Page 3473 of 4770
± ENGINE MECHANICAL (5S±FE)ENGINE UNIT
EM±81
1253 Author: Date:
38. INSTALL AIR CLEANER CAP
(a) Connect the air cleaner hose to the throttle body.
(b) Attach the air cleaner cap to the air cleaner case, and
install the 2 clamps.
(c) Tighten the air cleaner hose clamp.
(d) Connect the PCV hose to the cylinder head cover.
(e) Connect the EVAP hose to the throttle body.
(f) Connect the EVAP hose to the VSV.
(g) Connect the IAT sensor connector.
(h) Connect the VSV connector for the EVAP.
39. CONNECT ACCELERATOR CABLE
40. INSTALL ENGINE FENDER APRON SEALS
41. INSTALL HOOD
42. FILL ENGINE WITH OIL
43. FILL WITH ENGINE COOLANT
44. START ENGINE AND CHECK FOR LEAKS
45. RECHECK ENGINE COOLANT AND OIL LEVELS
Page 3474 of 4770
EM08H±03
A07366
No.2 Timing Belt
Cover
No.1 Timing Belt
Cover
Crankshaft
Pulley
No.2 Idler PulleyTension Spring* Gasket
Timing Belt Guide Timing Belt
High±Tension Cord
Spark Plug
N´m (kgf´cm, ft´lbf)Wire
ClampGenerator
Wire Clamp
Crankshaft Timing Pulley
Camshaft Timing Pulley
No.1 Idler PulleyWire ClampWire Clamp
108 (1,100, 80)
54 (550, 40)
42 (425, 31)
18 (180, 13)
42 (425, 31)
: Specified torque* Gasket
* Replace only if damaged
EM±82
± ENGINE MECHANICAL (5S±FE)CYLINDER BLOCK
1254 Author: Date:
CYLINDER BLOCK
COMPONENTS
Page 3475 of 4770
A07354
Grommet
Cylinder Head
Cover
Gasket
Camshaft Oil Seal
Cylinder Head Assembly
No.3 Timing Belt Cover
Crankshaft Position Sensor
ConnectorWire Clamp Water Bypass Hose Exhaust Camshaft Intake Camshaft
Camshaft Bearing Cap PCV Hose
Cylinder Head Gasket
IAC Valve Water Bypass Hose
Knock Sensor 1 Connector
N´m (kgf´cm, ft´lbf)
Non±reusable part
44 (450, 33)
19 (190, 14)
VSV for EGR
: Specified torquex 10
1st 49 (500, 36)
2nd Turn 90° See page EM±53
± ENGINE MECHANICAL (5S±FE)CYLINDER BLOCK
EM±83
1255 Author: Date:
Page 3476 of 4770
A07367
Water Pump, Water Bypass Pipe
and Oil Cooler Assembly
Water Pump and Water
Bypass Pipe Assembly
(w/o Oil Cooler)
Union Bolt
Generator Drive Belt Adjusting Bar
Knock Sensor 1Oil Filter
Oil Dipstick
PS Pump
Bracket
Crankshaft Position Sensor Connector
Oil Pump
Gasket x 10
Oil Strainer
Oil Pan
Drain Plug
N´m (kgf´cm, ft´lbf)
Non±reusable partx 17 Gasket
Gasket O±Ring
8.8 (90, 78 in.´lbf)5.4 (55, 48 in.´lbf)
5.4 (55, 48 in.´lbf)
O±Ring
78.5 (800, 58)
w/ Oil Cooler
: Specified torque
Crankshaft
Front Oil
Seal
EM±84
± ENGINE MECHANICAL (5S±FE)CYLINDER BLOCK
1256 Author: Date:
Page 3477 of 4770
A07353
No.1 Piston Ring
No.2 Piston Ring
Oil Ring (Side Rail)
Snap Ring
Connecting Rod
Connecting Rod Bearing
Connecting Rod Cap
Cylinder Block
Upper Crankshaft
Thrust Washer
Crankshaft
Lower Crankshaft
Thrust Washer
Adjusting Spacer
Engine Balancerx 6
Main Bearing CapLower Main Bearing Upper Main Bearing Gasket Rear Oil Seal
Retainer
Crankshaft
Rear Oil
Seal Connecting Rod BushingPiston Pin Snap Ring Oil Ring (Expander)
Non±reusable part
N´m (kgf´cm, ft´lbf)x 6 Piston
1st 25 (250, 18)
2nd Turn 90°
59 (600, 43)
49 (500, 36): Specified torque
See page EM±107
± ENGINE MECHANICAL (5S±FE)CYLINDER BLOCK
EM±85
1257 Author: Date:
Page 3478 of 4770

EM0YW±01
S06011
1
3
2 EM±86
± ENGINE MECHANICAL (5S±FE)CYLINDER BLOCK
1258 Author: Date:
DISASSEMBLY
1. INSTALL ENGINE TO ENGINE STAND FOR DIS-
ASSEMBLY
2. REMOVE TIMING BELT AND PULLEYS
(See page EM±17)
3. REMOVE CYLINDER HEAD ASSEMBLY
(a) Remove the 3 bolts and No.3 timing belt cover.
(b) Remove the cylinder head cover.
(1) Disconnect the PCV hose from the intake manifold.
(2) Remove the 4 nuts, 4 grommets, head cover and
gasket.
(c) Remove the camshafts. (See page EM±33)
(d) Disconnect the knock sensor 1 connector.
(e) Disconnect the crankshaft position sensor connector.
(f) Disconnect the wire clamp from the generator drive belt
adjusting bar.
(g) Disconnect the IAC valve water bypass hose from the wa-
ter bypass pipe.
(h) Disconnect the water bypass hose (from the water by-
pass pipe) from the water outlet.
(i) Remove the bolt holding the VSV for EGR to the intake
manifold.
(j) Remove the 2 bolts holding the water bypass pipe to the
cylinder head.
(k) Remove the cylinder head assembly.
(See page EM±33)
4. REMOVE OIL DIPSTICK
5. REMOVE OIL PAN AND OIL PUMP
(a) Disconnect the crankshaft position sensor connector
from the generator drive belt adjusting bar.
(b) Remove the oil pan and oil pump. (See page LU±7)
6. REMOVE PS PUMP BRACKET
Remove the 3 bolts and pump bracket.
7. REMOVE KNOCK SENSOR 1 (See page SF±57)
8. REMOVE OIL FILTER (See page LU±2)
9. REMOVE WATER PUMP, WATER BYPASS PIPE AND
OIL COOLER (w/ OIL COOLER) ASSEMBLY
(a) w/ Oil Cooler:
Remove the nut and union bolt, and disconnect the oil
cooler. Remove the O±ring.
(b) Remove the bolt and generator drive belt adjusting bar.
(c) Remove the 3 bolts in the sequence shown, remove the
water pump, water bypass pipe, oil cooler (w/ oil cooler)
assembly and O±ring.
Page 3479 of 4770
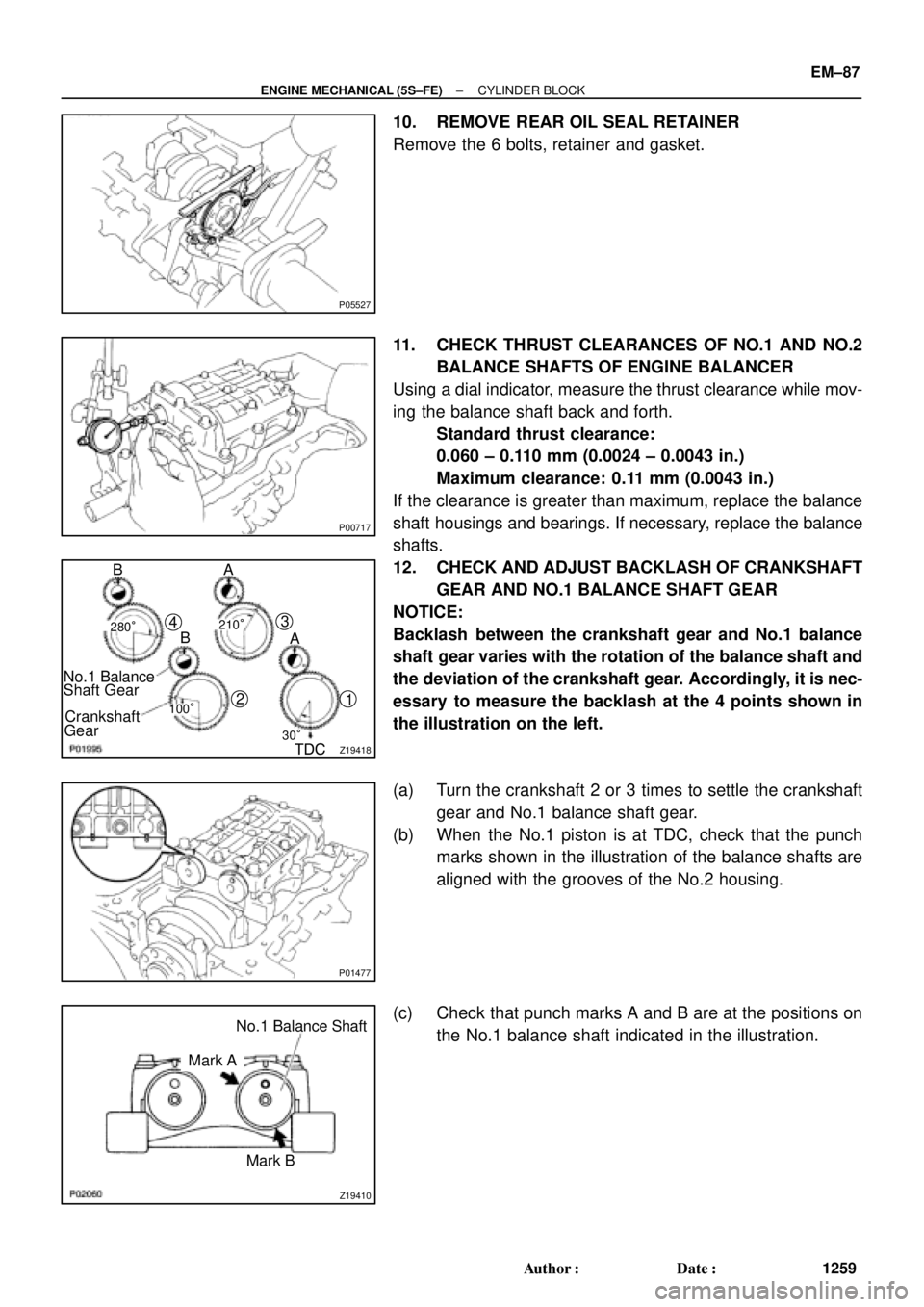
P05527
P00717
Z19418
No.1 Balance
CrankshaftA
A B B
1 23
4
30°TDC
Shaft Gear
Gear
210°
280°
100°
P01477
Z19410
No.1 Balance Shaft
Mark A
Mark B
± ENGINE MECHANICAL (5S±FE)CYLINDER BLOCK
EM±87
1259 Author: Date:
10. REMOVE REAR OIL SEAL RETAINER
Remove the 6 bolts, retainer and gasket.
11. CHECK THRUST CLEARANCES OF NO.1 AND NO.2
BALANCE SHAFTS OF ENGINE BALANCER
Using a dial indicator, measure the thrust clearance while mov-
ing the balance shaft back and forth.
Standard thrust clearance:
0.060 ± 0.110 mm (0.0024 ± 0.0043 in.)
Maximum clearance: 0.11 mm (0.0043 in.)
If the clearance is greater than maximum, replace the balance
shaft housings and bearings. If necessary, replace the balance
shafts.
12. CHECK AND ADJUST BACKLASH OF CRANKSHAFT
GEAR AND NO.1 BALANCE SHAFT GEAR
NOTICE:
Backlash between the crankshaft gear and No.1 balance
shaft gear varies with the rotation of the balance shaft and
the deviation of the crankshaft gear. Accordingly, it is nec-
essary to measure the backlash at the 4 points shown in
the illustration on the left.
(a) Turn the crankshaft 2 or 3 times to settle the crankshaft
gear and No.1 balance shaft gear.
(b) When the No.1 piston is at TDC, check that the punch
marks shown in the illustration of the balance shafts are
aligned with the grooves of the No.2 housing.
(c) Check that punch marks A and B are at the positions on
the No.1 balance shaft indicated in the illustration.
Page 3480 of 4770
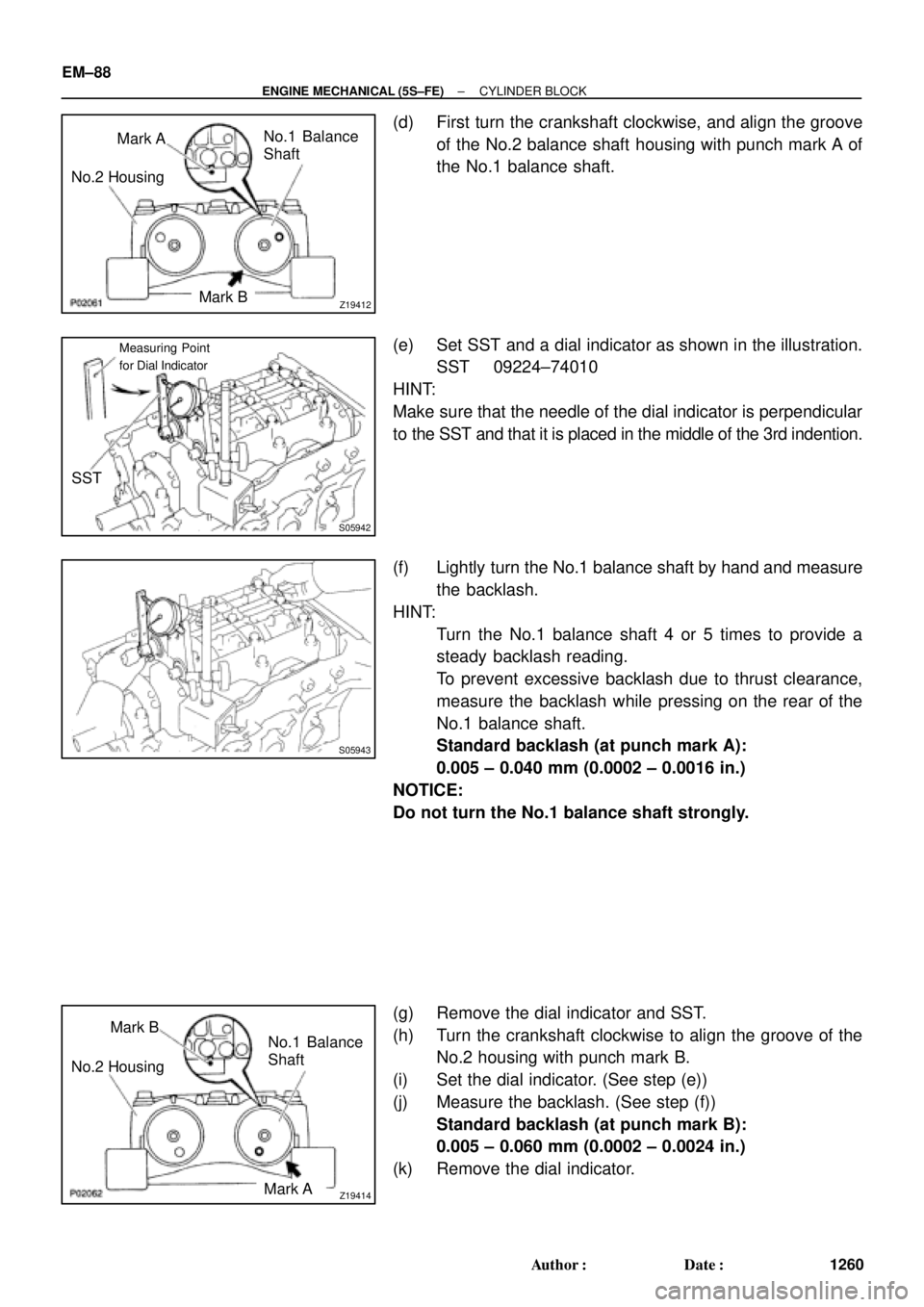
Z19412
No.1 Balance
Shaft Mark A
Mark B No.2 Housing
S05942
Measuring Point
for Dial Indicator
SST
S05943
Z19414
No.1 Balance
Shaft
Mark A Mark B
No.2 Housing EM±88
± ENGINE MECHANICAL (5S±FE)CYLINDER BLOCK
1260 Author: Date:
(d) First turn the crankshaft clockwise, and align the groove
of the No.2 balance shaft housing with punch mark A of
the No.1 balance shaft.
(e) Set SST and a dial indicator as shown in the illustration.
SST 09224±74010
HINT:
Make sure that the needle of the dial indicator is perpendicular
to the SST and that it is placed in the middle of the 3rd indention.
(f) Lightly turn the No.1 balance shaft by hand and measure
the backlash.
HINT:
Turn the No.1 balance shaft 4 or 5 times to provide a
steady backlash reading.
To prevent excessive backlash due to thrust clearance,
measure the backlash while pressing on the rear of the
No.1 balance shaft.
Standard backlash (at punch mark A):
0.005 ± 0.040 mm (0.0002 ± 0.0016 in.)
NOTICE:
Do not turn the No.1 balance shaft strongly.
(g) Remove the dial indicator and SST.
(h) Turn the crankshaft clockwise to align the groove of the
No.2 housing with punch mark B.
(i) Set the dial indicator. (See step (e))
(j) Measure the backlash. (See step (f))
Standard backlash (at punch mark B):
0.005 ± 0.060 mm (0.0002 ± 0.0024 in.)
(k) Remove the dial indicator.