Page 1609 of 4770
AC0NI±02
N21047
Fresh
Clamp
N20239
Clamp Cool
± AIR CONDITIONINGAIR CONDITIONING CONTROL ASSEMBLY
AC±87
2569 Author: Date:
INSTALLATION
Installation is in the reverse order of removal
(See page AC±82).
1. AFTER INSTALLATION INSPECT A/C CONTROL LE-
VER AND DIAL OPERATION
Move the control dial and lever left and right and check fro stiff-
ness and binding through the full range of the lever and dial.
If there is stiffness or binding, proceed next step.
2. ADJUST A/C CONTROL CABLES
(a) Set A/C control assembly in these conditions:
(1) Air inlet control lever in ºFRESHº position
(2) Temperature control dial in ºMAX. COOLº position.
(b) Adjust air inlet control cable.
(1) Pull out the inner of air inlet cable and hit the link of
blower unit on the link stopper.
(2) Set the cable connector to lever pin and clamp the
cable outer.
(c) Adjust air mix control cable.
Set the cable connector to air mix link pin on left side of
A/C unit and clamp the cable outer on.
Page 1610 of 4770
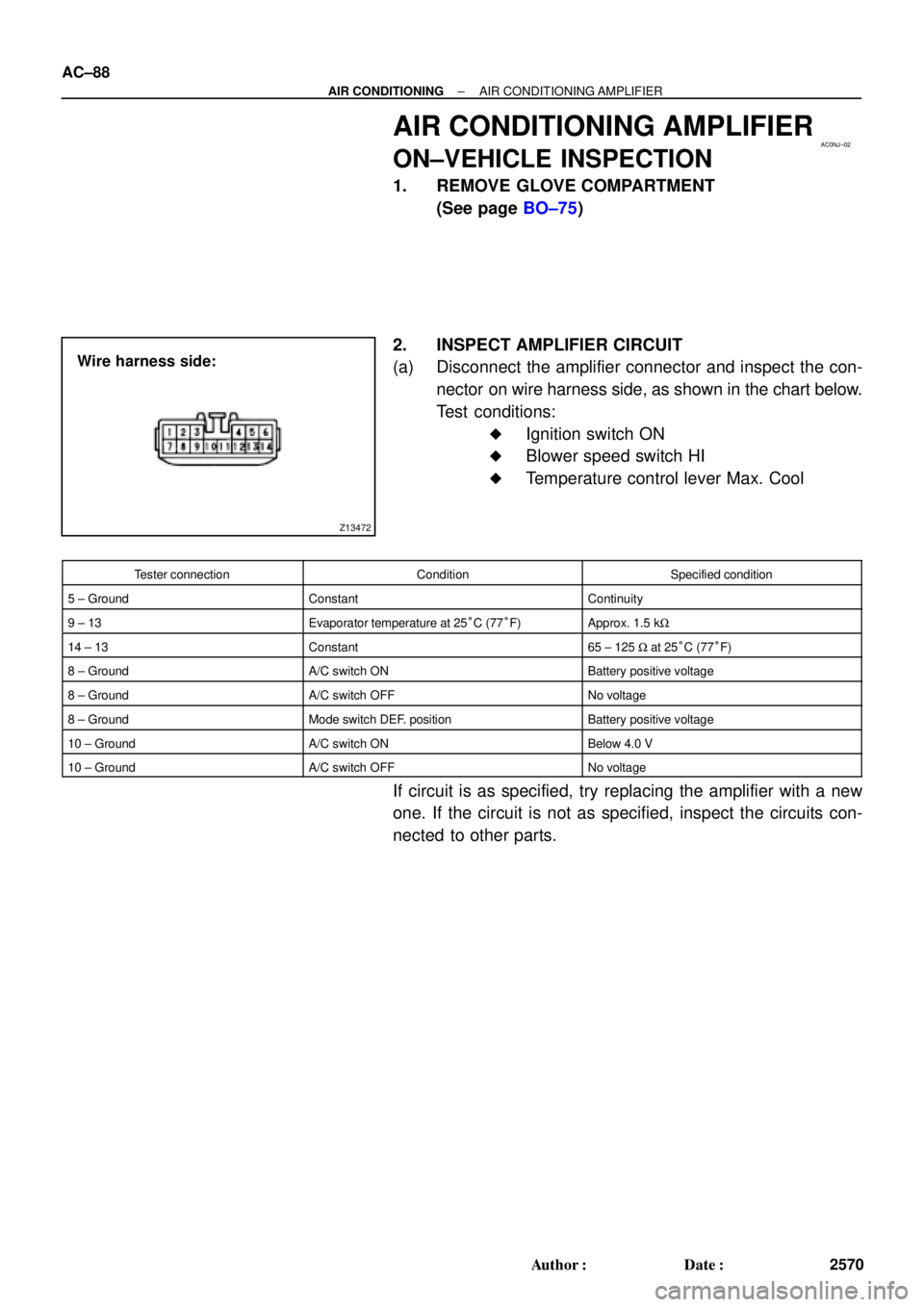
AC0NJ±02
Z13472
Wire harness side: AC±88
± AIR CONDITIONINGAIR CONDITIONING AMPLIFIER
2570 Author: Date:
AIR CONDITIONING AMPLIFIER
ON±VEHICLE INSPECTION
1. REMOVE GLOVE COMPARTMENT
(See page BO±75)
2. INSPECT AMPLIFIER CIRCUIT
(a) Disconnect the amplifier connector and inspect the con-
nector on wire harness side, as shown in the chart below.
Test conditions:
Ignition switch ON
Blower speed switch HI
Temperature control lever Max. Cool
Tester connectionConditionSpecified condition
5 ± GroundConstantContinuity
9 ± 13Evaporator temperature at 25°C (77°F)Approx. 1.5 kW
14 ± 13Constant65 ± 125 W at 25°C (77°F)
8 ± GroundA/C switch ONBattery positive voltage
8 ± GroundA/C switch OFFNo voltage
8 ± GroundMode switch DEF. positionBattery positive voltage
10 ± GroundA/C switch ONBelow 4.0 V
10 ± GroundA/C switch OFFNo voltage
If circuit is as specified, try replacing the amplifier with a new
one. If the circuit is not as specified, inspect the circuits con-
nected to other parts.
Page 1611 of 4770
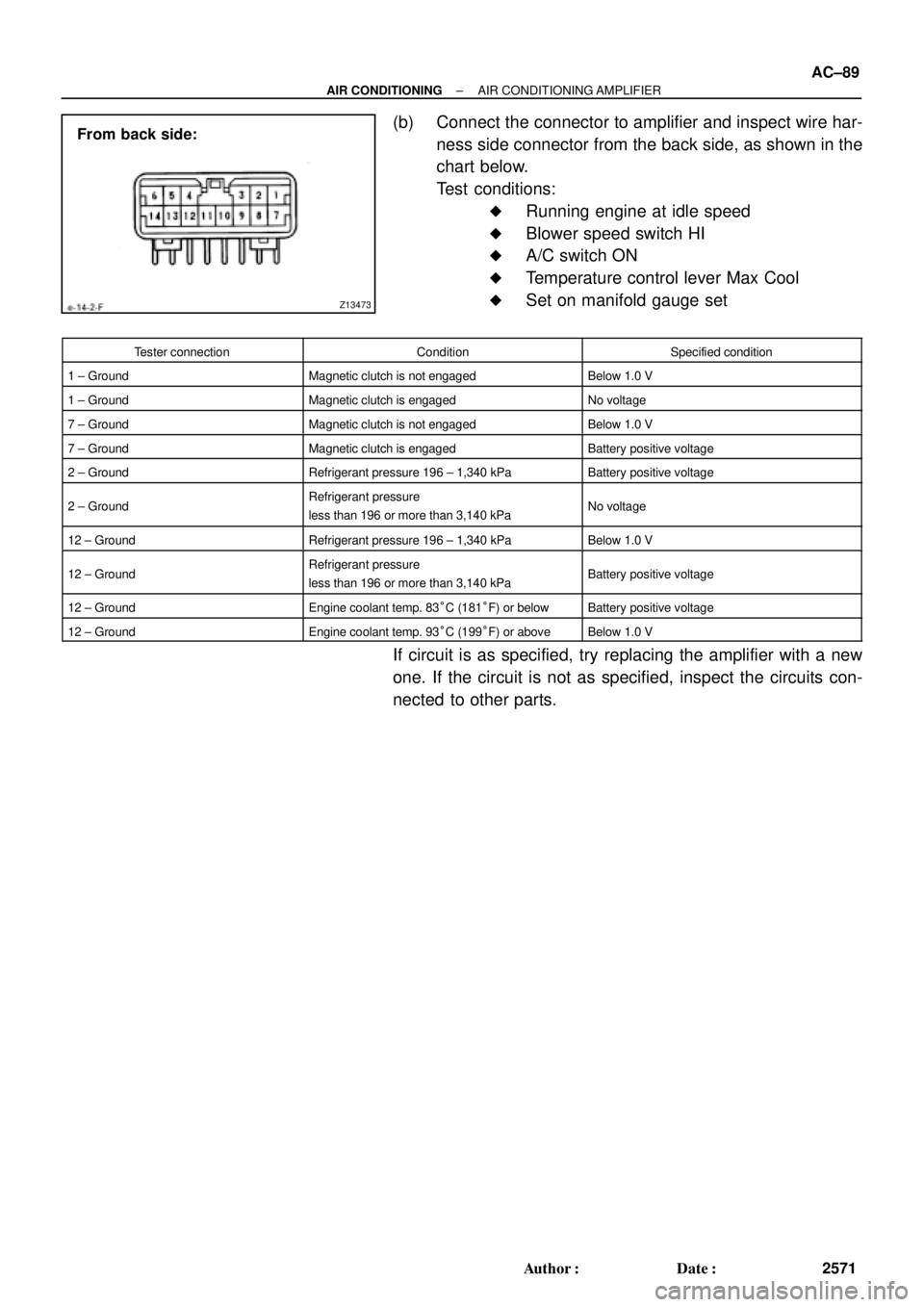
Z13473
From back side:
± AIR CONDITIONINGAIR CONDITIONING AMPLIFIER
AC±89
2571 Author: Date:
(b) Connect the connector to amplifier and inspect wire har-
ness side connector from the back side, as shown in the
chart below.
Test conditions:
Running engine at idle speed
Blower speed switch HI
A/C switch ON
Temperature control lever Max Cool
Set on manifold gauge set
Tester connectionConditionSpecified condition
1 ± GroundMagnetic clutch is not engagedBelow 1.0 V
1 ± GroundMagnetic clutch is engagedNo voltage
7 ± GroundMagnetic clutch is not engagedBelow 1.0 V
7 ± GroundMagnetic clutch is engagedBattery positive voltage
2 ± GroundRefrigerant pressure 196 ± 1,340 kPaBattery positive voltage
2 ± GroundRefrigerant pressure
less than 196 or more than 3,140 kPaNo voltage
12 ± GroundRefrigerant pressure 196 ± 1,340 kPaBelow 1.0 V
12 ± GroundRefrigerant pressure
less than 196 or more than 3,140 kPaBattery positive voltage
12 ± GroundEngine coolant temp. 83°C (181°F) or belowBattery positive voltage
12 ± GroundEngine coolant temp. 93°C (199°F) or aboveBelow 1.0 V
If circuit is as specified, try replacing the amplifier with a new
one. If the circuit is not as specified, inspect the circuits con-
nected to other parts.
Page 1612 of 4770
AC0NK±02
N20285
AC±90
± AIR CONDITIONINGAIR CONDITIONING AMPLIFIER
2572 Author: Date:
REMOVAL
1. REMOVE GLOVE COMPARTMENT
(See page BO±75)
2. REMOVE A/C AMPLIFIER
(a) Disconnect the connector.
(b) Release the 2 claws and pull out the amplifier.
Page 1613 of 4770
AC0NL±01
± AIR CONDITIONINGAIR CONDITIONING AMPLIFIER
AC±91
2573 Author: Date:
INSTALLATION
Installation is in the reverse order of removal (See page AC±90).
Page 1614 of 4770
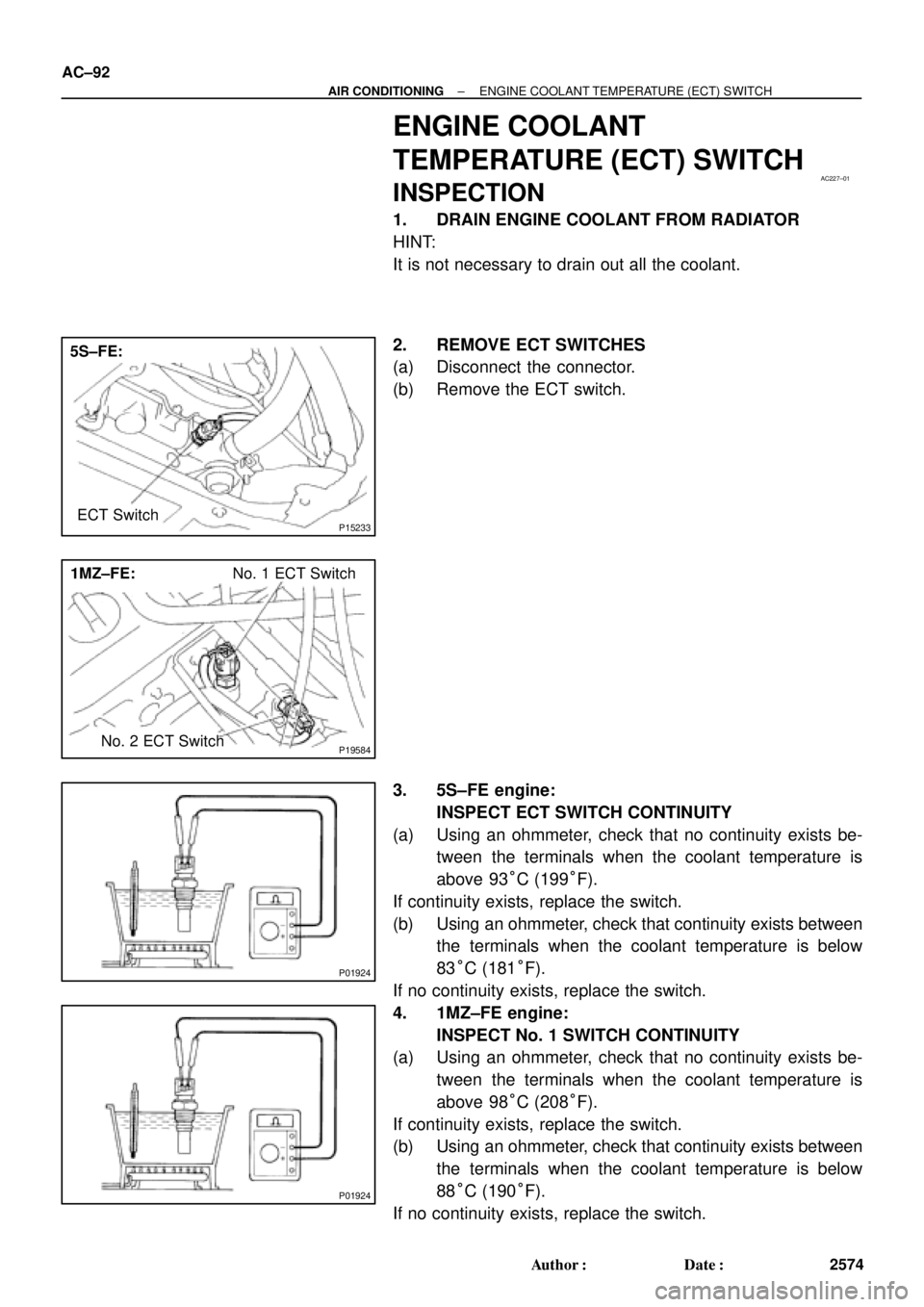
AC227±01
P15233
5S±FE:
ECT Switch
P19584
1MZ±FE:No. 1 ECT Switch
No. 2 ECT Switch
P01924
P01924
AC±92
± AIR CONDITIONINGENGINE COOLANT TEMPERATURE (ECT) SWITCH
2574 Author: Date:
ENGINE COOLANT
TEMPERATURE (ECT) SWITCH
INSPECTION
1. DRAIN ENGINE COOLANT FROM RADIATOR
HINT:
It is not necessary to drain out all the coolant.
2. REMOVE ECT SWITCHES
(a) Disconnect the connector.
(b) Remove the ECT switch.
3. 5S±FE engine:
INSPECT ECT SWITCH CONTINUITY
(a) Using an ohmmeter, check that no continuity exists be-
tween the terminals when the coolant temperature is
above 93°C (199°F).
If continuity exists, replace the switch.
(b) Using an ohmmeter, check that continuity exists between
the terminals when the coolant temperature is below
83°C (181°F).
If no continuity exists, replace the switch.
4. 1MZ±FE engine:
INSPECT No. 1 SWITCH CONTINUITY
(a) Using an ohmmeter, check that no continuity exists be-
tween the terminals when the coolant temperature is
above 98°C (208°F).
If continuity exists, replace the switch.
(b) Using an ohmmeter, check that continuity exists between
the terminals when the coolant temperature is below
88°C (190°F).
If no continuity exists, replace the switch.
Page 1615 of 4770
P06722
P15233
5S± FE:
ECT Switch
P19584
1MZ±FE:
No. 1 ECT Switch
No. 2 ECT Switch
± AIR CONDITIONINGENGINE COOLANT TEMPERATURE (ECT) SWITCH
AC±93
2575 Author: Date:
5. 1MZ±FE engine:
INSPECT No. 2 SWITCH CONTINUITY
(a) Using an ohmmeter, check that no continuity exists be-
tween the terminal and switch body when the coolant
temperature is above 93°C (199°F).
If continuity exists, replace the switch.
(b) Using an ohmmeter, check that continuity exists between
the terminals when the coolant temperature is below
83°C (181°F).
If no continuity exists, replace the switch.
6. INSTALL ECT SWITCHES
(a) Install the ECT switch.
HINT:
Lubricate a new O±ring with soapy water and install the switch.
(b) Connect the connector.
Page 1616 of 4770
INTRODUCTIONHOW TO USE THIS MANUAL ±
IN±1
HOW TO USE THIS MANUAL
To assist you in finding your way through the manual, the Section Title and major heading are given
at the top of every page.
PREPARATION
Preparation lists the SST (Special Service Tools), recommended tools, equipment, lubricant and SSM
(Special Service Materials) which should be prepared before beginning the operation and explains the
purpose of each one.
REPAIR PROCEDURES
Most repair operations begin with an overview illustration. It identifies the components and shows how
the parts fit together.
Example:
IN002±0W