Page 609 of 4770
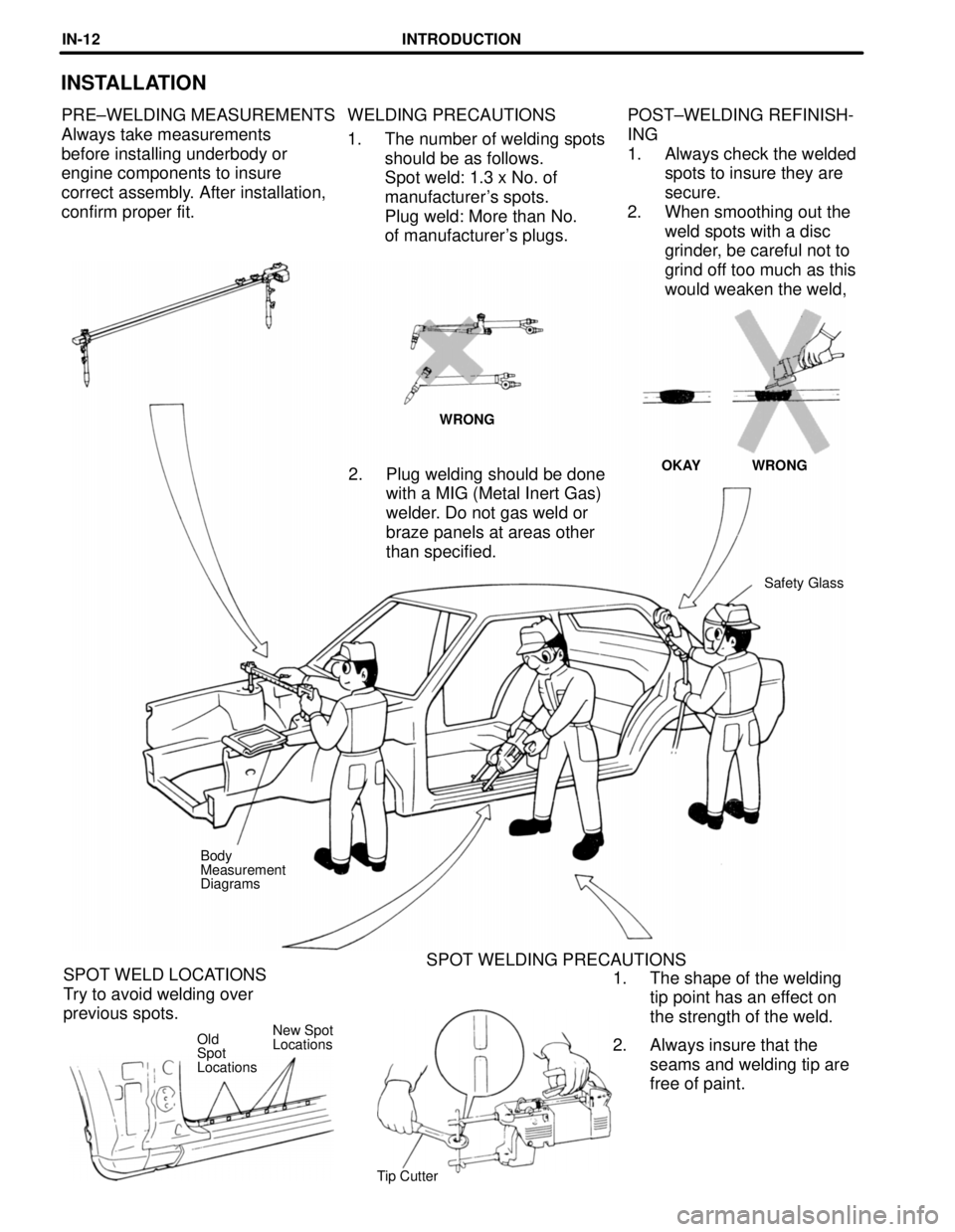
POST±WELDING REFINISH-
ING
1. Always check the welded
spots to insure they are
secure.
2. When smoothing out the
weld spots with a disc
grinder, be careful not to
grind off too much as this
would weaken the weld,
INSTALLATION
WELDING PRECAUTIONS
1. The number of welding spots
should be as follows.
Spot weld: 1.3 x No. of
manufacturer's spots.
Plug weld: More than No.
of manufacturer's plugs. PRE±WELDING MEASUREMENTS
Always take measurements
before installing underbody or
engine components to insure
correct assembly. After installation,
confirm proper fit.
WRONG
OKAYWRONG
2. Plug welding should be done
with a MIG (Metal Inert Gas)
welder. Do not gas weld or
braze panels at areas other
than specified.
Safety Glass
Body
Measurement
Diagrams
SPOT WELDING PRECAUTIONS
SPOT WELD LOCATIONS
Try to avoid welding over
previous spots.
Old
Spot
LocationsNew Spot
Locations
1. The shape of the welding
tip point has an effect on
the strength of the weld.
2. Always insure that the
seams and welding tip are
free of paint.
Tip Cutter
INTRODUCTIONIN-12
Page 610 of 4770
Tube Type
ANTI±RUST TREATMENT
When replacing body panels, always apply body sealer, anti±rust agent or undercoat according to the re-
quirements of your country.
HINT: For further details, see the description given in Section AR of this manual.
BODY SEALER
Apply body sealer to the
required areas.ANTI±RUST AGENT (WAX)
Cartridge Type
Apply anti±rust agent to
following sections.
Inside of the hems of the
doors and hood.
Around the hinges of the
doors and hood.
Inside of the welded parts
with boxed cross±section.
UNDERCOAT
Apply undercoat to the underbody and
wheel housings.
Spray Gun Undercoating
(Oil base)Undercoating
(Water base)
INTRODUCTIONIN-13
Page 611 of 4770
SUPPORT POSITIONPANTOGRAPH JACK POSITION
Front Front crossmember. . . . . . . .
Rear Rear axle beam. . . . . . . . .
CAUTION: Before jacking±up the rear and front, make sure the car is
not carrying any extra weight.
JACK POSITION
Front
Safety stand and swing arm type lift . . . . . . . . . . . . . . . . . . . . . . . . . . . .
VEHICLE LIFT AND SUPPORT LOCATIONS
INTRODUCTIONIN-14
Page 612 of 4770
200 mm (7.87 in.) 100 mm (3.94. in.)70 mm (2.76 in.) 85 mm (3.35 in.)
Attachment dimensionsAlign the cushion gum ends of the plate
with the attachment lower ends (A, C).
Align the attachment upper end (B) with
the front jack supporting point (). Front and rear set positionPlace the vehicle over the center of the lift. Left and right set position
HINT:
Attachment
PLATE TYPE LIFTINTRODUCTION
IN-15
Page 613 of 4770
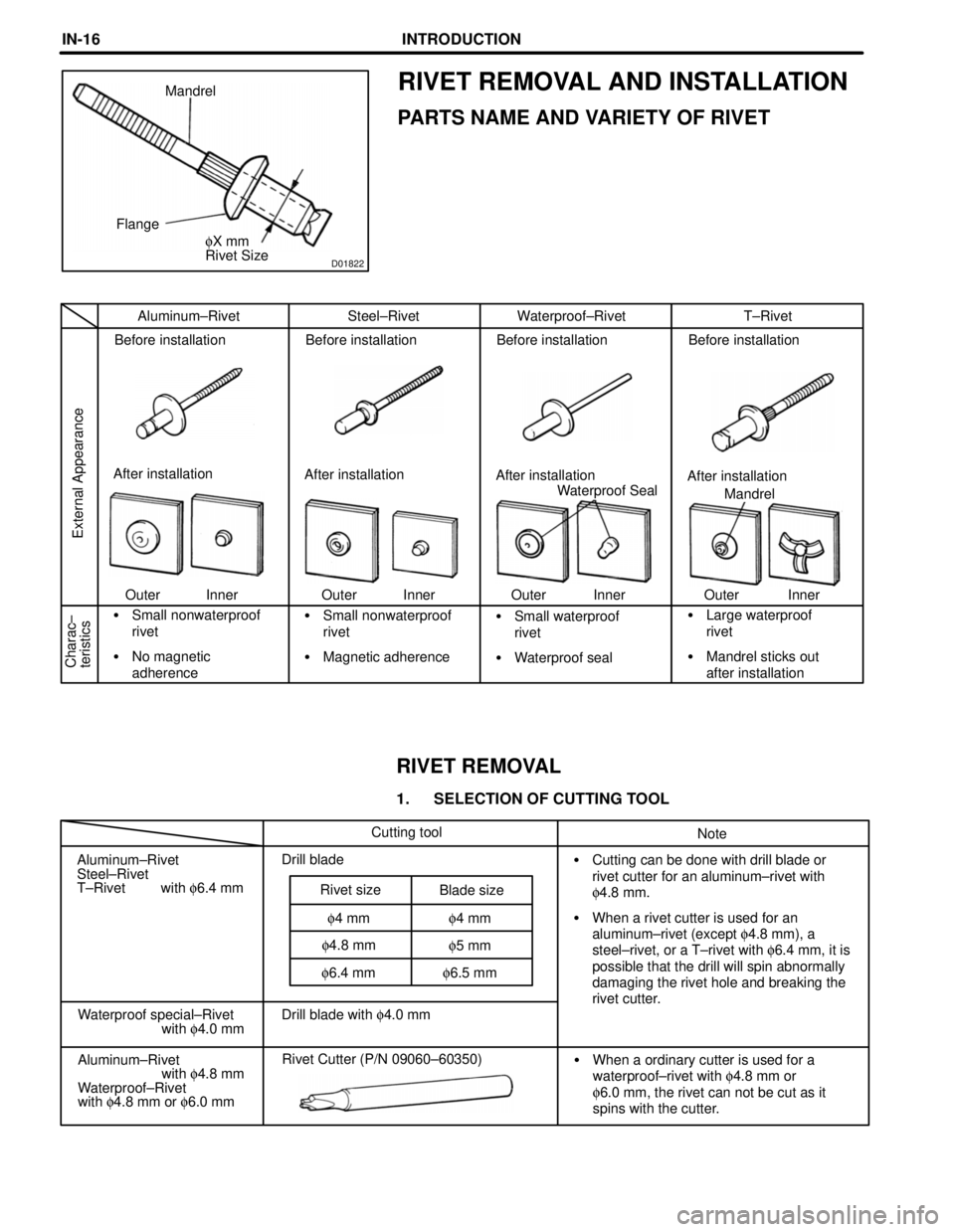
Rivet size
Blade size
f4 mmf4 mm
f4.8 mm
f5 mm
f6.4 mmf6.5 mm Cutting tool
Note
Aluminum±Rivet
Steel±Rivet
T±Rivet with f6.4 mmDrill blade
Cutting can be done with drill blade or
rivet cutter for an aluminum±rivet with
f4.8 mm.
When a rivet cutter is used for an
aluminum±rivet (except f4.8 mm), a
steel±rivet, or a T±rivet with f6.4 mm, it is
possible that the drill will spin abnormally
damaging the rivet hole and breaking the
rivet cutter.
Waterproof special±Rivet
with f4.0 mmDrill blade with f4.0 mm
Aluminum±Rivet
with f4.8 mm
Waterproof±Rivet
with f4.8 mm or f6.0 mmRivet Cutter (P/N 09060±60350)
When a ordinary cutter is used for a
waterproof±rivet with f4.8 mm or
f6.0 mm, the rivet can not be cut as it
spins with the cutter. Aluminum±Rivet Steel±Rivet Waterproof±Rivet T±Rivet
External Appearance
Inner Outer After installationBefore installation
Inner Outer After installationBefore installation
Inner Outer After installationBefore installation
Waterproof Seal
Inner Outer After installationBefore installation
Mandrel
Charac±
teristics
Small nonwaterproof
rivet
No magnetic
adherenceSmall nonwaterproof
rivet
Magnetic adherenceSmall waterproof
rivet
Waterproof sealLarge waterproof
rivet
Mandrel sticks out
after installation
D01822
fX mm
Rivet Size FlangeMandrel
RIVET REMOVAL AND INSTALLATION
PARTS NAME AND VARIETY OF RIVET
RIVET REMOVAL
1. SELECTION OF CUTTING TOOL
INTRODUCTIONIN-16
Page 614 of 4770
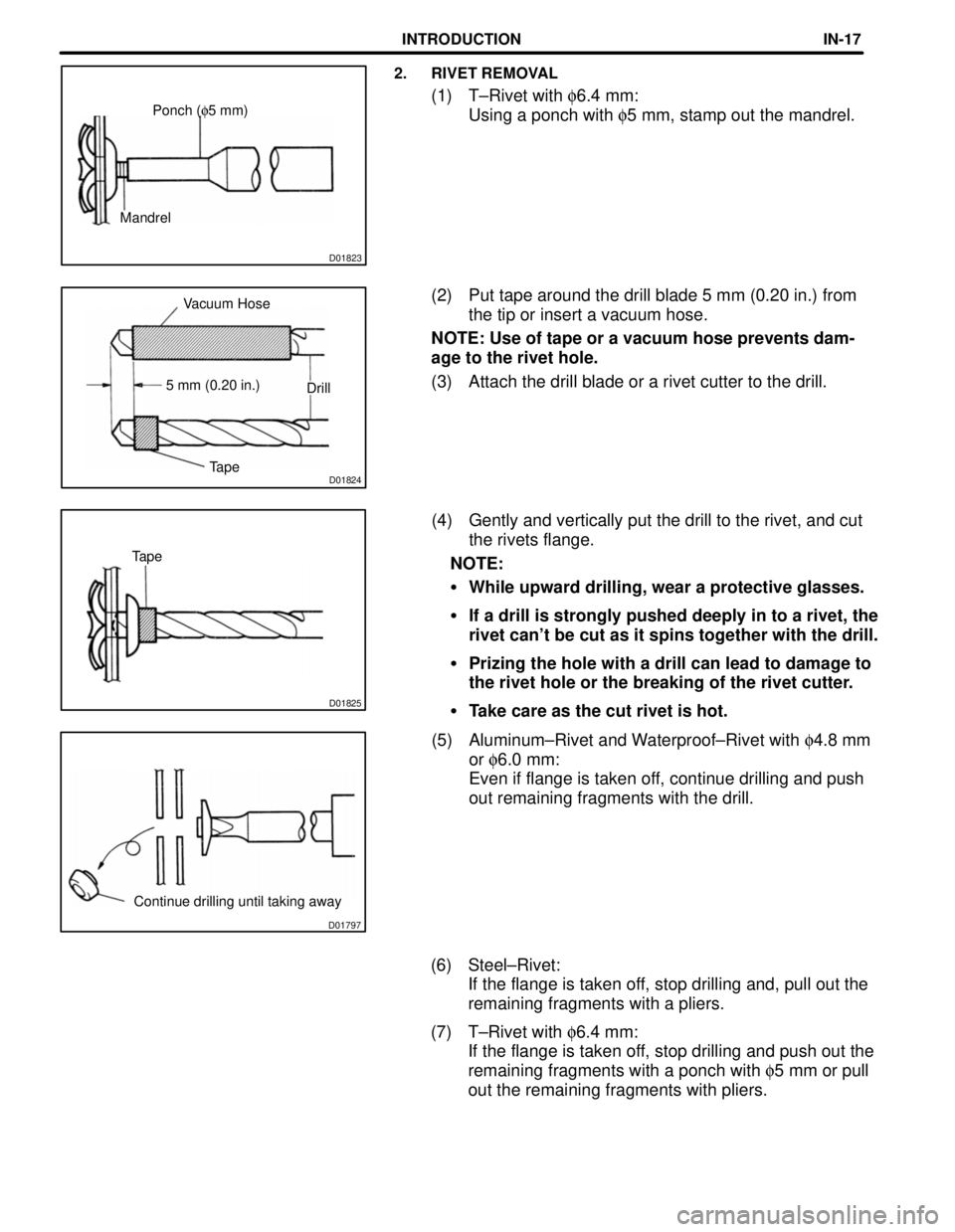
D01797
Continue drilling until taking away
D01825
Tape
D01824TapeDrill 5 mm (0.20 in.)Vacuum Hose
D01823
MandrelPonch (f5 mm)
2. RIVET REMOVAL
(1) T±Rivet with f6.4 mm:
Using a ponch with f5 mm, stamp out the mandrel.
(2) Put tape around the drill blade 5 mm (0.20 in.) from
the tip or insert a vacuum hose.
NOTE: Use of tape or a vacuum hose prevents dam-
age to the rivet hole.
(3) Attach the drill blade or a rivet cutter to the drill.
(4) Gently and vertically put the drill to the rivet, and cut
the rivets flange.
NOTE:
While upward drilling, wear a protective glasses.
If a drill is strongly pushed deeply in to a rivet, the
rivet can't be cut as it spins together with the drill.
Prizing the hole with a drill can lead to damage to
the rivet hole or the breaking of the rivet cutter.
Take care as the cut rivet is hot.
(5) Aluminum±Rivet and Waterproof±Rivet with f4.8 mm
or f6.0 mm:
Even if flange is taken off, continue drilling and push
out remaining fragments with the drill.
(6) Steel±Rivet:
If the flange is taken off, stop drilling and, pull out the
remaining fragments with a pliers.
(7) T±Rivet with f6.4 mm:
If the flange is taken off, stop drilling and push out the
remaining fragments with a ponch with f5 mm or pull
out the remaining fragments with pliers.
INTRODUCTIONIN-17
Page 615 of 4770
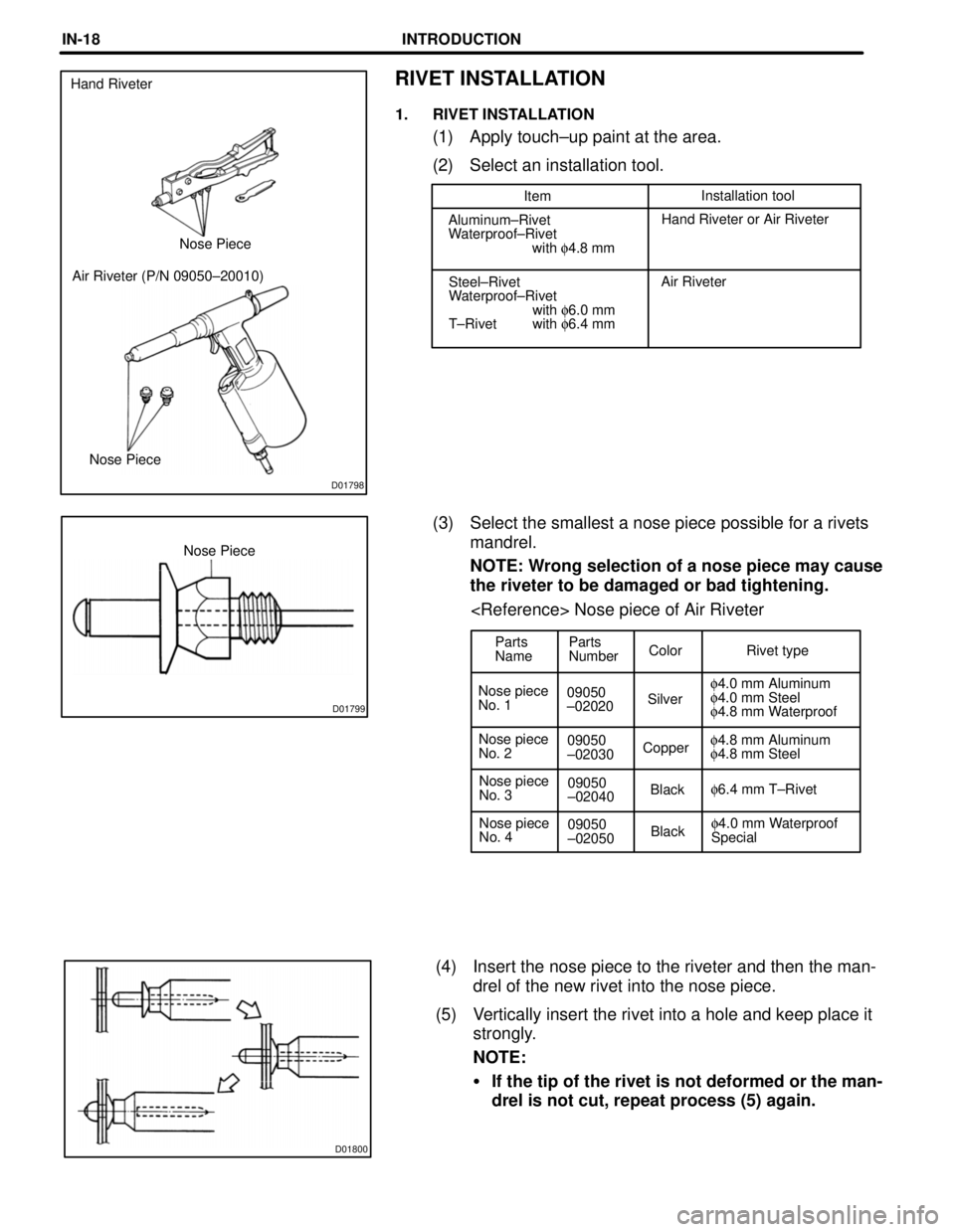
D01800 D01799
Nose Piece
Parts
NameParts
NumberColorRivet type
Nose piece
No. 109050
±02020Silverf4.0 mm Aluminum
f4.0 mm Steel
f4.8 mm Waterproof
Nose piece
No. 209050
±02030Copperf4.8 mm Aluminum
f4.8 mm Steel
Nose piece
No. 309050
±02040Blackf6.4 mm T±Rivet
Nose piece
No. 409050
±02050Blackf4.0 mm Waterproof
Special
D01798
Nose Piece Air Riveter (P/N 09050±20010)Nose Piece Hand Riveter
ItemInstallation tool
Aluminum±Rivet
Waterproof±Rivet
with f4.8 mmHand Riveter or Air Riveter
Steel±Rivet
Waterproof±Rivet
with f6.0 mm
T±Rivet with f6.4 mmAir Riveter
Nose piece of Air Riveter
1. RIVET INSTALLATION
(1) Apply touch±up paint at the area.
(2) Select an installation tool.
RIVET INSTALLATION
(3) Select the smallest a nose piece possible for a rivets
mandrel.
NOTE: Wrong selection of a nose piece may cause
the riveter to be damaged or bad tightening.
(4) Insert the nose piece to the riveter and then the man-
drel of the new rivet into the nose piece.
(5) Vertically insert the rivet into a hole and keep place it
strongly.
NOTE:
If the tip of the rivet is not deformed or the man-
drel is not cut, repeat process (5) again.
INTRODUCTIONIN-18
Page 616 of 4770
D01805
Mandrel
D01804
Riveter
D01803
Riveter Riveter
D01802Mandrel Riveter
D0180120 mm
(0.79 in.)20 mm
(0.79 in.) Riveter
T±Rivet with 6.4 mm:
Do not place your hands or the wire harness
within a radius of 20 mm (0.70 in.) from the riv-
et, as the rivet is cut and opened in this area.
Prizing a riveter damages the riveter showing
that it is not tightened correctly and bends the
mandrel.
Loose tightening may result from either tilting
the riveter while handling or the riveter not con-
necting to the material.
Loose tightening also occurs when a rivet is
applied between materials without touching.
T±Rivet with 6.4 mm:
When a mandrel of a rivet is lost, the rivet
should be replaced to prevent loose tightening.
INTRODUCTIONIN-19