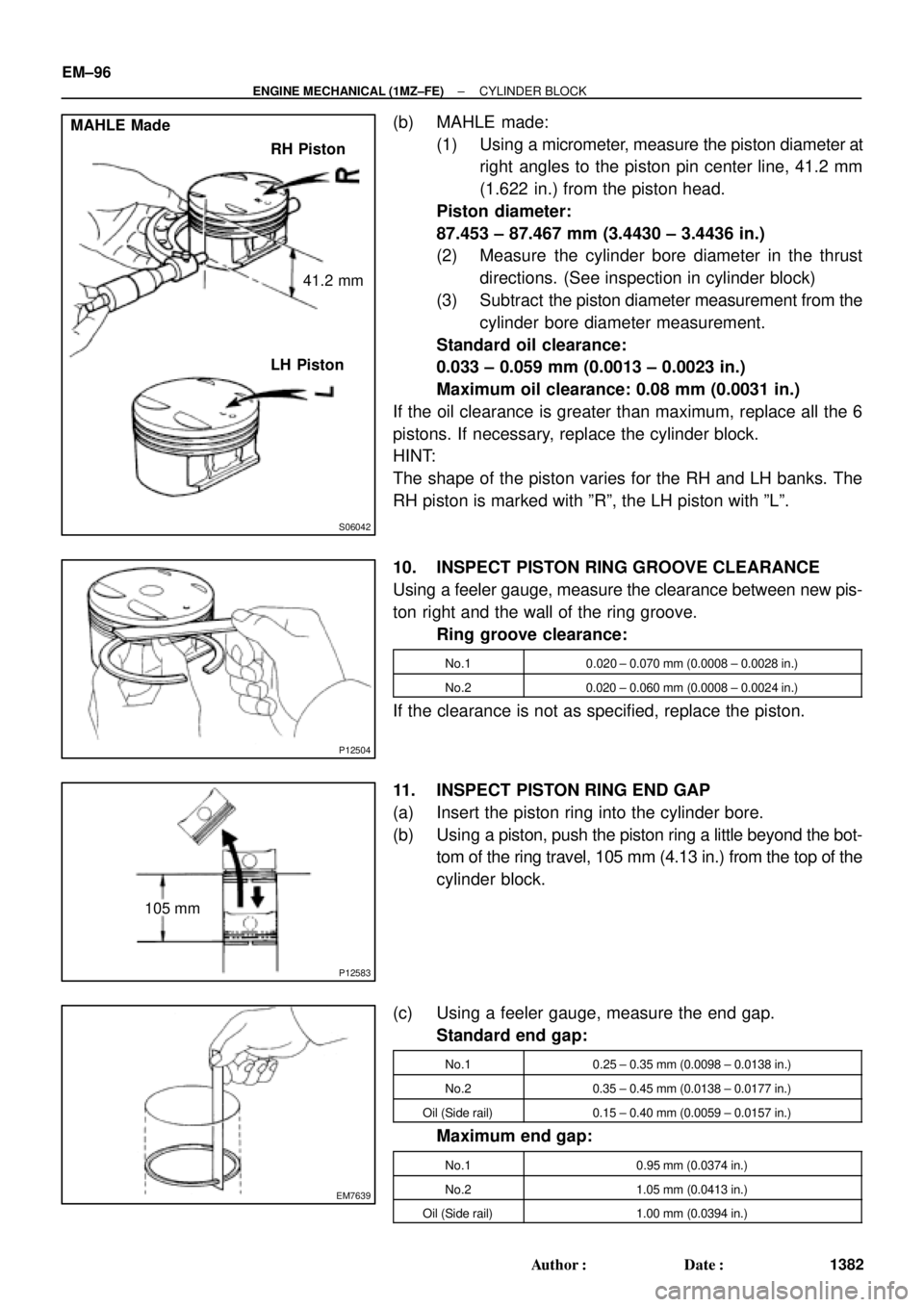
S06042
MAHLE Made
RH Piston
41.2 mm
LH Piston
P12504
P12583
105 mm
EM7639
EM±96
± ENGINE MECHANICAL (1MZ±FE)CYLINDER BLOCK
1382 Author: Date:
(b) MAHLE made:
(1) Using a micrometer, measure the piston diameter at
right angles to the piston pin center line, 41.2 mm
(1.622 in.) from the piston head.
Piston diameter:
87.453 ± 87.467 mm (3.4430 ± 3.4436 in.)
(2) Measure the cylinder bore diameter in the thrust
directions. (See inspection in cylinder block)
(3) Subtract the piston diameter measurement from the
cylinder bore diameter measurement.
Standard oil clearance:
0.033 ± 0.059 mm (0.0013 ± 0.0023 in.)
Maximum oil clearance: 0.08 mm (0.0031 in.)
If the oil clearance is greater than maximum, replace all the 6
pistons. If necessary, replace the cylinder block.
HINT:
The shape of the piston varies for the RH and LH banks. The
RH piston is marked with ºRº, the LH piston with ºLº.
10. INSPECT PISTON RING GROOVE CLEARANCE
Using a feeler gauge, measure the clearance between new pis-
ton right and the wall of the ring groove.
Ring groove clearance:
No.10.020 ± 0.070 mm (0.0008 ± 0.0028 in.)
No.20.020 ± 0.060 mm (0.0008 ± 0.0024 in.)
If the clearance is not as specified, replace the piston.
11. INSPECT PISTON RING END GAP
(a) Insert the piston ring into the cylinder bore.
(b) Using a piston, push the piston ring a little beyond the bot-
tom of the ring travel, 105 mm (4.13 in.) from the top of the
cylinder block.
(c) Using a feeler gauge, measure the end gap.
Standard end gap:
No.10.25 ± 0.35 mm (0.0098 ± 0.0138 in.)
No.20.35 ± 0.45 mm (0.0138 ± 0.0177 in.)
Oil (Side rail)0.15 ± 0.40 mm (0.0059 ± 0.0157 in.)
Maximum end gap:
No.10.95 mm (0.0374 in.)
No.21.05 mm (0.0413 in.)
Oil (Side rail)1.00 mm (0.0394 in.)
Page 3603 of 4770
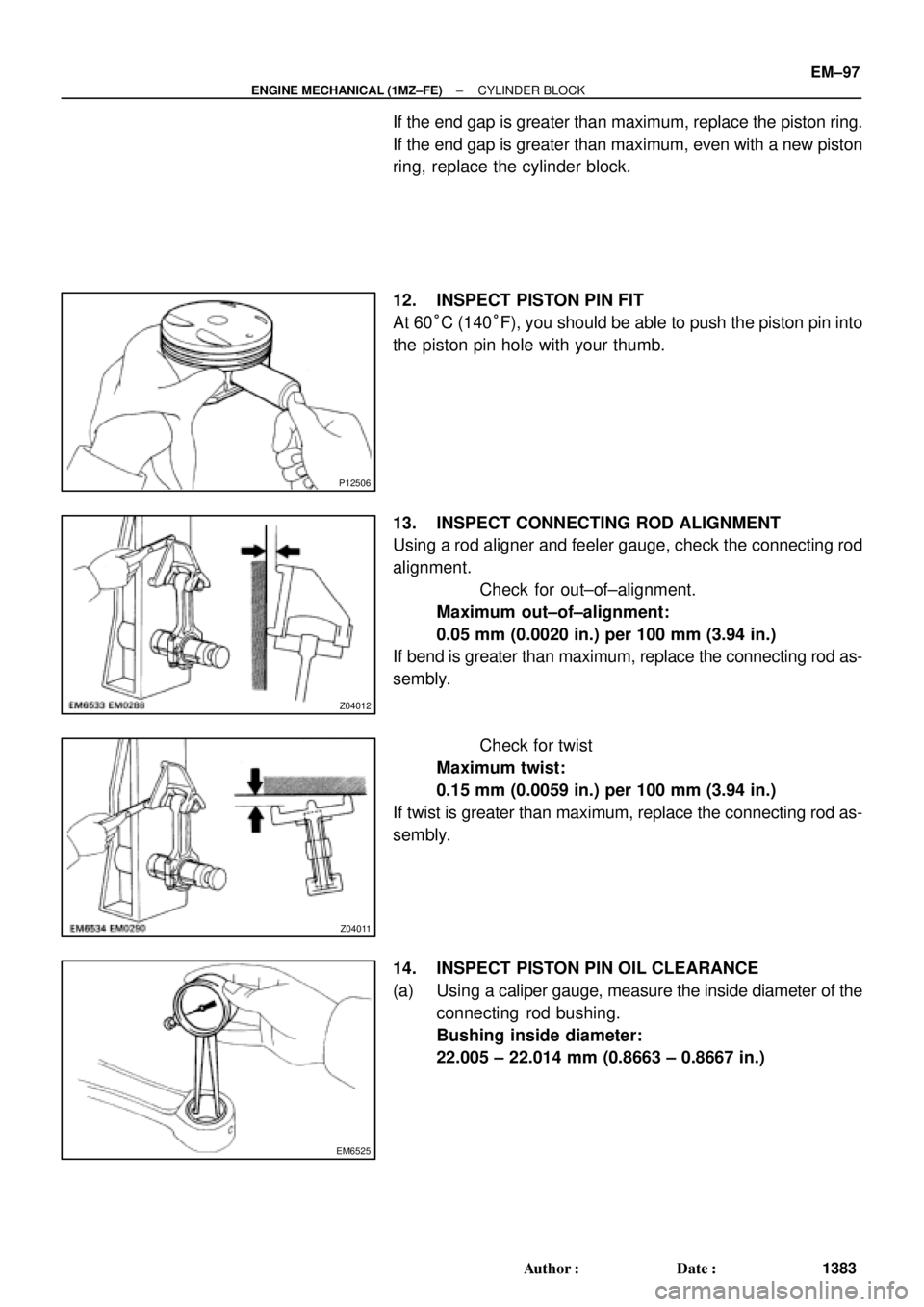
P12506
Z04012
Z04011
EM6525
± ENGINE MECHANICAL (1MZ±FE)CYLINDER BLOCK
EM±97
1383 Author: Date:
If the end gap is greater than maximum, replace the piston ring.
If the end gap is greater than maximum, even with a new piston
ring, replace the cylinder block.
12. INSPECT PISTON PIN FIT
At 60°C (140°F), you should be able to push the piston pin into
the piston pin hole with your thumb.
13. INSPECT CONNECTING ROD ALIGNMENT
Using a rod aligner and feeler gauge, check the connecting rod
alignment.
Check for out±of±alignment.
Maximum out±of±alignment:
0.05 mm (0.0020 in.) per 100 mm (3.94 in.)
If bend is greater than maximum, replace the connecting rod as-
sembly.
Check for twist
Maximum twist:
0.15 mm (0.0059 in.) per 100 mm (3.94 in.)
If twist is greater than maximum, replace the connecting rod as-
sembly.
14. INSPECT PISTON PIN OIL CLEARANCE
(a) Using a caliper gauge, measure the inside diameter of the
connecting rod bushing.
Bushing inside diameter:
22.005 ± 22.014 mm (0.8663 ± 0.8667 in.)
Page 3604 of 4770
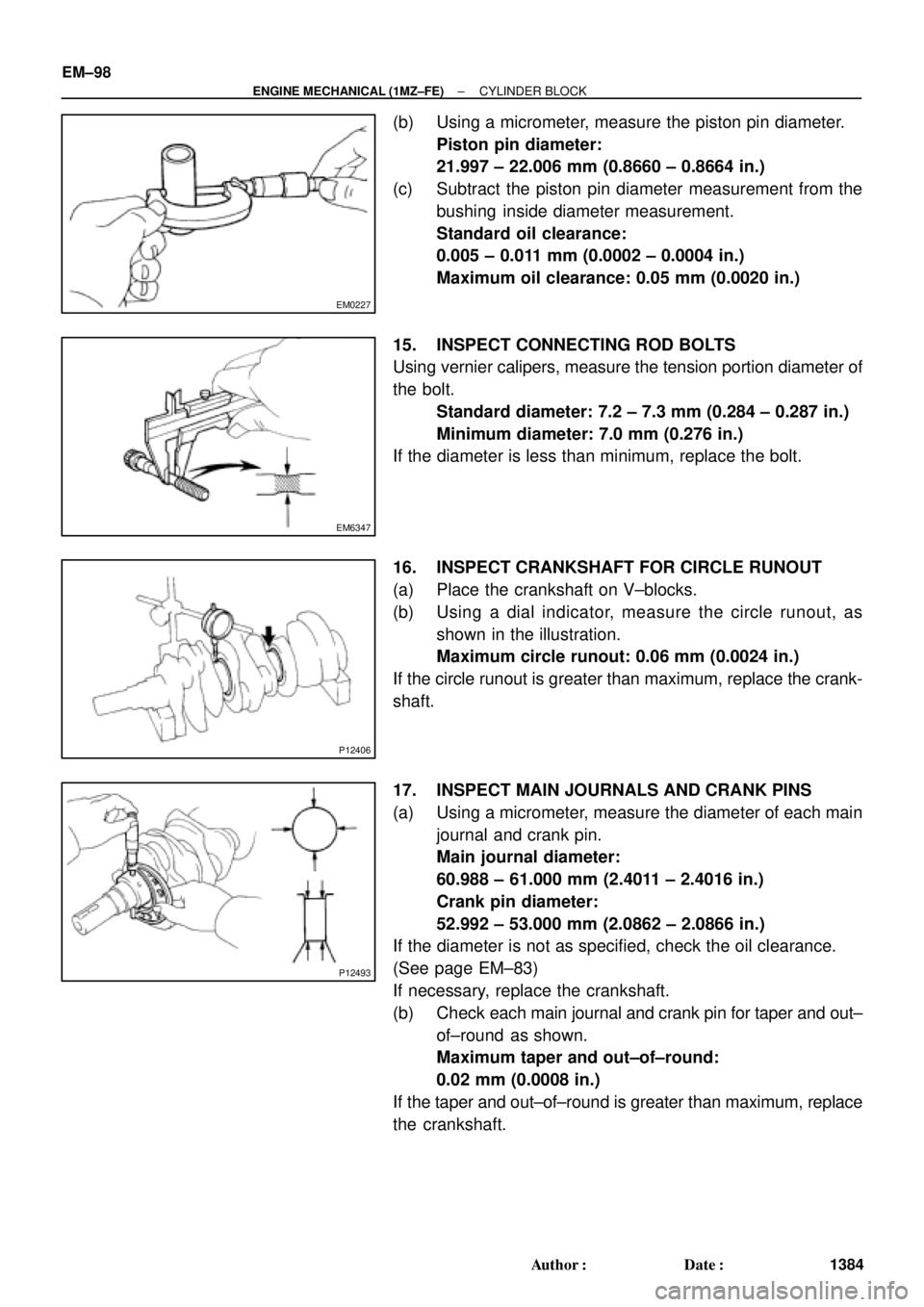
EM0227
EM6347
P12406
P12493
EM±98
± ENGINE MECHANICAL (1MZ±FE)CYLINDER BLOCK
1384 Author: Date:
(b) Using a micrometer, measure the piston pin diameter.
Piston pin diameter:
21.997 ± 22.006 mm (0.8660 ± 0.8664 in.)
(c) Subtract the piston pin diameter measurement from the
bushing inside diameter measurement.
Standard oil clearance:
0.005 ± 0.011 mm (0.0002 ± 0.0004 in.)
Maximum oil clearance: 0.05 mm (0.0020 in.)
15. INSPECT CONNECTING ROD BOLTS
Using vernier calipers, measure the tension portion diameter of
the bolt.
Standard diameter: 7.2 ± 7.3 mm (0.284 ± 0.287 in.)
Minimum diameter: 7.0 mm (0.276 in.)
If the diameter is less than minimum, replace the bolt.
16. INSPECT CRANKSHAFT FOR CIRCLE RUNOUT
(a) Place the crankshaft on V±blocks.
(b) Using a dial indicator, measure the circle runout, as
shown in the illustration.
Maximum circle runout: 0.06 mm (0.0024 in.)
If the circle runout is greater than maximum, replace the crank-
shaft.
17. INSPECT MAIN JOURNALS AND CRANK PINS
(a) Using a micrometer, measure the diameter of each main
journal and crank pin.
Main journal diameter:
60.988 ± 61.000 mm (2.4011 ± 2.4016 in.)
Crank pin diameter:
52.992 ± 53.000 mm (2.0862 ± 2.0866 in.)
If the diameter is not as specified, check the oil clearance.
(See page EM±83)
If necessary, replace the crankshaft.
(b) Check each main journal and crank pin for taper and out±
of±round as shown.
Maximum taper and out±of±round:
0.02 mm (0.0008 in.)
If the taper and out±of±round is greater than maximum, replace
the crankshaft.
Page 3605 of 4770
EM0YT±01
EM6363
SST
EM6364
Oil
Hole
EM6535
P00326
P12589
± ENGINE MECHANICAL (1MZ±FE)CYLINDER BLOCK
EM±99
1385 Author: Date:
REPLACEMENT
1. REPLACE CONNECTING ROD BUSHING
(a) Using SST and a press, press out the bushing.
SST 09222±30010
(b) Align the oil holes of a new bushing and the connecting
rod.
(c) Using SST and a press, press in the bushing.
SST 09222±30010
(d) Using a pin hole grinder, hone the bushing to obtain the
standard specified clearance (See page EM±93) be-
tween the bushing and piston pin.
(e) Check the piston pin fit at normal room temperature. Coat
the piston pin with engine oil, and push it into the connect-
ing rod with your thumb.
2. REPLACE CRANKSHAFT FRONT OIL SEAL
(See page LU±13)
3. REPLACE CRANKSHAFT REAR OIL SEAL
HINT:
There are 2 methods ((a) and (b)) to replace the oil seal which
are as follows:
(a) If the rear oil seal retainer is removed from the cylinder
block.
(1) Using a screwdriver and hammer, tap out the oil
seal.
Page 3606 of 4770
P12570
SST
P12808
Cut Position
P12810
SST EM±100
± ENGINE MECHANICAL (1MZ±FE)CYLINDER BLOCK
1386 Author: Date:
(2) Using SST and a hammer, tap in a new oil seal until
its surface is flush with the rear oil seal retainer
edge.
SST 09223±15030, 09950±70010 (09951±07100)
(3) Apply MP grease to the oil seal lip.
(b) If the rear oil seal retainer is installed to the cylinder block.
(1) Using a knife, cut off the oil seal lip.
(2) Using a screwdriver, pry out the oil seal.
NOTICE:
Be careful not to damage the crankshaft. Tape the screw-
driver tip.
(3) Apply MP grease to a new oil seal lip.
(4) Using SST and a hammer, tap in the oil seal until its
surface is flush with the rear oil seal retainer edge.
SST 09223±15030, 09950±70010 (09951±07100)
Page 3607 of 4770
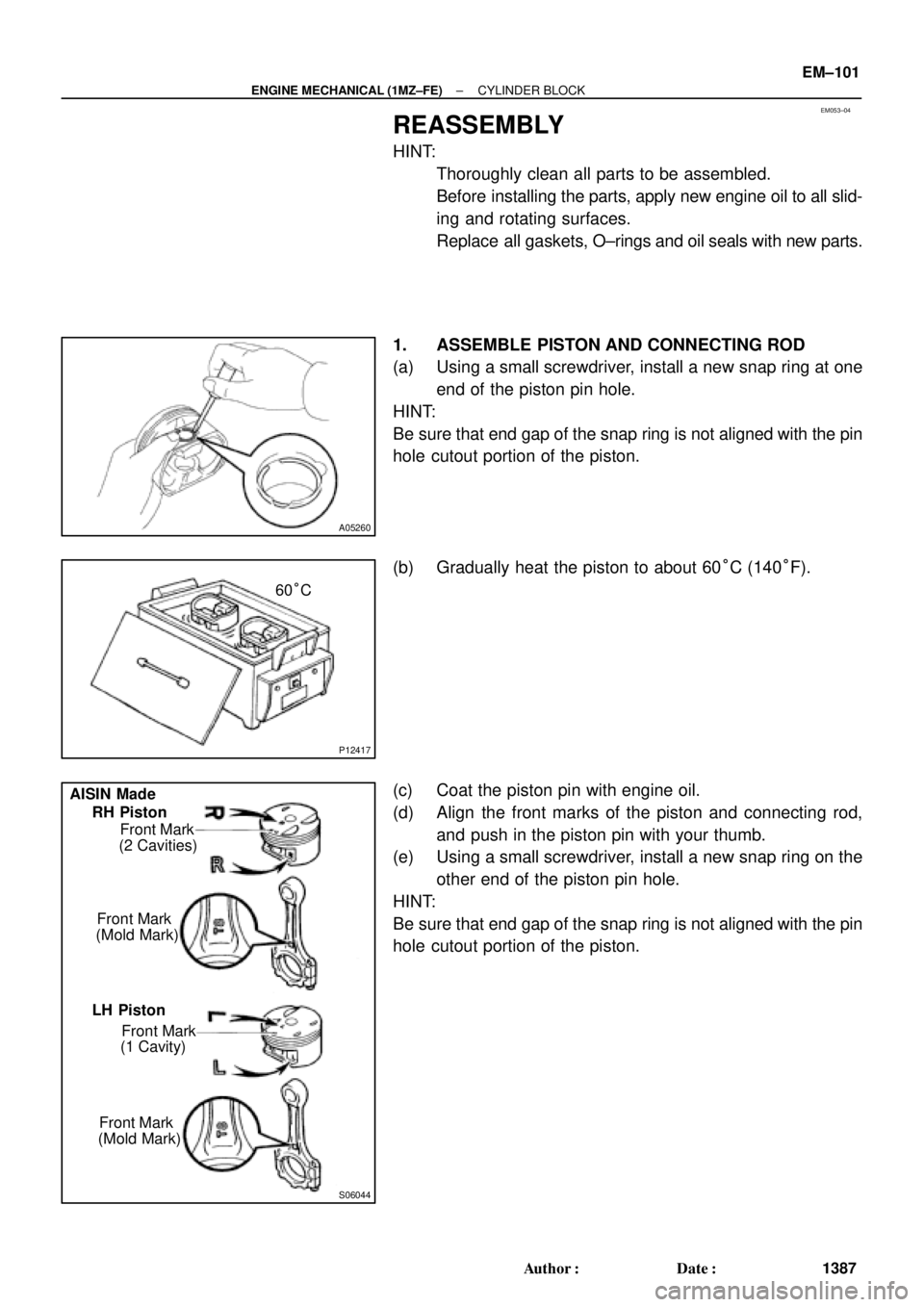
EM053±04
A05260
P12417
60°C
S06044
Front Mark AISIN Made
RH Piston
LH Piston(2 Cavities)
Front Mark
(Mold Mark)
Front Mark
(1 Cavity)
Front Mark
(Mold Mark)
± ENGINE MECHANICAL (1MZ±FE)CYLINDER BLOCK
EM±101
1387 Author: Date:
REASSEMBLY
HINT:
Thoroughly clean all parts to be assembled.
Before installing the parts, apply new engine oil to all slid-
ing and rotating surfaces.
Replace all gaskets, O±rings and oil seals with new parts.
1. ASSEMBLE PISTON AND CONNECTING ROD
(a) Using a small screwdriver, install a new snap ring at one
end of the piston pin hole.
HINT:
Be sure that end gap of the snap ring is not aligned with the pin
hole cutout portion of the piston.
(b) Gradually heat the piston to about 60°C (140°F).
(c) Coat the piston pin with engine oil.
(d) Align the front marks of the piston and connecting rod,
and push in the piston pin with your thumb.
(e) Using a small screwdriver, install a new snap ring on the
other end of the piston pin hole.
HINT:
Be sure that end gap of the snap ring is not aligned with the pin
hole cutout portion of the piston.
Page 3608 of 4770
S06043
Front Mark MAHLE Made
RH Piston
LH Piston(1 Cavity)
Front Mark
(Mold Mark)
Front Mark
(1 Cavity)
Front Mark
(Mold Mark)
Z09179
Code Mark
Code Mark No.1
No.2
S06058
RH Piston
Lower Side Rail
No.2
Compression
Front Mark
Expander
Upper Side Rail
No.1
Compression
Lower Side Rail
Upper Side RailFront Mark LH PistonNo.2
Compression
Expander
No.1
CompressionFront Markor EM±102
± ENGINE MECHANICAL (1MZ±FE)CYLINDER BLOCK
1388 Author: Date:
2. INSTALL PISTON RINGS
(a) Install the oil ring expander and 2 side rails by hand.
(b) Using a piston ring expander, install the 2 compression
rings with the code mark facing upward.
Code mark:
No.11R, T or G1
No.22R, 2T or G2
(c) Position the piston rings so that the ring ends are as
shown.
NOTICE:
Do not align the ring ends.