Page 1729 of 4770
AUTOMATIC TRANSAXLEDIFFERENTIAL ASSEMBLY ±
AX±96
(b) Measure the oil seal press in depth.
Oil seal press in depth:
4 mm (0.16 in.)
(c) With the oil seal lip facing upward, use SST to press in a
new oil seal until its end is flush with the surface of the
cage.
SST 09350±32014 (09351±32090)
(d) Coat the oil seal lip with MP grease.
3. INSTALL SHAFT BEARING OUTER RACE TO CAGE
Using SST, press a new outer race into the cage.
SST 09350±32014 (09351±32111, 09351±32130)
4. INSTALL DRIVE PINION SHAFT BEARING
Using SST, press in the bearing.
SST 09350±32014 (09351±32100)
5. PLACE BEARING CAGE ONTO DRIVE PINION SHAFT
Be careful not to damage the oil seal with the splines.
Page 1730 of 4770
AUTOMATIC TRANSAXLEDIFFERENTIAL ASSEMBLY ±
AX±97
DIFFERENTIAL SIDE BEARING PRELOAD
ADJUSTMENT
1. PLACE OUTER RACE AND ADJUSTING SHIM ONTO
RH SIDE BEARING
Use the adjusting shim which was removed or one 2.40
mm (0.0945 in.) thick.
2. PLACE DIFFERENTIAL CASE INTO TRANSAXLE
CASE
Be sure to install the adjusting shim.
3. INSTALL LH BEARING RETAINER
(a) Do not install the O±ring yet.
(b) Do not coat the bolt threads with sealant yet.
(c) Temporarily tighten the bolts evenly and gradually while
turning the ring gear.
4. INSTALL RH SIDE BEARING CAP
Tighten the bolts evenly and gradually while turning the
ring gear.
Torque: 72 N´m (730 kgf´cm, 53 ft´lbf)
5. TIGHTEN LH BEARING RETAINER
Torque: 19 N´m (195 kgf´cm, 14 ft´lbf)
AX0GL±02
Page 1731 of 4770
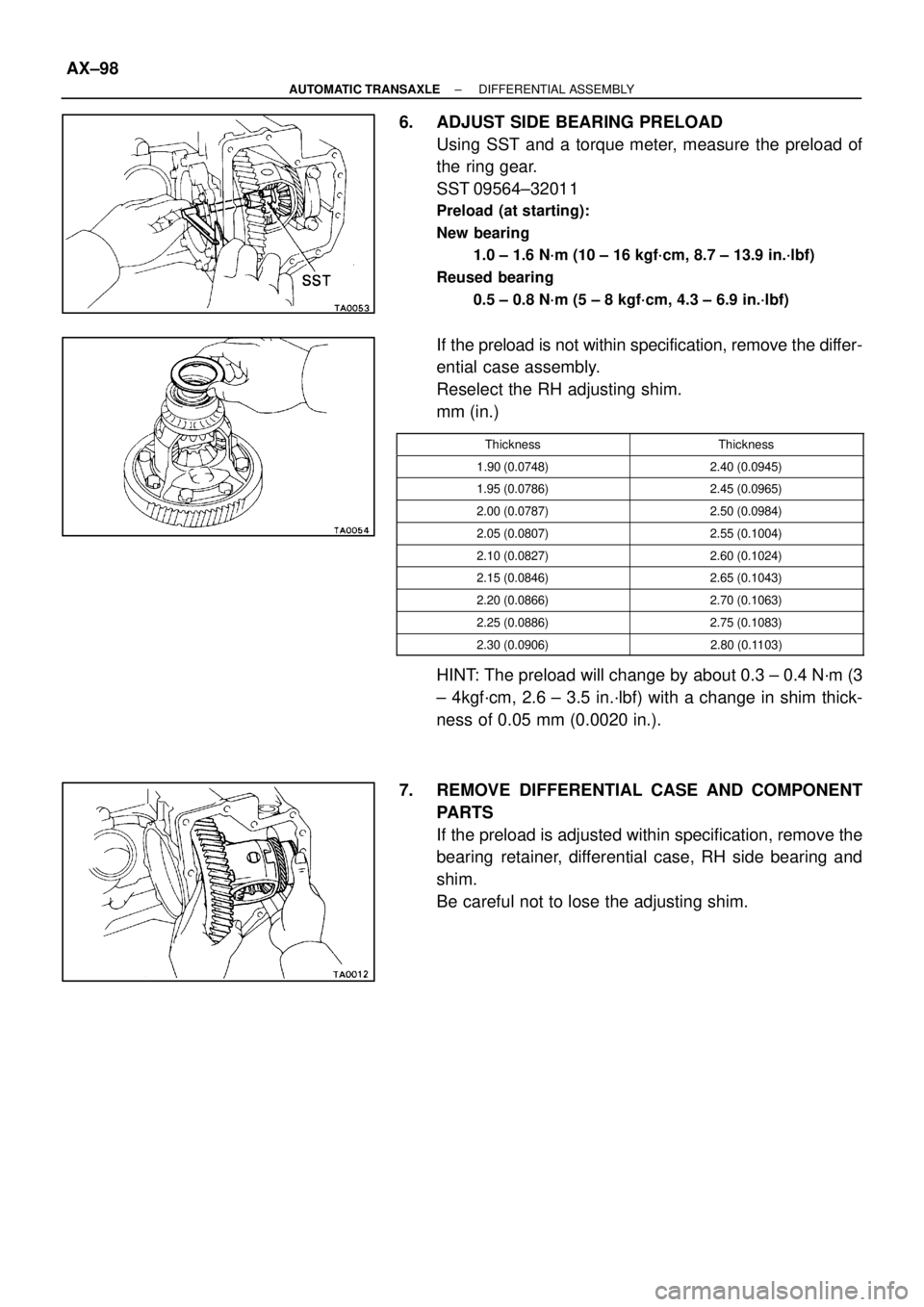
AUTOMATIC TRANSAXLEDIFFERENTIAL ASSEMBLY ±
AX±98
6. ADJUST SIDE BEARING PRELOAD
Using SST and a torque meter, measure the preload of
the ring gear.
SST 09564±32011
Preload (at starting):
New bearing
1.0 ± 1.6 N´m (10 ± 16 kgf´cm, 8.7 ± 13.9 in.´lbf)
Reused bearing
0.5 ± 0.8 N´m (5 ± 8 kgf´cm, 4.3 ± 6.9 in.´lbf)
If the preload is not within specification, remove the differ-
ential case assembly.
Reselect the RH adjusting shim.
mm (in.)
ThicknessThickness
1.90 (0.0748)2.40 (0.0945)
1.95 (0.0786)2.45 (0.0965)
2.00 (0.0787)2.50 (0.0984)
2.05 (0.0807)2.55 (0.1004)
2.10 (0.0827)2.60 (0.1024)
2.15 (0.0846)2.65 (0.1043)
2.20 (0.0866)2.70 (0.1063)
2.25 (0.0886)2.75 (0.1083)
2.30 (0.0906)2.80 (0.1103)
HINT: The preload will change by about 0.3 ± 0.4 N´m (3
± 4kgf´cm, 2.6 ± 3.5 in.´lbf) with a change in shim thick-
ness of 0.05 mm (0.0020 in.).
7. REMOVE DIFFERENTIAL CASE AND COMPONENT
PARTS
If the preload is adjusted within specification, remove the
bearing retainer, differential case, RH side bearing and
shim.
Be careful not to lose the adjusting shim.
Page 1732 of 4770
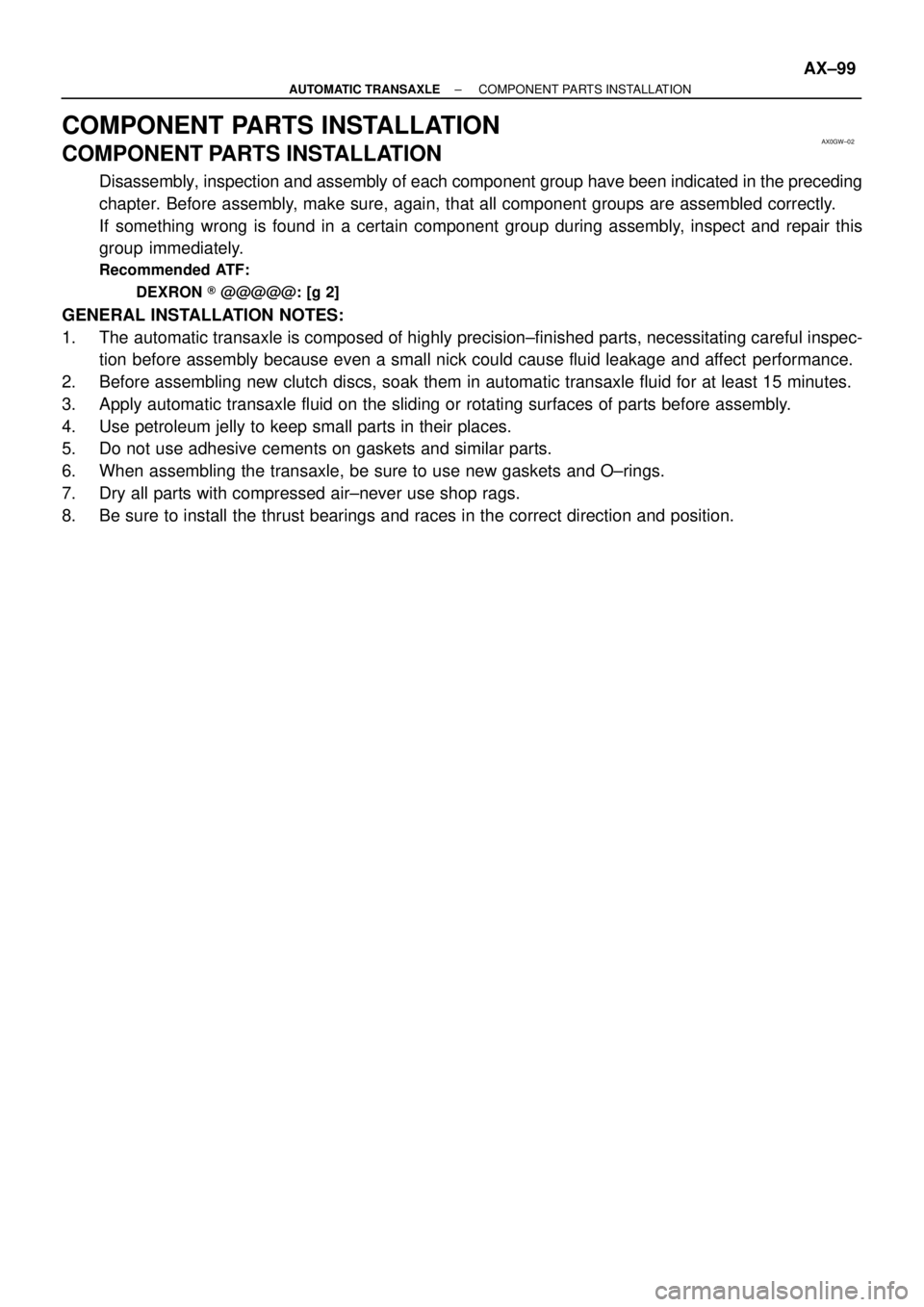
AUTOMATIC TRANSAXLECOMPONENT PARTS INSTALLATION ±
AX±99
COMPONENT PARTS INSTALLATION
COMPONENT PARTS INSTALLATION
Disassembly, inspection and assembly of each component group have been indicated in the preceding
chapter. Before assembly, make sure, again, that all component groups are assembled correctly.
If something wrong is found in a certain component group during assembly, inspect and repair this
group immediately.
Recommended ATF:
DEXRON ® @@@@@: [g 2]
GENERAL INSTALLATION NOTES:
1. The automatic transaxle is composed of highly precision±finished parts, necessitating careful inspec-
tion before assembly because even a small nick could cause fluid leakage and affect performance.
2. Before assembling new clutch discs, soak them in automatic transaxle fluid for at least 15 minutes.
3. Apply automatic transaxle fluid on the sliding or rotating surfaces of parts before assembly.
4. Use petroleum jelly to keep small parts in their places.
5. Do not use adhesive cements on gaskets and similar parts.
6. When assembling the transaxle, be sure to use new gaskets and O±rings.
7. Dry all parts with compressed air±never use shop rags.
8. Be sure to install the thrust bearings and races in the correct direction and position.
AX0GW±02
Page 1733 of 4770
AUTOMATIC TRANSAXLECOMPONENT PARTS INSTALLATION ±
AX±100
BEARING AND RACE DIAMETERS
mm
(in.)Front Bearing Race
Outer / Inner DiameterThrust Bearing Race
Outer / Inner DiameterRear Bearing Race
Outer / Inner Diameter
@@
@@
@:
[c A]
43.0 / 30.5 (1.693 / 1.201)42.0 / 28.9 (1.654 / 1.138)42.0 / 27.1 (1.654 / 1.067)
Page 1734 of 4770
AUTOMATIC TRANSAXLECOMPONENT PARTS INSTALLATION ±
AX±101
@@
@@
@:
[c B]
37.9 / 22.0 (1.492 / 0.866)36.1 / 22.2 (1.421 / 0.874)35.7 / 23.0 (1.406 / 0.906)
@@
@@
@:
[c C]
37.9 / 22.0 (1.492 / 0.866)36.1 / 22.2 (1.421 / 0.874)35.0 / 19.0 (1.378 / 0.748)
@@
@@
@:
[c D]
45.0 / 28.0 (1.772 / 1.102)45.0 / 30.0 (1.772 / 1.181)±
@@
@@
@:
[c E]
37.3 / 24.1 (1.469 / 0.949)37.6 / 24.0 (1.480 / 0.945)37.6 / 22.2 (1.480 / 0.874)
@@
@@
@:
[c F]
±46.3 / 26.2 (1.823 / 1.031)43.0 / 24.5 (1.693 / 0.965)
DRIVE PINION ASSEMBLY INSTALLATION
1. INSTALL NEW O±RING ONTO BEARING CAGE
2. INSTALL DRIVE PINION SHAFT INTO CASE
Slightly tap the cage into the case until the groove with the
bore can be see.
HINT: Drive in the bearing cage until the surface of the
bearing cage passes through the groove with the bore.
AX0GM±02
Page 1735 of 4770
AUTOMATIC TRANSAXLECOMPONENT PARTS INSTALLATION ±
AX±102
3. INSTALL SNAP RING INTO CASE
(a) Using SST, install the snap ring into the groove.
SST 09350±32014 (09351±32050)
(b) Slightly tap the drive pinion to fit the snap ring into the
groove.
4. INSTALL ROTOR SENSOR
Install the rotor sensor, facing the magnet outward.
5. INSTALL OIL SLINGER
Install the oil slinger, facing the lip outward.
6. INSTALL OUTER RACE
Using SST, drive the outer race into the case.
SST 09350±32014 (09351±32100, 09351±32140)
Page 1736 of 4770
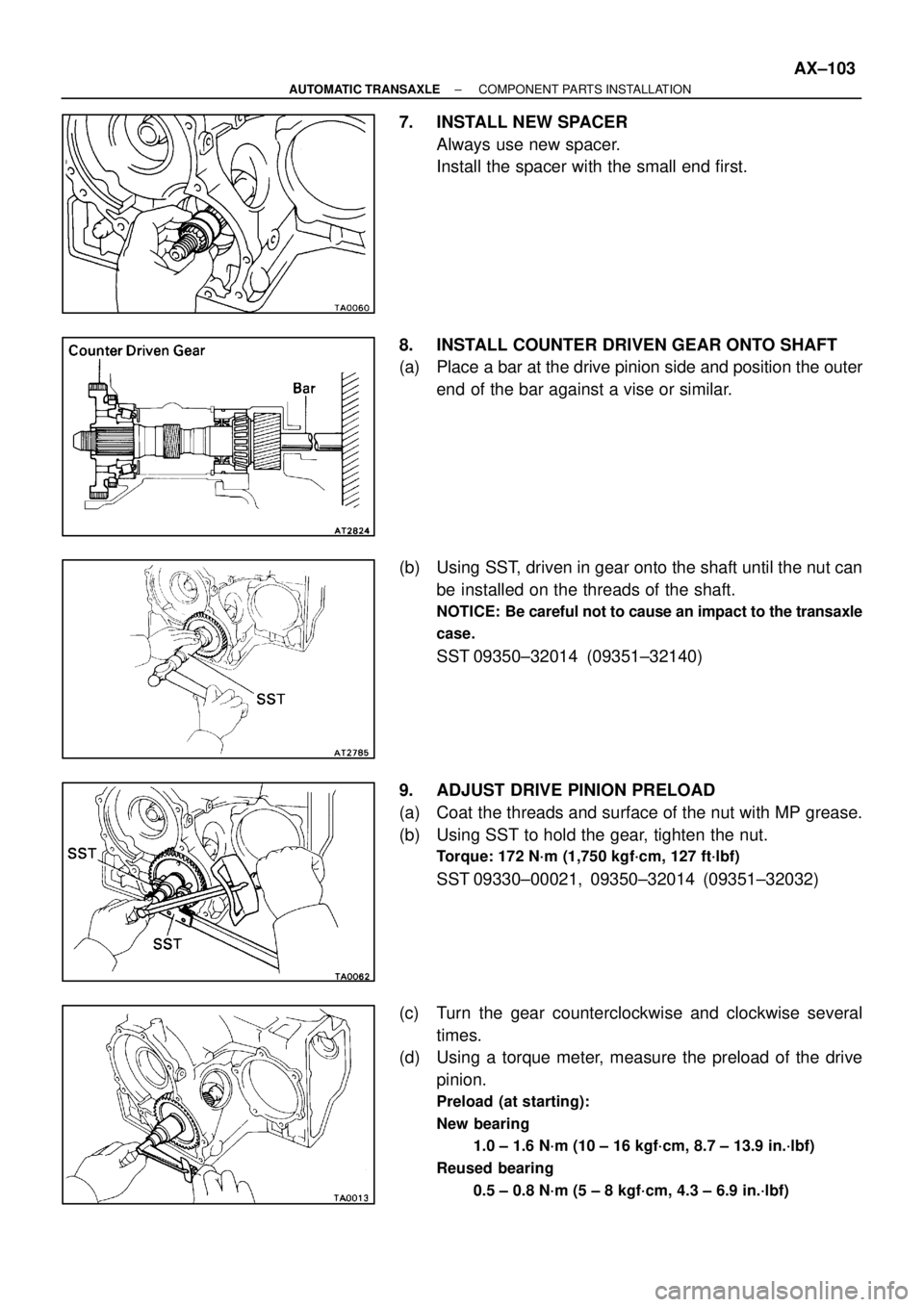
AUTOMATIC TRANSAXLECOMPONENT PARTS INSTALLATION ±
AX±103
7. INSTALL NEW SPACER
Always use new spacer.
Install the spacer with the small end first.
8. INSTALL COUNTER DRIVEN GEAR ONTO SHAFT
(a) Place a bar at the drive pinion side and position the outer
end of the bar against a vise or similar.
(b) Using SST, driven in gear onto the shaft until the nut can
be installed on the threads of the shaft.
NOTICE: Be careful not to cause an impact to the transaxle
case.
SST 09350±32014 (09351±32140)
9. ADJUST DRIVE PINION PRELOAD
(a) Coat the threads and surface of the nut with MP grease.
(b) Using SST to hold the gear, tighten the nut.
Torque: 172 N´m (1,750 kgf´cm, 127 ft´lbf)
SST 09330±00021, 09350±32014 (09351±32032)
(c) Turn the gear counterclockwise and clockwise several
times.
(d) Using a torque meter, measure the preload of the drive
pinion.
Preload (at starting):
New bearing
1.0 ± 1.6 N´m (10 ± 16 kgf´cm, 8.7 ± 13.9 in.´lbf)
Reused bearing
0.5 ± 0.8 N´m (5 ± 8 kgf´cm, 4.3 ± 6.9 in.´lbf)