Page 145 of 4770
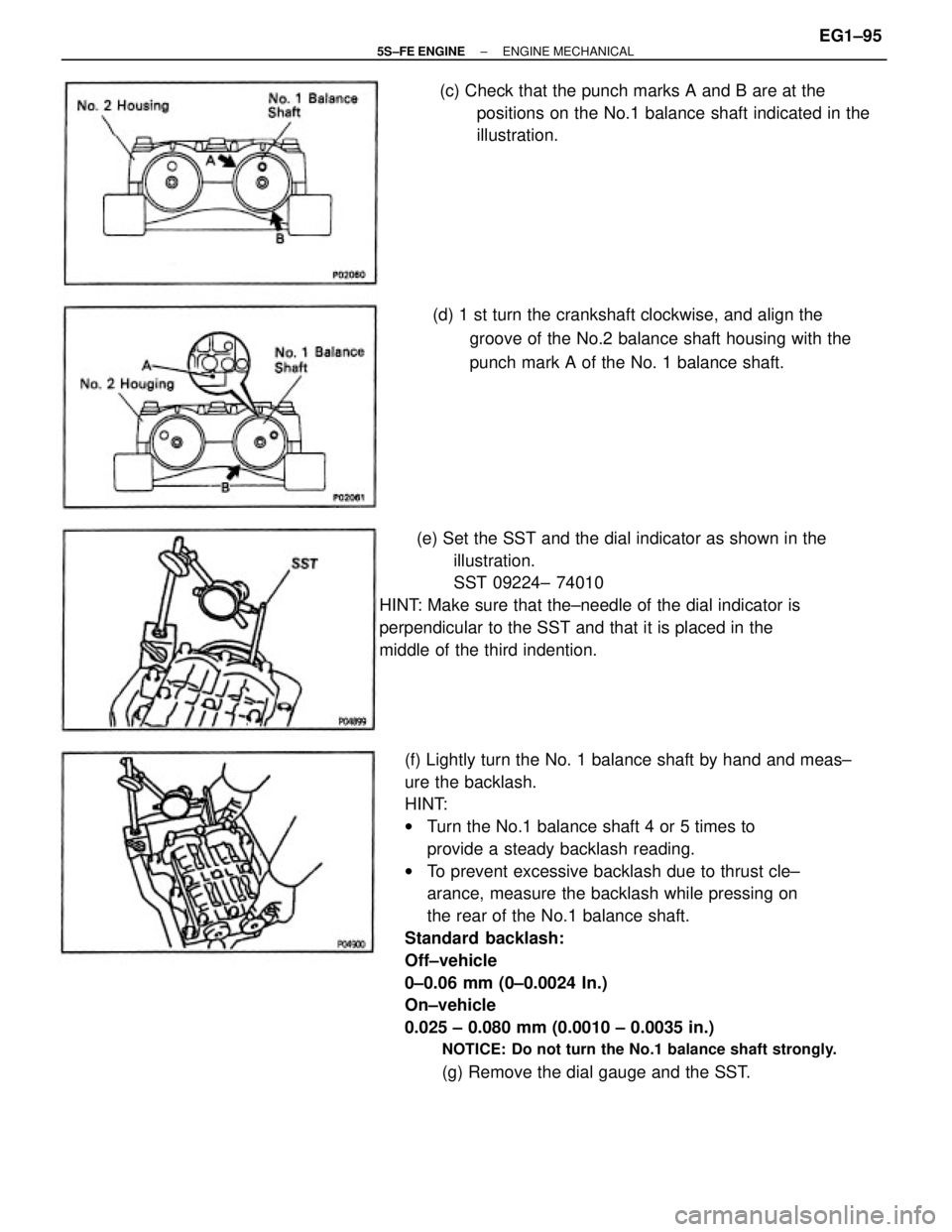
(f) Lightly turn the No. 1 balance shaft by hand and meas±
ure the backlash.
HINT:
wTurn the No.1 balance shaft 4 or 5 times to
provide a steady backlash reading.
wTo prevent excessive backlash due to thrust cle±
arance, measure the backlash while pressing on
the rear of the No.1 balance shaft.
Standard backlash:
Off±vehicle
0±0.06 mm (0±0.0024 In.)
On±vehicle
0.025 ± 0.080 mm (0.0010 ± 0.0035 in.)
NOTICE: Do not turn the No.1 balance shaft strongly.
(g) Remove the dial gauge and the SST. (e) Set the SST and the dial indicator as shown in the
illustration.
SST 09224± 74010
HINT: Make sure that the±needle of the dial indicator is
perpendicular to the SST and that it is placed in the
middle of the third indention.(d) 1 st turn the crankshaft clockwise, and align the
groove of the No.2 balance shaft housing with the
punch mark A of the No. 1 balance shaft. (c) Check that the punch marks A and B are at the
positions on the No.1 balance shaft indicated in the
illustration.
± 5S±FE ENGINEENGINE MECHANICALEG1±95
Page 146 of 4770
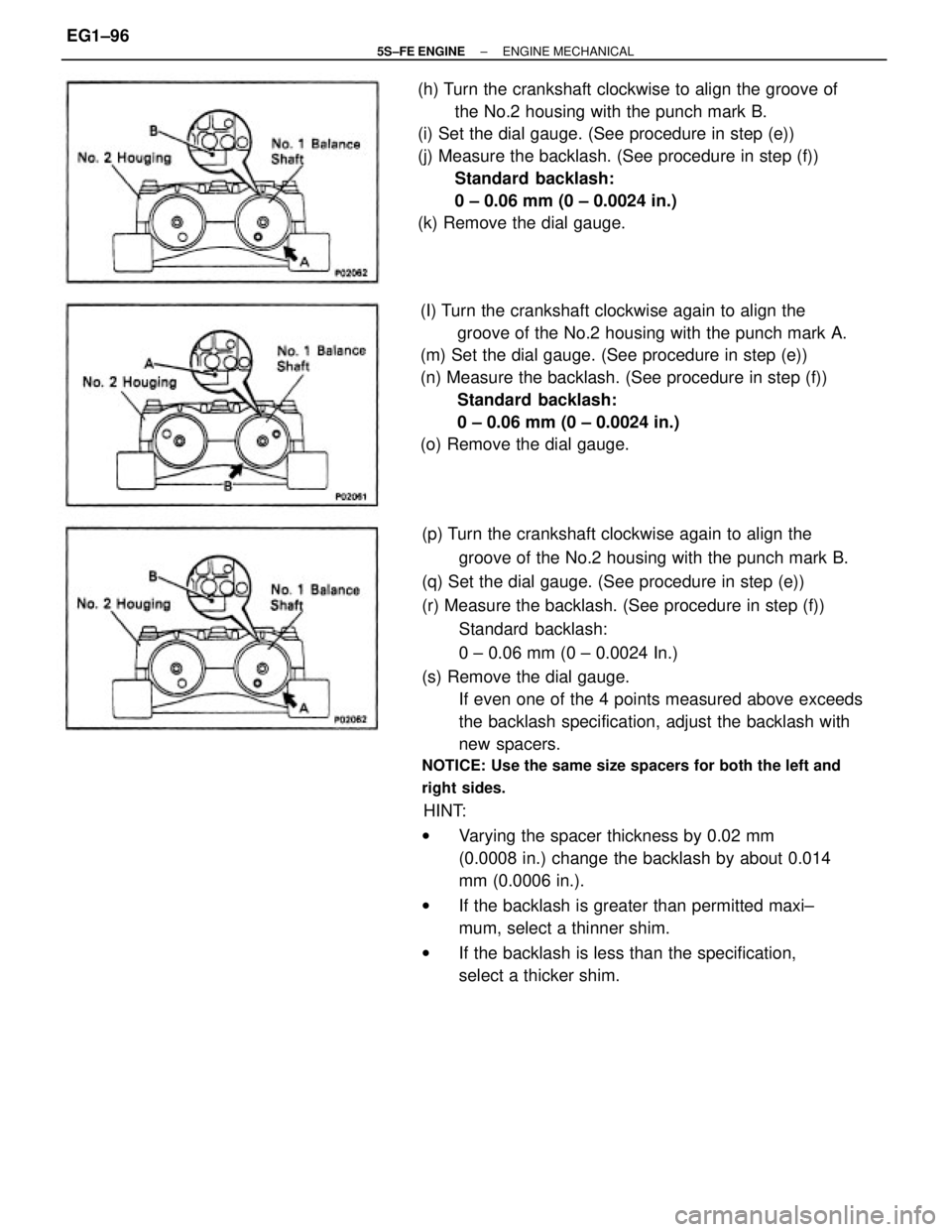
(p) Turn the crankshaft clockwise again to align the
groove of the No.2 housing with the punch mark B.
(q) Set the dial gauge. (See procedure in step (e))
(r) Measure the backlash. (See procedure in step (f))
Standard backlash:
0 ± 0.06 mm (0 ± 0.0024 In.)
(s) Remove the dial gauge.
If even one of the 4 points measured above exceeds
the backlash specification, adjust the backlash with
new spacers.
NOTICE: Use the same size spacers for both the left and
right sides.
HINT:
wVarying the spacer thickness by 0.02 mm
(0.0008 in.) change the backlash by about 0.014
mm (0.0006 in.).
wIf the backlash is greater than permitted maxi±
mum, select a thinner shim.
wIf the backlash is less than the specification,
select a thicker shim. (I) Turn the crankshaft clockwise again to align the
groove of the No.2 housing with the punch mark A.
(m) Set the dial gauge. (See procedure in step (e))
(n) Measure the backlash. (See procedure in step (f))
Standard backlash:
0 ± 0.06 mm (0 ± 0.0024 in.)
(o) Remove the dial gauge. (h) Turn the crankshaft clockwise to align the groove of
the No.2 housing with the punch mark B.
(i) Set the dial gauge. (See procedure in step (e))
(j) Measure the backlash. (See procedure in step (f))
Standard backlash:
0 ± 0.06 mm (0 ± 0.0024 in.)
(k) Remove the dial gauge.
± 5S±FE ENGINEENGINE MECHANICALEG1±96
Page 147 of 4770
± 5S±FE ENGINEENGINE MECHANICALEG1±97
Page 148 of 4770
5. CHECK CONNECTING ROD THRUST CLEARANCE
Using a dial indicator, measure the thrust clearance
while moving the connecting rod back and forth.
Standard thrust clearance:
0.160 ± 0.312 mm (0.0063 ± 0.0123 in.)
Maximum thrust clearance:
0.36 mm (0.0138 in.)
If the thrust clearance is greater than maximum, re±
place the connecting rod assembly. If necessary, re±
place the crankshaft.
6. REMOVE CONNECTING ROD CAPS AND CHECK
OIL CLEARANCE
(a) Check the matchmarks on the connecting rod and cap
to ensure correct reassembly.
(c) Using a plastic±faced hammer, lightly tap the con±
necting rod bolts and lift off the connecting rod cap.
HINT: Keep the lower bearing inserted with the con±
necting rod cap.4. REMOVE ENGINE BALANCER
(a) Uniformly loosen and remove the 6 bolts in several
passes, in the sequence shown.
(b) Remove the engine balancer and spacers.
(b) Using SST, remove the connecting rod cap nuts.
SST 09011±38121
± 5S±FE ENGINEENGINE MECHANICALEG1±98
Page 149 of 4770
(e) Clean the crank pin and bearing.
(f) Check the crank pin and bearing for pitting and scrat±
ches.
If the crank pin or bearing is damaged, replace the
bearings. If necessary, grind or replace the crankshaft.
(h) Install the connecting rod cap.
(See step 6 on pages EG1±122)
1st
Torque: 25 N±m (250 kgf±cm, 18 ft±lbf)
2nd Turn 905
NOTICE: Do not turn the crankshaft.
(d) Cover the connecting rod bolts with a short piece of
hose to protect the crankshaft from damage.
(i) Remove the connecting rod cap.
(See procedure (b) and (c) on the previous page) (g) Lay a strip of Plastigage across the crank pin.
± 5S±FE ENGINEENGINE MECHANICALEG1±99
Page 150 of 4770
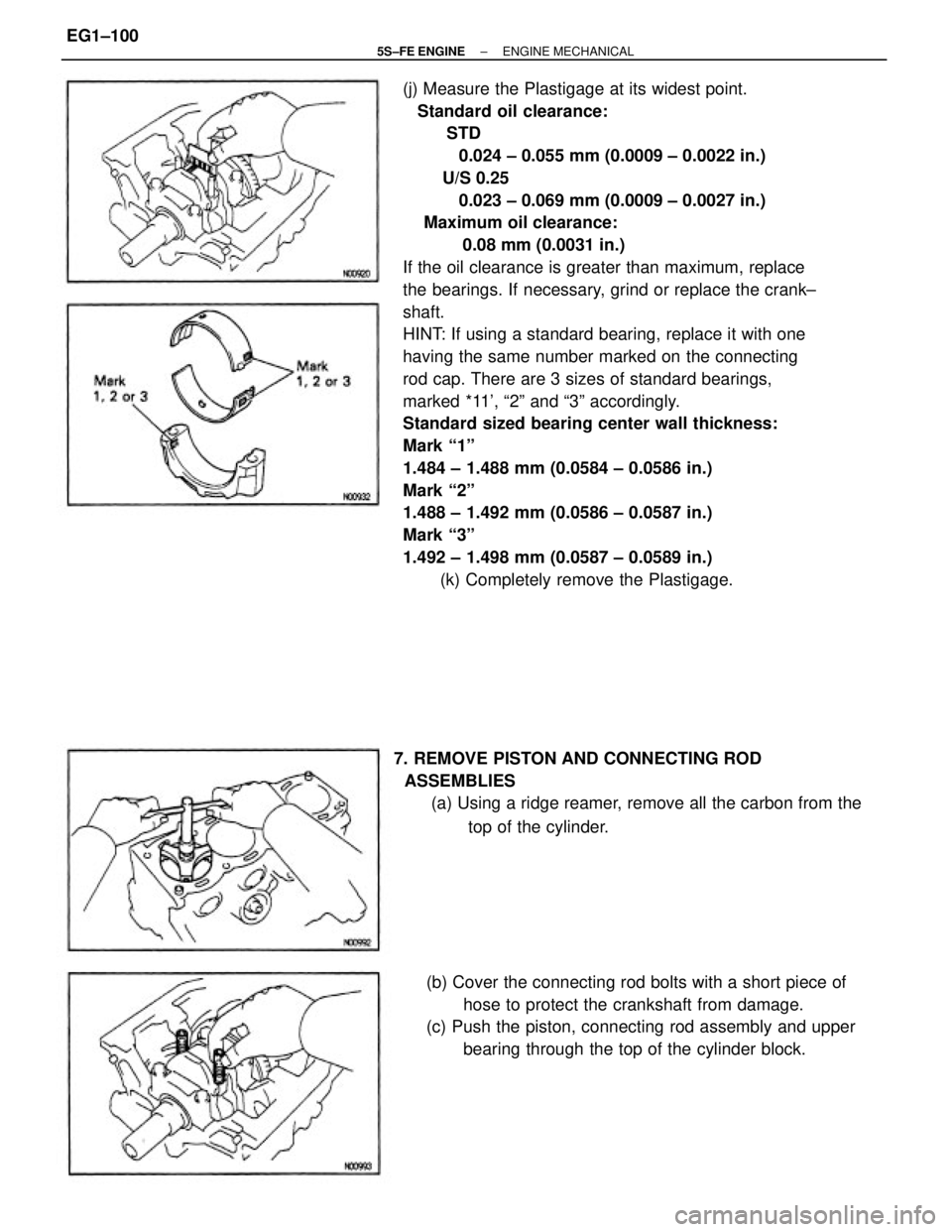
(j) Measure the Plastigage at its widest point.
Standard oil clearance:
STD
0.024 ± 0.055 mm (0.0009 ± 0.0022 in.)
U/S 0.25
0.023 ± 0.069 mm (0.0009 ± 0.0027 in.)
Maximum oil clearance:
0.08 mm (0.0031 in.)
If the oil clearance is greater than maximum, replace
the bearings. If necessary, grind or replace the crank±
shaft.
HINT: If using a standard bearing, replace it with one
having the same number marked on the connecting
rod cap. There are 3 sizes of standard bearings,
marked *11', ª2º and ª3º accordingly.
Standard sized bearing center wall thickness:
Mark ª1º
1.484 ± 1.488 mm (0.0584 ± 0.0586 in.)
Mark ª2º
1.488 ± 1.492 mm (0.0586 ± 0.0587 in.)
Mark ª3º
1.492 ± 1.498 mm (0.0587 ± 0.0589 in.)
(k) Completely remove the Plastigage.
(b) Cover the connecting rod bolts with a short piece of
hose to protect the crankshaft from damage.
(c) Push the piston, connecting rod assembly and upper
bearing through the top of the cylinder block. 7. REMOVE PISTON AND CONNECTING ROD
ASSEMBLIES
(a) Using a ridge reamer, remove all the carbon from the
top of the cylinder.
± 5S±FE ENGINEENGINE MECHANICALEG1±100
Page 151 of 4770
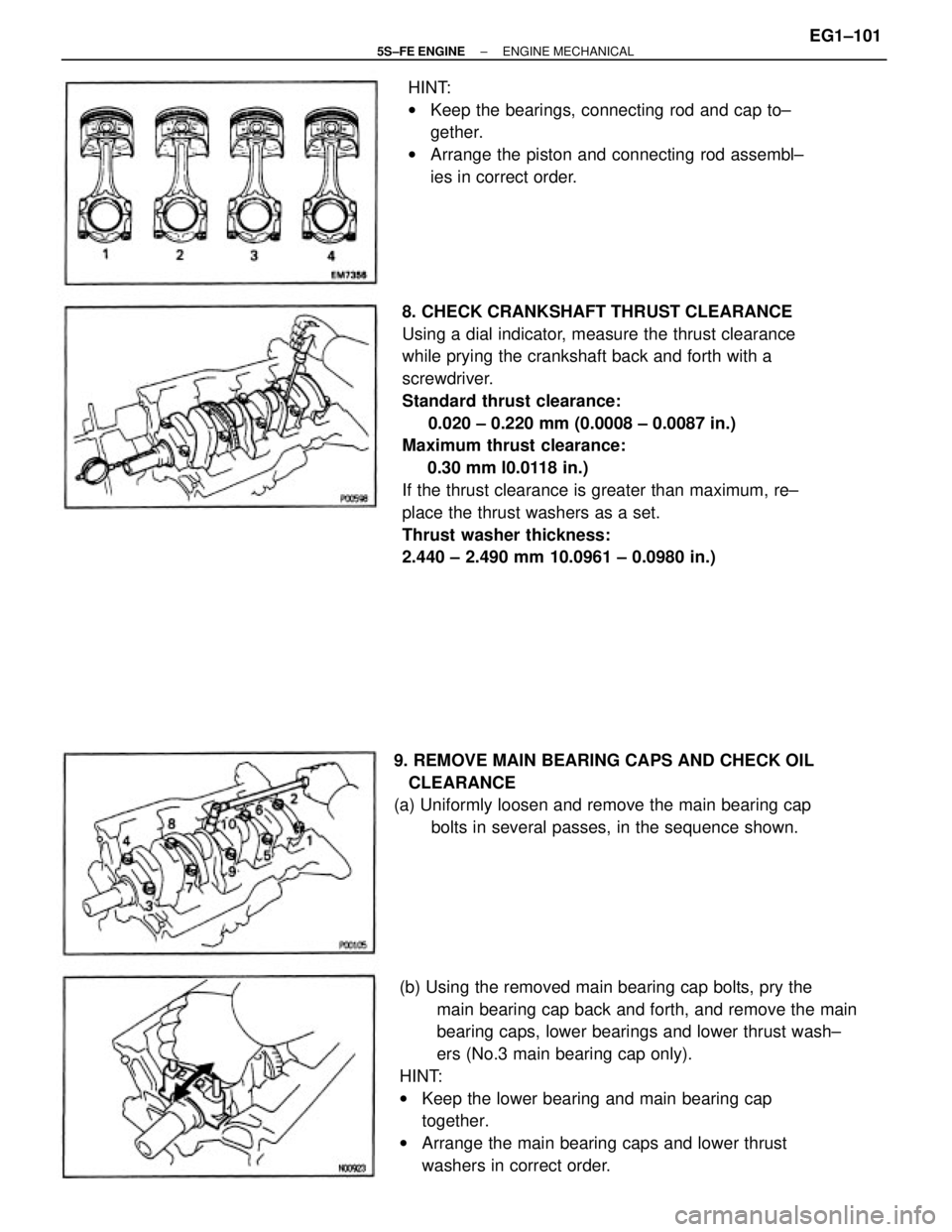
8. CHECK CRANKSHAFT THRUST CLEARANCE
Using a dial indicator, measure the thrust clearance
while prying the crankshaft back and forth with a
screwdriver.
Standard thrust clearance:
0.020 ± 0.220 mm (0.0008 ± 0.0087 in.)
Maximum thrust clearance:
0.30 mm l0.0118 in.)
If the thrust clearance is greater than maximum, re±
place the thrust washers as a set.
Thrust washer thickness:
2.440 ± 2.490 mm 10.0961 ± 0.0980 in.)
(b) Using the removed main bearing cap bolts, pry the
main bearing cap back and forth, and remove the main
bearing caps, lower bearings and lower thrust wash±
ers (No.3 main bearing cap only).
HINT:
wKeep the lower bearing and main bearing cap
together.
wArrange the main bearing caps and lower thrust
washers in correct order. HINT:
wKeep the bearings, connecting rod and cap to±
gether.
wArrange the piston and connecting rod assembl±
ies in correct order.
9. REMOVE MAIN BEARING CAPS AND CHECK OIL
CLEARANCE
(a) Uniformly loosen and remove the main bearing cap
bolts in several passes, in the sequence shown.
± 5S±FE ENGINEENGINE MECHANICALEG1±101
Page 152 of 4770
(d) Clean each main journal and bearing.
(e) Check each main journal and bearing for pitting and
scratches.
If the journal or bearing is damaged, replace the bear±
ings. If necessary, grind or replace the crankshaft. (c) Lift out the crankshaft.
HINT: Keep the upper bearing and upper thrust wash±
ers together with the cylinder block.
(h) Install the main bearing caps.
(See step 4 on page EG1±121)
Torque: 59 N±m (600 kgf±cm, 43 ft±lbf)
NOTICE: Do not turn the crankshaft.
(i) Remove the main bearing caps.
(See procedure (a) and (b) on the previous page) (f) Place the crankshaft on the cylinder block.
(g) Lay a strip of Plastigage across each journal.
± 5S±FE ENGINEENGINE MECHANICALEG1±102