Page 3393 of 4770
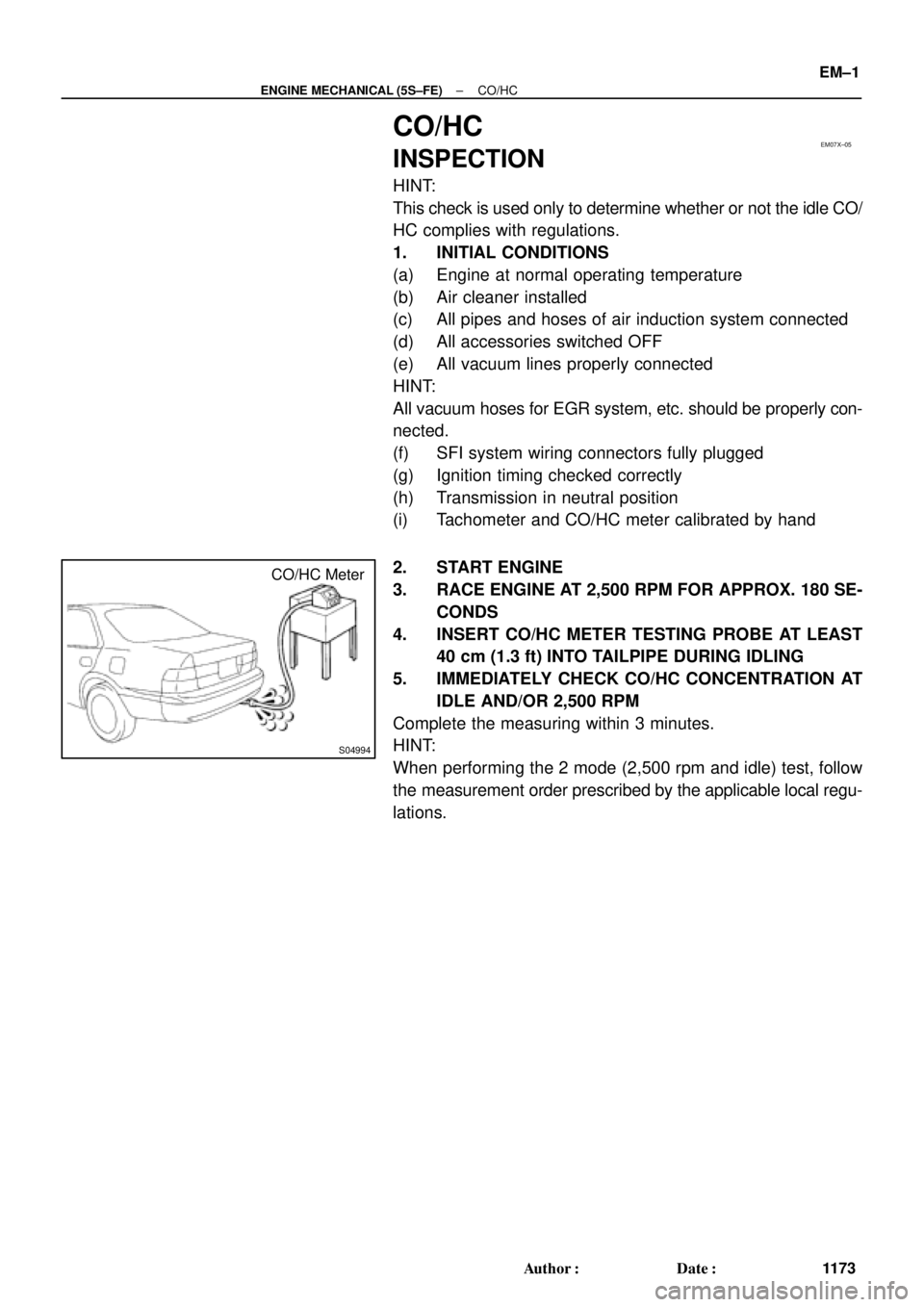
EM07X±05
S04994
CO/HC Meter
± ENGINE MECHANICAL (5S±FE)CO/HC
EM±1
1173 Author: Date:
CO/HC
INSPECTION
HINT:
This check is used only to determine whether or not the idle CO/
HC complies with regulations.
1. INITIAL CONDITIONS
(a) Engine at normal operating temperature
(b) Air cleaner installed
(c) All pipes and hoses of air induction system connected
(d) All accessories switched OFF
(e) All vacuum lines properly connected
HINT:
All vacuum hoses for EGR system, etc. should be properly con-
nected.
(f) SFI system wiring connectors fully plugged
(g) Ignition timing checked correctly
(h) Transmission in neutral position
(i) Tachometer and CO/HC meter calibrated by hand
2. START ENGINE
3. RACE ENGINE AT 2,500 RPM FOR APPROX. 180 SE-
CONDS
4. INSERT CO/HC METER TESTING PROBE AT LEAST
40 cm (1.3 ft) INTO TAILPIPE DURING IDLING
5. IMMEDIATELY CHECK CO/HC CONCENTRATION AT
IDLE AND/OR 2,500 RPM
Complete the measuring within 3 minutes.
HINT:
When performing the 2 mode (2,500 rpm and idle) test, follow
the measurement order prescribed by the applicable local regu-
lations.
Page 3394 of 4770
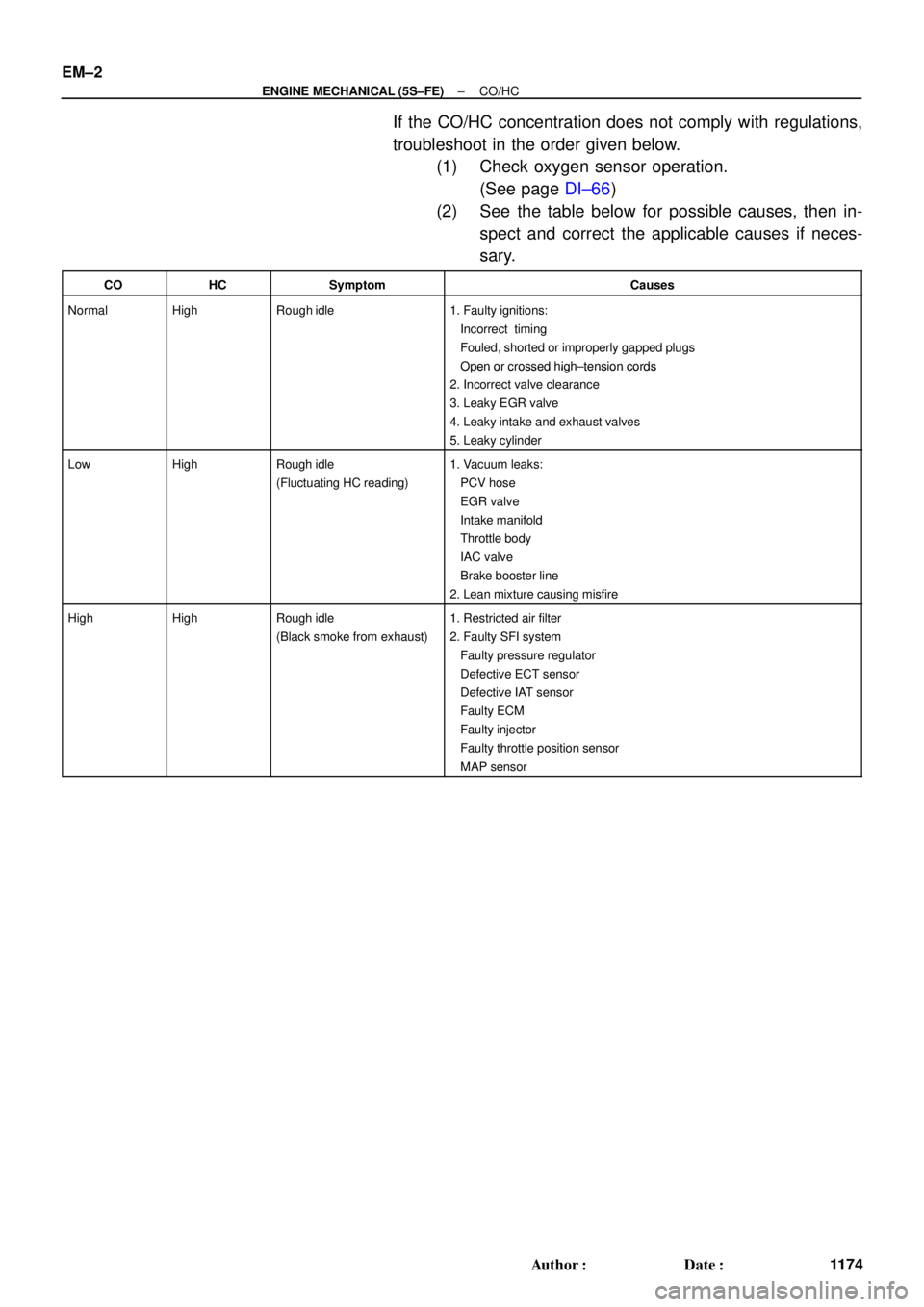
EM±2
± ENGINE MECHANICAL (5S±FE)CO/HC
1174 Author: Date:
If the CO/HC concentration does not comply with regulations,
troubleshoot in the order given below.
(1) Check oxygen sensor operation.
(See page DI±66)
(2) See the table below for possible causes, then in-
spect and correct the applicable causes if neces-
sary.
COHCSymptomCauses
NormalHighRough idle1. Faulty ignitions:
Incorrect timing
Fouled, shorted or improperly gapped plugs
Open or crossed hi
gh±tension cords Oen or crossed high±tension cords
2. Incorrect valve clearance
3. Leaky EGR valve
4. Leaky intake and exhaust valves
5. Leaky cylinder
LowHighRough idle
(Fluctuating HC reading)1. Vacuum leaks:
PCV hose
EGR valve
Intake manifold
Throttle body
IAC valve
Brake booster line
2. Lean mixture causing misfire
HighHighRough idle
(Black smoke from exhaust)1. Restricted air filter
2. Faulty SFI system
Faulty pressure regulator
Defective ECT sensor
Defective IAT sensor
Faulty ECM
Faulty injector
Faulty throttle position sensor
MAP sensor
Page 3395 of 4770
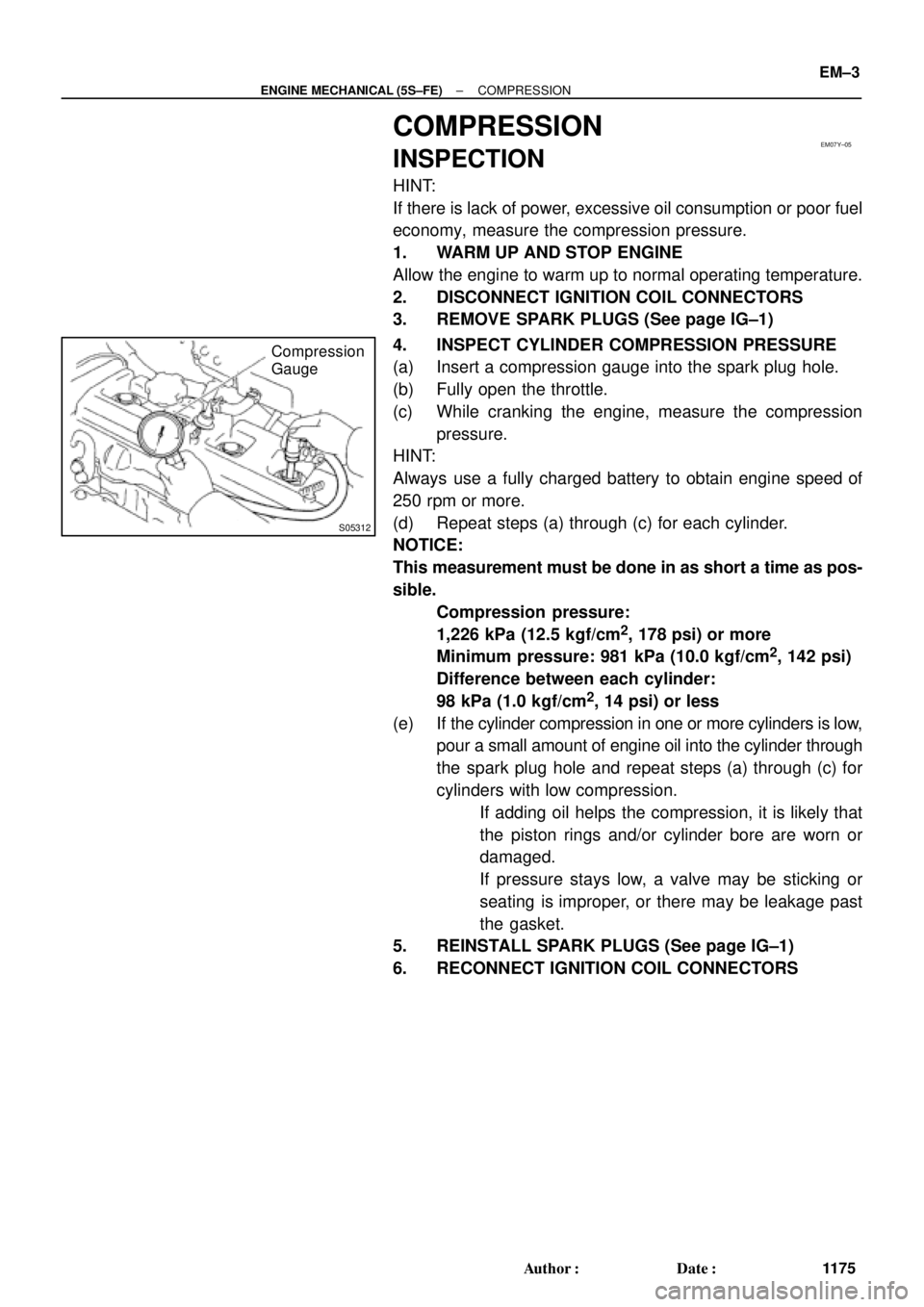
EM07Y±05
S05312
Compression
Gauge
± ENGINE MECHANICAL (5S±FE)COMPRESSION
EM±3
1175 Author: Date:
COMPRESSION
INSPECTION
HINT:
If there is lack of power, excessive oil consumption or poor fuel
economy, measure the compression pressure.
1. WARM UP AND STOP ENGINE
Allow the engine to warm up to normal operating temperature.
2. DISCONNECT IGNITION COIL CONNECTORS
3. REMOVE SPARK PLUGS (See page IG±1)
4. INSPECT CYLINDER COMPRESSION PRESSURE
(a) Insert a compression gauge into the spark plug hole.
(b) Fully open the throttle.
(c) While cranking the engine, measure the compression
pressure.
HINT:
Always use a fully charged battery to obtain engine speed of
250 rpm or more.
(d) Repeat steps (a) through (c) for each cylinder.
NOTICE:
This measurement must be done in as short a time as pos-
sible.
Compression pressure:
1,226 kPa (12.5 kgf/cm
2, 178 psi) or more
Minimum pressure: 981 kPa (10.0 kgf/cm
2, 142 psi)
Difference between each cylinder:
98 kPa (1.0 kgf/cm
2, 14 psi) or less
(e) If the cylinder compression in one or more cylinders is low,
pour a small amount of engine oil into the cylinder through
the spark plug hole and repeat steps (a) through (c) for
cylinders with low compression.
If adding oil helps the compression, it is likely that
the piston rings and/or cylinder bore are worn or
damaged.
If pressure stays low, a valve may be sticking or
seating is improper, or there may be leakage past
the gasket.
5. REINSTALL SPARK PLUGS (See page IG±1)
6. RECONNECT IGNITION COIL CONNECTORS
Page 3396 of 4770
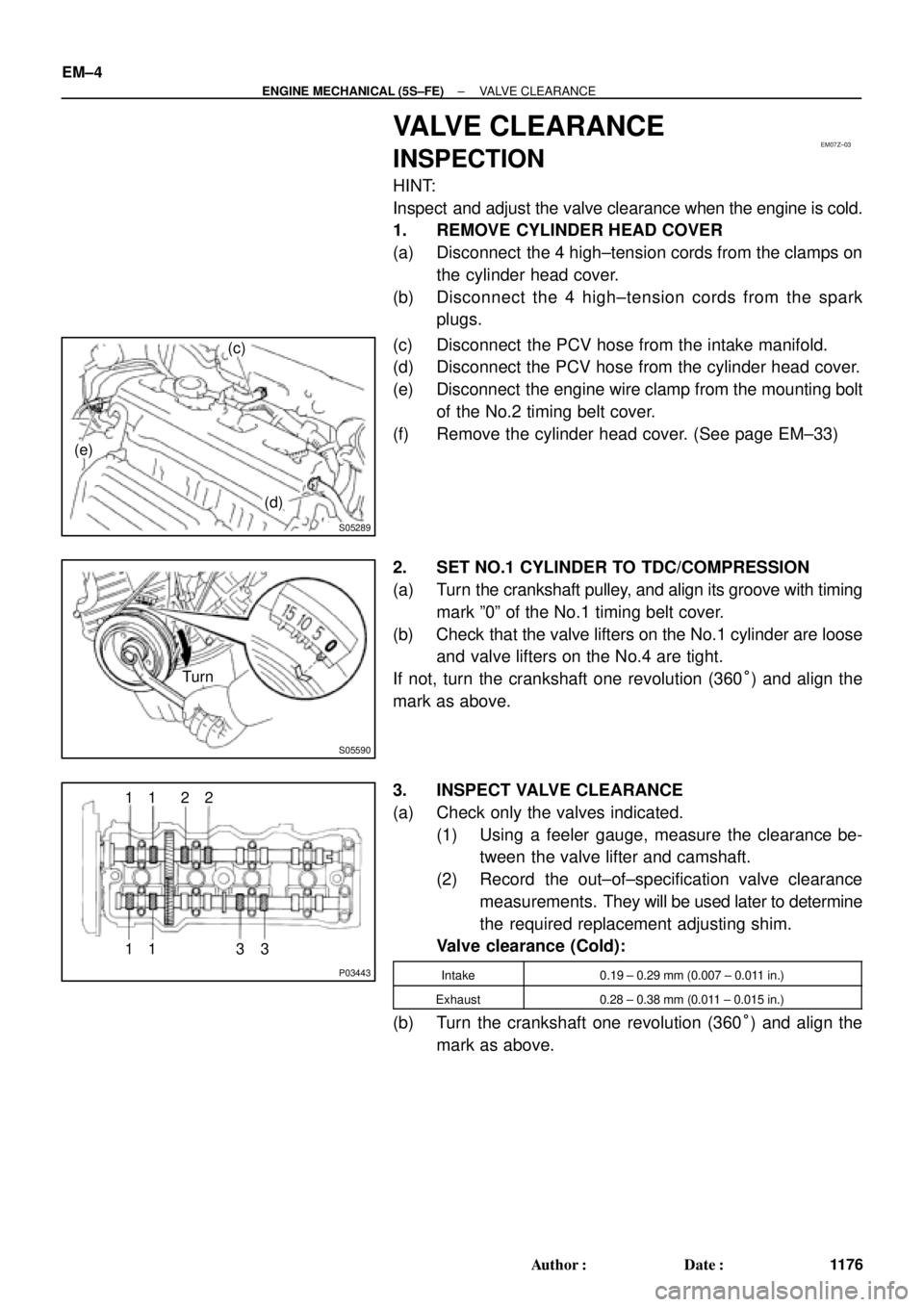
EM07Z±03
S05289
(c)
(d) (e)
S05590
Turn
P03443
1 11 122
33 EM±4
± ENGINE MECHANICAL (5S±FE)VALVE CLEARANCE
1176 Author: Date:
VALVE CLEARANCE
INSPECTION
HINT:
Inspect and adjust the valve clearance when the engine is cold.
1. REMOVE CYLINDER HEAD COVER
(a) Disconnect the 4 high±tension cords from the clamps on
the cylinder head cover.
(b) Disconnect the 4 high±tension cords from the spark
plugs.
(c) Disconnect the PCV hose from the intake manifold.
(d) Disconnect the PCV hose from the cylinder head cover.
(e) Disconnect the engine wire clamp from the mounting bolt
of the No.2 timing belt cover.
(f) Remove the cylinder head cover. (See page EM±33)
2. SET NO.1 CYLINDER TO TDC/COMPRESSION
(a) Turn the crankshaft pulley, and align its groove with timing
mark º0º of the No.1 timing belt cover.
(b) Check that the valve lifters on the No.1 cylinder are loose
and valve lifters on the No.4 are tight.
If not, turn the crankshaft one revolution (360°) and align the
mark as above.
3. INSPECT VALVE CLEARANCE
(a) Check only the valves indicated.
(1) Using a feeler gauge, measure the clearance be-
tween the valve lifter and camshaft.
(2) Record the out±of±specification valve clearance
measurements. They will be used later to determine
the required replacement adjusting shim.
Valve clearance (Cold):
Intake0.19 ± 0.29 mm (0.007 ± 0.011 in.)
Exhaust0.28 ± 0.38 mm (0.011 ± 0.015 in.)
(b) Turn the crankshaft one revolution (360°) and align the
mark as above.
Page 3397 of 4770
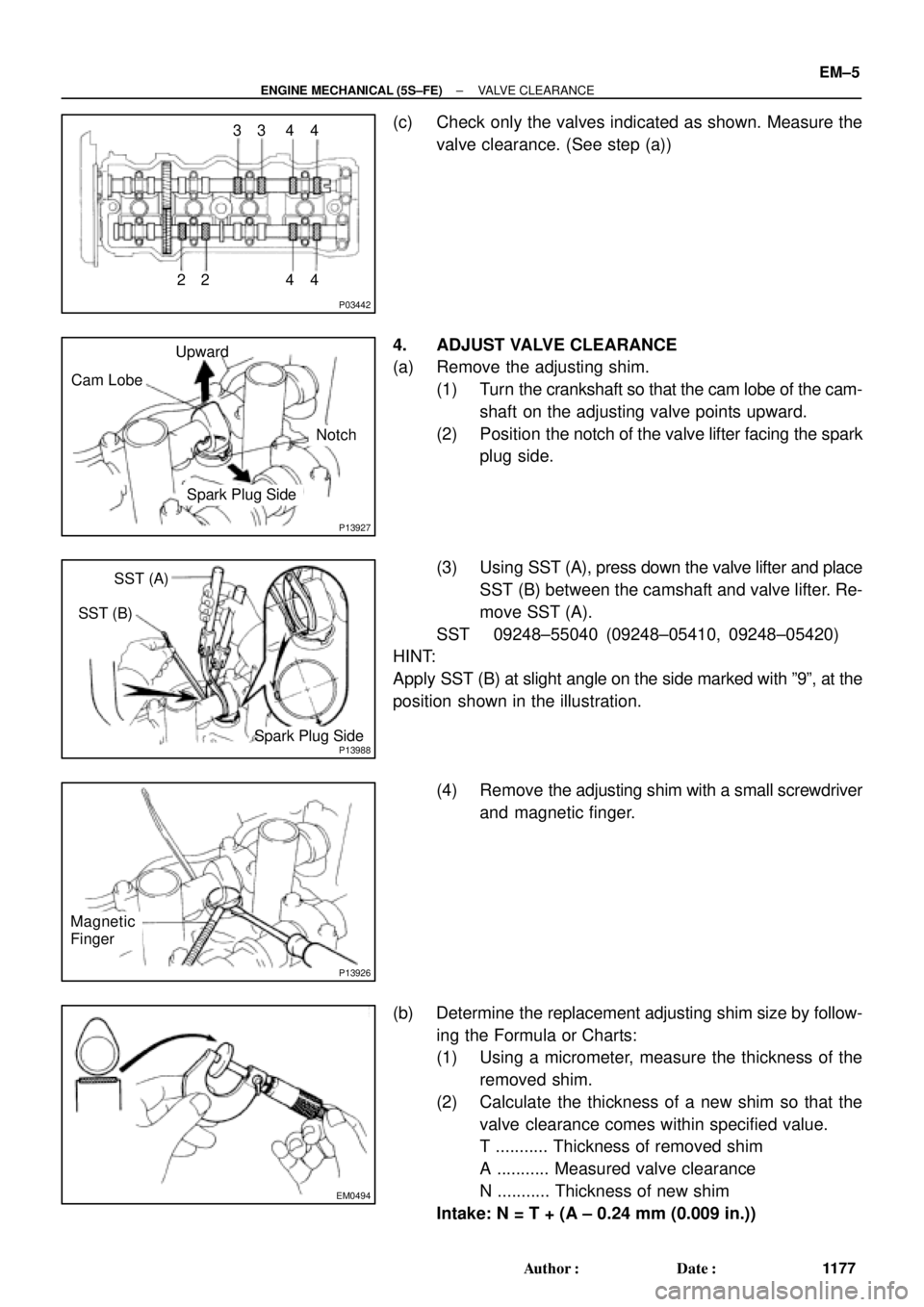
P03442
2 233 44
44
P13927
Upward
Cam Lobe
Notch
Spark Plug Side
P13988Spark Plug Side SST (A)
SST (B)
P13926
Magnetic
Finger
EM0494
± ENGINE MECHANICAL (5S±FE)VALVE CLEARANCE
EM±5
1177 Author: Date:
(c) Check only the valves indicated as shown. Measure the
valve clearance. (See step (a))
4. ADJUST VALVE CLEARANCE
(a) Remove the adjusting shim.
(1) Turn the crankshaft so that the cam lobe of the cam-
shaft on the adjusting valve points upward.
(2) Position the notch of the valve lifter facing the spark
plug side.
(3) Using SST (A), press down the valve lifter and place
SST (B) between the camshaft and valve lifter. Re-
move SST (A).
SST 09248±55040 (09248±05410, 09248±05420)
HINT:
Apply SST (B) at slight angle on the side marked with º9º, at the
position shown in the illustration.
(4) Remove the adjusting shim with a small screwdriver
and magnetic finger.
(b) Determine the replacement adjusting shim size by follow-
ing the Formula or Charts:
(1) Using a micrometer, measure the thickness of the
removed shim.
(2) Calculate the thickness of a new shim so that the
valve clearance comes within specified value.
T ........... Thickness of removed shim
A ........... Measured valve clearance
N ........... Thickness of new shim
Intake: N = T + (A ± 0.24 mm (0.009 in.))
Page 3398 of 4770
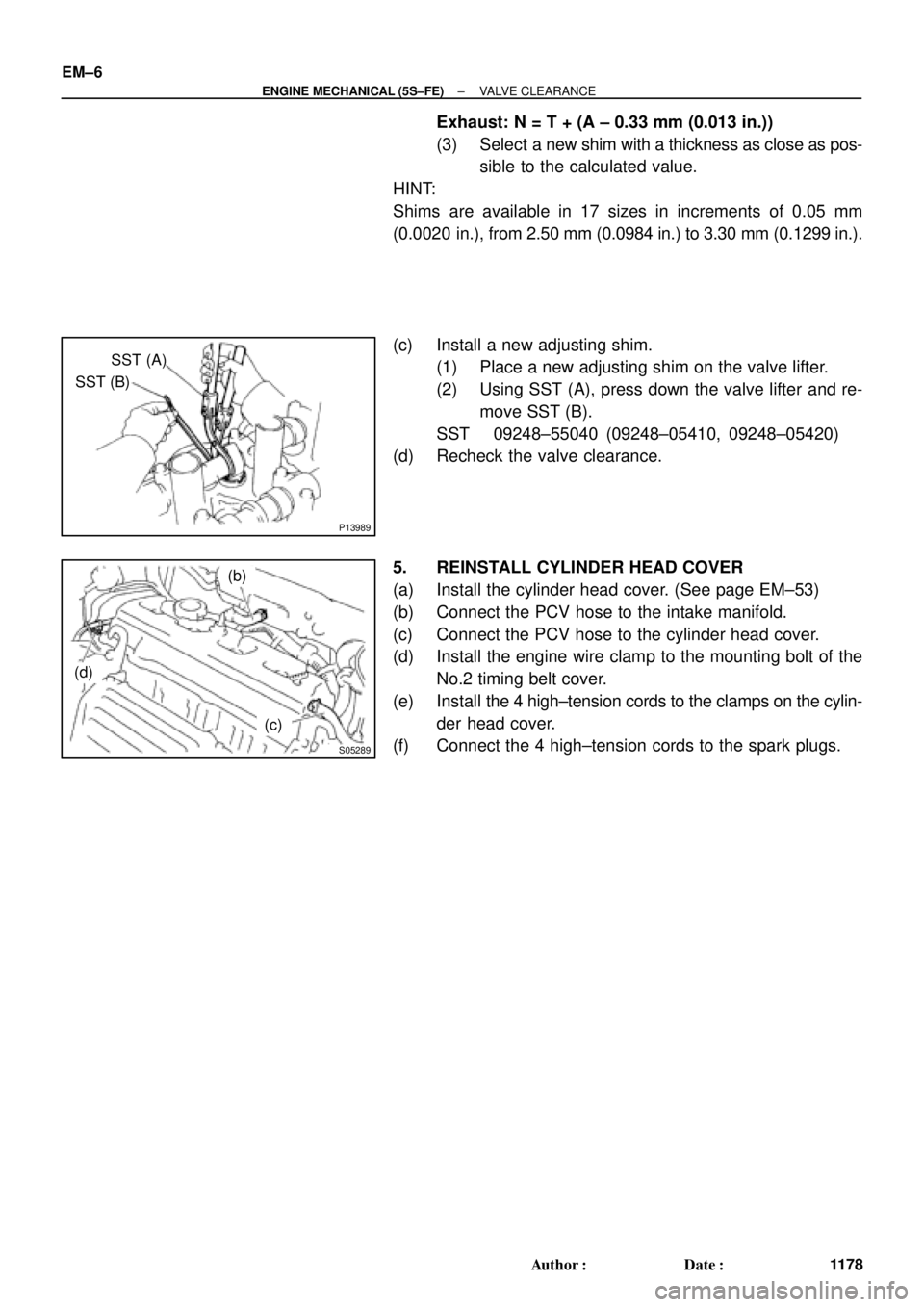
P13989
SST (A)
SST (B)
S05289
(b)
(c)
(d) EM±6
± ENGINE MECHANICAL (5S±FE)VALVE CLEARANCE
1178 Author: Date:
Exhaust: N = T + (A ± 0.33 mm (0.013 in.))
(3) Select a new shim with a thickness as close as pos-
sible to the calculated value.
HINT:
Shims are available in 17 sizes in increments of 0.05 mm
(0.0020 in.), from 2.50 mm (0.0984 in.) to 3.30 mm (0.1299 in.).
(c) Install a new adjusting shim.
(1) Place a new adjusting shim on the valve lifter.
(2) Using SST (A), press down the valve lifter and re-
move SST (B).
SST 09248±55040 (09248±05410, 09248±05420)
(d) Recheck the valve clearance.
5. REINSTALL CYLINDER HEAD COVER
(a) Install the cylinder head cover. (See page EM±53)
(b) Connect the PCV hose to the intake manifold.
(c) Connect the PCV hose to the cylinder head cover.
(d) Install the engine wire clamp to the mounting bolt of the
No.2 timing belt cover.
(e) Install the 4 high±tension cords to the clamps on the cylin-
der head cover.
(f) Connect the 4 high±tension cords to the spark plugs.
Page 3399 of 4770
V00867
EXAMPLE: The 2.800 mm (0.1102 in.) shim is installed,
and the measured clearance is 0.450 mm (0.0177 in.).
Replace the 2.800 mm (0.1102 in.) shim with a new No.11
shim.Adjusting Shim Selection Chart (Intake)
Intake valve clearance (Cold):
0.19 ± 0.29 mm (0.007 ± 0.011 in.)
2.500 (0.0984)
2.550 (0.1004)
2.600 (0.1024)
2.650 (0.1043)
2.700 (0.1063)
2.750 (0.1083)
2.800 (0.1102)
2.850 (0.1122)
2.900 (0.1142)2.950 (0.1161)
3.000 (0.1181)
3.050 (0.1201)
3.100 (0.1220)
3.150 (0.1240)
3.200 (0.1260)
3.250 (0.1280)
3.300 (0.1299) Shim
No.ThicknessShim
No.Thickness
4
5
6
7
8 3 2
1
910
11
12
13
14
15
16
17
HINT: New shims have the thickness in millimeters
imprinted on the face.
Installed shim thickness
Measured clearancemm (in.)
mm (in.)
New shim thickness
mm (in.)
± ENGINE MECHANICAL (5S±FE)VALVE CLEARANCE
EM±7
1179 Author: Date:
Page 3400 of 4770
V00868
2.500 (0.0984)
2.550 (0.1004)
2.600 (0.1024)
2.650 (0.1043)
2.700 (0.1063)
2.750 (0.1083)
2.800 (0.1102)
2.850 (0.1122)
2.900 (0.1142)2.950 (0.1161)
3.000 (0.1181)
3.050 (0.1201)
3.100 (0.1220)
3.150 (0.1240)
3.200 (0.1260)
3.250 (0.1280)
3.300 (0.1299) Shim
No.ThicknessShim
No.Thickness
4
5
6
7
8 3 2
1
910
11
12
13
14
15
16
17
HINT: New shims have the thickness in millimeters
imprinted on the face.
Adjusting Shim Selection Chart (Exhaust)
Exhaust valve clearance (Cold):
0.28 ± 0.38 mm (0.011 ± 0.015 in.)
EXAMPLE: The 2.800 mm (0.1102 in.) shim is installed,
and the measured clearance is 0.450 mm (0.0177 in.).
Replace the 2.800 mm (0.1102 in.) shim with a new No.9
shim.
Installed shim thickness
Measured clearancemm (in.)
mm (in.)
New shim thickness mm (in.)
EM±8
± ENGINE MECHANICAL (5S±FE)VALVE CLEARANCE
1180 Author: Date: