Page 169 of 4770
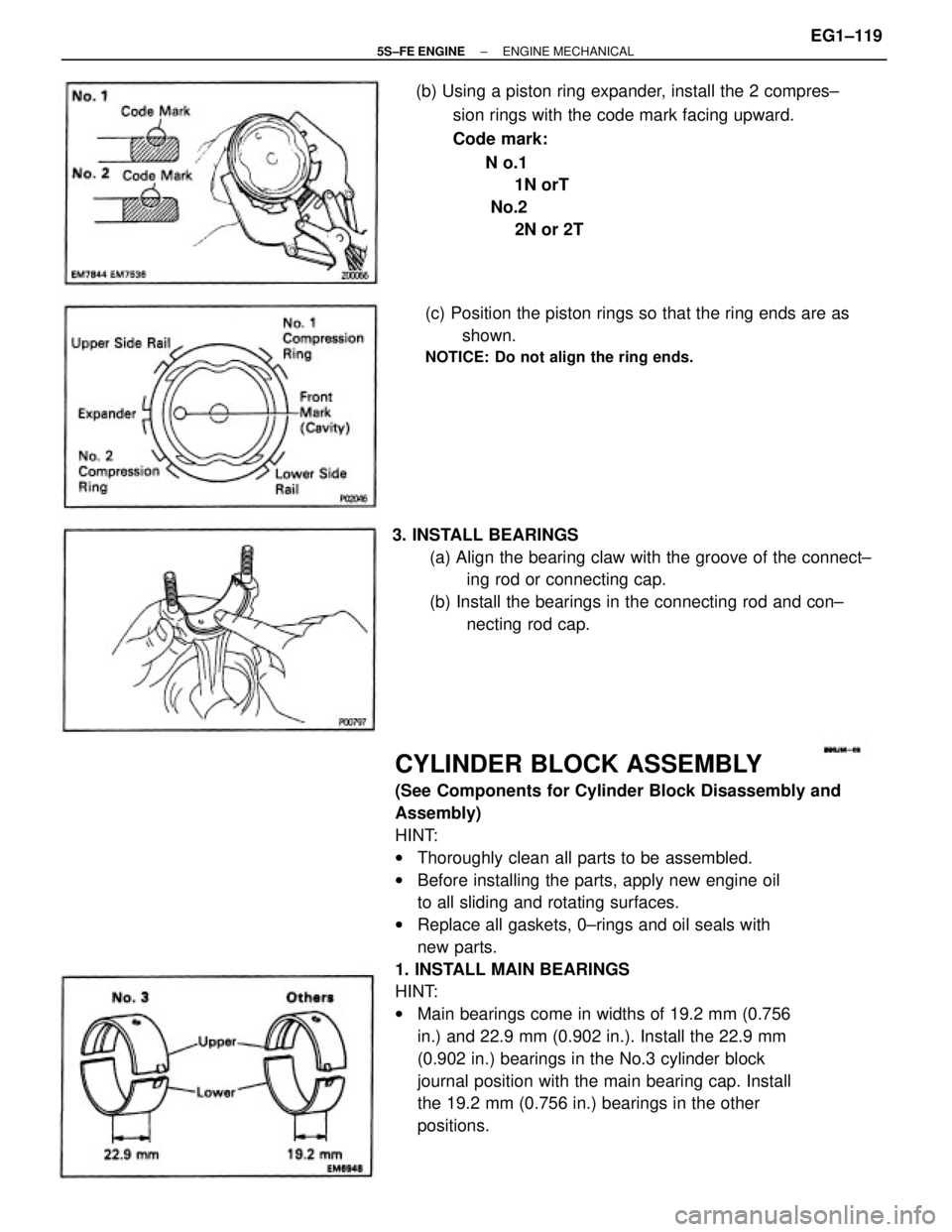
CYLINDER BLOCK ASSEMBLY
(See Components for Cylinder Block Disassembly and
Assembly)
HINT:
wThoroughly clean all parts to be assembled.
wBefore installing the parts, apply new engine oil
to all sliding and rotating surfaces.
wReplace all gaskets, 0±rings and oil seals with
new parts.
1. INSTALL MAIN BEARINGS
HINT:
wMain bearings come in widths of 19.2 mm (0.756
in.) and 22.9 mm (0.902 in.). Install the 22.9 mm
(0.902 in.) bearings in the No.3 cylinder block
journal position with the main bearing cap. Install
the 19.2 mm (0.756 in.) bearings in the other
positions. (b) Using a piston ring expander, install the 2 compres±
sion rings with the code mark facing upward.
Code mark:
N o.1
1N orT
No.2
2N or 2T
3. INSTALL BEARINGS
(a) Align the bearing claw with the groove of the connect±
ing rod or connecting cap.
(b) Install the bearings in the connecting rod and con±
necting rod cap. (c) Position the piston rings so that the ring ends are as
shown.
NOTICE: Do not align the ring ends.
± 5S±FE ENGINEENGINE MECHANICALEG1±119
Page 170 of 4770
(b) Align the bearing claw with the claw groove of the
main bearing cap, and push in the 5 lower bearings.
HINT: A number is marked on each main bearing cap
to indicate the installation position.
2. INSTALL UPPER THRUST WASHERS
Install the 2 thrust washers under the No.3 journal
position of the cylinder block with the oil grooves
facing outward.(a) Align the bearing claw with the claw groove of the
cylinder block, and push in the 5 upper bearings. wUpper bearings have an oil groove and oil holes;
lower bearings do not.
3. PLACE CRANKSHAFT ON CYLINDER BLOCK
± 5S±FE ENGINEENGINE MECHANICALEG1±120
Page 171 of 4770
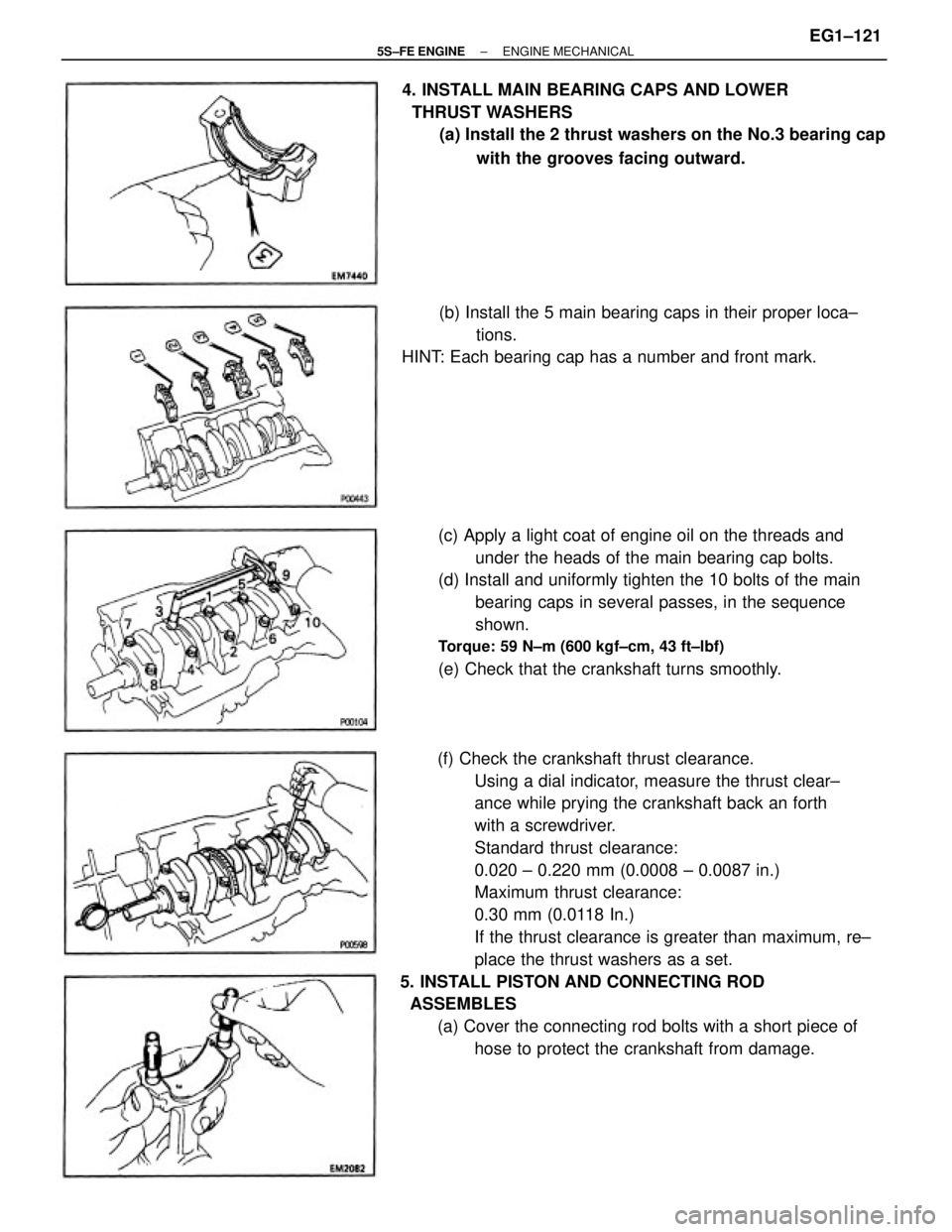
(f) Check the crankshaft thrust clearance.
Using a dial indicator, measure the thrust clear±
ance while prying the crankshaft back an forth
with a screwdriver.
Standard thrust clearance:
0.020 ± 0.220 mm (0.0008 ± 0.0087 in.)
Maximum thrust clearance:
0.30 mm (0.0118 In.)
If the thrust clearance is greater than maximum, re±
place the thrust washers as a set.
5. INSTALL PISTON AND CONNECTING ROD
ASSEMBLES
(a) Cover the connecting rod bolts with a short piece of
hose to protect the crankshaft from damage. (c) Apply a light coat of engine oil on the threads and
under the heads of the main bearing cap bolts.
(d) Install and uniformly tighten the 10 bolts of the main
bearing caps in several passes, in the sequence
shown.
Torque: 59 N±m (600 kgf±cm, 43 ft±lbf)
(e) Check that the crankshaft turns smoothly. 4. INSTALL MAIN BEARING CAPS AND LOWER
THRUST WASHERS
(a) Install the 2 thrust washers on the No.3 bearing cap
with the grooves facing outward.
(b) Install the 5 main bearing caps in their proper loca±
tions.
HINT: Each bearing cap has a number and front mark.
± 5S±FE ENGINEENGINE MECHANICALEG1±121
Page 172 of 4770
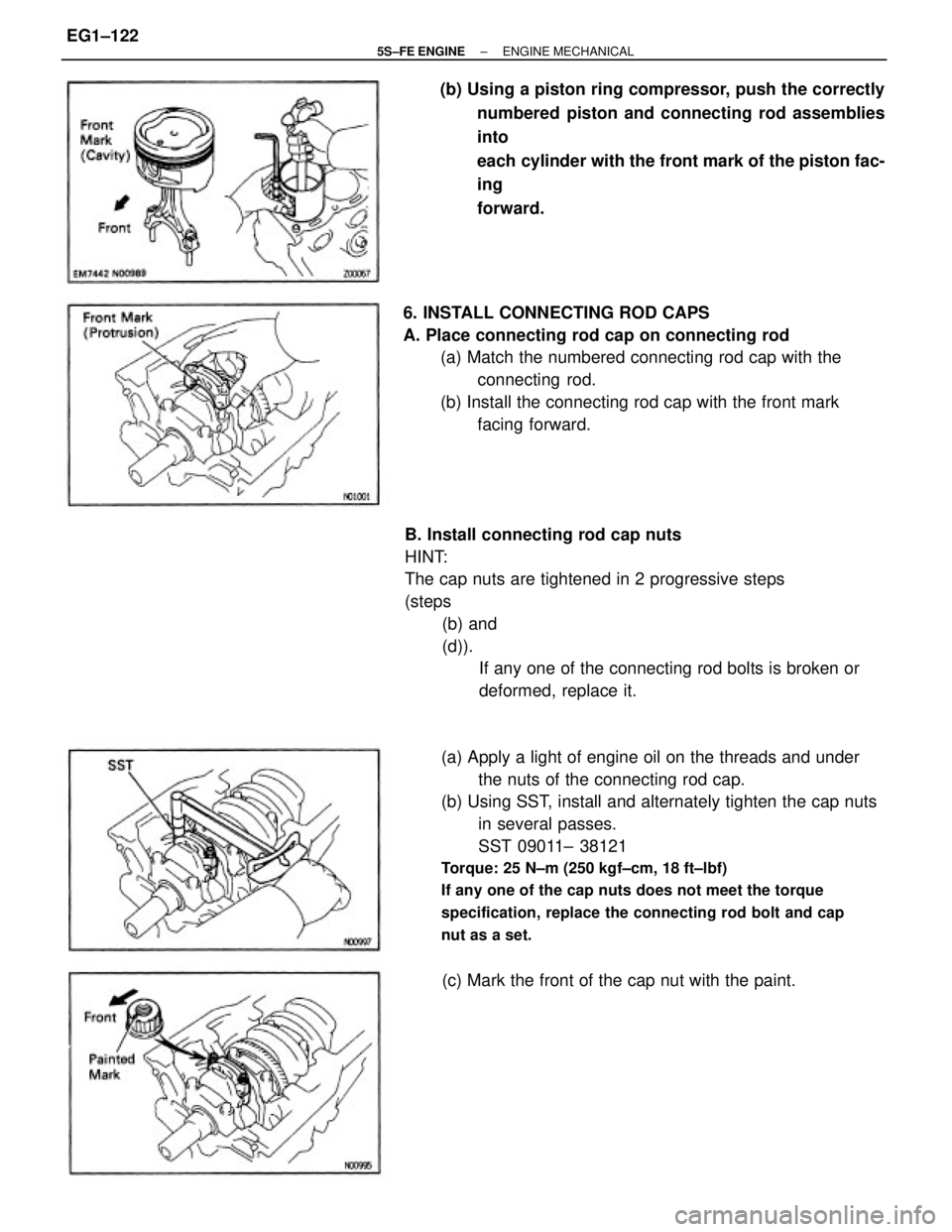
(a) Apply a light of engine oil on the threads and under
the nuts of the connecting rod cap.
(b) Using SST, install and alternately tighten the cap nuts
in several passes.
SST 09011± 38121
Torque: 25 N±m (250 kgf±cm, 18 ft±lbf)
If any one of the cap nuts does not meet the torque
specification, replace the connecting rod bolt and cap
nut as a set.
B. Install connecting rod cap nuts
HINT:
The cap nuts are tightened in 2 progressive steps
(steps
(b) and
(d)).
If any one of the connecting rod bolts is broken or
deformed, replace it. 6. INSTALL CONNECTING ROD CAPS
A. Place connecting rod cap on connecting rod
(a) Match the numbered connecting rod cap with the
connecting rod.
(b) Install the connecting rod cap with the front mark
facing forward. (b) Using a piston ring compressor, push the correctly
numbered piston and connecting rod assemblies
into
each cylinder with the front mark of the piston fac-
ing
forward.
(c) Mark the front of the cap nut with the paint.
± 5S±FE ENGINEENGINE MECHANICALEG1±122
Page 173 of 4770
(g) Check the connecting rod thrust clearance.
Using a dial indicator, measure the thrust clear±
ance while moving the connecting rod back an
forth.
Standard thrust clearance:
0.160 ± 0.312 mm (0.0063 ± 0.0123 In.)
Maximum thrust clearance:
0.35 mm 10.0138 In.)
If the thrust clearance is greater than maximum, re±
place the connecting rod assembly. If necessary, re±
place the crankshaft. (d) Retighten the cap nuts 90 as shown.
(e) Check that the painted mark is now at a 90 angle to
the front.
(f) Check that the crankshaft turns smoothly.
7. INSTALL ENGINE BALANCER
(a) Turn the crankshaft, and set the No. 1 cylinder TDC as
shown in the illustration.
(b) Set the balance shafts so that the punch marks of the
balance shafts are aligned with the grooves of the
No.
2 housing.
± 5S±FE ENGINEENGINE MECHANICALEG1±123
Page 174 of 4770
(h) Recheck that the punch marks of the balance shafts
are aligned with the grooves of No.2 housing.
8. CHECK AND ADJUST BACKLASH OF
CRANKSHAFT GEAR AND NO.1 BALANCE SHAFT
GEAR (See page EG1±94) (c) Wipe clean the installation surface of the spacer.
(d) Place the spacers on the cylinder block.
HINT: When replacing the crankshaft and/or balance
shaft, use the thickest spacers.
(e) Place the engine balancer on the cylinder block.
(f) Check that punch marks shown in the illustration of
the balance shafts are align with the grooves of the
No.2 housing.
(g) While pulling the center part of the engine balancer
in the direction of the arrow, uniformly tighten the
6
bolts in several passes, in the sequence shown.
Torque: 49 N±m (500 kgf±cm, 36 ft±lbf)
9. INSTALL REAR OIL SEAL RETAINER
Install a new gasket and the retainer with the 6 bolts.
Torque: 9.3 N±m (95 kgf±cm, 82 in.±lbf)
± 5S±FE ENGINEENGINE MECHANICALEG1±124
Page 175 of 4770
2. w/ OIL COOLER:
INSTALL OIL COOLER
3. INSTALL OIL FILTER
4. INSTALL OIL PUMP AND OIL PAN
5. INSTALL WATER PUMP AND GENERATOR
ADJUSTING BAR
6. INSTALL CYLINDER HEAD
7. INSTALL PULLEYS AND TIMING BELT
POST ASSEMBLY
1. INSTALL KNOCK SENSOR
Using SST, install the knock sensor.
SST 09816±30010
Torque: 37 N±m (380 kgf±cm. 27 ft±lbf)
8. INSTALL PS PUMP BRACKET
Install the PS pump bracket with 3 bolts.
Torque: 43 N±m (440 kgf±cm, 32 ft±lbf)
9. INSTALL GENERATOR
10. INSTALL DISTRIBUTOR
11. REMOVE ENGINE STAND
12. INSTALL REAR END PLATE
Torque: 9.3 N±m (95 kgf±cm, 82 in.±lbf)
± 5S±FE ENGINEENGINE MECHANICALEG1±125
Page 176 of 4770
13. M/T:
INSTALL FLYWHEEL
(a) Apply adhesive to 2 or 3 threads of the mounting bolt
end.
Adhesive:
Part No.08833±00070. THREE BOND 1324 or equi±
valent
14. A/T:
INSTALL DRIVE PLATE (See procedure step 13)
Torque: 83 N±m (850 kgf±cm, 61 ft±lbf)
15. M/T:
INSTALL CLUTCH DISC AND COVER(b) Install the flywheel on the crankshaft.
(c) install and uniformly tighten the mounting bolts in
several passes, in the sequence shown.
Torque: 88 N±m (900 kgf±cm, 66 ft±lbf)
± 5S±FE ENGINEENGINE MECHANICALEG1±126