Page 4257 of 4770
B01161
P13528
± STARTING (5S±FE)STARTER
ST±7
1714 Author: Date:
5. REMOVE BRUSH HOLDER
(a) Remove the 2 screws and end cover from the field frame.
Torque: 1.5 N´m (15 kgf´cm, 13 in.´lbf)
(b) Remove the O±ring from the field frame.
(c) Using a screwdriver, hold the spring back and disconnect
the brush from the brush holder. Disconnect the 4
brushes, and remove the brush holder.
NOTICE:
Check that the positive (+) lead wires are not grounded.
6. REMOVE ARMATURE FROM FIELD FRAME
Page 4258 of 4770
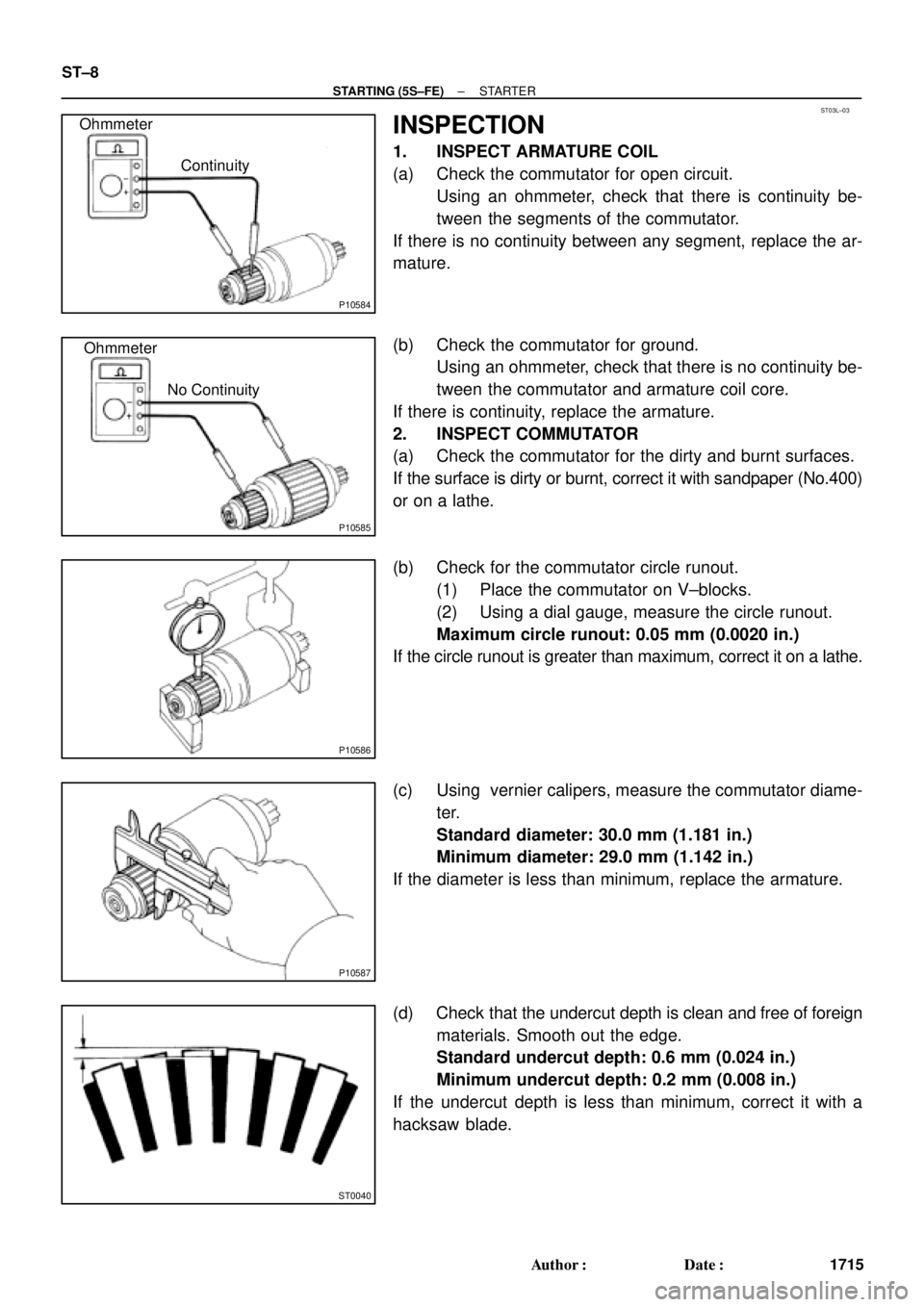
ST03L±03
P10584
Ohmmeter
Continuity
P10585
Ohmmeter
No Continuity
P10586
P10587
ST0040
ST±8
± STARTING (5S±FE)STARTER
1715 Author: Date:
INSPECTION
1. INSPECT ARMATURE COIL
(a) Check the commutator for open circuit.
Using an ohmmeter, check that there is continuity be-
tween the segments of the commutator.
If there is no continuity between any segment, replace the ar-
mature.
(b) Check the commutator for ground.
Using an ohmmeter, check that there is no continuity be-
tween the commutator and armature coil core.
If there is continuity, replace the armature.
2. INSPECT COMMUTATOR
(a) Check the commutator for the dirty and burnt surfaces.
If the surface is dirty or burnt, correct it with sandpaper (No.400)
or on a lathe.
(b) Check for the commutator circle runout.
(1) Place the commutator on V±blocks.
(2) Using a dial gauge, measure the circle runout.
Maximum circle runout: 0.05 mm (0.0020 in.)
If the circle runout is greater than maximum, correct it on a lathe.
(c) Using vernier calipers, measure the commutator diame-
ter.
Standard diameter: 30.0 mm (1.181 in.)
Minimum diameter: 29.0 mm (1.142 in.)
If the diameter is less than minimum, replace the armature.
(d) Check that the undercut depth is clean and free of foreign
materials. Smooth out the edge.
Standard undercut depth: 0.6 mm (0.024 in.)
Minimum undercut depth: 0.2 mm (0.008 in.)
If the undercut depth is less than minimum, correct it with a
hacksaw blade.
Page 4259 of 4770
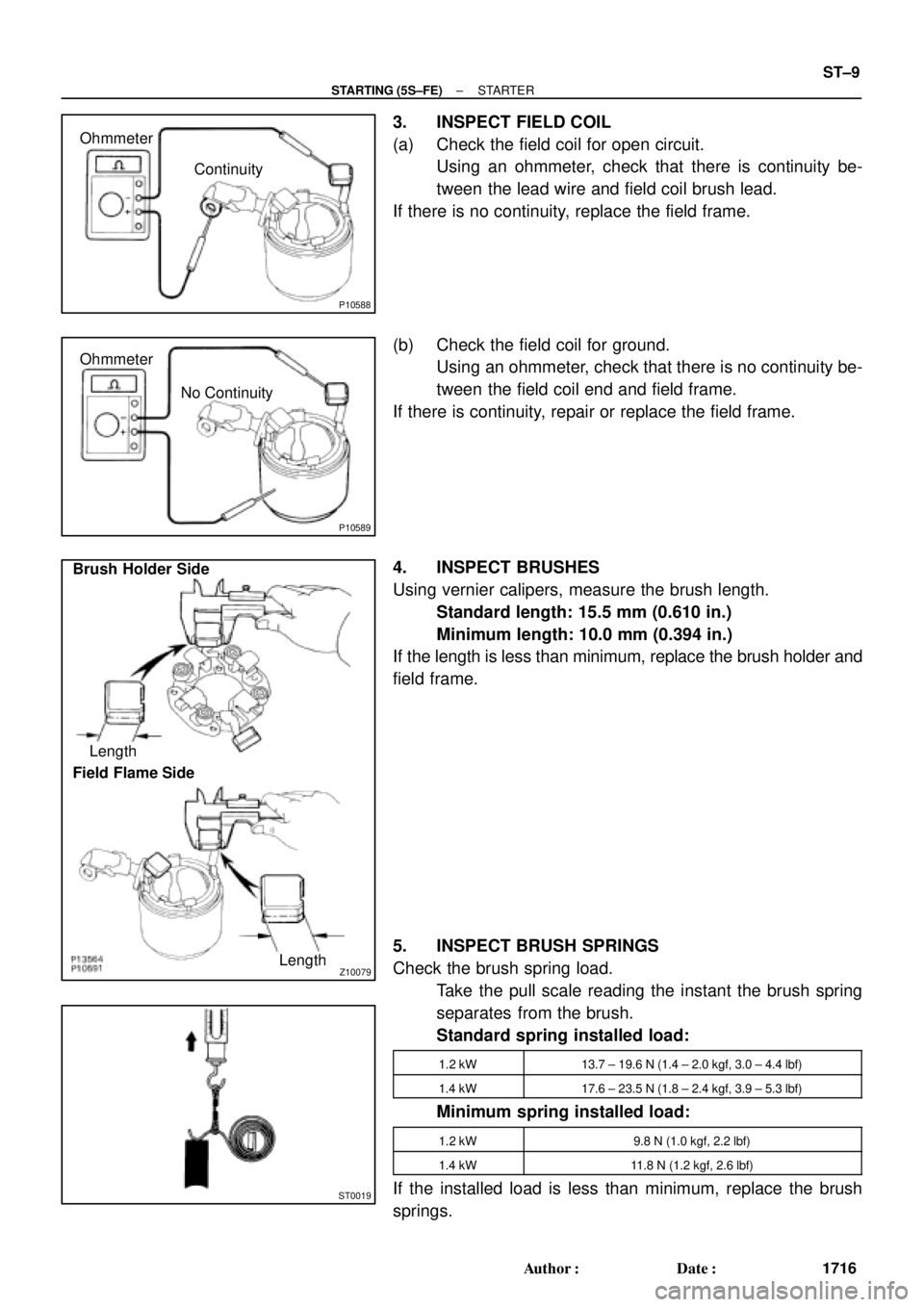
P10588
Ohmmeter
Continuity
P10589
Ohmmeter
No Continuity
Z10079
Brush Holder Side
Field Flame SideLength
Length
ST0019
± STARTING (5S±FE)STARTER
ST±9
1716 Author: Date:
3. INSPECT FIELD COIL
(a) Check the field coil for open circuit.
Using an ohmmeter, check that there is continuity be-
tween the lead wire and field coil brush lead.
If there is no continuity, replace the field frame.
(b) Check the field coil for ground.
Using an ohmmeter, check that there is no continuity be-
tween the field coil end and field frame.
If there is continuity, repair or replace the field frame.
4. INSPECT BRUSHES
Using vernier calipers, measure the brush length.
Standard length: 15.5 mm (0.610 in.)
Minimum length: 10.0 mm (0.394 in.)
If the length is less than minimum, replace the brush holder and
field frame.
5. INSPECT BRUSH SPRINGS
Check the brush spring load.
Take the pull scale reading the instant the brush spring
separates from the brush.
Standard spring installed load:
1.2 kW13.7 ± 19.6 N (1.4 ± 2.0 kgf, 3.0 ± 4.4 lbf)
1.4 kW17.6 ± 23.5 N (1.8 ± 2.4 kgf, 3.9 ± 5.3 lbf)
Minimum spring installed load:
1.2 kW9.8 N (1.0 kgf, 2.2 lbf)
1.4 kW11.8 N (1.2 kgf, 2.6 lbf)
If the installed load is less than minimum, replace the brush
springs.
Page 4260 of 4770
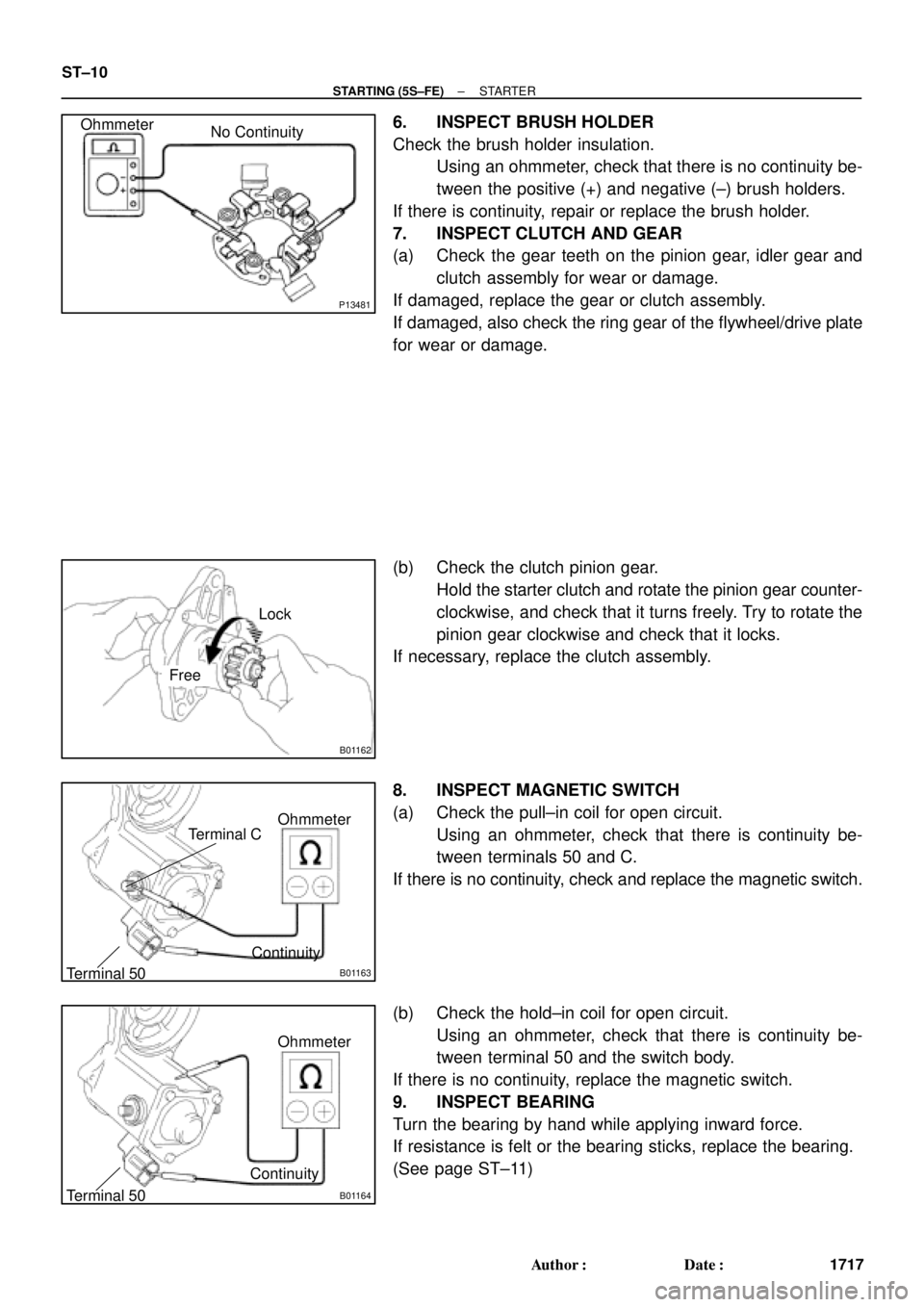
P13481
No Continuity Ohmmeter
B01162
Lock
Free
B01163
Ohmmeter
Terminal 50Terminal C
Continuity
B01164
Ohmmeter
Terminal 50Continuity
ST±10
± STARTING (5S±FE)STARTER
1717 Author: Date:
6. INSPECT BRUSH HOLDER
Check the brush holder insulation.
Using an ohmmeter, check that there is no continuity be-
tween the positive (+) and negative (±) brush holders.
If there is continuity, repair or replace the brush holder.
7. INSPECT CLUTCH AND GEAR
(a) Check the gear teeth on the pinion gear, idler gear and
clutch assembly for wear or damage.
If damaged, replace the gear or clutch assembly.
If damaged, also check the ring gear of the flywheel/drive plate
for wear or damage.
(b) Check the clutch pinion gear.
Hold the starter clutch and rotate the pinion gear counter-
clockwise, and check that it turns freely. Try to rotate the
pinion gear clockwise and check that it locks.
If necessary, replace the clutch assembly.
8. INSPECT MAGNETIC SWITCH
(a) Check the pull±in coil for open circuit.
Using an ohmmeter, check that there is continuity be-
tween terminals 50 and C.
If there is no continuity, check and replace the magnetic switch.
(b) Check the hold±in coil for open circuit.
Using an ohmmeter, check that there is continuity be-
tween terminal 50 and the switch body.
If there is no continuity, replace the magnetic switch.
9. INSPECT BEARING
Turn the bearing by hand while applying inward force.
If resistance is felt or the bearing sticks, replace the bearing.
(See page ST±11)
Page 4261 of 4770
ST03M±03
B01224
B01225
B01226
B01227
Stop Collar
Pinion Gear
Compression
Spring
B01228
± STARTING (5S±FE)STARTER
ST±11
1718 Author: Date:
REPLACEMENT
1. REPLACE CLUTCH ASSEMBLY
(a) Disassemble the starter housing and the clutch assembly.
(1) Mount a brass bar in a vise, and install the starter
housing and clutch assembly to the brass bar.
(2) Push down the pinion gear.
(3) Using a plastic±faced hammer, tap down the stop
collar.
(4) Using a screwdriver, pry out the snap ring.
(5) Remove these parts:
Stop collar
Pinion gear
Compression spring
(6) Push down the starter housing, and remove the
spring retainer.
(7) Disassemble these parts:
Starter housing
Starter clutch
Compression spring
Clutch shaft
Page 4262 of 4770
B01229
Starter Housing
Starter
ClutchCompression
Spring
Clutch
Shaft
B01230
B01231B01670
Spring
Compression PinionStop
Collar
Gear
Spring
Retainer
B01232
B01233
ST±12
± STARTING (5S±FE)STARTER
1719 Author: Date:
(b) Assemble the starter housing and the clutch assembly
(1) Assemble these parts:
Starter housing
Starter clutch
Compression spring
Clutch shaft
(2) Mount a brass bar in a vise, install the starter hous-
ing and clutch assembly to the brass bar.
(3) Push down the starter housing, and install these
parts:
Spring retainer
Compression spring
Pinion gear
Stop collar
(4) Push down the pinion gear.
(5) Using snap ring pliers, install a new snap ring.
(6) Using pliers, compress the snap ring.
(7) Check that the snap ring fits correctly.
Page 4263 of 4770
B01165
P10595
SST
P10596
SSTUpward
Downward
P10593
SST
P10594
± STARTING (5S±FE)STARTER
ST±13
1720 Author: Date:
(8) Remove the starter housing and clutch assembly
from the brass bar.
(9) Using a plastic±faced hammer, tap the clutch shaft
and install the stop collar onto the snap ring.
2. REPLACE FRONT BEARING
(a) Using SST, remove the bearing.
SST 09286±46011
(b) Using SST and a press, press in a new bearing.
NOTICE:
Be careful of the bearing installation direction.
SST 09820±00030
3. REPLACE REAR BEARING
(a) Using SST, remove the bearing.
SST 09286±46011
(b) Using a press, press in a new bearing.
Page 4264 of 4770
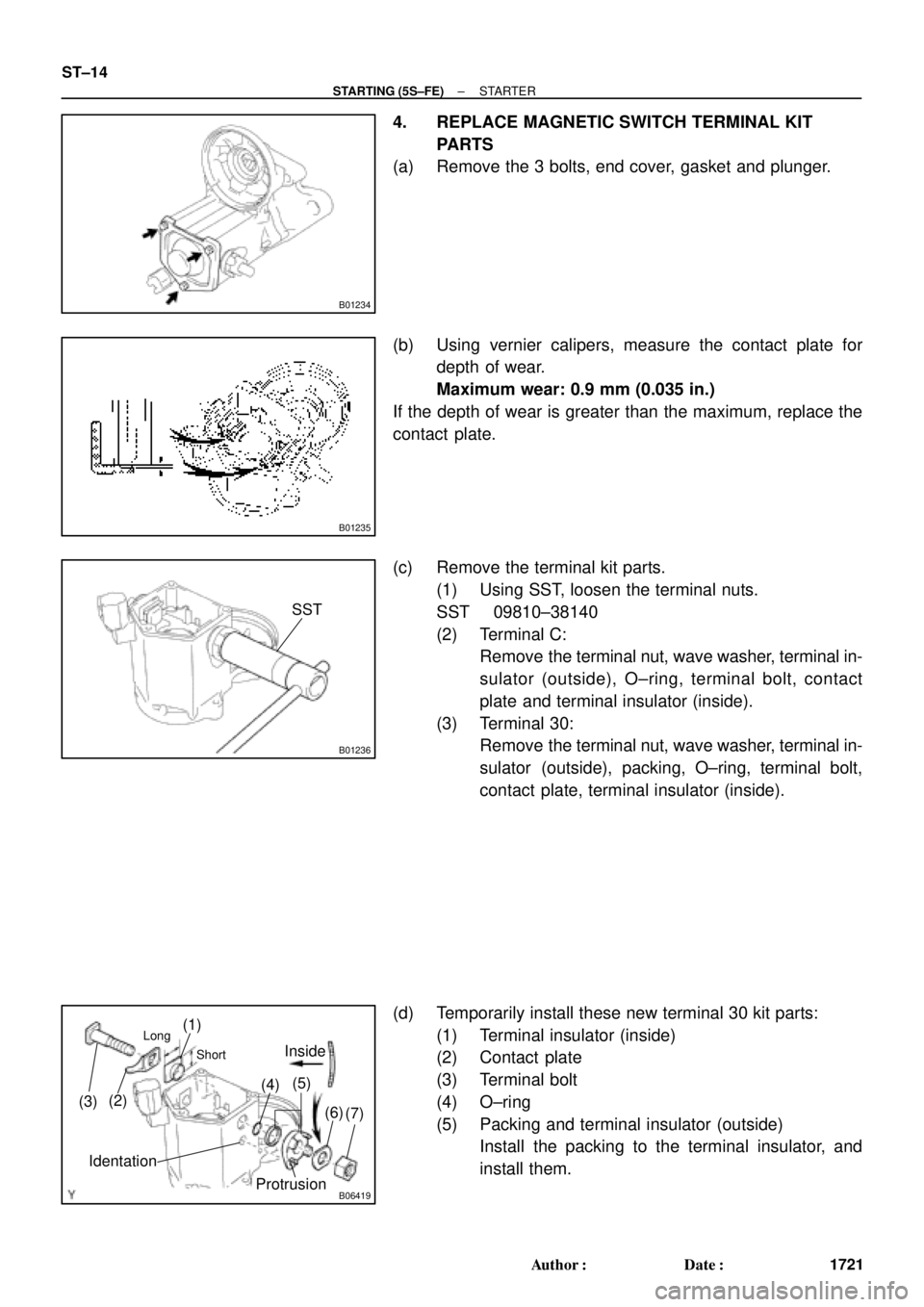
B01234
B01235
B01236
SST
B06419
(1)
(2)
(3)(4)(5)Long
Short
(6)
(7)
Inside
Protrusion
Identation
ST±14
± STARTING (5S±FE)STARTER
1721 Author: Date:
4. REPLACE MAGNETIC SWITCH TERMINAL KIT
PARTS
(a) Remove the 3 bolts, end cover, gasket and plunger.
(b) Using vernier calipers, measure the contact plate for
depth of wear.
Maximum wear: 0.9 mm (0.035 in.)
If the depth of wear is greater than the maximum, replace the
contact plate.
(c) Remove the terminal kit parts.
(1) Using SST, loosen the terminal nuts.
SST 09810±38140
(2) Terminal C:
Remove the terminal nut, wave washer, terminal in-
sulator (outside), O±ring, terminal bolt, contact
plate and terminal insulator (inside).
(3) Terminal 30:
Remove the terminal nut, wave washer, terminal in-
sulator (outside), packing, O±ring, terminal bolt,
contact plate, terminal insulator (inside).
(d) Temporarily install these new terminal 30 kit parts:
(1) Terminal insulator (inside)
(2) Contact plate
(3) Terminal bolt
(4) O±ring
(5) Packing and terminal insulator (outside)
Install the packing to the terminal insulator, and
install them.