Page 601 of 4770
SYMBOLSMEANINGILLUSTRATION
SAW CUT OR
ROUGH CUT
REMOVE BRAZE
(See page IN±5) SPOT WELD OR
MIG PLUG WELD WELD POINTS
BRAZE CONTINUOUS MIG
WELD (BUTT WELD
OR TACK WELD)
BODY SEALER
SYMBOLS
The following symbols are used in the welding Diagrams in Section RE of this manual to indicate cutting
areas and the types of weld required.
INTRODUCTIONIN-4
Page 602 of 4770
Remove weld point and panel positionWeld points
REMOVAL
Weld method and panel positionWeld points
INSTALLATION
SYMBOL MEANING ILLUSTRATIONSYMBOL
Spot WeldMEANINGILLUSTRATION
Remove
Weld
Points
(Outside)
Mig Plug
Weld
(Middle)
(Inside)
Spot MIG
Weld
HINT: Panel position syrnbols are as seen from the
working posture.
Illustration of Weld Point Symbols
EXAMPLE:
INTRODUCTIONIN-5
Page 603 of 4770
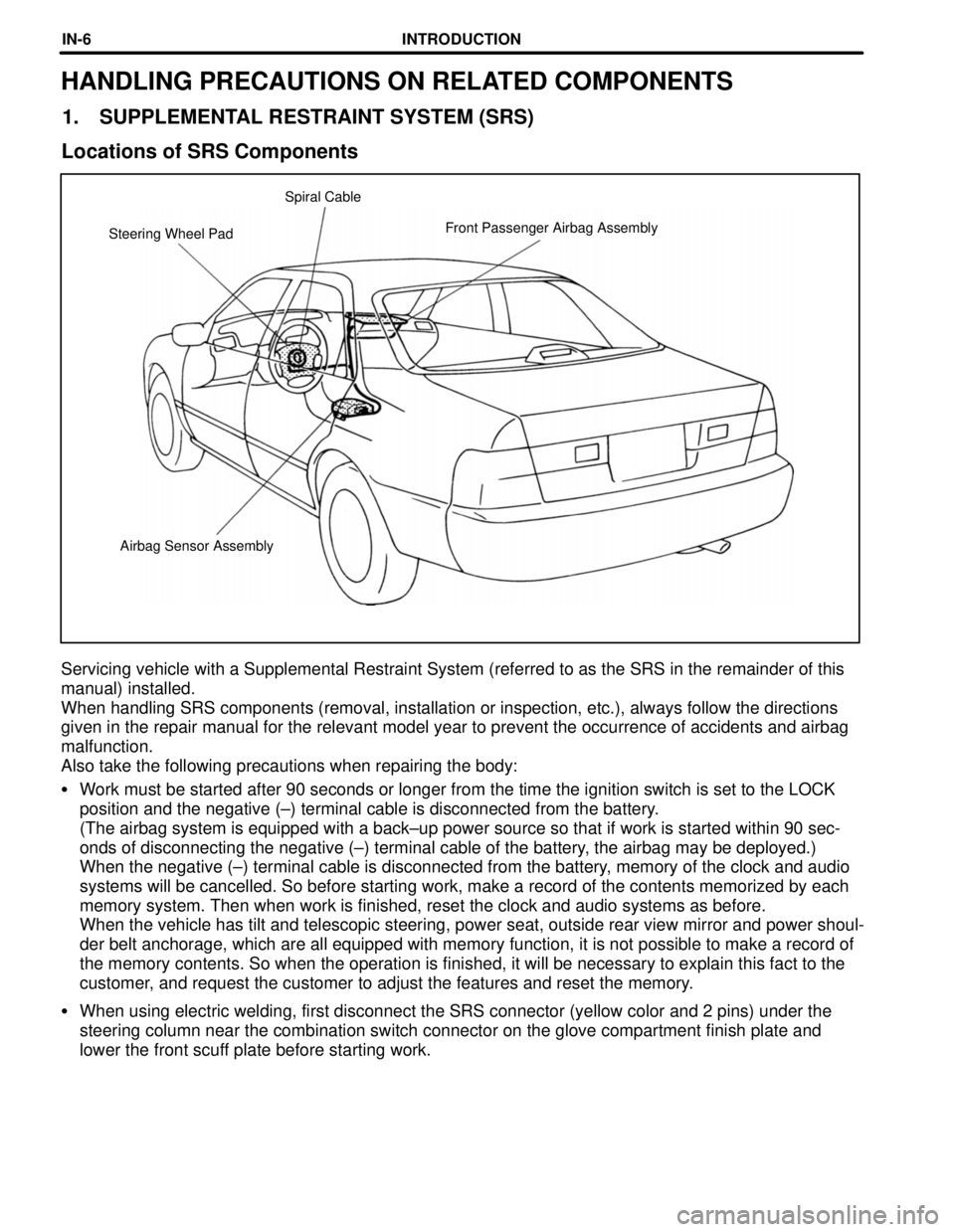
Airbag Sensor Assembly Steering Wheel PadFront Passenger Airbag Assembly Spiral Cable
HANDLING PRECAUTIONS ON RELATED COMPONENTS
1. SUPPLEMENTAL RESTRAINT SYSTEM (SRS)
Locations of SRS Components
Servicing vehicle with a Supplemental Restraint System (referred to as the SRS in the remainder of this
manual) installed.
When handling SRS components (removal, installation or inspection, etc.), always follow the directions
given in the repair manual for the relevant model year to prevent the occurrence of accidents and airbag
malfunction.
Also take the following precautions when repairing the body:
Work must be started after 90 seconds or longer from the time the ignition switch is set to the LOCK
position and the negative (±) terminal cable is disconnected from the battery.
(The airbag system is equipped with a back±up power source so that if work is started within 90 sec-
onds of disconnecting the negative (±) terminal cable of the battery, the airbag may be deployed.)
When the negative (±) terminal cable is disconnected from the battery, memory of the clock and audio
systems will be cancelled. So before starting work, make a record of the contents memorized by each
memory system. Then when work is finished, reset the clock and audio systems as before.
When the vehicle has tilt and telescopic steering, power seat, outside rear view mirror and power shoul-
der belt anchorage, which are all equipped with memory function, it is not possible to make a record of
the memory contents. So when the operation is finished, it will be necessary to explain this fact to the
customer, and request the customer to adjust the features and reset the memory.
When using electric welding, first disconnect the SRS connector (yellow color and 2 pins) under the
steering column near the combination switch connector on the glove compartment finish plate and
lower the front scuff plate before starting work.
INTRODUCTIONIN-6
Page 604 of 4770
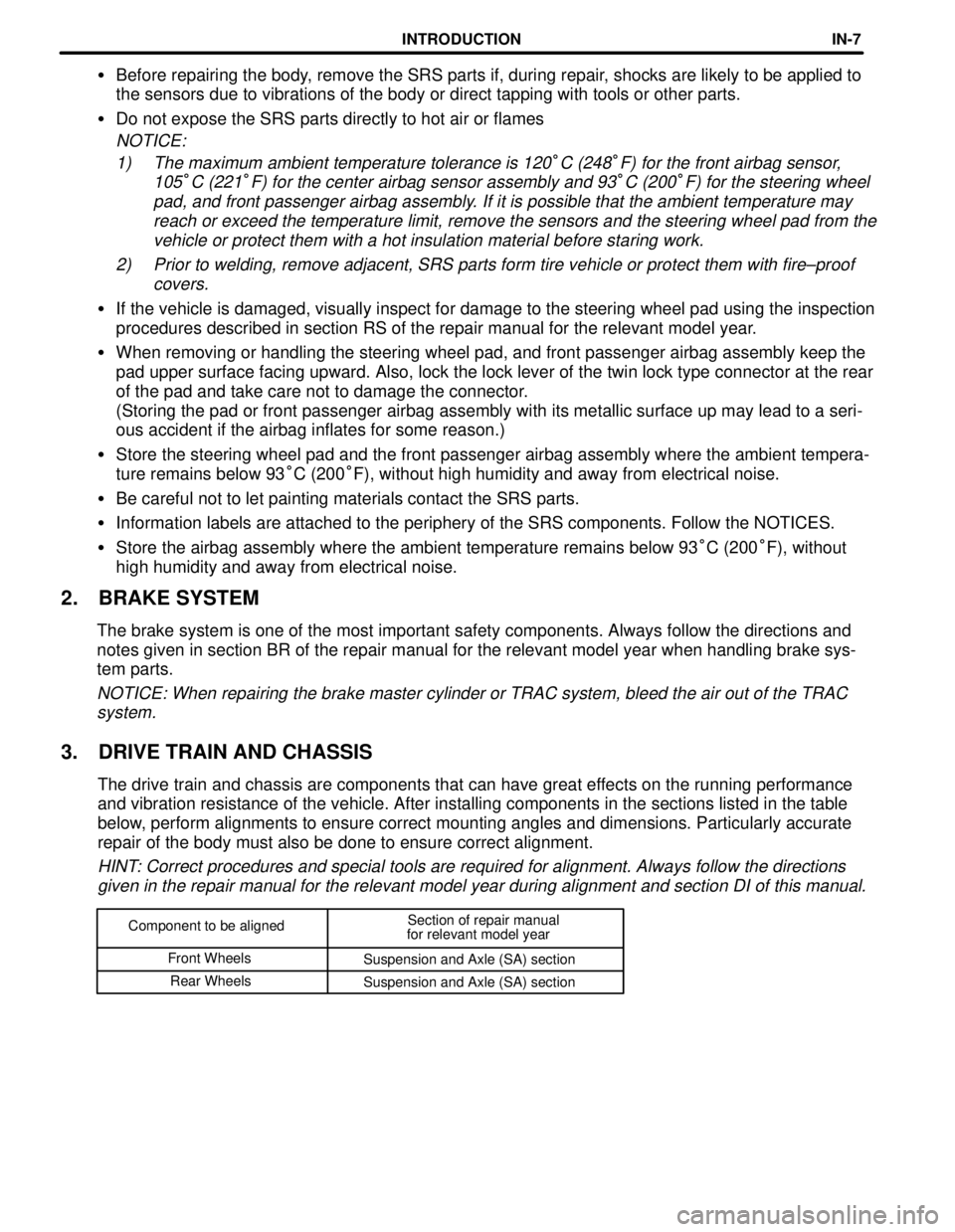
Component to be alignedSection of repair manual
for relevant model year
Front Wheels
Suspension and Axle (SA) section
Rear Wheels
Suspension and Axle (SA) section
Before repairing the body, remove the SRS parts if, during repair, shocks are likely to be applied to
the sensors due to vibrations of the body or direct tapping with tools or other parts.
Do not expose the SRS parts directly to hot air or flames
NOTICE:
1) The maximum ambient temperature tolerance is 120
°C (248°F) for the front airbag sensor,
105
°C (221°F) for the center airbag sensor assembly and 93°C (200°F) for the steering wheel
pad, and front passenger airbag assembly. If it is possible that the ambient temperature may
reach or exceed the temperature limit, remove the sensors and the steering wheel pad from the
vehicle or protect them with a hot insulation material before staring work.
2) Prior to welding, remove adjacent, SRS parts form tire vehicle or protect them with fire±proof
covers.
If the vehicle is damaged, visually inspect for damage to the steering wheel pad using the inspection
procedures described in section RS of the repair manual for the relevant model year.
When removing or handling the steering wheel pad, and front passenger airbag assembly keep the
pad upper surface facing upward. Also, lock the lock lever of the twin lock type connector at the rear
of the pad and take care not to damage the connector.
(Storing the pad or front passenger airbag assembly with its metallic surface up may lead to a seri-
ous accident if the airbag inflates for some reason.)
Store the steering wheel pad and the front passenger airbag assembly where the ambient tempera-
ture remains below 93°C (200°F), without high humidity and away from electrical noise.
Be careful not to let painting materials contact the SRS parts.
Information labels are attached to the periphery of the SRS components. Follow the NOTICES.
Store the airbag assembly where the ambient temperature remains below 93°C (200°F), without
high humidity and away from electrical noise.
2. BRAKE SYSTEM
The brake system is one of the most important safety components. Always follow the directions and
notes given in section BR of the repair manual for the relevant model year when handling brake sys-
tem parts.
NOTICE: When repairing the brake master cylinder or TRAC system, bleed the air out of the TRAC
system.
3. DRIVE TRAIN AND CHASSIS
The drive train and chassis are components that can have great effects on the running performance
and vibration resistance of the vehicle. After installing components in the sections listed in the table
below, perform alignments to ensure correct mounting angles and dimensions. Particularly accurate
repair of the body must also be done to ensure correct alignment.
HINT: Correct procedures and special tools are required for alignment. Always follow the directions
given in the repair manual for the relevant model year during alignment and section DI of this manual.
INTRODUCTIONIN-7
Page 605 of 4770
4. COMPONENTS ADJACENT TO THE BODY PANELS
Various types of component parts are mounted directly on or adjacently to the body panels. Strictly
observe the following precautions to prevent damaging these components and the body panels dur-
ing handling.
Before repairing the body panels, remove their components or apply protective covers over the
components.
Before prying components off using a screwdriver or a scraper, etc., attach protective tape to the
tool tip or blade to prevent damaging the components and the body paint.
Before removing components from the outer surface of the body, attach protective tape to the body
to ensure no damage to painted areas.
HINT: Apply touch±up paint to any damaged paint surfaces.
Before drilling or cutting sections, make sure that there are no wires, etc. on the reverse side.
INTRODUCTIONIN-8
Page 606 of 4770
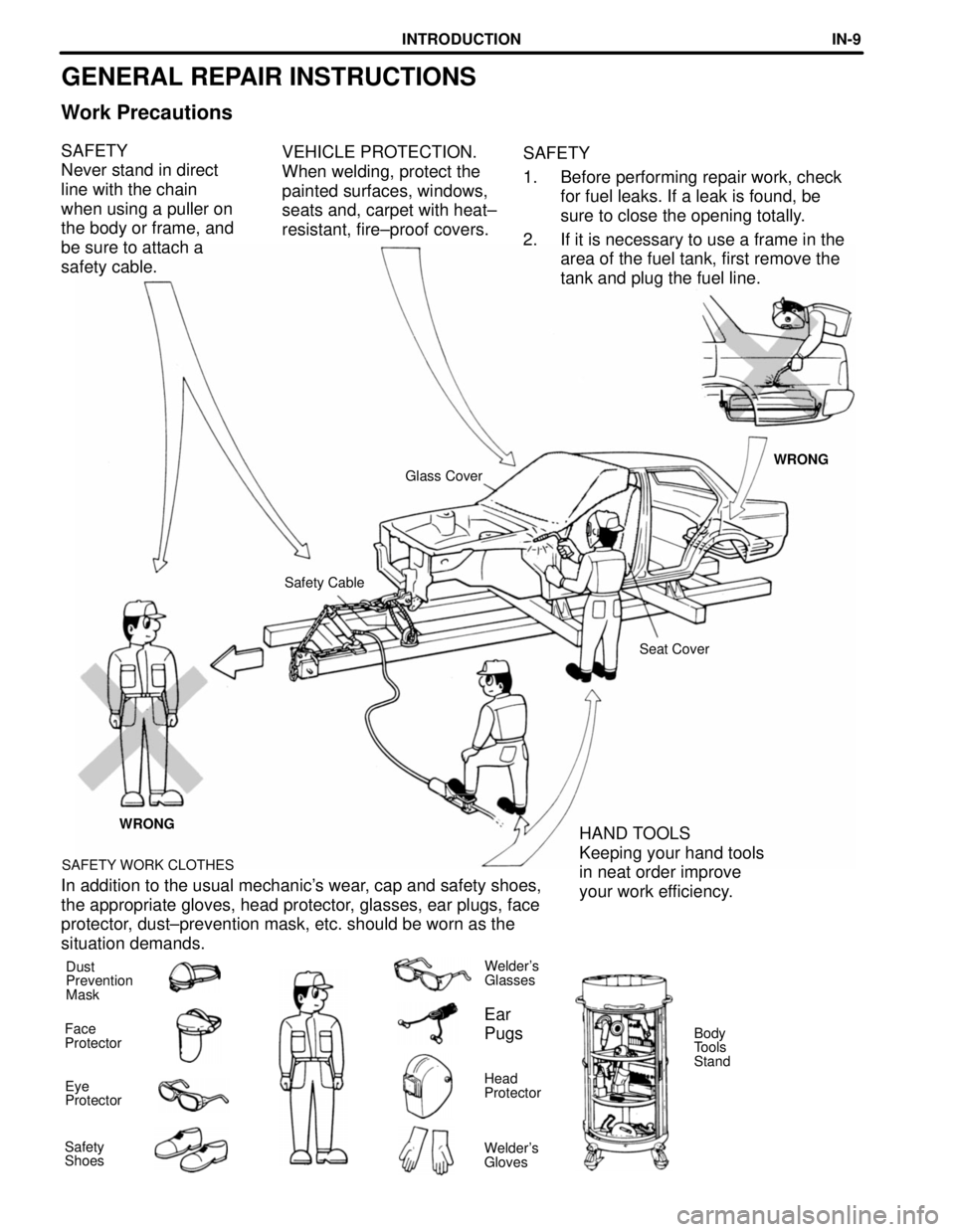
GENERAL REPAIR INSTRUCTIONS
Work Precautions
SAFETY
Never stand in direct
line with the chain
when using a puller on
the body or frame, and
be sure to attach a
safety cable.SAFETY
1. Before performing repair work, check
for fuel leaks. If a leak is found, be
sure to close the opening totally.
2. If it is necessary to use a frame in the
area of the fuel tank, first remove the
tank and plug the fuel line. VEHICLE PROTECTION.
When welding, protect the
painted surfaces, windows,
seats and, carpet with heat±
resistant, fire±proof covers.
WRONG
Glass Cover
Safety Cable
Seat Cover
WRONG
SAFETY WORK CLOTHES
HAND TOOLS
Keeping your hand tools
in neat order improve
your work efficiency. In addition to the usual mechanic's wear, cap and safety shoes,
the appropriate gloves, head protector, glasses, ear plugs, face
protector, dust±prevention mask, etc. should be worn as the
situation demands.
Dust
Prevention
MaskWelder's
Glasses
Ear
Pugs
Body
Tools
Stand Face
Protector
Head
Protector Eye
Protector
Safety
ShoesWelder's
Gloves
INTRODUCTIONIN-9
Page 607 of 4770
Proper and Efficient Work Procedures
REMOVAL
NUMBER OF SPOT WELDS AND PANEL POSITIONS
The number of spot welds and the panel positions
to be removed are shown for your reference.
HINT: See ºSymbolsº on page IN±4, 5.
PRE±REMOVAL MEASURING
Before removal or cutting
operations, take measurements
in accordance with the dimension
diagram. Always use a puller to
straighten a damaged body or
frame.
REMOVAL OF ADJACENT COMPONENTS
When removing adjacent components,
apply protective tape to the surrounding
body and your tools to prevent damage.
HINT: See ºHandling Precautions on
Related Componentsº on page IN±6.
PRECAUTIONS FOR DRILLING OR
CUTTING
Check behind any area to be drilled or
cut to insure that there are no hoses,
wires, etc., that may be damaged.
HINT: See ºHandling Precautions on
Related Componentsº on page IN±6.
CUTTING AREA
Always cut in a straight
line and avoid reinforced
area.
Cutting Okay
Corners
Reinforcement
WRONG
INTRODUCTIONIN-10
Page 608 of 4770
Thickness of
welded portionSize of plug hole
1.0 (0.04) under
5 (0.20) f over
1.0 (0.04) ± 1.5 (0.06) 6.5 (0.26) f over
1.5 (0.06) over
8 (0.31) f over
REFERENCE:
mm (in.)
PREPARATION FOR INSTALLATION
SPOT WELD POINTS
APPLICATION OF WELD±THROUGH PRIMER
(SPOT SEALER)
When welding panels with
a combined thickness of
over 3 mm (0.12 in.), use a
MIG (Metal Inert Gas)
welder for plug welding.
HINT: Spot welding will
not provide sufficient
durability for panels over
3 mm (0.12 in.) thick.
Less than.
3 mm
Remove the paint
from the new parts
and body to be
welded, and apply
weld±through primer.
HINT: See ºANTI±
RUST TREATMENTº
on page AR±2.
Air Saw
WRONG
Puncher
20 ± 30 mrn
Overlap
MAKING HOLES FOR PLUG WELDING
For areas where a spot welder cannot
be used, use a puncher or drill to make
holes for plug welding. ROUGH CUTTING OF JOINTS
For joint areas, rough cut the
new parts, leaving 20 ± 30 mm
(0.79 ± 1.18 in.) overlap.
INTRODUCTIONIN-11