Page 3481 of 4770
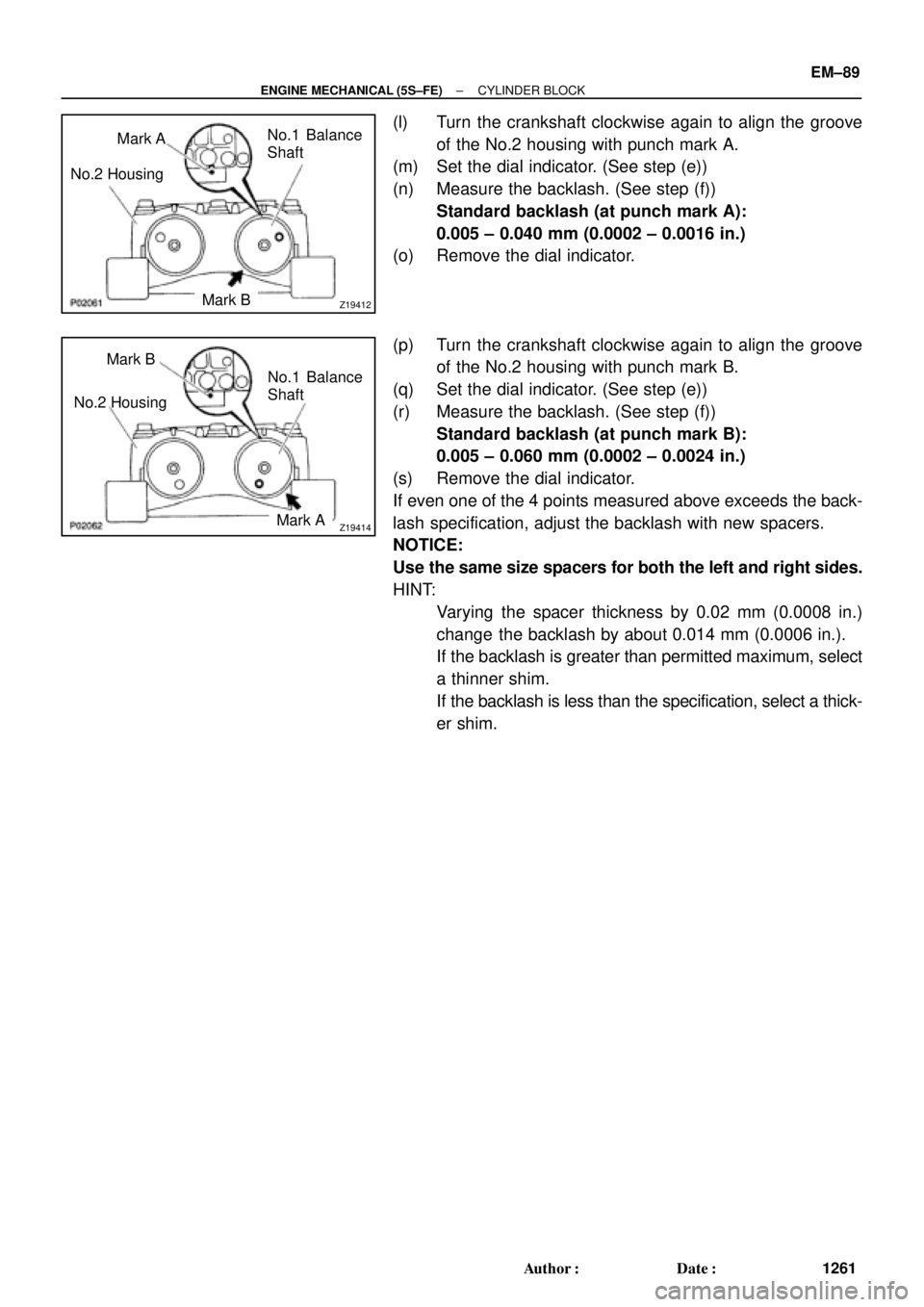
Z19412
No.1 Balance
Shaft Mark A
Mark B No.2 Housing
Z19414
Mark B
No.2 Housing
Mark A No.1 Balance
Shaft
± ENGINE MECHANICAL (5S±FE)CYLINDER BLOCK
EM±89
1261 Author: Date:
(l) Turn the crankshaft clockwise again to align the groove
of the No.2 housing with punch mark A.
(m) Set the dial indicator. (See step (e))
(n) Measure the backlash. (See step (f))
Standard backlash (at punch mark A):
0.005 ± 0.040 mm (0.0002 ± 0.0016 in.)
(o) Remove the dial indicator.
(p) Turn the crankshaft clockwise again to align the groove
of the No.2 housing with punch mark B.
(q) Set the dial indicator. (See step (e))
(r) Measure the backlash. (See step (f))
Standard backlash (at punch mark B):
0.005 ± 0.060 mm (0.0002 ± 0.0024 in.)
(s) Remove the dial indicator.
If even one of the 4 points measured above exceeds the back-
lash specification, adjust the backlash with new spacers.
NOTICE:
Use the same size spacers for both the left and right sides.
HINT:
Varying the spacer thickness by 0.02 mm (0.0008 in.)
change the backlash by about 0.014 mm (0.0006 in.).
If the backlash is greater than permitted maximum, select
a thinner shim.
If the backlash is less than the specification, select a thick-
er shim.
Page 3482 of 4770
A01917
Adjusting Spacer Selection Chart (Off±Vehicle)
Standard backlash (at punch mark A):
0.005 ± 0.40 mm (0.0002 ± 0.0016 in.)
EXAMPLE: The No.26 spacers are installed, and the measured backlash is
0.120 mm (0.0047 in.). Replace the No. 26 spacers with new No.11 spacers.New spacer thickness mm (in.)
1.74 (0.0685)
1.76 (0.0693)1.94 (0.0764)
1.78 (0.0701)1.96 (0.0772)
1.80 (0.0709)1.98 (0.0780)
1.82 (0.0717)1.84 (0.0724)
1.86 (0.0732)2.04 (0.0803)
2.06 (0.0811)
2.08 (0.0819)
2.00 (0.0787)
2.02 (0.0975)2.10 (0.0827)
2.12 (0.0835) 1.88 (0.0740)
1.90 (0.0748)
1.92 (0.0756) 01
05
0911
15
1923
2731
35
37
39 13
1721
25
2933
03
07 No. Thickness Thickness Thickness ThicknessNo. No.No.
Installed spacer
Measured
backlashNo.
mm (in.)
EM±90
± ENGINE MECHANICAL (5S±FE)CYLINDER BLOCK
1262 Author: Date:
Page 3483 of 4770
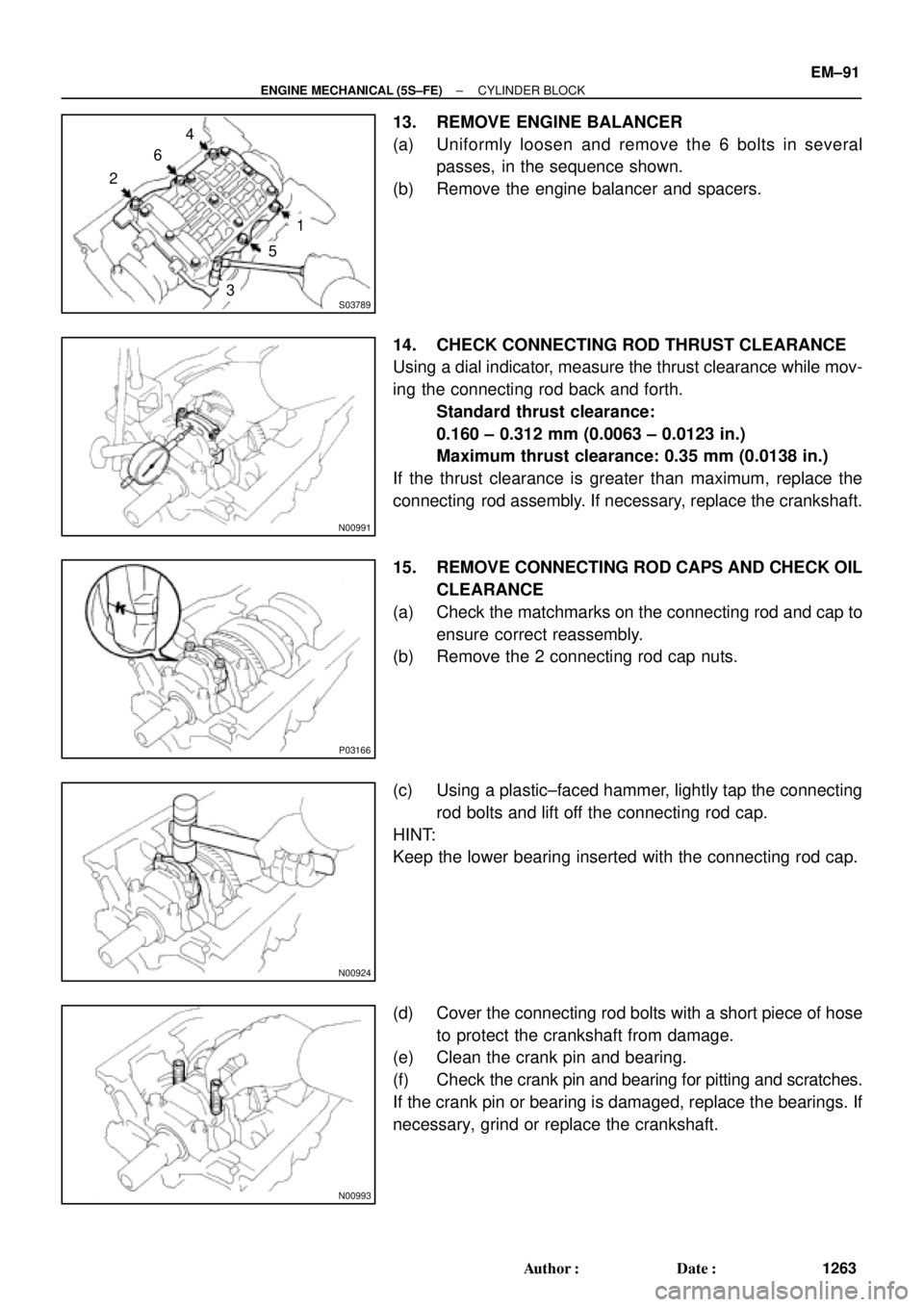
S03789
1
4
6
5
2
3
N00991
P03166
N00924
N00993
± ENGINE MECHANICAL (5S±FE)CYLINDER BLOCK
EM±91
1263 Author: Date:
13. REMOVE ENGINE BALANCER
(a) Uniformly loosen and remove the 6 bolts in several
passes, in the sequence shown.
(b) Remove the engine balancer and spacers.
14. CHECK CONNECTING ROD THRUST CLEARANCE
Using a dial indicator, measure the thrust clearance while mov-
ing the connecting rod back and forth.
Standard thrust clearance:
0.160 ± 0.312 mm (0.0063 ± 0.0123 in.)
Maximum thrust clearance: 0.35 mm (0.0138 in.)
If the thrust clearance is greater than maximum, replace the
connecting rod assembly. If necessary, replace the crankshaft.
15. REMOVE CONNECTING ROD CAPS AND CHECK OIL
CLEARANCE
(a) Check the matchmarks on the connecting rod and cap to
ensure correct reassembly.
(b) Remove the 2 connecting rod cap nuts.
(c) Using a plastic±faced hammer, lightly tap the connecting
rod bolts and lift off the connecting rod cap.
HINT:
Keep the lower bearing inserted with the connecting rod cap.
(d) Cover the connecting rod bolts with a short piece of hose
to protect the crankshaft from damage.
(e) Clean the crank pin and bearing.
(f) Check the crank pin and bearing for pitting and scratches.
If the crank pin or bearing is damaged, replace the bearings. If
necessary, grind or replace the crankshaft.
Page 3484 of 4770
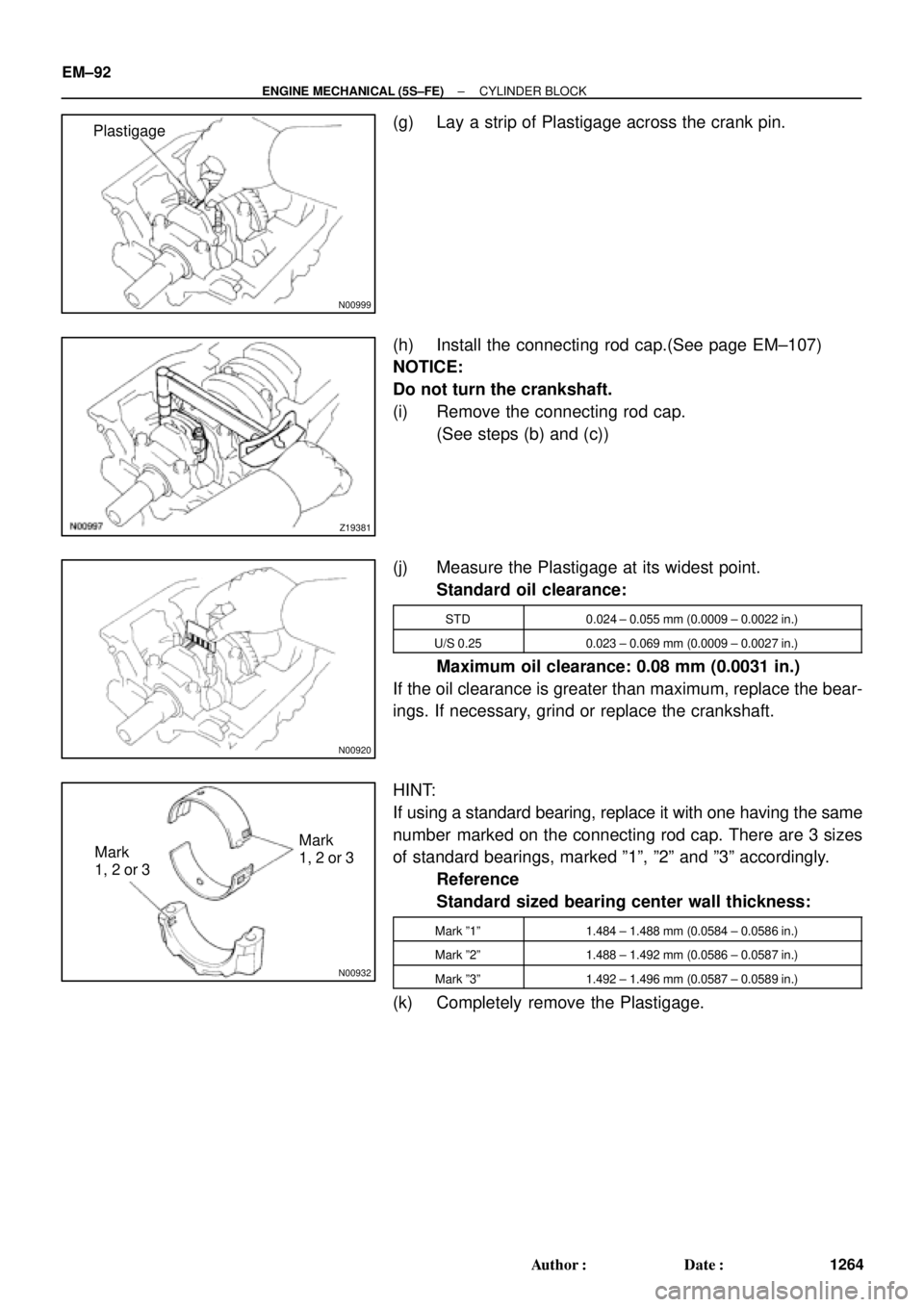
N00999
Plastigage
Z19381
N00920
N00932
Mark
1, 2 or 3Mark
1, 2 or 3 EM±92
± ENGINE MECHANICAL (5S±FE)CYLINDER BLOCK
1264 Author: Date:
(g) Lay a strip of Plastigage across the crank pin.
(h) Install the connecting rod cap.(See page EM±107)
NOTICE:
Do not turn the crankshaft.
(i) Remove the connecting rod cap.
(See steps (b) and (c))
(j) Measure the Plastigage at its widest point.
Standard oil clearance:
STD0.024 ± 0.055 mm (0.0009 ± 0.0022 in.)
U/S 0.250.023 ± 0.069 mm (0.0009 ± 0.0027 in.)
Maximum oil clearance: 0.08 mm (0.0031 in.)
If the oil clearance is greater than maximum, replace the bear-
ings. If necessary, grind or replace the crankshaft.
HINT:
If using a standard bearing, replace it with one having the same
number marked on the connecting rod cap. There are 3 sizes
of standard bearings, marked º1º, º2º and º3º accordingly.
Reference
Standard sized bearing center wall thickness:
Mark º1º1.484 ± 1.488 mm (0.0584 ± 0.0586 in.)
Mark º2º1.488 ± 1.492 mm (0.0586 ± 0.0587 in.)
Mark º3º1.492 ± 1.496 mm (0.0587 ± 0.0589 in.)
(k) Completely remove the Plastigage.
Page 3485 of 4770
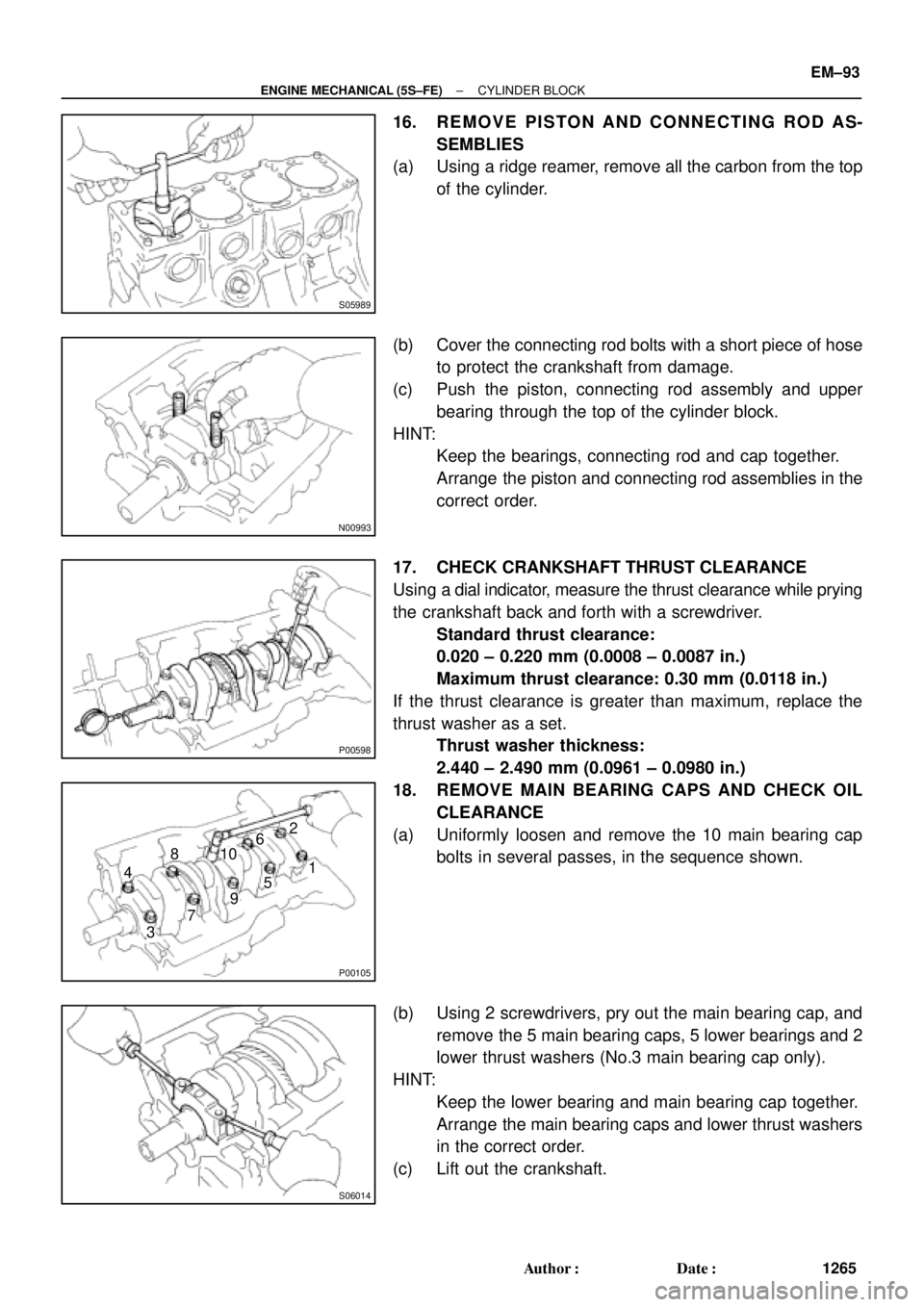
S05989
N00993
P00598
P00105
481062
1
5
9
7
3
S06014
± ENGINE MECHANICAL (5S±FE)CYLINDER BLOCK
EM±93
1265 Author: Date:
16. REMOVE PISTON AND CONNECTING ROD AS-
SEMBLIES
(a) Using a ridge reamer, remove all the carbon from the top
of the cylinder.
(b) Cover the connecting rod bolts with a short piece of hose
to protect the crankshaft from damage.
(c) Push the piston, connecting rod assembly and upper
bearing through the top of the cylinder block.
HINT:
Keep the bearings, connecting rod and cap together.
Arrange the piston and connecting rod assemblies in the
correct order.
17. CHECK CRANKSHAFT THRUST CLEARANCE
Using a dial indicator, measure the thrust clearance while prying
the crankshaft back and forth with a screwdriver.
Standard thrust clearance:
0.020 ± 0.220 mm (0.0008 ± 0.0087 in.)
Maximum thrust clearance: 0.30 mm (0.0118 in.)
If the thrust clearance is greater than maximum, replace the
thrust washer as a set.
Thrust washer thickness:
2.440 ± 2.490 mm (0.0961 ± 0.0980 in.)
18. REMOVE MAIN BEARING CAPS AND CHECK OIL
CLEARANCE
(a) Uniformly loosen and remove the 10 main bearing cap
bolts in several passes, in the sequence shown.
(b) Using 2 screwdrivers, pry out the main bearing cap, and
remove the 5 main bearing caps, 5 lower bearings and 2
lower thrust washers (No.3 main bearing cap only).
HINT:
Keep the lower bearing and main bearing cap together.
Arrange the main bearing caps and lower thrust washers
in the correct order.
(c) Lift out the crankshaft.
Page 3486 of 4770
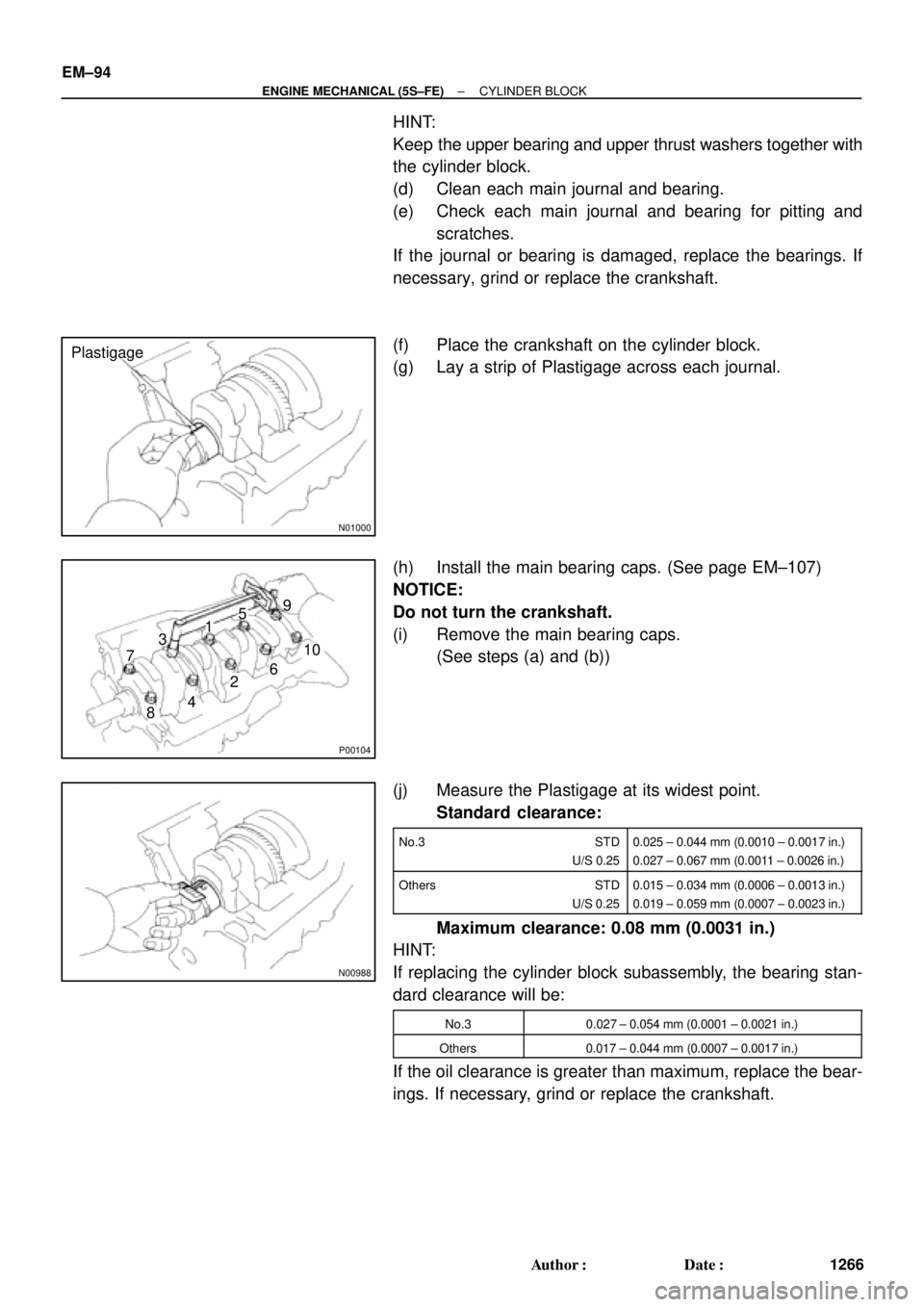
N01000
Plastigage
P00104
10 159
73
4
86
2
N00988
EM±94
± ENGINE MECHANICAL (5S±FE)CYLINDER BLOCK
1266 Author: Date:
HINT:
Keep the upper bearing and upper thrust washers together with
the cylinder block.
(d) Clean each main journal and bearing.
(e) Check each main journal and bearing for pitting and
scratches.
If the journal or bearing is damaged, replace the bearings. If
necessary, grind or replace the crankshaft.
(f) Place the crankshaft on the cylinder block.
(g) Lay a strip of Plastigage across each journal.
(h) Install the main bearing caps. (See page EM±107)
NOTICE:
Do not turn the crankshaft.
(i) Remove the main bearing caps.
(See steps (a) and (b))
(j) Measure the Plastigage at its widest point.
Standard clearance:
No.3 STD
U/S 0.250.025 ± 0.044 mm (0.0010 ± 0.0017 in.)
0.027 ± 0.067 mm (0.0011 ± 0.0026 in.)
Others STD
U/S 0.250.015 ± 0.034 mm (0.0006 ± 0.0013 in.)
0.019 ± 0.059 mm (0.0007 ± 0.0023 in.)
Maximum clearance: 0.08 mm (0.0031 in.)
HINT:
If replacing the cylinder block subassembly, the bearing stan-
dard clearance will be:
No.30.027 ± 0.054 mm (0.0001 ± 0.0021 in.)
Others0.017 ± 0.044 mm (0.0007 ± 0.0017 in.)
If the oil clearance is greater than maximum, replace the bear-
ings. If necessary, grind or replace the crankshaft.
Page 3487 of 4770
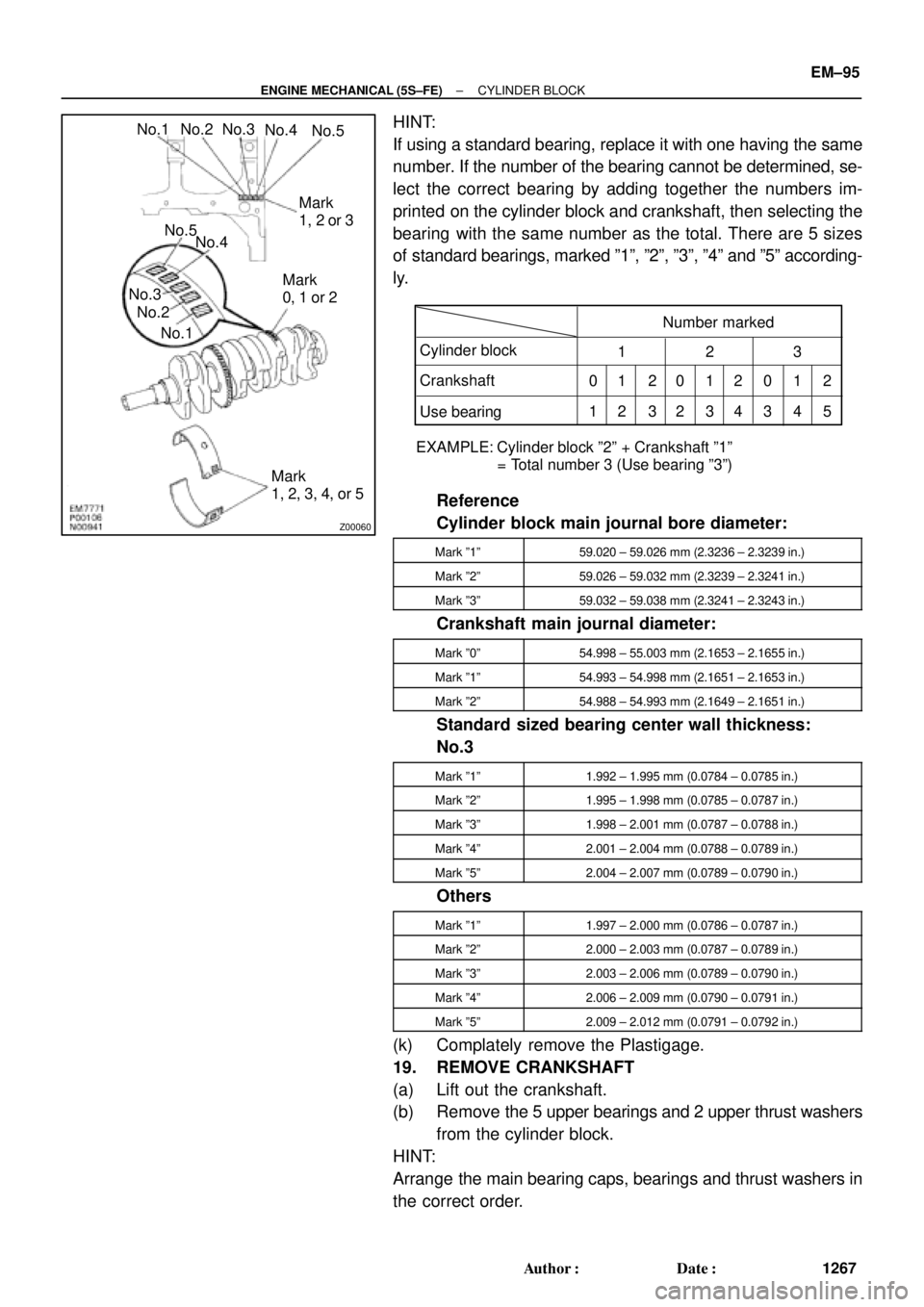
Z00060
No.1 No.2 No.3
No.4
No.5
No.1 No.2 No.3No.5
No.4Mark
1, 2 or 3
Mark
0, 1 or 2
Mark
1, 2, 3, 4, or 5
EXAMPLE: Cylinder block º2º + Crankshaft º1º
= Total number 3 (Use bearing º3º)
Number marked
Cylinder block
Crankshaft
Use bearing123
1
111 2
22
22
333445 000
± ENGINE MECHANICAL (5S±FE)CYLINDER BLOCK
EM±95
1267 Author: Date:
HINT:
If using a standard bearing, replace it with one having the same
number. If the number of the bearing cannot be determined, se-
lect the correct bearing by adding together the numbers im-
printed on the cylinder block and crankshaft, then selecting the
bearing with the same number as the total. There are 5 sizes
of standard bearings, marked º1º, º2º, º3º, º4º and º5º according-
ly.
Reference
Cylinder block main journal bore diameter:
Mark º1º59.020 ± 59.026 mm (2.3236 ± 2.3239 in.)
Mark º2º59.026 ± 59.032 mm (2.3239 ± 2.3241 in.)
Mark º3º59.032 ± 59.038 mm (2.3241 ± 2.3243 in.)
Crankshaft main journal diameter:
Mark º0º54.998 ± 55.003 mm (2.1653 ± 2.1655 in.)
Mark º1º54.993 ± 54.998 mm (2.1651 ± 2.1653 in.)
Mark º2º54.988 ± 54.993 mm (2.1649 ± 2.1651 in.)
Standard sized bearing center wall thickness:
No.3
Mark º1º1.992 ± 1.995 mm (0.0784 ± 0.0785 in.)
Mark º2º1.995 ± 1.998 mm (0.0785 ± 0.0787 in.)
Mark º3º1.998 ± 2.001 mm (0.0787 ± 0.0788 in.)
Mark º4º2.001 ± 2.004 mm (0.0788 ± 0.0789 in.)
Mark º5º2.004 ± 2.007 mm (0.0789 ± 0.0790 in.)
Others
Mark º1º1.997 ± 2.000 mm (0.0786 ± 0.0787 in.)
Mark º2º2.000 ± 2.003 mm (0.0787 ± 0.0789 in.)
Mark º3º2.003 ± 2.006 mm (0.0789 ± 0.0790 in.)
Mark º4º2.006 ± 2.009 mm (0.0790 ± 0.0791 in.)
Mark º5º2.009 ± 2.012 mm (0.0791 ± 0.0792 in.)
(k) Complately remove the Plastigage.
19. REMOVE CRANKSHAFT
(a) Lift out the crankshaft.
(b) Remove the 5 upper bearings and 2 upper thrust washers
from the cylinder block.
HINT:
Arrange the main bearing caps, bearings and thrust washers in
the correct order.
Page 3488 of 4770
A06590
A06589
A06587
A01774
A01775
EM±96
± ENGINE MECHANICAL (5S±FE)CYLINDER BLOCK
1268 Author: Date:
20. CHECK FIT BETWEEN PISTON AND PISTON PIN
Try to move the piston back and forth on the piston pin.
If any movement is felt, replace the piston and pin as a set.
21. REMOVE PISTON RINGS
(a) Using a piston ring expander, remove the No.1 and No.2
piston rings.
(b) Remove the 2 side rails and oil ring expander by hand.
HINT:
Arrange the piston rings in correct order only.
22. DISCONNECT CONNECTING ROD FROM PISTON
(a) Using a small screwdriver, pry out the 2 snap rings.
(b) Gradually heat the piston to 80 ± 90°C (176 ± 194°F).
(c) Using a plastic±faced hammer and brass bar, lightly tap
out the piston pin and remove the connecting rod.
HINT:
The piston and pin are a matched set.
Arrange the pistons, pins, rings, connecting rods and
bearings in the correct order.