Page 281 of 4770
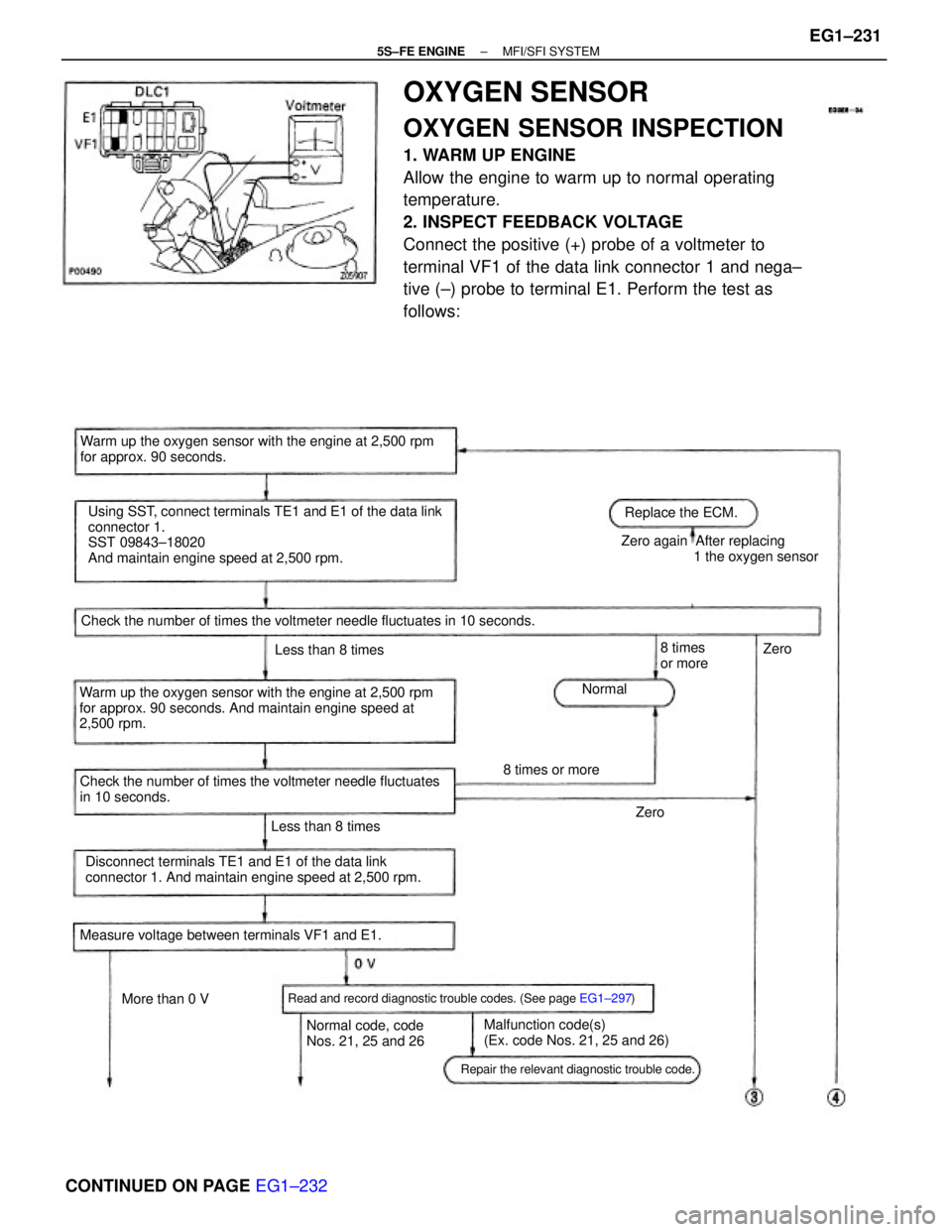
OXYGEN SENSOR
OXYGEN SENSOR INSPECTION
1. WARM UP ENGINE
Allow the engine to warm up to normal operating
temperature.
2. INSPECT FEEDBACK VOLTAGE
Connect the positive (+) probe of a voltmeter to
terminal VF1 of the data link connector 1 and nega±
tive (±) probe to terminal E1. Perform the test as
follows:
Using SST, connect terminals TE1 and E1 of the data link
connector 1.
SST 09843±18020
And maintain engine speed at 2,500 rpm.
Warm up the oxygen sensor with the engine at 2,500 rpm
for approx. 90 seconds. And maintain engine speed at
2,500 rpm.Warm up the oxygen sensor with the engine at 2,500 rpm
for approx. 90 seconds.
CONTINUED ON PAGE EG1±232
Disconnect terminals TE1 and E1 of the data link
connector 1. And maintain engine speed at 2,500 rpm. Check the number of times the voltmeter needle fluctuates
in 10 seconds.Zero again After replacing
1 the oxygen sensor
Check the number of times the voltmeter needle fluctuates in 10 seconds.
Read and record diagnostic trouble codes. (See page EG1±297)
Malfunction code(s)
(Ex. code Nos. 21, 25 and 26) Measure voltage between terminals VF1 and E1.
Repair the relevant diagnostic trouble code.
Normal code, code
Nos. 21, 25 and 26Replace the ECM.
Less than 8 timesLess than 8 times
8 times or more
More than 0 V8 times
or more
NormalZero
Zero
± 5S±FE ENGINEMFI/SFI SYSTEMEG1±231
Page 282 of 4770
Disconnect the engine coolant temp. sensor connector and
connect resistor with a resistance of 4 ± 8 k
or send an
equivalent simulation signal.
Warm up the oxygen sensor with the engine at 2,500 rpm for
approx. 90 seconds. And maintain engine at 2,500 rpm.Disconnect terminals TE1 and E1 of the data link connector 1.
And maintain engine at 2,500 rpm.
CONTINUED FROM PAGE EG1±231
Read and record diagnostic trouble codes. (See page
EG1±297)
Connect terminals TE1 and E1 of the data link connector 1.Malfunction code(s)
(Ex. code Nos. 21, 25 and 26)
Measure voltage between terminals VF1 and E1.
Measure voltage between terminals VF1 and E1, Measure voltage between terminals VF1 and E1.Repair the relevant diagnostic trouble code.
Normal code, code Nos.
21, 25 and 26
Replace the oxygen sensor. Disconnect the PCV hose.
Repair (Over Lean) Repair (Over rich)More than 0 V
± 5S±FE ENGINEMFI/SFI SYSTEMEG1±232
Page 283 of 4770
SUB OXYGEN SENSOR
SUB OXYGEN SENSOR INSPECTION
INSPECT SUB OXYGEN SENSOR
HINT: Inspect only when code No. 27 is displayed.
(a) Cancel the diagnostic trouble code. (See page EG1±299)
(b) Warm up the engine until it reaches normal operating
temperature.
(c) M/T:
Drive for 5 minutes or more at a speed less than 80
km/h (50 mph) in 4th or 5th gear.
A/T:
Drive for 5 minutes or more at a speed less than 80
km/h (50 mph) in ªDº position.
(d) Following the conditions in step (c), fully depress on
the accelerator pedal for 2 seconds or more.
(e) Stop the vehicle and turn the ignition switch OFF.
(f) Carry out steps (b), (c) and (d) again to test accelera±
tion. If code No.27 appears again, check the sub oxygen
sensor circuit. If the circuit is normal, replace the sub
oxygen sensor.
± 5S±FE ENGINEMFI/SFI SYSTEMEG1±233
Page 284 of 4770
ENGINE CONTROL MODULE (ECM)
ECM REMOVAL AND INSTALLATION
ECM INSPECTION
(See page EG1±318)
± 5S±FE ENGINEMFI/SFI SYSTEMEG1±234
Page 285 of 4770
2. CONNECT TACHOMETER TO ENGINE
Connect the test probe of a tachometer to terminal IG
(±) of the data link connector 1.
NOTICE:
wNEVER allow the tachometer terminal to touch
ground as it could result in damage to the igniter
and/or ignition coil.
wAs some tachometers are not compatible with this
ignition system, we recommend that you confirm
the compatibility of yours before use.
3. INSPECT FUEL CUT RPM
(a) Increase the engine speed to at least 2,500 rpm.
(b) Use a sound scope to check for injector operating
noise.
(c) Check that when the throttle lever is released, injector
operation noise stops momentarily and then resumes.
HINT: Measure with the A/C OFF.
Fuel return speed:
1,500 rpm
4. DISCONNECT TACHOMETER
FUEL CUT RPM
FUEL CUT RPM INSPECTION
1. WARM UP ENGINE
Allow the engine to warm up to normal operating
temperature.
± 5S±FE ENGINEMFI/SFI SYSTEMEG1±235
Page 286 of 4770
Clearance between stop screw and lever
0 mm (0 in.)
0.50 mm (0.020 in.)
0.70 mm (0.028 in.)
Throttle valve fully open
SERVICE SPECIFICATIONS
SERVICE DATA
Resistance
Injection volume
Difference between each cylinder
Fuel leakage
Throttle body fully closed angle
Throttle opener setting speed
VSV for Fuel
pressure
(California
only)
EG R gas
temperature
sensorResistance (+B ± ISCC or ISCO) Throttle
position
sensor Fuel pressure
regulator
A/C idle ±up
valvePower source voltage
Fuel return rpm Fuel pressure
Throttle body
Fuel cut rpm VSV for EG Rat no vacuum
MAP sensor Fuel pump
IAT sensorECT sensor
Resistance Resistance
Resistance
Resistance Resistance
Resistance Resistance IAC valve Injector
± 5S±FE ENGINEMFI/SFI SYSTEMEG1±236
Page 287 of 4770
TORQUE SPECIFICATIONS
No.1 air intake chamber stay x Intake manifold
No.1 air intake chamber stay x Cylinder headFuel return pipe x Fuel pressure regulator Fuel pressure regulator x Delivery pipe
Fuel pulsation damper x Delivery pipe
Intake manifold stay x Intake manifold
Intake manifold stay x Cylinder blockFuel line (Flare nut type ± use SST)
Throttle body x Intake manifoldIntake manifold x Cylinder headDelivery pipe x Cylinder head
EGR pipe x Intake manifoldFuel pump side
Others Fuel line (Union bolt type)
Fuel pump x Fuel tankFuel tank band x Body
EGR pipe union nutPart tightened
± 5S±FE ENGINEMFI/SFI SYSTEMEG1±237
Page 288 of 4770
The cooling system is composed of the water jacket (inside the cylinder block and cylinder head),
radiator, water pump, thermostat, electric fan, hoses and other components.
Engine coolant which is heated in the water jacket is pumped to the radiator, through which an
electric fan blows air to cool the coolant as it passes through. Engine coolant which has been
cooled is then sent back to the engine by the water pump, where it cools the engine.
The water jacket is a network of channels in the shell of the cylinder block and cylinder head
through which coolant passes. It is designed to provide adequate cooling of the cylinders and
combustion chambers which become heated during engine operation.
DESCRIPTION
This engine utilizes a pressurized forced circulation cooling system which includes a thermostat
equipped with a bypass valve mounted on the inlet side.
OPERATIONCOOLING SYSTEM
± 5S±FE ENGINECOOLING SYSTEMEG1±238