Page 3505 of 4770
± ENGINE MECHANICAL (5S±FE)CYLINDER BLOCK
EM±113
1285 Author: Date:
(f) Install the wire clamp to the generator drive belt adjusting
bar.
(g) Connect the IAC valve water bypass hose to the water by-
pass pipe.
(h) Connect the water bypass hose (from the water bypass
pipe) to the water outlet.
(i) Install the camshafts. (See page EM±53)
(j) Install the cylinder head cover.
(1) Install the cylinder head cover. (See page EM±53)
(2) Connect the PCV hose to the intake manifold.
(k) Install the No.3 timing belt cover with the 3 bolts.
Torque: 7.8 N´m (80 kgf´cm, 69 in.´lbf)
23. INSTALL TIMING BELT AND PULLEYS
(See page EM±23)
24. DISCONNECT ENGINE FROM ENGINE STAND
Page 3506 of 4770
EM08M±03
A07369
Heated Oxygen Sensor (Bank 1 Sensor 2)
HINT:
Before installing oxygen sensor, twist
sensor wire counterclockwise 3 and 1/2
turns.
After installing oxygen sensor, check that
sensor wire is not twisted. If it is twisted,
remove oxygen sensor and reinstall it.
Heat Insulator
Bracket
RingTailpipe
Gasket
Center Exhaust Pipe
Heated Oxygen Sensor
(Bank 1 Sensor 2)
TWC (Except California)
Rear TWC (California)
Front Exhaust Pipe Bracket
StayBracket
N´m (kgf´cm, ft´lbf)
Non±reusable part Gasket
Gasket
Heat Insulator Heat Insulator
Heat Insulator
56 (570, 41)
44 (450, 32)
62 (630, 46)
56 (570, 41)
Bracket
: Specified torqueRing
19 (195, 14)
33 (330, 24)
33 (330, 24)
33 (330, 24)
EM±114
± ENGINE MECHANICAL (5S±FE)EXHAUST SYSTEM
1286 Author: Date:
EXHAUST SYSTEM
COMPONENTS
Page 3507 of 4770
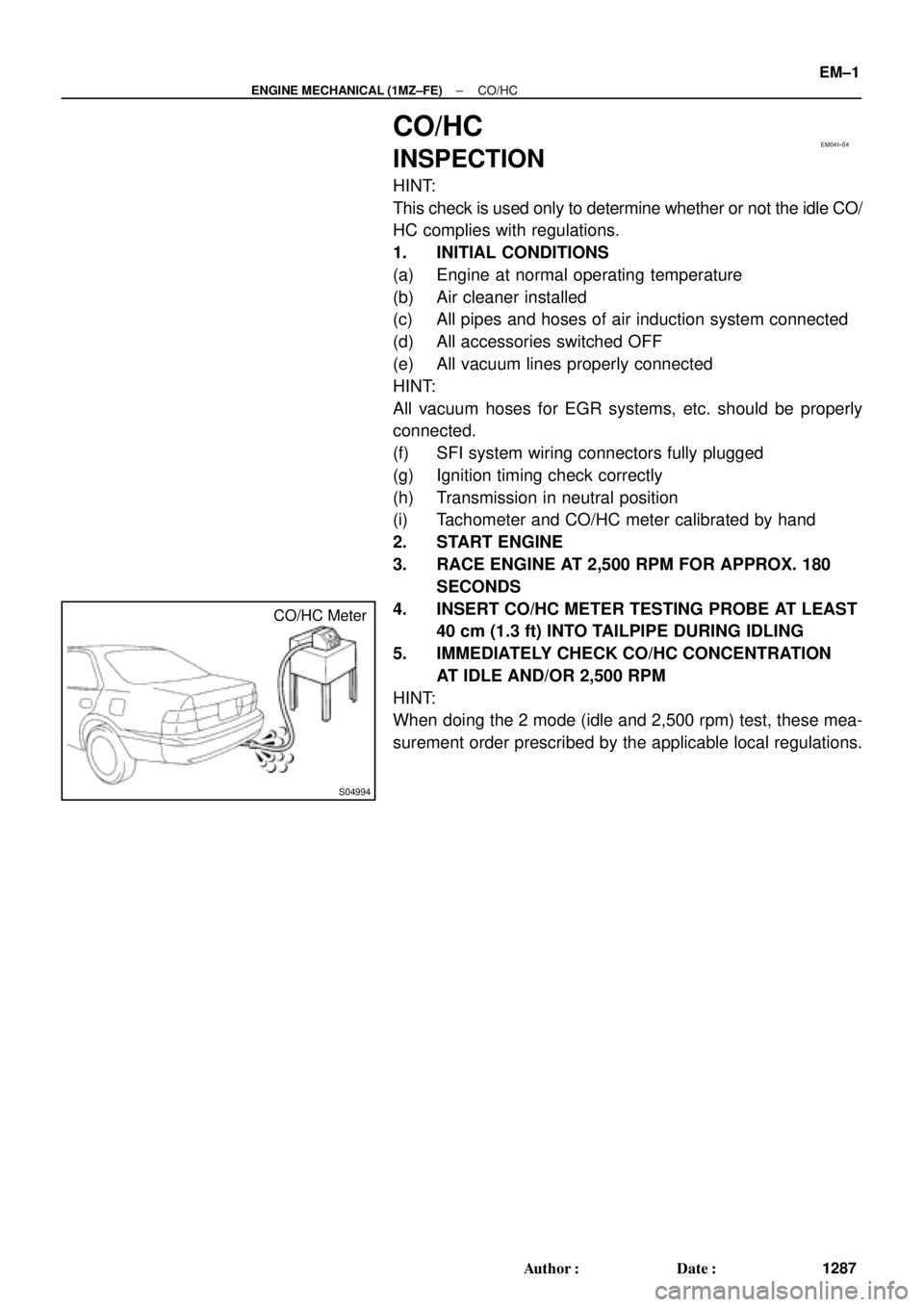
EM04I±04
S04994
CO/HC Meter
± ENGINE MECHANICAL (1MZ±FE)CO/HC
EM±1
1287 Author: Date:
CO/HC
INSPECTION
HINT:
This check is used only to determine whether or not the idle CO/
HC complies with regulations.
1. INITIAL CONDITIONS
(a) Engine at normal operating temperature
(b) Air cleaner installed
(c) All pipes and hoses of air induction system connected
(d) All accessories switched OFF
(e) All vacuum lines properly connected
HINT:
All vacuum hoses for EGR systems, etc. should be properly
connected.
(f) SFI system wiring connectors fully plugged
(g) Ignition timing check correctly
(h) Transmission in neutral position
(i) Tachometer and CO/HC meter calibrated by hand
2. START ENGINE
3. RACE ENGINE AT 2,500 RPM FOR APPROX. 180
SECONDS
4. INSERT CO/HC METER TESTING PROBE AT LEAST
40 cm (1.3 ft) INTO TAILPIPE DURING IDLING
5. IMMEDIATELY CHECK CO/HC CONCENTRATION
AT IDLE AND/OR 2,500 RPM
HINT:
When doing the 2 mode (idle and 2,500 rpm) test, these mea-
surement order prescribed by the applicable local regulations.
Page 3508 of 4770
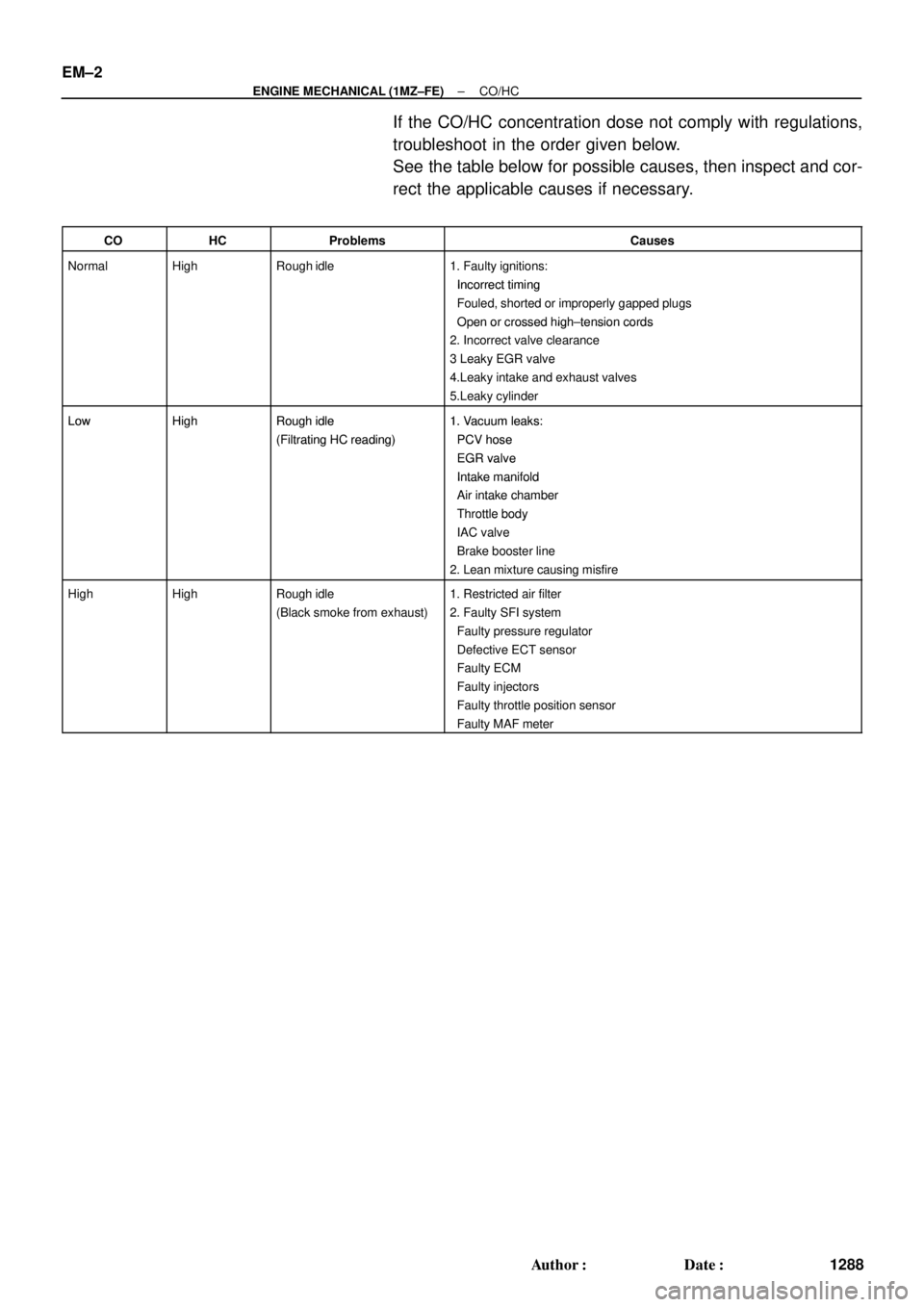
EM±2
± ENGINE MECHANICAL (1MZ±FE)CO/HC
1288 Author: Date:
If the CO/HC concentration dose not comply with regulations,
troubleshoot in the order given below.
See the table below for possible causes, then inspect and cor-
rect the applicable causes if necessary.
COHCProblemsCauses
NormalHighRough idle1. Faulty ignitions:
Incorrect timin
gIncorrect timing
Fouled, shorted or improperly gapped plugs
Open or crossed hi
gh±tension cordsOen or crossed high±tension cords
2. Incorrect valve clearance
3 Leaky EGR valve
3 Leaky EGR valve
4.Leaky intake and exhaust valves
5.Leaky cylinder
LowHighRough idle1. Vacuum leaks:LowHighRough idle
(
Filtrating HC reading)
1. Vacuum leaks:
PCV hose(Filtrating HC reading)PCV hose
EGR valveEGR valve
Intake manifoldIntake manifold
Air intake chamberAir intake chamber
Throttle bodyThrottle body
IAC valveIAC valve
Brake booster lineBrake booster line
2. Lean mixture causing misfire
HighHighRough idle
(Black smoke from exhaust)1. Restricted air filter
2. Faulty SFI system
Faulty pressure regulator
Defective ECT sensor
Faulty ECM
Faulty injectors
Faulty throttle position sensor
Faulty MAF meter
Page 3509 of 4770
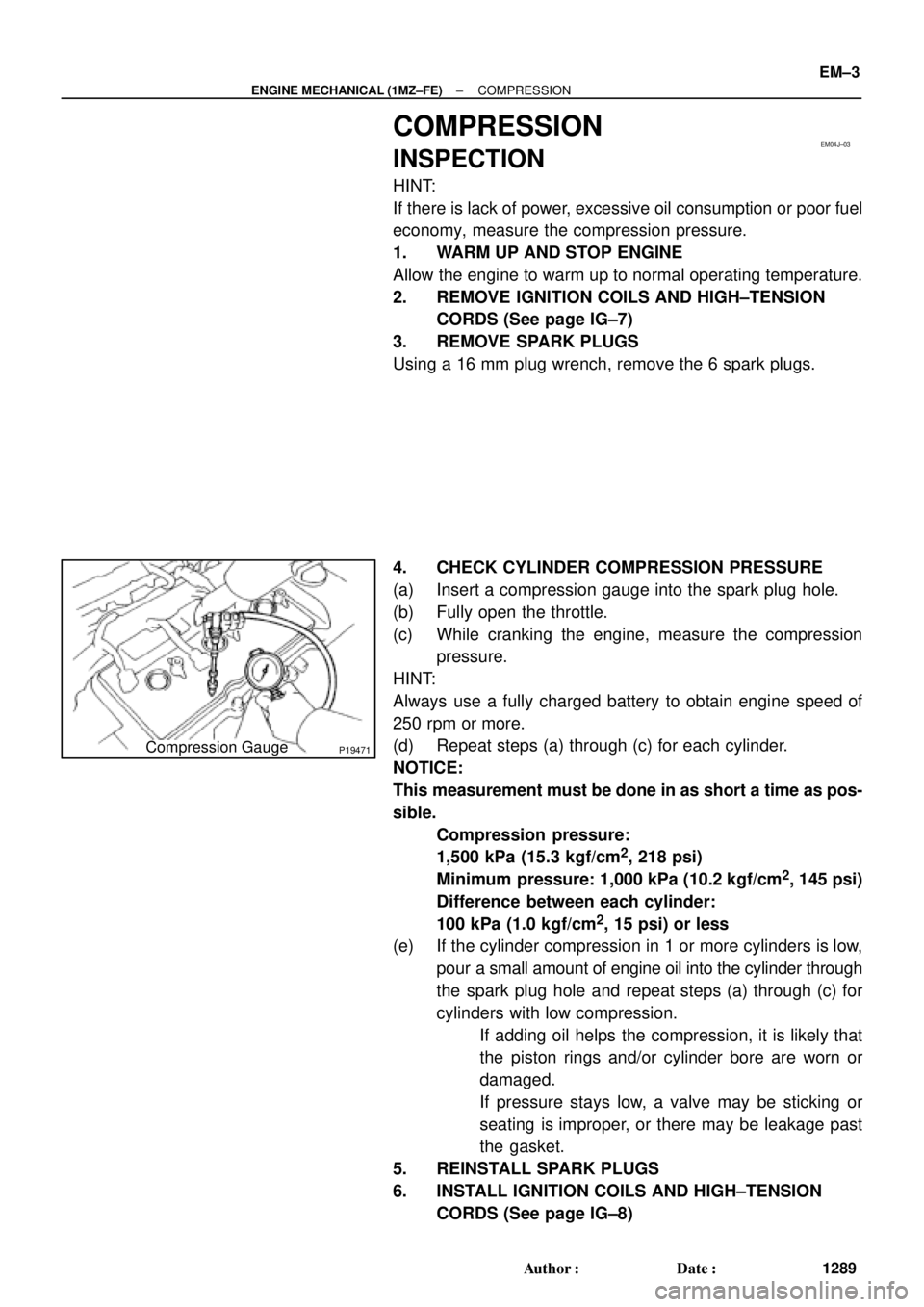
EM04J±03
P19471Compression Gauge
± ENGINE MECHANICAL (1MZ±FE)COMPRESSION
EM±3
1289 Author: Date:
COMPRESSION
INSPECTION
HINT:
If there is lack of power, excessive oil consumption or poor fuel
economy, measure the compression pressure.
1. WARM UP AND STOP ENGINE
Allow the engine to warm up to normal operating temperature.
2. REMOVE IGNITION COILS AND HIGH±TENSION
CORDS (See page IG±7)
3. REMOVE SPARK PLUGS
Using a 16 mm plug wrench, remove the 6 spark plugs.
4. CHECK CYLINDER COMPRESSION PRESSURE
(a) Insert a compression gauge into the spark plug hole.
(b) Fully open the throttle.
(c) While cranking the engine, measure the compression
pressure.
HINT:
Always use a fully charged battery to obtain engine speed of
250 rpm or more.
(d) Repeat steps (a) through (c) for each cylinder.
NOTICE:
This measurement must be done in as short a time as pos-
sible.
Compression pressure:
1,500 kPa (15.3 kgf/cm
2, 218 psi)
Minimum pressure: 1,000 kPa (10.2 kgf/cm
2, 145 psi)
Difference between each cylinder:
100 kPa (1.0 kgf/cm
2, 15 psi) or less
(e) If the cylinder compression in 1 or more cylinders is low,
pour a small amount of engine oil into the cylinder through
the spark plug hole and repeat steps (a) through (c) for
cylinders with low compression.
If adding oil helps the compression, it is likely that
the piston rings and/or cylinder bore are worn or
damaged.
If pressure stays low, a valve may be sticking or
seating is improper, or there may be leakage past
the gasket.
5. REINSTALL SPARK PLUGS
6. INSTALL IGNITION COILS AND HIGH±TENSION
CORDS (See page IG±8)
Page 3510 of 4770
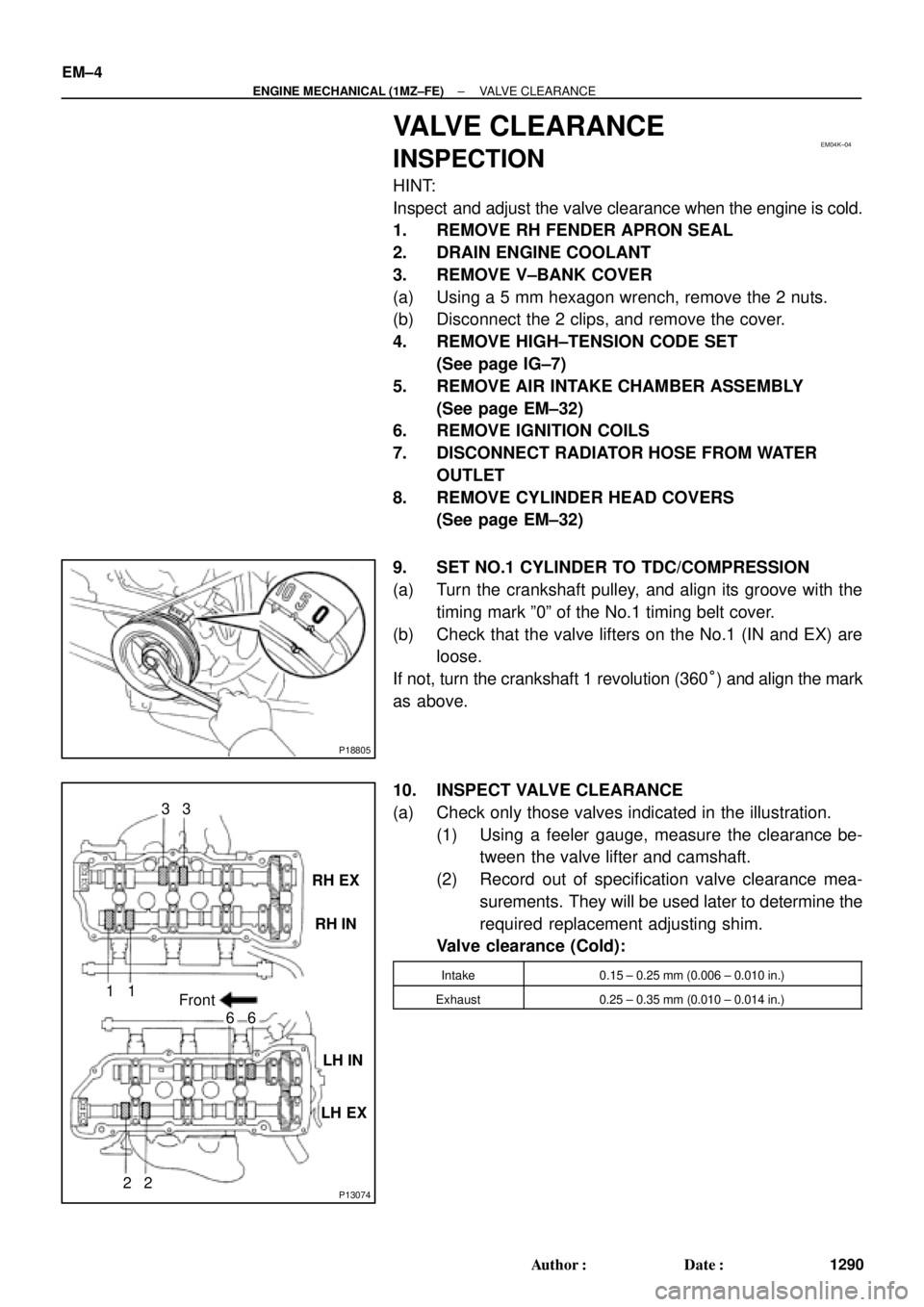
EM04K±04
P18805
P13074
RH EX
RH IN
LH IN
LH EX 13
6
23
1
6
2Front EM±4
± ENGINE MECHANICAL (1MZ±FE)VALVE CLEARANCE
1290 Author: Date:
VALVE CLEARANCE
INSPECTION
HINT:
Inspect and adjust the valve clearance when the engine is cold.
1. REMOVE RH FENDER APRON SEAL
2. DRAIN ENGINE COOLANT
3. REMOVE V±BANK COVER
(a) Using a 5 mm hexagon wrench, remove the 2 nuts.
(b) Disconnect the 2 clips, and remove the cover.
4. REMOVE HIGH±TENSION CODE SET
(See page IG±7)
5. REMOVE AIR INTAKE CHAMBER ASSEMBLY
(See page EM±32)
6. REMOVE IGNITION COILS
7. DISCONNECT RADIATOR HOSE FROM WATER
OUTLET
8. REMOVE CYLINDER HEAD COVERS
(See page EM±32)
9. SET NO.1 CYLINDER TO TDC/COMPRESSION
(a) Turn the crankshaft pulley, and align its groove with the
timing mark º0º of the No.1 timing belt cover.
(b) Check that the valve lifters on the No.1 (IN and EX) are
loose.
If not, turn the crankshaft 1 revolution (360°) and align the mark
as above.
10. INSPECT VALVE CLEARANCE
(a) Check only those valves indicated in the illustration.
(1) Using a feeler gauge, measure the clearance be-
tween the valve lifter and camshaft.
(2) Record out of specification valve clearance mea-
surements. They will be used later to determine the
required replacement adjusting shim.
Valve clearance (Cold):
Intake0.15 ± 0.25 mm (0.006 ± 0.010 in.)
Exhaust0.25 ± 0.35 mm (0.010 ± 0.014 in.)
Page 3511 of 4770
P13072
RH IN
LH IN
LH EX RH EX 5
3
435
4 22Front
P13073
RH IN
LH IN
LH EX RH EX
5 1
4
65
4 1
6 Front
P12919
Upward
Notch
± ENGINE MECHANICAL (1MZ±FE)VALVE CLEARANCE
EM±5
1291 Author: Date:
(b) Turn the crankshaft 2/3 of a revolution (240°), and check
only the valves indicated in the illustration. Measure the
valve clearance. (See step (a))
(c) Turn the crankshaft a further 2/3 of a revolution (240°),
and check only the valves indicated in the illustration.
Measure the valve clearance. (See step (a))
11. ADJUST VALVE CLEARANCE
(a) Remove the adjusting shim.
(1) Turn the camshaft so that the cam lobe for the valve
to be adjusted faces up.
(2) Turn the valve lifter with a screwdriver so that the
notches are perpendicular to the camshaft.
Page 3512 of 4770
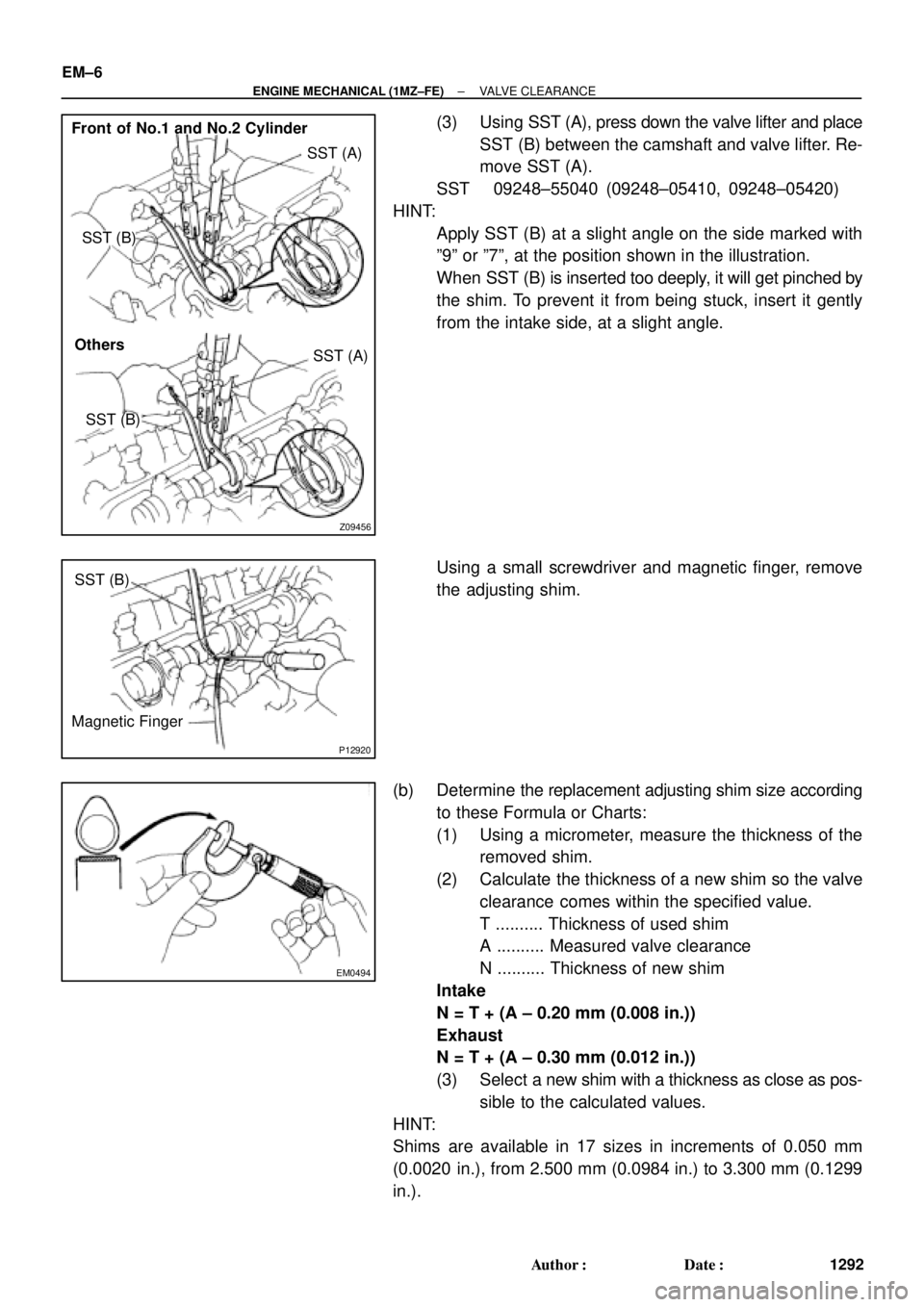
Z09456
Front of No.1 and No.2 Cylinder
OthersSST (A)
SST (B) SST (B)
SST (A)
P12920
SST (B)
Magnetic Finger
EM0494
EM±6
± ENGINE MECHANICAL (1MZ±FE)VALVE CLEARANCE
1292 Author: Date:
(3) Using SST (A), press down the valve lifter and place
SST (B) between the camshaft and valve lifter. Re-
move SST (A).
SST 09248±55040 (09248±05410, 09248±05420)
HINT:
Apply SST (B) at a slight angle on the side marked with
º9º or º7º, at the position shown in the illustration.
When SST (B) is inserted too deeply, it will get pinched by
the shim. To prevent it from being stuck, insert it gently
from the intake side, at a slight angle.
Using a small screwdriver and magnetic finger, remove
the adjusting shim.
(b) Determine the replacement adjusting shim size according
to these Formula or Charts:
(1) Using a micrometer, measure the thickness of the
removed shim.
(2) Calculate the thickness of a new shim so the valve
clearance comes within the specified value.
T .......... Thickness of used shim
A .......... Measured valve clearance
N .......... Thickness of new shim
Intake
N = T + (A ± 0.20 mm (0.008 in.))
Exhaust
N = T + (A ± 0.30 mm (0.012 in.))
(3) Select a new shim with a thickness as close as pos-
sible to the calculated values.
HINT:
Shims are available in 17 sizes in increments of 0.050 mm
(0.0020 in.), from 2.500 mm (0.0984 in.) to 3.300 mm (0.1299
in.).